Our Team
Our team possesses unique backgrounds within Industrial and Manufacturing Engineering, allowing each member to specialize in their role.
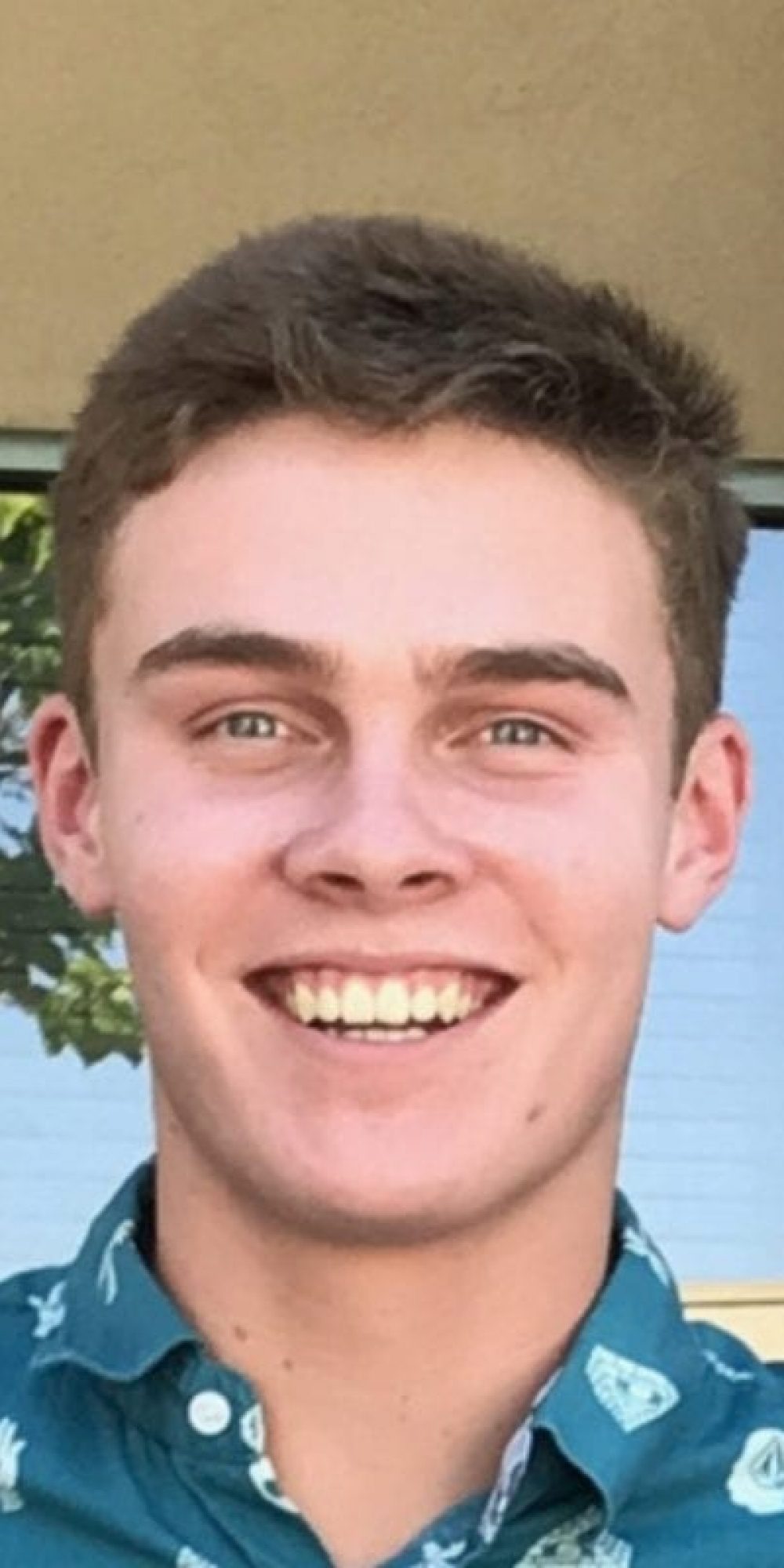
Jason Johnson-Yurchak
Project Manager
Jason is the President of the Society of Manufacturing Engineers at Cal Poly and interned at the High-Energy-Density Physics department at Lawrence Livermore National Laboratory.
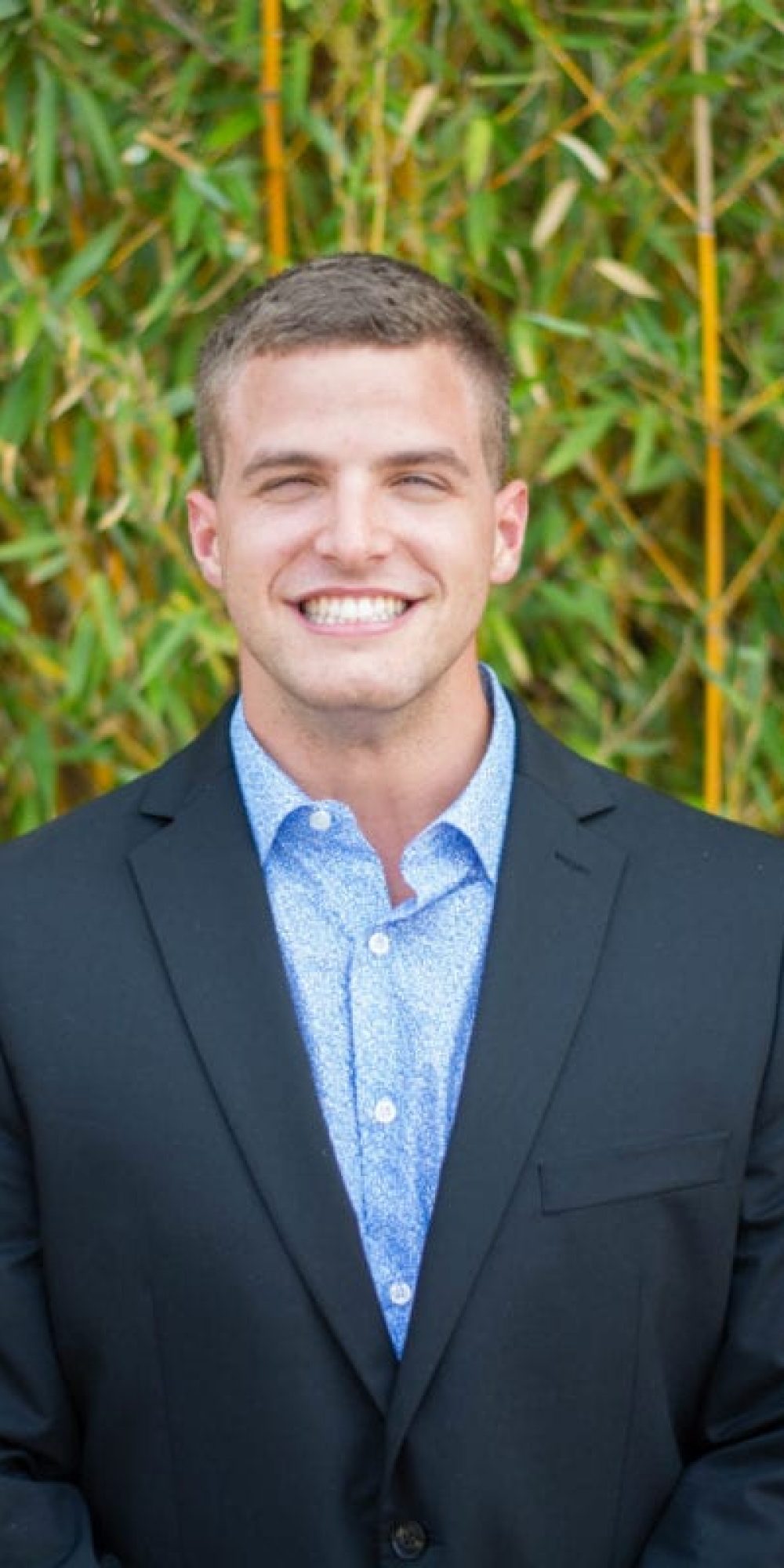
Cole Sheedy
Solutions Analyst
Cole was an Operations Intern at Bonduelle Fresh Americas for a condiment yield improvement project and will be working as an Applications Engineer at Motion Industries following graduation.
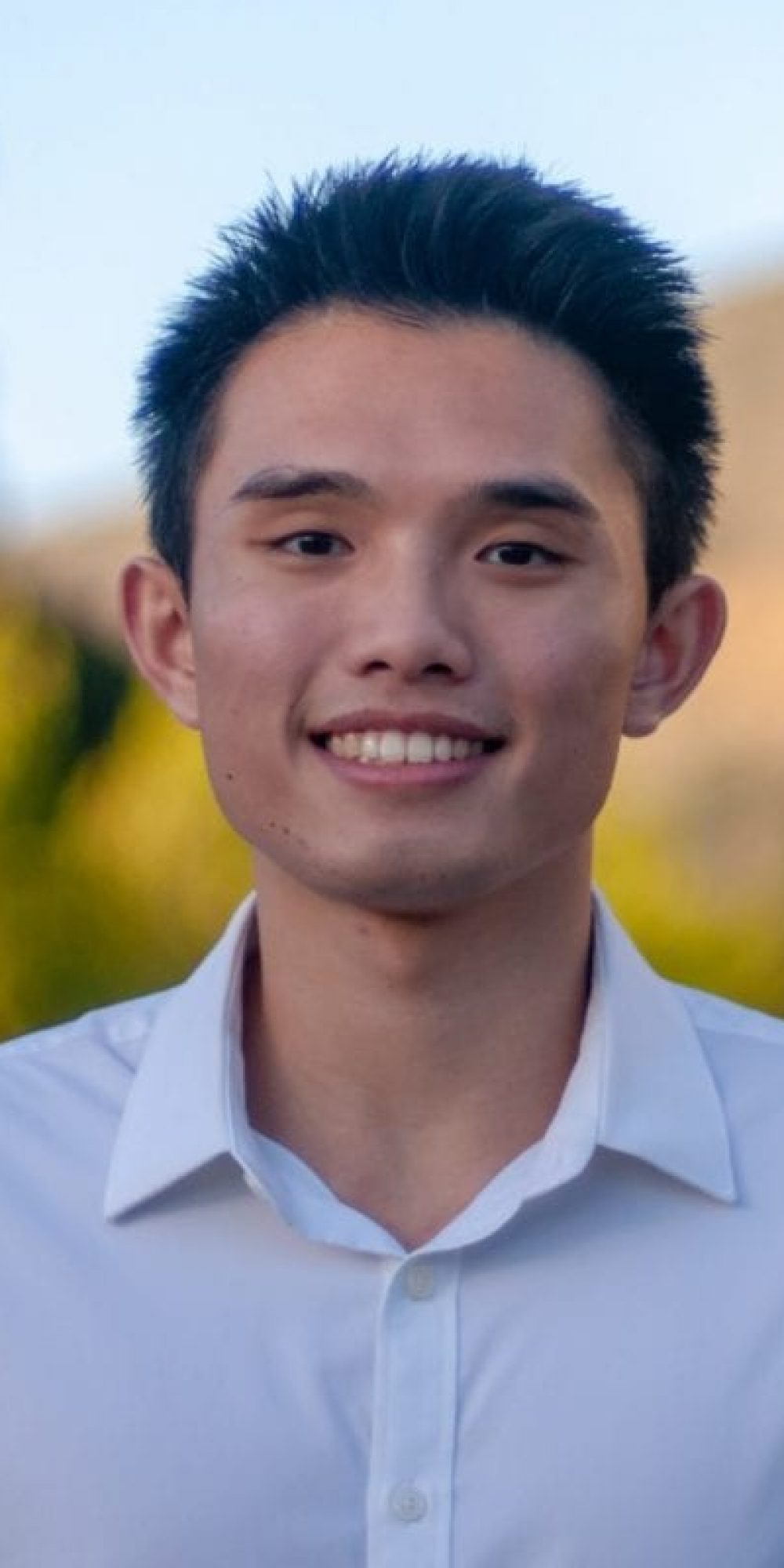
Andy Wei
Data Analyst
Andy is passionate about aeronautics and interned at Northrop Grumman as an Industrial Engineer. He hopes to continue working in the aeronautics industry past graduation.
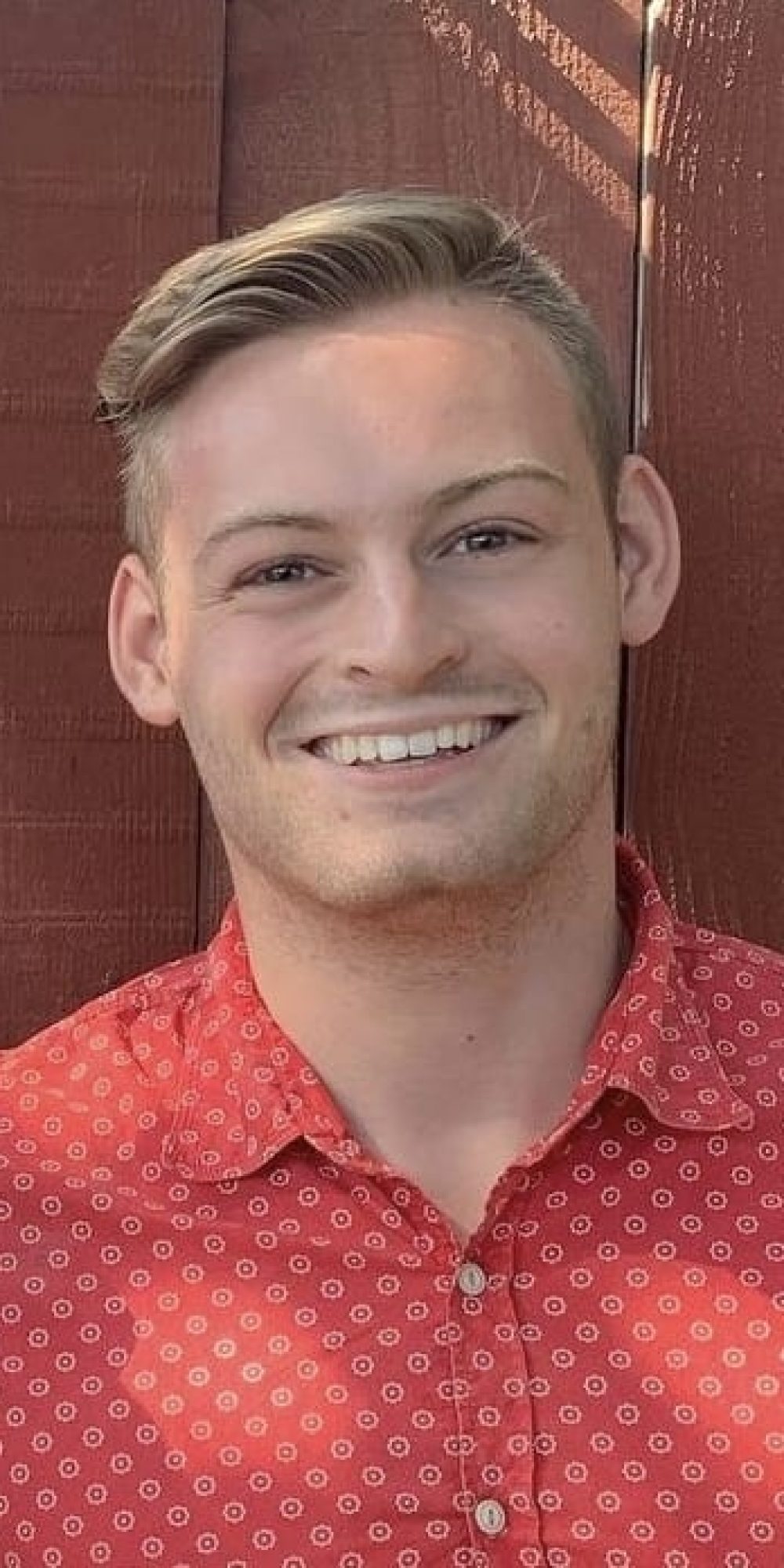
Christian Berger
Communications / Data Analyst
Christian is a member of Cal Poly’s Institute of Industrial and Systems Engineers chapter, along with the consulting and accounting clubs on campus. Following graduation, he will join KPMG as a consultant in their IT strategy arm.
Acknowledgements
Special thanks to Josh Seelhoff, Tali Freed, Matt Schuler, Jim Erdmann, Don Russell, Josh Tooley, Chris Chan, Ahn Ndao, and the crane operating staff at Everett, Washington.
Project Video
The research conducted throughout this project highlights the associated financial records, legal concerns, and safety history, while exploring the applications of overhead cranes in the industry. The proposed solutions include operations conducted via a remote workstation, a factory floor operation, and an ergonomically redesigned environment. The solution down selection process accounted for economic scales, ergonomic standards, cultural restraints, scheduling impacts, ease of implementation, learning and training programs, reliability, legality, functionality, policy alignment, and aesthetics.
Boeing Overhead Cranes Project
Problem Statement
We are investigating the feasibility of integrating an improved crane operating system into Boeing’s Everett facility. The project topic was originally proposed by Josh Seelhoff, Industrial Engineering Senior Lead, to management in the summer of 2020. When Boeing built their South Carolina facility in Charleston, the concept of outside cab operation was considered but not implemented, so this technology is still new to the company.
Objectives
Our goals are to find a solution that reduces safety problems leading to liability issues along with potential damage to reputation while diminishing high costs associated with crane operators in terms of medical compensations, delays, and lost productivity.
Background
The Boeing Company is an American corporation that is one of the largest aerospace manufacturers in the world. Boeing’s Everett Facility has the largest building by volume in the world and contains a team of approximately 74 operators whom which transport plane parts via 9 four-block and 19 single-block cranes.
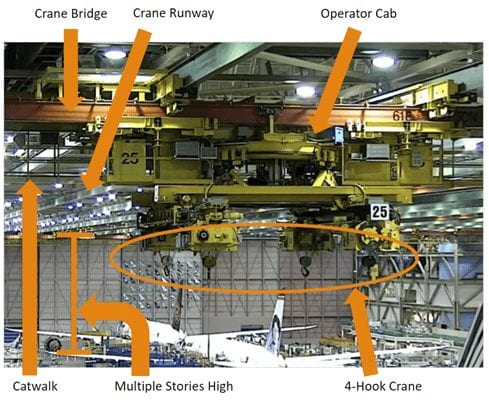
Current State
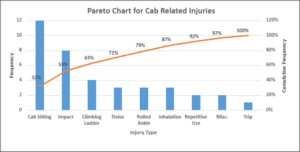
Constraints: upfront costs, cultural changes, hardware compatibility, revised safety factors, union regulations, and facility layout restrictions
Operator Duties and Responsibilities:
- – Guide movements with visible or audible signals
- – Operate cab-controlled crane by radio
- – Coordinate/develop safety protocol
Current State Process Flow:
- 1. Operator starts workday and enters shop floor
- 2. Operator ascends to crane cab
- 3. Operator performs average shift time
- 4. Operator descends to shop floor
- *Repeat cycle as operator cycles through shifts*
SIMULATION RESULTS:
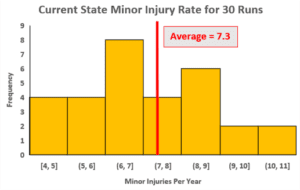
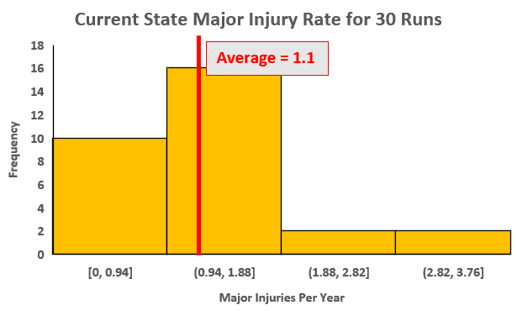
Ergonomics Research
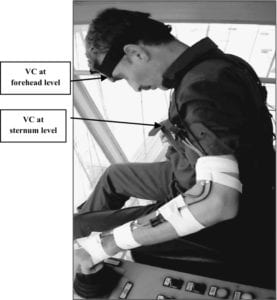
From research on crane operator injuries, we found between 70% to 90% of overhead crane operators are affected by musculoskeletal disorders due to the prolonged forward bent sitting position.
When researching potential solutions, we found the port industry was much further ahead with regards to protecting its’ operators from injuries. Also, Demag cranes currently supplies Airbus with remote operation crane equipment.
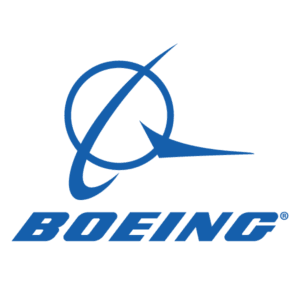
Boeing Overhead Cranes
This project is sponsored by The Boeing Company.
Design Alternatives
ERGONOMIC APPROACH
This design alternative focuses on redesigning ergonomics of the factory work environment to prevent fatigue and optimize performance. Examples include a dynamic seat and protective padding on potential striking locations.
Pros:
– No significant change to operator’s roles or responsibilities
– Operators remain employed by Boeing
– Inexpensive and quicker to implement
– Improves operator quality of life without forcing drastic change
Constraints:
– Operator remains in cab and cab-related accidents remain a concern
– Could take longer than expected to see quantitative improvements
– Removes the possibility of broadening the role to disabled workers
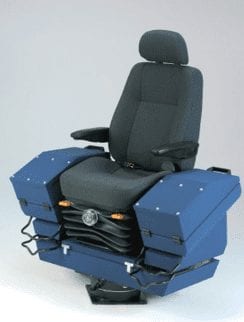
REMOTE WORKSTATION
This design alternative focuses on removing the operator from the crane cab to eliminate risks.
Pros:
– Operator works from ergonomically designed workstation
– Technology and proof of concept exists
– Ability to switch between crane cabs increasing productivity
Constraints:
– Large upfront cost for consulting, new hardware, downtime
– Time for engineering consulting, retrofitting, and implementation
– Labor laws and unions may resist change to work environment
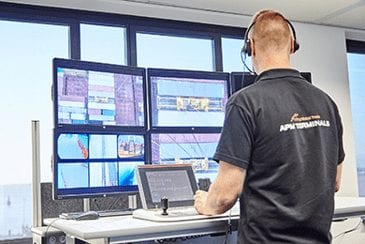
FACTORY FLOOR OPERATION
This design alternative focuses on conserving operator to hook tender communication using a belly-box controller from the floor.
Pros:
– Operator easily communicates with hook tenders
– Technology exists and has worked for others in airline industry
– Less expensive than remote workstation
Constraints:
– Overcoming radiofrequency difficulties with near by Naval Base
– Loss of “birds-eye view”
– Multitasking walking and operating may result in unforeseen risks
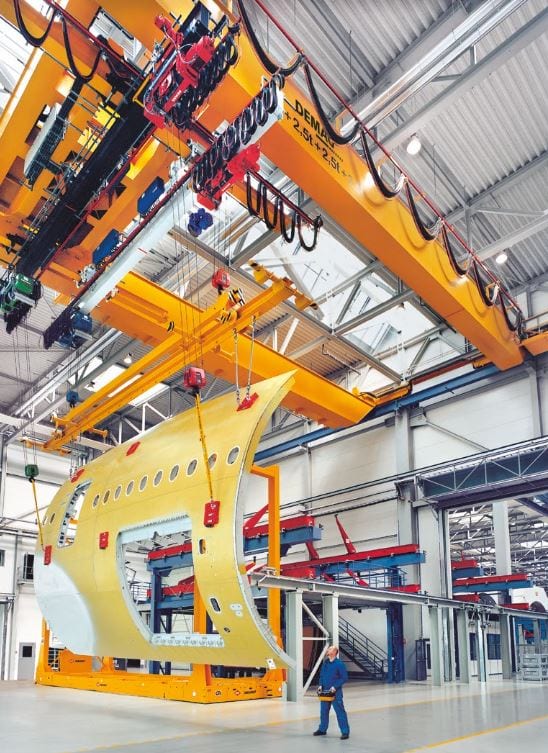
Down Selection Approach
To determine the best solution, we analyzed the ergonomic performance of each solution via simulation to compare with the current state. An economic analysis is drawn from the simulation results to estimate cost savings. Lastly, considerations for other constraints are taken.
Solution Analysis
AnyLogic Simulation Analysis
Based on running a discrete process flow simulation 30 times for a duration of 2 years, we found the following results:
Remote Workstation:
– 2.2 Minor Injuries per Year
– 0.35 Major Injuries per Year
Factory Floor Operation:
– 3.25 Minor Injuries per Year
– 0.65 Major Injuries per Year
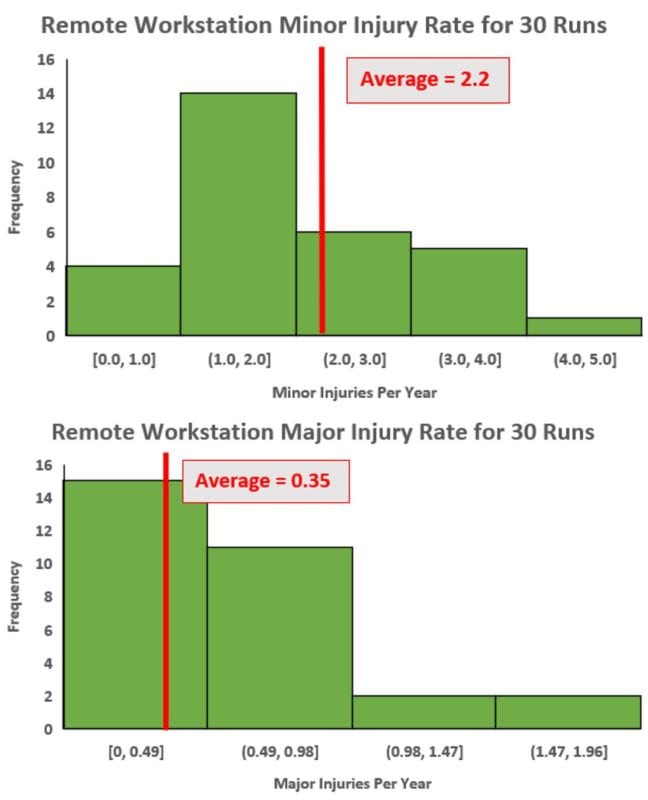
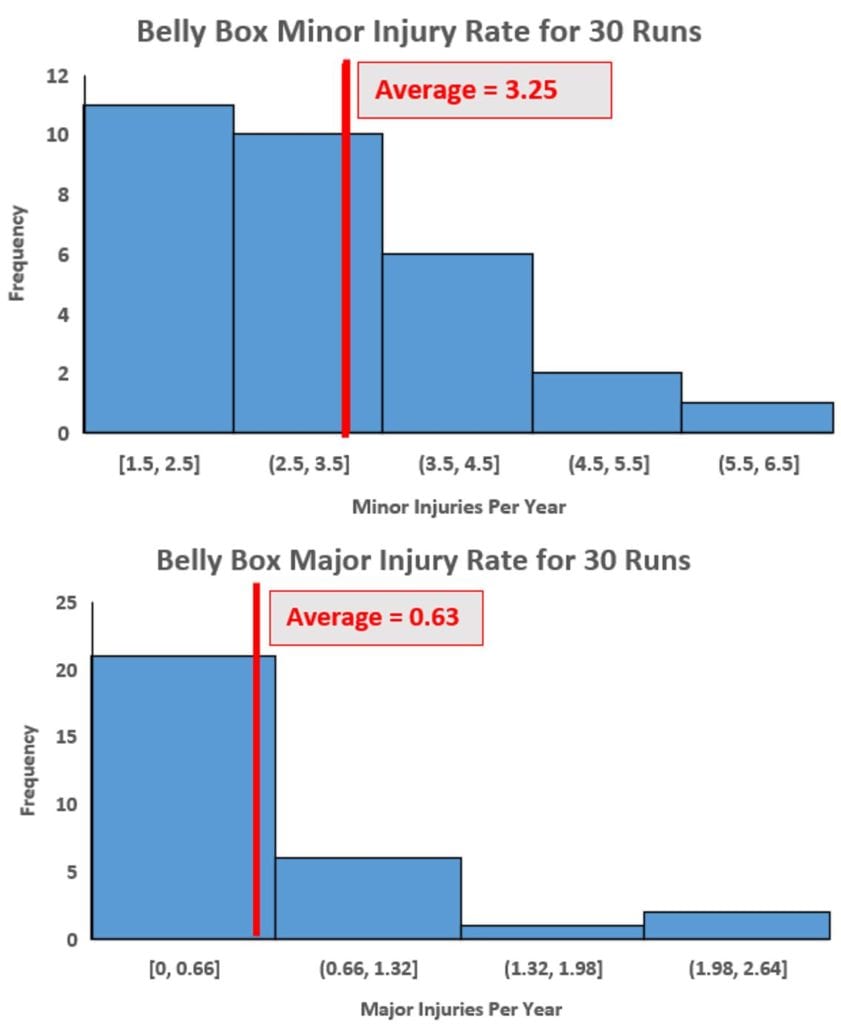
Assuming the ergonomic approach is only a temporary solution, we find the remote workstation and factory floor operation solutions produce significantly less injury compared to the current 7.3 minor and 2.1 major injuries per year.
Economic Analysis
Based on a cost savings calculator provided by Boeing, we discovered a a returns of approximately $50,000 per year if either of the long-term solutions were implemented.
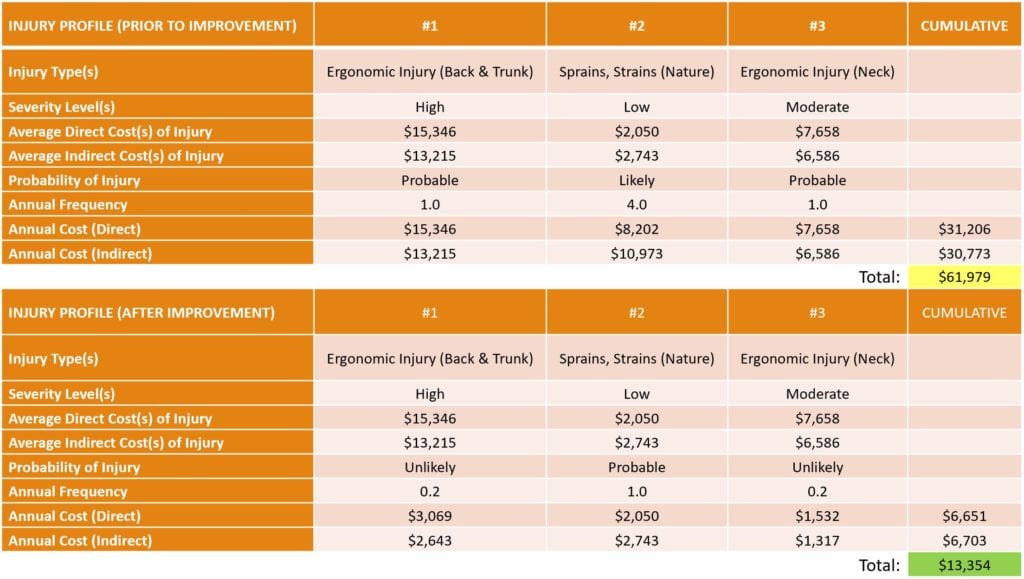
Conclusions
Considering the risks associated with the failure of this system, either technologically or logistically, our team studied other crane systems in modern manufacturing industries to determine project feasibility. When inspecting long-term solutions, investments were centered towards boosting productivity and reducing costs for the future, so our team analyzed the scale of investment for these solutions.
Our team created the following decision matrix based on a weight of one to five with six categories of inspection; this tool was used to determine the best solution to meet the company’s needs for this project.
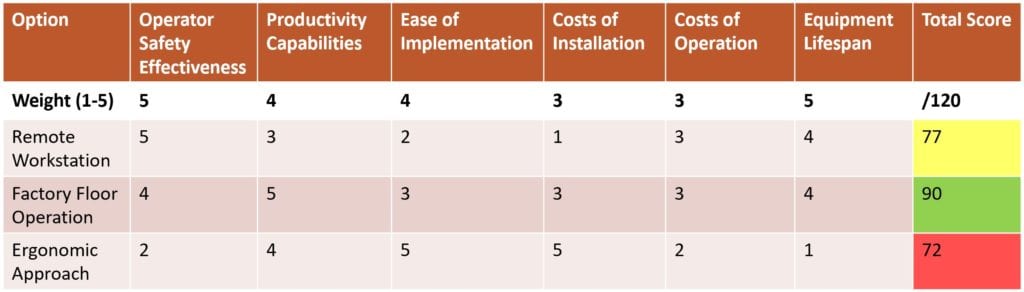
As a result, our research found that a remote workstation or factory floor operation would improve the quality of life of the employees and increase productivity more than the ergonomic approach. Although the ergonomic approach would potentially address minor injuries, this solution would only provide short-term risk prevention when it comes to operator safety. However, immediate improvements to the operator’s environment would require minimal investment with time and budget to this project, leading to fast results.
Although operator safety effectiveness is best achieved through the remote workstation, productivity is weakened as the operator would be separated from the crane operation line with the hook tenders. Because Boeing’s current system also relies heavily on hand signals and vocal commands, the operators would be more comfortable transitioning to factory floor operation while the costs of operation are still similar.
The Boeing Company’s principles state, “in everything we do and in all aspects of our business, we will make safety our top priority, strive for first-time quality, and hold ourselves to the highest ethical standards,” and our team concludes that a factory floor operation system would allow the company’s crane operation to prosper in the future.
Recommendations
The next step for this project is to collaborate with Boeing’s facilities and engineering team to determine the feasibility of implementation. Working with third-party vendors like ABB, Demag, Konecranes, etc. and proofing out the selected solution will not only save Boeing costs from injury and damage product, but the comfort of the operator will improve as well.
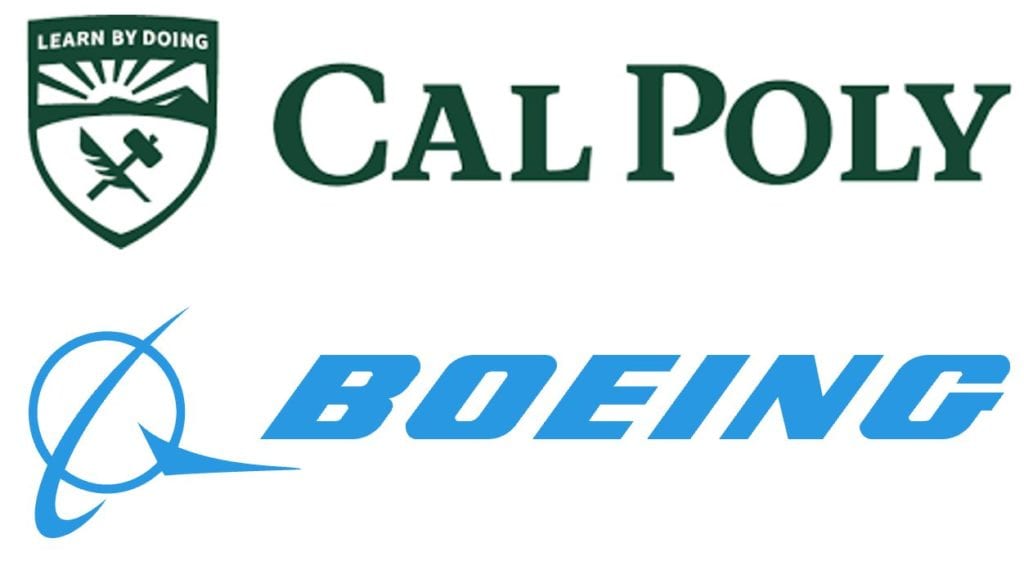