Our Team
Team of four mechanical engineering students tasked with designing a modular buoy.
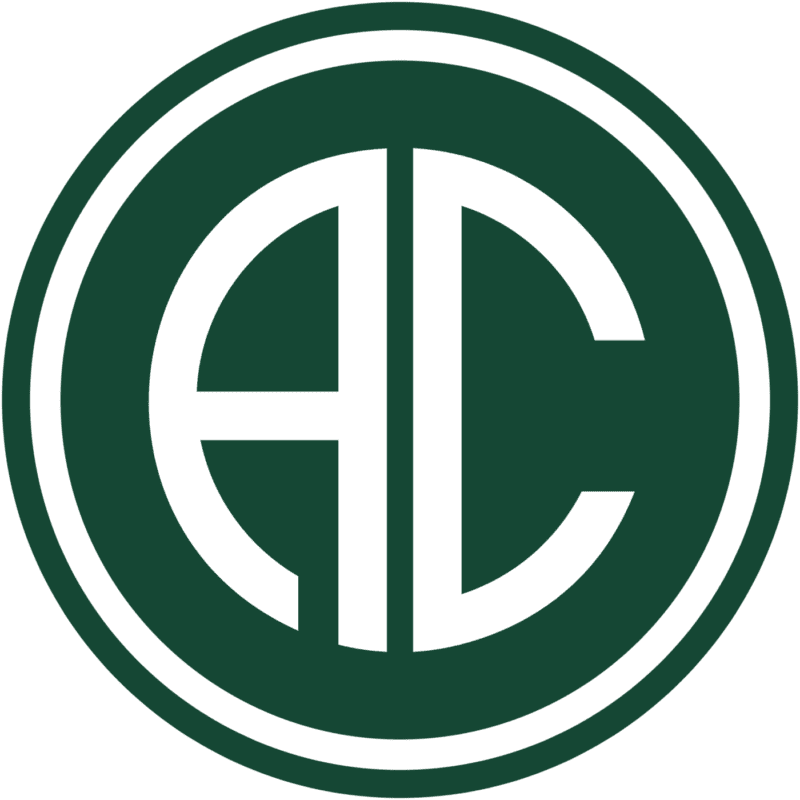
Anthony Catello
Validation Lead
Anthony oversaw all analysis and testing of the buoy to ensure all specifications were met. His experience as a scuba diver and strong understanding of fluid dynamics made him essential to the team.
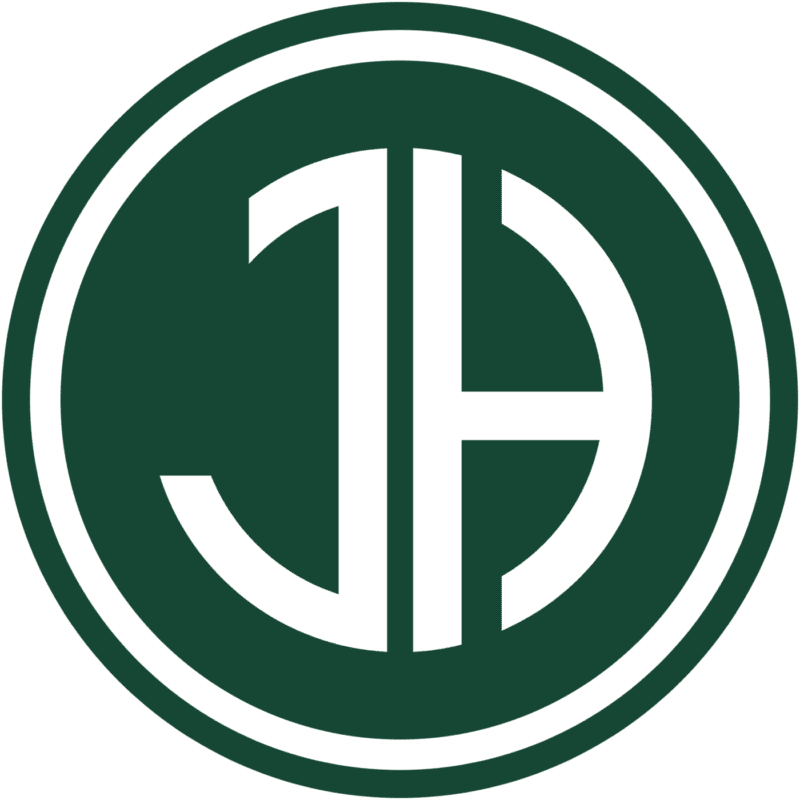
joseph heald
Budget Lead
Joseph was responsible for tracking all expenses and maintaining a project budget. His out of box thinking and creativity inspired innovative design solutions.
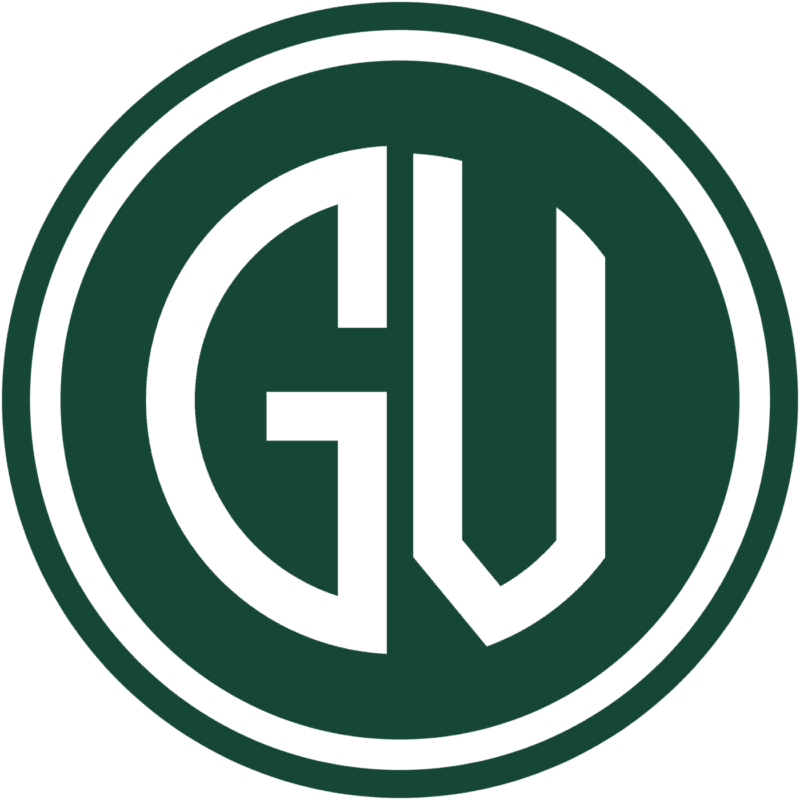
gabriela vargas
Design lead
Gabriela was responsible for designing the buoy system in Solidworks. Her previous knowledge of how saltwater can affect material proved valuable in effectively designing a buoy that can survive in harsh ocean conditions.
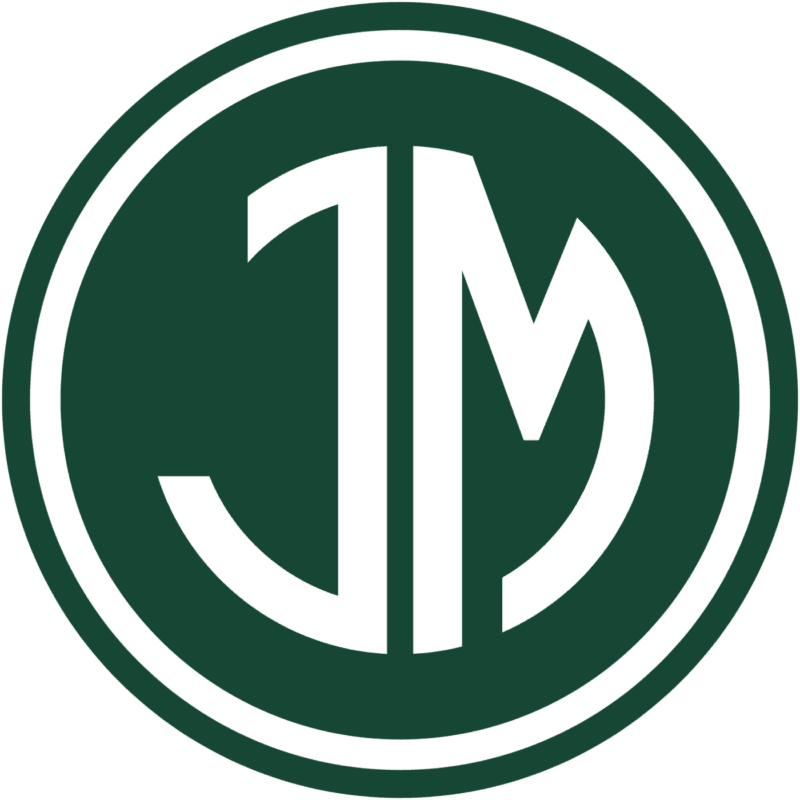
james marinas
Manufacturing lead
James was entrusted to lead our team’s manufacturing efforts. His passion for hands on learning made him even more committed to fabricating a high quality product.
Our Project Videos
Our Project's Digital Poster
Problem Statement
Cable terminations are often the least reliable and most expensive components of a maritime system. These cables are suspended in water by a buoy to reduce wear at the terminations. The Naval Information Warfare Center requires a modular auxiliary float with tunable buoyancy that can be placed along such cable. Our system must be able to be deployed, adjusted,and retrieved quickly and easily.
Design Constraints
- Working depth of 2000 foot sea water (fsw)
- Deployment and retrieval time less than 5 min
- Features to protect cable from exceeding bend radius
- System must have adjustable total buoyancy between 100-700 lbs.
Concept Prototype
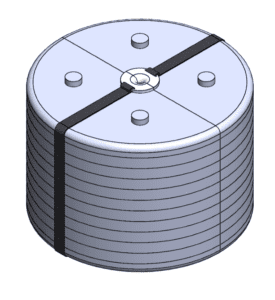
100 lb buoyancy concept CAD rendering features:
- 1 top module assembly, 2 inner module assemblies, and 1 bottom module assembly
- Collar contains slotted feature for webbing to wrap through and permanently be sewn together
- Alignment rods in each assembly to allow the user to easily stack multiple module assemblies together
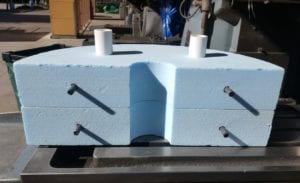
Concept prototype concerns to be addressed in final design:
- Possible rotation from circular collar
- Oceanic build up on surfaces during three month deployment
- Manufacturing cost associated with mating pin features in module
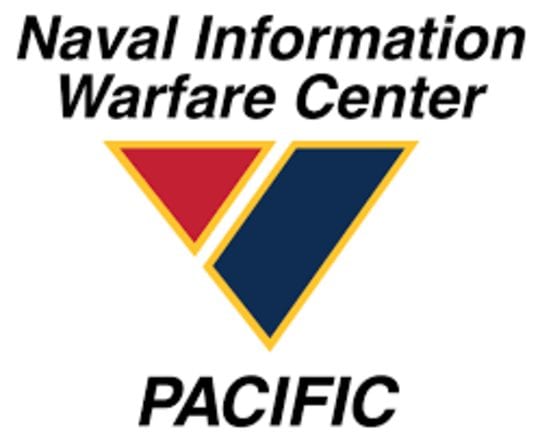
This project is sponsored by the Naval Information Warfare Center.
Analysis
The analysis conducted on our system focused on the collar and cable interaction. This interaction is critical because the goal of our design was to protect the cable. To perform this analysis a press fit model found in Shigley’s Mechanical Engineering Design was used.
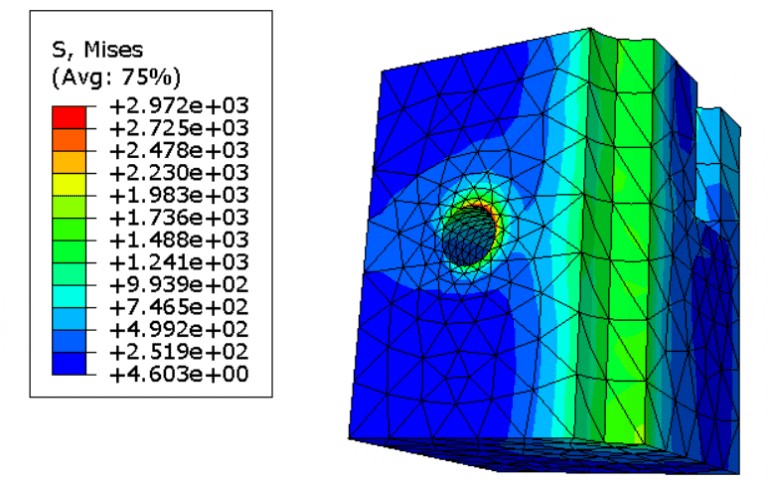
By creating a convergence study on the most critical point the stress seen by the collar was verified to be well below the yield stress of the two-piece Delrin collar.
Design Validation
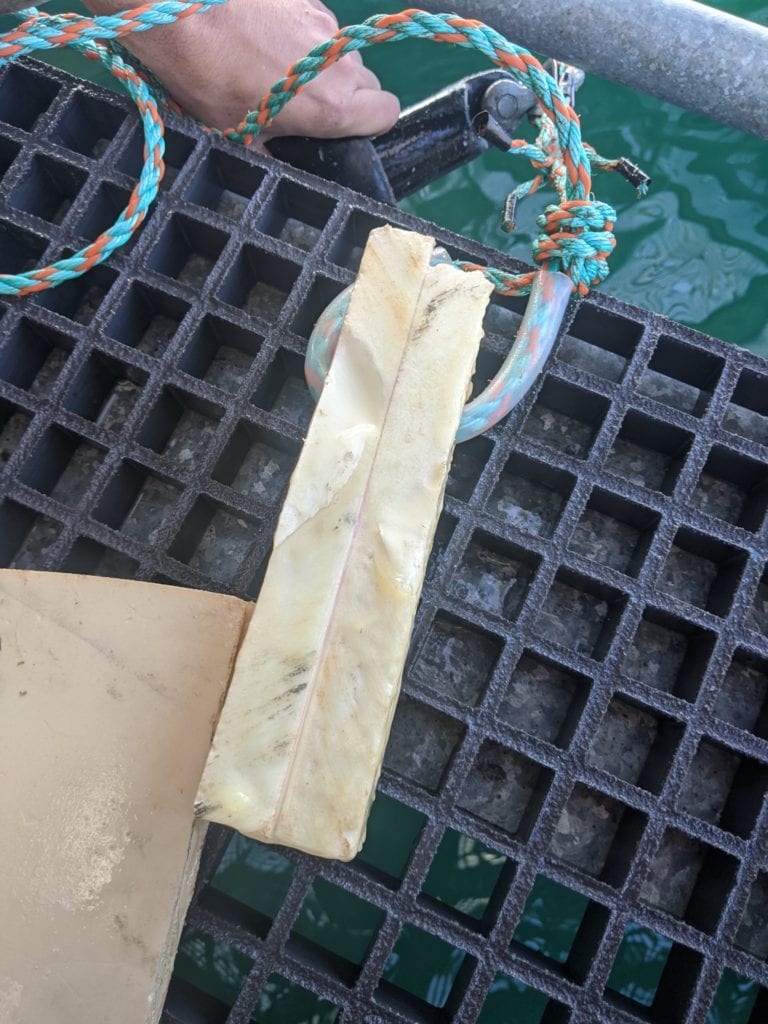
Side view of test sample prior to deployment.
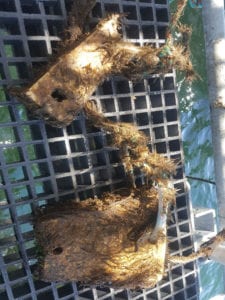
Samples removed after 8 weeks submersed in water.
Submersion Test- This test would verify if the lamination method and epoxy coating was an effective way of binding layers of the GUIRT syntactic foam together to form each module. We were able to conduct this test for a period of 8 weeks submersed under water. There was significantly more algae build up than expected. One reason for this was due to it’s placement under the dock which sees more algae than in open ocean water. The amount of build up was so much that reconsideration of the epoxy coating and lamination method would need to occur in future design iterations.
Final Design
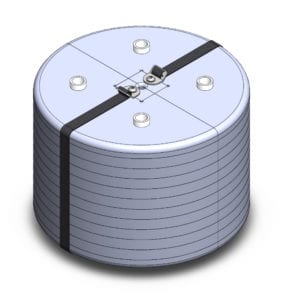
Design Specifications:
- 17.5 in. in Diameter
- Working depth of 2000 fsw
- Adjustable total buoyancy of 100-700 lbs.
Key Features:
- Modular and compact
- Marine grade material
- Features for quick and easy deployment
Design Justification:
- Two piece collar verified by FEA to be able to withstand required attachment hold force
- Modules made of GURIT syntactic foam meets buoyancy and operational depth requirements
- Stainless steel hardware to meet strength specifications and for superior corrosion resistance
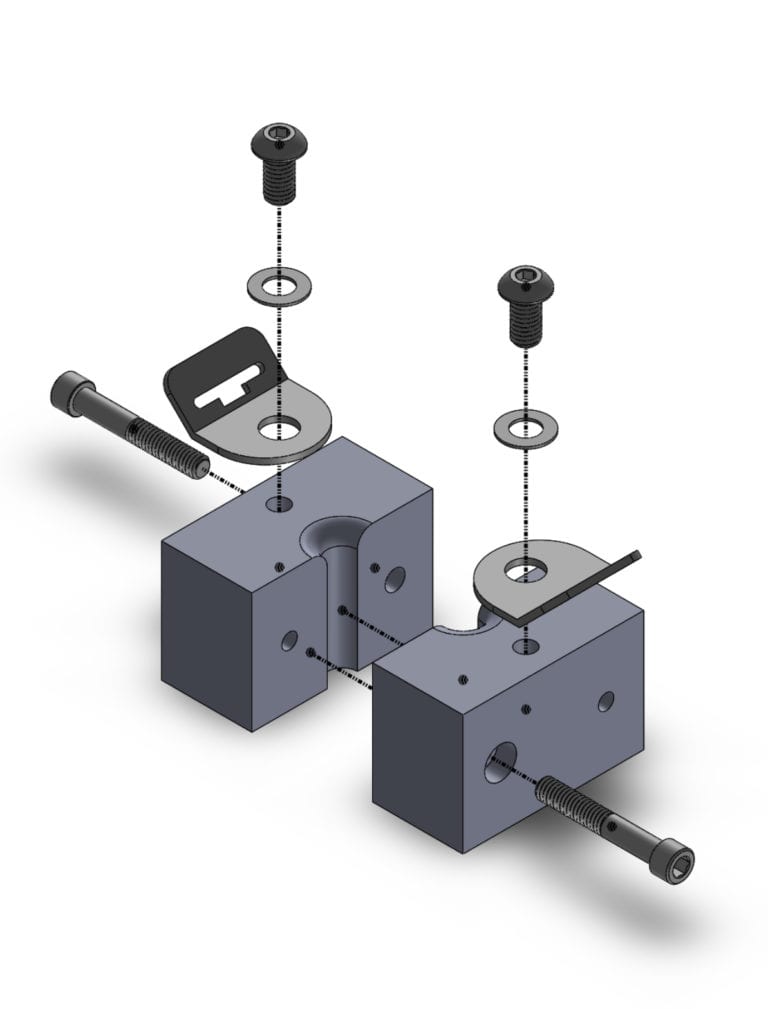
Exploded view of collar assembly featuring a Delrin two-piece collar, stainless steel hardware, and a webbing anchor plate.
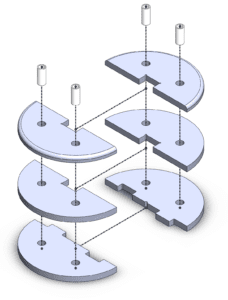
Exploded view of the top module assembly. The design features an updated profile and mating features.
Recommendations
Improvements to be made if the buoy were to be re-designed:
- Additional epoxy coatings to reduce build up and further research into lamination methods
- Add additional features to protect the cable from exceeding the maximum bend radius
- Complete design validation testing to verify material changes and feature changes will function as expected.
Acknowledgements
We would like to express a special thanks of gratitude to our project advisor Professor Sarah Harding and our sponsor liaison Kevin Merhoff. We also like to extended our gratitude to Jason Felton from the Center for Coastal Marine Sciences at Cal Poly for sharing his expertise and allowing us to perform testing at the facility.