Our Team
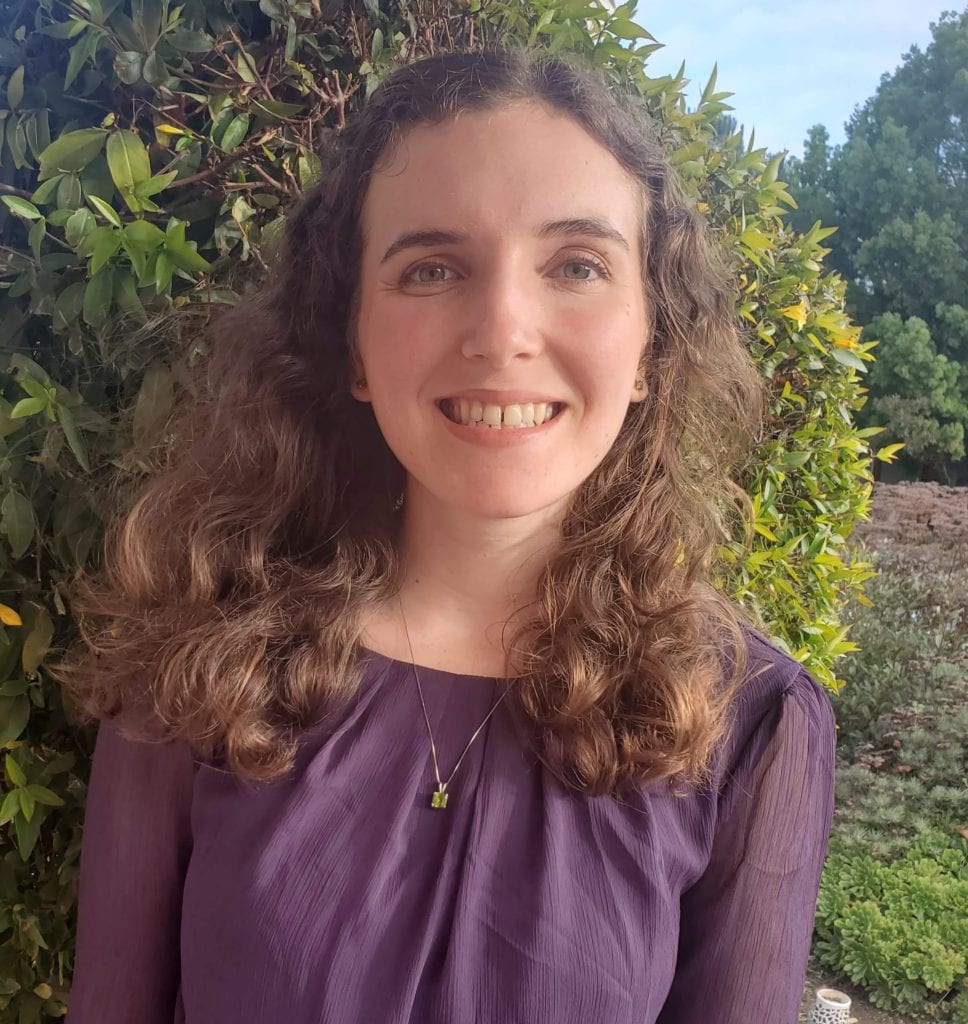
Amanda Robinson
Amanda is a 4th year Industrial Engineering student from Bakersfield, CA. She is graduating in June 2021 and will be working full-time as an Industrial Engineer in Santa Maria, CA.
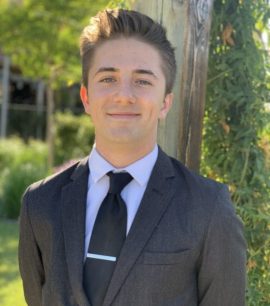
Giorgio Agostini
Gio is a 4th year Industrial Engineering student from Los Angeles, CA. He is graduating in December 2021 and will work this Summer as a Transmission & Distribution Intern for Southern California Edison.
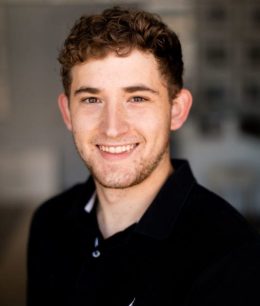
Matthew Grywczynski
Matthew is a 4th year Industrial Engineering student from Danville, CA. He is graduating in the Fall of 2021 and is working this Summer as a Sales Engineer Intern for Cisco Air Systems.
Acknowledgements
Thank you to our sponsors, Henry, Massimo, and Kat for being so supportive and awesome! Also thank you to Driscoll’s sensory technicians Sergio and Oscar for helping us out.
We would also like to thank Andrew Fleming for being our 3D printing guru and design consultant.
Lastly, thank you to Karen and Tali for all of your support throughout our project and for helping us make things happen!
Our Project's Videos
Our Project's Digital Poster
Background
- Driscoll’s technicians manually label thousands of sample cups per day for berry flavor sensory panels.
- Samples cups are labeled to differentiate between different berry varieties being tasted.
- The same process is used worldwide at other Driscoll’s locations.
Problem Statement
- Driscoll’s technicians label 4,000 sample cups per workday at the Cassin Ranch R&D facility in Watsonville, CA.
- Each technician spends an average 320 hours/year manually labeling sample cups.
- 16.67% of one technician’s working hours/year is spent labeling.
- Time spent labeling could instead be used to perform value-added tasks such as berry sampling and survey preparation.
Current State
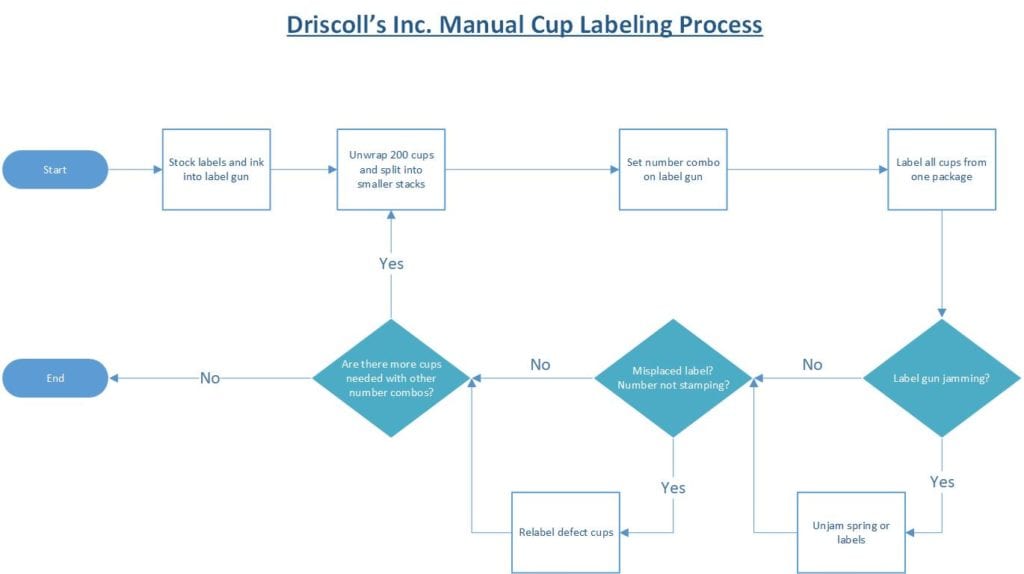
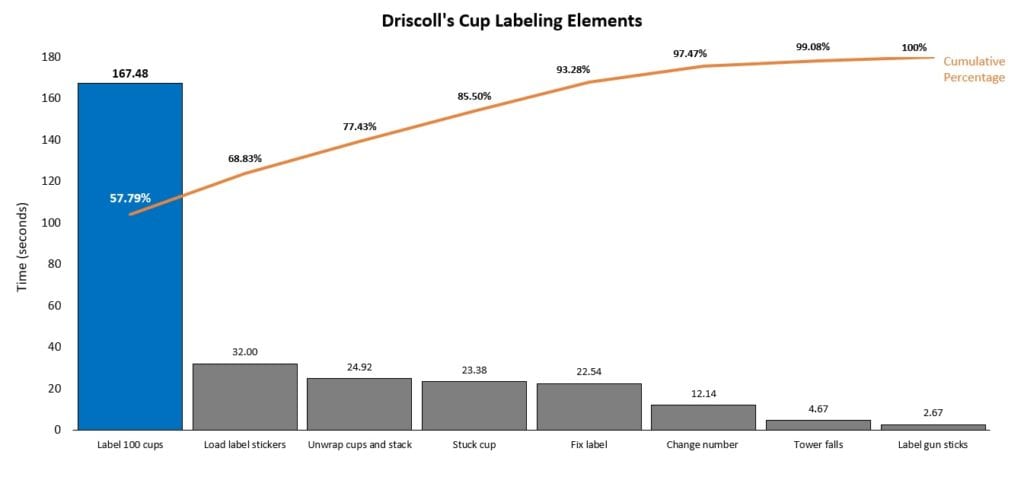
Time studies show manually labeling cups is +50% of the entire process time. Minimizing cup labeling time would save the most time and money. Increasing the labeling efficiency could also reduce error elements such as jams and defects.
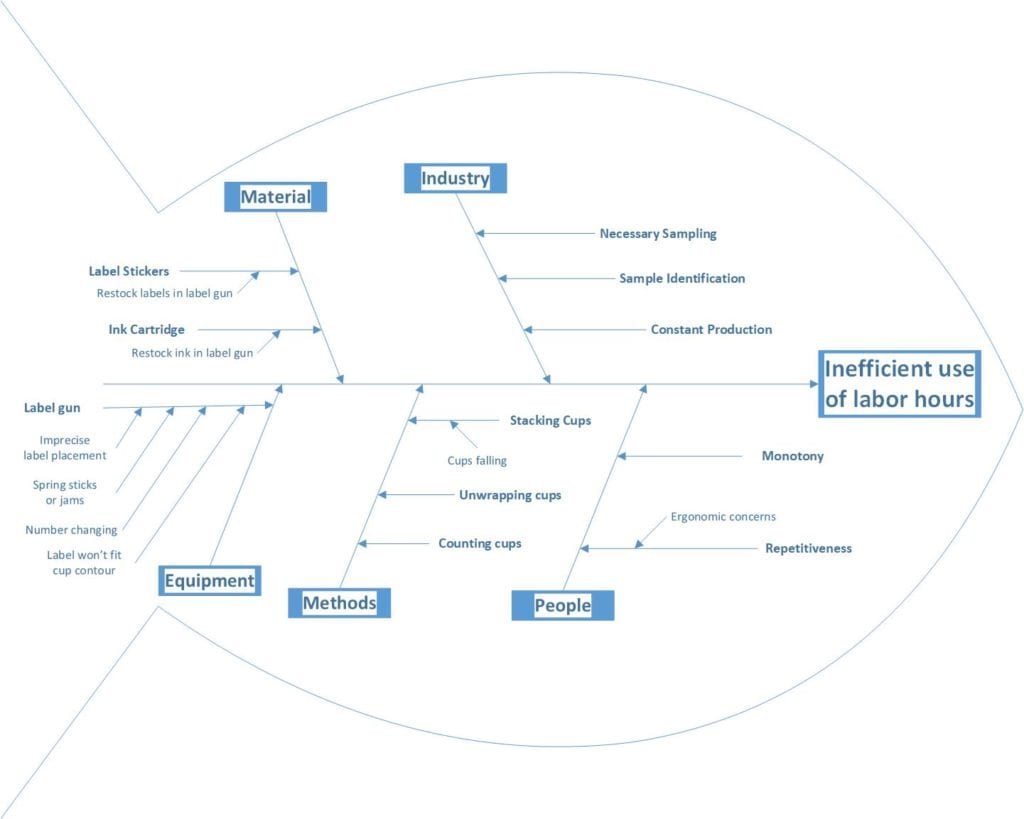
Root Cause Analysis shows that the majority of issues come from the labeling gun equipment. Replacing the manual label gun with another machine would make technician labor hours more efficient.
Project Goals & Objectives
The main goal is to minimize the cup labeling time. Instead of spending time labeling cups, technicians could be performing other valuable tasks in R&D Department.
The current label gun is manually operated, frequently jams, and slows down labeling time. It should be replaced with a more efficient labeler, like an automated machine.
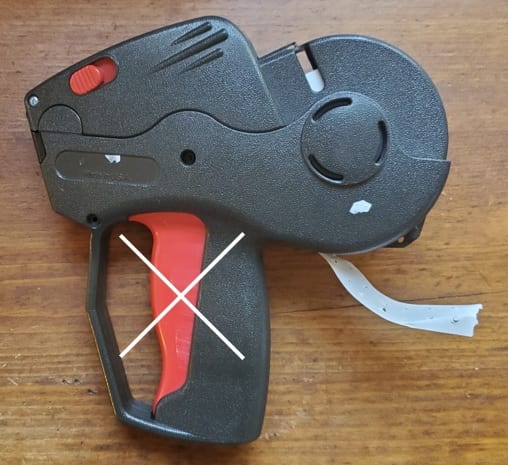
Technician feedback claimed that the label gun frequently malfunctions because of issues related to the trigger.
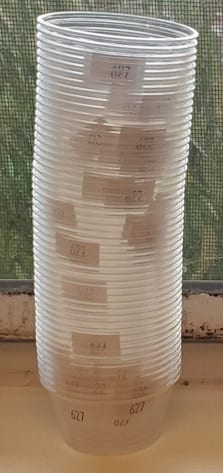
After labeling is complete, cups with the same batch number need to be stacked. A labeler that stacks cups would be preferred, or else technicians would need to stack cups.
There is one useful feature from the manual labeling gun that a new machine should provide : number-changing.
Driscoll’s needs to know the sample batches being tested, so the new labeler must be able to print any 3-digit number.
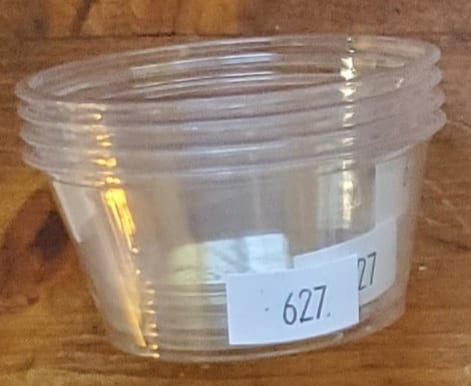
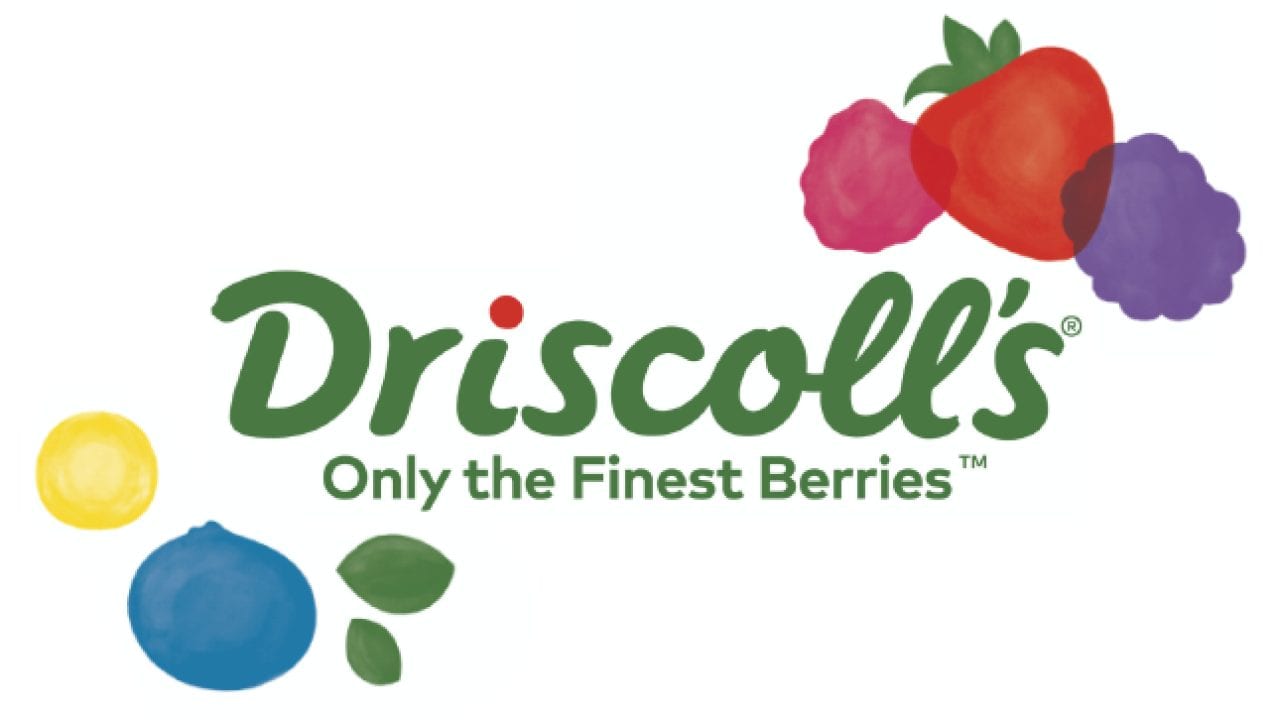
This project is sponsored by Driscoll's
Solution Alternatives
Alternative 1: Handheld Inkjet Printers
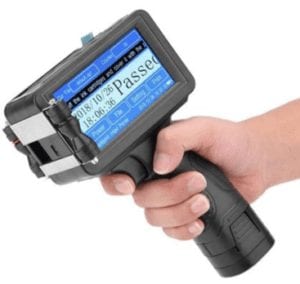
Alternative 2: Gravity Automation
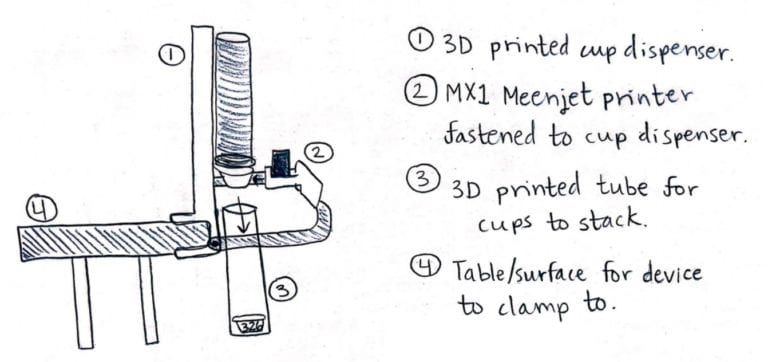
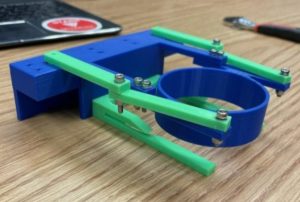
Alternative 3: Conveyor Automation
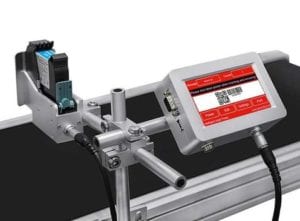
Economic Analysis
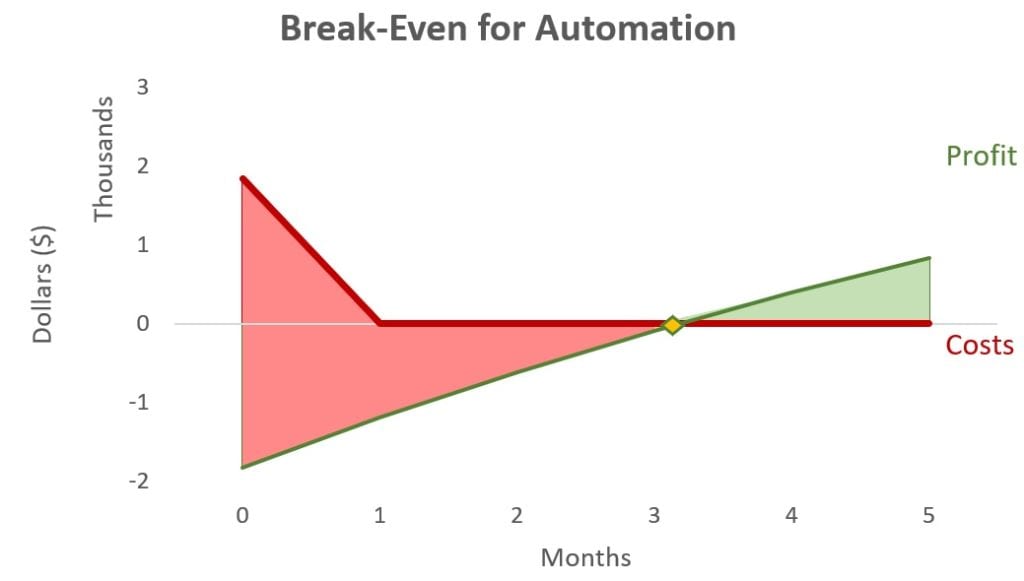
The Automation options (Gravity or Conveyor Belt) reduce the labor time by ~77%. This lowers annual operations cost so tremendously that the product has a break-even point around the 3-month mark.
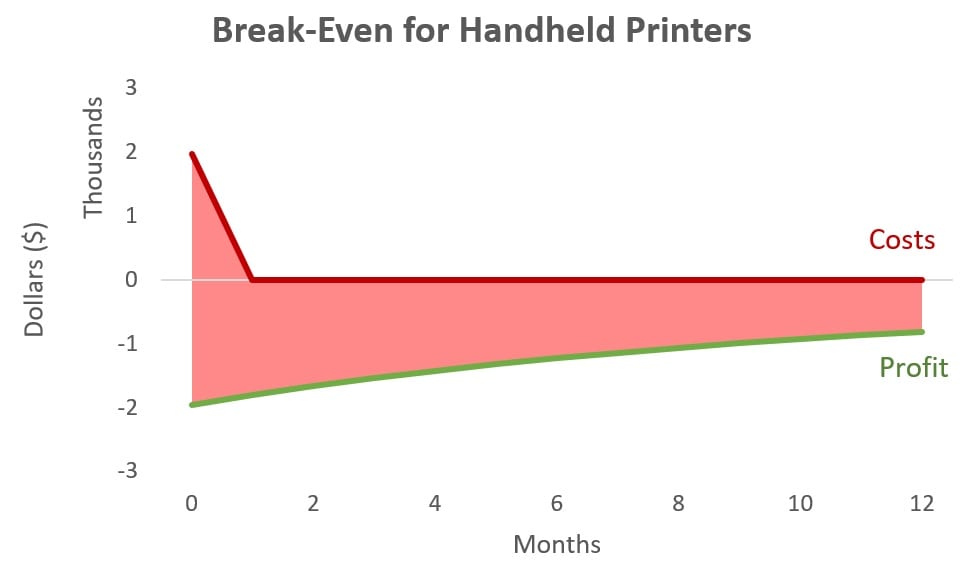
The handheld printers only reduce labor time by ~19%. The profit margin is much lower and does not break-even in the first year.
The best choice after this economic analysis is Automation.
Analytical Hierarchy Process
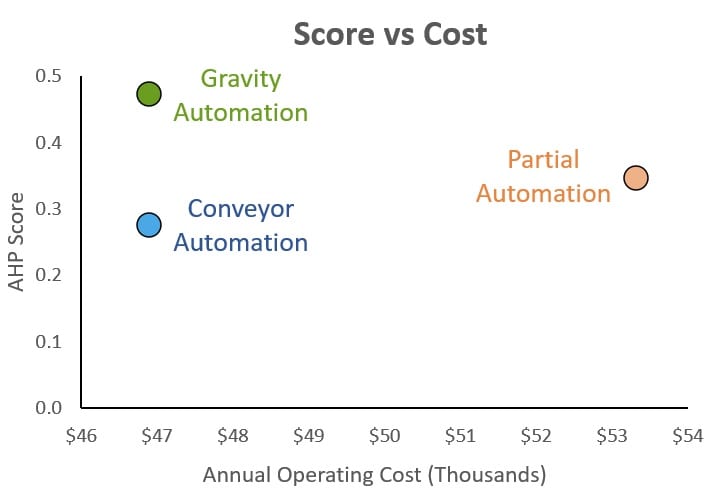
Solution alternatives were evaluated in terms of the following requirements: reduced manual labor, user-friendliness, and ease of repair.
Gravity Automation had the highest AHP score in terms of the solution requirements and the lowest annual operating cost.
Impact Analysis
Sustainability- The team examined the footprint of our project solution and found most of the materials used have a long useful life or are reusable. Beyond the useful life of the inkjet printer, most materials can still be used and only the printer will go to waste.
Ergonomics- The team’s project solution is compliant within industry ergonomic standards, i.e. it lies within the range of standards for height, reach distance, and fatigue. Additionally, risk factors such as awkward postures and bending likely won’t arise due to our solution’s process and the layout of Driscoll’s workstations.
Social- Automation can substantially increase the need for skilled, value-added manual labor. Our solution reduced hands-on labeling time for technicians, which means they can focus on more skilled, value-added tasks related to sampling.
Verification & Validation
Gravity Automation Prototyping

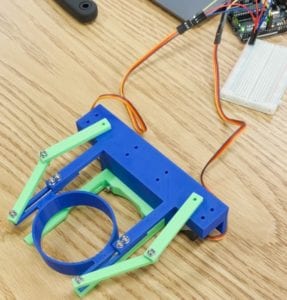
Cup Dispenser Arduino Testing
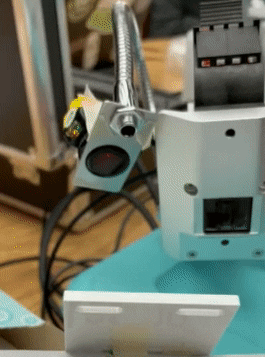
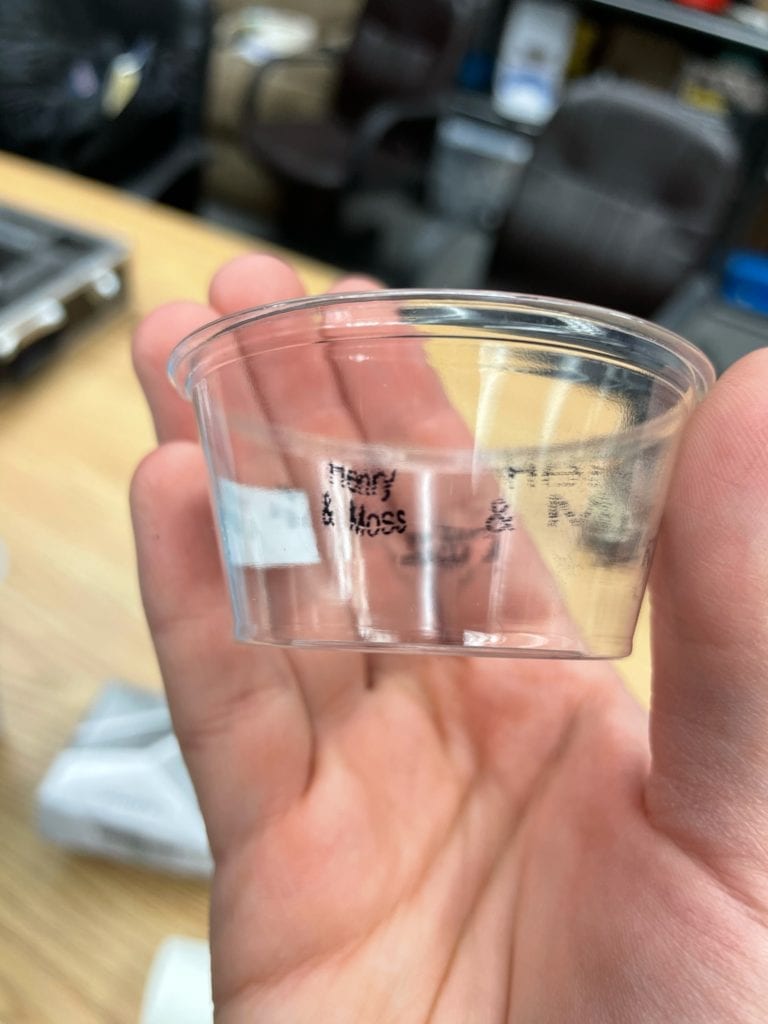
MX1 Printer Message Testing
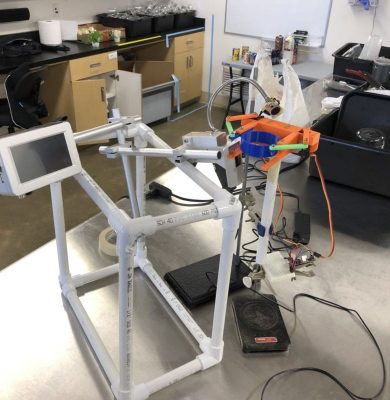
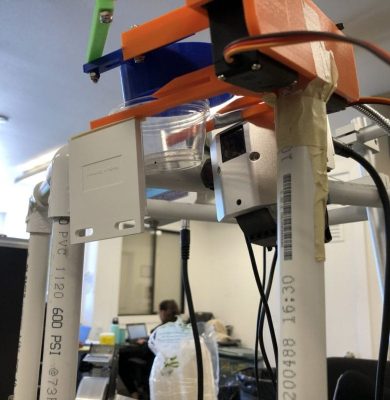
PVC Structure Set-up
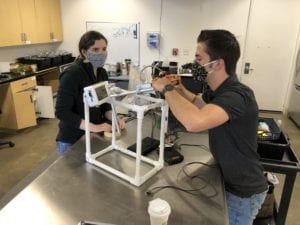
Prototyping at Driscoll’s Inc. Facility

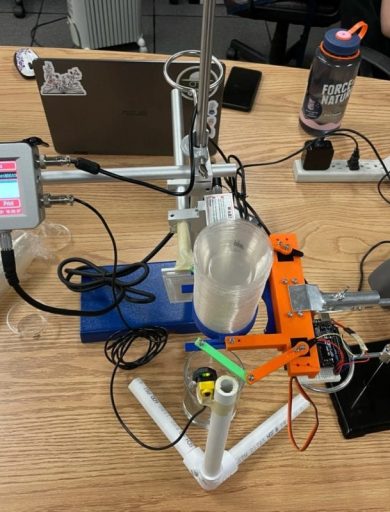
Laboratory Stand Set-up
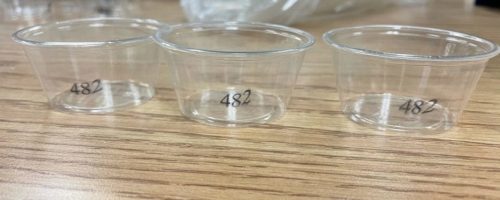
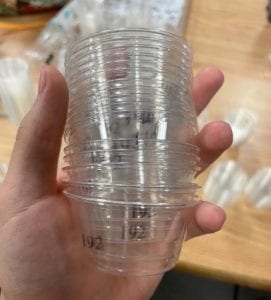
Implementation Plan
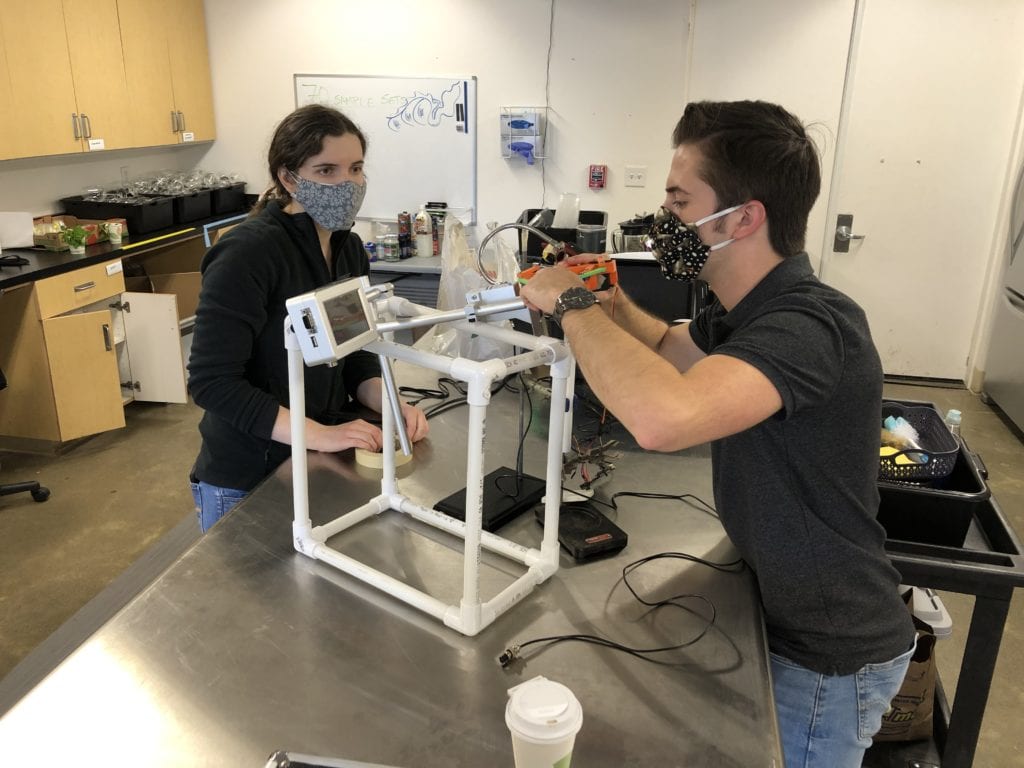
Our site visit in early May served as an important day of prototyping and observation of the Driscoll’s lab. It provided the team with clarification as to how Driscoll’s would utilize the solution device. Pictured is a middle-stage prototype of the device
Build Your Own Manual
- Assembly instructions with pictures & videos
- Help with future implementation
Training Manual
- Correct device set up and clean up
- Printer & ink troubleshooting
Maintenance Manual
- Assembly operation
- Detailed tutorials on printer settings
Future Directions
Strength – 3D print parts with stronger, more durable material (PET-G)
Features –Scale 3D printed parts to fit different sizes of cups
Scalability – CAD files, material list, and manuals to implement system at other facilities
Project Poster
