Our Team
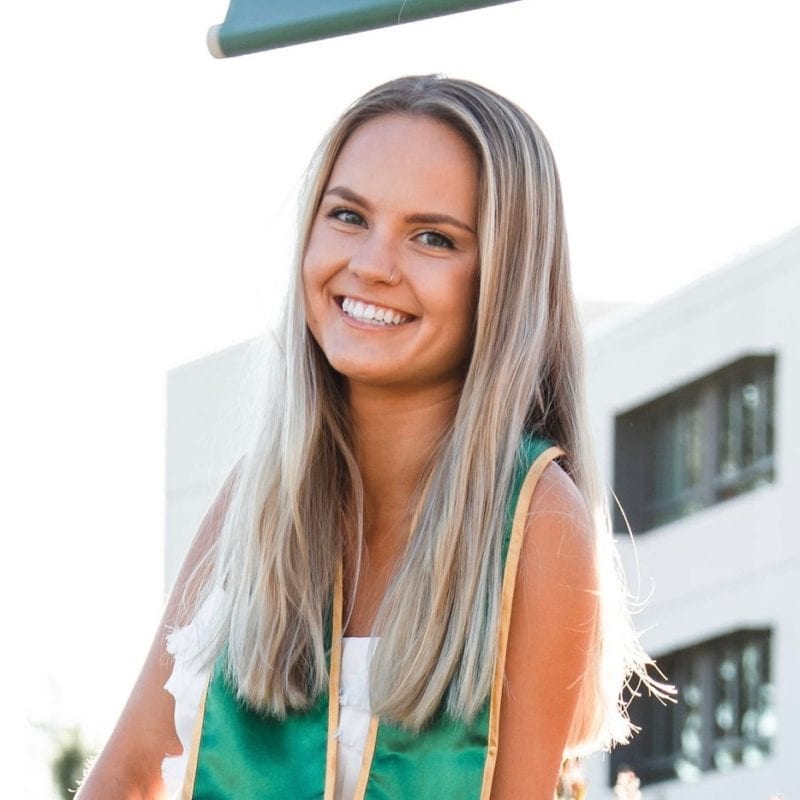
Julia Denison
I am a fifth-year Mechanical Engineering student with a concentration in Manufacturing. I am from New York, but will be staying in California! In my free time, I like to surf, run, and do home-improvement/DIY projects. I’ve always been drawn to the biomedical field and am excited to be working at Abbott Laboratories upon graduation.
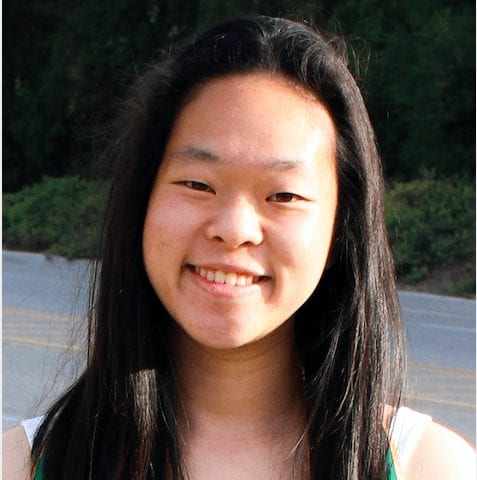
Christina Fong
I am a fourth-year Mechanical Engineering student with a general concentration. I am from the Bay Area and have enjoyed playing on the club ultimate frisbee team, conducting biomechanics research, and participating in outreach events whilst a student at Cal Poly. Come fall, I will be continuing at Cal Poly to earn my master’s degree in Mechanical Engineering.
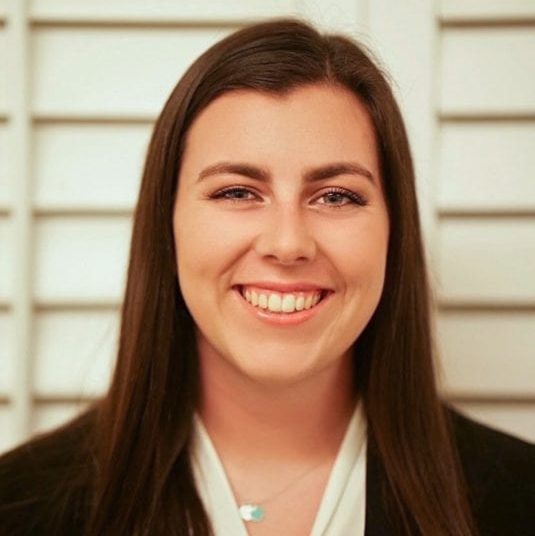
Melissa Kurani
I am a fourth-year Biomedical Engineering student, concentrating in Mechanical Design. I am from the Greater Sacramento area, and in my free time I enjoy spending time outdoors, such as hiking or hanging out at the beach. I am excited to be returning to Cal Poly next year to pursue my master’s degree in Biomedical Engineering.
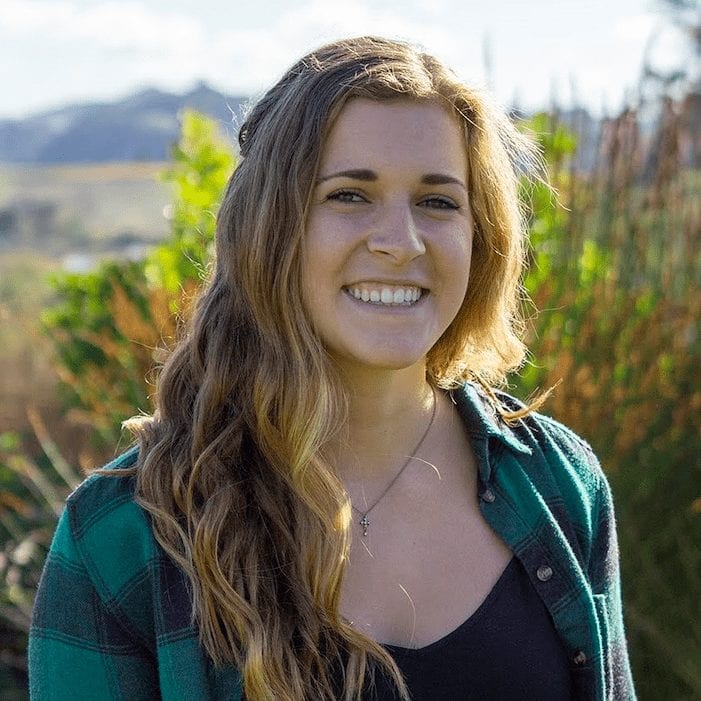
Autumn Rexford
I am a fourth-year Industrial Engineering student from Santa Barbara, CA. At Cal Poly I have really enjoyed being involved in Week of Welcome and Open House. Outside of school, I love camping, hiking, and building stuff! I am graduating Magna Cum Laude and am excited to be moving up to the Bay Area to start a full time position in Process Improvement.
Acknowledgements
We would like to thank our senior project advisors, Karla Carichner and Dr. Lily Laiho, for all their help and advice this past year. We would also like to thank Professor Chuck Bland for his technical help and for lending us his time and resources in putting together the electrical components of the device. This project would not have been possible without their dedication and assistance. We would also like to thank our sponsor, Bill Phelps, for his continual support and encouragement throughout the process. Additionally, we would like to acknowledge our funding by the TECHE lab. Thank you also to everyone who helped with the various prototyping and testing of our device.
Video of Project Tests and Examples
Our Project's Digital Poster
Problem Statement
The goal of Good Grips was to make a functional assistive device that helps our sponsor, Bill, use his hands more effectively. Bill has Inclusion Body Myositis (IBM), a disabling inflammatory muscular disease that causes progressive weakness of the muscles. Since his 2005 diagnosis, he has lost the majority of in his legs, wrists, and hands and will continue to lose strength as the disease progresses. Creating a device that could allow Bill to grip and hold common objects (cup, fork, toothbrush, etc.) will improve his quality of life and help him complete tasks independently.
Design Constraints
- Grip strength of 2.5 lbs
- Hold items of 0.25-5 in. diameter
- Device weight limit of 2 lbs
- Comfort level of 7 on a 1-10 subjective scale
- Touch screen compliant
- Maximum of 90 degree bend of left pinky finger
Design Process
Cable Design:
The fishing wire cables function similarly to the tendons of the human hand, closing the fingers as the cables are pulled down and tightened.
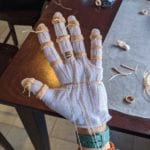
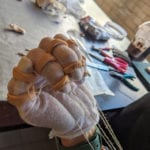
Motor Design:
Gear motors were chosen over servo motors because of their ability to rotate 360 degrees instead of only 180 degrees. Gear motors were also much smaller in size and weight and were able to output a comparable holding torque.
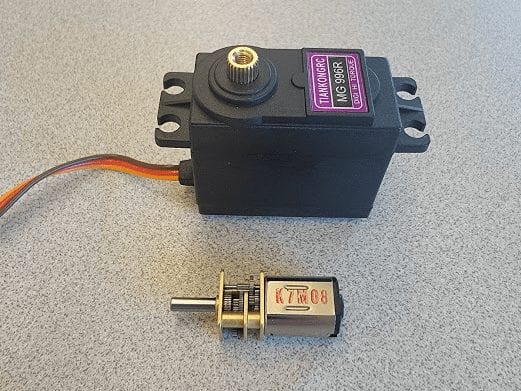
Glove Design:
A pre-existing weight-lifting glove was chosen as the base of our glove due to its ample wrist support, open back, and comfortable fit. The wrist support helps to prevent Bill’s wrists from breaking when he lifts heavier objects, and the open back allows for breathability of the glove. The open design and velcro features also makes the glove very easy for our sponsor to put on. This glove was then modified to fit the rest of our design constraints.
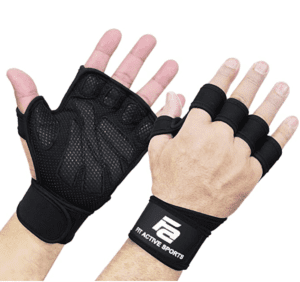
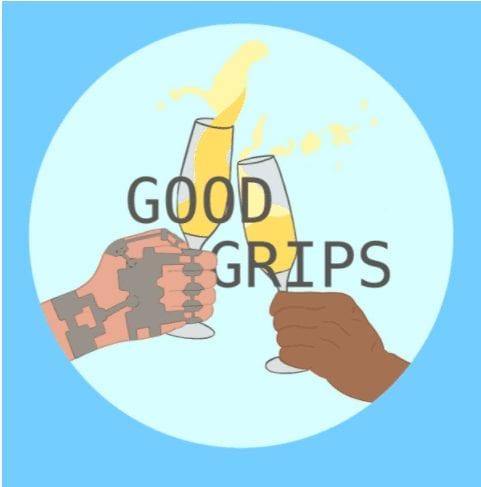
This project is sponsored by Bill Phelps.
Electronics
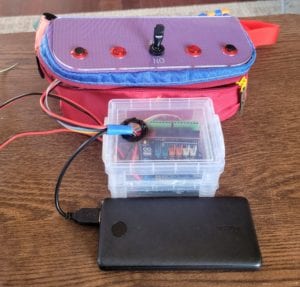
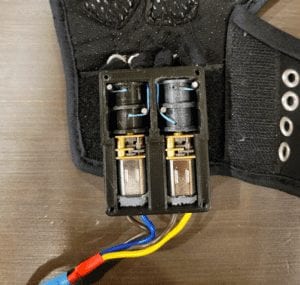
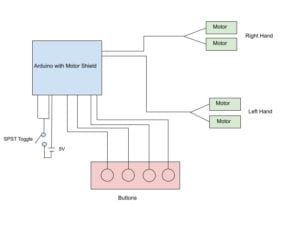
Casing inside the fanny pack houses an Arduino Uno, Arduino Motor Shield, and a Gikfun Screw Shield Expansion Board. Inside the fanny pack, there is also a 10000 mAh Anker rechargeable battery. Housed on top of the fanny pack are 4 buttons and an on/off switch which control the close and release motions of the gear motors. The motors and spools are located on the base of the glove.
Software
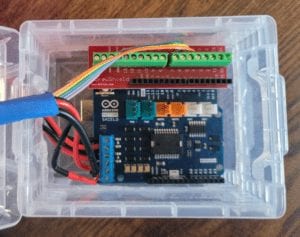
In order to control the opening and closing movements of the glove, an Arduino script was created to program the buttons and the emergency on/off switch. This program allows for only one button to function at a time, with options for each hand to close and release individually. If the emergency switch is turned to the “off” position, the device will immediately turn off and stop moving.
Manufacturing
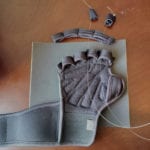
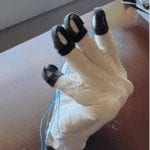
The glove components, including the finger caps, were all hand sewn from nylon, neoprene, and elastic material. The motor casing and spools were both 3D printed. All electrical components were connected via solder, screw terminals, and shrink wrap.
Bill lives in Park City, Utah, so we were not able to work with him directly when manufacturing the gloves. Instead, we used molds of his hands to help with sizing during the glove construction.
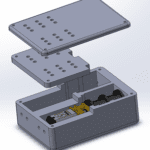
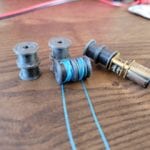
Final Design
Specifications
Final Weight of Glove: 0.30 lbs
Grip Strength: 3 lbs
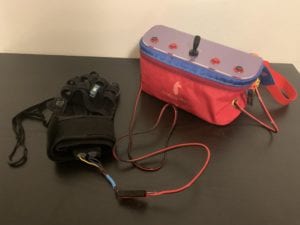
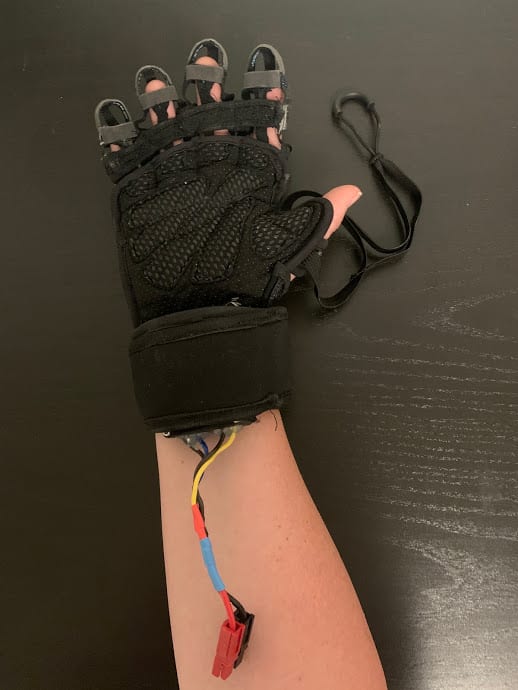
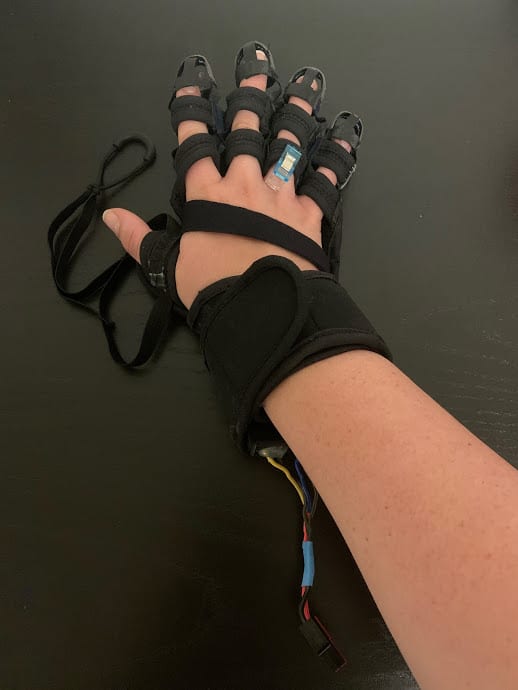
Electrical Components:
- Arduino Uno
- Arduino motor shield
- Gikfun screw shield expansion board
- Pololu 6V micro metal gear motors
- Anker 10000 mAh rechargeable battery
Glove Components:
- Neoprene weight-lifting gloves
- Nylon
- 3M grip material
- Polyester blend tracks
- Fishing wire cables
- Elastic thumb strap
Testing
- Cable Concept: confirmed cable concept functionality
- Force to Close: determined force needed to close hand to be 2.2 lbs
- Gear Motor Functionality: confirmed functionality of gear motors to close hand
- Electronics Functionality: confirmed functionality of entire electrical system
- Grip Strength: measured grip strength applied by glove to be 3 lbs
- Hand Function: measured grip strength, finger control, and diameter limits of items
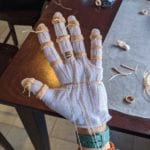
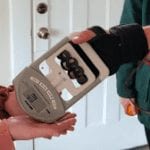
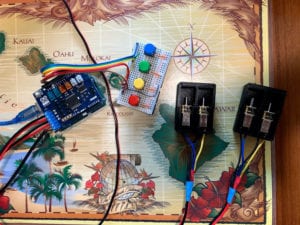
Recommendations
In the future we would recommend looking into more solutions for the thumb. The thumb does not move like the rest of the fingers and goes in varying positions to grip different objects. In order to be able to use the thumb as normal, a much more complex design is needed which would require more experimentation and testing. Additionally, we think this design could be improved and made to fit other customers if a professional tailor was brought in to improve the sewing and make sewing patterns for future use.