Our Team
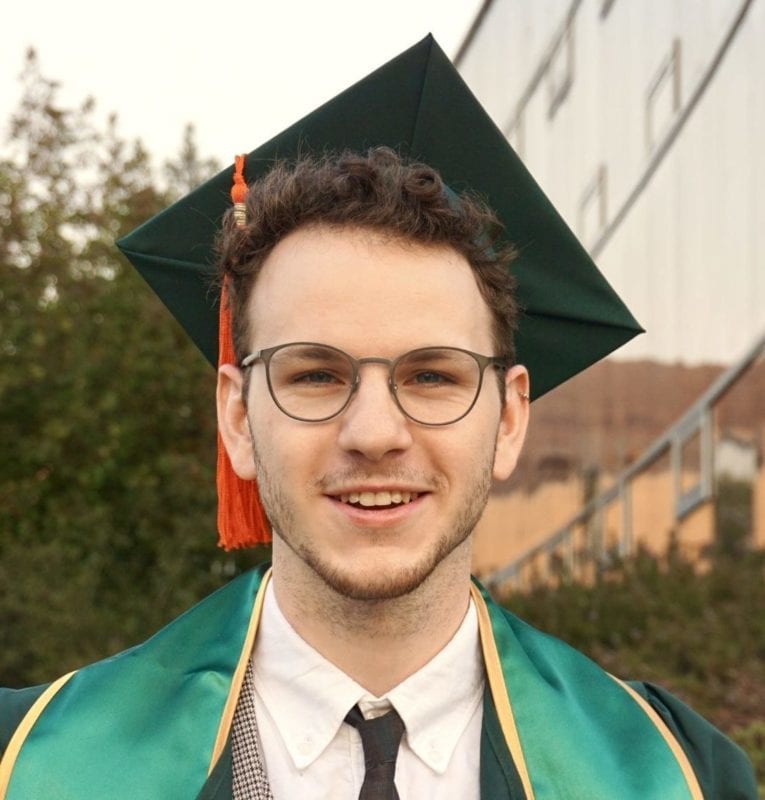
Henry Terrell
Communication/planner
I am studying mechanical engineering with a concentration in manufacturing. Activities I enjoy are hiking, snowboarding and reading. I was very excited to design the housing of the robotic leg, and learn many new skills along the way.
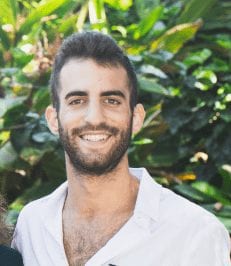
Oded Tzori
Secretary
I am studying mechanical engineering with a concentration in engineering resources. I was eager to design and build this leg because I am driven by project organization and completion. In my personal time I enjoy playing music and the outdoors.
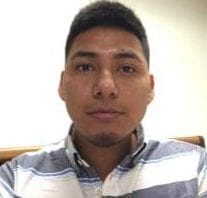
Adan Martinez-Cruz
Treasurer
I am studying mechanical engineering with a concentration in mechatronics. I could not wait to learn to apply things I learned in my mechatronics classes to this project. Outside of school I like to clean and stay organized, and watch Netflix.
Team Capy's Digital Poster
Project Summary
The Cal Poly Mechatronics Department does not have a quadruped robot to use for research and teaching. Professor Xing proposed the project to build a 2 Degree of Freedom robotic leg that can accurately jump 10 cm. The ‘hip’ will be attached to a stand and only be allowed to move vertically. Team Capy was tasked with taking Cal Poly’s first step into the race for quadruped technology by building the functioning robotic leg and its stand.
Scope of Work
- Design and build a 2 Degree of Freedom robotic leg
- Leg must be able to jump accurately and make a kicking motion
- Design and build a test stand for the leg
- Use pre-designated motors
Concept Design
- belt drive
- 4 bar linkage
- gear track & lever arm
Brainstormed ideas for test stand design:
- 2 guide wires
- diamond track with bearings
- pole with keyway
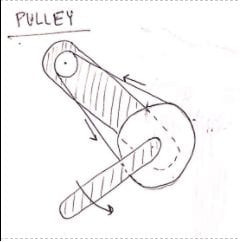
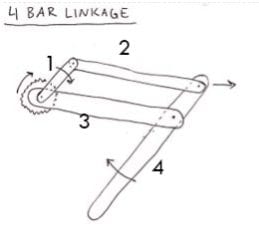
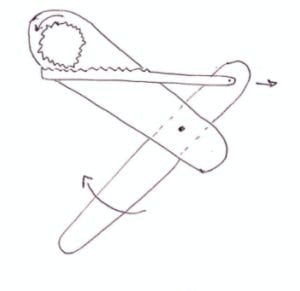
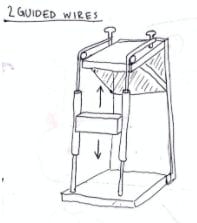
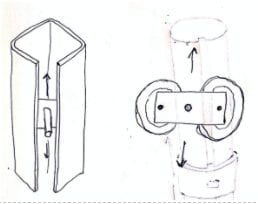
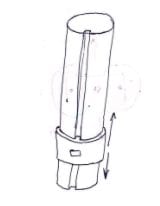
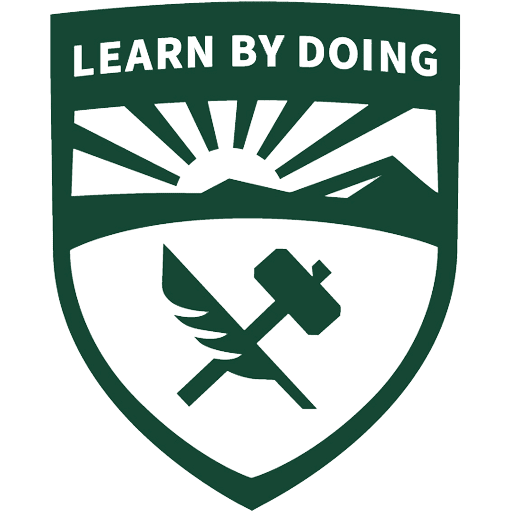
This project is sponsored by the Mechatronics and Controls Departments at Cal Poly, San Luis Obispo.
Final Design
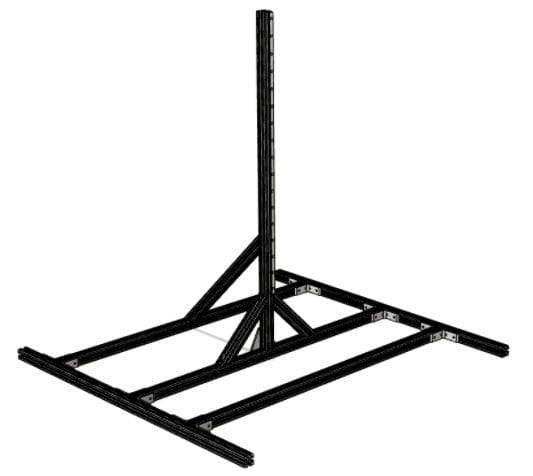
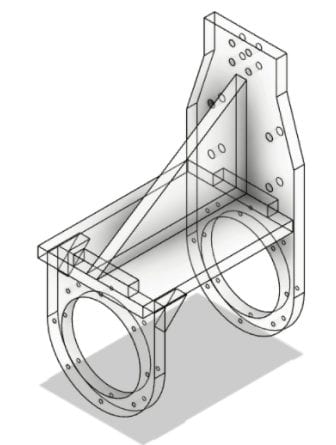
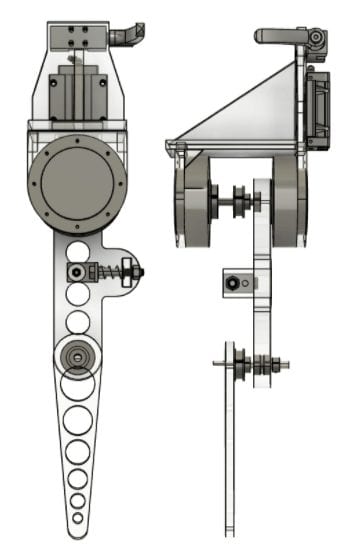
Fabrication
The drawings below are of all the parts that were fabricated.
The parts for the motor casing, as well as the upper and lower leg were cut using the waterjet. The shaft was connected by a weld to the base steel plate. The landing pad was cut using a circular saw.
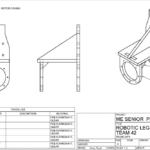
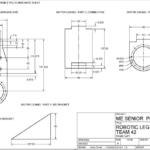
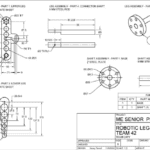
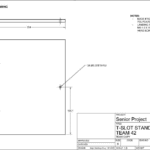
Stock Parts
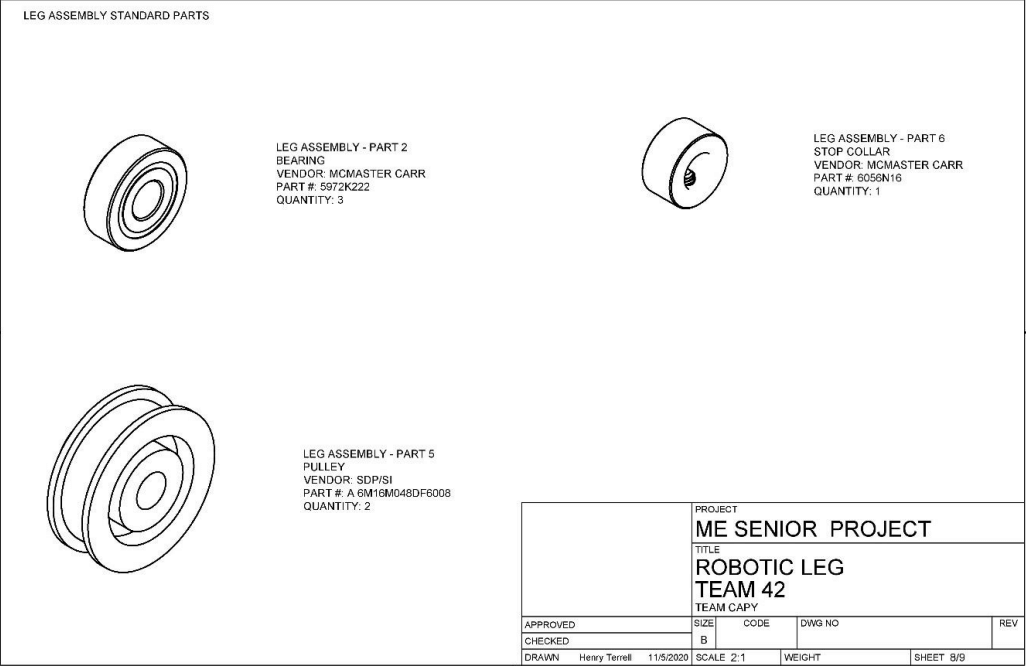
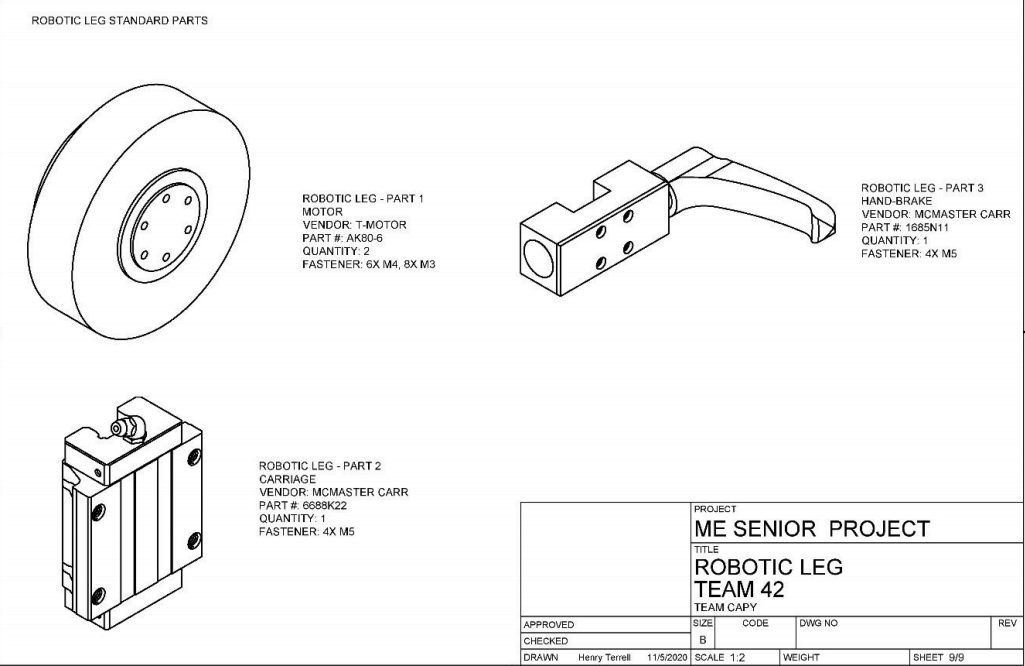
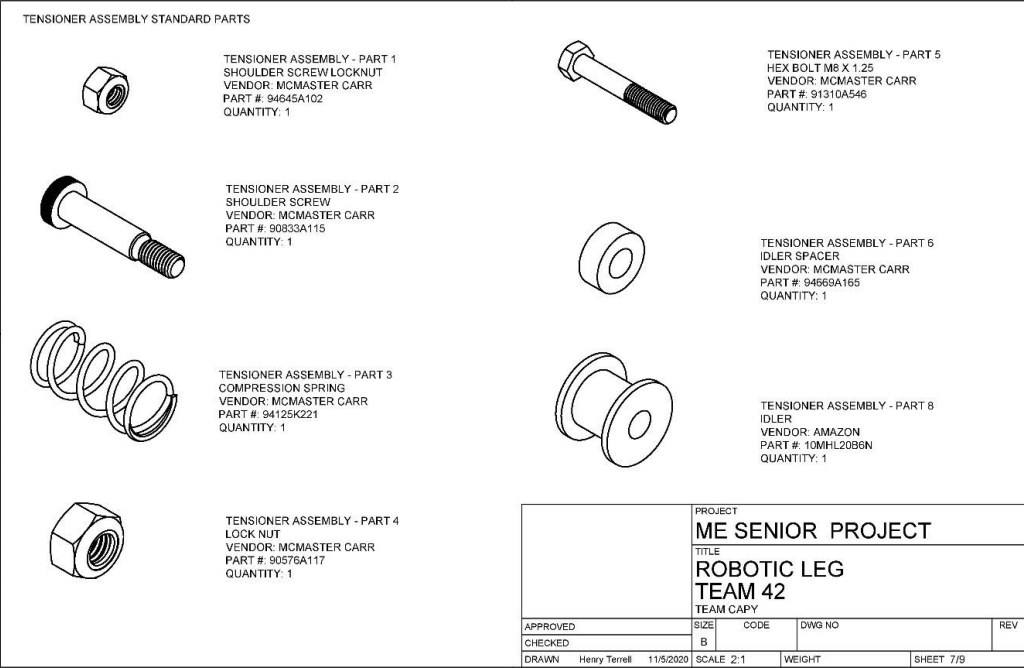
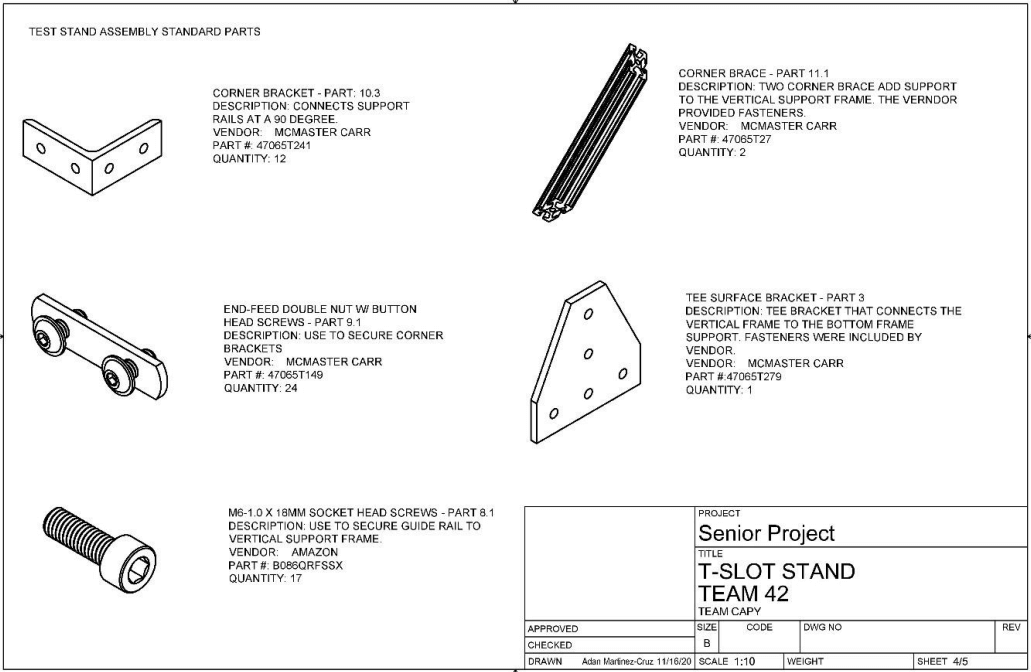
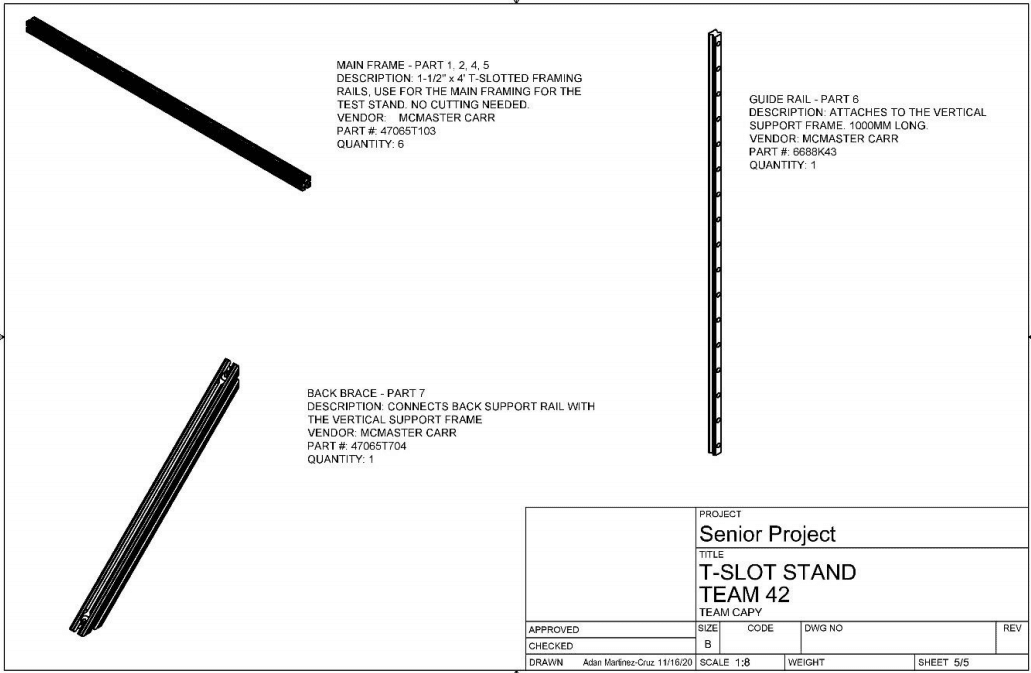
Full Assembly
Fabricated Components
- Motor Casing
- Upper Leg
- Lower Leg
- Shaft
- Steel Base
- Landing Pad
Stock Components
- 8020 Frame Parts
- Guide Rail & Carriage
- Motors
- Pulleys & Belt
- Tensioner Parts
- Bearing & Stop Collar
Next Steps
Team Capy accomplished the first stage of many before the greater goal of a quadruped robot is achieved. A senior project that started in Spring 2020 at Cal Poly is focusing on writing the controls simulation for the motors, and will be taking over. There will be a quadruped robot at Cal Poly within the next 4-5 years!
Recommendations
Recommended safety measures to be taken
It is recommended for the next group to design and utilize an acrylic casing that will surround the entire leg and test stand during testing. The acrylic casing have a switch, where unless the casing is in place, the leg can not operate. This is to ensure that no fingers can be pinched, or electrocutions occur during operation.
Recommended motion analysis methods
The next steps include analyzing the motion capable and achieved from a control simulation, and improving it. There are two methods Team Capy recommends for analyzing motion.
1) Using a modern phone camera to capture slow-motion footage against a linear background is a cheap, tedious way to calculate the velocity and acceleration vectors of the legs.
2) Utilizing non-contact encoders is the expensive, easy and accurate method to ensure rapid and iterative data collection.
Acknowledgements
This senior project was sponsored by Siyuan Xing, a Professor in the Controls Department at Cal Poly, SLO.
Special thank you to Simon, Charlie, and Lee.