Our Team
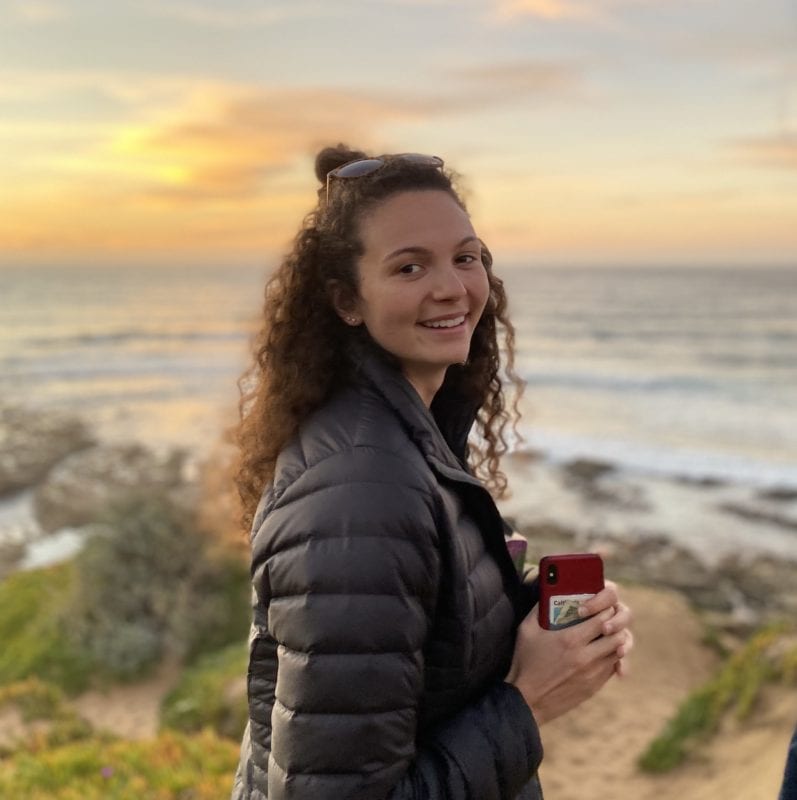
Thaïs Bertolus
I’m a mechanical engineering student from the San Francisco Bay Area. I chose this project because I wanted to improve my mechanical design skills and be involved in a project that improves people’s day to day lives. When not in school, I enjoy doing anything active and being outdoors!
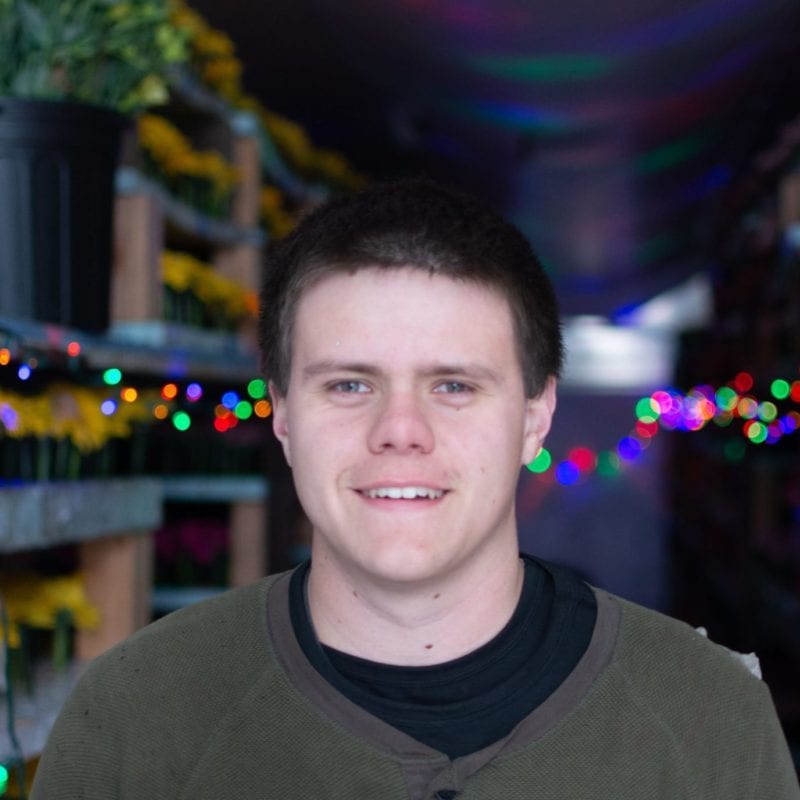
Jarod
Kinney
I am a mechanical engineering student with an emphasis in mechatronics. I chose this project because I wanted to see and be a part of developing and implementing a manufacturing process from start to finish. I am also a part of the Cal Poly Rose Float program doing structural and mechanical work for the float.
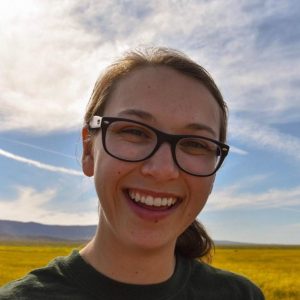
Alexa
Steidl
I am a mechanical engineering undergraduate pursuing a master’s in industrial engineering. This project piqued my curiosity due to both the mechanical and manufacturing design. When I am not doing school work, I enjoy skating, hacky-sacking, and watching sunsets.
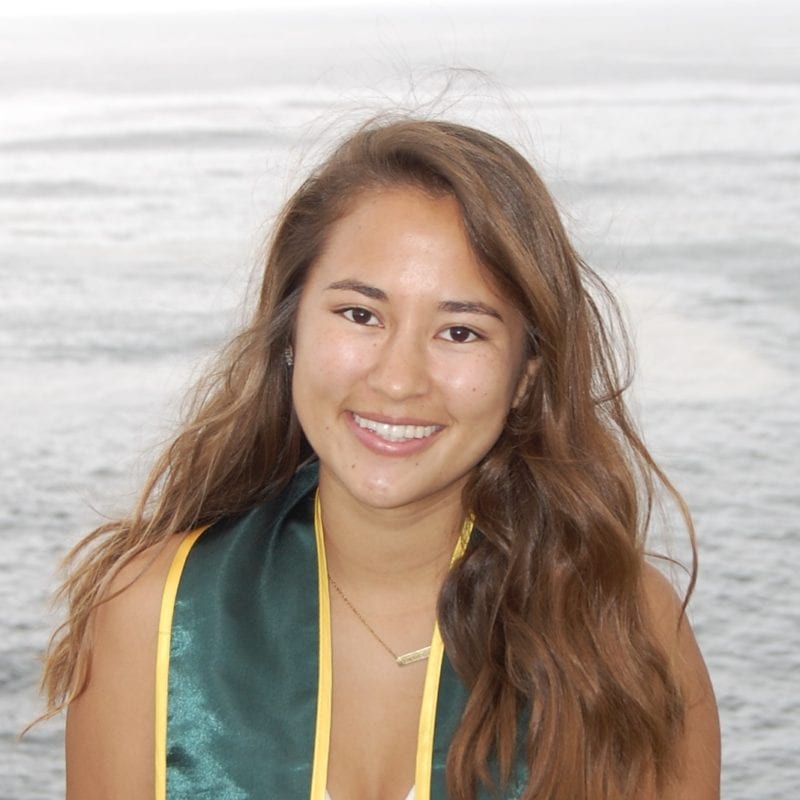
Hana
Welsh
I am a mechanical engineering student with an emphasis in manufacturing. I chose to work on this project so I could develop my skills and professional experience with both mechanical and manufacturing design. Outside of academics, I run for Cal Poly’s Track & Field team and enjoy being outdoors and traveling.
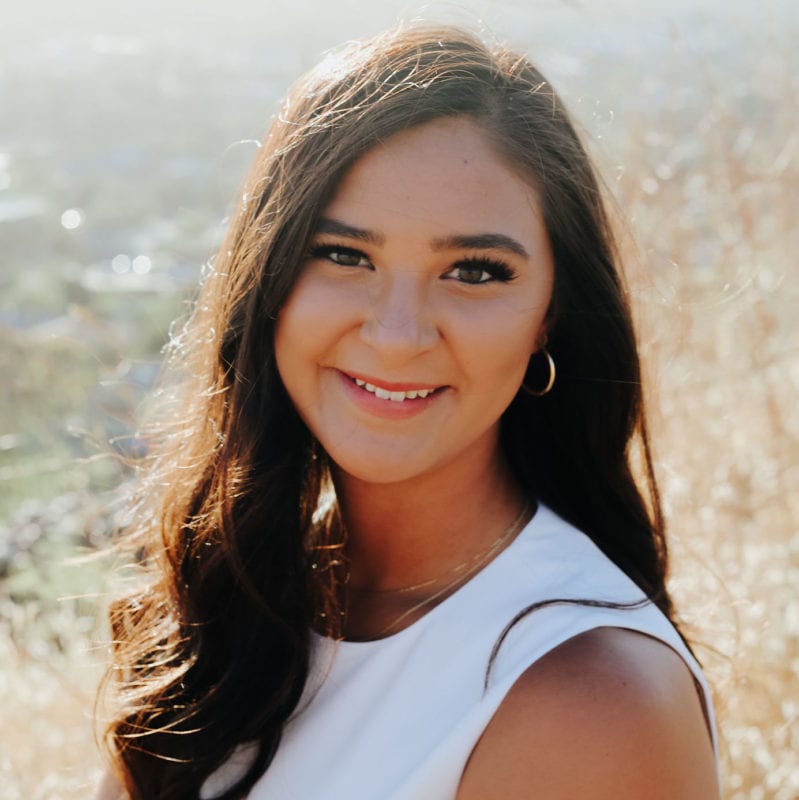
Maya Willis
I am a mechanical engineering student originally from Palos Verdes, CA. This project interested me because of the technical and communication development skills that come with working with people who are not familiar with the engineering world. Outside of school, I enjoy rock climbing and working with children.
Acknowledgements
We would like to thank our senior project advisor, Professor Lee McFarland for all of the wisdom and guidance he has given us throughout the completion of this project.
We would also like to give thanks to our project sponsors Sally Moyer and Carrie Vickerman at A.C. Moyer Company for being so supportive and understanding despite the unprecedented uncertainty of the project and its completion.
Our Project's Videos
Our Project's Digital Poster
Problem Statement
A.C. Moyer’s current eye cap manufacturing process is both slow and unsafe. Primarily, the company owners are concerned with the amount of operator interaction needed to produce the product, especially when this interaction is both dangerous and repetitive. We have been tasked with updating the manufacturing process to provide increased capacity and safety, while adding the potential to manufacture oval-shaped eye caps.
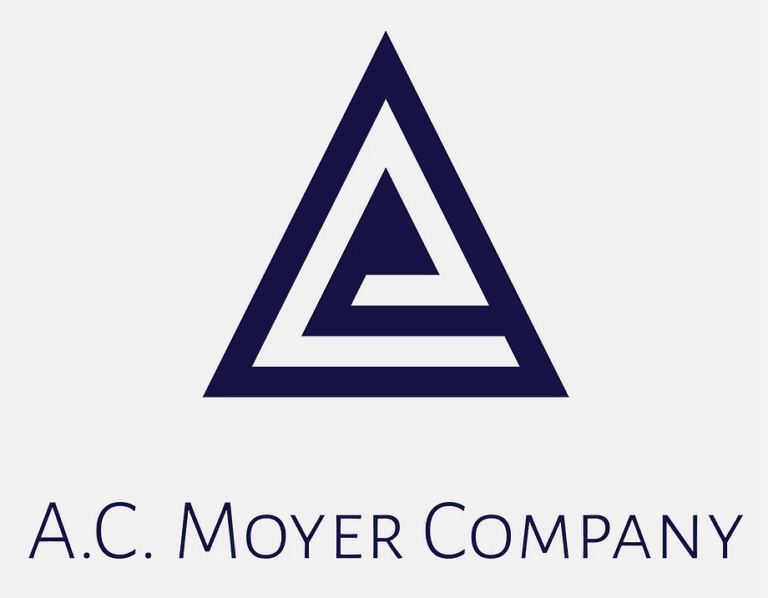
This project is sponsored by A.C. Moyer Company.
Current Process
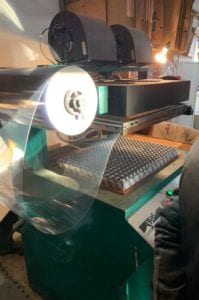
Current thermoformer system
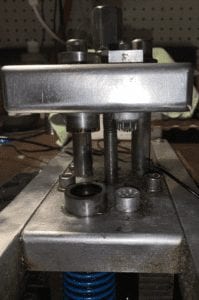
Current die-cutting assembly
Manufacturing Issues
Thermoforming Process Issues
- PVC sheet fails to completely mold to the eye cap geometry
- Heated plastic fumes enclosed in workspace
Die-Cutting Process Issues
- Produces one eye cap per one pedal actuation
- Air compressor capacity drained rapidly due to inefficient air cylinder
- Only circular eye caps possible
Project Goals
- Re-design, manufacture, and assemble an entirely new pneumatic die-punch machine
- Increase of yield and run-rate of punched eye caps by three fold
- Eliminate operator access to high-force pinch points
- Include oval-shaped die replacements
- Add improvements to the current thermoforming machine in order to increase yield
Initial Analysis
Cutting Pressure Test
Test Purpose
Determine what the ideal operating pressure is for cutting the molded PVC on old die-cutting system.
Procedure
Iterate cutting actuation 3 times at each operating pressure, 100-125 psi, by increments of 5 psi.
Results
Clean, no snag cut achieved at 120 psi, minimum cutting pressure 105 psi.
Thermoformer Insulation
0.3125” thick double reflection insulation was installed around the heating area to prevent workspace conditions from negatively influencing molding quality.
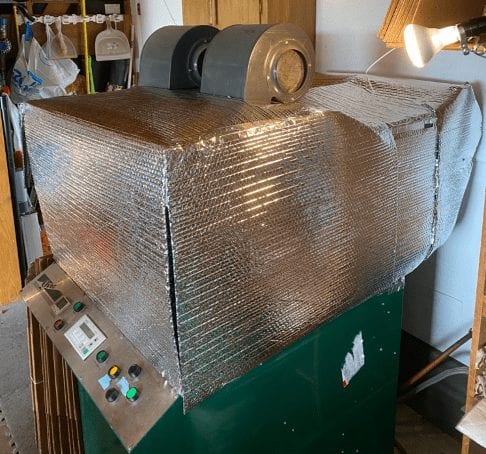
The thermoformer with insulation installed around the heating area
Full Die-Cutting Assembly
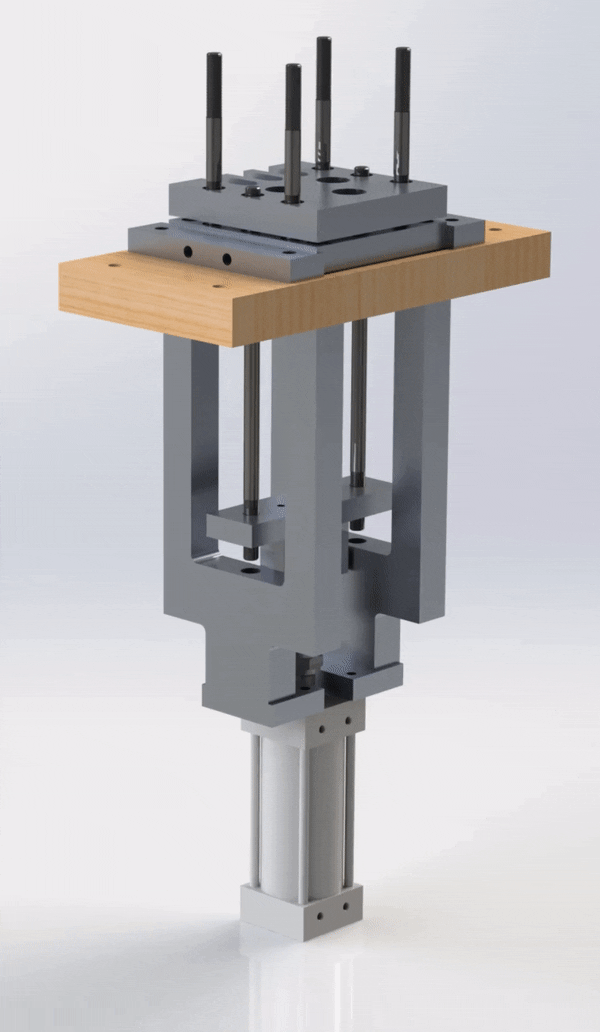
The final die-cutting assembly design CAD
U-Shape Assembly
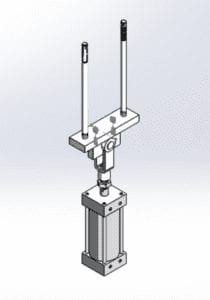
Air Cylinder U-Shape Attachment
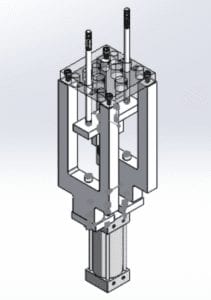
U-Shape Assembly and Bottom Plate Interaction
- Updated air cylinder requires smaller volumetric flow rate
- Development of U-shape attachment to air cylinder
- Updated from previous design (single rod) to two threaded rods
- Better load distribution with increased top plate mass and male die/pin quantity
- Cylinder to bottom plate attachment block design considerations:
- Sufficient area near female dies to allow for simple insertion of dies into bottom plate
- Mounting capability to the bottom plate and air cylinder given space limitations
U-Shape Assembly FEA
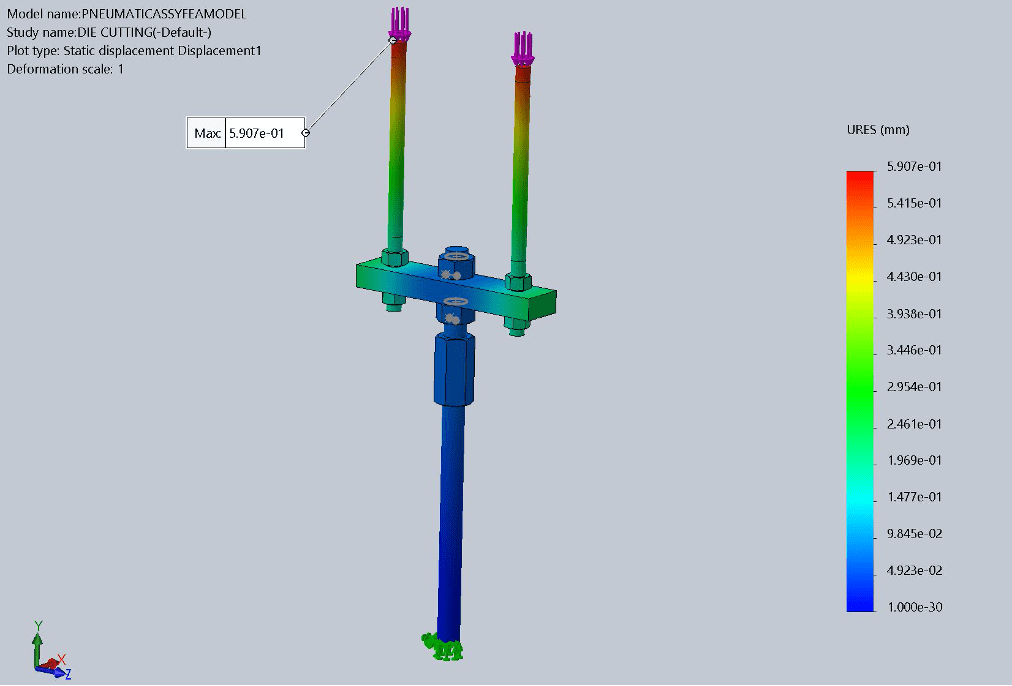
Deflection FEA Results
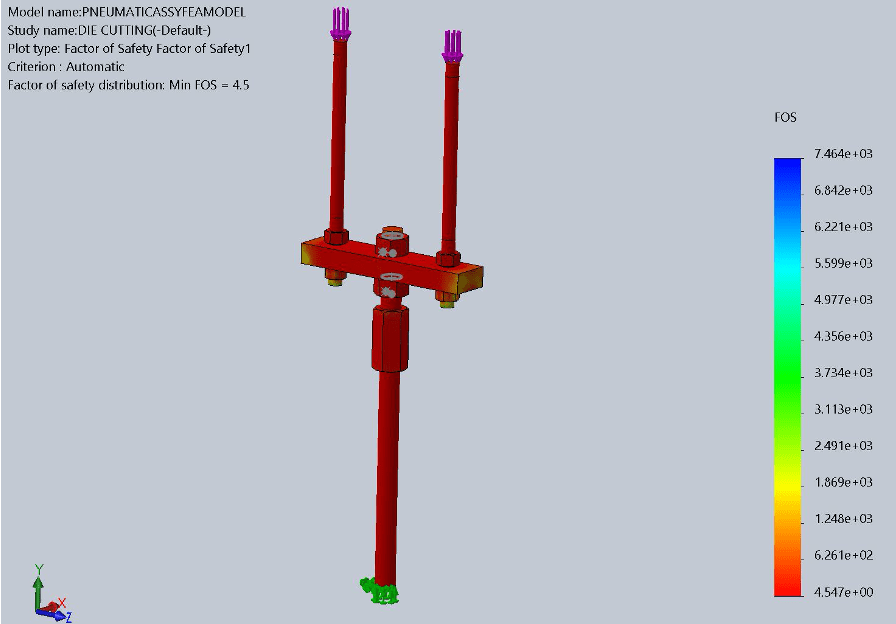
Factor of Safety FEA Results
Simulated load was determined by multiplying the maximum working pressure of the air compressor and the cross sectional area of the air cylinder (1400 lbf).
- Max deflection: 0.0232 in
- Minimum factor of safety: 4.55
Dies and Perforator
Dies
- Various sized dies, machined from tool steel, produce small, medium, and large circular eye caps as well as a one-sized oval-shaped eye cap
- The female dies rest on top of the bottom plate, while the male dies are inserted into the top plate. Both are secured in place with snap rings around the shaft at the location of the machined groove
- The oval dies feature press-fit dowel pins, which slide into a corresponding notch on the top and bottom plates in order to restrict rotational movement of the dies
- Collection tubes attached to the end of the female dies underneath the bottom plate remove and organize punched eye caps
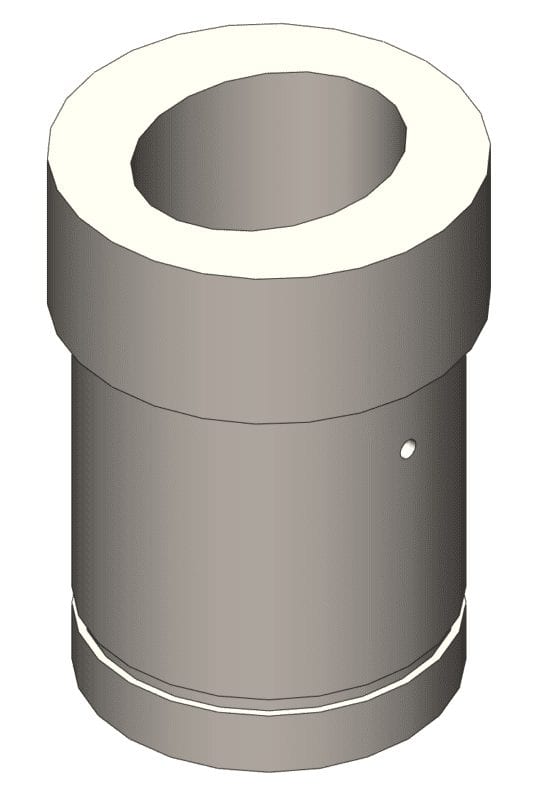
Female oval-shaped die
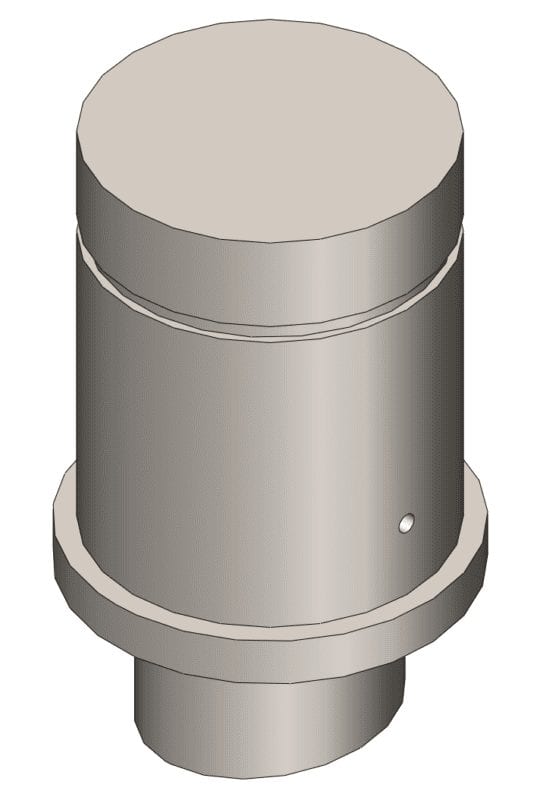
Male oval-shaped die
Note that the dowel pin hole for rotational alignment will be featured on only the oval-shaped dies and perforator pins, as shown above and below.
Perforator Pin
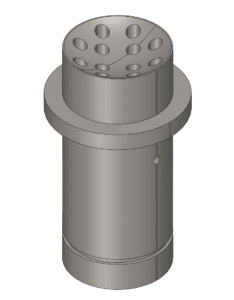
Female-side perforator
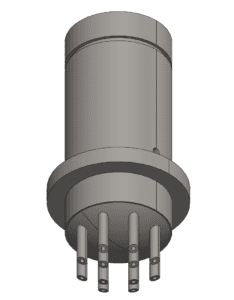
Male-side perforator
- Perforators are assembled into the top and bottom plates similar to the the dies, with snap ring securement
- Dowel pin insert is used to prohibit rotational movement
Platform Assembly
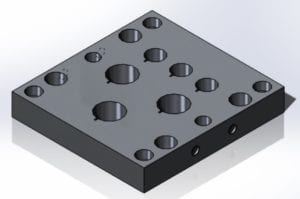
Bottom Plate
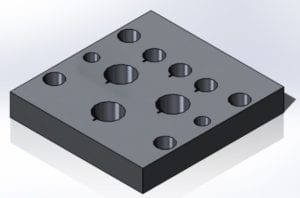
Top Plate
- Modified both platforms to accommodate 3 dies and perforators instead of just one
- Small notch was added on the platform to accommodate for the dowel pins on each through hole
- Four guide rails press fit into the bottom platform that mate to the top platform with linear bearings
- Two rods coming from the air cylinder attachment are rigidly attached to the top platform using nuts and washers
Final Results
- 3X production capacity
- Increased air compressor efficiency
- Thermoforming quality improvement
- Development of oval-shape dies to appeal to larger customer base
- Initialized safety regulations
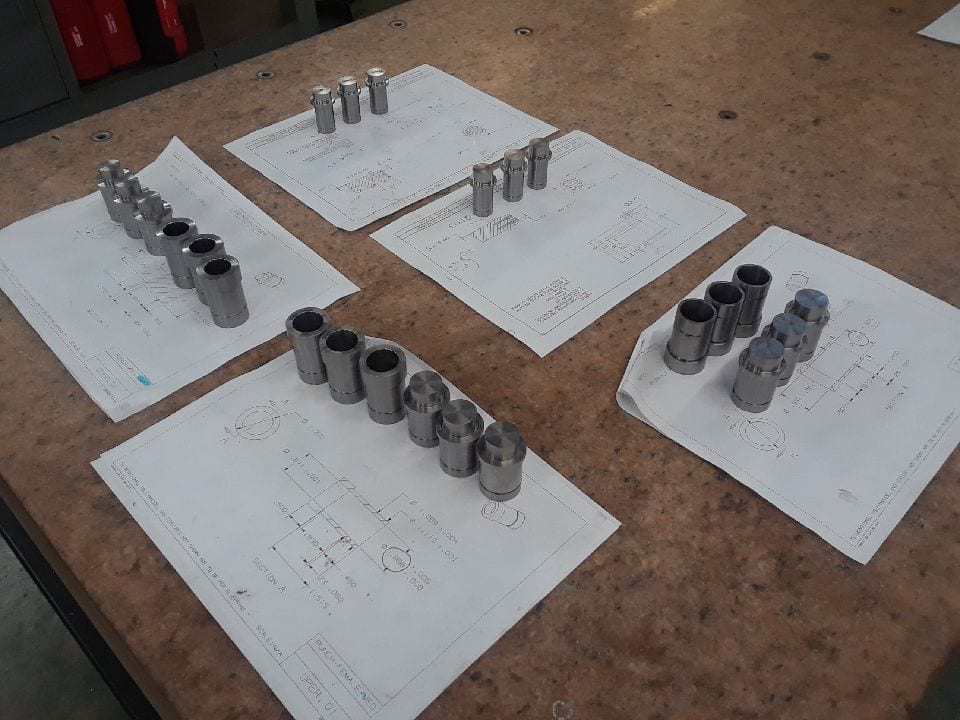
Newley Machined Dies