Our Team
Blake Robinson, Arash Akhavi, David Albarran-Martinez
As three materials engineering students who have known each other for a few years, we were able to successfully work together as peers throughout the duration of the project.
Acknowledgements
Dr. Trevor Harding (Faculty Advisor)
Dr. Armen Kvryan (Industry Sponsor)
Anton Hochschild (Manufacturer, APPF)
Dr. Ajay Kathuria (Packaging Department)
Green Dot Bioplastics (Polymer Supplier)
Tom Moylan (Cal Poly Pier)
Eric Beaton (Lab Technician)
FTIR Analysis
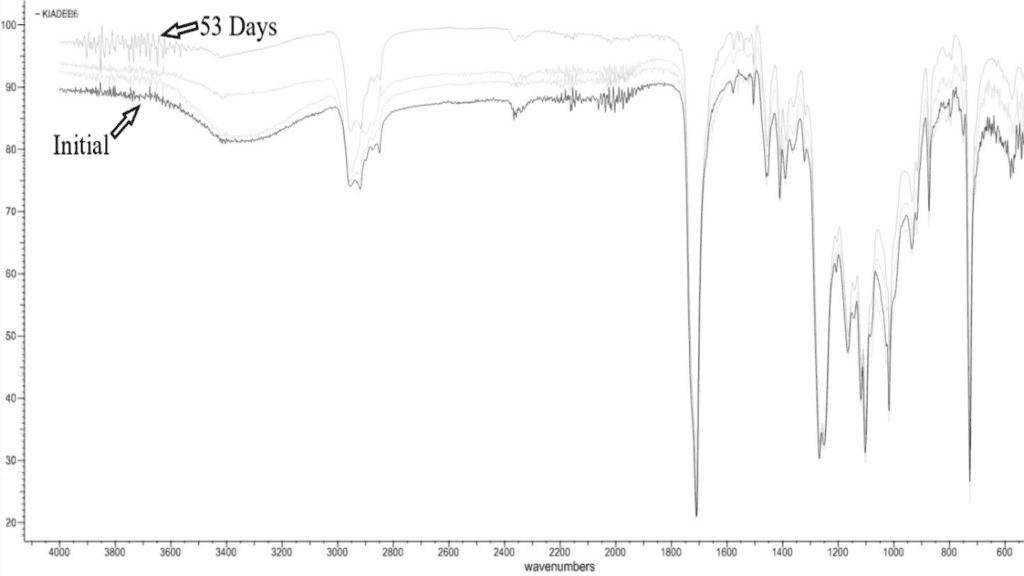
This is one of the sets of data from testing with the FTIR, specifically BD3001 in the dark simulated ocean. Many spectra were generated based on how long the sample was exposed to the simulated ocean and then they were overlapped to show any differences.
The peak at approximately 1700 wavenumber was of particular interest due to it representing the ester bond which is sensitive to microbial attack. For this data set, and all the others, there are close to no changes at all, again giving no evidence of biodegradation occurring.
Gravimetry Data
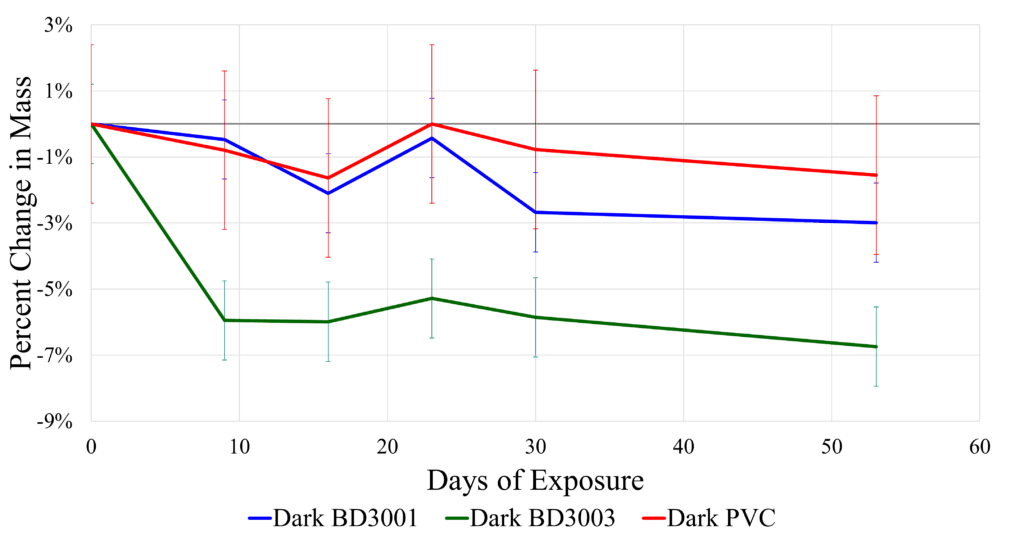
This was one set of data gathered for percent change in mass. After each sample was taken from the simulated ocean test and prepped, it was then weighed. This gave us 5 data points over the course of 53 days to track the mass of the samples. We expected the PVC to remain constant and the other polymers to linearly or exponentially reduce in mass. However, the BD3001 match the PVC almost perfectly, so the only changes can likely be attributed to inaccuracies with the scale that we used. BD3003 did have a drop in mass, but it occurred within the first 9 days then stayed constant. Our hypothesis is that the BD3003 was not dried sufficiently initially, so when taken out of the test and dried sufficiently, it dropped in mass due to less moisture content. The other sets of mass data looked similar and could be explained with similar explanations. All in all, gravimetry did not give evidence that biodegradation occurred.
DSC Analysis
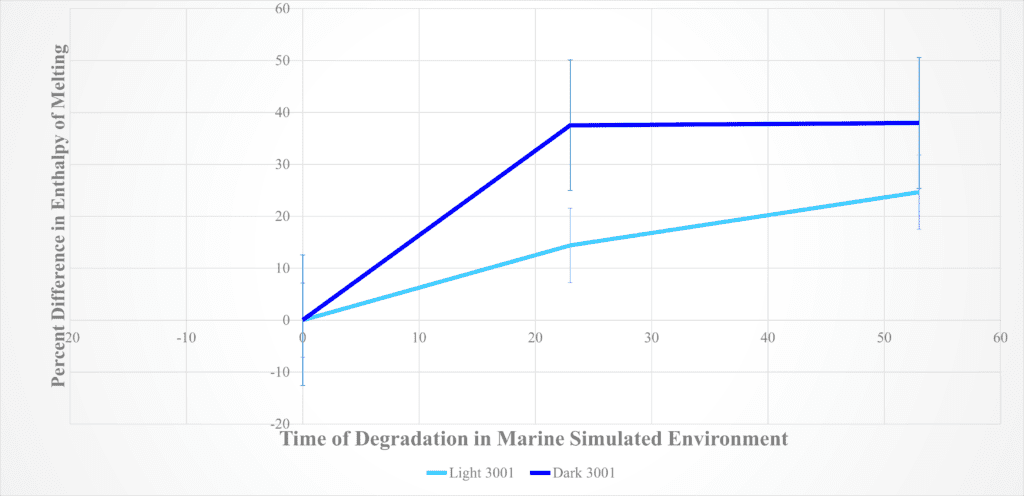
This graphs shows the trend of the melting enthalpy of 3001 samples that had been placed in the separate tanks. The melting enthalpy was of interest because it has a direct correlation to crystallinity. If there is an increase to the melting enthalpy, then there is an increase to the crystallinity. If biodegradation occurs, then a polymer should become more crystalline. There was a greater percent difference in the enthalpy of melting for the samples that were placed in the dark marine environment as shown by the darker blue line. It had been hypothesized that the trend would show increasing percent difference with time of degradation. However, the difference between the sample taken out at the 23rd day and 53rd day is minimal. It was also hypothesized that samples in the light marine environment would have a greater percent difference , but this was not the case. The same trend applied to the 3003 samples where the 3003 samples placed in the dark marine environment had a higher percent difference than the 3003 samples placed in the light marine environment. The minimal change in the degree of crystallinity indicates that biodegradation is very minimally occurring or not occurring.
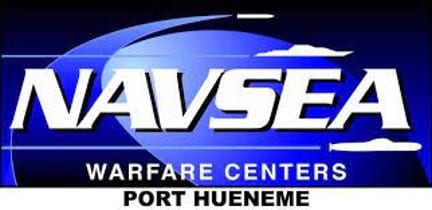
NAVSEA
This project is sponsored by the Naval Surface Warfare Center, Port Hueneme
Tensile Testing Analysis
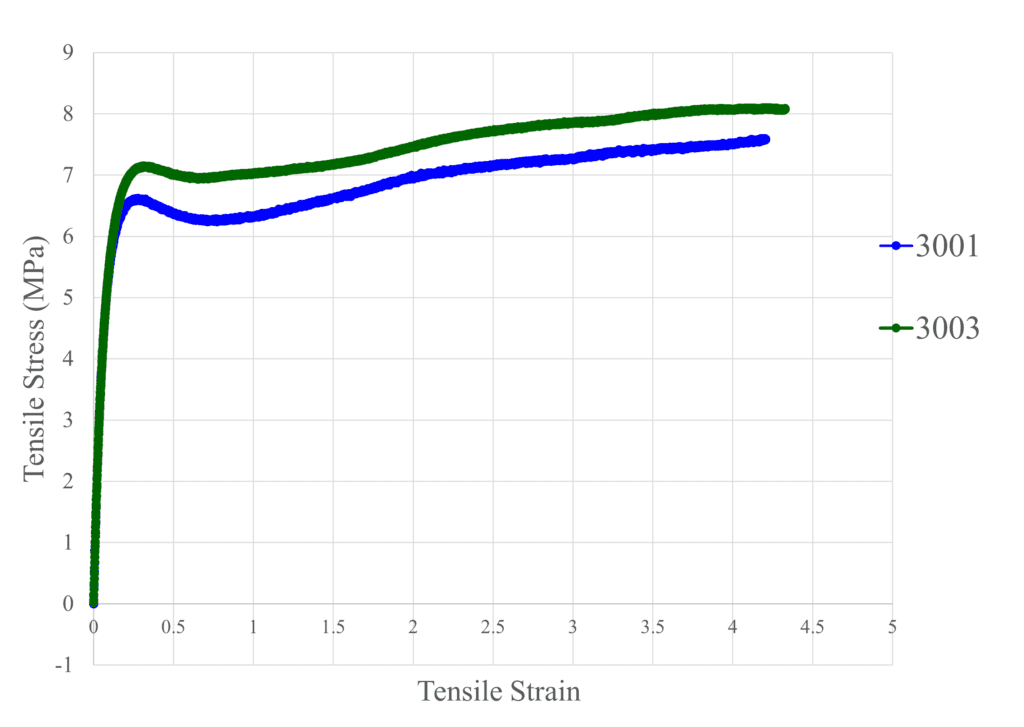
Five specimens were tested and averaged for each sample. The tensile stress for the 3001 sample was 7.60 MPa and elastic modulus of 57.2 MPa The tensile stress for the 3003 sample was 8.1MPa and elastic modulus of 59.6. The material Data Sheet of the current material used for the killer tomatoes was given by APPF and it states that the current material has a tensile stress of 15.66MPa. The Killer tomatoes are currently designed using the minimum amount of the stronger PVC material. More material would be required if the killer tomatoes were to be manufactured using either the 3001 or 3003 material, and that extra material needed could be costly.
RF Weldability Analysis
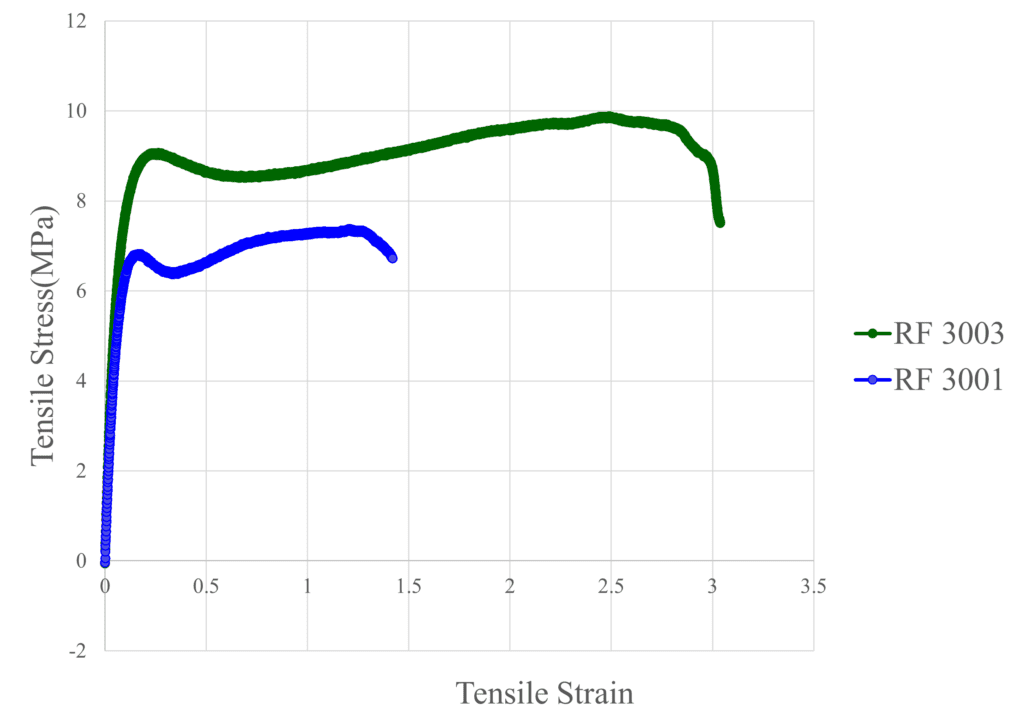
Two specimens were average for each sample. The tensile stress for the RF welded 3003 sample was 9.88 MPa and elastic modulus was 66 MPa. The tensile stress for the RF welded 3001 sample was 7.38 MPa and elastic modulus was 69.80 MPa. Both RF welded also had a lower percent elongations compared to non RF welded samples. The similar tensile stress of the RF welded samples compared to the non RF welded samples indicates the 3001 and 3003 samples are capable of being RF weldable.
Conclusions
Polymers BD3001 and BD3003 were manufacturable. There were no issues with shelf life or RF welding. Based on the information we received from APPF.
Based on the tensile testing and PVC data we have the mechanical properties not comparable to PVC.
Minimal biodegradability occurred in during the duration of the marine biodegradation test. All tests, Gravimetry, FTIR, DSC, and tensile testing agree with this statement. (SEM is in progress).
UV radiation had very little to no effect on the biodegradability of the polymers in the experiment.
Both BD3001 and BD3003 polymers performed very similarly.
Future Recommendations
Extending the duration of the test could produce better results.
We recommend finding more potential polymers to test.
Potentially adding additives to a polymer to try and accelerate marine biodegradation.
Changing the testing mechanism could produce better results. We simulated an ocean environment using ocean water, oxygen, chillers, and tanks. An experiment in the actual pacific ocean could produce better results. Additionally an accelerated test could produce promising results.
Sheet Extrusion
With the help of Dr. Kathuria and the Industrial Technology and Packaging department the sheet extruder was used to extrude the polymer resin into sheet form.
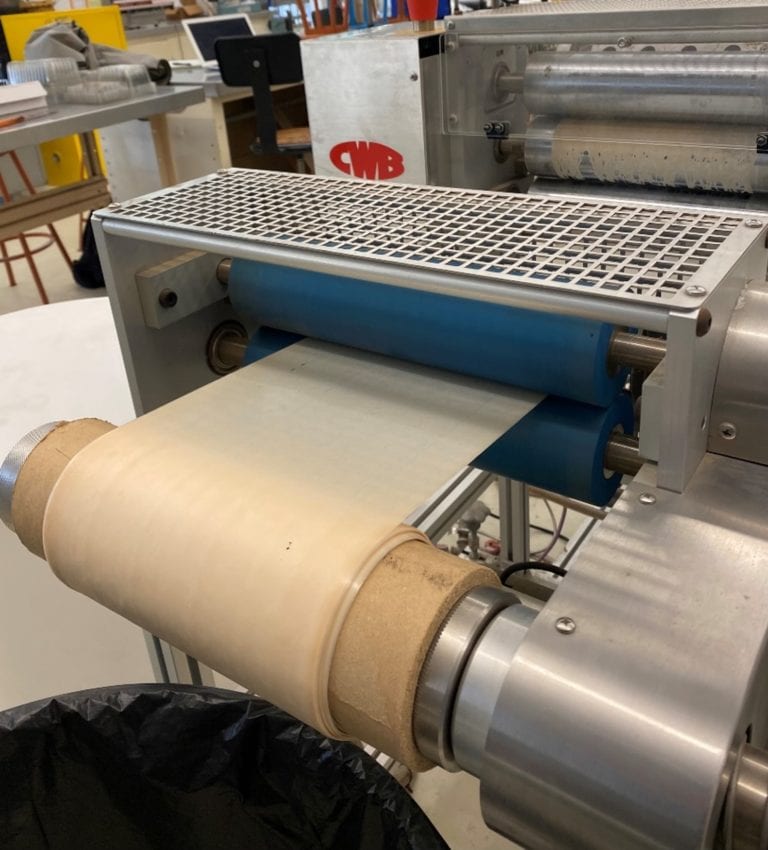
The first thing we had to do was setup the extruder and connect tubes for water cooling. Once it was ready to go I accessed the material data sheets that Green Dot bioplastics gave to us when we purchased the polymers. These data sheets were incomplete but gave enough info to help with the processing. It recommended drying the pellets, which we did using a vacuum furnace. Next, we had to set the temperatures of each heated section of the extruder with the program that worked with the machine. Once heated to the appropriate temperatures the pellets were added and the rpm was increased to allow the melt to flow.
The extrusion process was difficult and took many attempts to get an even sheet of the polymers, but eventually both BD3001 and BD3003 were successfully extruded.
SEM Initial Images
BD 3001
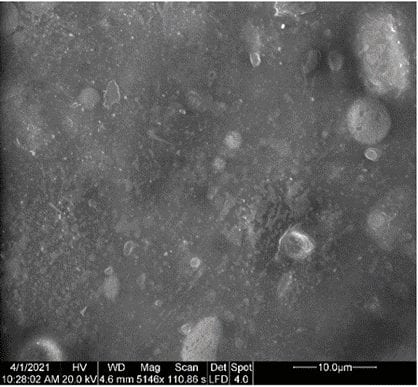
BD 3003
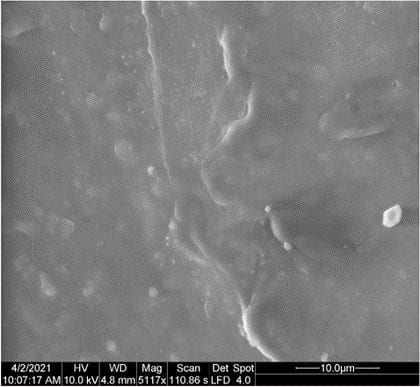
After extruding the polymer resins into sheet form they were cut to size and observed under a SEM. This was done to determine the initial surface morphology of the polymer samples and to identify any damage done to the surface as a result of manufacturing.