Our Team
Our team consists of three senior Cal Poly Engineering majors responsible for the research, design, and prototyping of the adjustable bite block
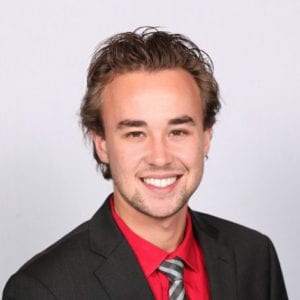
Jonah Holbrook
Biomedical Engineering
Jonah was responsible for the initial design and prototype generation of the Bite Block as well as being the primary point of contact for the project. Coming from Salt Lake City, UT, Jonah was drawn to the beautiful west coast and Cal Poly’s rigorous curricula in engineering and the sciences. During his time at Cal Poly, Jonah has had the true pleasure of serving as the president of Cal Poly’s Medical Design Club while also performing research in the Martinez biology lab developing 3D printed point-of-care medical diagnostics. When he’s not in the lab, Jonah can be found exploring new trails in the area or road tripping to a new national park. Jonah is applying to medical school during the 2020 application cycle and will be completing a gap year medical fellowship at South Bay Vascular Center in San Jose, CA.
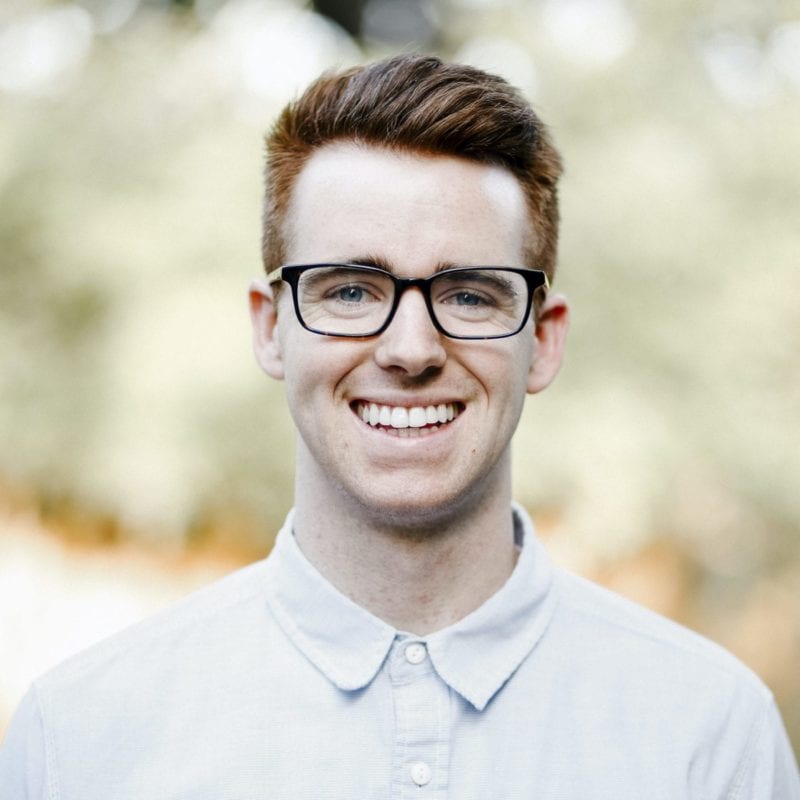
Everett Johnson
Mechanical Engineering
Everett was responsible for utilizing CAD software to design the bite block assembly, conducting finite element analysis on critical design features, and developing engineering drawings for the bite block components. Originally from Orange County, CA, Everett grew up with a passion for product design. As a high school senior, he was attracted to Cal Poly for its reputable engineering program, learn-by-doing philosophy, and outdoor landscape. Since attending Cal Poly, Everett is especially thankful for the Mechanical Engineering program’s blend of technical education and hands-on project opportunities and is looking forward to pursuing a career as a product design engineer.
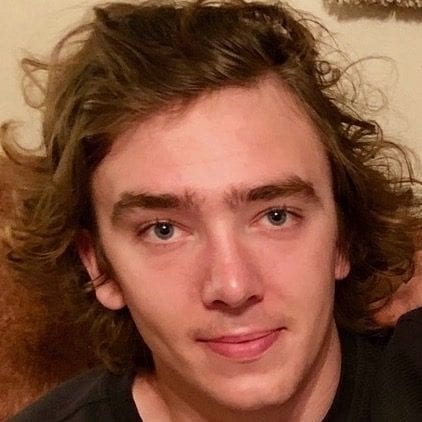
Connor Merrick
General Engineering
Connor was responsible for the manufacturing, planning and sourcing for the bite block. He is majoring in general engineering and minoring in biology. Originally residing in Saugus, CA, Connor was drawn to Cal Poly by its well-regarded engineering program and SLO’s beautiful scenery. Connor enjoys spending time outdoors in and around SLO. After graduating, Connor would like to find a job in the automotive industry.
Adjustable Bite Block Digital Poster
Background
When visiting a dentist for an oral procedure, patients are often required to maintain their mouth at an open angle for the entire duration of the procedure. The most common method used to maintain an open mouth is the implementation of a dental bite block: a simple yet effective device placed between the patient’s upper and lower teeth. The key to a successful bite block lies in the balance between comfortably supporting the patient’s jaw while allowing maximum access and range of motion for the dentist. Many bite blocks currently exist on the market. However, each current design contains one or more key limitations in need of improvement. The comfort of patients prevails above all else, and the limited sizing options offered by current bite blocks fail to provide optimal patient comfort. Thus, the goal of this project was to develop a fully adjustable bite block that enables maximum comfort for patients and ease of use for dental staff.
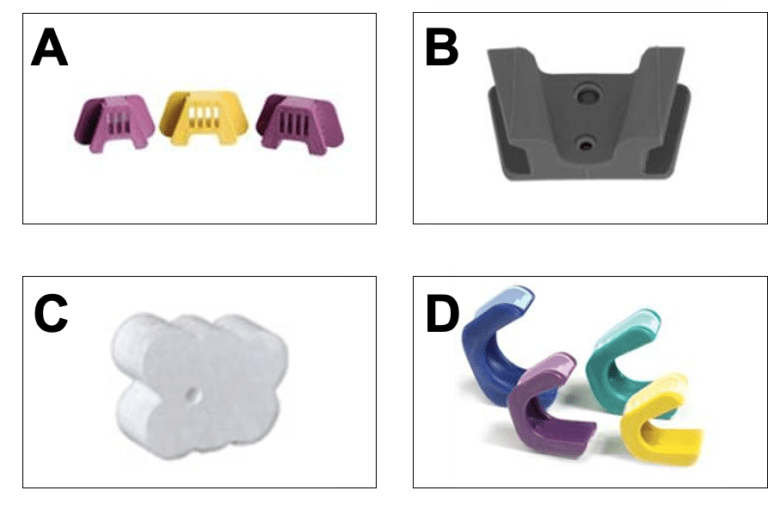
Figure 1: Current Top-Selling Bite Block Products. A) Ultradent PropGard. Does not allow access for dental instruments. B) Hu-Friedy Markel Mouth Prop. Offers only a single size. C) Denstsply E-Z Mouth Prop. Is not autoclave sterilizable. D) Common Sense LogiBloc. Offers limited sizes and is expensive.
Key Design Requirements
- Allows for a range of adjustability
- Comfortable for all patients
- Safe for all patients
- Easy access for dental instruments
- Easy and intuitive to assemble, disassemble, and use
- Reusable for at least 100 cycles
- Cost kept to a minimum
Corresponding Design Features
- Offers 5 sizes that can easily be toggled between
- Contains soft Santoprene padding and maintains an open mouth angle of 16˚
- Contains no sharp edges and can withstand up to a 75 lbf bite force
- Maintains a cut-out U shape to offer maximum working space
- Consists of only two parts that interact via a snap-to-fit mechanism
- Composed of durable and autoclave -safe glass reinforced polypropylene
- Injection moldable for as little as $6.90 per unit
Final Design Concept
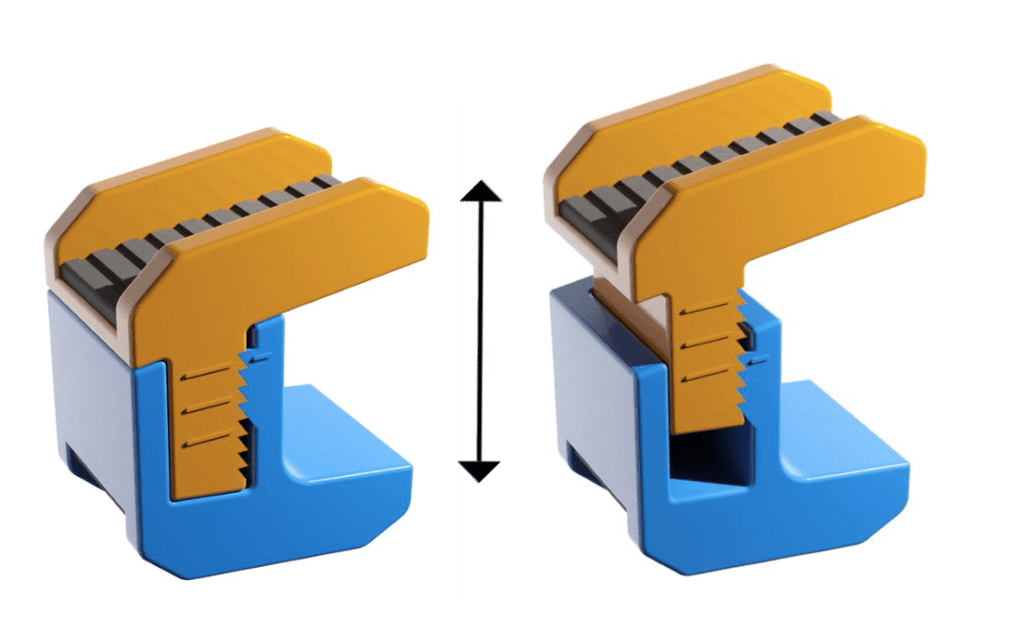
Figure 2: Final Adjustable Bite Block Concept. The final design for the adjustable bite block consists of two independent parts with interlocking teeth that are loaded from the side.
Design Overview
The final bite block design consists of two adjustable components with interlocking teeth. The design is easy to use and use would entail the following steps:
- Connection of the two bite block components from the side, ensuring that the components have a tight fit.
- If the patient’s mouth requires a larger size, dental professionals can simply remove the bite block and use the injection molded hash marks to increase the size to the desired size for the patients mouth.
- Dental professionals can take note of the patient’s unique bite block size and include that number in their chart for future visits.
- After the procedure, disconnect by simply sliding apart the two components until they are completely separated.
- Sterilize via ultrasonic bath and autoclave.
Finite Element Analyses
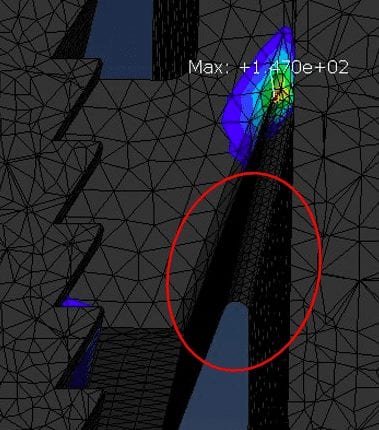
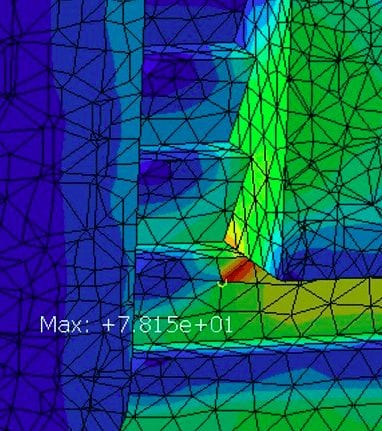
Figure 3: Bite Block Finite Element Analyses. Top) Finite Element analysis on adjustability tab of initial design. FEA shows a stress of 147 MPa on the living hinge compared to the flexural strength of 135 MPa of glass filled polypropylene. Thus, the mechanism design was reconsidered. Bottom) Finite element analysis on the teeth of the finalized design. FEA shows a stress of 78 MPa compared to the flexural strength of 135 MPa of glass filled polypropylene yielding a factor of safety of 1.7.
Materials Selection and Manufacturing
The bite block must be composed of a material that is rigid yet flexible, safe for use in the human body, and able to withstand the environment of the autoclave. Thus, the following materials were selected for the final design:
Main Body:
- 40% glass reinforced polypropylene
- FDA approved material for medical and dental use
- Glass reinforcement increases strength and stiffness during use
Tooth Contact Pads:
- Santoprene (Vulcanized alloy of polypropylene and EPDM rubber)
- Chemically bonds with polypropylene body eliminating need for adhesive
- Offers physical properties of polypropylene with softness of rubber
Both bite block components can be injection molded with Santoprene overmolding in a single step for an average cost of $6.90 per unit.
Testing Outline
The following tests are required to verify the safety of the final injection molded bite block product before it reaches the market.
- In-Office Testing: Dr. Ng and his associates will test the ease-of-use of the finalized bite block and will also test the comfort of the design. This test is qualitative, but after the approval from Dr. Ng, the following tests will be performed.
- Compressive testing: Using an Instron materials testing machine, the bite block will be compressed with a force of 75 lbf (334 MPa) for 200 cycles to ensure it can withstand a lifetime of maximum bite force.
- Autoclave Testing: Between every two compressive tests, a cycle of autoclave sterilization will be performed to ensure the product can withstand the autoclave environment for 100 cycles.
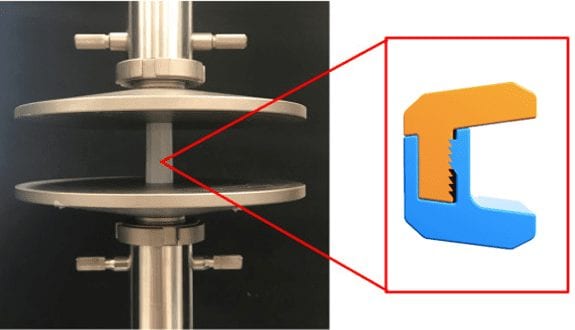
Future Steps
After selecting the injection molding manufacturer and receiving the first order of adjustable bite blocks, the tests listed above must be performed. These tests may be performed by dental personnel in San Luis Obispo in collaboration with a club or organization at Cal Poly with access to the proper testing instruments. Upon successful completion of the tests, Dr. Ng and collaborators will begin seeking partnership with a Dental supply company to begin marketing and distribution.