Our Team
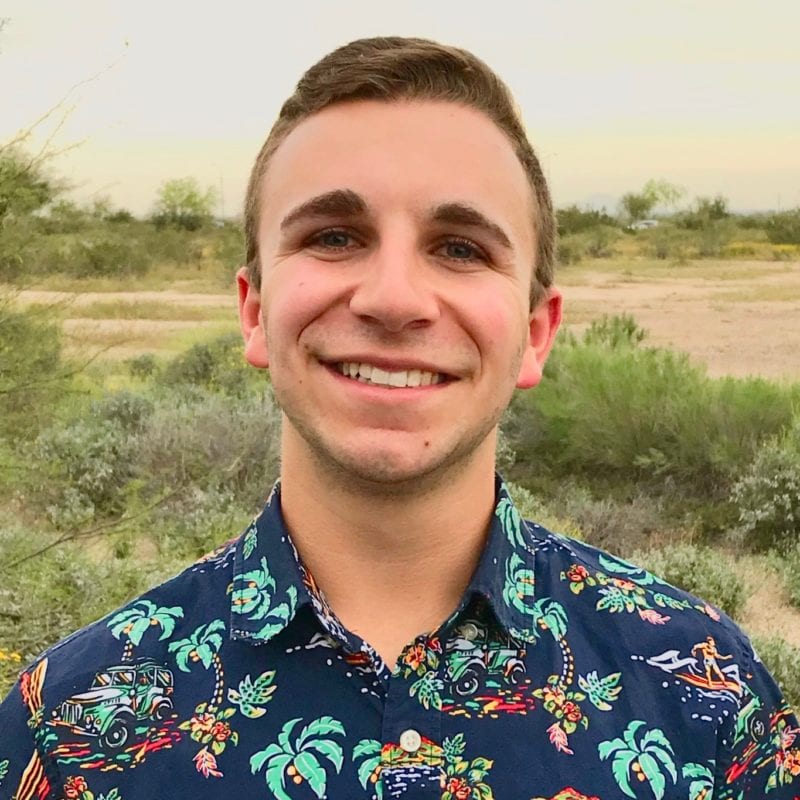
Nim
Medicine
Project manager
Nick Mediati is an industrial engineer from Moraga, CA. His main responsibilities consisted of managing communication with the sponsor, setting deadlines, design implementation, and feasibility testing.
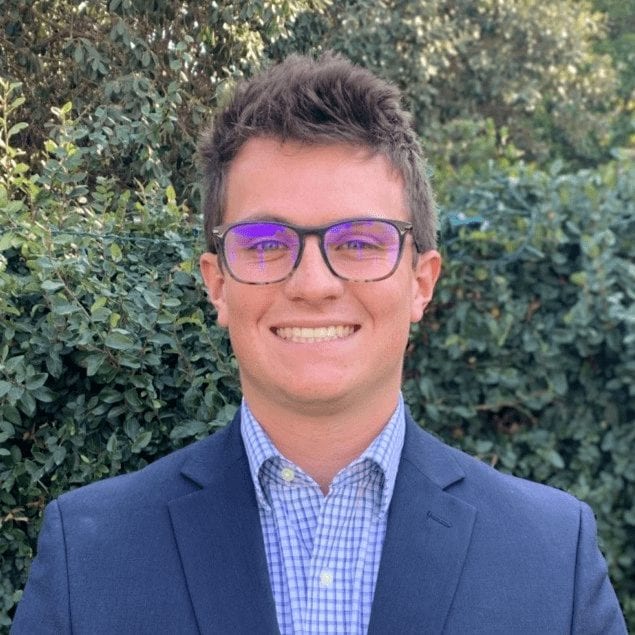
Cord
Albertsons
python programmer
Cade Alonzo is an industrial engineer from Kirkland, WA. He took on some very important roles, including process design, testing, and automation programming.
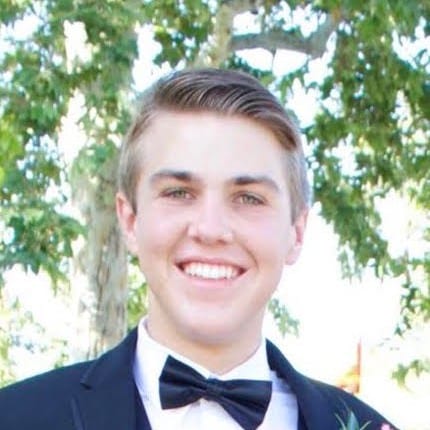
Jam
Sandisk
Design
engineer
Jack Surdyk is a an industrial engineering major from Calabasas, CA. His main roles were research, prototype design, and testing analysis.
Acknowledgements
A special thank you to our Driscoll’s sponsors Henry Yeung, Massimo Migliore, and Kat Phetxumphou, as well as our project advisor Tali Freed.
Our Project's Videos
Below is our project presentation showing our prototype in action, as well as an AnyLogic simulation of the current state of Driscoll’s BRIX juicing & recording process.
Our Project's Digital Poster
Problem Statement
Driscoll’s Watsonville, CA facility’s juicing & BRIX measuring process for berries is using overqualified workers to manually perform up to 100,000 tests per year, costing the company up to $39,300 per year in worker compensation and leading to employee dissatisfaction.
Objective
Create a self-cleaning automated system capable of juicing and straining the four major types of berries (blackberry, blueberry, strawberry, and raspberry) to be subsequently analyzed for Brix values.
Testing
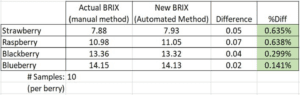
Two major tests post-prototype:
- Brix validation testing to ensure Brix values are not swayed by system.
- Deionized water test to ensure system is being effectively cleaned between tests.
Usability testing also led to slight modifications for ease of user operation (e.g. ergo-dynamic clamp for blower port).
Cleaning Sequence
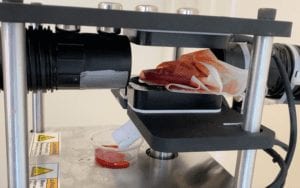
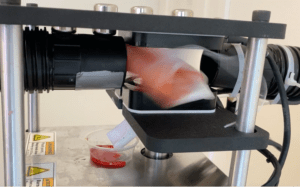
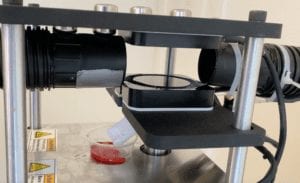
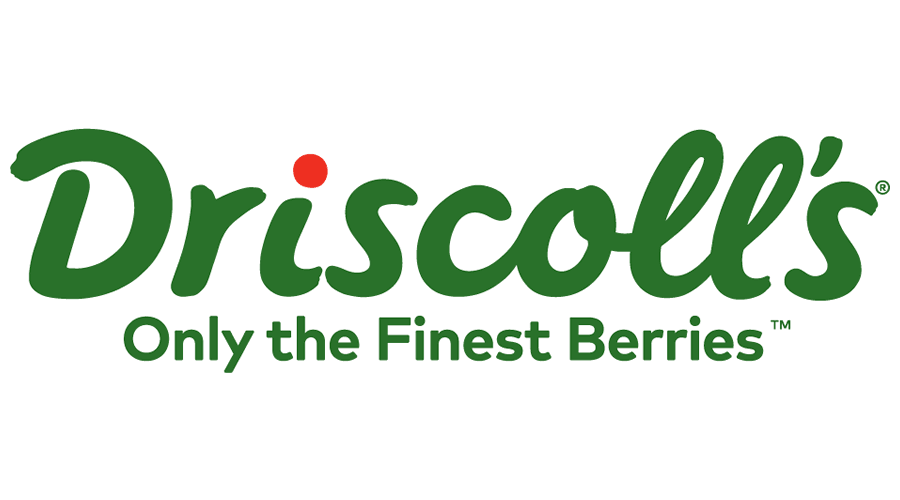
This project is sponsored by Driscoll's
Solution Design
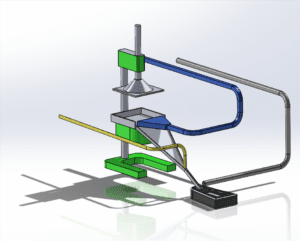
For juicing the berries, we’ve chosen to go with a vertical automated pneumatic press that provides constant pressure between two parallel plates to force the juice out of the berry.
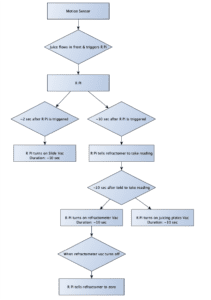
Systems architecture diagram used to build Raspberry Pi backend.
Solution Design Included:
- – AHP analysis to determine best type of juicer (vertical press) given key objectives.
- – Initial automation ideas consisted of hydrophobic coatings to guide juice flow/clean and vacuum ports to remove juice/berry excess throughout the system.
- – Systems architecture diagram for planning Raspberry Pi coding.
Implementation Plan
- Introduce system checkup/review periods to help realize pros and cons of implemented system.
- Hand over automated juicer/cleaning system with User Guide to be picked up by Driscoll’s R&D sponsors.
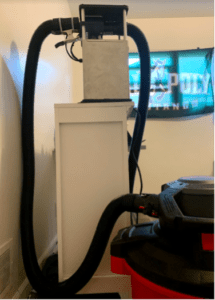
Final Design
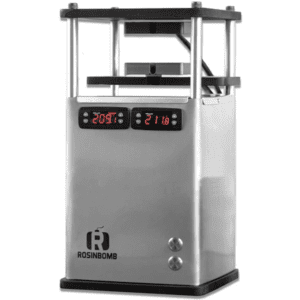
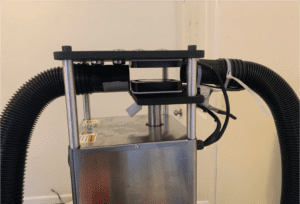
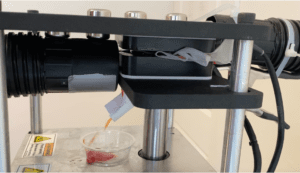
Final Design Includes:
- – Rosinbomb electric vertical press
- – Reusable mesh bags to strain berries
- – Hydrophobic juice flow channel/slide to guide juice
- – Raspberry Pi-automated blower/vacuum ports to remove the mesh bag/excess berry juice and clean the system
Conclusions & Recommendations
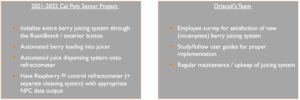
Further Recommendations:
- Further EE/CPE automation is incredibly necessary to automate entire system
- Full value of system will not be realized until full automation is reached and employees have minimal interaction with the system (besides berry loading).