The Project
This project is one of several intercollegiate competitions hosted and funded by NASA RASC-AL. The Moon to Mars Ice and Prospecting Challenge for 2020 aims to explore methods for acquiring liquid water on the surface of Mars. Because all known deposits of water on Mars are underground and in solid ice form, there are significant challenges to overcome. This challenge also requires teams to investigate methods that can be used to collect data about the moon’s subsurface geology.
Main Project Goals:
- Drill through various layers simulating Martian soil
- Collect data about the thickness and hardness of each layer
- Collect clean, liquid water from below the layers
- Document design choices and address necessary changes for real spacecraft use.
STYX is one of ten teams chosen to receive funding to build a prototype of our proposed design. This also means that the team will travel to NASA’s test facility in Langley, Virginia to demonstrate our prototype in a simulated Martian environment with the goal of proving our prototype’s capability and potentially contributing useful design concepts to robotic space exploration efforts for future missions.
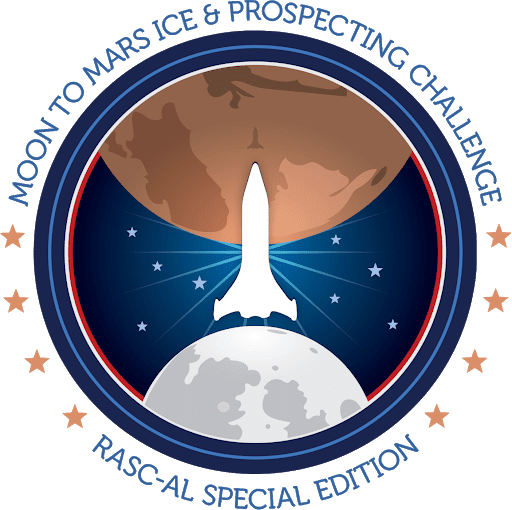
STYX
This project is sponsored by NIA, Baker-Koob, Capstan, and MESFAC
Count down to Competition
Meet the team
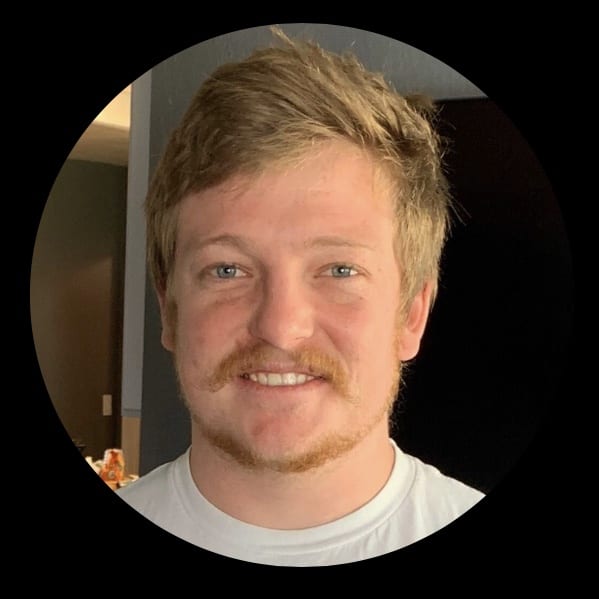
Aaron Ericson
I’m Aaron Ericson and I’m the Structures, Programming, and Controls lead for the STYX team. I’m a fourth year mechanical engineering student with a concentration in mechatronics. Additionally, I have work experience in conceptual design, subsystems, and mechanical part design in the aerospace industry.
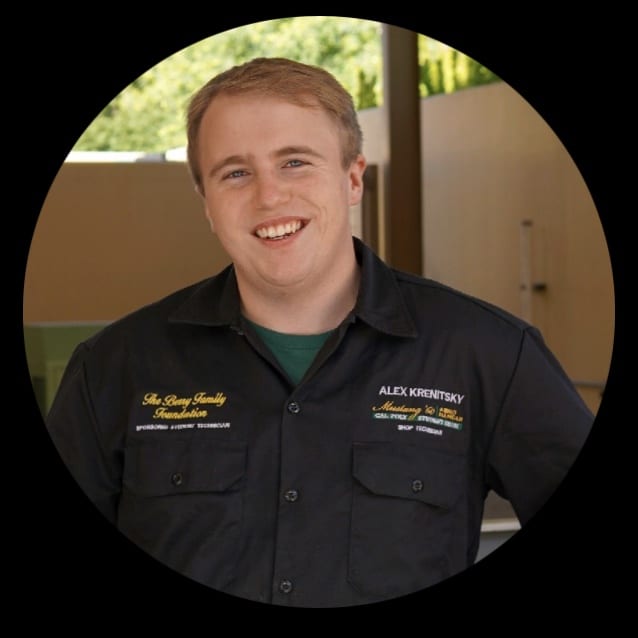
Alex Krenitsky
My name is Alex Krenitsky and I am the Thermal Systems, Linear Motion, and Tooling Lead. I am a fifth year mechanical engineering student pursuing my Bachelors’ and Masters’ degrees. I have work experience via several civil construction and aerospace internships and I work on campus as a lead shop tech for Cal Poly’s Mustang ’60 machine shop.
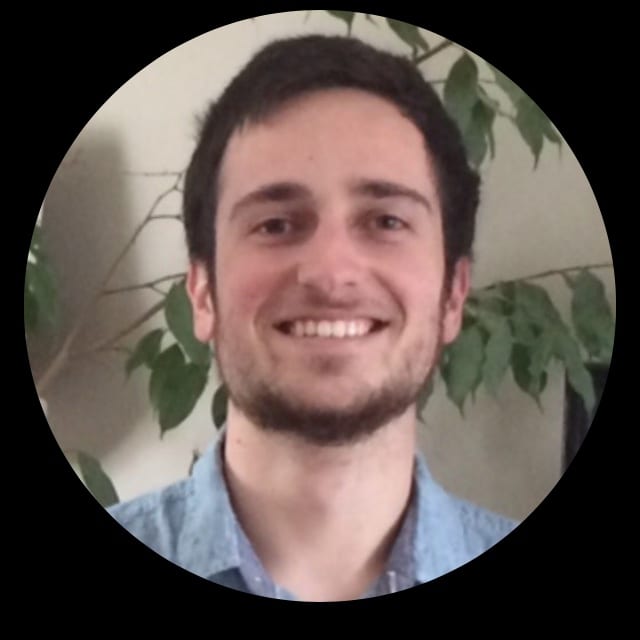
Ryan Locatelli
My name is Ryan Locatelli and I am fourth year mechanical engineering student. I am the Manufacturing Lead and Water Processing Design Lead. I am also involved in the design of the tool changer. I have work experience in the wastewater treatment industry.
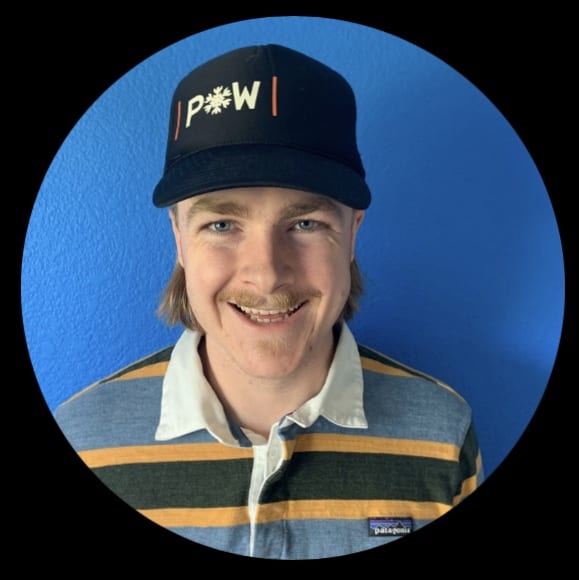
Chris Boone
My name is Chris Boone and I am the Telemetry Systems, Outreach and Documentation Lead. I am a fifth year mechanical engineering student graduating this year and continuing on to grad school for education. I have work experience with both autonomous flight and RF systems.
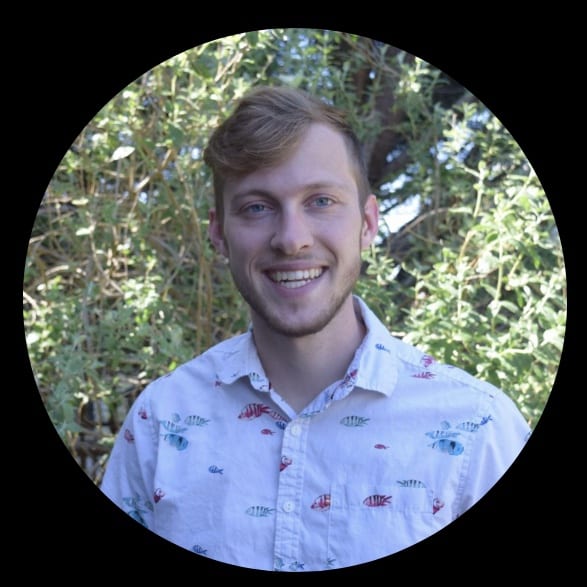
Westin McHaney
My name is Westin McHaney I’m the the Webmaster and provide manufacturing support. I am a fifth year mechanical engineering student with a concentration in energy resources graduating this year. I have work experience in prototyping and product design through internships in the music and water sports industries.
Project Poster
list of Project Requirements
Collect subsurface layer data and extract liquid water from subsurface ice deposits via a robotic platform in simulated Martian conditions provided by NASA.
Main Specifications:
- Max Weight: 60 kg (132 lbs)
- Max Power: 9A, 120VAC
- Max Dimensions: 1m x 1m x 2m
- Max Downward Applied Force: 150 N
- Provide: Regolith Layer Thickness Data
- Provide: Regolith Layer Hardness Data
- Provide: Maximum Possible Quantity and Clarity of Liquid Water
- Recommended: Autonomous Operation
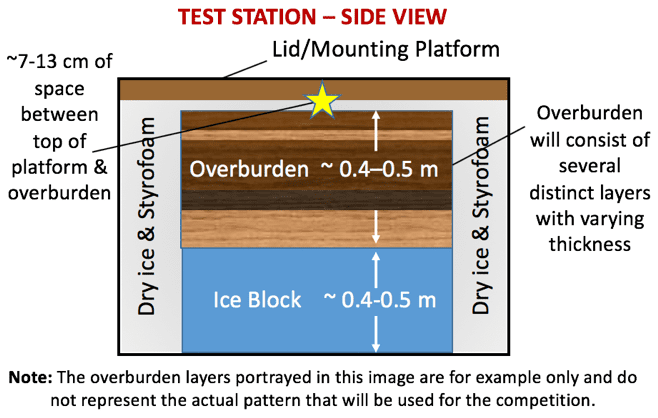
Design Process
Ideation methods like brainstorming and concept sketching were combined with prioritization and decision-making strategies like functional decomposition and weighted decision matrices to drive the final design.
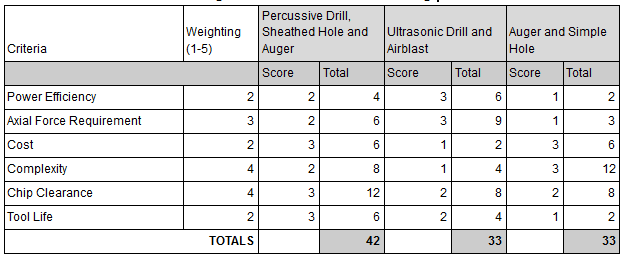
Design Concept / Preliminary Testing
One of the first choices to make was the penetration method. While conventional drilling and ultrasonic drilling methods were considered, hammer drilling was decided as the path forward.
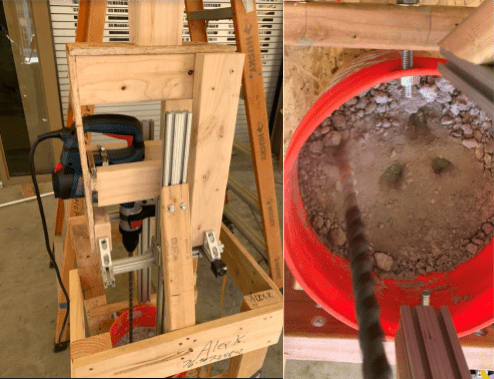
A preliminary test using a wooden frame prototype was conducted to ensure that hammer drilling would be effective with the restriction on downward applied force. This test exceeded our expectations for penetration rate. Through this testing we also found that clearing debris from the drilled hole would be a significant challenge.
Final Design Path
The characteristics of the final prototype were chosen to be:
- Aluminum tube frame
- 2 axes of motion
- 3-step, 3-tool drilling process
- Hammer drill
- Insert sheath
- Auger debris
- Hammer drill for prospecting
- Camera probe for telemetry
- Actuating heater probe
- Rotating tool rack
- Two-stage water filtration
- Control via Nucleo w/ Micropython
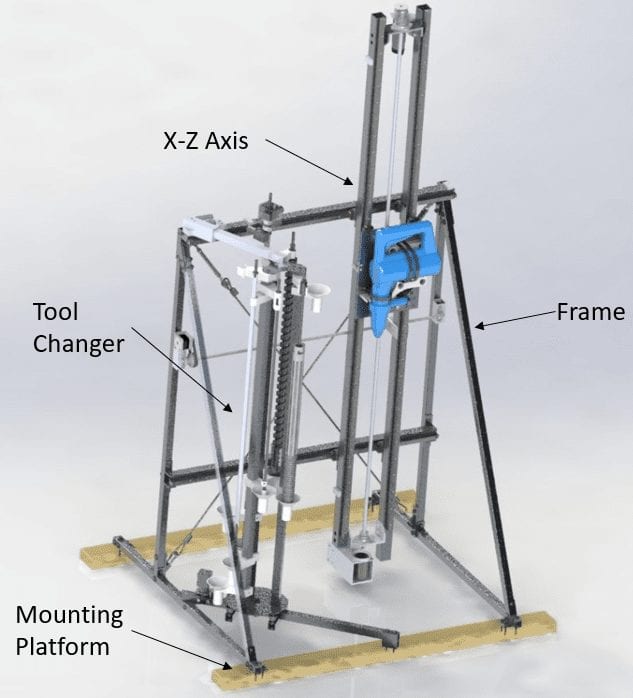
Analysis
Frame Analysis
Matlab calculations for buckling, compressive stress, and bending stress were conducted for all significant members of the frame. This calculation was completed for several square and rectangle profile dimensions and was plotted as a surface to aid with sizing critical members.
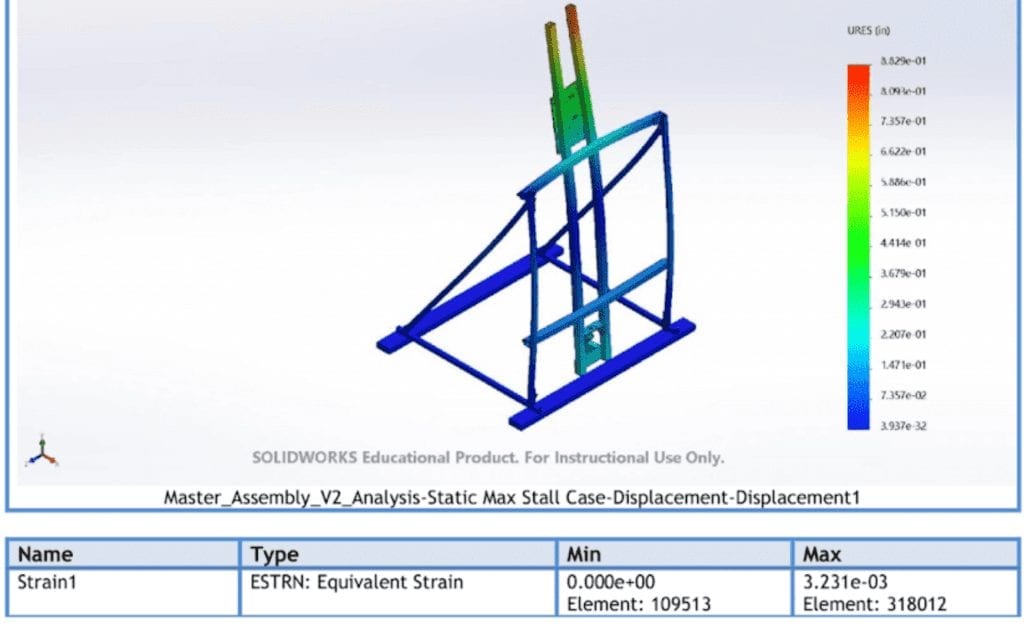
FEA was used to estimate deflections and to ensure smaller details were captured in the analysis. The primary load case was selected to be as conservative as possible with a F.S of 1.5 on the worst load case.
Sheath and Sheath tool analysis
A worst case loading condition was used to check stress and deflections via FEA.
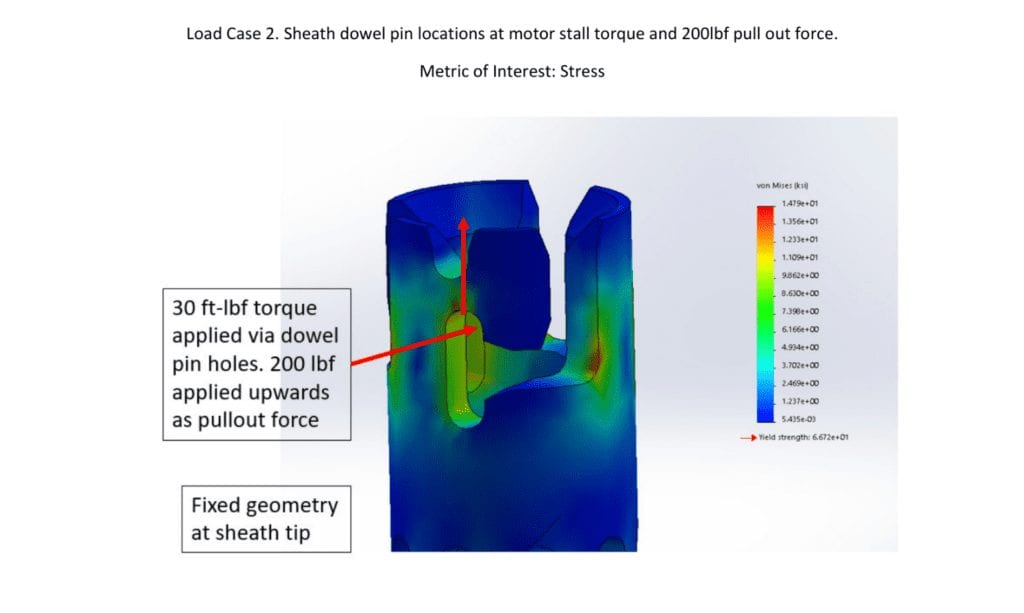
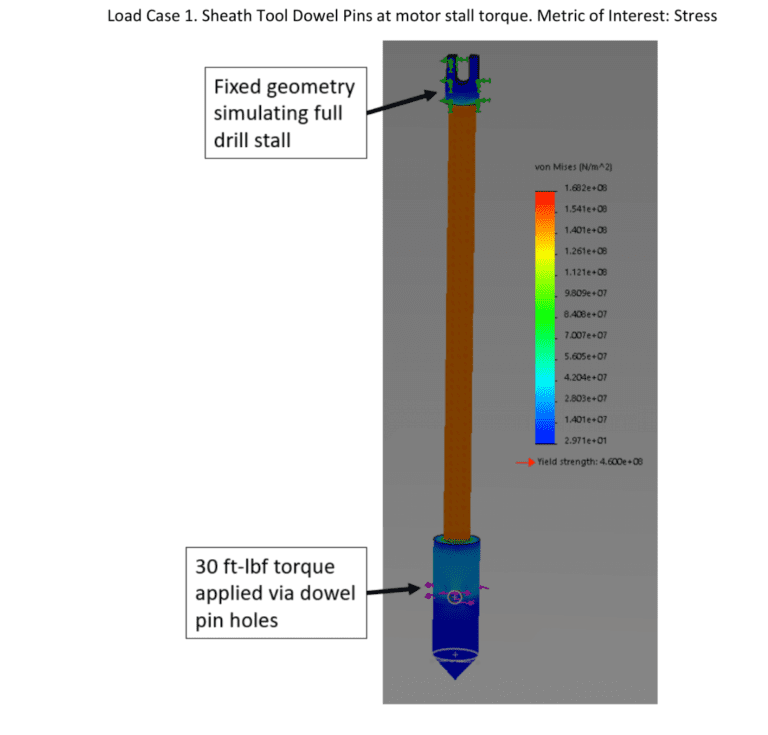
Heater Probe analysis
The maximum melt rate of the 1000W heater tip was calculated to be ~140ml/min in an ideal scenario. The heater tip actuation is designed to stall in the fully open and fully closed positions for simplicity. This requires the actuation motor and the heater probe components to withstand these loads without excessive stress or deflection. MATLAB calculations were performed for the actuation string, shaft bending, and motor. More complex interactions, such as the square axle and copper tip interactions were modeled using FEA.
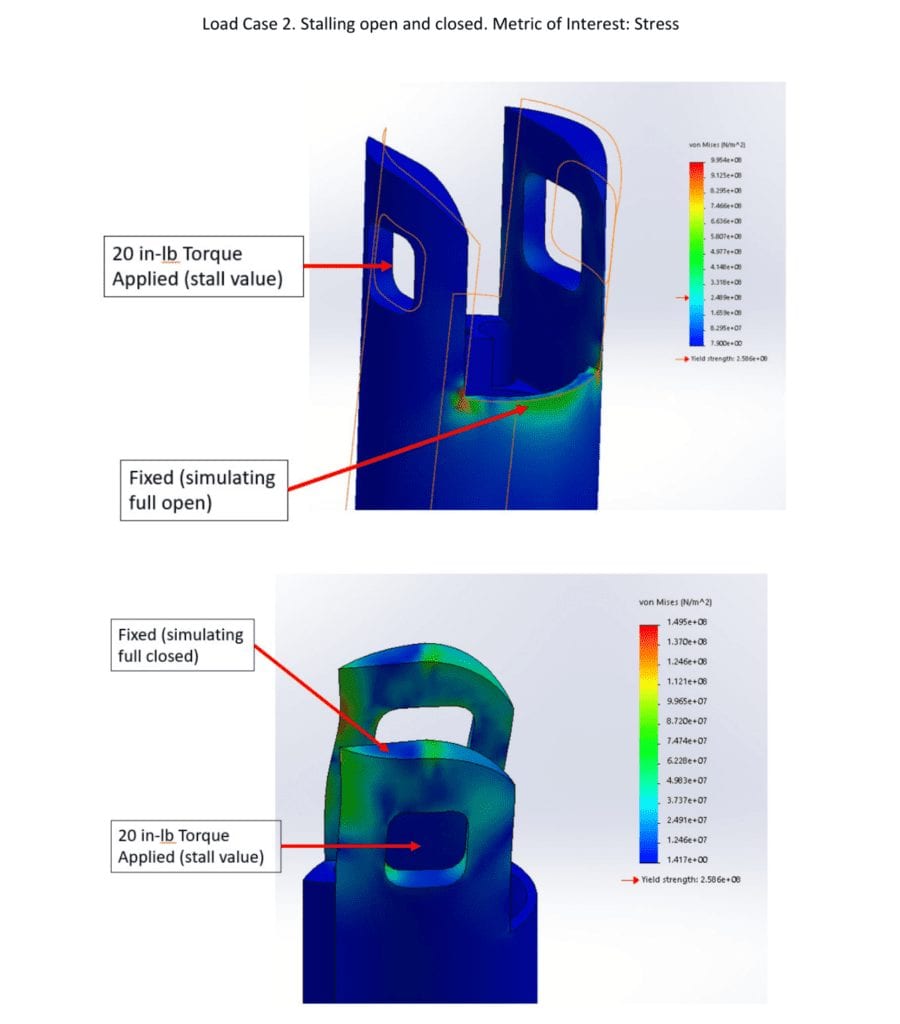
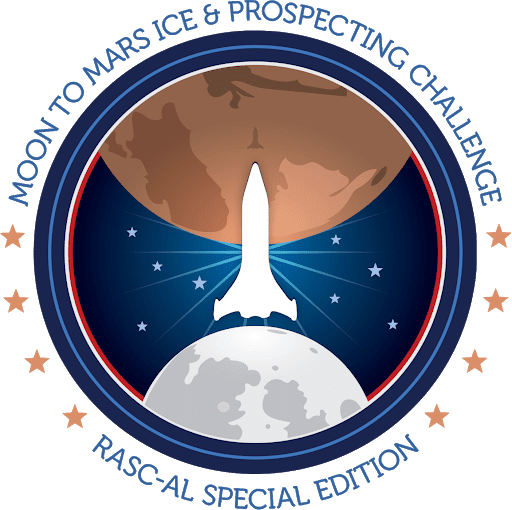
STYX
This project is sponsored by NIA, Baker-Koob, Capstan, and MESFAC
Subsystems
Frame
The frame is made of thin wall aluminum selected to be the largest size tube for the thinnest wall thickness in the pursuit of stiffness. Bolted connections alleviate the need for difficult welds and allows the frame to be disassembled for easier transport to competition. Pretensioned cable stabilization stiffens the frame and increases shear load acceptance, while reducing the weight.
X-Z Motion
The linear motion system is divisible into actuation and load carrying. Integrated into the linear motion system is the force gauge portion of the telemetry system. To measure downwards force accurately, and reduce spikes in data caused by hammering, a dual spring-damper load cell arrangement is being used. To actuate the x-axis an open loop stepper driver drives a lead screw. The z-axis uses a DC servo motor with an encoder to drive a lead screw.
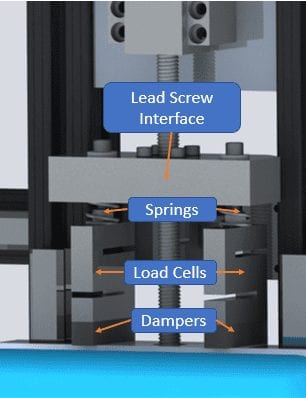
Filtration System
The water processing system was designed to extract liquid water from below the regolith, remove impurities, and deliver water to a holding tank.
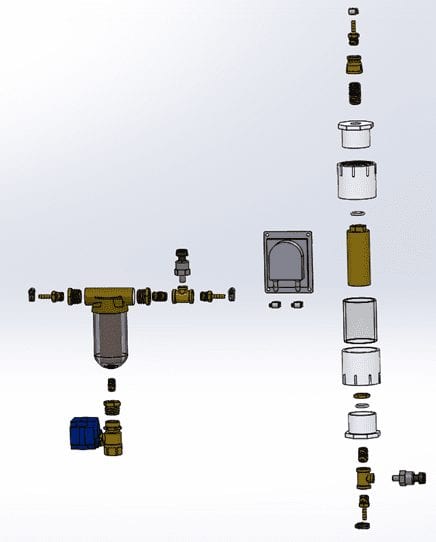
The main components within this subsystem are:
- Self priming peristaltic pump to pull water from the sub surface ice layer
- Sediment trap to capture large solids
- 40 micron pre-filter to alleviate fouling of secondary filter
- Motorized ball valve to empty sediment trap accumulation
- Capstan 5 micron sintered bronze filter*
- Pressure transducers to monitor flow
Programming/Controls
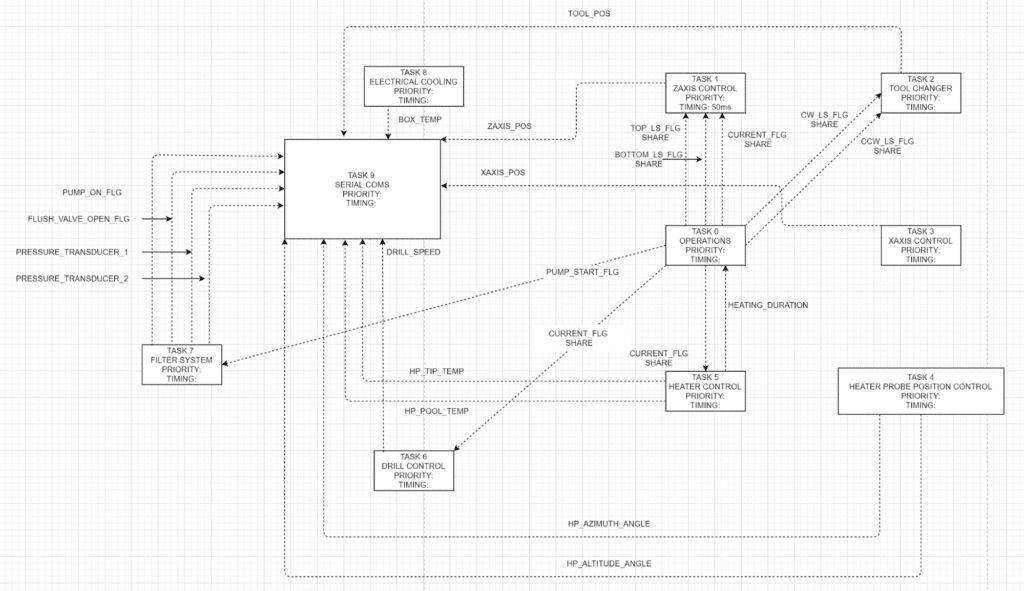
The programming is being completed on micropython and the microprocessor being used is the NUCLEO L476RG. The prototype requires that many closed loop operations be running simultaneously: such as closed loop position control with encoders, closed loop load control with the load cells, and closed loop heater control with the thermocouple. To achieve the functionality of closed loop operation and also be able to issue commands in a procedural fashion, a task scheduler and operations tasks were implemented.
Electronics
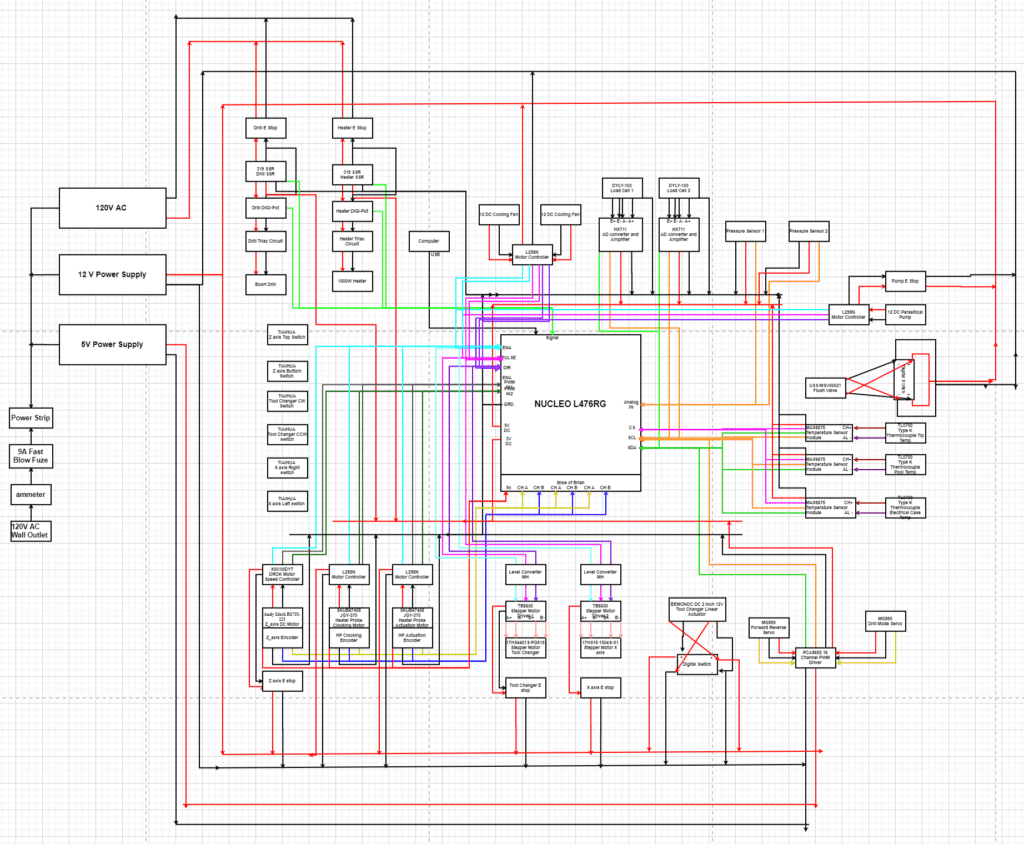
Components of the Electronics Subsystem
- 120V AC -used to power the drill and the heating element
- 12V DC -used to power the actuation motors and peristaltic pump
- 5V DC – used to power micro controller and servos.
Tool Changer
A rotary tool changer allows 5 tools to be swapped autonomously to the hammer drill. Precision, repeatability, and deflection are critical metrics to ensure reliability. MATLAB calculations showed that geared stepper motors would provide the necessary positional accuracy. Preliminary testing showed that both top and bottom supports would be required to achieve the minimal deflection.
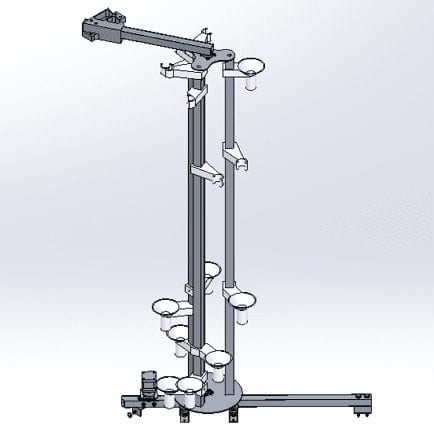
Tools
Hammer Drill


The initial hole that is drilled to reach ice is performed using a 1.5” masonry drill bit. The magnetic floating collar interfaces with the frame to increase drilling stability. This drill bit operates in a rotary-percussive manner. The hammering action provided by the Bosch rotary hammer drill ensures that no large solid pieces will be left inside of the hole when the drill bit is extracted.
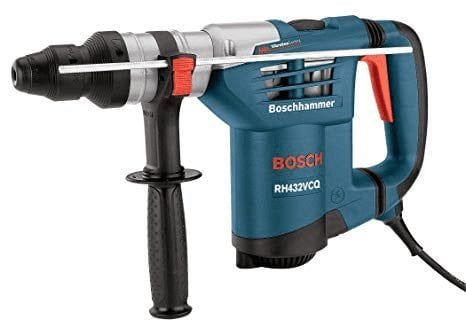
Sheath and Sheath Tool
After the preliminary hole is drilled, the sheath is removed from the tool changer and hammered into the hole to prevent soft under burden layers from filling the hole. Spinning the drill allows the sheath tool to engage and disengage with the sheath. The sheath is left in the hole while the sheath tool is placed back into the tool changer.
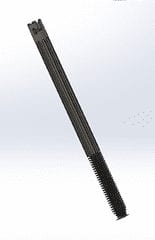
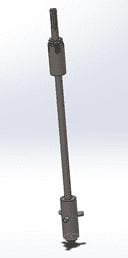
Features on the sheath include:
- Slots that allow the tool to be lifted out of the hole
- Fins that constrain the tool from rotating in the hole while being cleared out
- Exterior threads that constrain the tool vertically in loose regolith
- Holes that allow the camera probe to view the regolith layers
Tools Continued
Auger
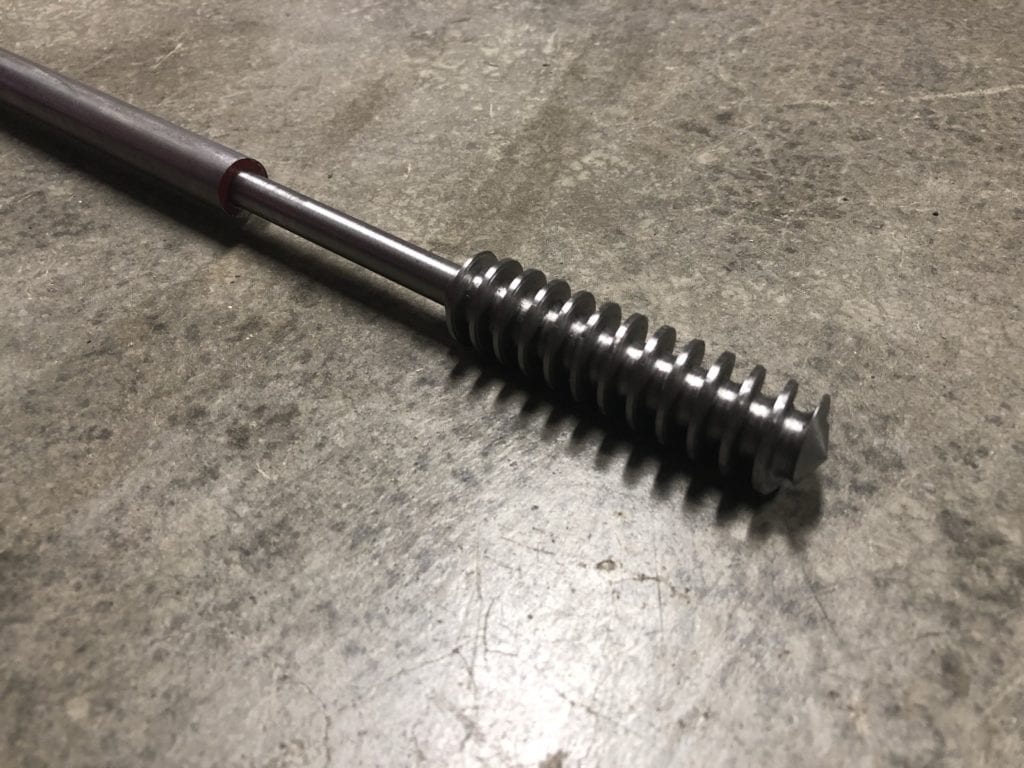
The auger is used to clear the sheath of any remaining regolith. This will ensure that the heater probe will have direct contact with ice, and minimize the amount of water contamination when the ice is melted.
Heater Probe
The heater probe contains a heating element used to melt the ice and a tube through which water is extracted. The heater probe is lowered down the sheath where it is powered on and begins its plunge into the ice. Once it reaches its target depth, the copper heating tip is actuated outwards. It can then be simultaneously spun in a circle while plunging downwards, creating a 14” diameter cylindrical melting pattern.
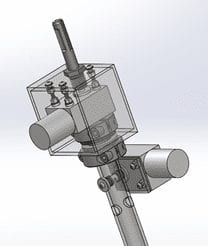


Camera Probe
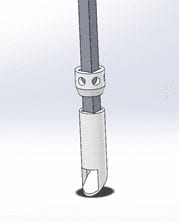
The camera probe is used as a means of confirming data regarding regolith composition. A wireless camera probe is inserted into the sheathed hole. The sheath has a set of holes drilled down its length that allow the camera to view the material along the entire depth of the drilled hole.
Design Verification Prototype
To satisfy NASA’s mid-point review requirement, a mostly integrated test demonstrating penetrating capability was required. The video below contains footage of that test along with many other points of progress that NASA was interested in. The drilling test shows effective penetration of concrete, dirt, sand, and ice. The rest of the video demonstrates linear motion actuation, tool loading, heater probe prototyping, and water pumping/filtration.
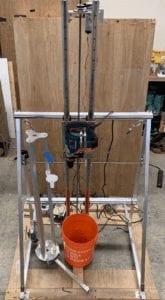
The results of this testing on the partially completed prototype netted the following results:
- Vibration requires lock nuts everywhere
- Tool changer requires additional support to prevent deflection
- Alignment of linear rails is necessary to provide quality load cell data
- Frame design is adequate – Very little deflection observed
Current Status and Recommendations
Construction of the prototype is continuing at our respective homes due to COVID-19 restrictions. Ryan Locatelli is managing manufacturing. Alex Krenitsky is responsible for integration. Aaron is developing programming and electronics. Chris developed plans for a test bed and is working with Westin on documentation.
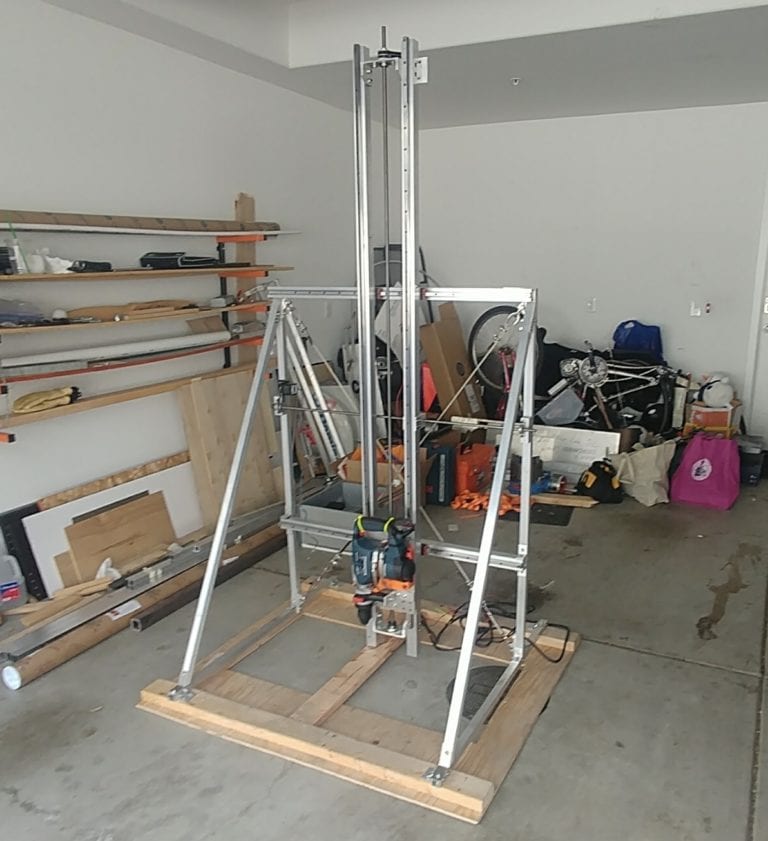
Full integration and testing is expected in the month of August, with competition following immediately after. Following competition, the project will be returned to Cal Poly for the potential of future senior project use.
Although no complete system testing has occurred yet, the major findings from this prototype are:
- Tool access for assembly is important
- Having multiple tools increases complexity greatly
- Wire routing is not simple
- Plan for contingencies, both engineering and logistical
- Future teams recommended to focus on improving a few subsystems instead of building from scratch
- Off the shelf parts wherever possible saved a lot of time
NASA submissions
Mid Point Review Video
This video report was sent to NASA, to show show that we are making progress on the build of our robot, and are including all the systems that we specified in the Project Plan. This video along with the Mid Project Review was sent to NASA and guaranteed us one of the 10 competition spots. The Mid Point Review video discusses our solutions for the programming, control, motion, water-collection, and test-bed mounting.