Our Out of this World Team
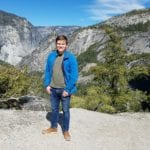
Jack Boulware
Planet Mover
I am a fourth year Mechanical Engineering major with a Philosophy minor graduating Spring Quarter 2020. After graduation, I plan to return home to Seattle, WA. I love literature, hiking, and pursuing new experiences.
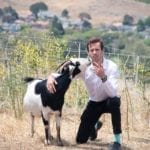
Braden Lockwood
Ball lead
I am a Mechanical Engineering student graduating Spring 2020. I have a passion for environmental sustainability and I’m getting my concentration in Renewable Energy . I have lived in Salt Lake City, Utah, Redmond, Washington, and now San Luis Obispo, California. I love building things and spending time in nature.
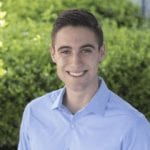
Justin Spitzer
Shaft lead
I am a fourth year mechanical engineering major originally from Orange, CA. I am a Type I Diabetic, one of my major reasons for choosing to do engineering and enjoying lifting weights in my free time. I do not currently have a job lined up after graduation, but hope to work on medical devices or work in biomechanics.
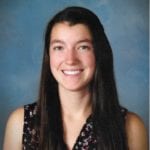
Allison Turnbaugh
Star Lord
I am a fourth year Mechanical Engineering with an Architectural Engineering minor graduating in the Fall of 2020. I am from Fountain Valley, California. After graduation I plan on pursuing a career in the theme park industry.
Acknowledgements
This project was made possible by our sponsor, Dr. Barata of the Cal Poly Music Department and through gracious funding from the Baker-Koob Foundation!
Special thanks to our awesome project advisor Sarah Harding!
project videos
elevator pitch
project overview
Our Project's Digital Poster
Planetary Problem Statement
Cal Poly RSVP needs a way to suspend, store and deploy numerous planetary bodies for a production, directed by Dr. Barata because there is currently no system that can raise and lower the bodies to carry out Dr. Barata’s vision for the play. The mechanism designed must be safe, quiet, reliable and complete by the day of load-in for the theater.
Solar System Constraints
- Must be capable of repeatedly moving up to 20 ‘planet’ props 24 feet vertically.
- Must be installable by two workers in less than a full work day.
- Must safely suspend the props overhead, conforming to a theater factor of safety of 9, and be completely fire retardant.
- If electrically powered, must be operable on command by stage techs. If manually powered, must be operable with a low amount of exertion.
'Wind-Up Rod' Design
Spooling cable around disks of varying size was chosen for the following reasons:
- Allows for either electrical or manual control.
- Reduces system footprint behind the curtain, as disks can be placed relatively close to one another with little adverse effects.
- Allows for flexibility in prop control; props can be lowered in small groups rather than all at once.
- Much less expensive than large-production solutions.
Other design choices to note:
- Inflatable plastic balls used to simulate planets, drastically reducing load on the system.
- Material choice of wood for ‘wind-up rod’ due to low cost and relatively small loads.
- Manual power chosen to reduce cost and avoid stringent regulations pertaining to electrically powered systems.
- Props connected to system via ring/cable net, reducing system visibility while preserving aesthetic effect of moving planets.
- System kept in place with pin fixture, ensuring safe and simple operation.
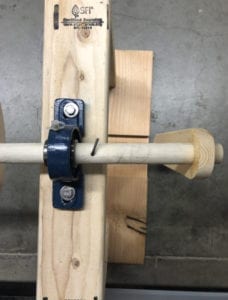
Pin connection to hold planets in place once raised or lowered to the correct height.
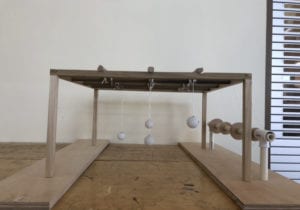
Small scale prototype to verify different diameter discs result in planets dropping at different rates and different heights.
Revolutionary Design Concept
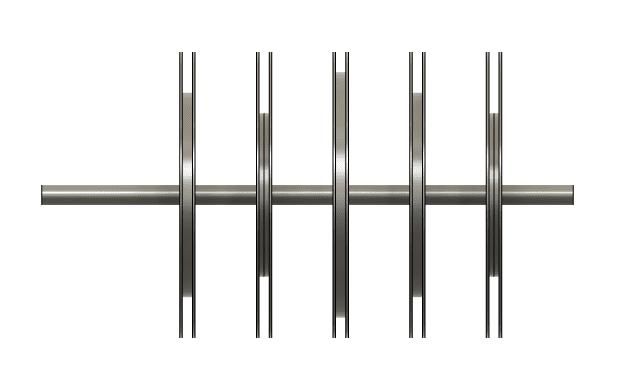
Side view of rod with discs showing the different diameter discs.
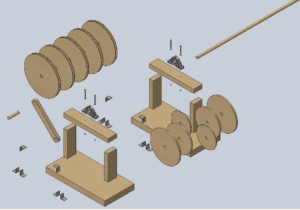
Exploded view to show all components included in the fully assembled wind-up rod.
This CAD model allowed for dimensions of various components to be finalized and aided in determining tolerances necessary for manufacturing and assembly.
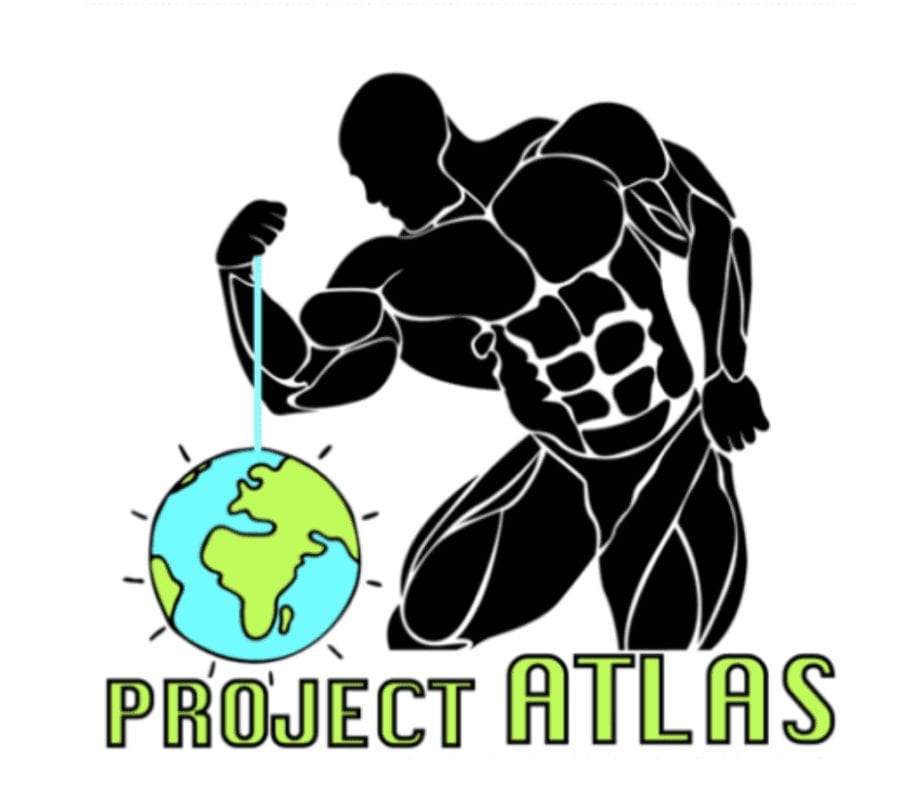
Heavenly Bodies RsVP
This project is sponsored by Dr. Barata from the Cal Poly Music Department and funded by the Baker-Koob Foundation.
Constellation Complications
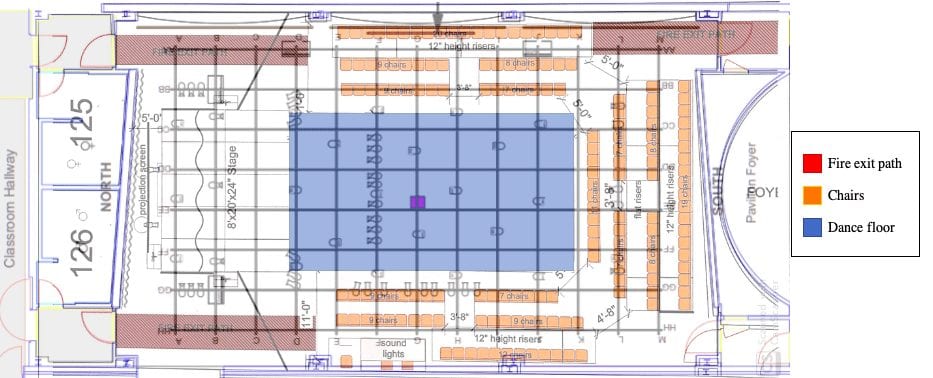
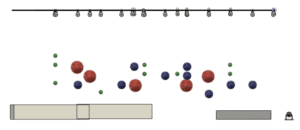
‘Planet’ drop zones needed to be determined in reference to theater support scaffold, as well as stage lights and other props.
Basic Terraforming:
Manufacturing Process and Components
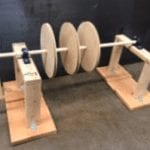
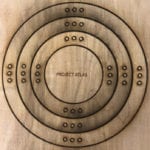
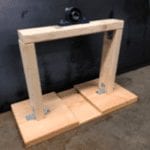
Design Verification
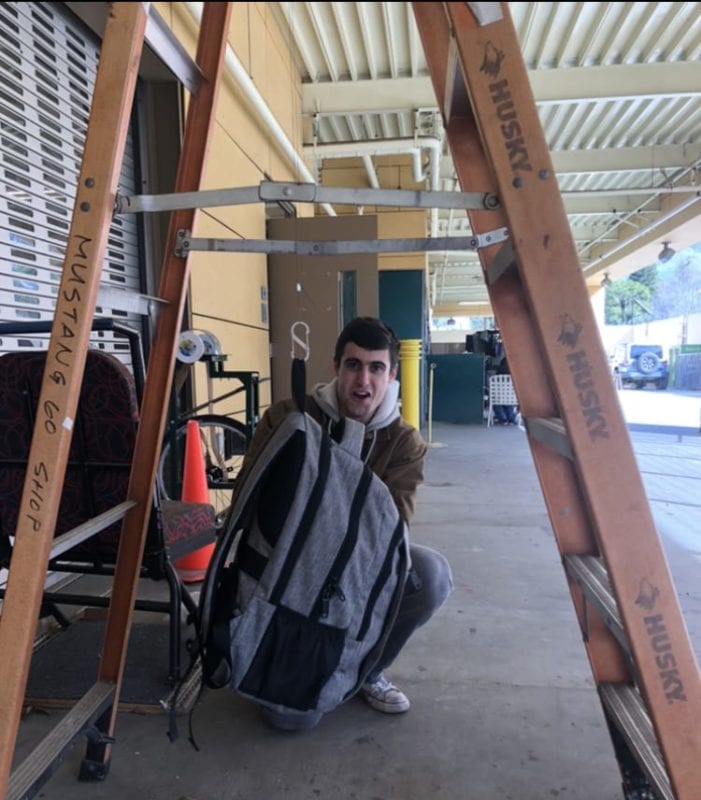
Testing the strength of the cable intended to suspend the planets.
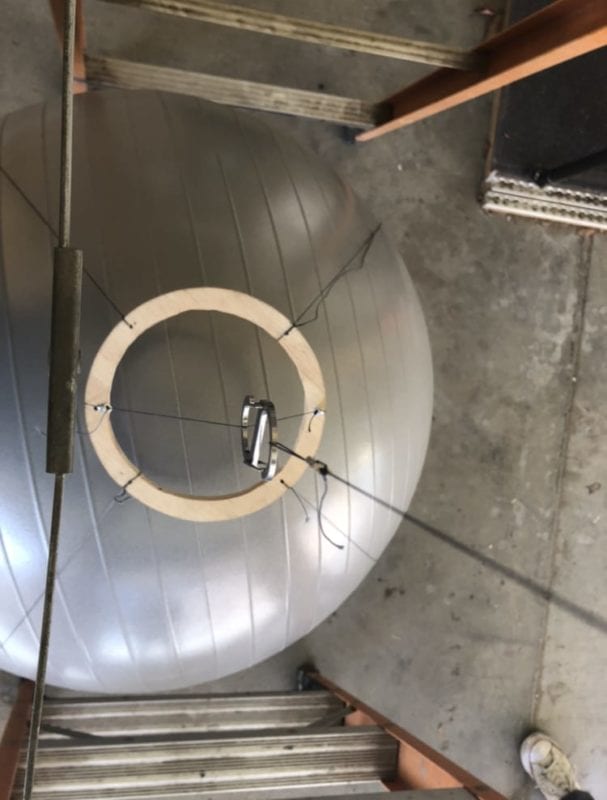
Testing the validity of the ring design to keep the planet in place and withstand the force pulling the planet.
Strength Test – Our design was verified by testing the strength of the cable used – to be allowed to hang overhead, a factor of safety of at least 9 was required. By using the system to hoist increasingly large weights, we were able to determine that the fishing line desired would not be acceptable, as it failed to hoist 50 lbs. After this test, the team switched to 1/16″ aircraft cable, which could easily support the loads required.
Manual Operation Verification – The ability of a theater tech to operate the system without undue stress was verified. In addition, this test verified that the system could move the planet props the full 24 ft within 5 sec, as requested for full effect during the production.
Noise Test – In order for the system to be effective, it must be as quiet as possible to ensure that the audience does not know planets are moving before they should. To ensure this, the team selected higher quality pulleys which would minimize noise overhead. This was ensured through comparing the noise produced by the system (which was simulated in a similar space on campus) to expected ambient noise in the theater. This test ensured that, though the system would produce some noise in operation, it would not distract from the performance, and it would maintain maximum aesthetic effect.
Out of this World Final Design
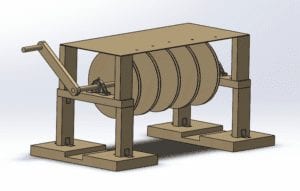
Custom Components
- Wood Ring Connectors
- Crank Handle
Stock Components
- Pillow Block Bearings
- Angle Brackets
- 2×12 Wood Stock
- 2×4 Wood Stock
- 14′ Wood Disks
- 12′ Wood Disks
- 10′ Wood Disks
- 8′ Wood Disks
- 1′ Dowel Rods
- Exercise Balls
COVID-19's Repercussions: The Meteoric Fall
Though the system’s final design was completed early in 2020, the onset of COVID-19 required the team to cease physical work on the project in early March. Shortly thereafter, the theater production for which the system was designed was cancelled. Though this meant the full system would not be manufactured, the team quickly pivoted to accomodate these setbacks. Rather than build the system as intended, the team created an online ‘Instructable’ which can guide readers to build their own copy of the final design, at no cost.
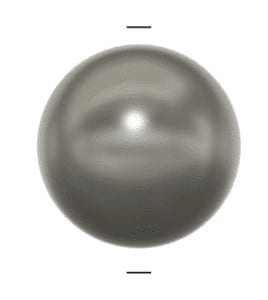
Model of exercise ball and both ring bases.
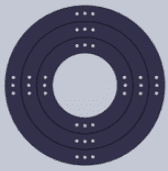
Top ring base design. Three concentric rings associated with the three planet sizes.
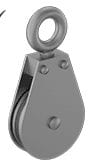
3/16″ Grooved pulley with swivel eye.
Recommendations
Improvements to be made if the system were to be re-designed for future performances:
- Incorporate electrical motors in order to operate the system more smoothly.
- Design a braking/fixing system that is easier to operate by theater techs.
- Increase the thickness of inner disks, giving the cable more room to spool up, while reducing cable rubbing against outer disks.
- Use disk flanges to attach disks to the spinning rod more securely.
- Design a less noticeable connection between ‘planet’ props and the suspension system.
Instructables
instructables username - rsvpheavenlyengineers
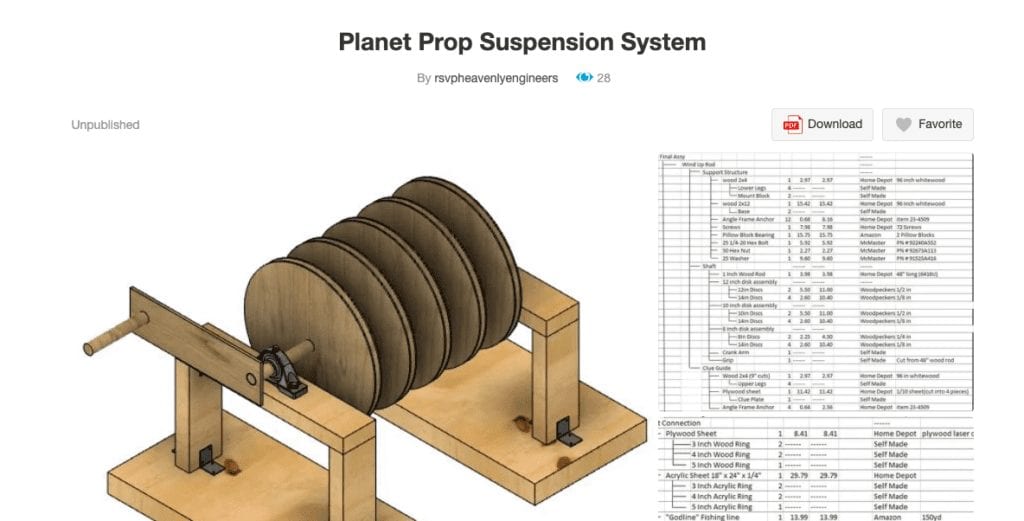