Our Team
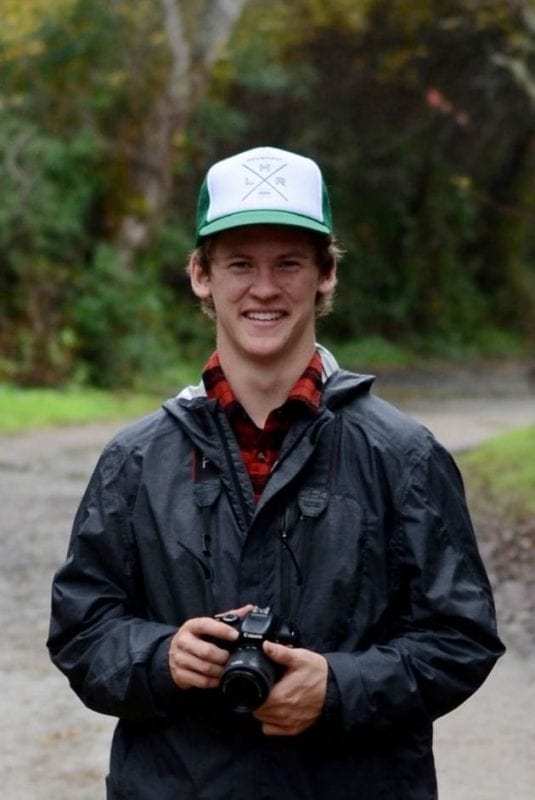
JP Purdom
I’m JP. I am a fifth year Mechanical Engineering student and enjoy automotive projects, mountain biking, and photography. I love being outdoors and always look for new ways to enjoy our beautiful world.
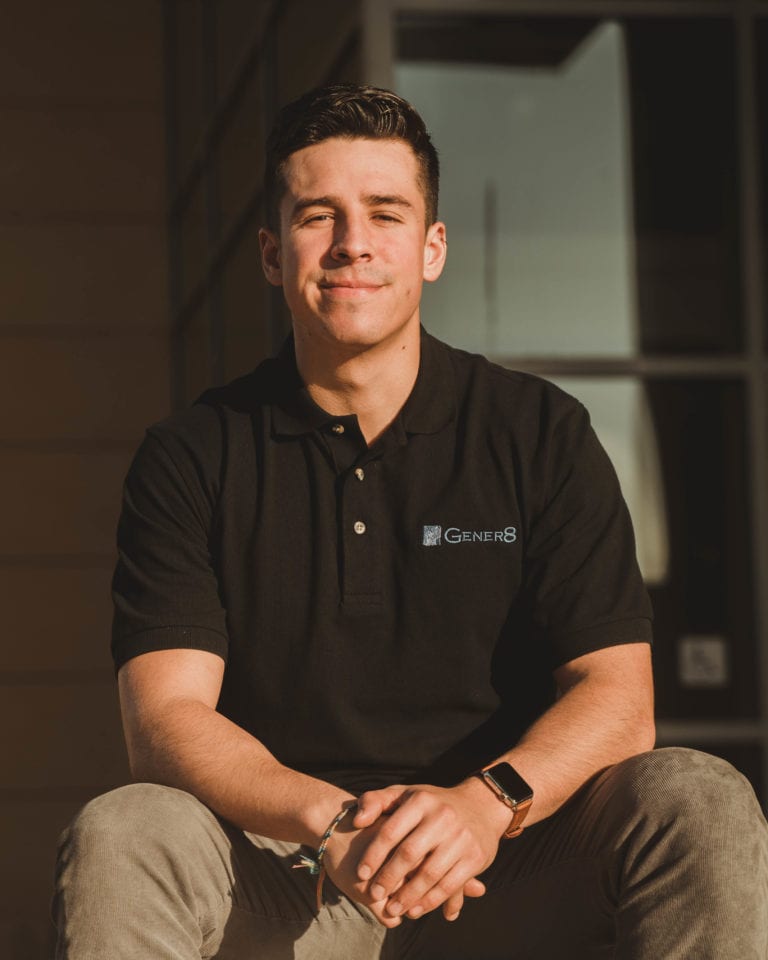
Leo franco
Hi I’m Leo Franco. I’m a really active person who likes to always stay busy and engaged! I enjoy surfing, cooking, and all things musical. I’m very interested in the aerospace and additive manufacturing industries.
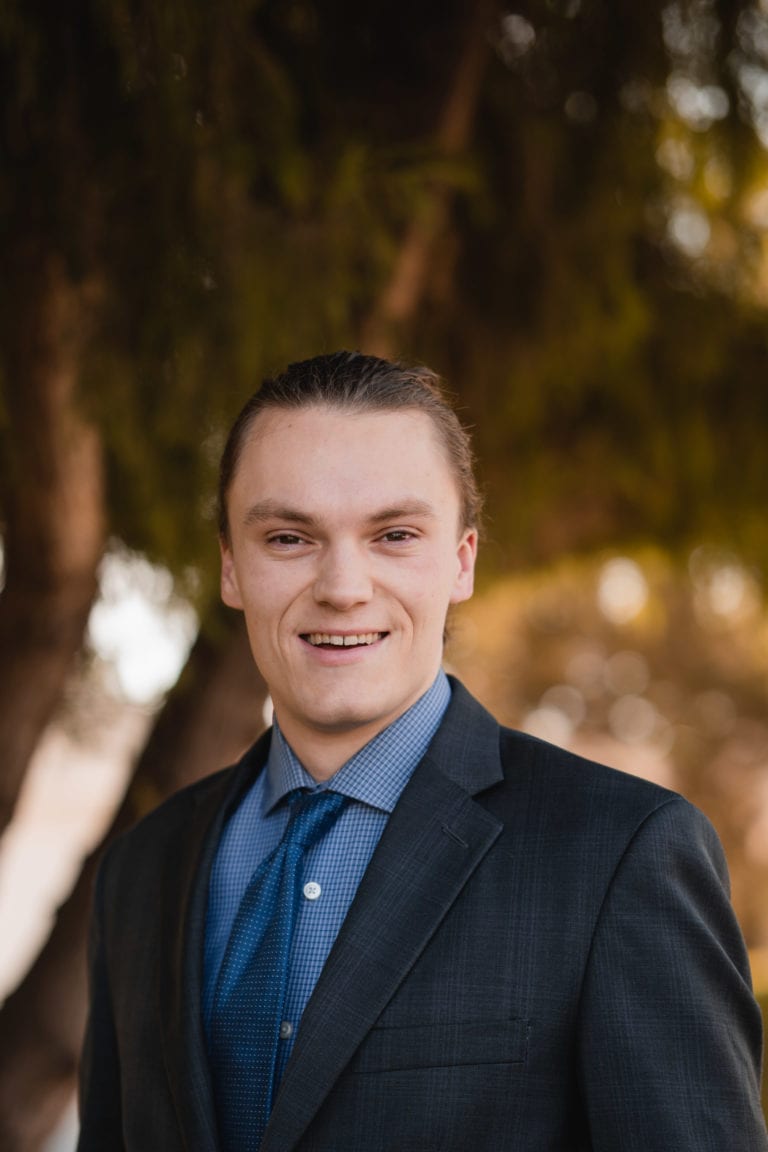
Sam Noble
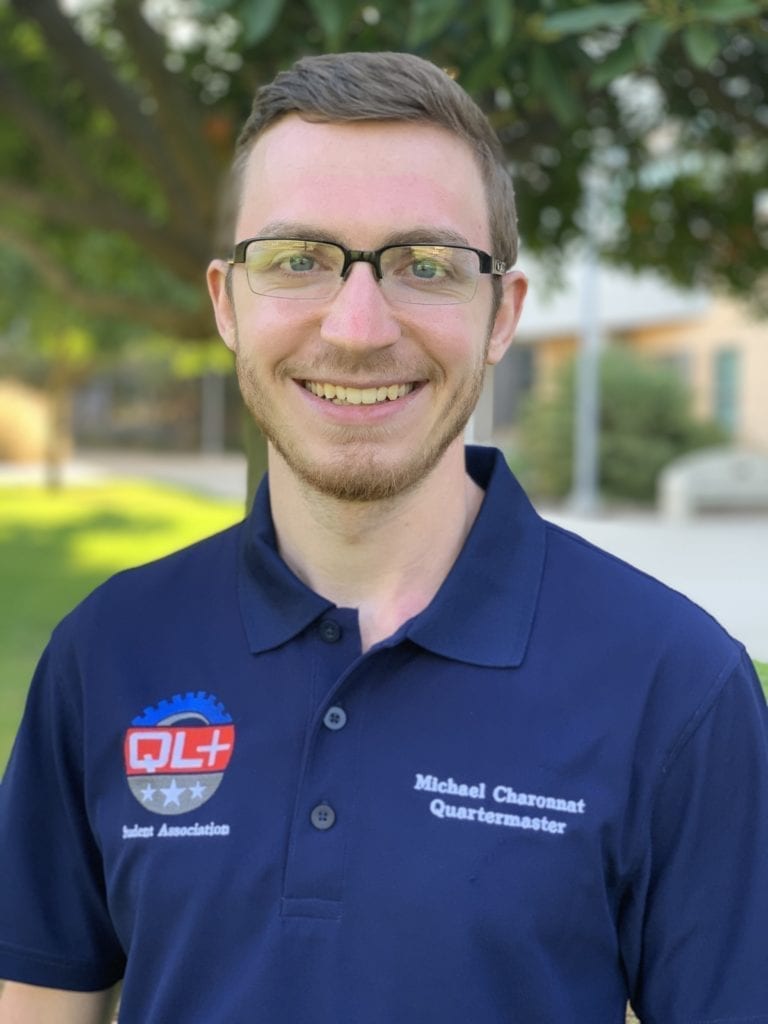
Michael Charonnat
Hi! My name is Michael Charonnat, and I’m from Thousand Oaks, CA. I’m finishing up my fourth year at Cal Poly and plan to begin the ME master’s blended program next fall. My primary interests are in aerospace, particularly fluids applications. In my free time, I enjoy road cycling, backpacking, and playing Spikeball.
Acknowledgements
- Cal Poly ME Department
- Professor Peter Schuster (Project Advisor)
- Jorge Hernandez (Design Engineer, Solar Turbines)
- Professor Xuan Wang (Additive Manufacturing, IME Department)
Our Project Videos
General Information regarding our project
Engineering analysis and in-depth description
Our Project's Digital Poster
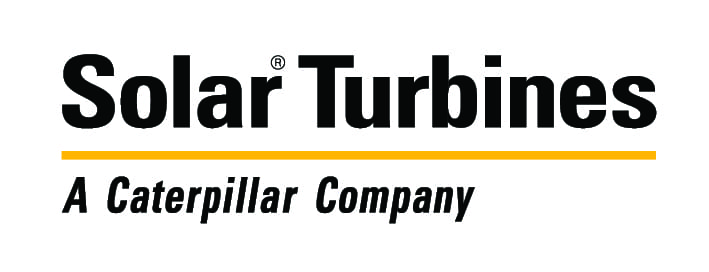
Problem Statement
- Explore the benefits of Additive Manufacturing (AM) compared to traditional manufacturing
- Construct a methodology for redesigning parts for mass reduction
- Construct a methodolgy for redesinging parts for warpage compensation in thin-walled members
COVID-19 Update
Due to COVID-19, we were unable to complete the original scope of work. In order to adapt to the situation, we pivoted to a software comparison instead of printing and comparing physical parts to simulated prints. This way, we were still able to provide Solar Turbines with useful information to help them in their design for AM process.
What is Additive Manufacturing?
- Additive Manufacturing (AM), sometimes referred to as 3-D printing, is a form of manufacturing that allows geometries to be “printed” on a layer-by-layer basis
- The metal AM process used in this project is Laser Powder Bed Fusion (L-PBF), which consists of fusing metal powder using a high powered laser to create completely metal parts.
Why AM?
- Shape Complexity: Build complex geometries while consolidating parts
- Hierarchical Complexity: control structures on multiple size scales
- Material Complexity: process material layer-by-layer
- Functional Complexity: consolidate assemblies
- Manufacturing Improvements:
- Increase prototyping speed
- Decrease lead times
- Decrease component weight & cost
- Hold tighter tolerances compared to casting processes
Design For Mass Reduction
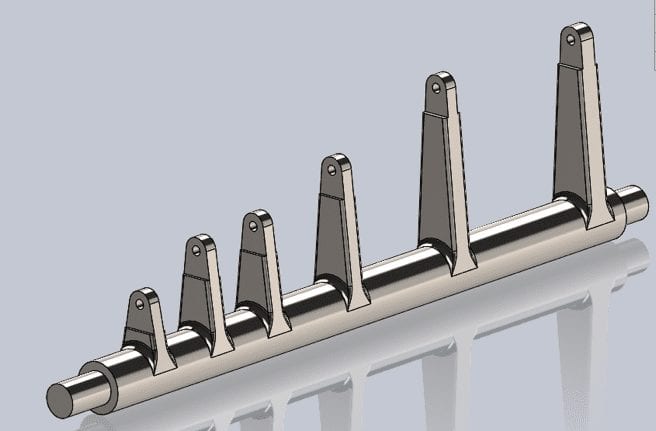
Methodology
- Understand fit, form, & function
- Benchmark current design
- Conduct shape studies
- Investigate principles of design for AM
- Generate initial design concepts
Benchmarking
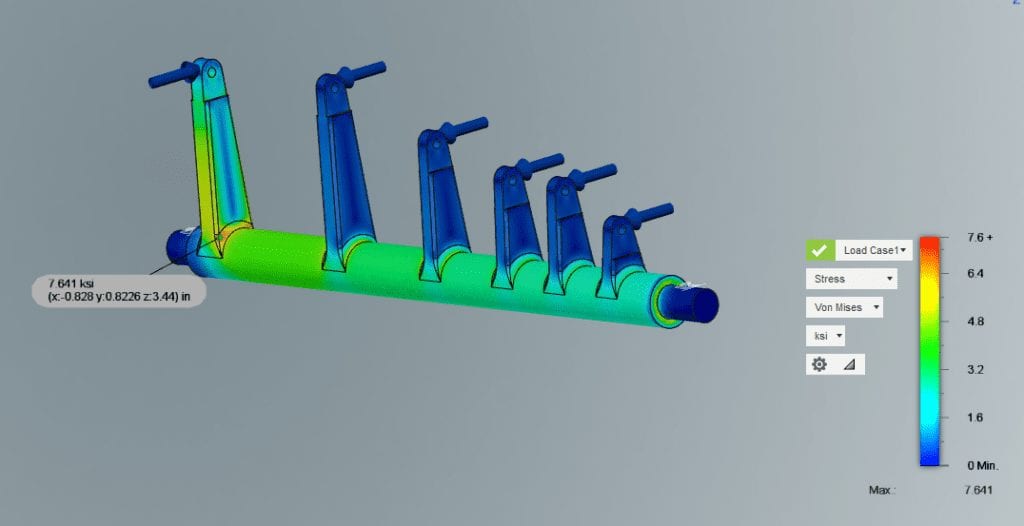
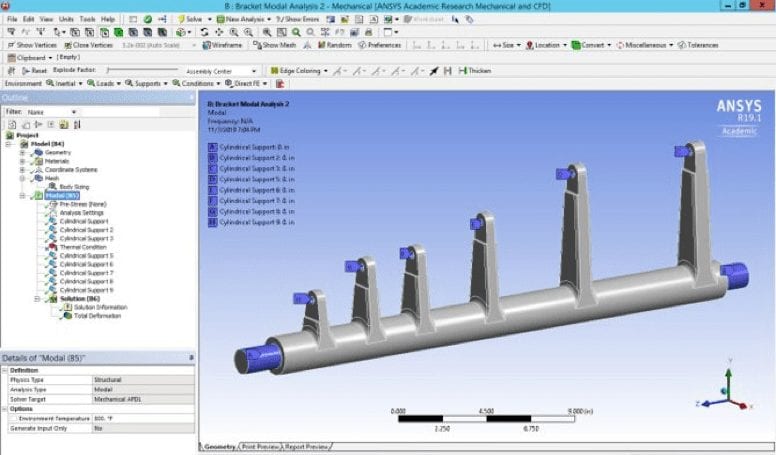
- Identified stress concentrations
- Conducted modal analysis
- Formed criteria for shape studies
- Baseline for comparison with re-design concepts
Shape Studies
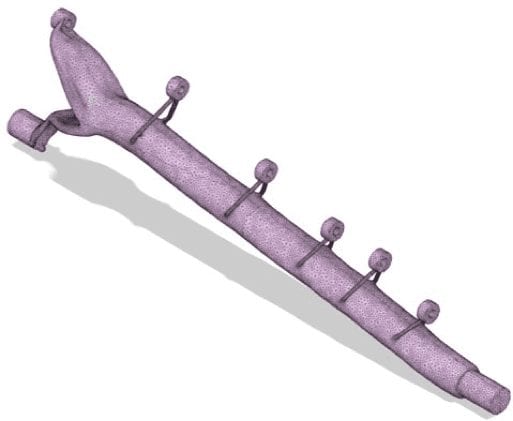
- Load on bracket arms decreased by angled shaft orientation
- Organic nature of the part rendered it too costly to print
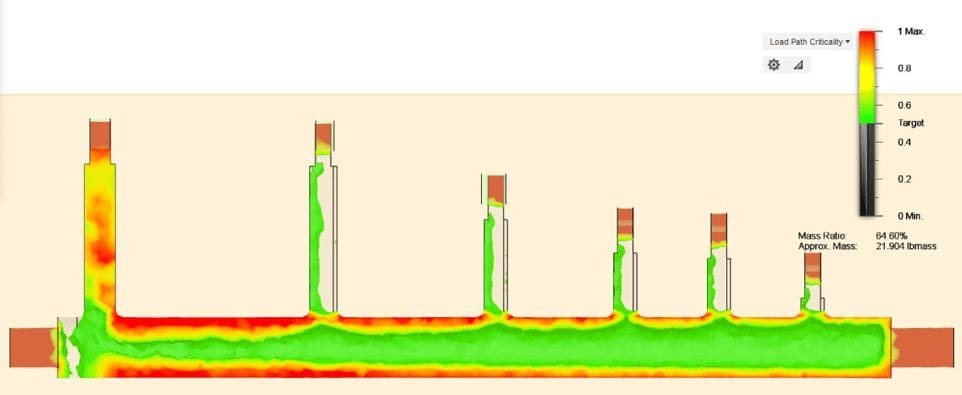
- Identified regions of material not necessary to support loading
- Aided team in decision to hollow out the cylinder and remove material from individual arms
final prototype design
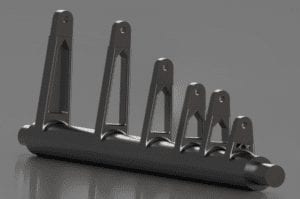
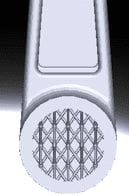
- Material removed from vertical bracket arms
- Lattice structure inside of cylindrical section
Design for am
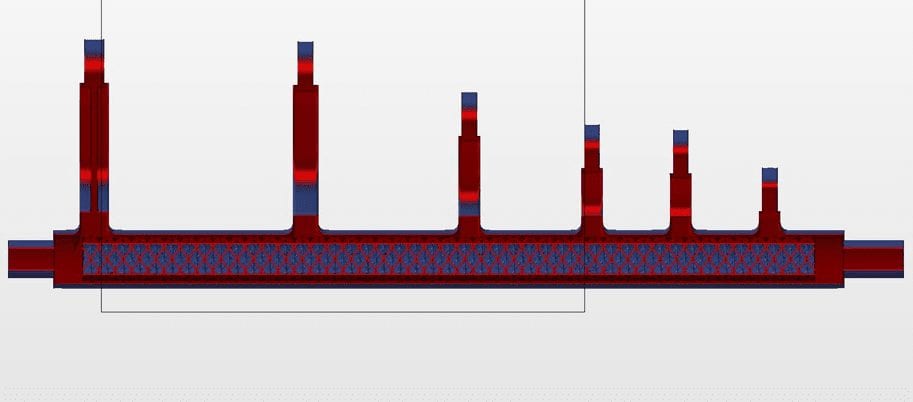

- Vertical print orientation allows for the simplest post-processing and minimizes need for support structures
- Lattice type selected for inside of the shaft allows the lattice to serve as support structure in cylindrical section
Final product Prototype
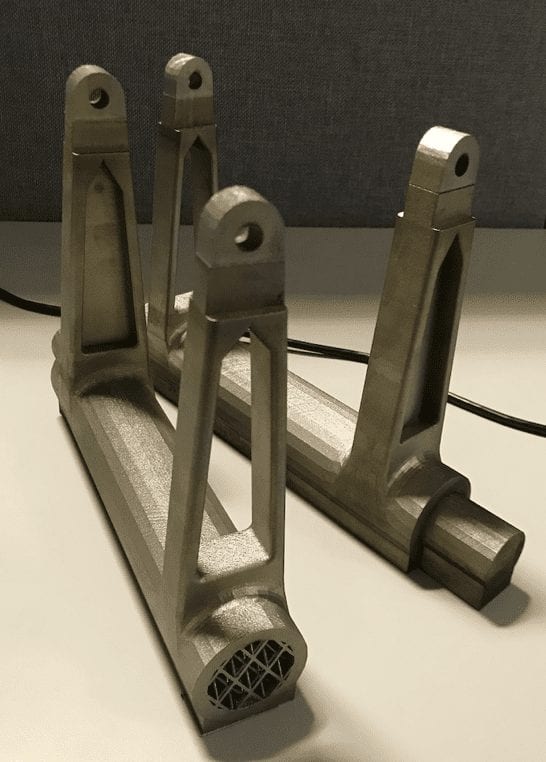
planned Testing and Verification
- Use a laser EDM and a finishing process to remove additional support material
- Test modal frequency with shake table
- Verify essential geometrical features with a CMM
Design For Warpage Compensation
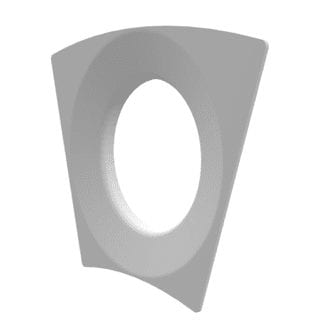
Methodology
- Utilize deflection simulation software to identify warpage locations
- Generate compensated geometry and run test prints (printing cancelled due to COVID)
- Compare simulation software packages and provide assessment to Solar Turbines
Design For am
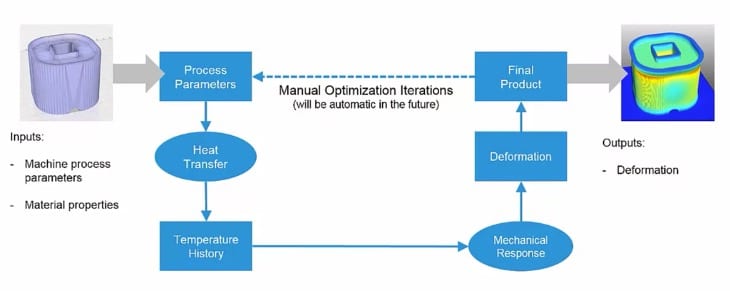
- Designing thin parts for AM is an iterative process, as seen in the above diagram
- Begins with importing a geometry and running a simulation
- After warpage is simulated and compensated geometry is generated, a second simulation can be run to verify the compensation
Netfabb simulation & Print
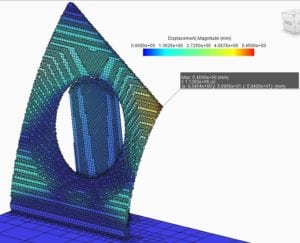
- Simulated real-time deflection and stresses in the printing of a simplified part model
- Identified locations of significant warpage
- Generated pre-warped (compensated) STL for printing
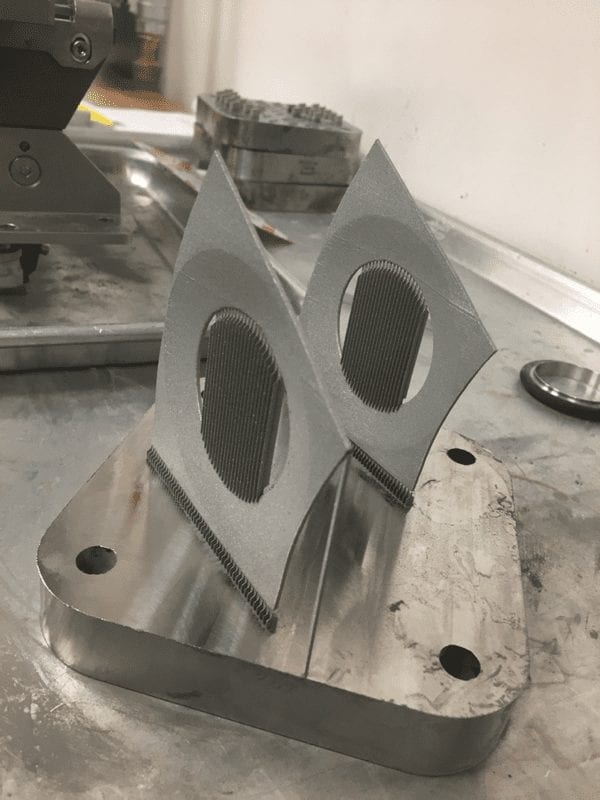
- Printed two copies of original part
- Planned to print compensated parts and compare deflection with CMM measurements (COVID restrictions prevented further prints)
3Dxpert Simulation
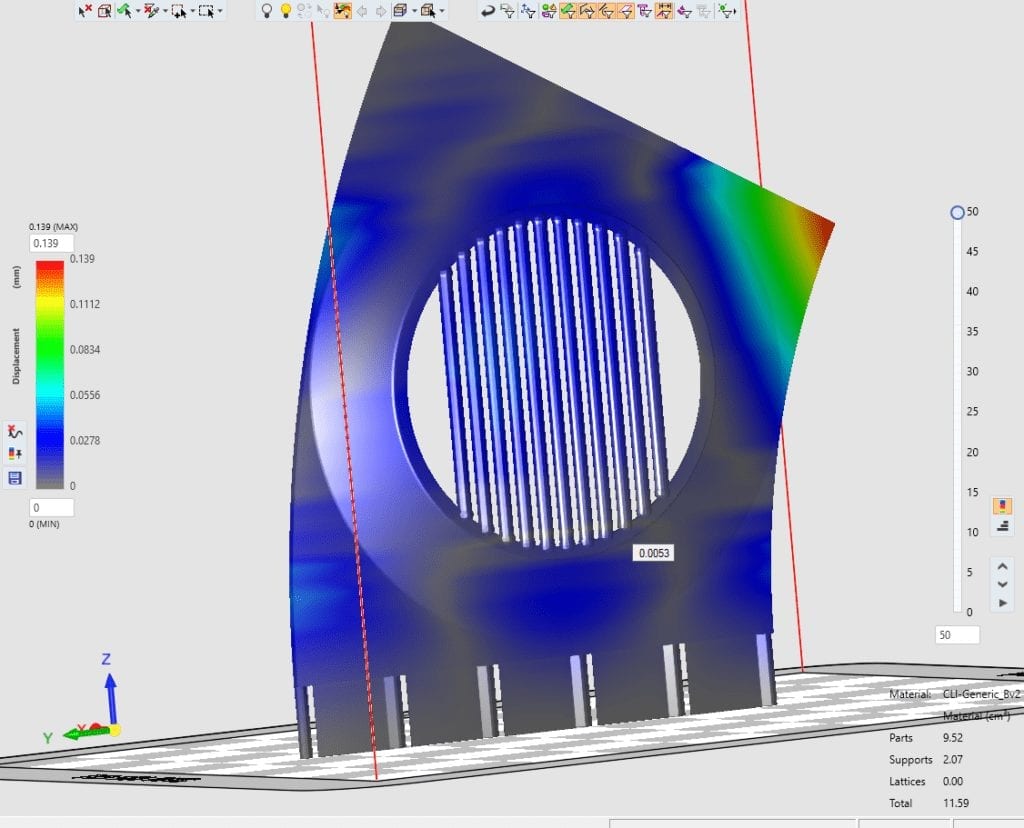
- Used 3DXpert to generate support structure and run simulation of print process
- Studied results for residual stress, distortion, and compensated geometry
AnSys Simulation
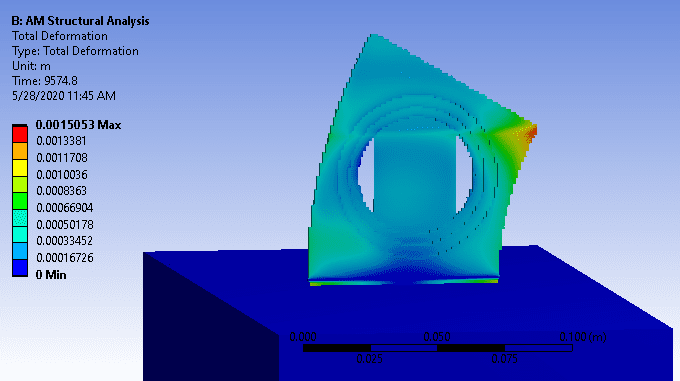
- Generated support structure using AM Wizard
- Ran thermal and structural simulation of part printing
- Obtained distortion results and warped geometry
Simulation software comparison
Netfabb:
- Easy learning curve
- Comes with predefined printer settings
- Allows for limited editing of imported geometry
- Confusing material property and print parameter interface
- Automatic & manual support generation
- Lacks control over mesh sizing
- Generates compensated STL
3DXpert:
- Intuitive interface
- Interfaces with SolidWorks
- Comes with predefined printer options and print parameters
- Automatic & manual support generation
- Confusing material property interface
- Easy to control mesh element sizing
- Generates compensated geometry
- Solar Turbines printer type not included in printer options (but may be added in the near future)
ANSYS Additive:
- Difficult to learn
- Simplified SolidWorks-like CAD functionality
- No predefined printer options or parameters
- Comes with extensive material database
- Generates support automatically, but only uses a singular support type
- Highly adjustable mesh settings
- Does not generate compensated geometry
Next steps
In order to continue this process of designing for AM, we recommend validation of our results by continuing the iterative process of printing and comparing those prints to software predictions. We believe the most effective way of generating an effective design is to run further testing such as CMM and shake table tests as we mentioned above. As for the software comparison, this depends on what ones specific needs are and what features are desire in a software. Out of the three different software we used, 3DXpert is the most comprehensive and intuitive. Using this software to design a part and simulate printing, followed by testing and iterations is an effective way to design for AM.
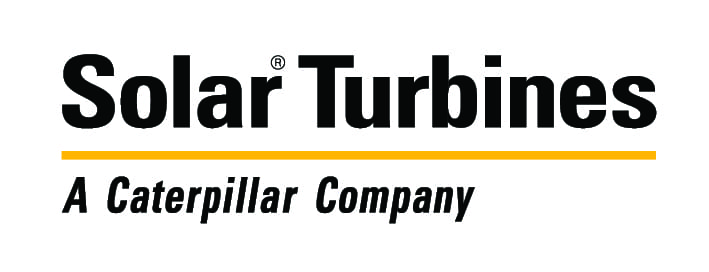