Our Team
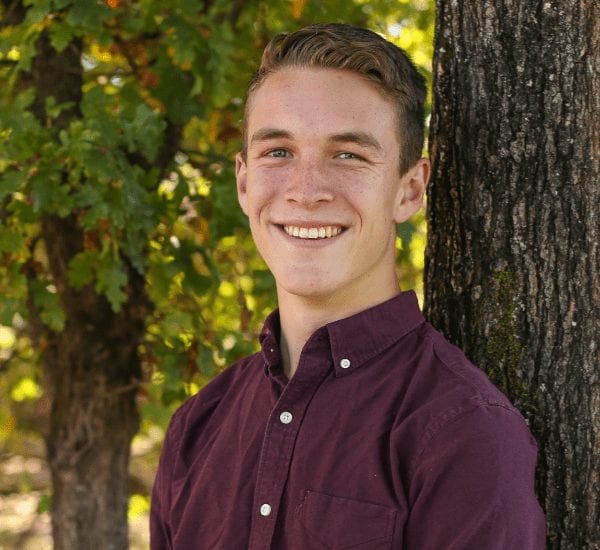
Sam Hunt
Project Manager
Sam Hunt is a Manufacturing Engineer from Santa Rosa, CA. His main roles were CAD Modeling potential solutions, design analysis, manufacturing, and testing. Sam reported data directly to the team to analyze, and documented testing results through caliper measurements, pictures, and video recordings. This was crucial for finalizing and concluding the recommendation report.
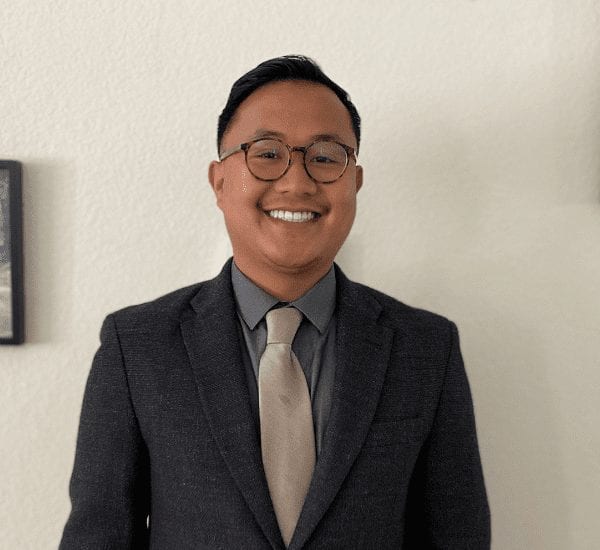
Ronel Ordona
Design Analysis Lead
Ronel Ordona is a fourth-year Manufacturing Engineering student at California Polytechnic State University, San Luis Obispo. His main roles were design analysis, manufacturing, and testing. Ronel researched mechanical properties in potential materials, assisting the team with prototype design and testing methods. He will continue on with the project in Fall 2021 to design the layout for Armadillo Designs new facility
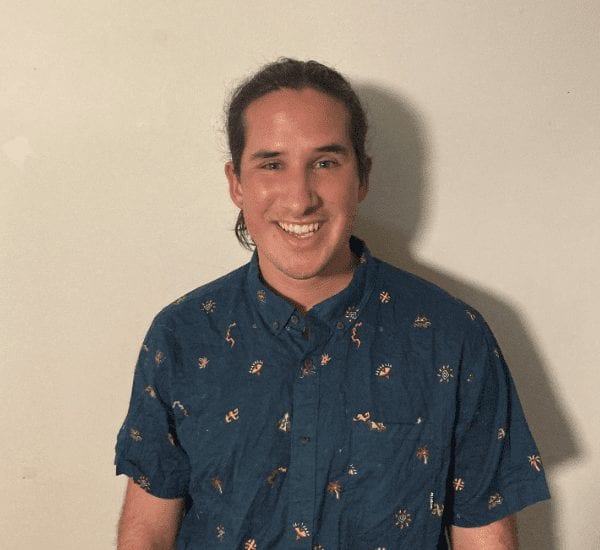
Austin Warren
Production Organizer
Austin Warren is a fourth year Industrial Engineering major from Berkeley, CA. His main roles were design analysis, testing, researching material properties, prototyping, brainstorming potential solutions. This was all beneficial for the finalization and overall product as a whole.
Acknowledgements
We would like to thank our sponsor Fabian Araujo for allowing us to work on this project, and guiding us through the current state. We would also like to thank Jill Speece for guiding our team on a weekly basis to the final report, and Trian Georgeou of the IME Department for his industry insights and material recommendations.
Our Project's Videos
Our Project's Digital Poster
Problem Statement
Armadillo Design has a demand from a local retailer for 10 shells a month that they cannot fulfill due to product defects. This calculates to $168,000 in annual lost revenue. The shell is not completely water resistant and is only able to fit the Ford F150 standard bed. The company would like their truck shell to fit multiple truck make and models. The current retractable roof system is outsourced from a Peragon® truck bed covers. Armadillo Designs is seeking to design their own roof system that is capable of accommodating multiple truck bed dimensions and will reduce manufacturing costs. Armadillo Designs is acquiring a new facility and needs to design a layout that will allow them to efficiently manufacture their truck shells to meet demand.
Current State
- Armadillo Designs current design is catered to the Ford F150 standard bed.
- The truck shell uses a water resistant retractable roof system that is outsourced from Peragon® truck bed covers.
- The back door of the shell uses a hinge mechanism that is not water resistant.
- The shell walls are made with fiberglass panelling and the frame is made with plain carbon steel. The frame is outsourced from Austin Waterjet; a metal fabrication shop located in Austin, Texas.
Key Metrics
The main goal of the team when finding key metrics was improving the original prototype brought to them by Armadillo Designs.
- The first was to minimize cost and keep it below a total of $2,500 per unit.
- The next was to have the shell have less than 5 leak spots throughout the entire structure.
- The next was to keep the total number of parts under 60.
- The final metric was the overall weight of the shell which the team aimed to keep under 250 pounds for ease of shipping and maneuverability.
Test Summary
To evaluate the different designs and materials for our project, we used priority matrix diagrams to come up with the highest benefit and easiest to implement solutions. To test the HDPE, we subjected it to a water test and then direct sunlight for a week. After this time, there was considerable warpage and distortion in the panels. The team then tested fiberglass for the roof material, as well as a series of G-channels each designated for one of the panels. After creating the prototype, this design allowed the panels to slide very well – being able to be opened or closed within 5 seconds. However, there was still visible warpage in the middle of the fiberglass panels.
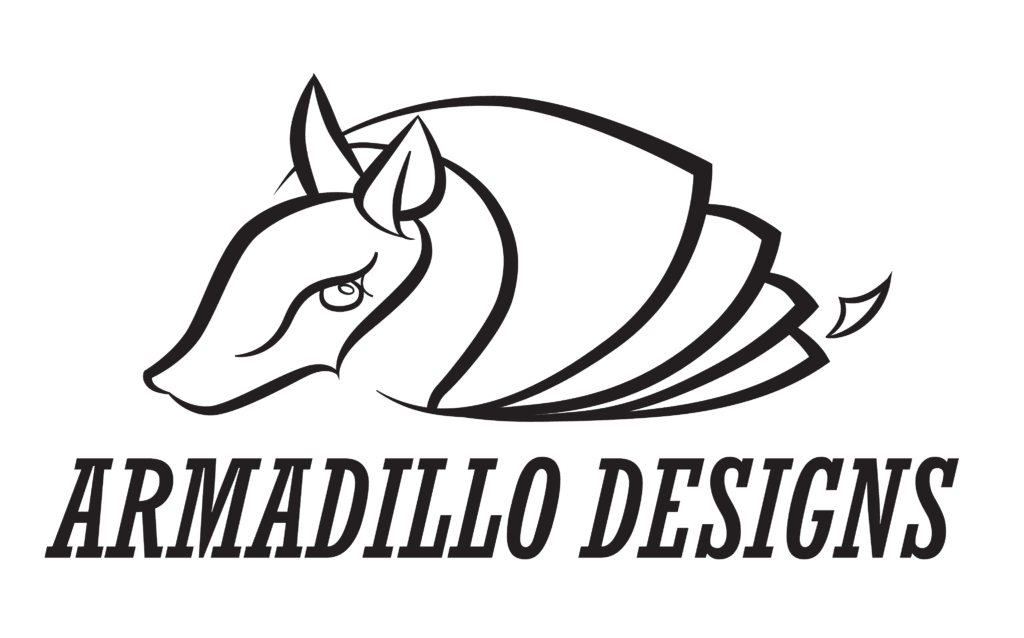
This project is sponsored by Armadillo Designs
Roof Materials
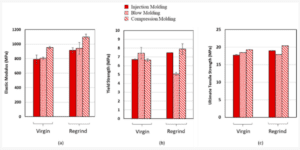
Due to its vibration resistance, machinability, and low coefficient of static friction, High Density Polyethylene (HDPE) was considered as a roofing material. HDPE Stress/Strain Graph received from (Amjadi & Fatemi, 2020)
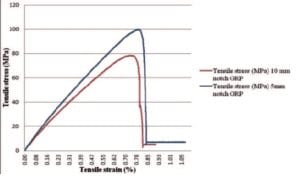
Due to being industry standard for truck shells, and having a high strength to weight ratio, Fiberglass Reinforced Plastic (FRP) was considered as a roofing material. Graph received from (Haery et al., 2012).
Material Analysis
HDPE was a top contender amongst other materials as it is very cost-effective. A 4mm thick sample had an ultimate tensile strength of about 20 MPa and an elastic modulus of about 800 MPa. HDPE is also a very slick material and will provide less sliding friction in the retractable roof mechanism. Fiberglass material is the industry standard in truck shells because it is lightweight and durable. It has excellent material properties, a 5 mm sample demonstrated an ultimate tensile strength of about 100 MPa. The downside of fiberglass is it is more expensive and brittle. If a failure event were to happen, fiberglass would break into pieces instead of deforming.
Material Tests
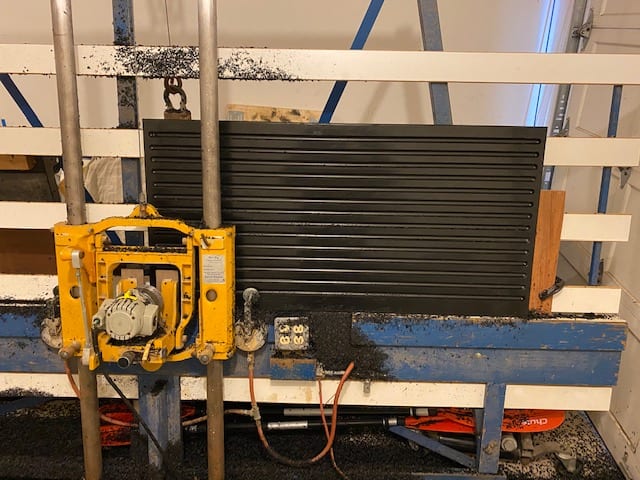
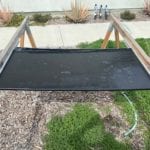
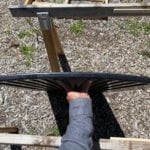
Verification & Validation
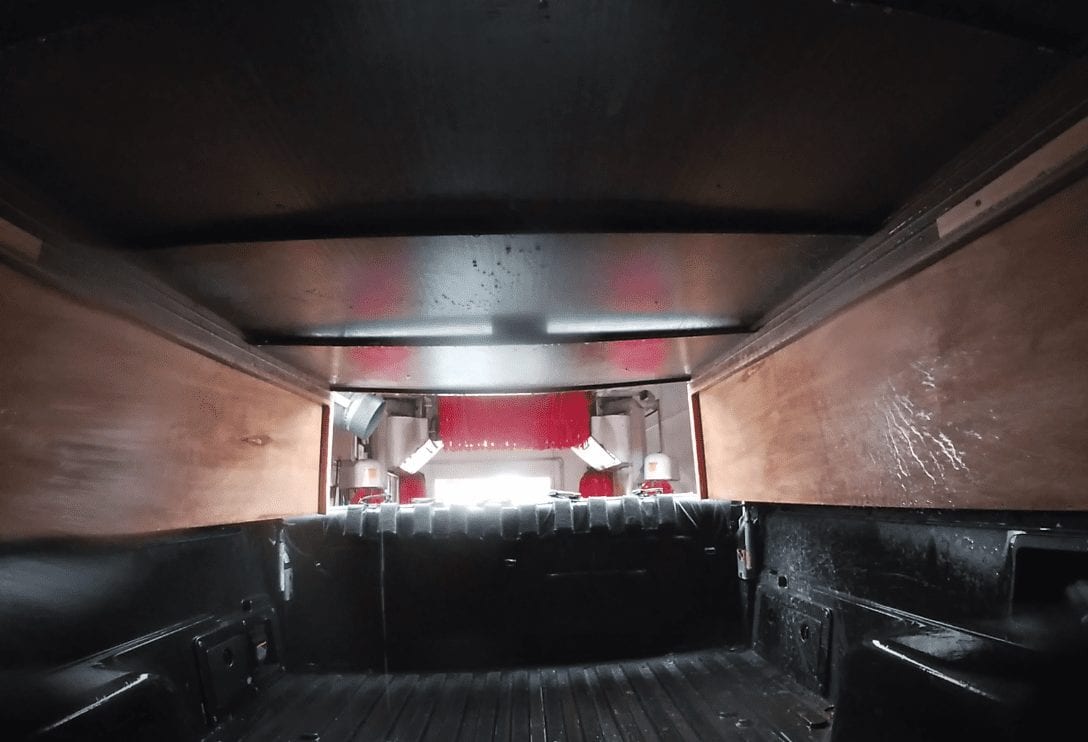
The shell was subjected to water-tightness tests, shock and vibration tests, construction site testing, as well as others.
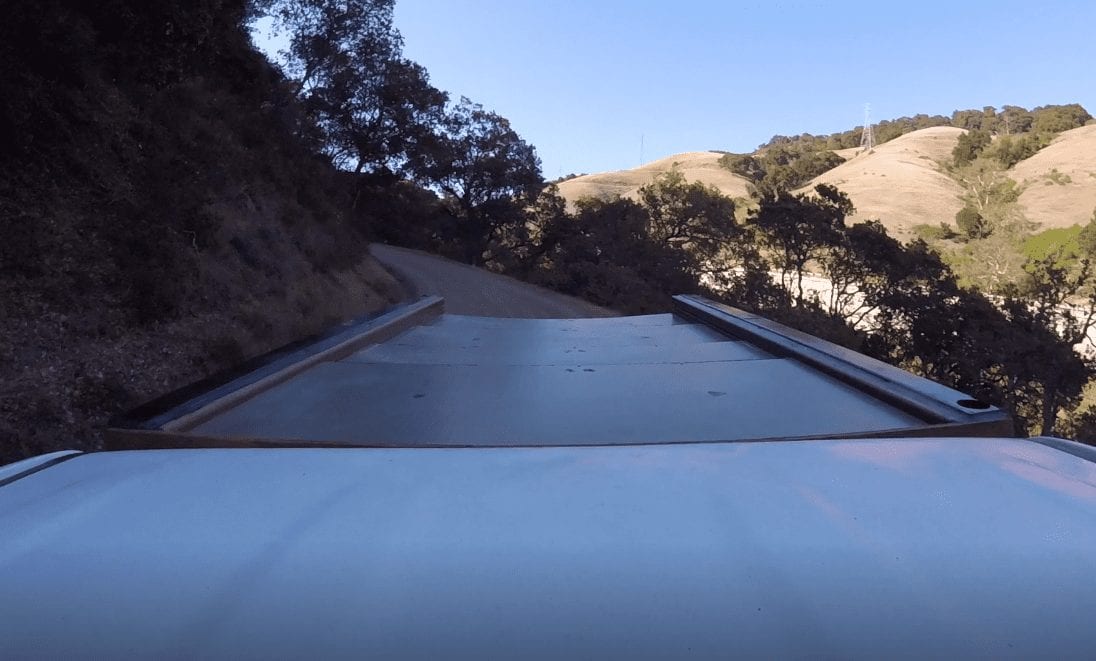
Video cameras were used to document the testing, and allow the team to analyze and observe results more closely post-testing
Verification and Validation Results
We focused on 6 criteria for our verification and validation of the convertible truck shell. The shell was tested to see if it can meet Amarillo Designs standards.
- Hog Wash – <5 water leak spots
- Drive-Through Car Wash – < 5 water leak spots
- Sun Exposure – < 1″ material deflection
- Functionality- Open/close shell in < 10 seconds
- Shock and Vibration – Observe overall durability
- Construction Site Test – Real world application
The truck shell was not able to pass the hogwash or drive-though car wash test as it showed have more than 5 leak spots. HDPE showed great deflections only after one day of being exposed to the sun. Although fiberglass panels was able to meet expectations. The truck shell was excellent during the functionality, construction site, and shock and vibration tests.
Final Design
Specifications
Weight ~200 lbs
Overall Cost – $2,147.52
# of Components – 55
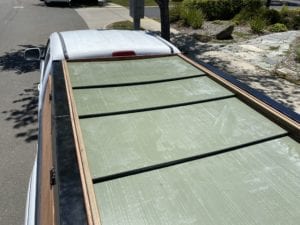
Custom Components
- Plywood Toolboxes
- Frame Rails
- Weatherproofing Strips
Stock Components
- Roof panels
- Hinges
- G-channel Rails
- Screws, Nuts, Bolts
- Washers
- Black Paint
- Toolbox Locks
Facility Layout
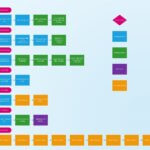
The team started with a flow process chart of all the notable steps of production for one truck shell as well as the location where the steps would take place. The team then created four rough draft layouts using Visio. With feedback from Armadillo Designs and Jill Speece, the team was able to narrow down to two layouts. The team analyzed these layouts by calculating total distance traveled to complete a truck shell using an Excel spread sheet.
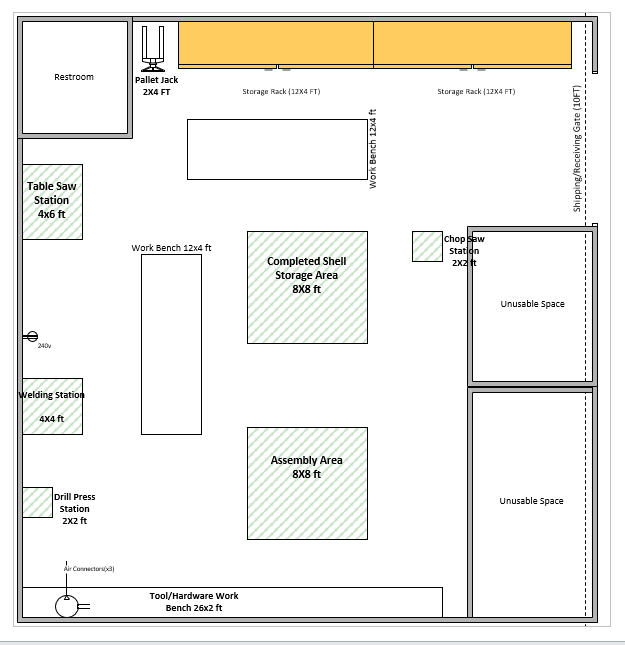
Layout 1: Total Distance Travelled 171.5 ft
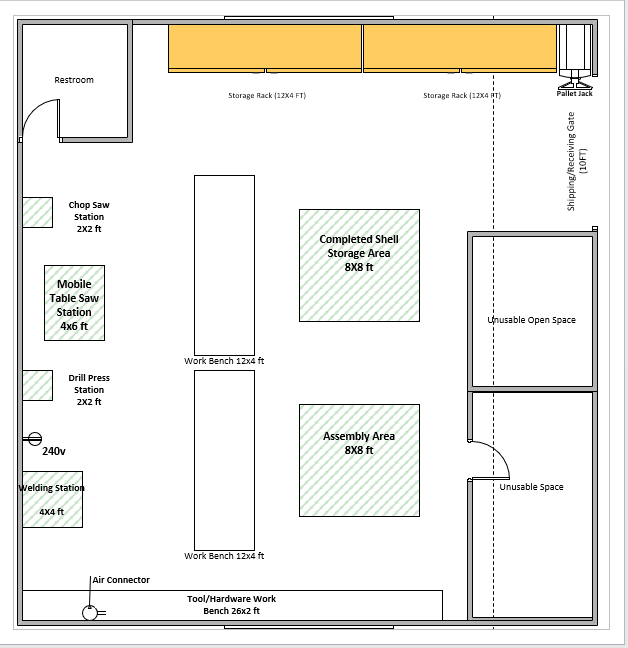
Layout 2: Total Distance Travelled 316 ft
Implemented Layout
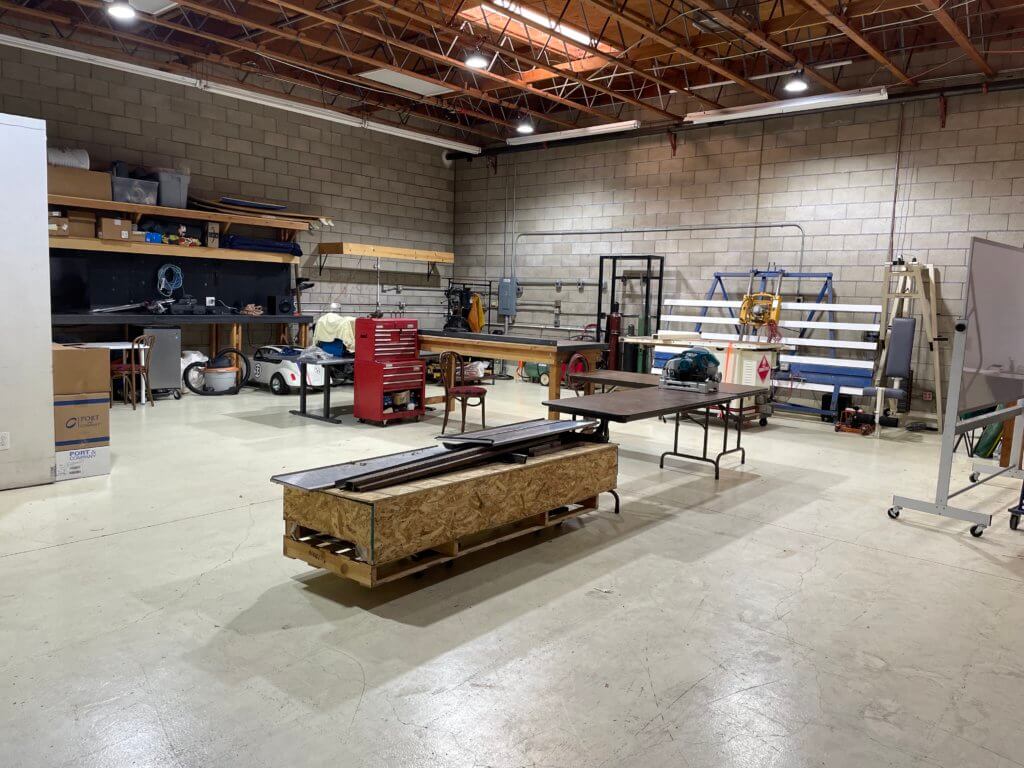
Conclusion
The team’s design was able to meet 3 out of 4 of the key metrics. The prototype cost a total of $2,023.12, well under the maximum of $2,500. The total number of parts came out to be 55 parts, and the weight of the shell ended up at 200 lbs overall. The one key metric the team was unable to meet was the total number of leak spots throughout the shell being under 5. The team concluded that this was because of the slight warpage of the fiberglass panels was detrimental to the water-tightness of the shell. Moving forward, the team recommends that Armadillo Designs keep the structure and G-channel design, but instead use an aluminum honeycomb panel. For the facility design, the team recommends going with layout #1 as it has the least amount of needed travel to complete a truck shell.
Works Cited
Amjadi, M., & Fatemi, A. (2020). Tensile Behavior of High-Density Polyethylene Including the Effects of Processing Technique, Thickness, Temperature, and Strain Rate. Polymers, 12(9), 1857. https://doi.org/10.3390/polym12091857
Haery, H., Zahari, R., Kuntjoro, W., & Taib, Y. (2012). Tensile strength of notched woven fabric hybrid glass, carbon/epoxy composite laminates. Journal Of Industrial Textiles, 43(3), 383-395. https://doi.org/10.1177/1528083712456055