Our Team
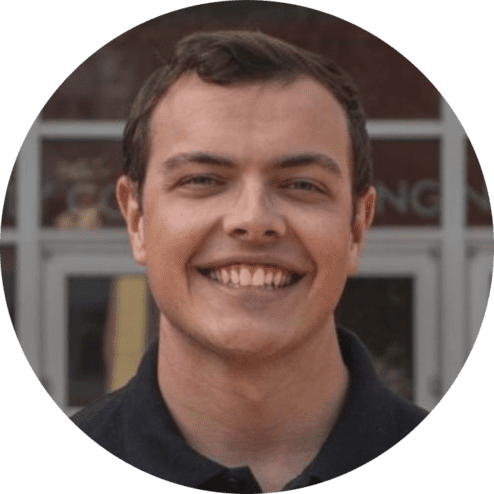
bailey groh
Bailey is a enrolled in the mechanical engineering blended BS/MS program with an expected graduation date of June 2021. His interests include mechatronics, controls, and software.
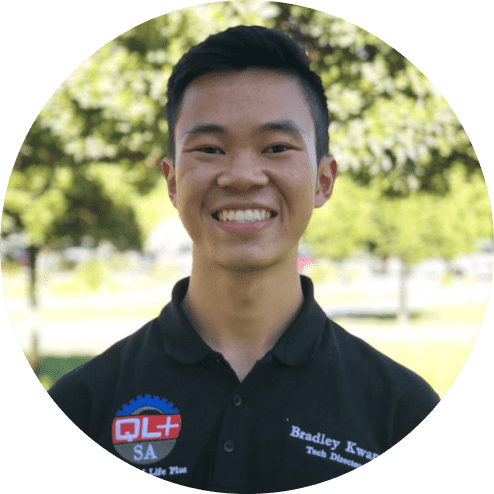
bradley kwan
Bradley is a mechanical engineering student enrolled in the blended BS/MS program with an expected graduation date of June 2021. His interests include design of electro-mechanical systems and computer modeling of systems.
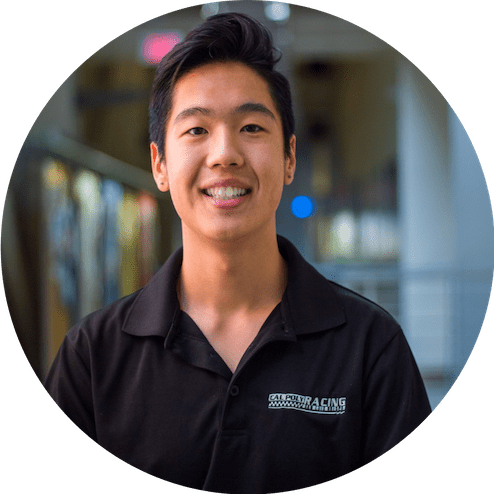
max wu
Max is a mechanical engineering student planning on graduating June 2021. He is involved in Formula SAE as one of the team’s technical directors. His main fields of interest are in autonomous/electric vehicles and other forms of consumer electronics.
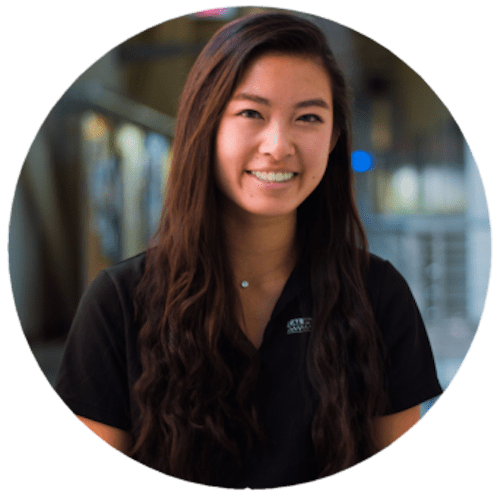
nicole yen
Nicole is a mechanical engineering student graduating in December 2020. Her interests include design for manufacturing in the field of consumer electronics.
Acknowledgements
Thank you to everyone who helped us with our project. We would like to give a special thanks to Kevin Ziemann, Austin Fisher, Henrique Chan, Peter Schuster, Siyuan Xing, Xi Wu, Bill Murray, Larry Coolidge, and Ben Carr.
Our Project Videos
Our Project's Digital Poster
Problem Statement
Develop a two-stage damping system that primarily utilizes viscoelastic material (VEM) to provide damping and structurally support a satellite payload. Multiple mounts can be used to support a single payload.
Design Constraints
- Thermal
- Operational: 10°C to 30°C
- Survivable: -30°C to 70°C
- Outgassing: <1% TML
- Mass: < 1lb per pedestal
- Quasi-static Loading
- Launch Frequency >50 Hz: 20 g
- Launch Frequency <50 Hz: 40 g
- Launch
- Target Frequency: 35-75 Hz
- Transmissibility: <4
- Orbit
- Target Frequency: 10-20 Hz
- Transmissibility: <2
Background
Previous senior project
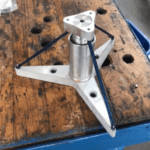
A senior project was completed last year dedicated to designing a single stage vibration isolator for satellites. As part of their project, they chose to design a passive vibration damping system using viscoelastic material. The result of the project was selection of an ideal viscoelastic material, the one used for our project, and a pedestal design that failed to fulfill the transmissibility requirements of their project.
Viscoelastic materials
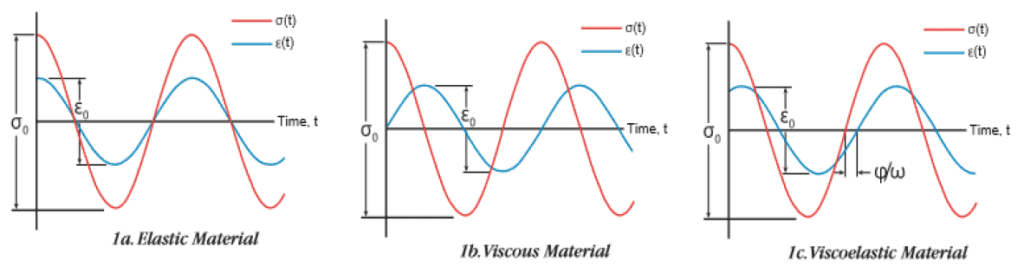
An elastic material follows Hooke’s Law where the stress is proportional to the strain and the elastic modulus is defined as the ratio of stress to strain. On the contrary, a viscous material does not return any energy stored during loading. Stress is proportional to the rate of strain for viscous materials. A material that shares both the properties of an elastic material and viscous material is called a viscoelastic material (VEM). These materials dissipate energy through shear deformation. The stiffness and damping properties of a viscoelastic material are commonly a function of several parameters, including frequency, temperature, dynamic strain rate, static preload, creep, relaxation, and aging.
Early Design Concepts
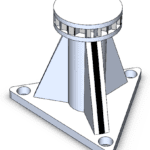
Issues
- High stiffness
- No damping in vertical axis
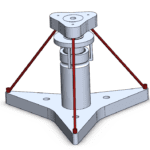
Issues
- Two stage contacts and parallel load paths fail under quasi-static loading
SPONSORED BY
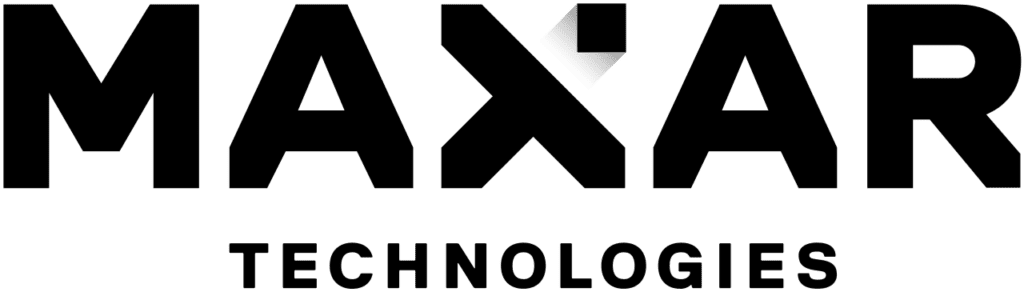
Final Design
Specifications
Weight: 1 lb per pedestal
Orbit Natural Frequency: 14 Hz
Launch Natural Frequency: 54 Hz
Orbit Transmissibility: 4
Launch Transmissibility: 16
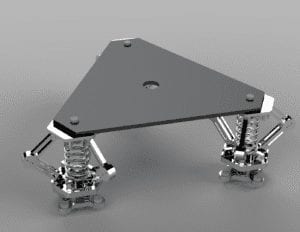
Key Features
- Passive two-stage damping
- Parallel load path to prevent creep
- Rotating linkages with potted VEM
- Modular design: Up to 6 linkages supported
Materials
- 6061 Aluminum
- Lightweight
- Machinable
- G-10 Garolite
- Impact Resistant
- Machinable
- Viscoelastic Material
Conclusion
- We were unable to manufacture or test the pedestal design due to COVID-19. According to our analysis, the final design met the majority of the requirements for the project. Using the specified viscoelastic material, the vibration isolation pedestal met the mass, two-stage frequency, and quasi-static requirements. Unfortunately, the final design failed to achieve the transmissibility goals for the project. The viscoelastic material was extremely stiff which made it difficult to simultaneously achieve the damping and stiffness requirements of the project.
Recommendations:
- Select a viscoelastic material with a lower stiffness for the design
- Include viscoelastic material in the lower section of the pedestal with very high strain energy density in orbit conditions
- Modify the upper section of the pedestal to remove the nonlinearity of the rotational joints which makes analyzing the system complicated
- Manufacture the pedestals
- Complete vibration, strength, and offload testing using the detailed test plans
- Using the test results, verify the accuracy of analysis tools and make any necessary changes
- Redesign pedestals with new viscoelastic material
Simscape Analysis
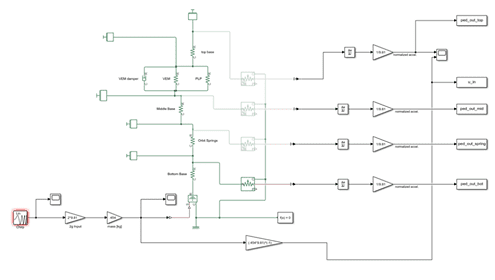
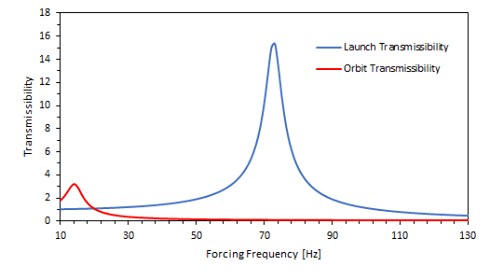
A Matlab Simscape model was constructed for analyzing the damping and natural frequency of the system. This analysis guided our detail design of components by determining the overall system stiffness and possible configurations for individual part stiffness.
Finite Element Analysis
Modal
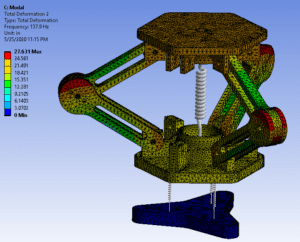
Modal analysis performed on overall structure in launch and orbit configurations for analysis of strain energy density and verification of natural frequency. Excitation mode of the VEM joints was the main area of focus as most damping occurs at this mode.
Structural
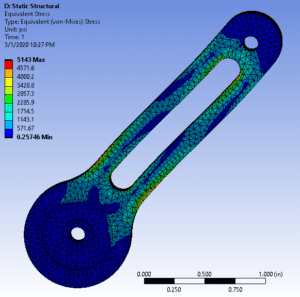
Structural analysis performed on individual components to assess failure under maximum loading conditions. Loading cases included a 20g quasi-static load or 32g vertical acceleration at max transmissibility.
Testing
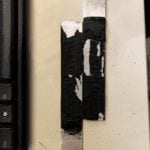
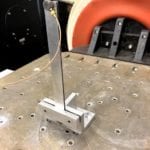
Viscoelastic Material Characterization
We performed a variety of tests to characterize the material properties of the viscoelastic material. A cantilever beam vibration test was performed on a shake table to characterize the vibration damping properties of the VEM following the ASTM E756 standard. A shear strength test was performed on an Instron using a lap joint.
Orbit and Launch Vibration Test
We planned to verify the natural frequency and transmissibility requirements for the damping system by utilizing a vibration table. The tests would consist of a 2g sine sweep from 5-200 Hz for the orbit test and an 8g sine sweep from 5-200 Hz for the launch test with accelerometers measuring at the center of the simulated payload.
Quasi-static Strength Test
We planned to verify the quasi-static requirements for the damping system by utilizing testing fixtures to hang weights from the center of gravity of the system in the x, y, and z axis.
Offloading Test
We planned to test the effect of uneven loading on the system by constraining one of the pedestals into the fully contacted, launch condition and performing the same quasi-static tests.