Our Team
Our team consisted of two students from the Materials Engineering Department from the Class of 2021.
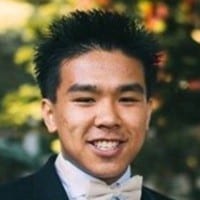
Andy Zhou
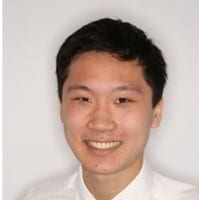
Kevin Iu
Acknowledgements
Project Sponsor: Chevron Corporation
Project Advisor: Dr. Trevor Harding
MATE Department Lab Technician: Eric Beaton
Our Project's Digital Poster
Problem Statement
For rolled AISI 1018 and 410 steel coupons in simulated seawater with a concentration of 36 parts per thousand NaCl and dissolved oxygen in the range of 0 to 650 ppb, immersed for 24 hours at 80°F and ambient pressure, Chevron is looking into the gravimetric oxygen corrosion rate of each metal as a function of oxygen content as well as how those rates compare to those determined by the OLI Studio: Corrosion Analyzer modelling software.
Background
Crude oil is valuable for its use in everyday products like gasoline and asphalt. A variety of enhanced recovery techniques are used in the oil and gas industry to maximize oil recovery from oil reservoirs. One of these techniques is called waterflooding and it involves the injection of water into oil reservoirs to maintain reservoir drive pressure.
On offshore oil platforms, seawater injection systems fabricated from carbon or stainless steel are used to perform waterflooding. The dissolved oxygen content of injection seawater is one of the major causes of corrosion in these systems. To counteract the reduction in service life that corrosion causes, seawater injection systems are typically designed to tolerate up to 4 miliinchs per year(mpy) in corrosion. The use of simulation software like OLI Studio: Corrosion Analyzer may aid the prediction of corrosion rates in these systems, but predicted rates must be confirmed with in-situ and laboratory testing.
ASTM Standards
ASTM G1: Standard Practice for Preparing, Cleaning, and Evaluating Corrosion Test Specimens
ASTM D1141: Standard Practice for the Preparation of Substitute Ocean Water
ASTM G31: Standard Guide for Laboratory Immersion Corrosion Testing of Metals
Corrosion Coupons
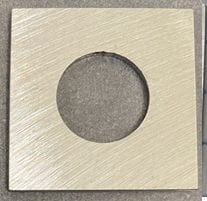
410 Stainless Steel Coupon
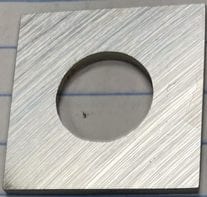
1018 Carbon Steel Coupon
Prelimnary Ultrasonic Cleaning in Isopropyl Alcohol (IPA)
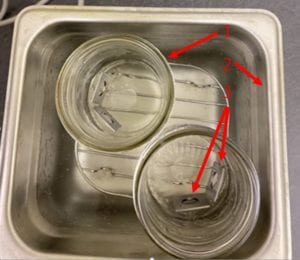
- 1. Mason Jar filled with IPA
- 2. Ultrasonic Cleaner
- 3. Corrosion Coupons
Typical Surface Micrography of Cleaned Coupons
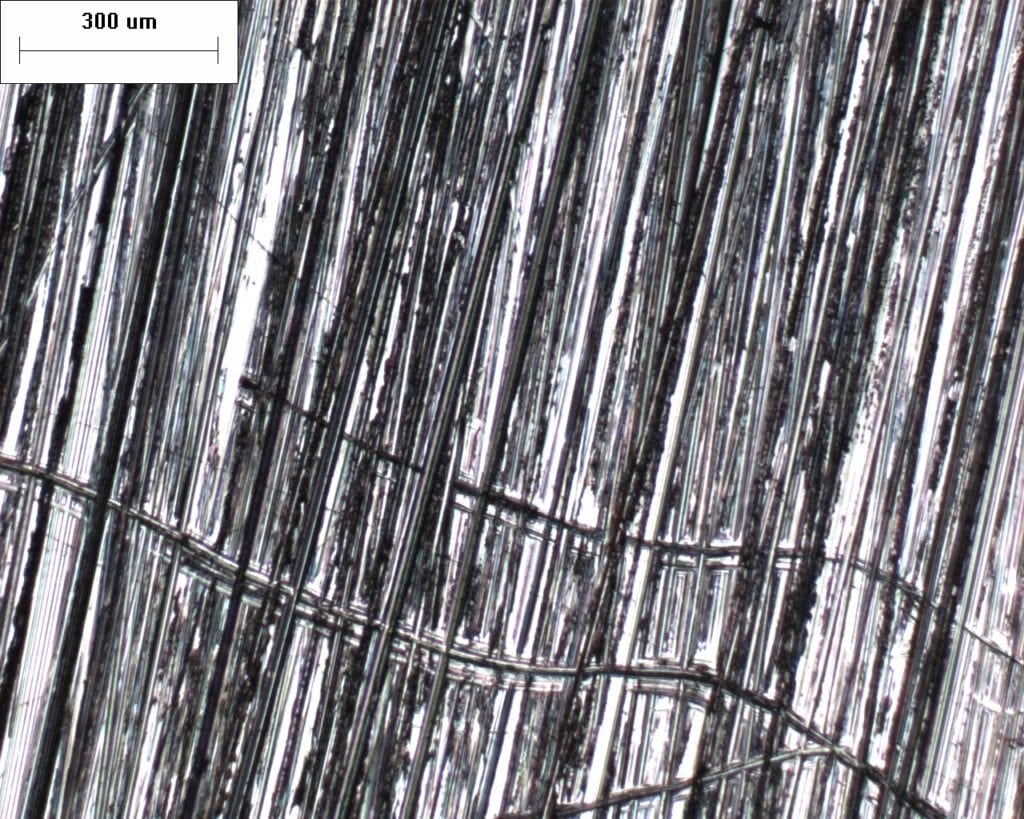
410 Stainless Steel 50x Magnification
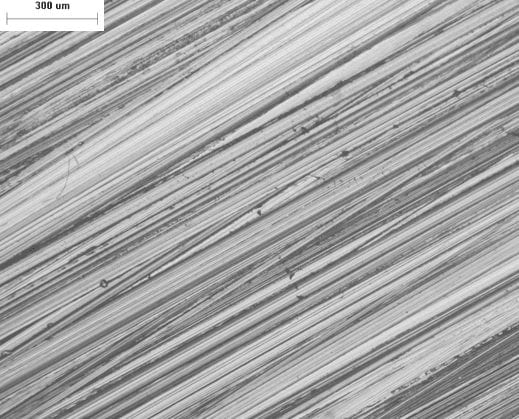
1018 Steel 50x Magnification
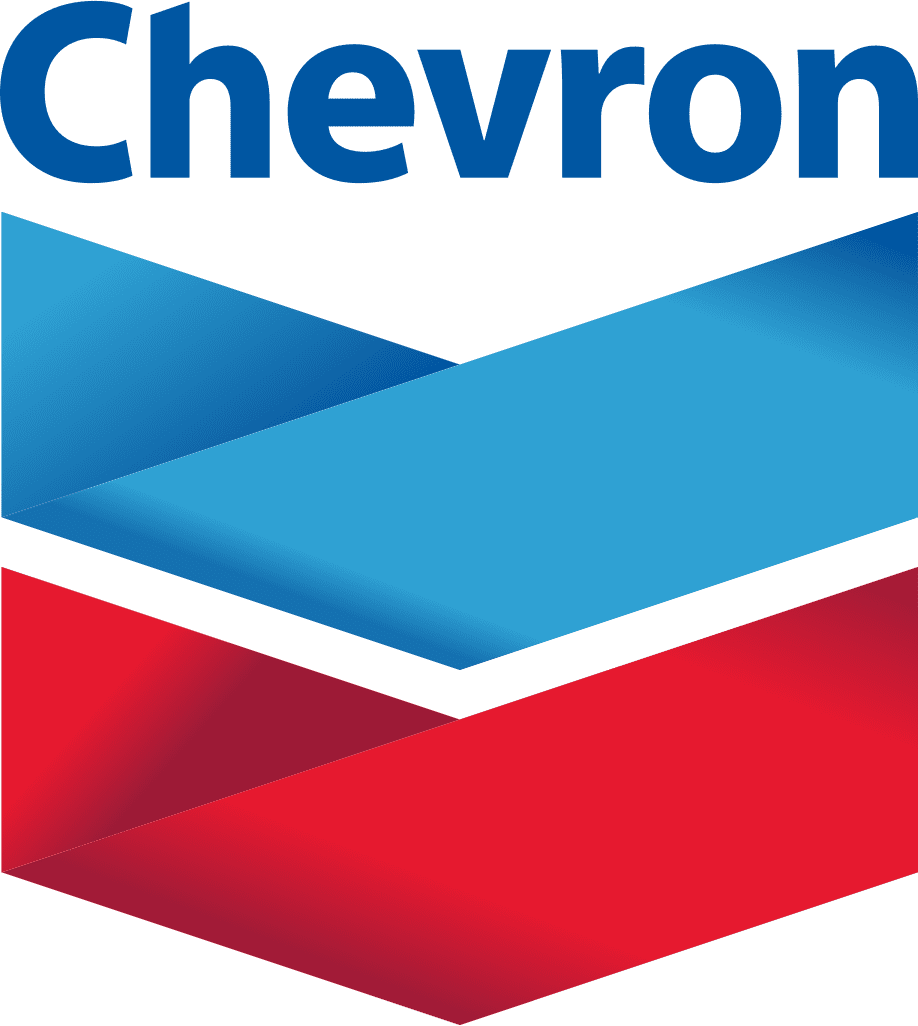
Project Sponsor: Chervon Corporation
Corrosion Cell Setup
Modified Corrosion Cell
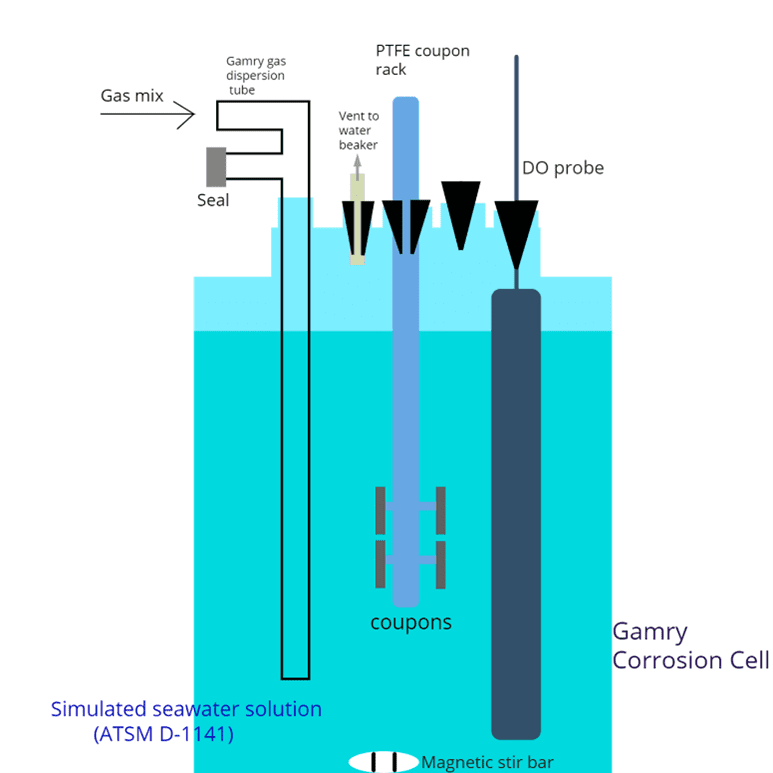
Modified MultiPort Gamry Corrosion Cell Kit
Heating Water Jacket Design
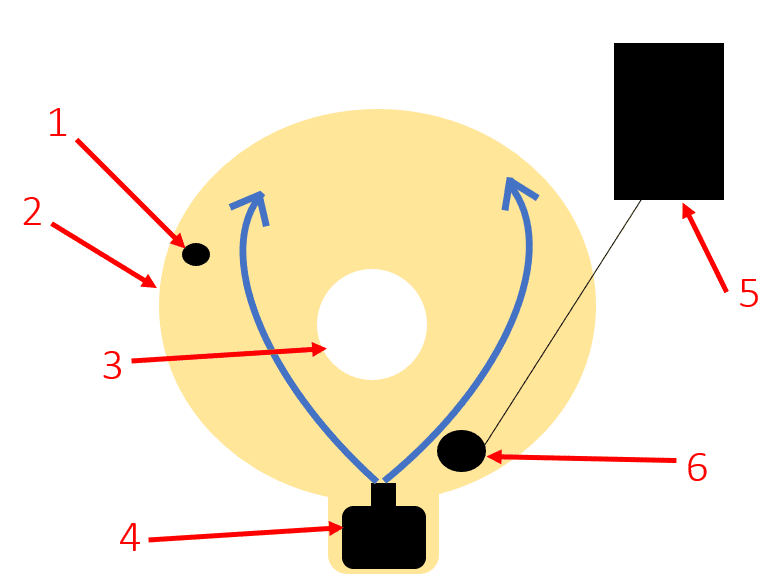
- 1. Temperature Probe
- 2. Water Jacket
- 3. Corrosion Cell
- 4. Water Pump
- 5. 2-Step Temperature Controller
- 6. Water Heater
Sparging Gas Setup
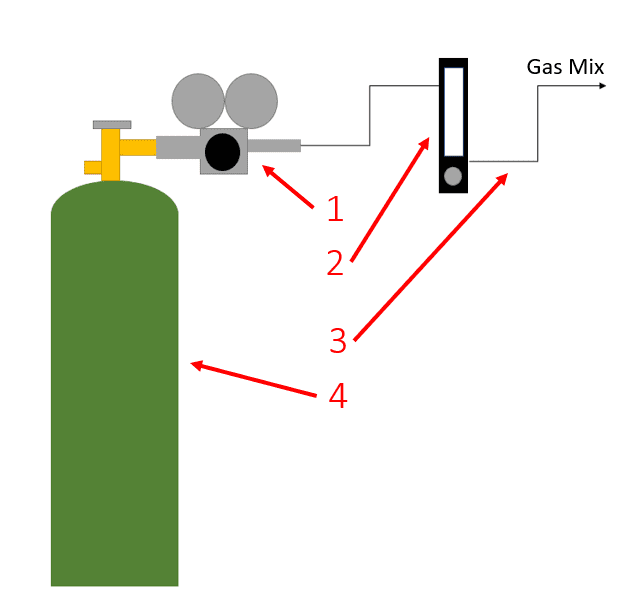
- 1. Gas Cylinder Regulator
- 2. 0.1-1.0 Lpm Flowmeter
- 3. Tubing
- 4. Mix Gas Cylinder
ASTM G1 Cleaning Solutions
Carbon Steel
- – 500 mL HCl
- – 2g hexamethylenetetramine (inhibitor)
- – Distilled Water
Stainless Steel
- – Distilled Water
Results
1018 Carbon Steel
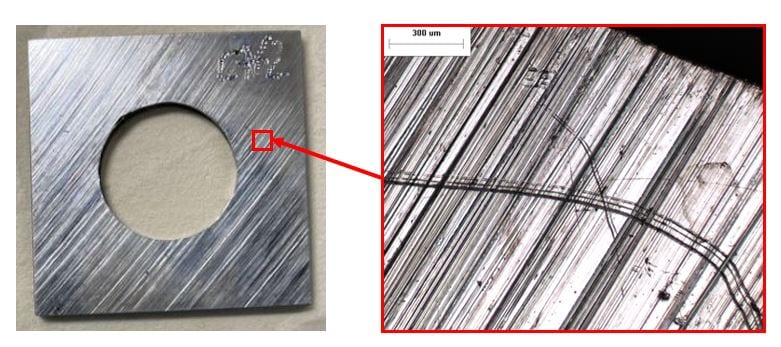
0 ppb DO seawater 50x. The surface appears to be uncorroded.
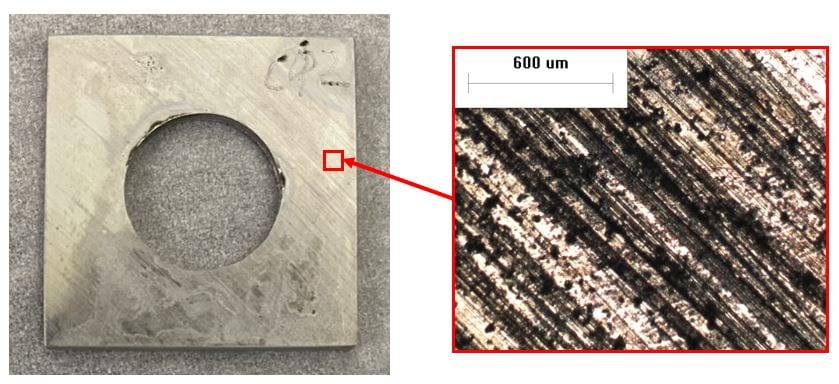
65 ppb DO seawater, 50x. General corrosion is present.
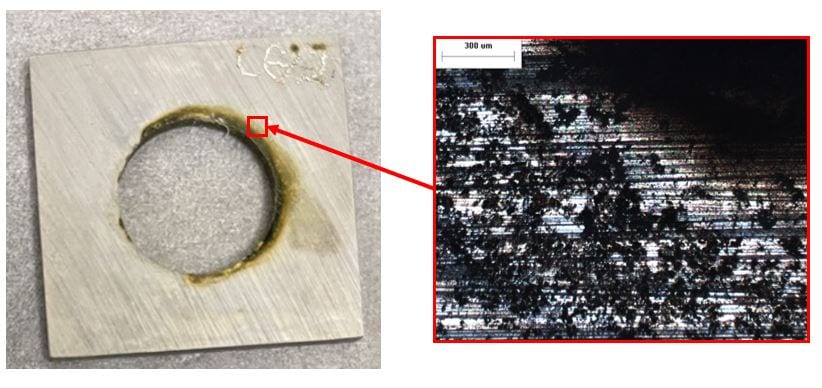
650 ppb DO seawater, 50x. Localized corrosion around the crevice between the coupon mount and coupon hole is present.
410 Stainless Steel
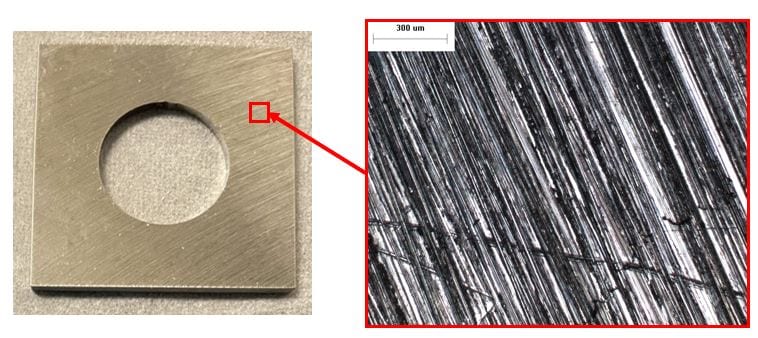
0 ppb DO seawater 50x. The surface appears to be uncorroded.
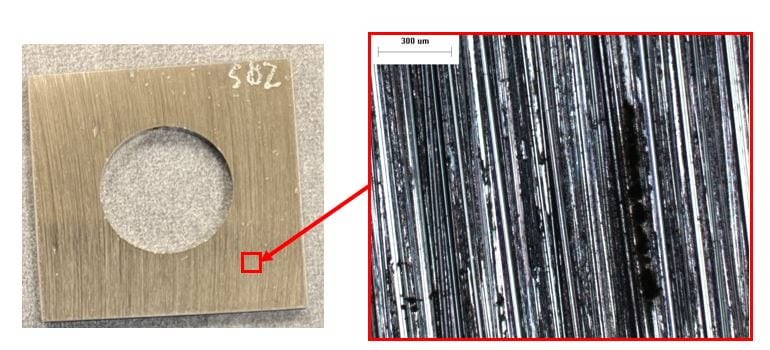
65 ppb DO seawater, 50x. Streaks of localized corrosion are observable with the naked eye.
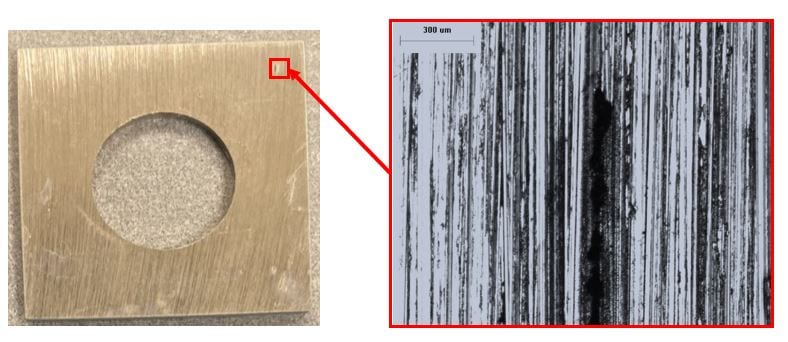
650 ppb DO seawater, 50x. More streaks of localized corrosion than observed with the coupons in the 65 ppb DO condition are present.
Comparison of Gravimetric Corrosion Rates to Simulation Rates
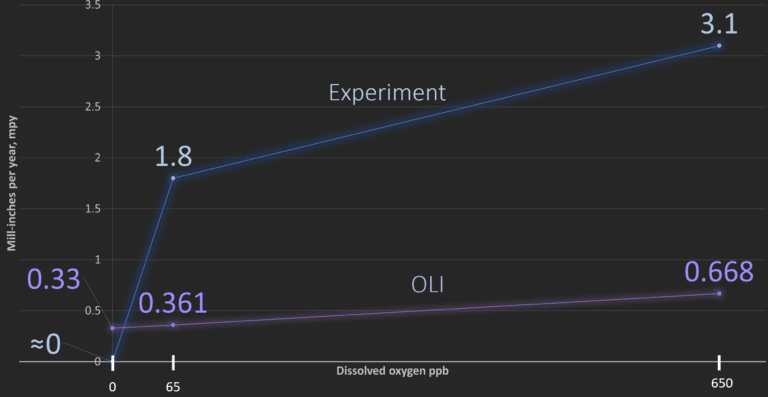
Plots of Experimental corrosion rates in carbon steel versus OLI Studio: Corrosion Analyzer prediction rates for each level of dissolved oxygen.
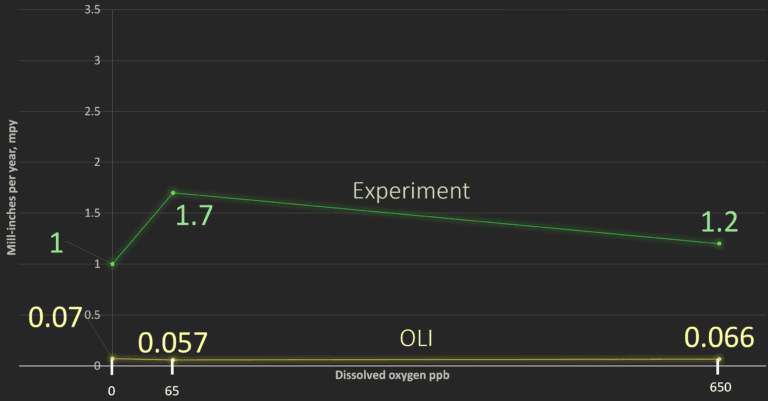
Plots of Experimental corrosion rates in stainless steel versus OLI Studio: Corrosion Analyzer prediction rates for each level of dissolved oxygen.
Conclusions
- 1. OLI Studio underpredicted corrosion rates for both carbon and stainless steel
- 2. Even at 650 ppb DO, neither metal experienced a corrosion rate >4 mpy