Our Team: The space cowboys
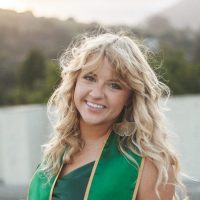
Emily Martin
Project Manager
Emily Martin is a 5th year Industrial Engineering transfer student who calls San Luis Obispo, CA home. She worked at JPL as an intern in the Summer of 2020 and acquired the contacts to make this project happen. Her main role on the project was being the Project Manager, which entailed being the main point of contact between JPL and the Space Cowboys, keeping the project on track, planning group events, and reaching out to the engineers and inspectors at JPL for interviews and meetings. Some of her hobbies include road biking, crocheting, and hiking. Following graduation, Emily will move to Pasadena, CA and start as a full time Process Improvement Engineer at NASA JPL.
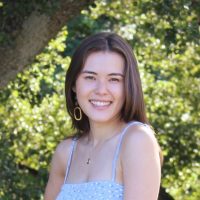
Camille Garlick
Project analyst
Camille Garlick is a 4th year Industrial Engineering student with a minor in Statistics from San Jose, California. For this project, she contributed to the team organization and development of two of the project’s main solutions: The scheduling tool and automated email. Additionally, she worked to ensure validation and verification of the team’s solutions as well as maintain documentation of the team’s progress throughout the year. Some of her hobbies include taking care of her plants, going to thrift stores, picking up different crafts, and enjoying the outdoors. After graduation she will be moving to Denver, Colorado to begin her job as an Application and Program Analyst with Deloitte Consulting and enjoying all the outdoors activities the Mile High City offers.
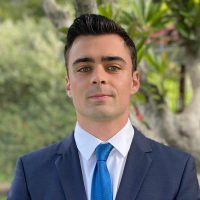
Jack Saavedra
head of research
Jack Saavedra is a 4th year Industrial Engineering student from Marin County, CA. His main roles throughout this project were problem identification and research early in the project. He was responsible for conducting research, communicating with experts, and ultimately writing the RFID tracking proposal. In his free time Jack likes to golf, play guitar and other instruments, and exercise in the gym or outdoors. Jack will be completing his bachelor’s degree in Fall 2021 and looks forward to what the future holds.
Acknowledgements
Thank you to Jill Speece for being a great advisor, Tonya Bakke for being a great Sponsor, and the entire Mechanical Inspection group for their continuous support.
Additional special thanks to Jorge Moreno Montoya, Tom Ruth, Otto Polanco, Moshe Bezkrovny, Tim Neville, Nicholas Onufer, and Tali Freed.
Our Project Video
Please enjoy this recorded presentation of our project development and final products.
Our Project's Digital Poster
Problem Statement
The Mechanical Inspection department at NASA JPL wanted to reduce the overall lead time of parts flowing through the lab. Parts to be examined vary widely in both size and complexity, resulting in variation of inspection cycle times. For this reason, the Space Cowboys focused on the reduction of queue time to reduce overall lead time, specifically the portion of queue time it takes to schedule and track jobs. As of November 2020, parts that came into the facility waited in the queue for an average of 15 days, and the longest job in the open queue is 33 days (QA Mechanical Inspection Metrics, 2020). Out of all the jobs, only 22% of jobs were completed within the goal time frame of 0-5 days of receiving the part. The percentage of jobs completed within this time frame needed to increase by 20% to significantly improve the efficiency of the Mechanical Inspection facility.
Background
Before being loaded onto crafts for space travel, mechanical parts must be inspected for any potential issues including cracks, strength issues, or discrepancies in tolerances. The Mechanical Inspection department handles these jobs with a team of 10 inspectors. The head scheduler, Jorge, assigns jobs to inspectors. There are different types of inspection, such as coordinate measuring machines (CMM), hand inspection, and rework. Inspectors also receive pressure from cognizant engineers, or Cog-Es, to complete inspections at an accelerated pace. Finally, inspectors have little transparency among themselves and with Cog-Es as to where parts are in the facility and when inspections are expected to be completed.
Problem Identification
To identify the problems affecting the mechanical inspection group, the Space Cowboys conducted a virtual Kaizen event with the inspection team over Zoom and using a Google Forms survey. The problems identified are displayed on the fishbone diagram below:
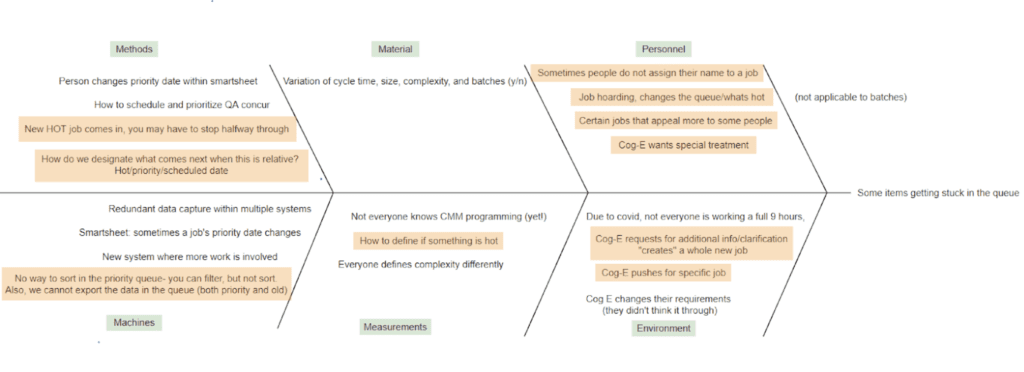
The team identified potential solutions to confront 3 identified problems, but due to time constraints and shifting priorities within the department, settled on three major solutions: to develop an automated email alerting Cog-Es that their part is being inspected and when it should be completed; to design and implement a new scheduling system which consolidates the three systems currently in use; and finally, to develop a proposal for an RFID-based tracking system to continuously locate assets within the facility.
Solution Design
Schedule view
The development of the schedule view happened over the course of the first few weeks of winter quarter. There were a few different design iterations, and the team worked closely with Tonya and Jorge to finalize what to include in the final design. The goal of this tool was to consolidate the priority queue, open queue, and Trello board into one cohesive tool. The three tools to be consolidated can be seen below (left to right: priority queue, open queue, Trello board):
Automated email
It was important to establish the current state of the automated email that was sent to Cog-E’s whenever they submitted a job so the Space Cowboys took a look at the information that was included in the current email draft:
It can be seen that this email contains details confirming that the part was submitted to the inspection department, how the part will be processed (FIFO) unless a need date is provided for the part, and a link to view the queue.
RFID Tracking
Our third solution is to confront the issue of confusion regarding part location in or around the facility by creating an RFID-based asset real-time locating system, or RTLS for short. An interesting caveat with this solution is that JPL wants to implement a consistent RFID system across the entire laboratory, a task that is far outside the scope of this project. As such, the solution is presented in the form of an implementation plan for JPL to use as a prototype for only the Mechanical Inspection department before expanding to the laboratory as a whole. To write the proposal, thorough research and consultation was conducted to find the best technology that fits the considerations of the Mechanical Inspection facility, such as facility size and radio frequency interference due to metallic surfaces, among others.
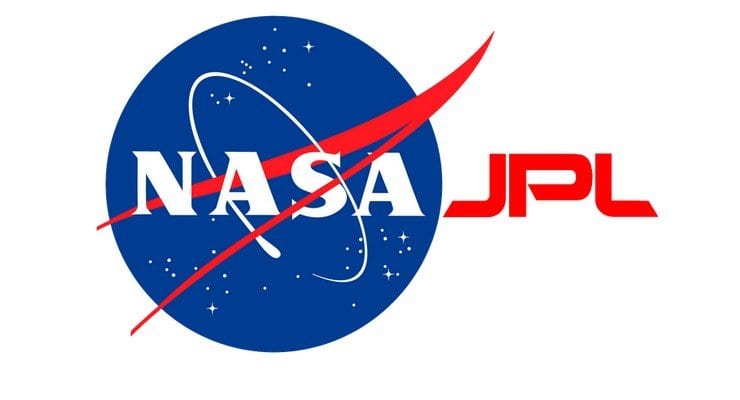
This project is sponsored by the NASA Jet Propulsion Laboratory
Verification & Validation
Schedule view
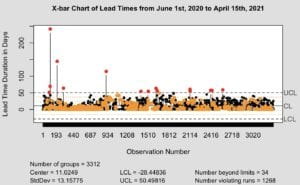
This control chart shows the lead times before the implementation of the schedule view in April. The process is wildly variable.
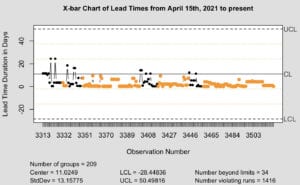
This chart shows the lead times after implementation. The process is more consistent and on average faster, due to the special cause variation of the schedule view.
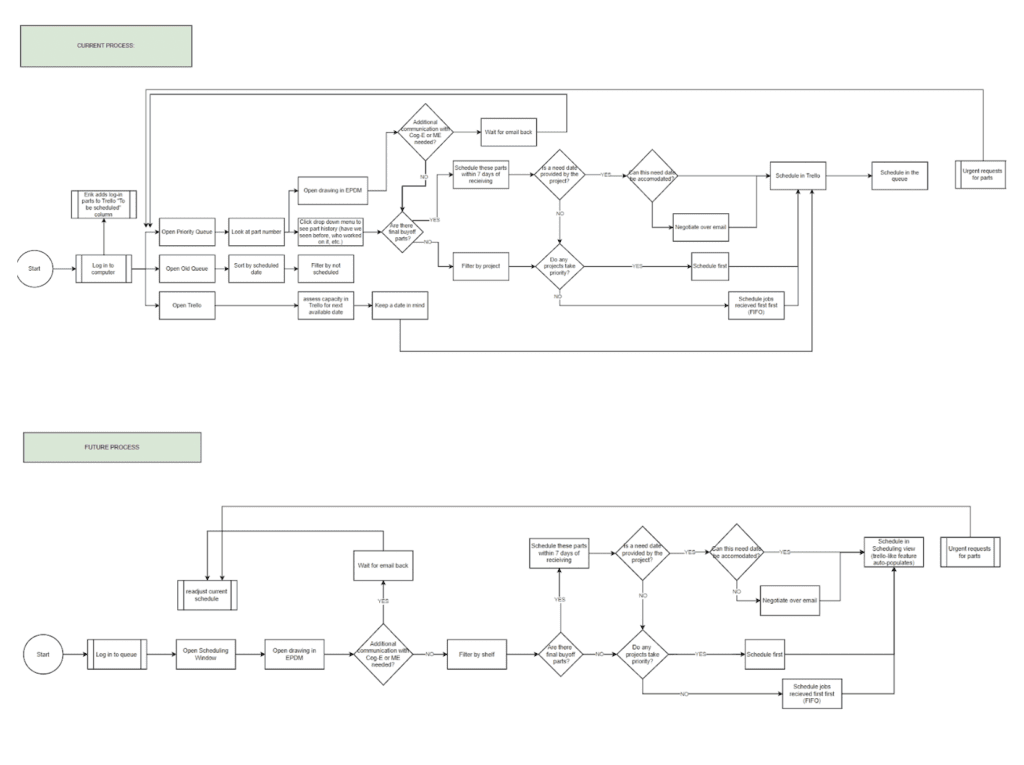
Above are the flowcharts representing the scheduling process before and after the redesigned schedule view. The latter flowchart eliminates several decision points and process steps, most of which were redundant in the prior system. The inspection team has also reported no technical issues since implementation in April 2021.
Automated Email & RFID Tracking
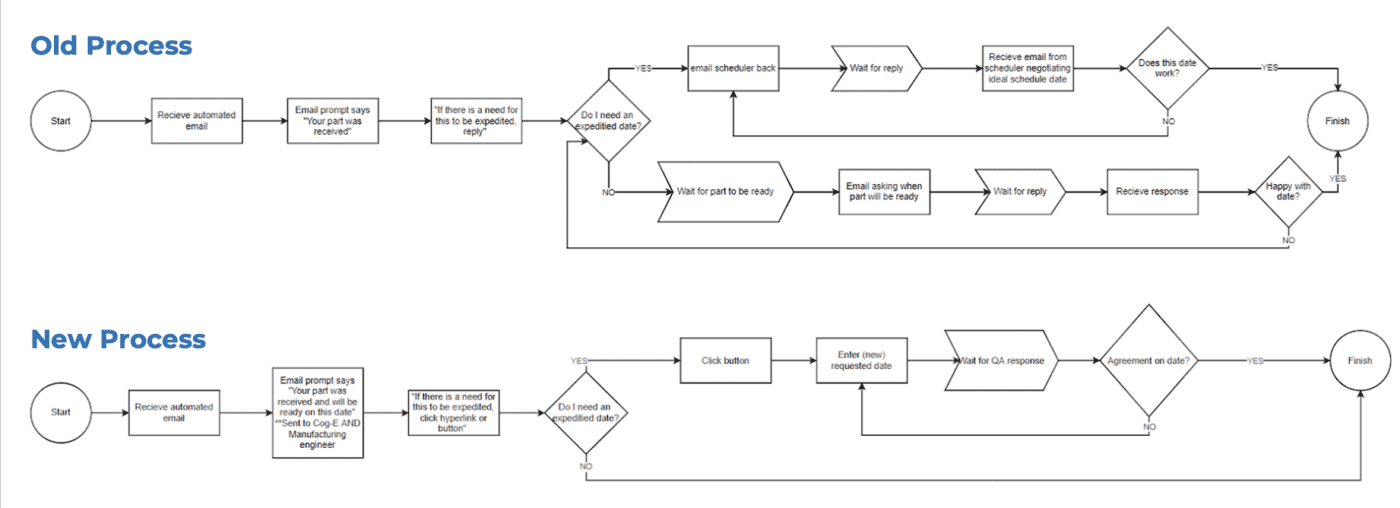
Similarly to the schedule view, the automated email eliminated several redundant steps from the old process to the new one. In this case, many of the steps eliminated involved communication between Cog-Es and inspectors, thanks to the included communication system and the predicted date which gives the Cog-Es more transparency in their project status.
The validation of the RFID tracking solution lies in a comparison between the cost of implementation and the future benefits of such a system. Those benefits are primarily due to process visibility, which eliminates wasted time searching for misplaced parts and increases transparency between inspectors. Visibility also aids in future continuous improvement initiatives, providing validation data. Because the RFID tracking solution is delivered as a proposal, there is no possible verification until after potential implementation. Similarly, JPL was unable to get the automated email system fully implemented before the conclusion of this project. In response, the Space Cowboys provided the department with a validation and verification plan.
Cost Analysis
The service rate is $201/hour for a total of 1911 emails in the past year. The old email system requires an estimated 1 hour for each request, between time for scheduler to rearrange work and respond, time for CogE communication, time for ME communication, and the disruption time for inspectors. In total the automated email is estimated to save a potential 1911*$201 = $384,111 per year.
The schedule view also applies to a service rate of $201/hour. Scheduling alone is charged $8,040.00 per week, or $402,000 per year (50 weeks). The new Scheduling View will save roughly 3-4 minutes per asset for 100 parts per week, leading to a potential savings of $1,005-$1340 per week, or $50,250-$67,000 per year. In total, between these solutions, the team predicts an estimated savings of $434k-451k per year.
Conclusion
Key success metrics were defined by our sponsor, Tonya Bakke, at the beginning of the project as reduction in cycle time, fewer steps in the process, fewer systems to access, reduction of manual data entry, and ease of use. The Space Cowboys worked closely with the scheduler, multiple Cog-Es, and Tonya Bakke, the sponsor to refine the original six proposed solutions down to three final solutions which were all moved forward with.: the scheduling window view, the improved automated email based on an algorithm, and the proposal of the RFID readers throughout the lab. The first two solutions listed above will reallocate a conservative estimate of $450,000 a year, which expands out to saving a million dollars for NASA in just over two years. The RFID proposal will serve as a roadmap to get the majority of JPL equipt with real time locating system tracking. All solutions meet at least three, some all, of the success metrics defined by the Sponsor at the beginning of the project. Although only the scheduling tool is implemented so far, the percentage of jobs moving through the facility within 0-5 days of receiving has increased from 22% (June – Nov. 2020 average) to an average of 52.2% (April & May 2021). As the difference between Fall and Spring greatly exceeds 20%, it is deemed a significant improvement to the Mechanical Inspection Facility, and the Space Cowboys aided in this positive change.
Final Designs
Scheduling Tool
The Scheduling View includes all of the same columns as the priority queue (parent level) except for the following: INSP Phase, Accept/Reject, Transfer to/Transfer, Hours, CMM Programmer, and Priority. Two columns were added: Days old, and Proposed Schedule Date. Within all columns, a multiple select feature was implemented in order to change multiple dates at once. Also, the default view shows at the top what is not yet scheduled, and the ability to export the data to excel exists just in case. The data shows a part’s full history so the scheduler knows what type of inspection this is and roughly how long it will take if the part has passed through Mechanical Inspection before. All columns are able to be both filtered and sorted to find exactly what is needed. It will also include a feature titled workload calendar, where the data automatically updates into a weekly calendar view that acts to replace Trello. Within the weekly workload calendar, inspectors schedule their own jobs, so they have transparent access to all the information known about a part as soon as they claim it. Below is the final layout of the combined scheduling tool:
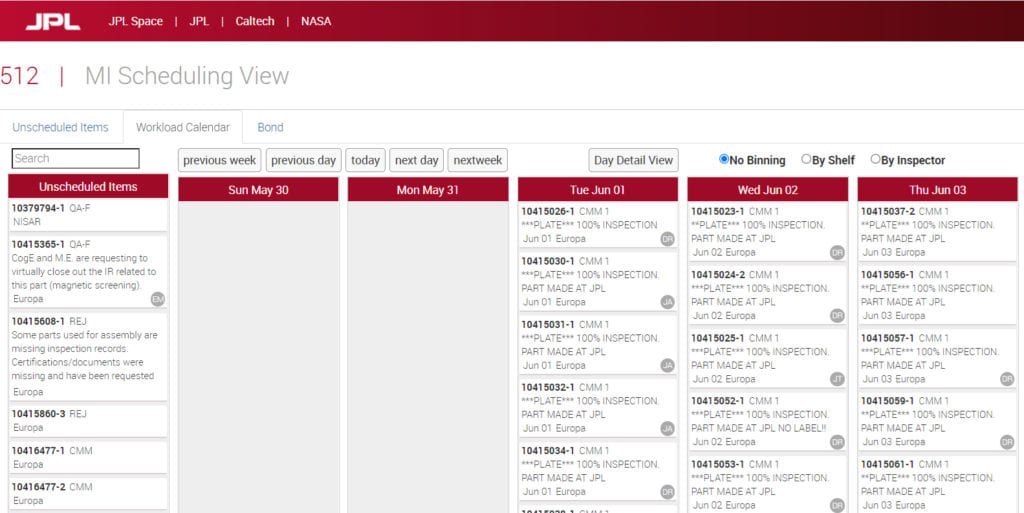
Automated email
The new automated email includes a proposed schedule date, algorithmically calculated based on historical averages for different types of jobs. This date is also automatically populated into the scheduling tool for the scheduler to reference. In addition to the schedule date, the email provides an estimated date of job completion to Cog-Es, allowing them to request need by dates from the scheduler right away, before the job has been scheduled. These requests can be done through a new two-way communication system, whose link is also included in the new automated email. This system was requested during interviews with Cog-Es, and it allows for direct contact with Inspectors and Cog-Es throughout the inspection process to increase transparency among departments.
RFID Tracking proposal
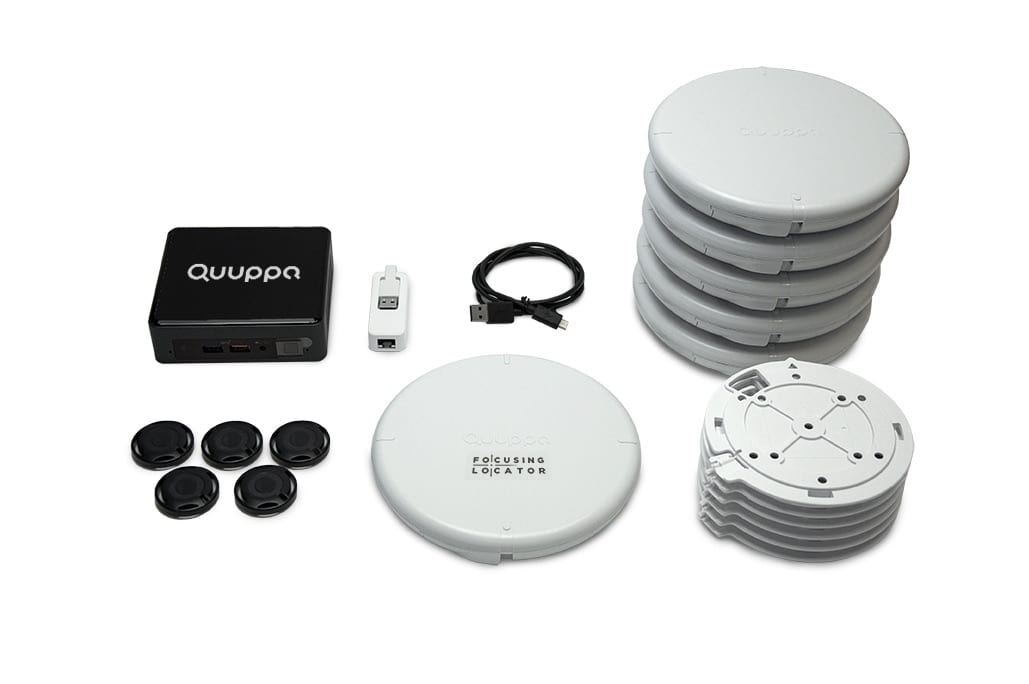
The final product for an asset tracking solution was an 11-page RFID proposal that will be submitted to receive potential funding after project completion. The proposal includes background on the technology and a recap of the system selection process based on a number of parameters. The team settled on recommending the development kit from Quuppa, an advanced RTLS technology company, for its versatile and capable active RFID tag system. The proposal includes a cost analysis of the development kit, recommended by Quuppa vice president because of the small-scale application of solely the mechanical inspection facility as a prototype and for its future scalability.
Future Directions
It is expected that the proposed completion date (as seen in the automated email) will soon populate a column in the new scheduling view to see when a part should be started for it to be done on time. Additionally, once RFID tagging is implemented across the lab, this data will be pulled into the queue so that everyone will know where each part is, and what stage of inspection it is in. All three of the Space Cowboy’s solutions working together will yield increased transparency to all parties involved.
The objective of these solutions that are being proposed is to improve the current state but allow for updating and maintenance as the lab grows and changes. Looking into the future, the lab will be able to reevaluate how these solutions are working for them and decide if they want to continue to use the solutions as they are or make changes to them as their requirements change. Making sure that the lab team is aware of why the decisions were made and how these solutions were implemented is integral to our project so that they have the autonomy to continually improve themselves after the project is completed, and self-sustain for the long run.
If the lab wants to do more beyond this project, they could consider more automation of data collection and a better way of tracking key data that would allow them higher visibility into their specific operation times and how long each inspection is taking. Additionally as stated in the beginning of this paper, Mechanical Inspection could consider using badge readers for job choosing purposes, or explore the scheduler assigning jobs. Error-proofing along with tracking more data could allow for the derivation of average job times for each type of inspection and create a better baseline for predicting lead times overall for scheduling purposes and for better communication with other members of JPL like the Cog-Es.