The ISEC team
Meet the engineers behind the project
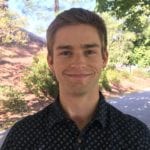
Simon Ford
Simon is a Mechanical Engineering senior. Simon loves being outdoors and riding his bike. His favorite part of senior project was the initial design iterations were the team built prototypes, brainstormed and though outside the box. After graduating, Simon will be joining the Harris & Sloan team in Sacramento, CA as a Mechanical Design Engineer focusing on MEP.
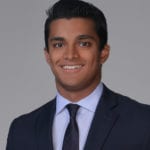
Sachin Gokhale
Sachin is a Mechanical Engineering senior with plans to continue his Cal Poly education in pursuit of a Master’s degree in the fall. His favorite part of senior project was the creative ideation and initial development of the product. After graduating, Sachin looks forward to starting a band and working in mechanical design as he begins his professional career.
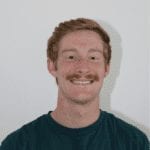
Brendan Lynn
Brendan is a Mechanical Engineering senior at Cal Poly graduating in the fall. His favorite part of senior project was working on interesting engineering problems with a close group of teammates. After graduation, he plans to work in renewable energy close to home in Northern California after traveling to Europe. In his free time he plans to continue playing sports, mountain biking, and exploring.
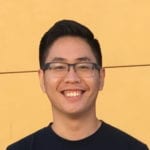
Richard Nguyen
Richard is a Mechanical Engineering senior at Cal Poly. His favorite part of senior project was working in an environment where everyone brought different skills to contribute to a common goal. After graduation, he plans on doing some travelling and working on home projects.
Acknowledgements
The ISEC team would like to acknowledge our sponsor, Pete Schwartz for his kindness and trust in us throughout the process. Additionally, we would like to acknowledge Tahry and all of the shop techs who lent a hand during our project.
ISEC Digital Expo Poster
Background
Each year, two million people die as a result of burning biomass fuels to cook or even heat their homes. This is where ISEC (Insulated Solar Electric Cooking) has the potential to change the world as we know it. ISEC stands for insulated solar electric cooking. Since 2015, Dr. Pete Schwartz and his team at California Polytechnic University, San Luis Obispo have been developing insulated cookers that are inexpensive and have the potential to provide clean cooking means for people in every corner of the world.
Engineering Specifications
Spec 1 – Easy to assemble – This spec was tested by assembling the ISEC with as few tools as possible and timing the process.
Spec 2 – Inexpensive – This spec was tested by summing the costs of all the equipment and materials required to build the ISEC.
Spec 3 – Insulated – This spec was tested by using a thermocouple to record the temperature of the outside of the ISEC during and after cooking.
Spec 4 – Large internal volume – This spec was tested by calculating the internal volume of the assembled ISEC.
Spec 5 – Durable – This spec was tested through daily cooking, transportation and storage with a inspection for wear/faulty components.
Spec 6 – Thermal conductivity – This spec was tested by measuring temperature change of boiling water and using a constant current power supply to hold the power constant.
Concept Sketches
Preliminary Design
The vacuum-seal on the inner pot is a design concept directly requested from our sponsor, Dr. Schwartz.
The press-fit locking mechanism was designed to keep the inner pot stable during transportation and to bolster the overall safety and durability of the device.
The fiberglass insulation on the lid was yet another solution designed to minimize heat loss. Fiberglass is inexpensive and paired with a ring lock top, will provide ample insulation.
The thermal fuse and thermal switch are safety features designed to regulate the temperature of the ISEC. The thermal switch will turn off at 180 ℃ and will turn back on at temperatures below 140 ℃, and the thermal fuse is destroyed at 220 ℃ which will interrupt the electric current.
The modular storage design allows the solar panel and the ISEC to be stored as one single unit. This improves the overall functionality of the device.
Further Reading
Professor Schwartz has been working on this project for many years with many different students, professors and people all around the world. He has a fantastic website that has more information on how to build an ISEC, their research into better methods of solar storage and all of the successful and unsuccessful attempts. Below is link to learn more!
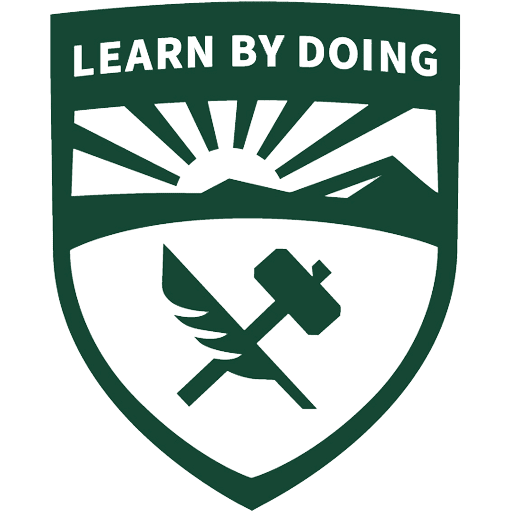
This project is sponsored by
Cal Poly Physics Department
Preliminary Sketch
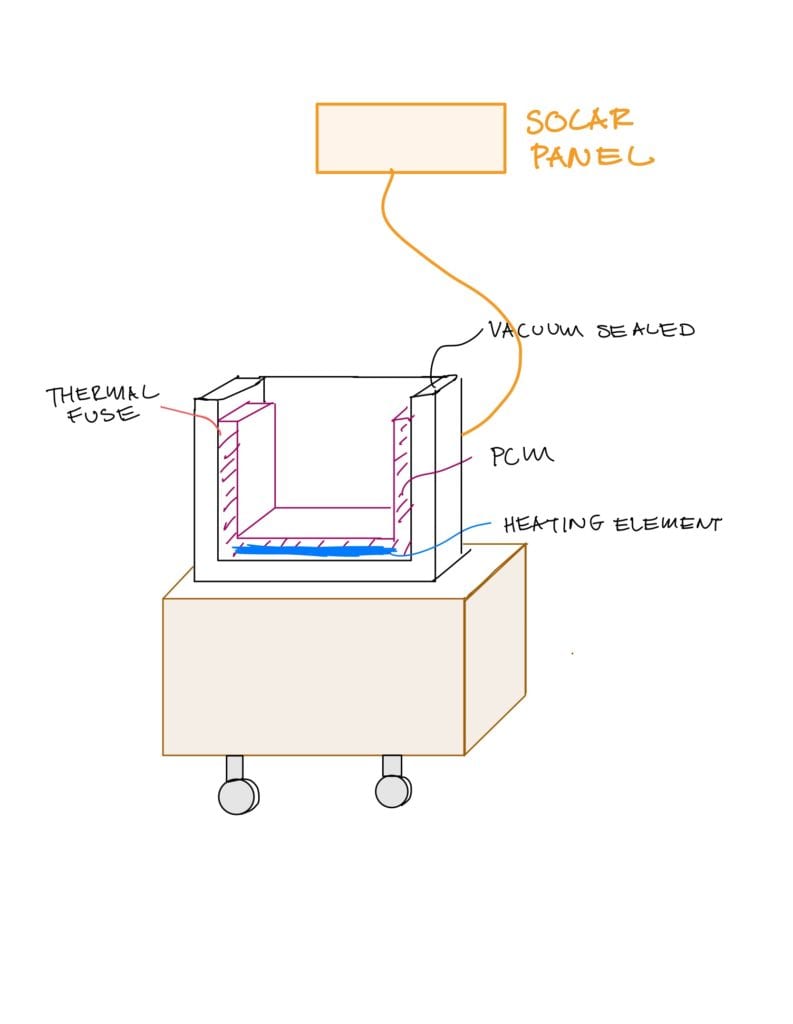
Our preliminary design included an ISEC and solar panel that would be mated so they could be transported easily as one piece. In addition a stand would be made to transport the ISEC. The inside of the ISEC would have a ring lock to ensure the cooking pot would not move, as well as a fiberglass top to improve insulation.
Using the ISEC to cook
Test Setup
Verification Prototype: Testing
Heat Loss Through Top – We measured the heat loss through the top of the ISEC by pouring boiling water into a stock vacuum sealed container with different tops and measured the rate at which the temperature decreased.
Ease of Building – This test was carried out while the PCM (Phase Change Material) ISEC was being assembled. The equipment needed includes all the parts needed to build the PCM ISEC as well as a stopwatch to log the time elapsed. The final time to build, without dry time, is 3 hours.
Cost – The ISEC must be inexpensive to build. The team kept a log of the cost of all materials needed to build the entire ISEC. Excluding labor (and the solar panel) the final cost was $71.25. This falls under the specified budget, but a solar panel costs around $100 extra so this must be taken into account.
Thermal Conductivity of Container – With the resistive heater hooked up to the DC power supply, a steady state internal temperature was achieved by modulating the power input. Once this point has been achieved, the temperature difference at this moment in time is used to calculate the thermal resistivity. This is similar to a hot box test used to find the resistivity of walls in a home.
Final Design
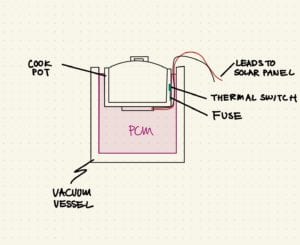
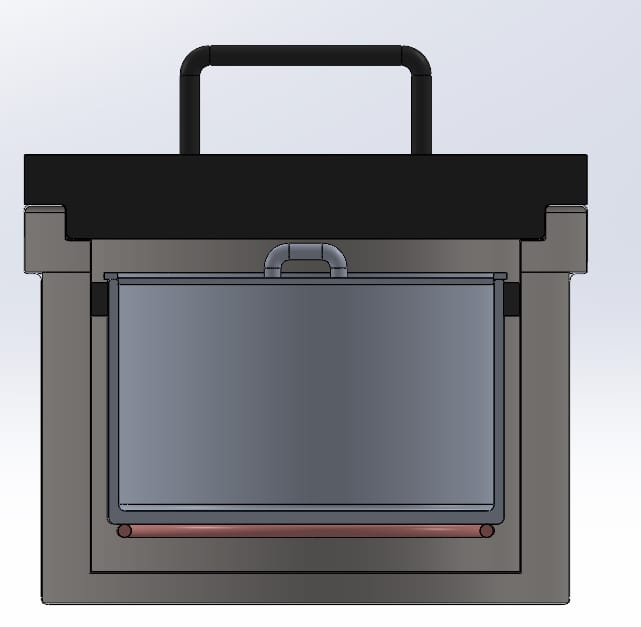
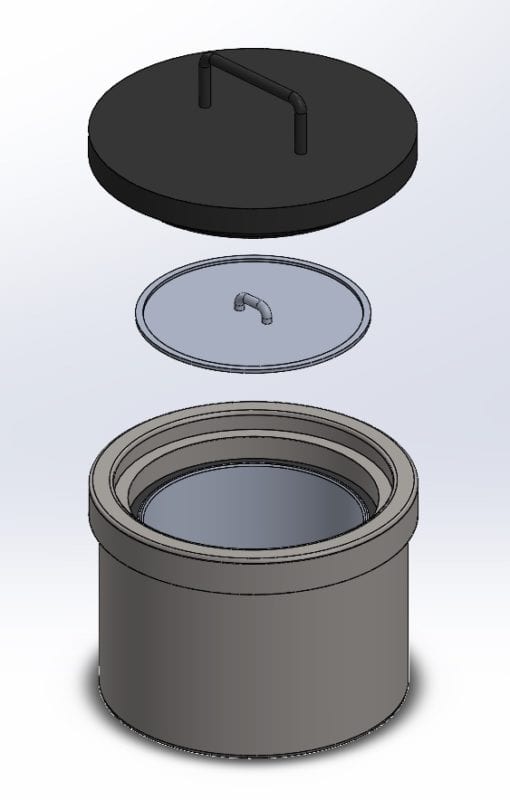
Testing Results
Specification Description | Requirement/Target | Test Result |
Easy to assemble | < 4 hours | 3 hours |
Inexpensive | < $100 | $71.26 |
Insulated | < 70 ℉ on outside | Cool to the touch |
Large | Approx. 300 in3 internal vol | 150 in3 |
Durable | > 10 ft drop test | Durable through daily use |
Thermal conductivity I | k < 0.15 W/K | k = 0.12 W/K |
Thermal conductivity II | k < 0.15 W/K | k = 0.114 W/K |
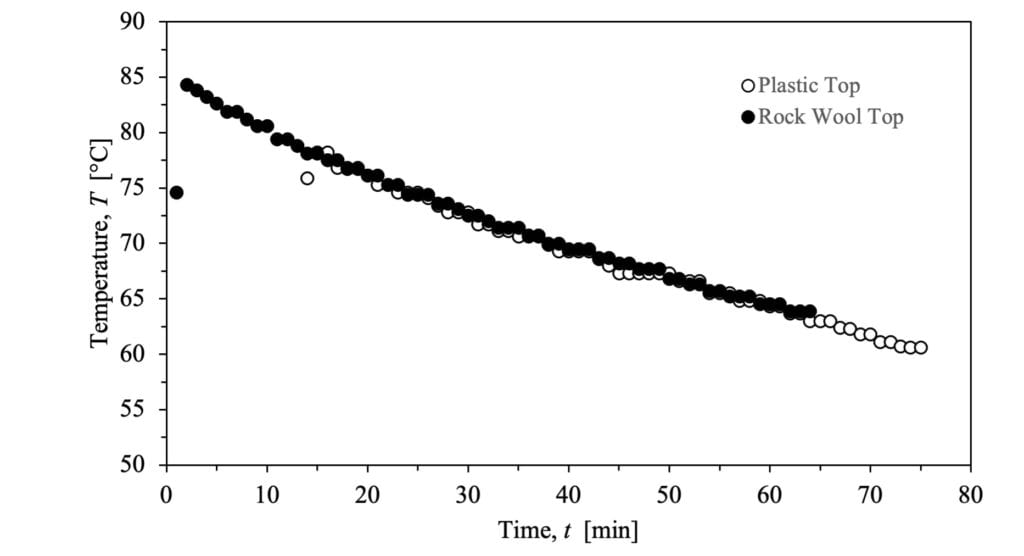
Although the ISEC itself performed similarly to previous iterations, the new Rock Wool top ultimately did not greatly improve the thermal insulation. However, other types of insulation are currently being explored including other rock wool derivatives and the potential to return to fiberglass given the good price and fire retardant properties.
Future Application
- The ISEC research team lead by Professor Schwartz will continue to investigate sodium nitrate as a replacement PCM to Erythritol, as well as better insulation solutions for both vaccum sealed vessels and other forms of the ISEC. After our efforts, the ISEC is more aesthetic, safer than the previous models and proves efficacy of the vacuum sealed pot as a vessel. The rock wool insulation top did not prove to be the best option for the top of the PCM ISEC after only performing slightly better than the stock plastic lid of the Stanley vacuum sealed container.