Our Team
Four mechanical engineering students put their skills to the test.
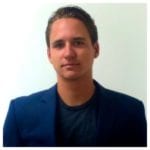
Ben Brough
Procurement Lead
I am the liaison for our team to contact companies and order parts for our needs.

Jacob David
Testing Lead
I am in charge of organizing the testing days and shifts as well as the expert on obtaining testing data.
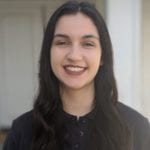
Jessica Mabry
Project Manager
I am in charge of tracking project status and deadlines, documentation, and checking criteria is met
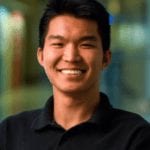
Justin Lam
Manufacturing Lead
I am in charge of developing the manufacturing schedule as well as manufacturing the parts.
Acknowledgements
This project would not have been possible without Dr. Peuker’s sponsorship and counsel. We would also like to thank Professor Harding for her guidance as well as the ME department and ASHRAE for this project opportunity.
OUR PROJECT VIDEOS
Cloud Catchers - Atmospheric Water harvester
Problem Statement
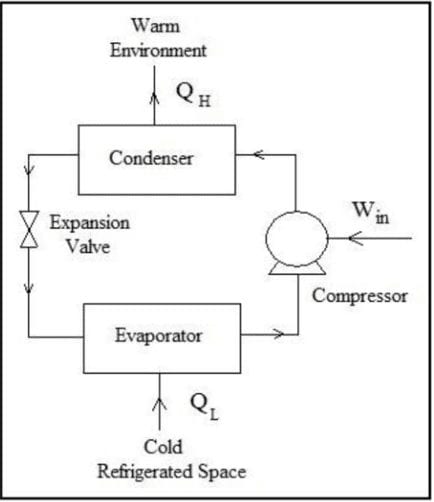
Certain climates and ecological areas do not have easy access to clean water and, thereby, require alternative water sources to supply their needs. The goal of this project is to provide insight into the status quo from a technical standpoint by improving the efficiency of active water collection from the atmosphere using a vapor compression cycle.
The specific scope of this senior project was to increase the efficiency of an existing atmospheric water harvester.
Design Constraints
- Must use R-134a
- Must be small enough to fit on a cart
- Must have a higher efficiency rate (2.4L/kWh @ 80% Relative Humidity)
AWH Design Improvement

Previous Piping Layout

New Piping Layout
Piping Layout:
- Piping layout was redesigned as to reduce the amount of inefficiencies from a theoretical minor loss coefficient of 2.4 down to 2.
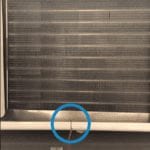
Previous thermocouple setup
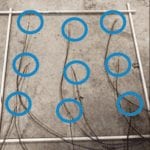
New thermocouple mesh
Thermocouple Mesh Design:
- We determined a single thermocouple node placed in front of the evaporator was prone to inaccuracy. Therefore, we decided to improve the reliability of the data by creating a thermocouple mesh of nine nodes that spanned the entire inlet of the evaporator. This mesh allowed us to obtain a hardware average of the recorded temperature of the air.
Bracket Design

Steel Brackets attached to the evaporator
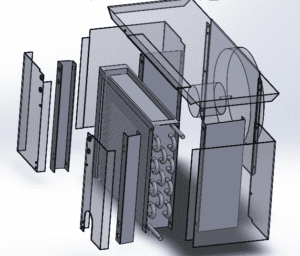
Exploded view to show all components included in the fully assembled evaporator.
The CAD model was necessary to determine how to manufacture the new brackets for the custom evaporator while maintaining compatibility with the old fan case.
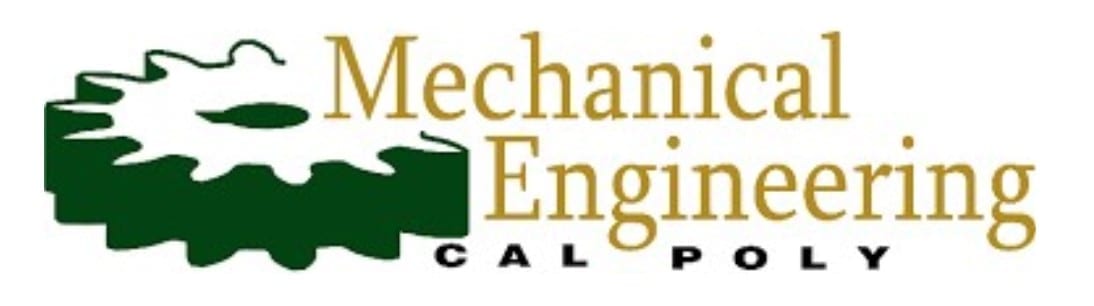
This project is sponsored by Dr. Steffen Peuker, Department of Mechanical Engineering
Evaporator Fin Comparison
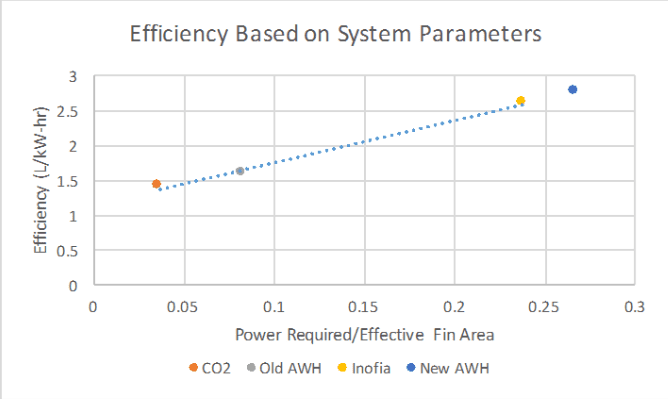
By comparing the testing data across three different Atmospheric Water Harvesting Systems (CO2 System, Inofia, and previous system), we determined a correlation between higher efficiency of the device and greater effective fin area.
Manufacturing Process and Components
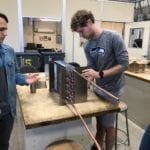
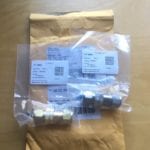
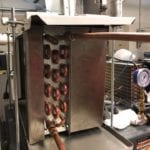
Design Verification
Most of the criteria aside from the efficiency testing was able to be tested before the shutdown for COVID-19.

Fan Speed Test-
The new evaporator has a closer fin spacing, which will change the resistance the air faces while flowing through the vent. In order to accurately determine the new fan speed settings, we used a flow-hood to measure each fan speed to obtain the new flow rates.
Thermocouple Mesh Verification-
The first two thermocouple nodes were hooked up in parallel via electrical nuts, which effectively created a hardware average of the nodes. When touching one of the nodes to our skin while keeping the other in the open, the reading averaged between the room temperature and the human body temperature. Hooking up 9 thermo-couple nodes in parallel resulted in similar results.
Leak Test-
Since the system is charged with R-134a, it is imperative that a leak test is performed before charging the system to ensure there are no leaks. The leak test is to be performed by a licensed HVAC professional, such as Dr. Peuker.
Final Evaporator Choice
We determined that the most effective method of increasing the efficiency would be improving the effective fin area of the evaporator.
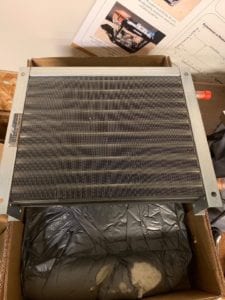
Previous Evaporator
- 12.5″ x 16″ x 3.5″
- 7 Fins/Inch
- 3/8″ tube
- 20 tubes
- 80.66ft^2 effective fin area
- Uses R-134a
Custom Evaporator
- 12.5″ x 16″ x 3.5″
- 16 Fins/Inch
- 3/8″ tube
- 20+ tubes
- 150 ft^2 effective fin area
- Uses R-134a
Future Improvement
Future iterations of this project will improve on this design by swapping out components, continuing to optimize the piping layout, and by gathering data on how the device performs.
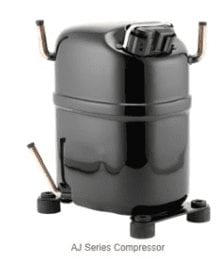
In order to match the new capacity of the evaporator, a new compressor/condensing unit will be required. However, upgrading the capacity will require a complex parallel/series configuration to continue using a 115 V power source.
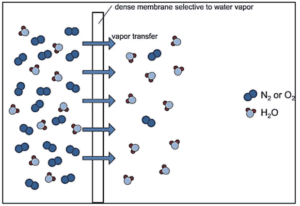
The next step may be to utilize a water vapor selective membrane to avoid cooling other atmospheric gases. Water vapor makes up a small component of air, which represents a large inefficiency.
Recommendations
Improvements to be made if the AWH were to be re-designed:
Manufacturing Tips
- When mapping out the piping configuration, use a stiff wire to map out exactly how the pipe should be oriented and where pipe bends should go
- When brazing pipes, rely on professional guidance during the design process
- Have a professional braze the pipes if the brazed junction is a likely failure mode
- Bend the pipes slowly to avoid kinks
Vendor Selection Tips
- Vendors should be carefully vetted prior to ordering
- Customer service and reliability are vendor traits that are often worth longer lead times and higher prices
- Vendors know their product catalog best and can assist in component selection for your application