Our Team: Experiment 626
Senior Project Team 45, otherwise known by their nickname “Experiment 626,” is comprised of four Cal Poly Mechanical Engineering students: Josh Clemens, Kellen Fujishin, Alysson Loo, and Sammie Van Blaricom.
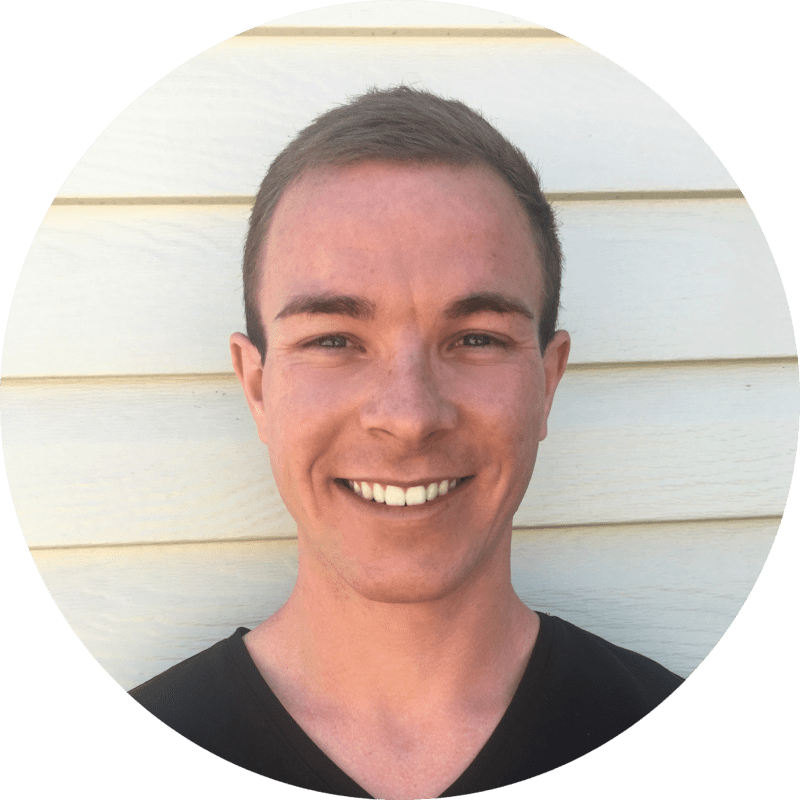
Josh
Manufacturing co-lead, testing lead
Besides keeping his teammates in stitches with his jokes, Josh’s concepts were crucial in finalizing the design of the final prototype, which he and Sammie manufactured and tested during Fall Quarter.
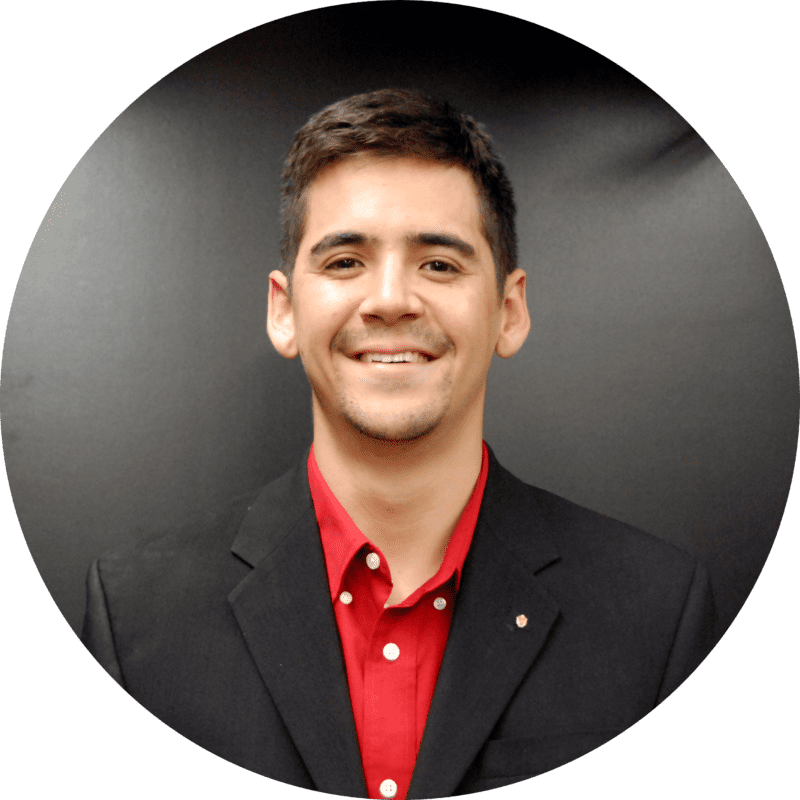
Kellen
documentation lead, visual materials lead
Kellen has been the main overseer of the presentations and visual materials given to sponsors, advisors, and interested parties, as well as documenting the process in various reports.
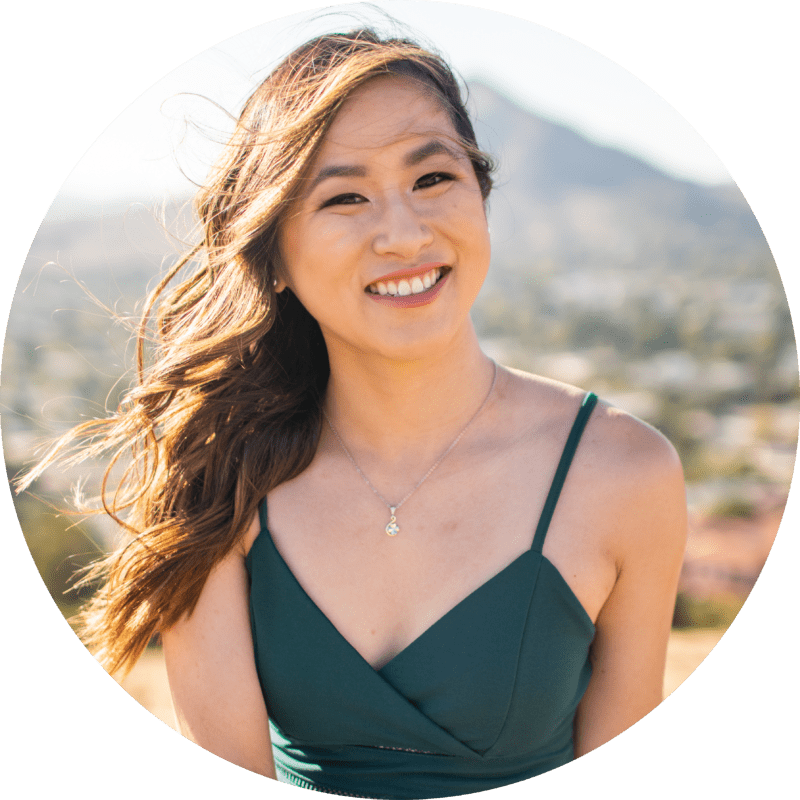
Alysson
CAD lead, treasurer
From the start, Alysson was responsible for creating intricate, detailed models of initial designs and the final prototype using Computer-Aided Design (CAD). Her detailed-oriented approach helped the team stick to the budget and avoid overruns.
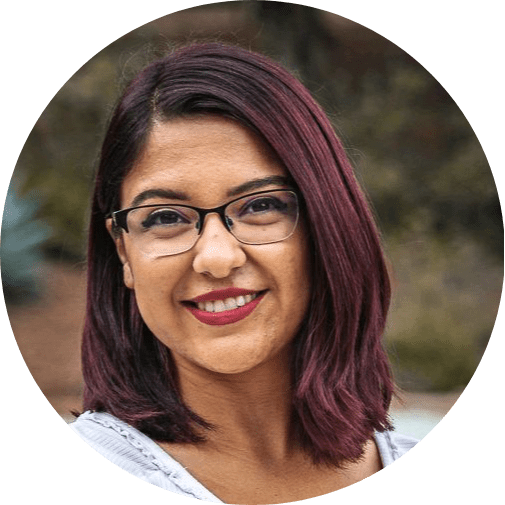
Sammie
Communications lead, manufacturing co-lead
Throughout the project, Sammie has worn many different hats. Playing a part manufacturing and initial presentations, her focus towards the end of the project was manufacturing of the prototype with Josh.
Acknowledgements
Team 45 would like to thank sponsors Christian Strauli and Jennifer Crooks, main adviser Lee McFarland, supporting advisers Peter Schuster and Eileen Rossman, and Bellevue-Santa Fe Charter School. Go Bulldogs!
SciTechatorium Shake Table
Project Overview
"An investment in knowledge pays the best interest" - Ben Franklin
In January 2020, Bellevue-Santa Fe Charter School requested that a senior project at Cal Poly be focused on creating a new, interactive STEM exhibit for the SciTechatorium, commonly known as the SciTech. Ideally, the exhibit had to strike a cohesive balance of a fun activity while being educational.
After deciding on the concept of a shake table with vertical and horizontal motion in Winter 2020, the team moved into designing the prototype in Spring 2020, and ordered parts at the end of Summer 2020. Finally, the project culminated in November 2020 with a manufactured prototype.
Project Requirements
- Withstand repeated use by children aged 5-12
- Huge emphasis placed on safety, especially concerning pinch points and tipping hazards.
- Demonstrate and educate a STEM concept to the aforementioned age range
- Incorporate both interactive, fun elements while maintaining a focus on education
- Mobility is a plus, but ultimately must fit through a standard size door frame
Ideation and Design
During brainstorming, initial ideas for a STEM-oriented activity included:
- Completing circuits to compete in a type of game
- Using magnets to launch projectiles at targets, similar to a coilgun
- Gear train simulations
Once a shake table was decided upon, the team had a number of design decisions to make:
- Would the display be electronically powered, or manually powered?
- What kind of motion do we want to see a structure subjected to?
- How do we keep it safe?
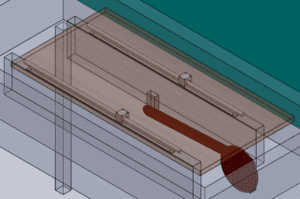
Initial concept of design: a single degree of freedom shake table, only moving in the horizontal direction
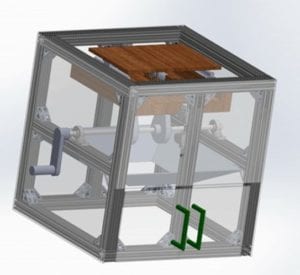
Intermediate concept design: a second degree of freedom, in the vertical direction, has been added along with safety barriers encasing the table
Component Strength
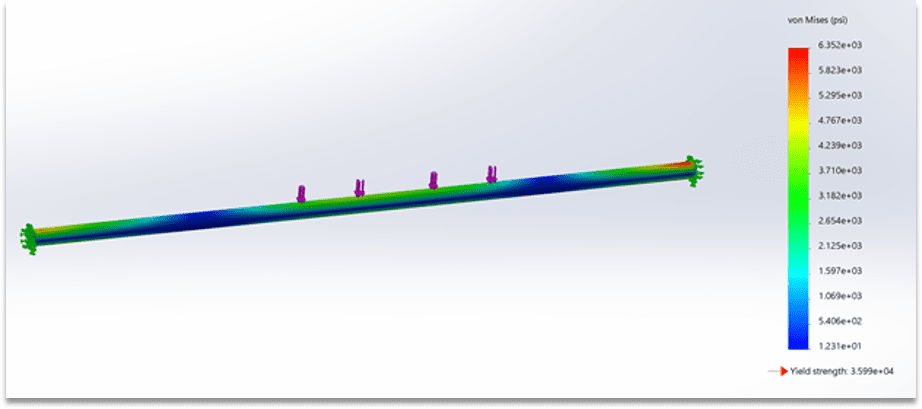
When subjected to an extreme load case of 70 pounds, the factor of safety of the shaft was 5.6, meaning it would take 5.6 times 70 pounds to buckle the shaft.
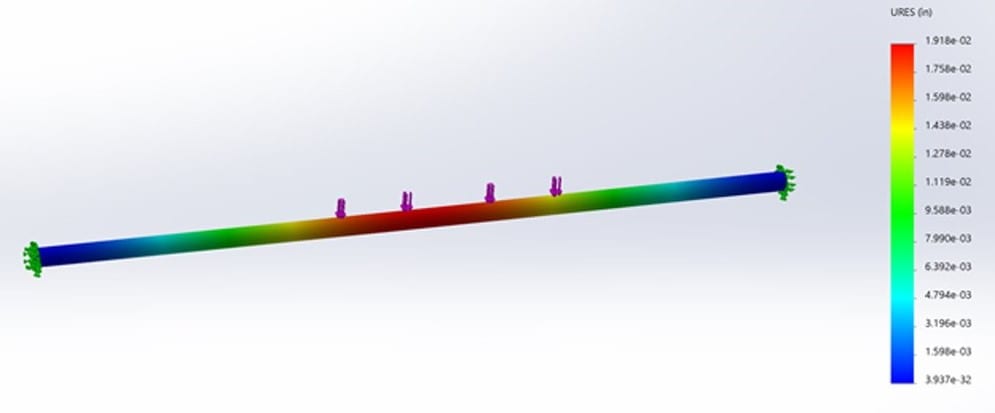
When subjected to the same 70 pounds, the center of the shaft only deflects to 0.02 inches away from its original position.
Stress Testing
The main motion mechanisms rest on a crucial part: a 0.75 inch shaft made of stainless steel, supported by two bearings. Using Finite Element Analysis (FEA), the team determined that the shaft could reliably take the weight of the mechanisms and any structure built on the table.

This project is sponsored by Bellevue-Santa Fe Charter School, with additional funding graciously provided by California Polytechnic State University.
Design and Function
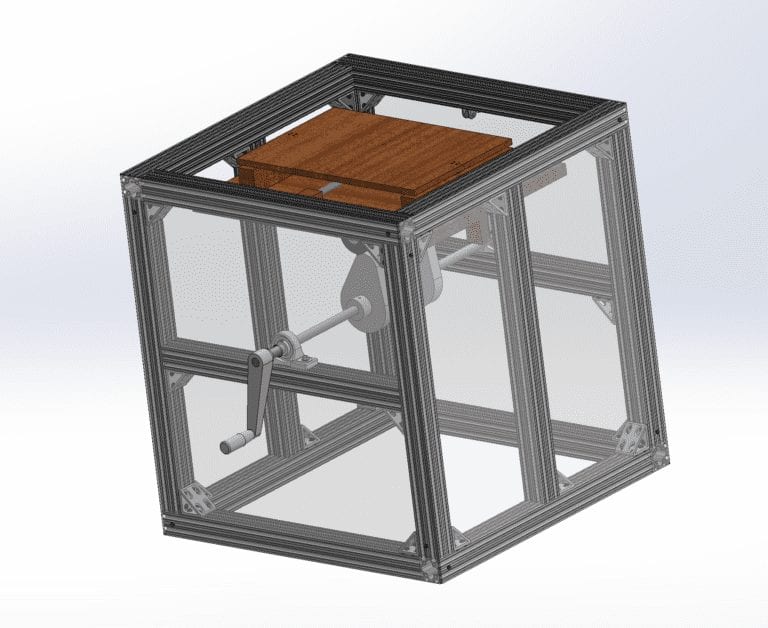
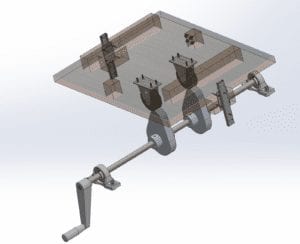
The vertical motion is produced by two identical cams. When rotated, the longer part of the cam causes the whole assembly to rise and fall, creating vertical motion.
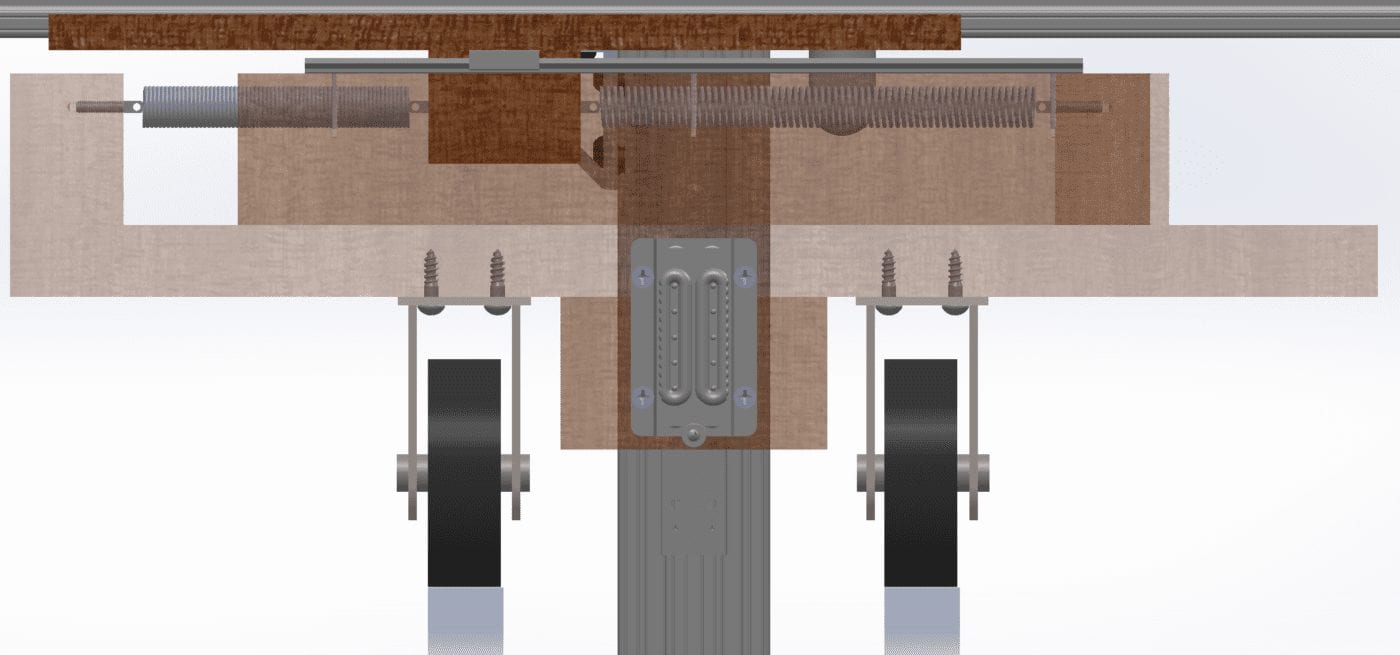
The horizontal motion is produced by potential energy stored in two springs, which cause the top platform to move horizontally when pulled to one side.
Design Overview
The shake table’s purpose is to emulate the motion of an earthquake in a more accurate way than many conventional shake tables. While many shake tables are able to achieve movement in one direction, usually horizontally (side-to-side), Team 45 sought to create a shake table that could more accurately mimic an s-wave, or shear wave, shown below. Using a combination of vertical and horizontal motion, the table can accurately emulate s waves.
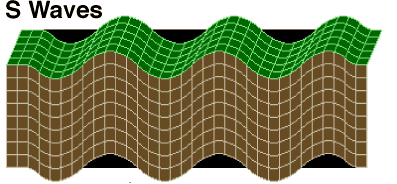
Manufacturing
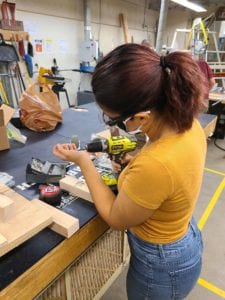
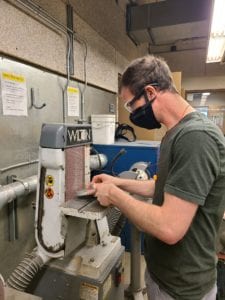
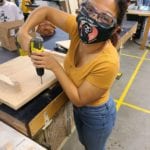
Testing
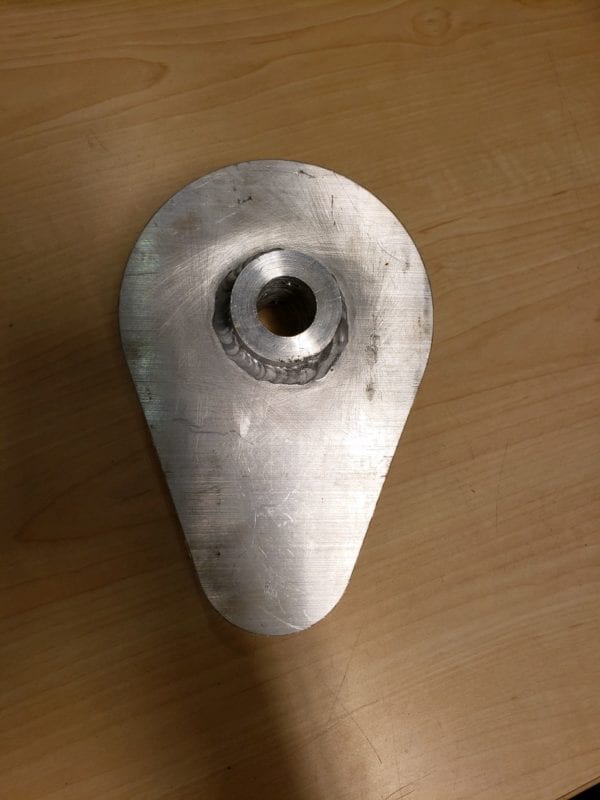
Original cam profile. Note the long shape, which was difficult to turn. The original design provided 2.5 inches of vertical displacement.

Modified cam profile. Note the shorter shape, which decreases the vertical displacement to 1 inch.
Frame Test – Using bodyweight, the aluminum frame was able to support at least 130 pounds.
Vertical Motion Test: Original Cams – The cams mounted on the shaft provide the vertical motion by having an uneven but still vaguely circular profile, giving a vertical displacement of 2.25 inches. The first vertical motion test was unsuccessful, as the crankshaft was very hard to turn. This led to a redesign of the cams.
Vertical Motion Test: Redesigned Cams –The new cam design gave a shorter vertical displacement of 1 inch, but was far easier to turn.
Horizontal Motion Test (TBD) – Once an additional spring is added, the top platform is expected to produce a stiff horizontal motion with a high frequency and low settling time.
Final Prototype
Specifications
Weight: ~90 lbs
Dimensions: 30” X 30” X 30”
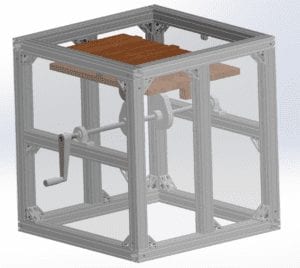
Custom Components
- Aluminum Rotary Cams
- Wood Shaking Platforms
Stock Components
- 8020 2 inch square frame pieces
- McMaster-Carr Shaft, Springs, Bearings, Pulleys, and Hardware
- TAPP Plastic Acrylic Sheets
Project Future
While COVID-19 currently prevents the team from seeing their project in action in the SciTech with students tumbling structures and building them back better, they are confident that this project will serve as both an educational and fun display, and maybe inspire a future seismologist or geologist.
Through the ups-and-downs of the project, the team has learned much about the engineering process and working together, and hope their project does the same for many children for year to come.
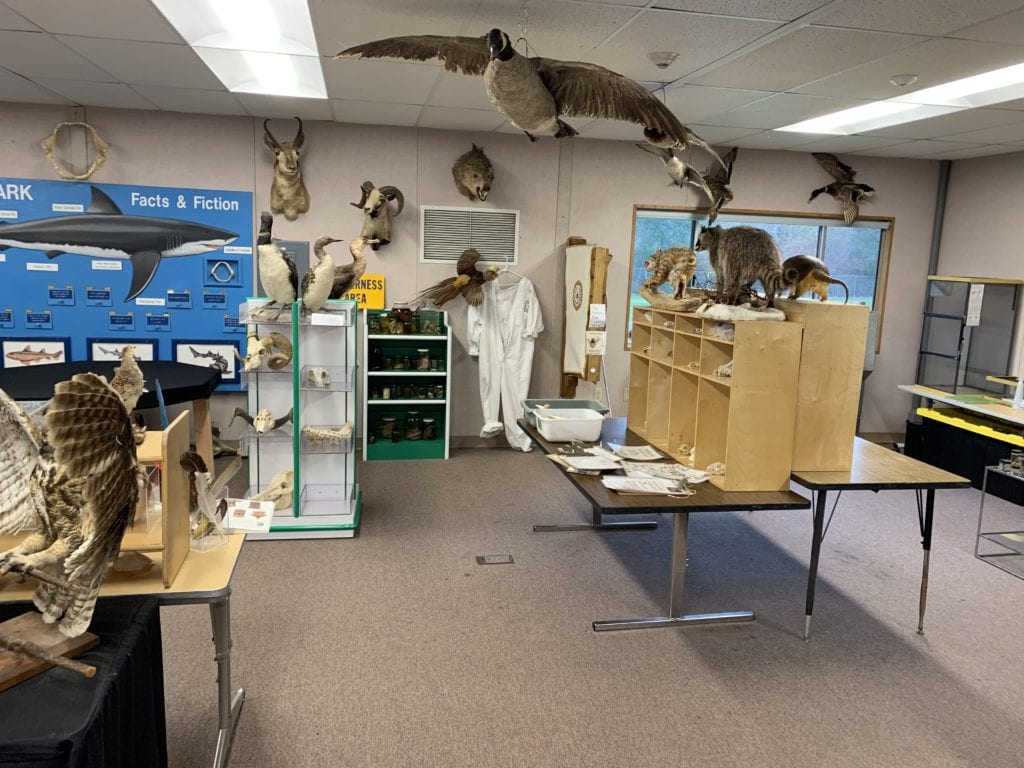
If we had a second chance...
Engineering is, above all, an iterative process. The mindset of the group was not to think of failure as a negative thing, but rather as finding ways that wouldn’t work, pushing them to a final solution. Here are some project notes that would have optimized the prototype:
- Testing different springs to find an optimally sourced part
- Sought input on the cam profile early on, or conducted preliminary testing on just the cams to identify flaws
- Optimize some of the heavier components, as some factors of safety were quite high and didn’t require as bulky of components
- Possibly incorporating a gear ratio to make the crankshaft easier to spin
- Optimize the prototype to possibly be smaller and more mobile