Our Team
Our team consists of three senior Cal Poly Mechanical Engineering majors responsible for MUVI Phase III’s three main subassemblies.
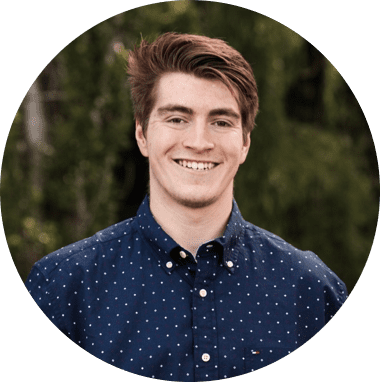
BRAD ALBRIGHT
INSTRUMENTATION FRAME LEAD DESIGNER
Brad was responsible for designing the instrumentation frame and integrating CAD models for the entire MUVI satellite. From Bothell, WA, Brad came to Cal Poly with an interest in Earth climate observation. During his time in SLO, Brad had the pleasure of serving as Braking Design Lead and Head of Operations for Cal Poly Hyperloop, a finalist at the 2019 SpaceX Hyperloop Pod Competition. Brad has enjoyed playing intramural soccer, surviving close encounters with sharks while surfing at Pismo Beach, and countless hours running the trails of Poly Canyon.
Brad has accepted a position for Maxar Technologies where he will help with NASA’s Artemis missions as a manufacturing and production engineer in Palo Alto, CA.
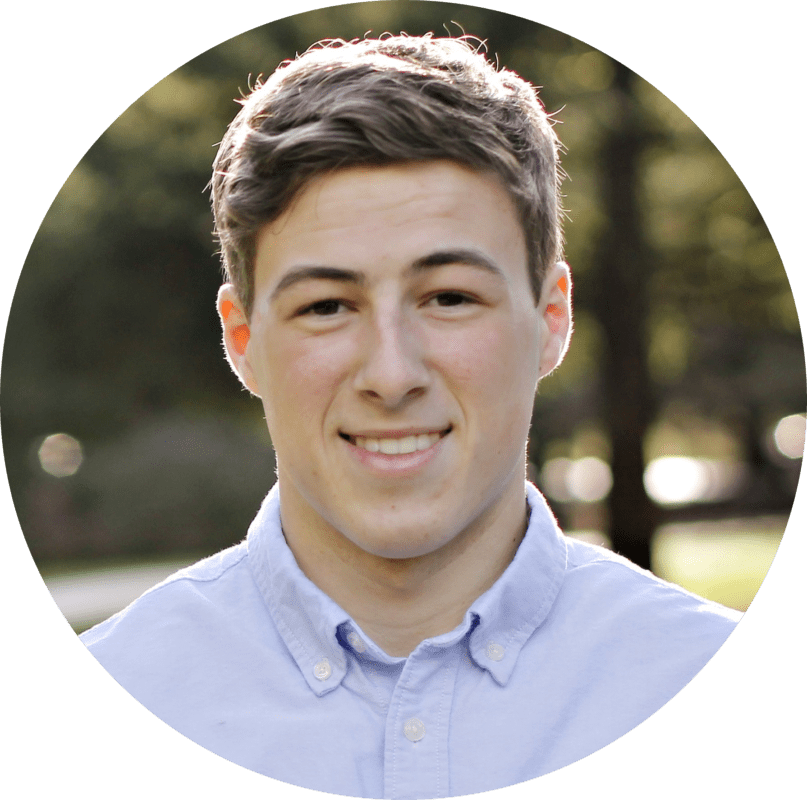
colin harrop
orbital deployment simulator lead designer
Colin was responsible for designing the On-Ground Orbital Deployment Simulator (OGODS), maintaining the project’s bill of materials and was lead on the frame’s engineering drawings. Born and raised in Seattle, WA, Colin was attracted to Cal Poly for its strong engineering program and beautiful outdoor opportunities. During his time at Cal Poly, Colin served as an officer on the Cal Poly Cycling Team, traveled all over California competing in collegiate races, and even built his own bike.
Through this project, Colin has earned a summer position as a graduate researcher for UC Berkeley’s Space Sciences Laboratory. Colin also plans on returning to Cal Poly in Fall 2020 to complete his master’s degree in mechanical engineering.
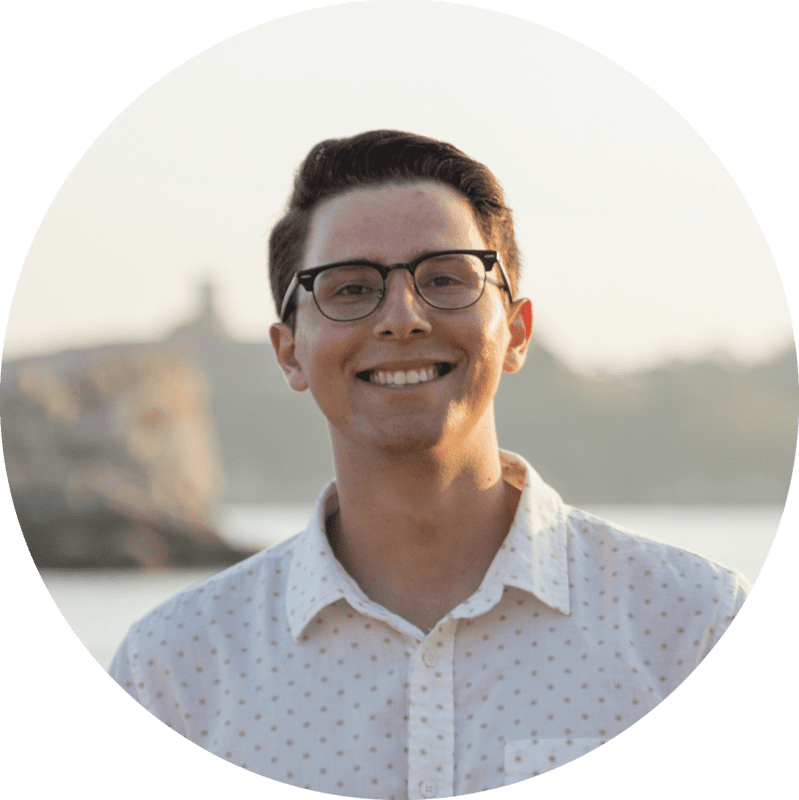
NICO armenta
optical sensor mounting flexure lead designer
Nico was responsible for designing the optical sensor mounting flexure and experimenting with different structural materials for the satellite. Coming up from San Diego, CA, Nico was convinced to attend Cal Poly by Mechanical Engineering Professor and family friend, Dr. Andrew Davol. Nico has enjoyed several seasons of intramural sports, spent significant time and effort in his studies of nuclear power, and is hands down the best chef on the team.
Nico was accepted into a Naval Nuclear Officer program early in his undergraduate career and will be heading to Newport, Rhode Island in July 2020 to complete Officer Training and Nuclear Power School.
Acknowledgements
We would like to express our appreciation to our advisor, Cal Poly Professor Dr. Eltahry Elghandour, and main sponsor from UCB SSL, Kodi Rider. Dr. Elghandour pushed us to complete tasks well beyond the minimum requirements and helped us to do so efficiently and on time. Mr. Rider invited us to Berkeley for several design reviews and shared his knowledge from experiences as an engineer for Lockheed Martin and UCB SSL.
We would also like to thank Dr. Thomas Immel and Jason Grillo of UCB SSL for their insight and support throughout the design process.
Finally, we are grateful for all the skills that Cal Poly’s Department of Mechanical Engineering has provided these past four years. We are sad to be saying goodbye to San Luis Obispo, but eager to share our newly derived engineering expertise in the professional world.
This work was supported by the NASA Science Mission Directorate, Heliophysics Division through contract 80NSSC19K0494
Our Project Videos
MUVI Digital Poster
Background
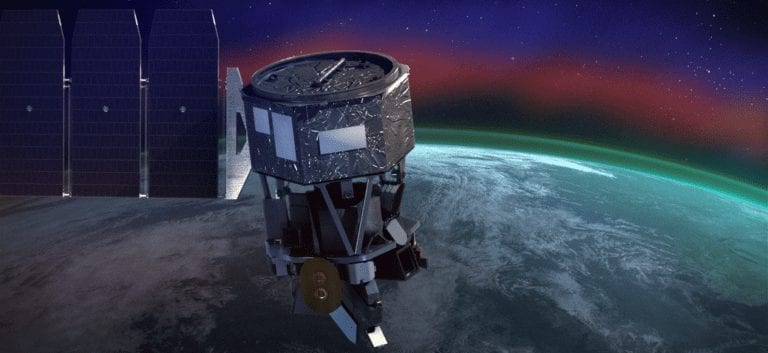
Interactions between Earth and space weather in the uppermost layer of the Earth’s atmosphere, the Ionosphere, are of interest to planetary scientists. Currently, the NASA satellite ICON is equipped with a UV imager to capture images of these interactions. It would be beneficial, however, if scientists could receive images from different vantage points and at shorter increments of time. MUVI, Miniaturized UV Imager, is a single-function, CubeSat intended to provide that benefit. Relative simplicity of design should make replication of MUVI practical and could thus allow for a multi-satellite mission.
Problem Statement
UC Berkeley SSL needs a structure on which to integrate the existing assemblies and features of a miniature satellite. The structure must adhere to the standards of a 2U CubeSat, and it must facilitate accurate alignment of the instrumentation. After manufacturing and assembly, the instruments and structure must undergo vibration testing to qualify for NASA TRL6
Design Constraints
- Nominal volume: 10 x 10 x 22.7 cm dimensions
- Max Mass: 2.66 kg
- Center of mass must be along longitudinal planes
- Adhere to NASA GEVS outgassing requirements and design validation (test) procedures
- Must accommodate existing assemblies with little to no alterations to fully fabricated components
Existing Assemblies
Lens Assembly
PHOTEK
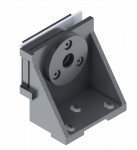
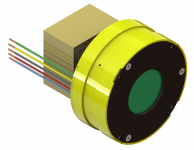
- Focuses UV light from mirrors to Photek
- Mounts atop datum plate, fastened from bottom
- No changes needed
- Image intensifier and optical sensor (camera) of satellite
- Requires mounting apparatus to dampen loads from launch (mounting flexure)
door & mirror assembly
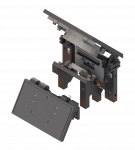
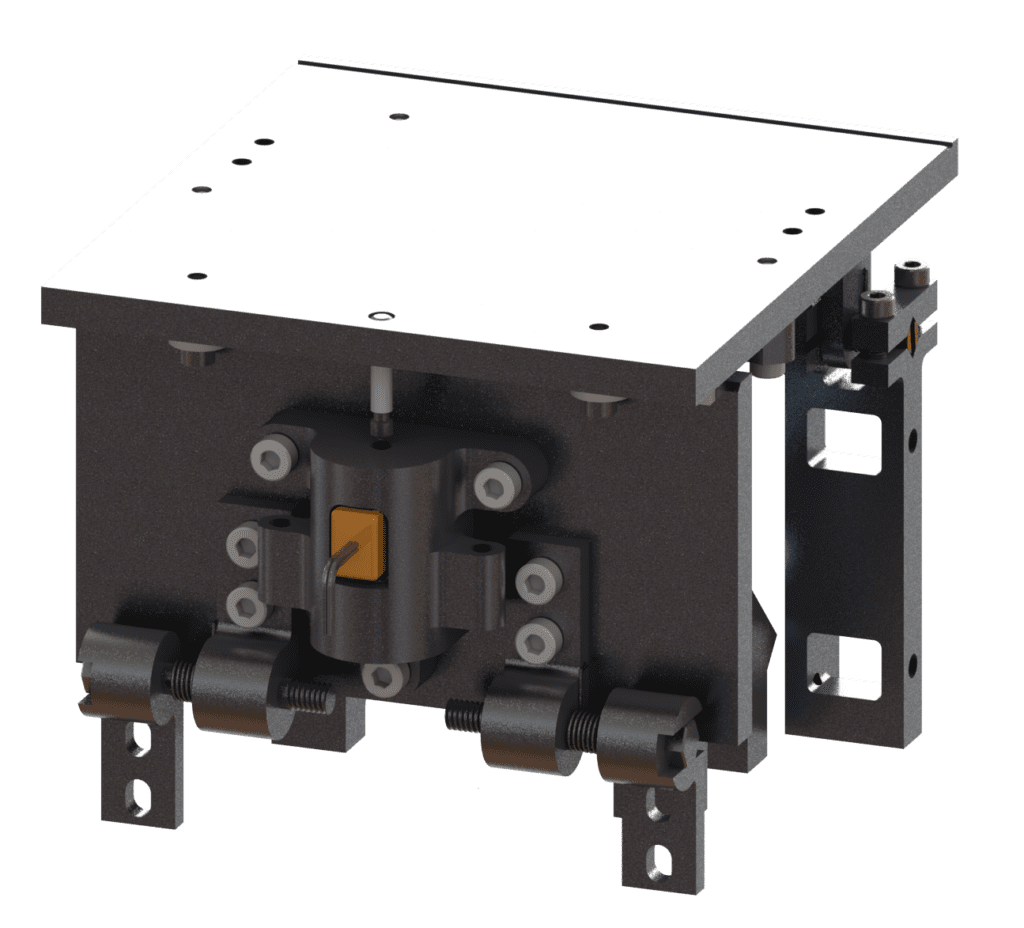
- Doors hold mirrors redirecting UV light from ionosphere to lens
- Doors need room to open (only 2mm of clearance from previous design)
- Adjusted to primarily mount from the bottom
- Top door seal removed and edges trimmed
- Door stops require redesign
- Mounts from datum and side plates
Design Features
- Seals (highlighted red in image) are required to prevent contamination of optical equipment by debris
- The low coefficient of friction of Delrin (at door hinge) prevents interference with the swinging
- Viton seals also serve as vibration dampers
- Seals are low outgassing
Viton Seals
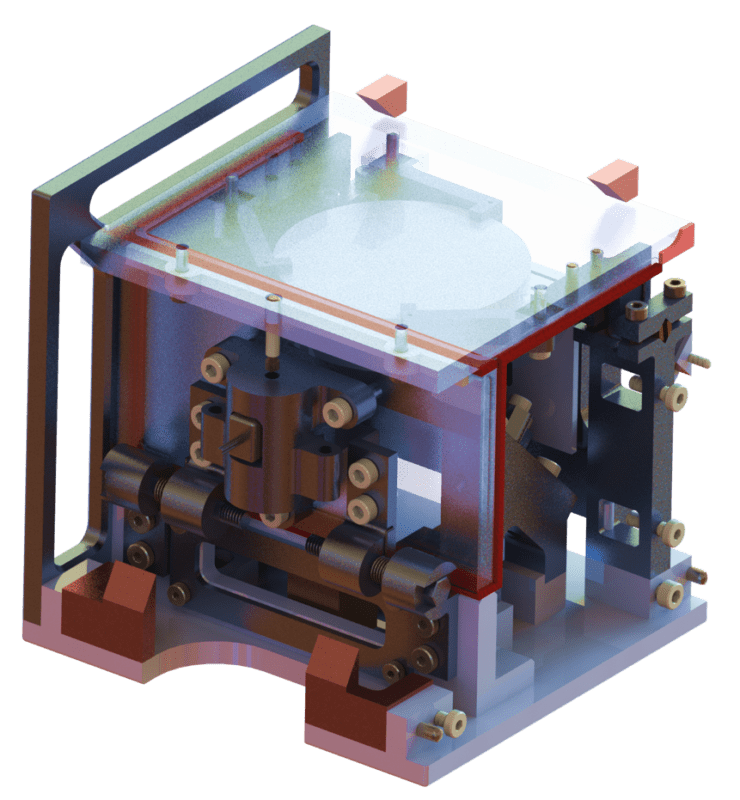
Delrin Door Stops
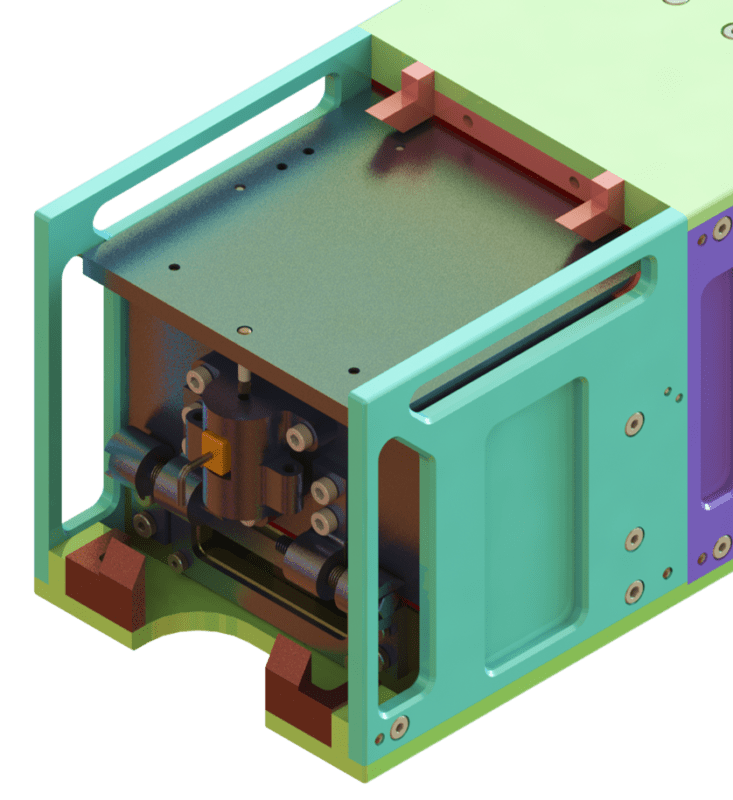
- Doorstops (colored red in image) absorb impact of opening doors, preventing shock to optical equipment
- Top doorstops hold top door at the proper angle to align top mirror
- Elasticity of Viton allows for dampening of vibrations from impact
- Nitrogen hose applies positive pressure before and during launch to keep out debris
- Stainless Steel mesh at the inlet and outlet keep dust and other particulates from getting inside
Nitrogen purge port
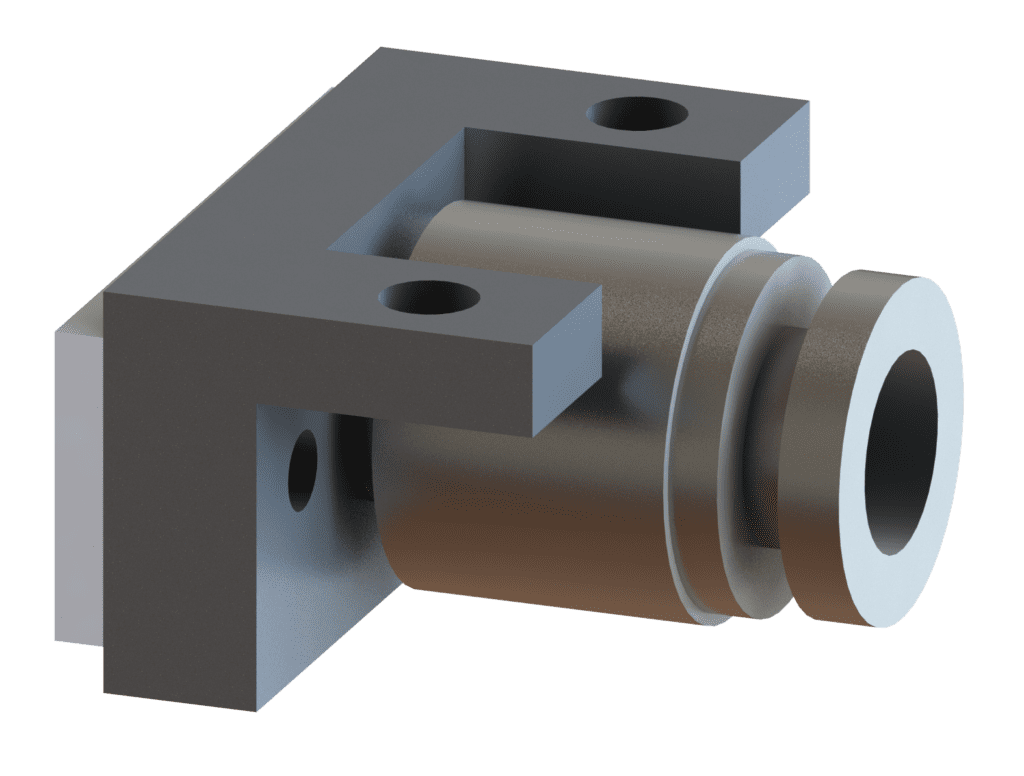
final design component layout
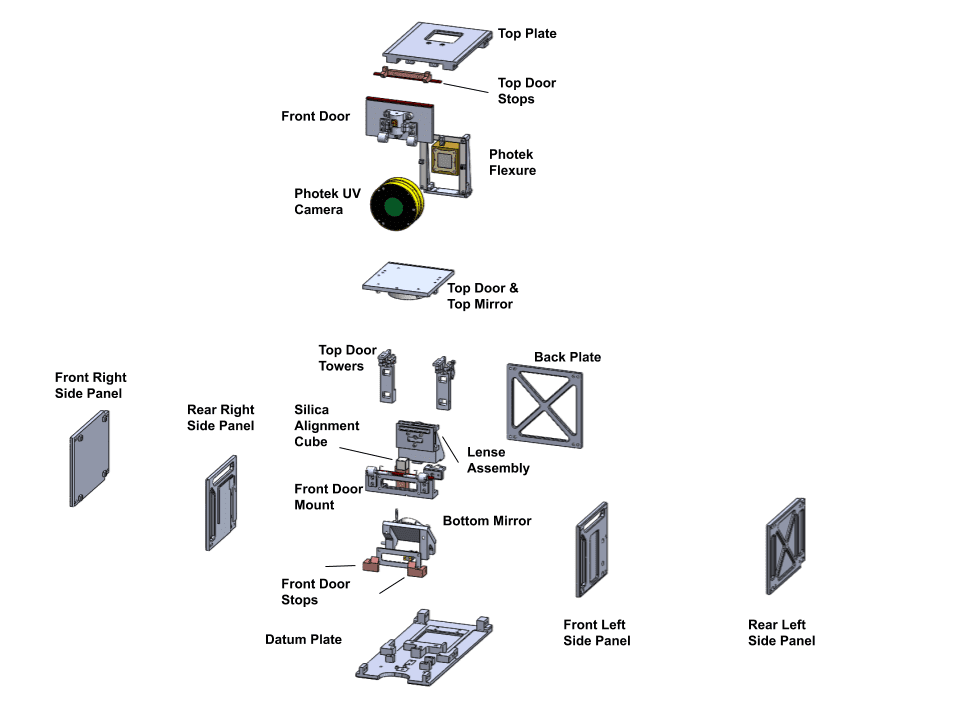
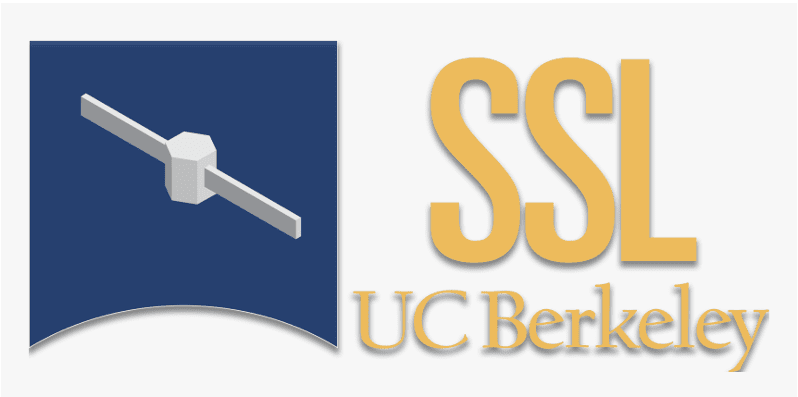
Berkeley Space Sciences Laboratory
This project was sponsored by Kodi Rider and Dr. Thomas Immel, with help from Cal Poly faculty advisor Dr. Eltahry Elghandour, and funding from NASA.
Design Concept
Flexure Mount Assembly
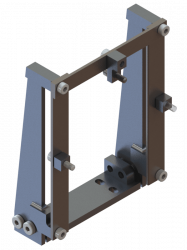
- Functions:
- Mount PHOTEK to structure
- Accurately align PHOTEK with incoming light
- Damp vibrational loads to protect PHOTEK
- Design Decisions:
- Mount exclusively from the bottom to avoid the need for high tolerances on more than one mounting surface
- Designed for adjustability — slots and gaps allow the position of the PHOTEK to be adjusted during assembly along all three primary axes to ensure accurate alignment without need for impractically small tolerances
- PHOTEK attaches at three points for proper constraint
- Material Selection:
- Mount: 6061 Aluminum — for high specific strength, ease of manufacturing, and widespread use in space applications
- Flexure blades: Ti-6Al-4V — high ductility and strength allows for large amounts of yield in thin blades, damping out vibration before they reach the PHOTEK
Datum Plate and Instrumentation Frame
- Functions:
- Act as bottom plate of frame enclosure
- Facilitate mounting and alignment of critical components and assemblies
datum plate
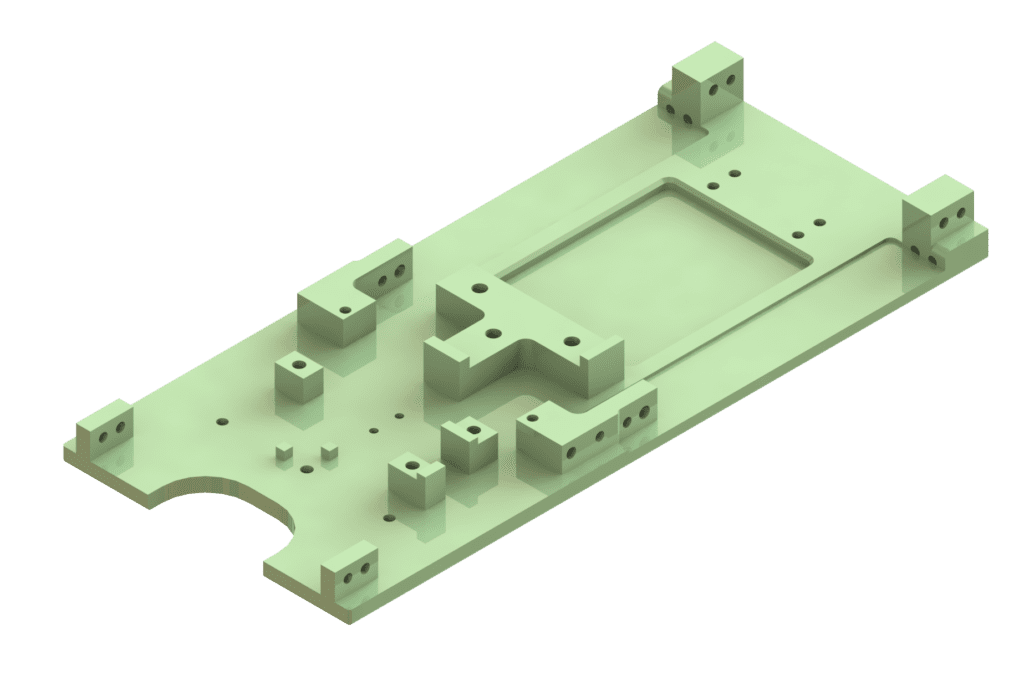
- Design Decisions:
- To reduce the need for high tolerances on multiple frame surfaces, the bottom plate (datum plate) was selected as the primary mounting surface for all critical assemblies
- Constraints allow the positions of critical assemblies to be adjusted during assembly to ensure accurate alignment without need for impractically small tolerances
- Material Selection:
- 6061 Aluminum — for high specific strength, ease of manufacturing, and widespread use in space applications
Instrumentation Frame Panels
Side Panels
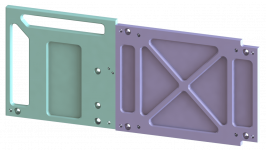
top panel
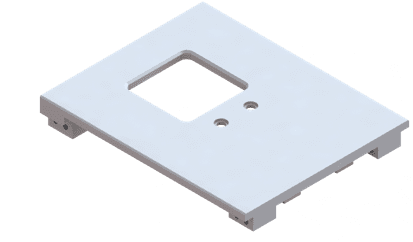
Back panel
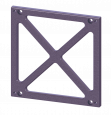
- Functions:
- Act as satellite enclosure
- Shift center of mass
- Stabilize top door towers
- Design Decisions:
- Dual side panels allow for easier assembly
- Cutouts on side panels shift the center of mass and reduce total mass
- Large holes in back panel allow for inclusion of a future third unit
- Material Selection:
- 6061 Aluminum — for high specific strength, ease of manufacturing, and widespread use in space applications
On Ground Orbital Deployer Simulator
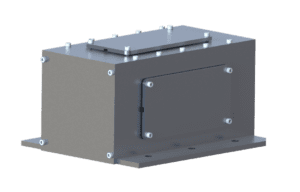
During launch, MUVI will be stowed in a Poly Picosatellite Orbital Deployer (P-POD), from which MUVI will be ejected once in outer space. The On Ground Orbital Deployer Simulator (OGODS) was designed and manufactured to replicate the boundary conditions MUVI will be subject to inside the P-POD while experiencing launch vibrations. OGODS was intended to be used to for vibration testing of MUVI, but due to COVID-19, vibration testing was not completed.
Exploded Assembly Render
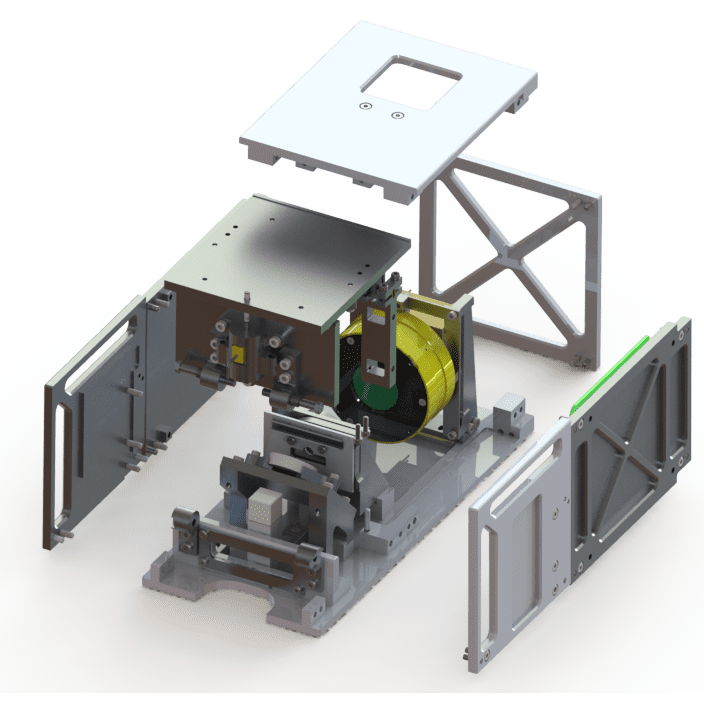
Analysis & Verification
Finite Element Analysis
Several FEA studies were performed during the analysis and verification stages of this project. During the initial design phases, 100G static loads were applied to the instrumentation frame and camera flexures. This loading condition is beyond what what the satellite is expected to see during launch; however, this study helped design plate thicknesses before performing any sort of in depth vibration studies.
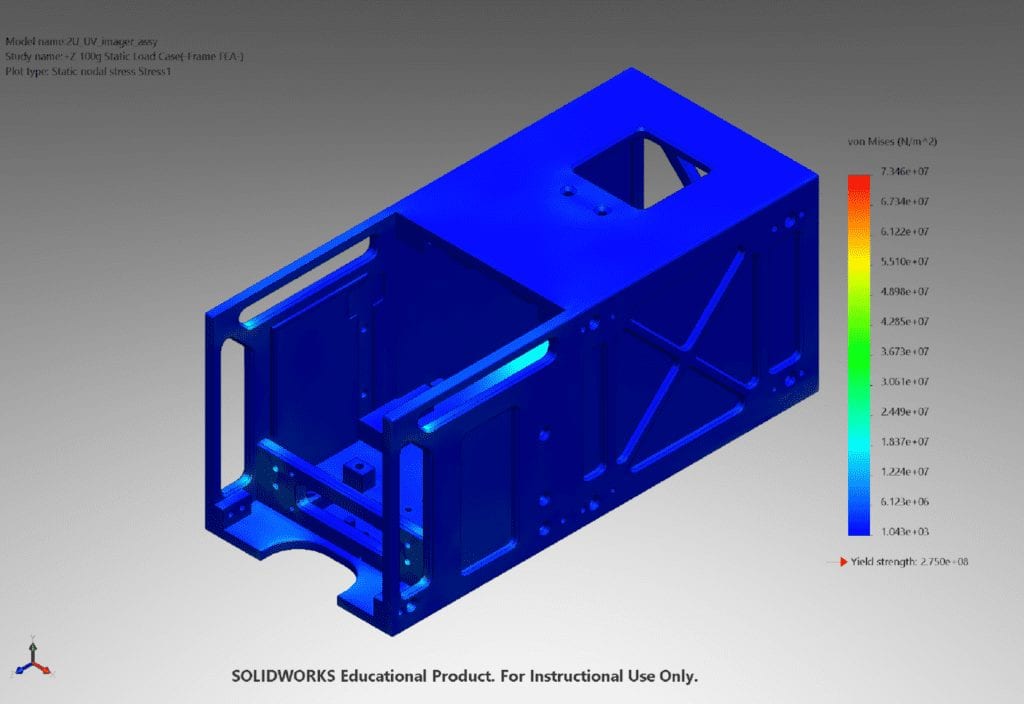
Shown is a snapshot of the stress distribution from a 100G loading condition in the +Z (longitudinal) direction on the instrumentation frame. This study, performed in SolidWorks, uses roller boundary conditions on the rails and front (left square face) of the frame. The mass and center of mass of each instrumentation component was measured and used to apply a 100G remote loads in the +Z direction. This process was repeated for the remaining five principal axis directions.
This study shows a maximum displacement of 0.075 mm and maximum von Mises stress of 1.24E+08 N/mm2. This results in a stress FOS of 2.23. Overall, this study indicated that the designed frame dimensions were acceptable to proceed with engineering drawings and more detailed vibration studies.
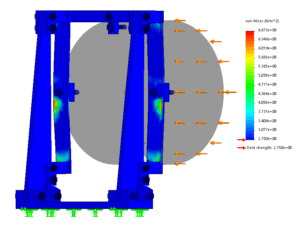
Static FEA studies were performed on the flexure mount assembly to determine if aluminum could suffice as the flexure blade material or if titanium would be required. Analysis showed that aluminum blades would need to be unacceptably thick not to yield under a 100G load case. Titanium, therefore, was ultimately chosen as the flexure blade material because the blades could carry the necessary loads while being thin enough to yield significantly and thus absorb vibrational loads before they reach the PHOTEK.
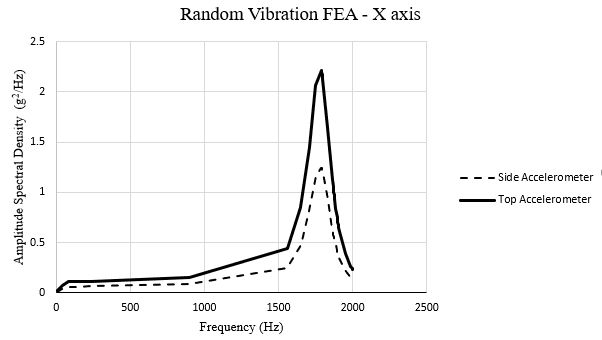
Vibration analysis in FEA was conducted to determine the natural frequencies of the OGODS, frame and flexure assemblies. The graph above shows the frequency response of the OGODS experience a random vibration analysis, indicating a natural frequency of roughly 1800Hz.
Manufacturing and Assembly
Due to the size and complexity of parts and the tight tolerances, manufacturing was outsourced. Assembly was planned to be done in-house but was never completed. Detailed Assembly procedures were completed and are available.
Final Design
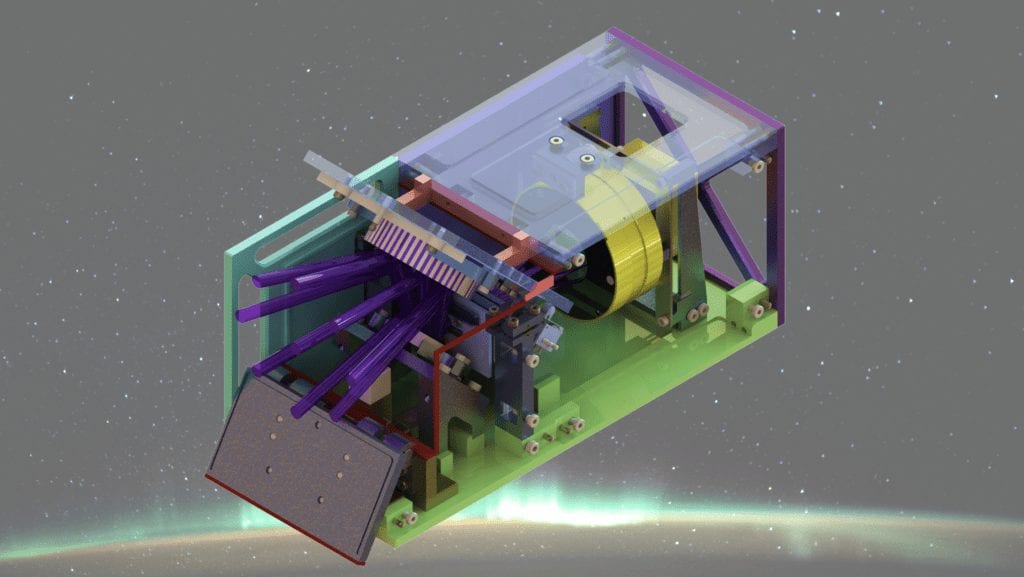
Completed Objectives:
- PHOTEK mounted to frame such that it should not take loading
- Critical assemblies can be mounted with room for adjustments to ensure proper alignment
- Frame fits within a 2U form factor without need to be excessively thin
- Structure is sealed from external debris yet remains uninhibited of opening doors
- Total assembly expected to adhere to mass and center of mass requirements
- Accommodations made for nitrogen purge port
Missing Objectives
- Timeline for manufacture and assembly was not met
- Total assembly has not undergone and passed vibration testing
- Doorstops lacking complete design
- Door Springs are needed further design and analysis
Next Steps
At the conclusion of MUVI Phase III, MUVI as a whole is still far from complete. COVID-19 related delays erased assembly and design verification with vibration testing from the scope of MUVI Phase III. As a result, the most immediate next steps for future participants is to assemble all the manufactured parts and complete vibration testing. In additions to these steps, the future of MUVI includes:
- Doorstop geometry redesign to ensure proper top mirror alignment
- Door Spring redesign for proper spring forces
- Mirror flexure redesign
- Addition of 3rd unit to include power and control systems
- Circuit board design
- Design of equipment for thermal management
- Thermal vacuum (TVAC) testing to ensure optical alignment is not compromised during change of environment