Our Team
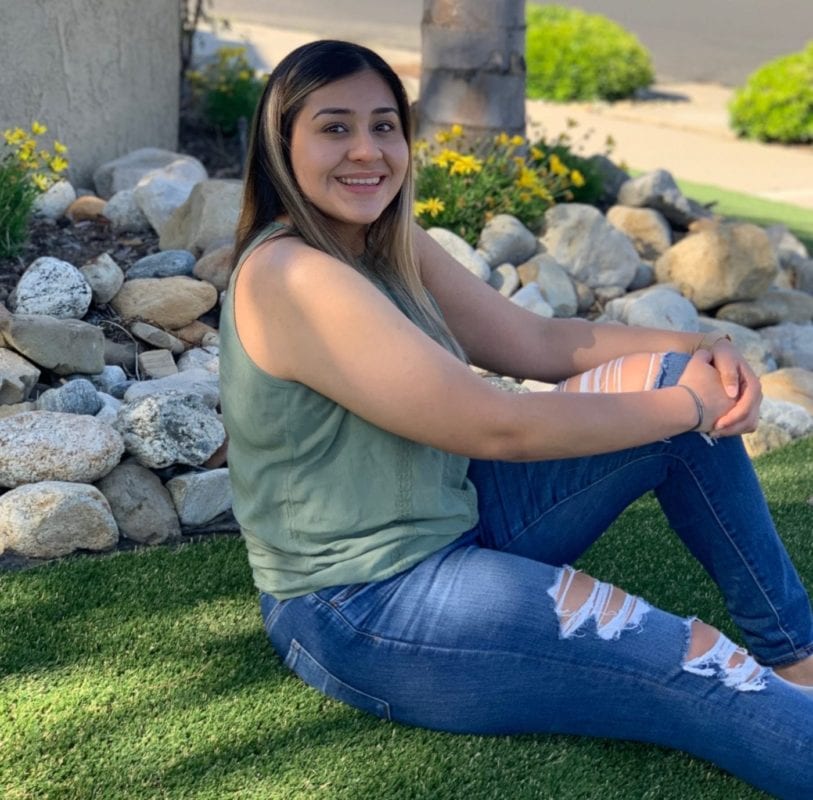
Kassandra Vega
Project Manager and Team Lead
My name is Kassandra but I go by Kassy. I am a fourth year Mechanical Engineering student concentrating in HVAC&R. I am from Oxnard, California. After graduation, I will be working as a Mechanical Design Engineer for Southland Industries in Garden Grove, California. I interned with Southland Industries based on a recommendation from a friend. I really enjoyed the experience and have continued to stay interested in this field.
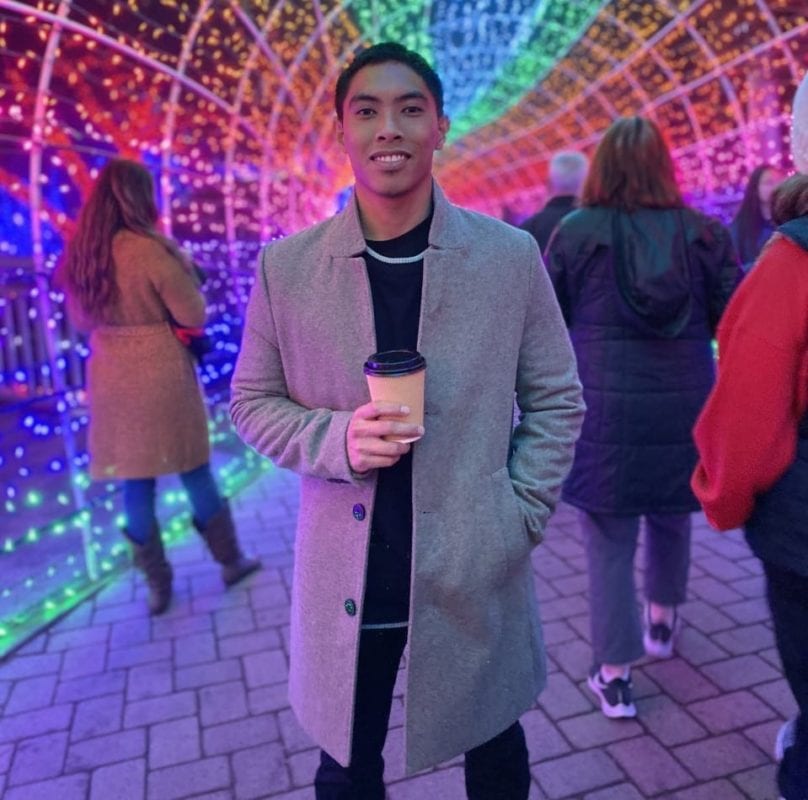
ANTHONY PAMINTUAN
CFD and Psychrometrics Lead
My name is Anthony and I’m from Los Angeles, California. I studied Mechanical Engineering with a concentration in HVAC&R for my undergrad but I am pursuing a career in Fire Protection Engineering (FPE). I have been continuing my internship remotely for Jensen Hughes and will work full time after graduation while pursuing my Master’s in FPE.
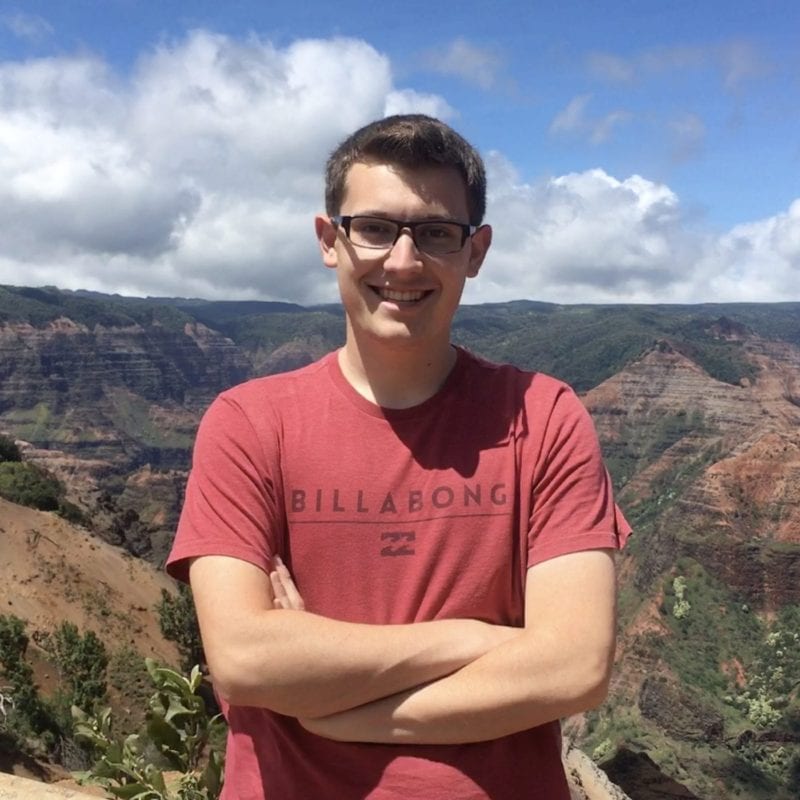
Caleb Granch
System Research and Outreach Lead
My name is Caleb and I’m a fourth year Mechanical Engineering student concentrating in HVAC&R. I’m from Orange County and will be moving to San Jose after graduation to work for Critchfield Mechanical as a project engineer. I interned with ACCO Engineered Systems after my sophomore year based on a recommendation from a friend. Although I had yet to take any thermodynamics courses, I enjoyed the experience and have continued to stay interested in the field.
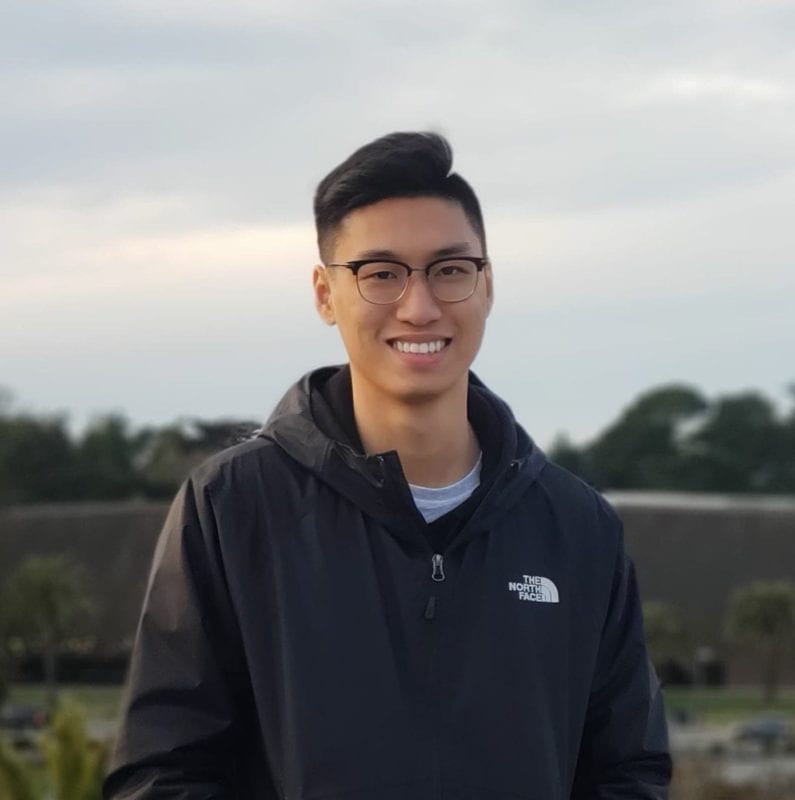
Zifeng zeng
Load Calculation and Outreach Lead
My name is Zi and I am a fourth year Mechanical Engineering student concentrating in HVAC&R. I am from Los Angeles and will be moving to the Bay Area after graduation to work as a design engineer for ACCO Engineered Systems in San Jose. I first grew interest in the HVAC&R concentration when I took my Thermodynamics 1 course with Dr. Locascio. Although he was tough on his students, I didn’t back down from it and ended up really liking Thermodynamics. Since then, my interest in HVAC&R has grown.
Throughout the process of collecting data/information, performing an analysis, and writing the report, several individuals were contacted for support and assistance. We would like to acknowledge the following people for their support and assistance: Dr. Jennifer Mott for guiding the team through the project, Kevin Reeder from AHI for providing the team with site visits and walkthroughs of the hydroponics greenhouse, Wendy Robinson for giving the team a tour of the Cal Poly greenhouses and basic greenhouse information, ASHRAE for creating standards for the health and safety of the occupants, Cal Poly for giving the team a place to work and access to Trace and SolidWorks, MicroCool for a quote regarding a fogging system, Micro Grow for a controls system quote for the fogging system, and finally Greenhouse Megastore for quotes on a shade cloth and a wet wall system.
Our Project Videos
Our Project's Digital Poster
AHI has partnered with the Cal Poly Mechanical Engineering Heating, Ventilating, Air-Conditioning, and Refrigeration (HVAC&R) program seeking help to design a ventilation system for their hydroponics greenhouse that overheats in the summer damaging the plants and creating uncomfortable working conditions.
Current Conditions:
- Greenhouse reaches temperatures up to 120 ºF.
Design Conditions:
- Temperature Range: 65-80 ºF
- Humidity range: 50-60% Relative Humidity.
- These ranges allows for different types of herbs to be grown in the greenhouse.
The hydroponics greenhouse has dimensions of 30’x120’x15′ and has an existing mechanical ventilation system in place:
- 3 controllable louvers
- 2 fans that exhaust 36,000 cubic feet per minute (cfm) combined
There are twenty-four 1000 Watt high pressure sodium growing lights that are evenly distributed.
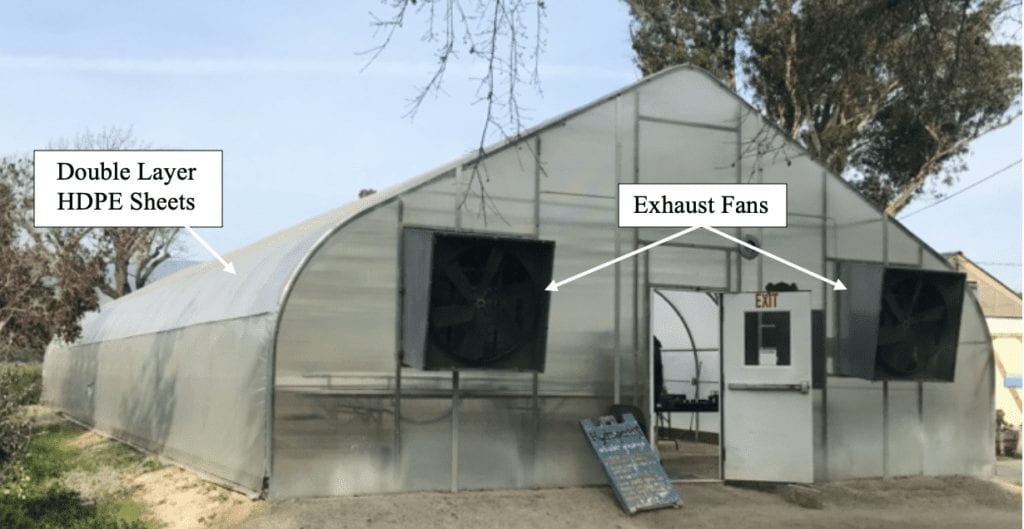
Exterior of the hydroponics greenhouse showing the two exhaust fans.
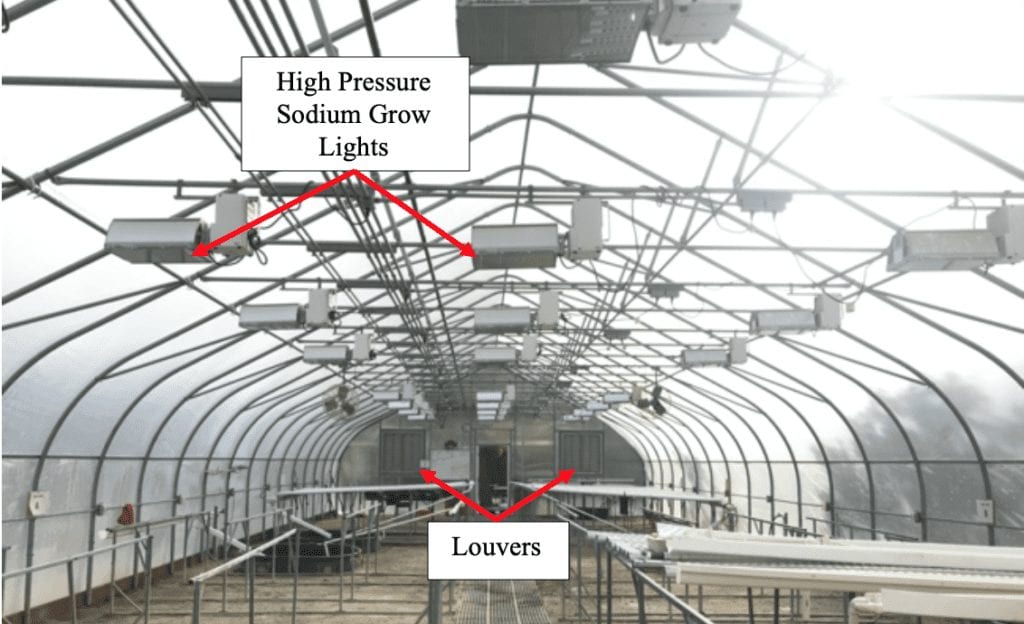
Interior of hydroponics greenhouse showing louvers and growing lights.
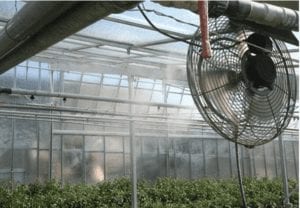
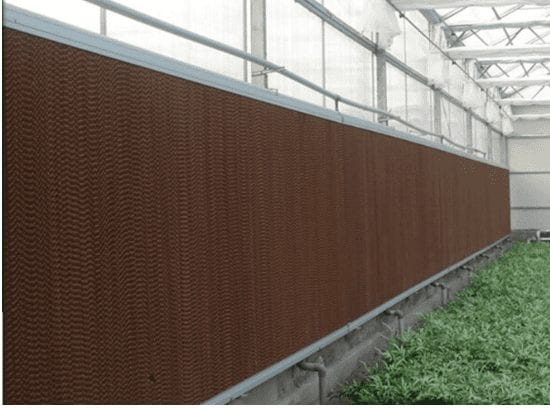
The cooling method was narrowed down to two evaporative cooling methods since evaporative cooling is cost effective and ideal in most greenhouse conditions. Evaporative cooling is a method of cooling a space that reduces the air temperature by injecting water into an airstream. The two evaporative cooling methods are:
Wet Wall:
- Consists of a fan and cellulose pad on the opposite end which has water going through it
- Pros
- Effective cooling
- Cons
- High fan power
- Imbalance of temperature zones
Fogging System:
- Sprays small droplets of water through the opening of the louvers
- Pros
- Desirable for plant conditions
- Evenly distributed temperatures
- Cons
- Requires extra pump, piping, and water supply installation
The hydroponics greenhouse was modeled in SolidWorks to run the CFD simulations and produce results.
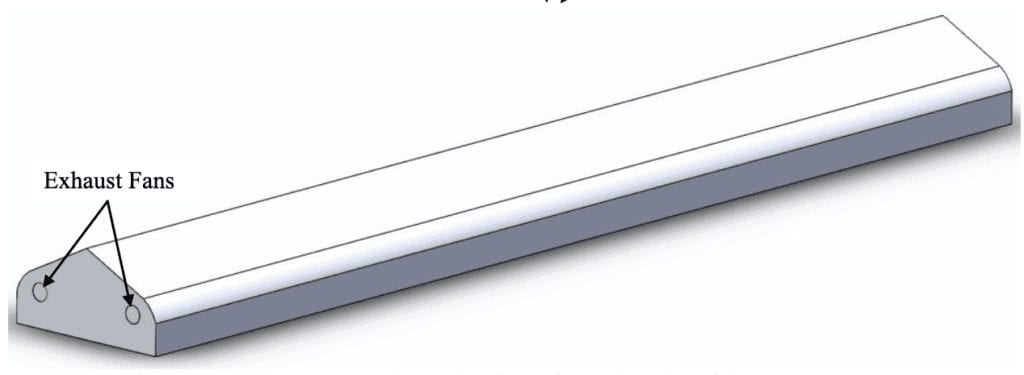
Exterior of the greenhouse model showing the exhaust fans.
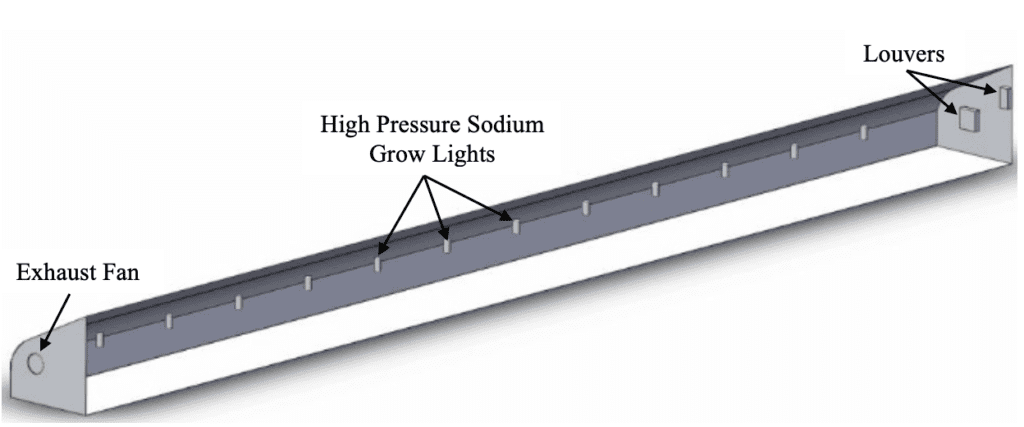
Cross sectional view of the greenhouse model showing the exhaust fans, growing lights, and louvers.
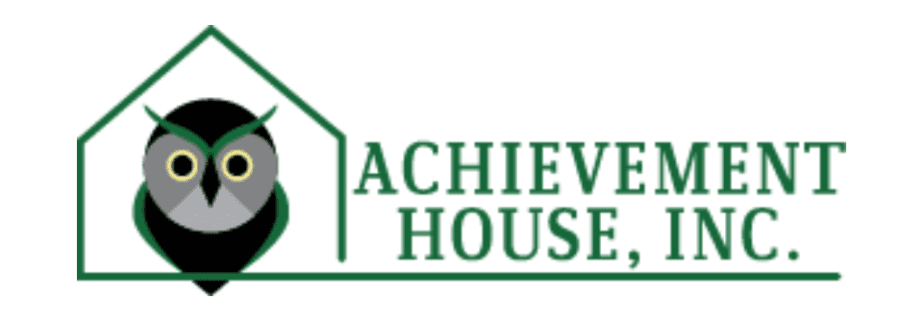
This project is sponsored by Achievement House Inc. (AHI). AHI is a private, non-profit organization created for the purpose of helping adults in rehabilitation and community living services.
Computational Fluid Dynamics (CFD):
A SolidWorks CFD transient analysis investigates the evaporative cooling effects for extreme hot weather conditions and common weather conditions. The analysis allowed us to determine the number of supply air louvers requiring evaporative cooling for each weather scenario.
The ideal configuration to meet required grow conditions and a comfortable work environment for occupants utilized:
- 2 louvers supplying conditioned air
- 1 louver supplying unconditioned outside air
This configuration minimizes high relative humidity alleviating potential algae growth while maintaining an acceptable temperature range for plants and people.
These temperature and relative humidity gradients were produced from the simulation for a peak summer day in San Luis Obispo, California. This ensured this configuration would work under peak temperature conditions.
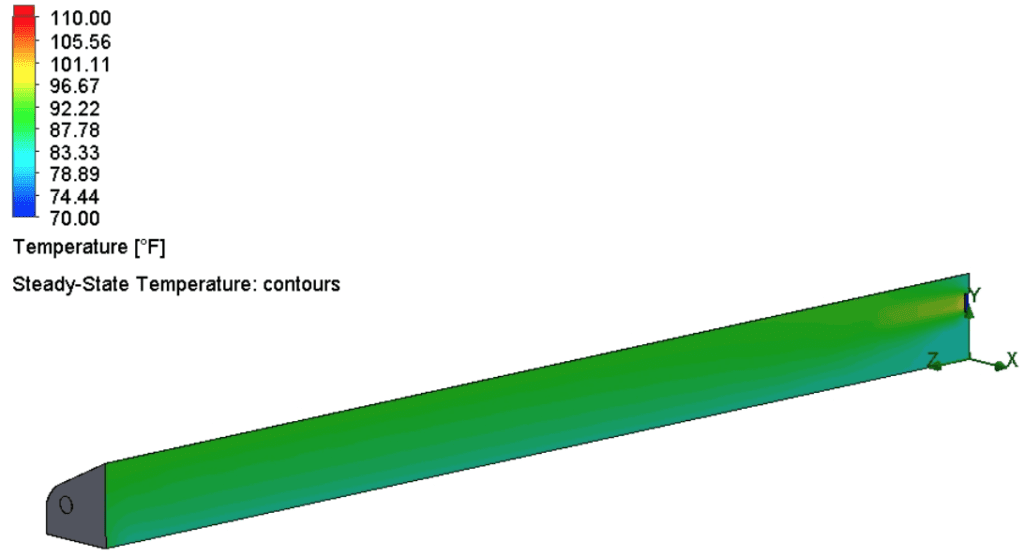
Steady-state temperature gradient with wet-wall evaporative cooling.
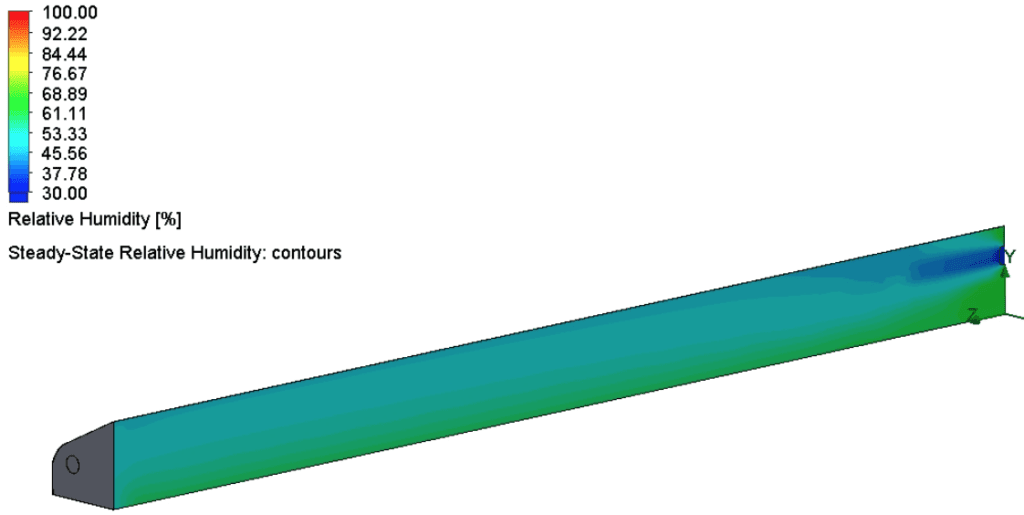
Steady-state relative humidity gradient with wet-wall evaporative cooling.
The Center for the Built Environment (CBE) at UC Berkley created a thermal comfort tool which was used to analyze the results and determine if they satisfy ASHRAE’s predicted thermal comfort.
The comfort range is determined based on the following properties:
- Dry-bulb temperature,
- Relative humidity,
- Air speed,
- Activity level, and
- Clothing level.
The red dot in the picture lies within the blue shaded area verifying the results are ASHRAE compliant.
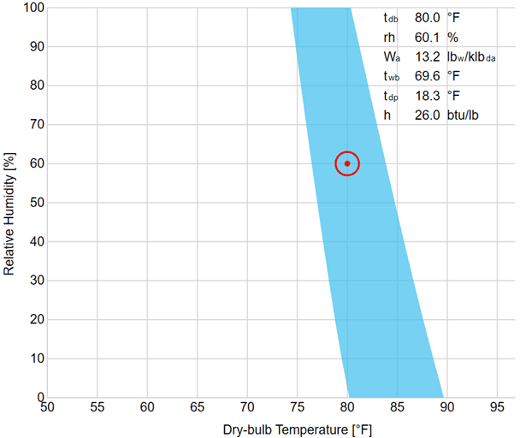
Thermal comfort analysis performed using the CBE Tool for a peak summer day in San Luis Obispo.
A psychrometric analysis was performed which calculated the expected evaporative cooling temperature and humidity (state 2) based on the entering temperature and humidity (state 1) at a conservative 80% heat exchanger efficiency. The wet wall was modeled as a heat exchanger to perform these calculations.
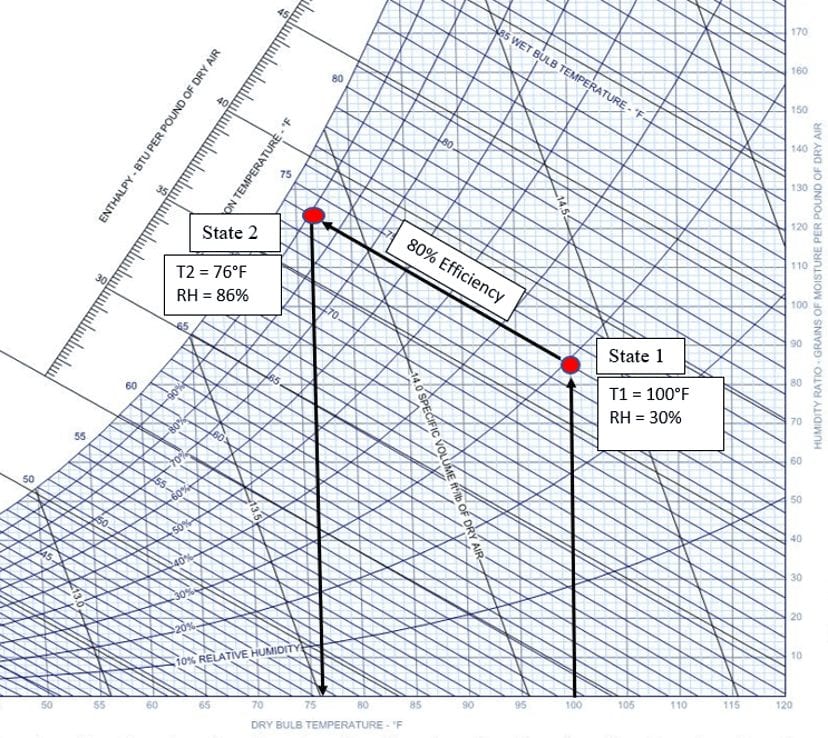
Psychrometric analysis to determine the state 2 properties based on state 1 properties and an 80% efficiency.
Quotes were acquired for both active evaporative cooling solutions. Greenhouse Megastore quoted the wet wall, MicroCool quoted the fogging system, and Micro Grow quoted the controls system.
Wet Wall
- Wet Wall
- $3,570 after tax/shipping
- Controls
- $1,400 after tax
- Contractors
- $4,000-$7,000
- Significant demolition, building, and framework required.
- Total
- $9,000-$12,000
Fogging
- Fogging System
- $6,300 after tax/shipping
- Controls
- $1,400 after tax
- Contractors
- $300-$1,300
- Electrician required to wire pump
- Plumber may be required to connect pump to reverse osmosis system.
- Total
- $8,000-$9,000
The final design recommended to AHI is the MicroCool fogging system in conjunction with the MicroGrow controls system. The fogging system is more efficient than the wet wall and will also create more equal temperature gradients. It is easier to install and less expensive than the wet wall.
What it comes with:
- Fogging System
- Complete kit with all necessary components and instructions
- Controls System
- Controller
- Temperature sensor
- Humidity sensor
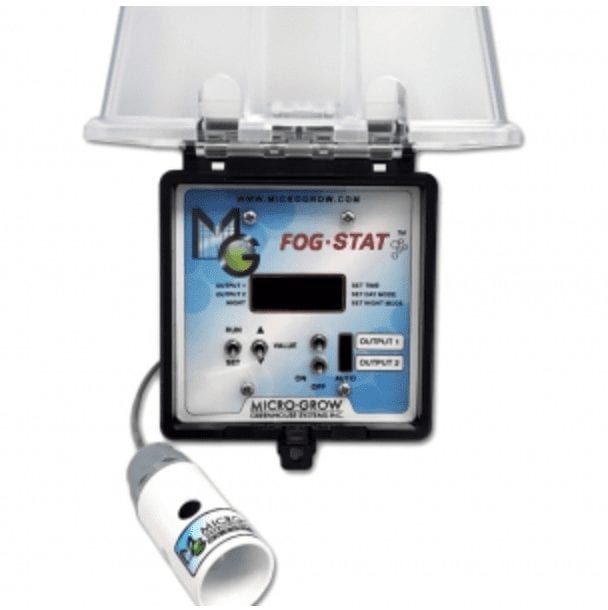
MicroGrow’s FogStat controls system specially designed for greenhouse fogging systems.
While exploring other cooling options at AHI, it is recommended to use a shade cloth as a temporary solution. A shade cloth can also be combined with the chosen cooling system to ensure correct temperature and humidity ranges especially on the hottest days.
Recommended Shade Cloth:
- 120′ x 40′ with 50% shading
- Priced at $2,000 as quoted from Greenhouse Megastore.
Shade cloths are the simplest and least expensive way to cool greenhouses. On an average day in the San Luis Obispo county, the shade cloth can provide almost 100,000 BTU/hour of cooling. The shade cloth combined with the existing cooling fans at AHI can produce around 236,000 BTU/hour of cooling; but it is still not enough to cool greenhouse to design conditions on the hottest day of the year.
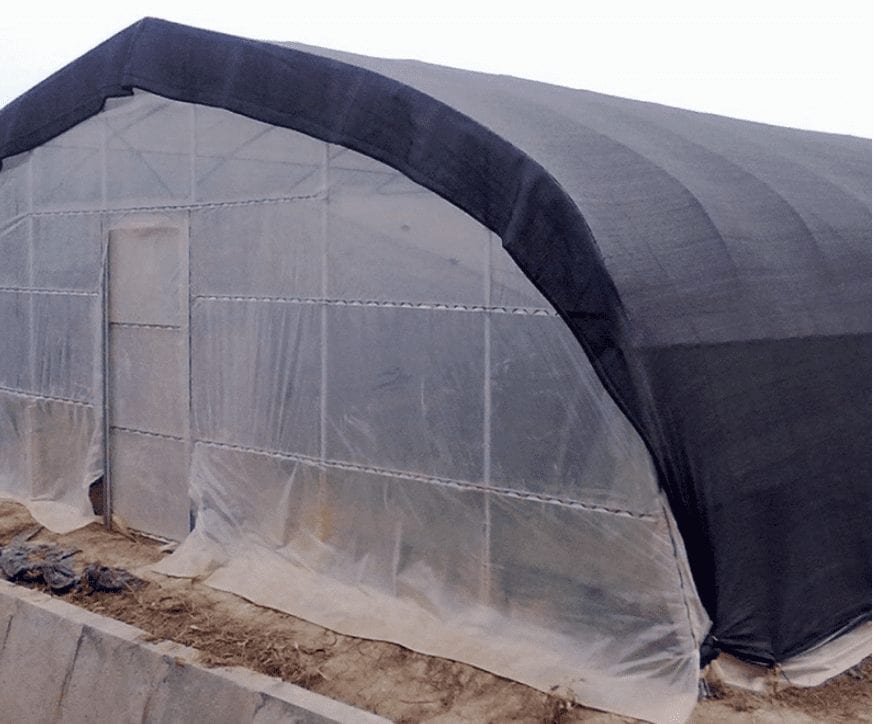
Shade cloth draped over the exterior of a greenhouse.