Our Team
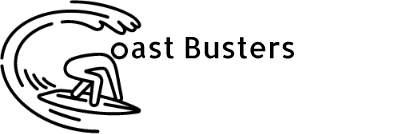
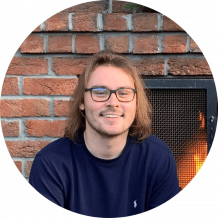
Ethan Frey
Testing
Ethan is a fourth-year Mechanical Engineering student with a general concentration. He is originally from Irvine, CA and will be graduating in Fall of 2020.
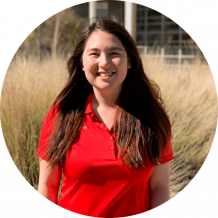
Kathryn Versteeg
Manufacturing
Kathryn is a fourth-year Mechanical Engineering student with a general concentration, minoring in Biology. She is originally from Orange County, CA and will be graduating in Fall of 2020.
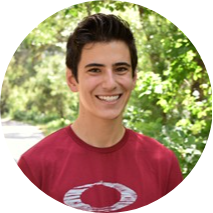
Jackson Tucker
Design Verification
Jackson is a fourth-year Mechanical Engineering student with a manufacturing concentration. He is originally from Poulsbo, Washington and will be graduating this spring.
Acknowledgements
We would like to acknowledge all the help and advice given to our group by our advisor, Dr. Brian Self, QL+ project manager, Vanessa Salas, and our challenger, Dana Cummings. We also appreciate the support given by our sponsor, QL+.
Our Project Videos
Our Project's Digital Poster
Problem Statement
Users of prosthetic legs have issues with current foot shells wearing out too quickly and needing to be replaced too often. They need a more durable foot shell that will last longer than commercially available options.
Design Constraints
- Must fit onto our challenger’s prosthesis
- Must be able to last one full year
Design Considerations
- Design had to be able to be molded and cast using urethane rubber materials.
- Design needed to be durable enough to resist wear but compliant enough to insert the prosthetic foot easily.
- Design needed to be cheap to manufacture and as realistic as possible.
Design Concept
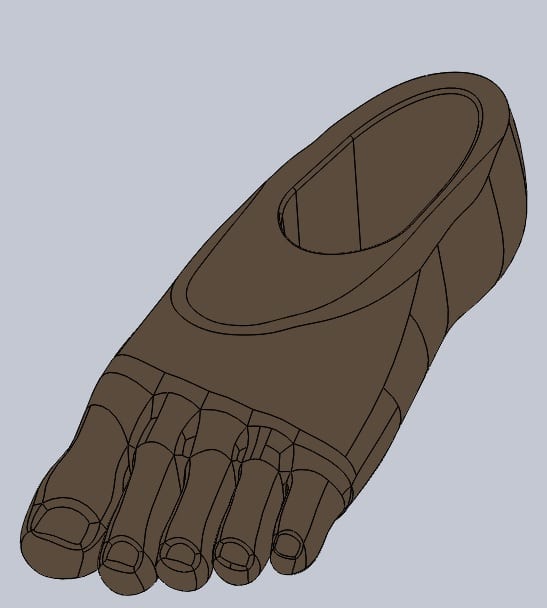
Rendered CAD model of prosthetic foot shell.
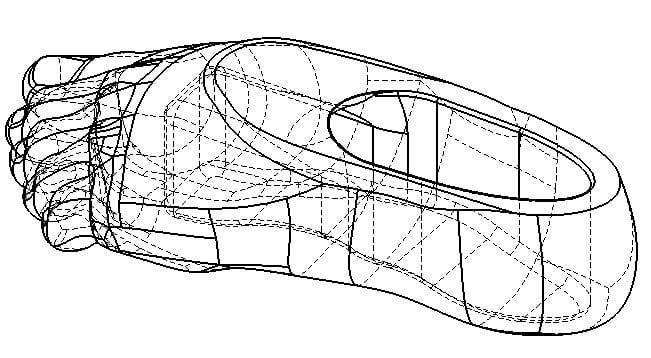
Detailed view of foot shell CAD model
This CAD model allowed for a scale model to be 3D printed along with serving as a base model to begin our manufacturing process.
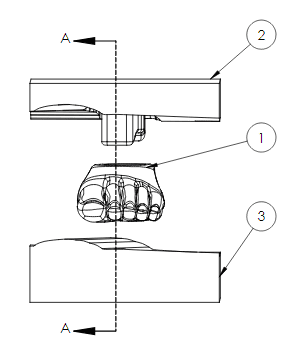
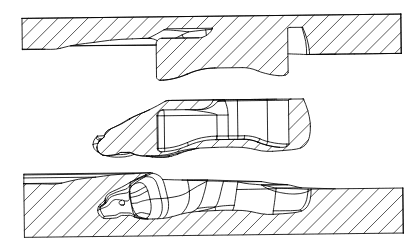
The above figures detail our molding assembly process, with our foot shell being constructed using one two-part mold that will mate together using built-in locator pins.
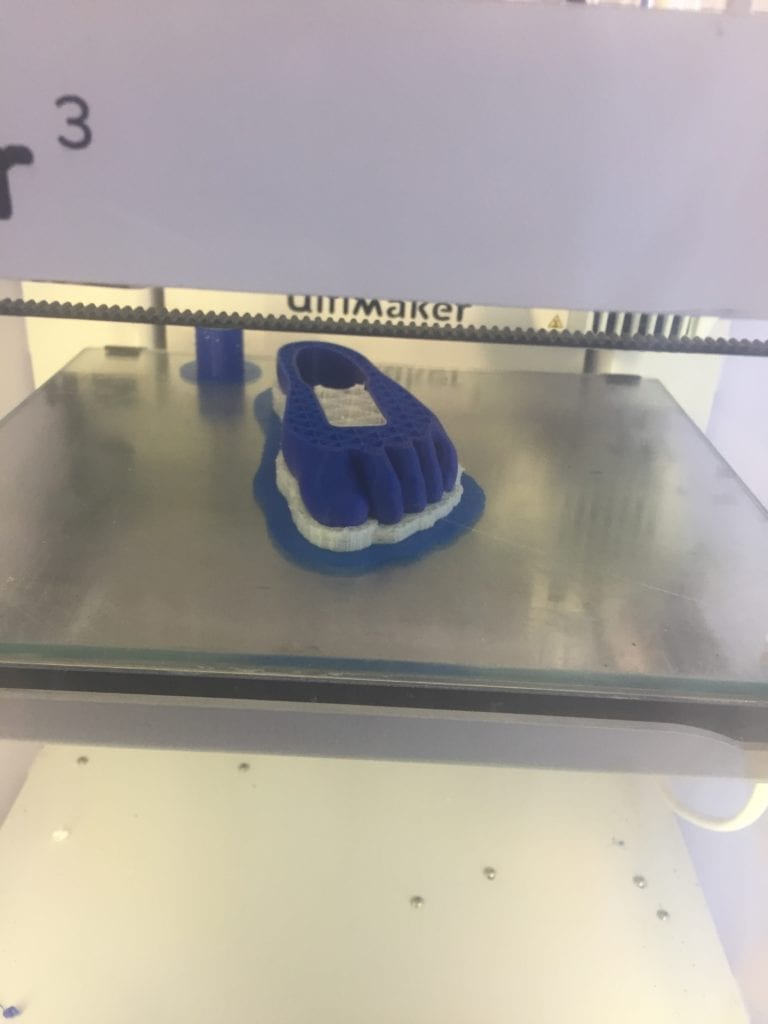
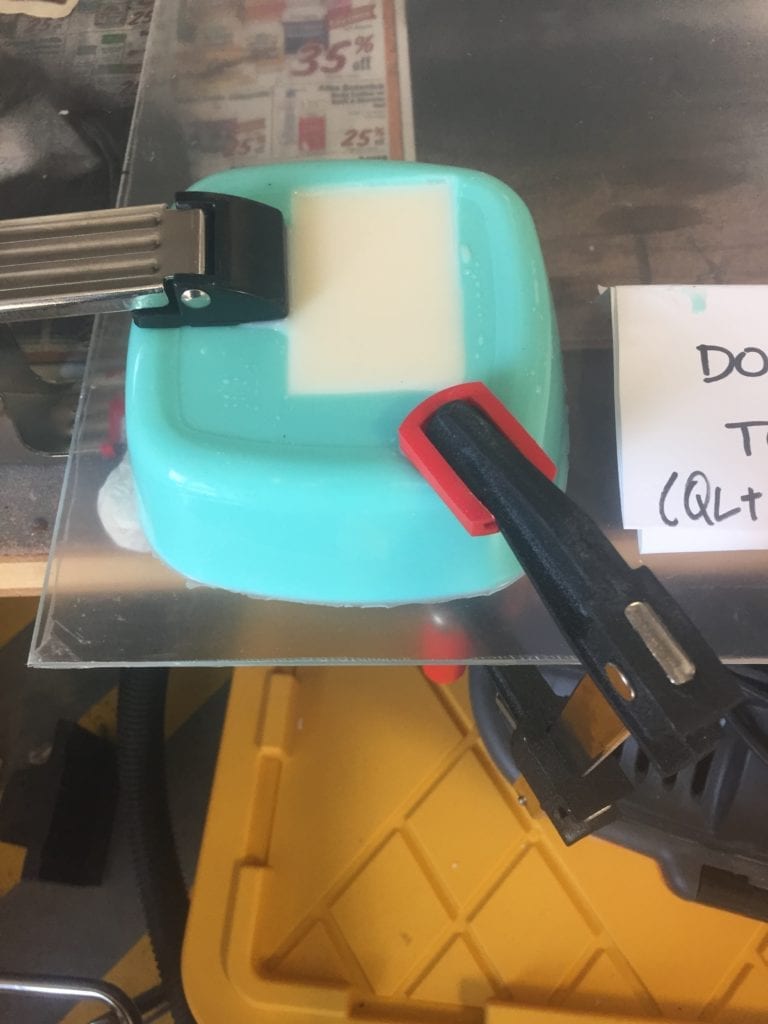
Our design concept prototype was constructed by using a 3D printer at the QL+ lab that was able to print the structure of the foot shell with one material and the supports of the foot shell with a water-soluble material. We also started our casting process using a silicone based mold but found that the silicone left a thin layer of tacky residue due to the incompatibility between the two types of plastic rubbers.
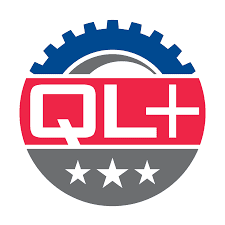
This project is sponsored by the Cal Poly branch of Quality of Life Plus (QL+)
Urethane Molding Analysis
Before a full size foot shell could be casted, we experimented with basic shapes to improve our casting ability as well as determine the durometers of the materials needed.
Urethane Bonding Testing
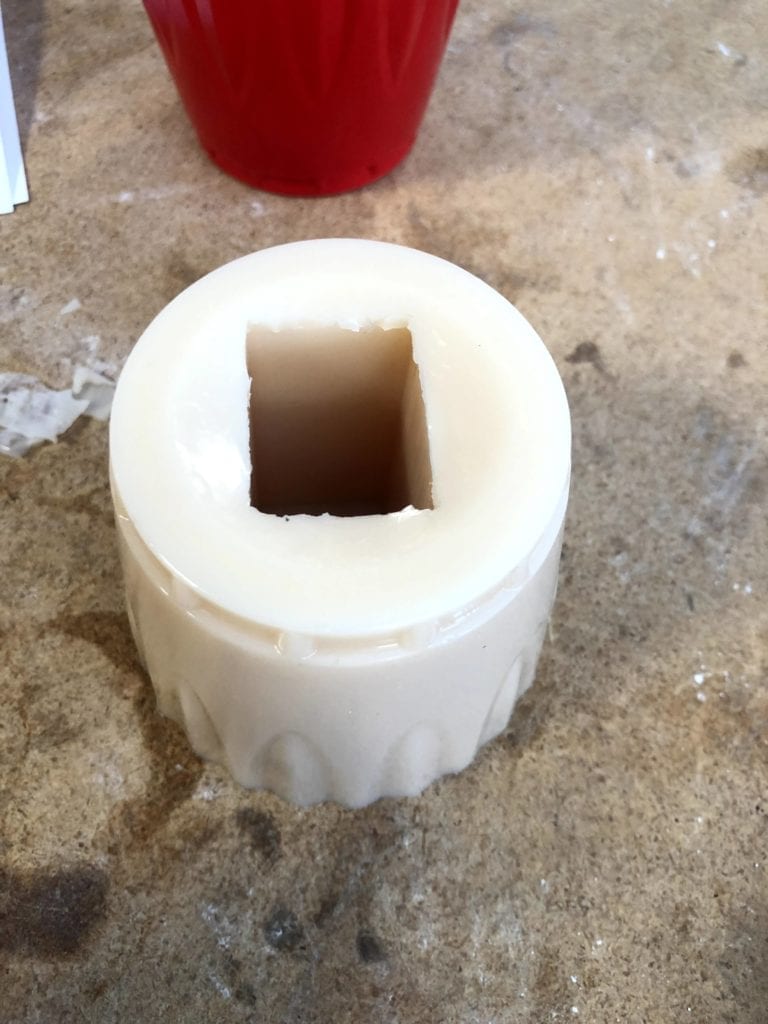
We began molding practice by molding a simple rectangular cube in a mold made from urethane. We used this mold to perform our bonding testing experiments.
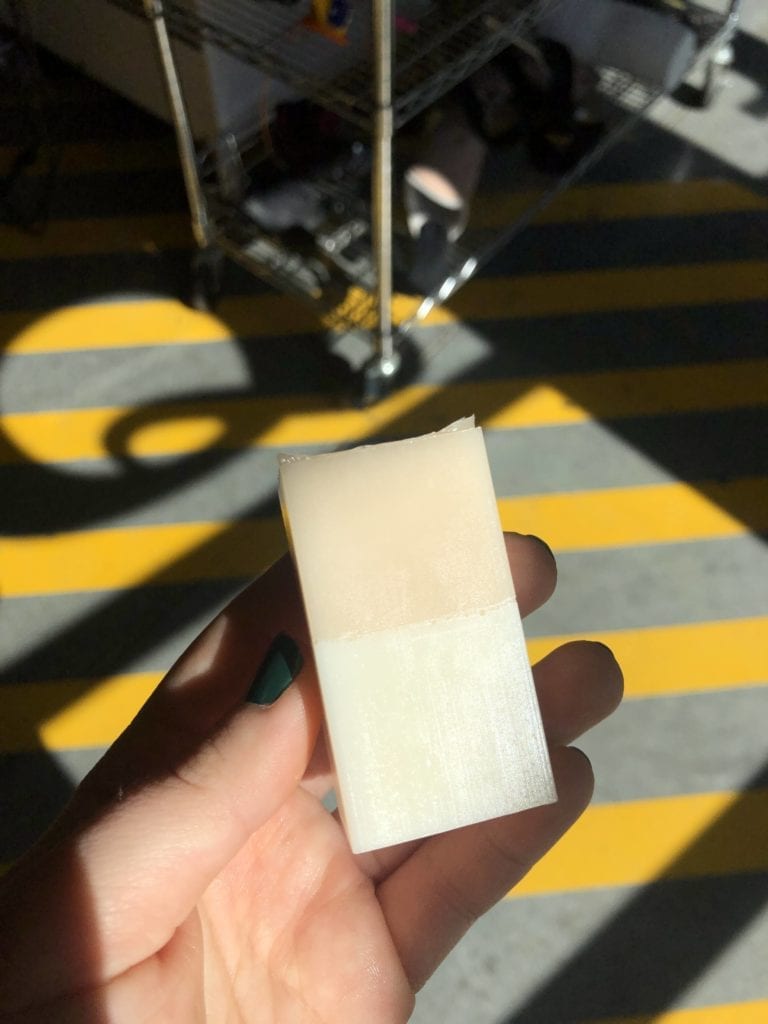
By molding the cube using two different durometer urethanes at different initial cure times, we found that the ideal time between layer pours is six hours.
durometer Testing
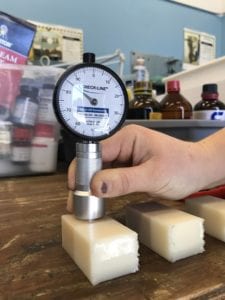
The durometer of the urethane rubber samples was tested to compare the hardness to an existing foot shell to ensure the prototype would have higher durability. Testing was conducted using a
Foot Shell Testing
and Test Fixture
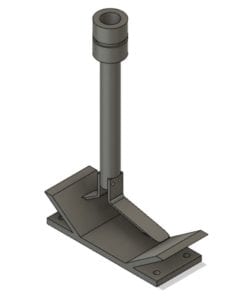
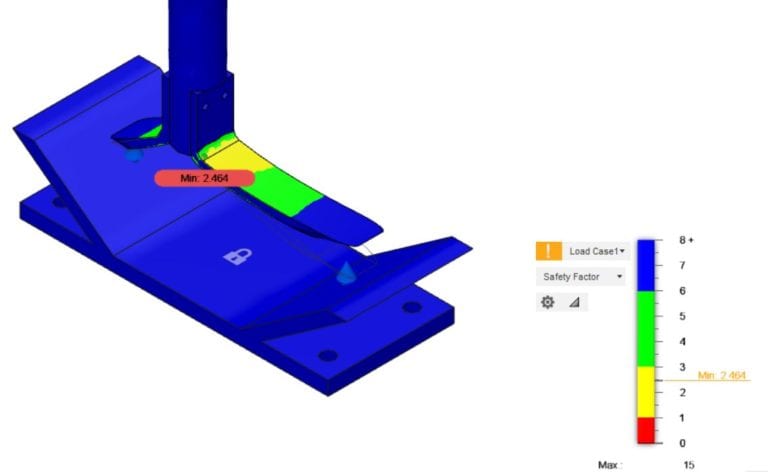
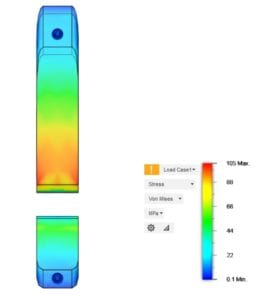
Because of the circumstances, fatigue testing on the foot shell was not able to be completed. A test fixture model with manufacturing steps and testing procedure were drafted to assist a future team that might continue the work of this project.
Manufacturing Process
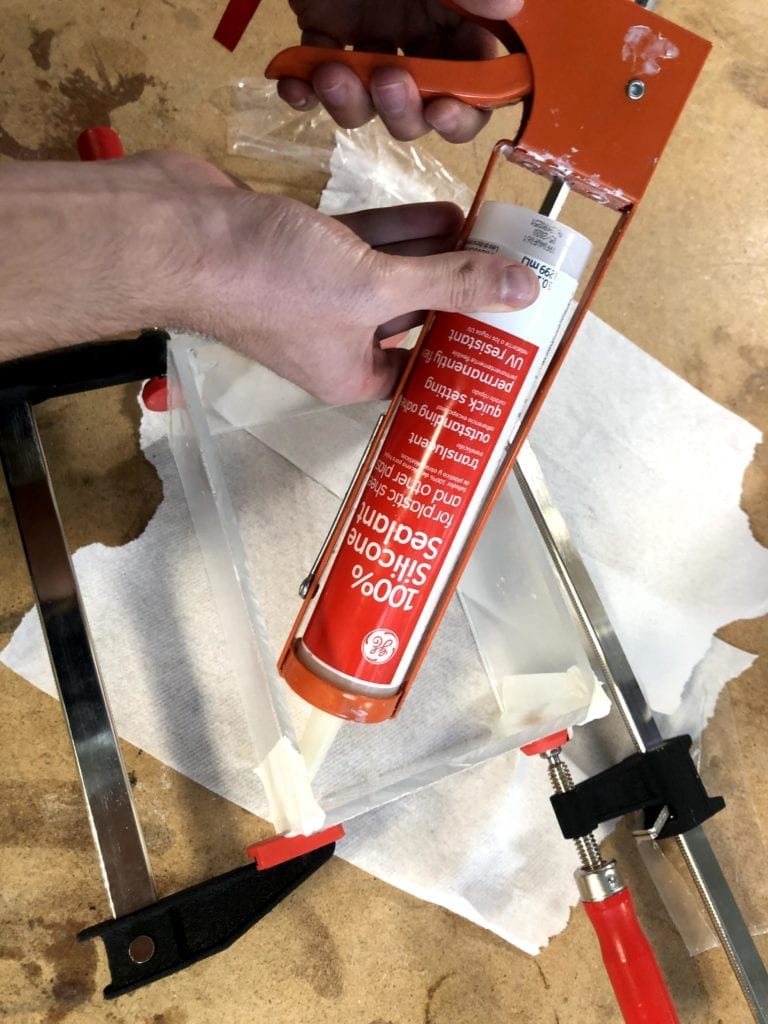
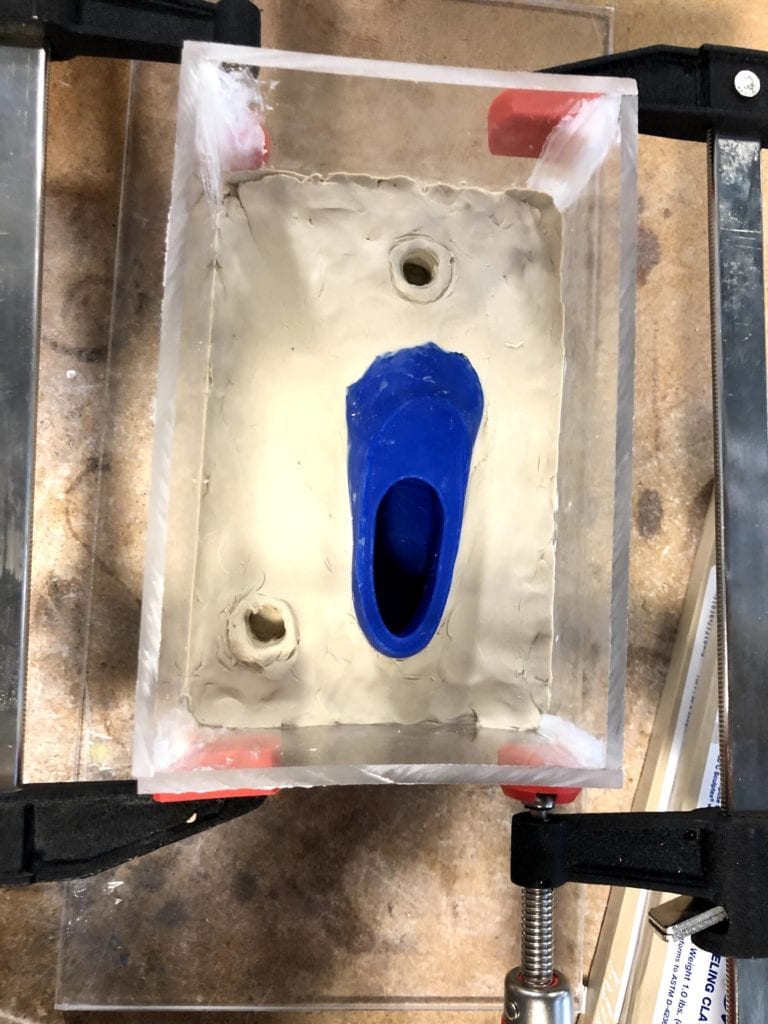
Our manufacturing process began by first constructing a mold box out of acrylic sheeting and silicone plastic adhesive. We then submerged a 3D printed version of our foot shell into modeling clay to prepare for the pour of our first mold half.
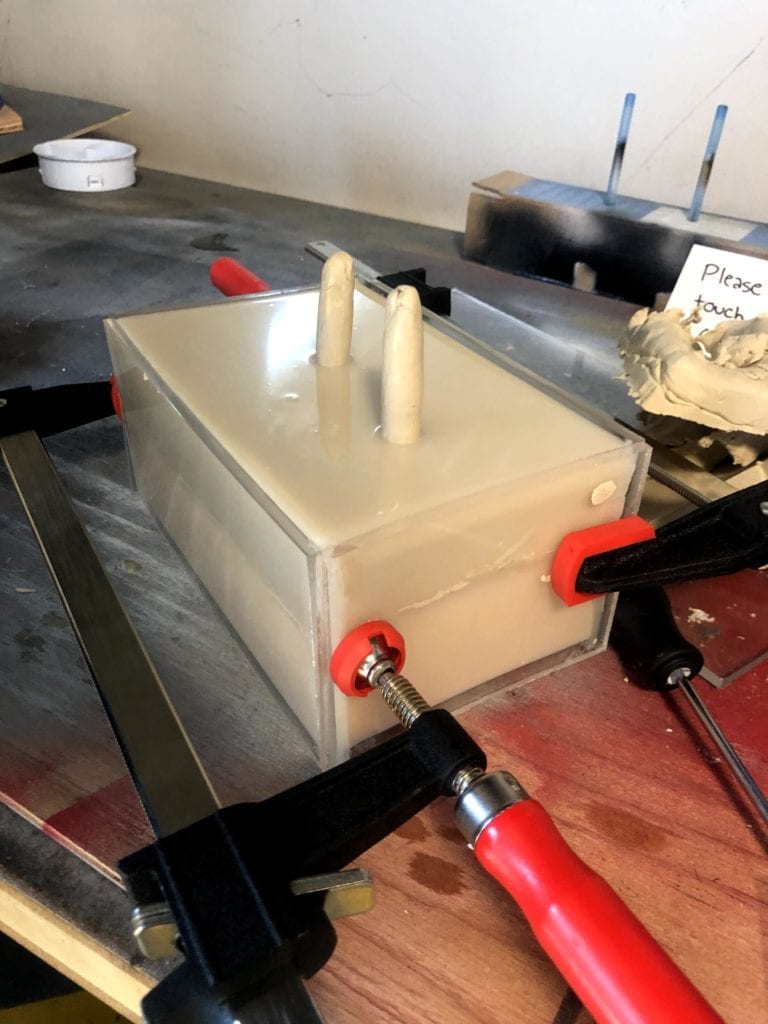
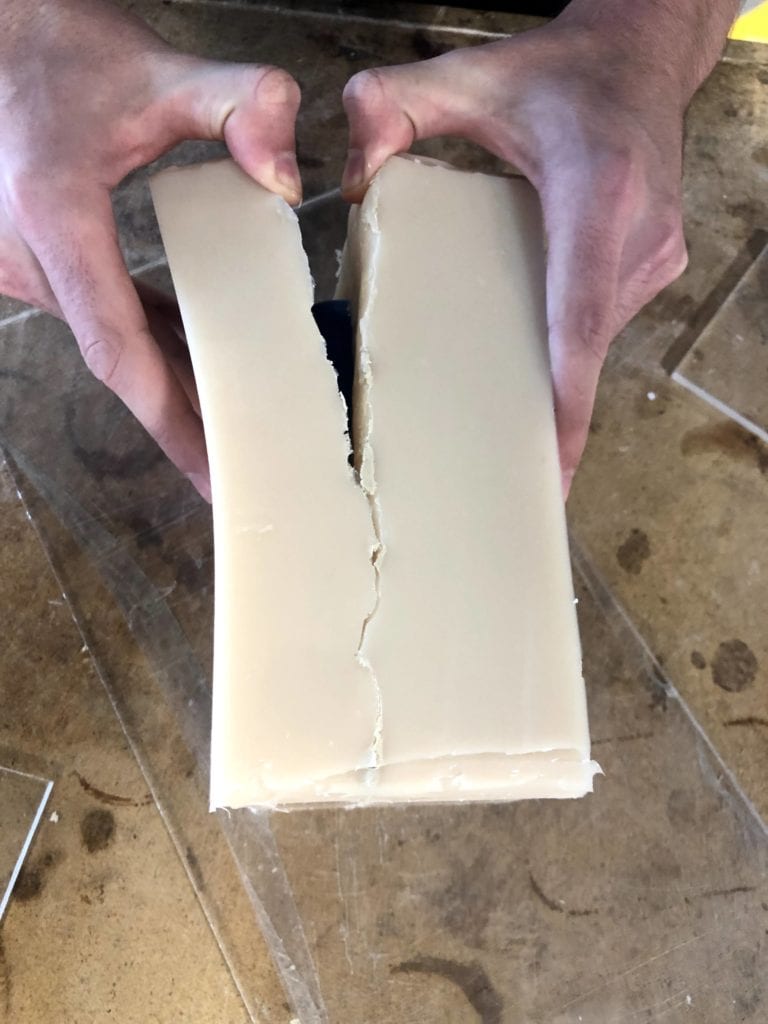
After pouring both halves of the mold, waiting the required 12 hours for the urethane to cure, the mold can be separated and the 3D foot shell can be removed. After removal, the urethane foot shell can be cast utilizing two sprue holes cast into the mold.
Prototype
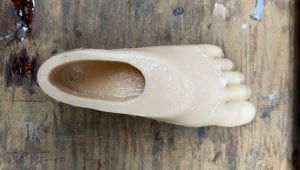
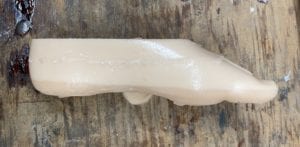
The current state of our prototype is a half-size model of the foot shell casted using PMC 70A urethane rubber on the bottom layer and Vytaflex 50A urethane rubber on the top layer.
Future Steps
Due to the coronavirus pandemic, process on our project was put on hold and we were unable to test or manufacture a full size prototype. Future steps for this project would be to first cast a full-size model of the foot shell, keeping in mind the different layers of urethane that will be used, then manufacture a testing fixture and test the foot shell using said fixture and an Instron testing machine. Other tests that would have be conducted rely upon the foot shell being attached to our challenger’s prosthesis and worn for a period of time.
Recommendations
Improvements to be made if foot shell project were to be continued
- Optimize layering of foot shell by specifying the exact height of each urethane layer
- Minimize formation of/reinforce air bubbles in the toes of the mold
- Design a molding process that allows for better movement of air away from the part (air vents, runners, etc.)
- Design additional testing fixtures for various types of tests (Compliance, Tensile, etc.)