Our team
Mechanical Engineering students concentrating in Heating, Ventilating, Air-Conditioning, and Refrigerating
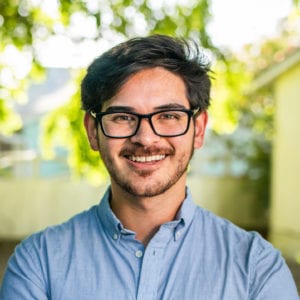
Jerry Wakai
head researcher
Future Project Engineer at Southland Industries, Union City, CA
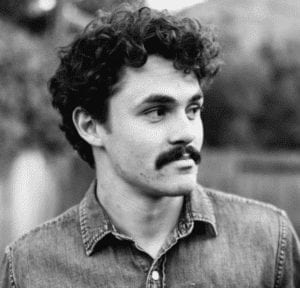
michael hanson
data analysis specialist
Future Graduate Mechanical Engineer at ARUP, Seattle, WA
Our Project Videos
Project Goals
- Gather and document information necessary to develop understanding of the mechanical systems in Building 41A and the Microfabrication Laboratory.
- Validate Microfabrication Laboratory’s operation as a Class 1000 clean room.
- Develop a Standard Operating Procedure for continual evaluation of indoor air quality.
- Investigate the condition of the HEPA filters and the potential effects of old filters.
Clean Room Classifications
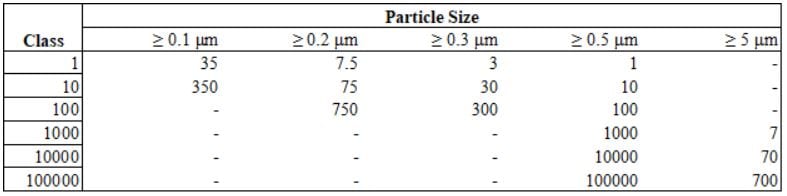
Under Federal Standard 209E, there are 6 classifications for clean rooms which correspond to the airborne particulate densities within the space. These classifications are shown above. The Microfabrication Laboratory is specified to operate as a Class 1000 clean space. To the knowledge of current directorship, Class 1000 performance had not been previously verified.
Standard Operating Procedure
A standard operating procedure was developed to aid in future verification of the laboratory air quality.
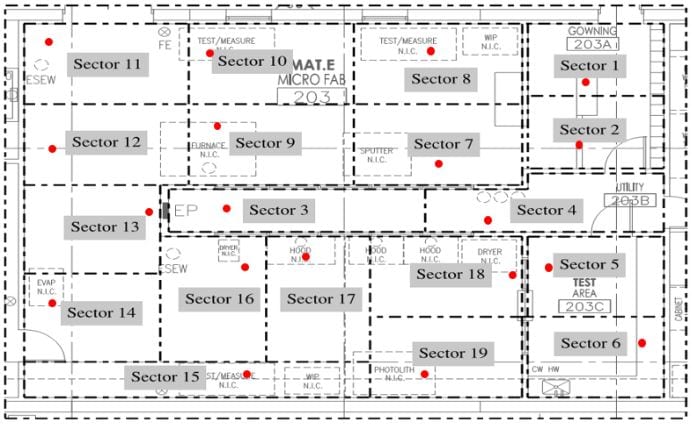
Mechanical System
There are three necessary room condition requirements for manufacturing and testing within the Microfabrication Laboratory: temperature of 68 °F, class 1000 clean air, and positive pressurization relative to adjacent spaces. These requirements are necessary for spaces within the Lab Plenum but not those within the Utility Plenum.
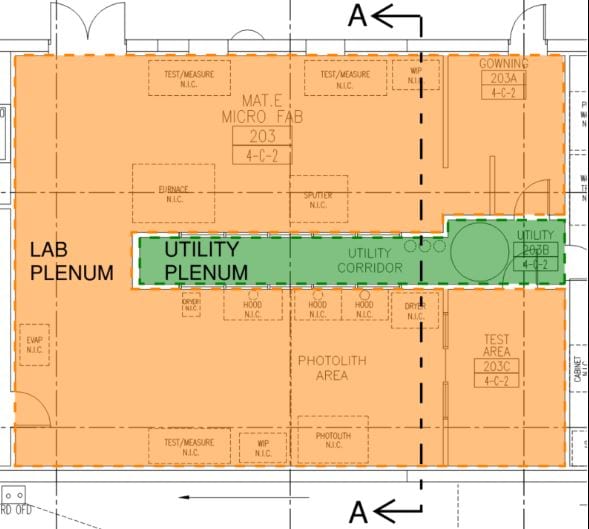
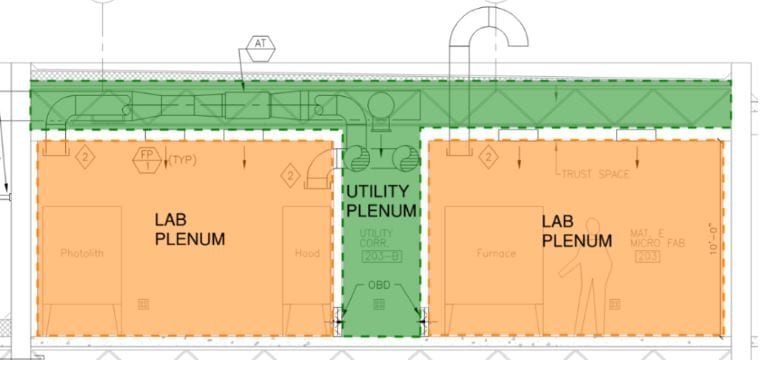
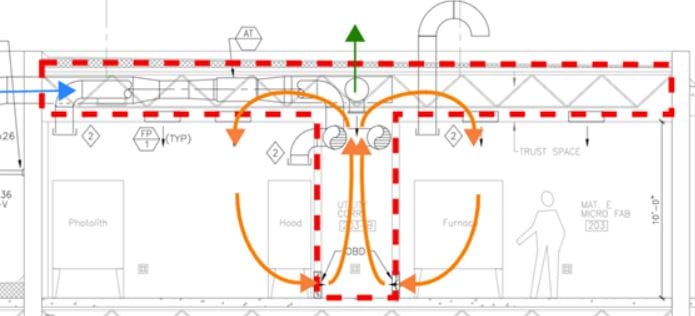
Results
It was observed that particulate densities within the Microfabrication Laboratory were highest during occupied conditions. We also observed that, during occupied conditions, particle densities for larger particles increased.
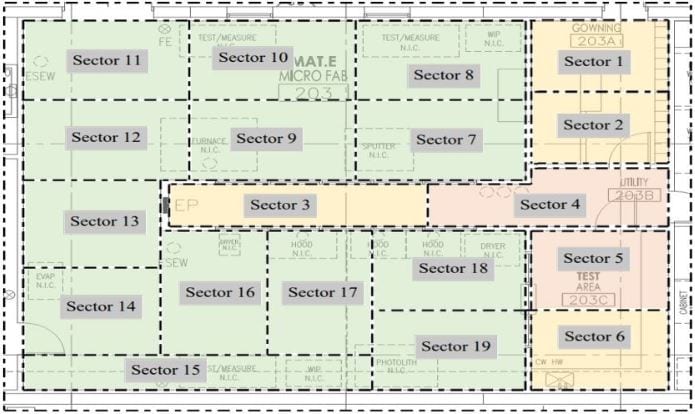
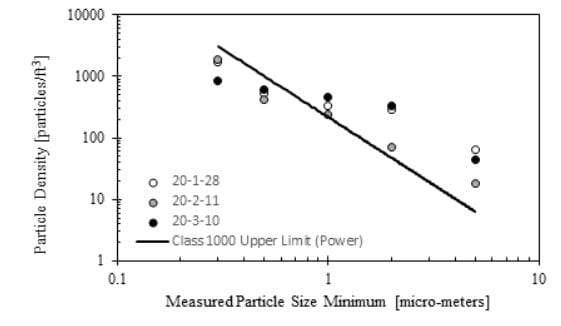