THE PROJECT
This project is one of several intercollegiate competitions hosted and funded by NASA RASC-AL. The Moon to Mars Ice & Prospecting Challenge for 2021 aims to explore methods for acquiring liquid water on the surface of Mars. Because all known deposits of water on Mars are underground and in solid ice form, there are significant challenges to overcome. This challenge also requires teams to investigate methods that can be used to collect data about Martian subsurface geology.
Main Project Goals:
- Drill through various layers simulating Martian soil
- Collect data about the thickness and hardness of each layer
- Collect clean, liquid water from below the layers
- Document design choices and address necessary changes for real spacecraft use.
STYX & STONES is one of 10 teams chosen to receive funding to build a prototype of our proposed design. This also means that the team will travel to NASA’s test facility in Hampton, Virginia to compete against other university teams and demonstrate our prototype in a simulated Martian environment.
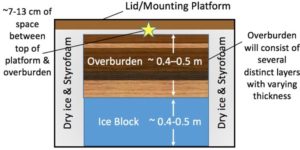
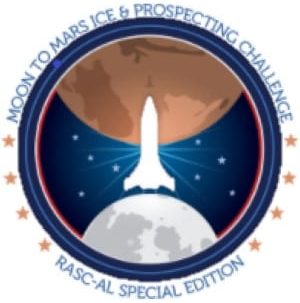
STYX & STONES
This project is sponsored by NIA, Capstan, and MESFAC
COUNTDOWN TO COMPETITION
The name “STYX & STONES” was chosen as homage to last year’s Cal Poly team members who were unable to participate in an on-site technical demonstration due to COVID-19. The name also refers to the comeback “sticks and stones may break my bones” as this year’s team intends to make a strong comeback considering the many challenges faced throughout 2020.
Mechanical team
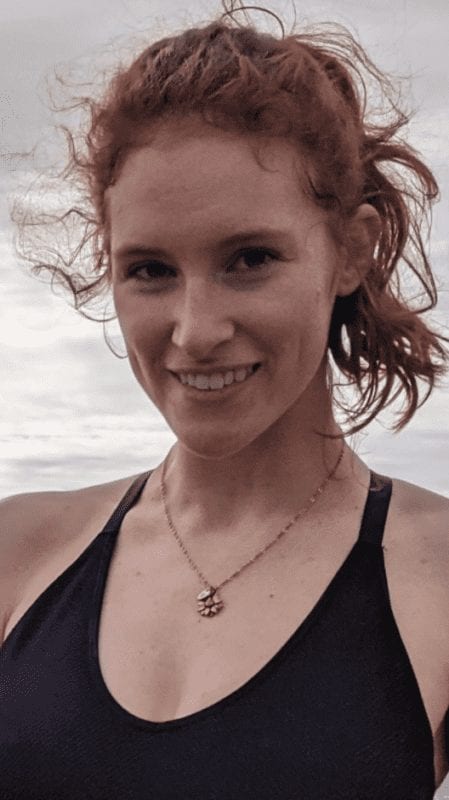
Michelle Leclere
My name is Michelle and I am the Mechanical Team Lead. I am a fourth year mechanical engineering student pursuing my Blended Master’s degree at Cal Poly. I have work experience in conceptual design, manufacturing, and part design in the aerospace industry.
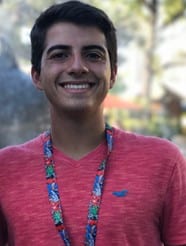
Alex Martinez
My name is Alex and I am the Excavation Design Lead. I am a senior ME student with a passion for solving challenging problems. Cal Poly’s labs and design projects have given me hands-on experience designing for manufacturability and analyzing large mechancial systems.
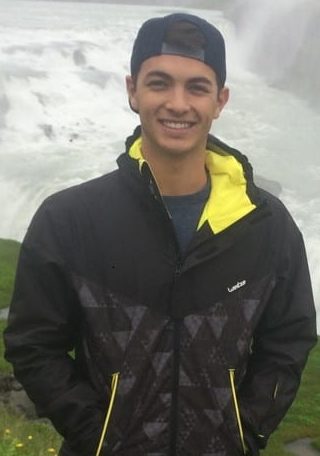
Dominic Duran
My name is Dom and I am the Structures Design Lead. I am a fourth year ME and work as a lab assistant for Cal Poly’s hand-drafting and SolidWorks labs. I have hands-on structural design and manufacturing experience from clubs and interning in the defense industry.
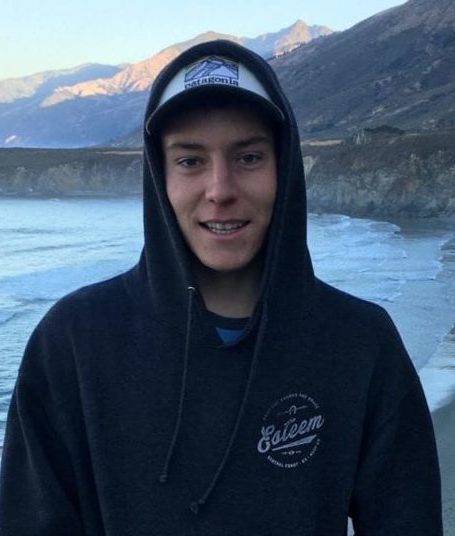
Brad Behrens
My name is Brad and I am the Water Processing Lead. I am a fourth year Mechanical Engineering student and will be graduating this June. I am pursuing a career in the aerospace industry and like to be outdoors with friends and family on my free time.
Mechatronics team
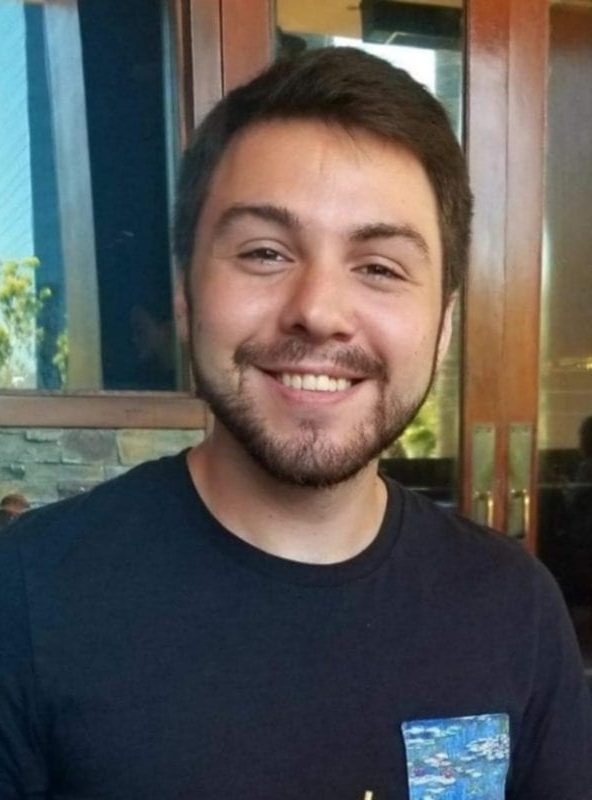
Schuyler Ryan
My name is Schuyler and I am the Mechatronics Team Lead. I am an ME student pursing a mechatronics concentration and minor in computer science. I have been involved with several robotics projects including building autonomous SUMO fight bots, making a light-following mouse-bot, and Cal Poly’s Robordentia competition.
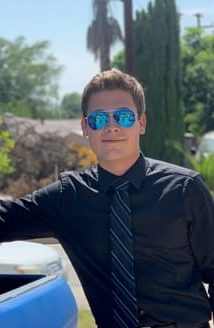
Tyler Guffey
My name is Tyler and I am the Electrical Design Lead. I am a 4th year mechanical engineering student concentrating in mechatronics. I have hands-on experience and real-world engineering knowledge from engaging in many interesting projects outside of class ranging from car restoration to wrought iron fences.
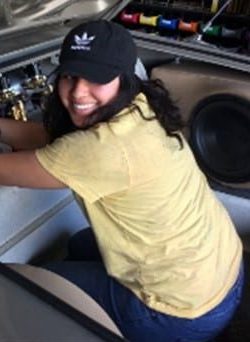
Rebecca Rodriguez
My name is Rebecca and I am the Telemetry Systems Lead. I am a fourth year mechanical engineering student concentrating in mechatronics. I have gained hands-on experience from working with my dad to wire solenoids for an air bag suspension, as well as installing a fuel level sensor for a gas tank.
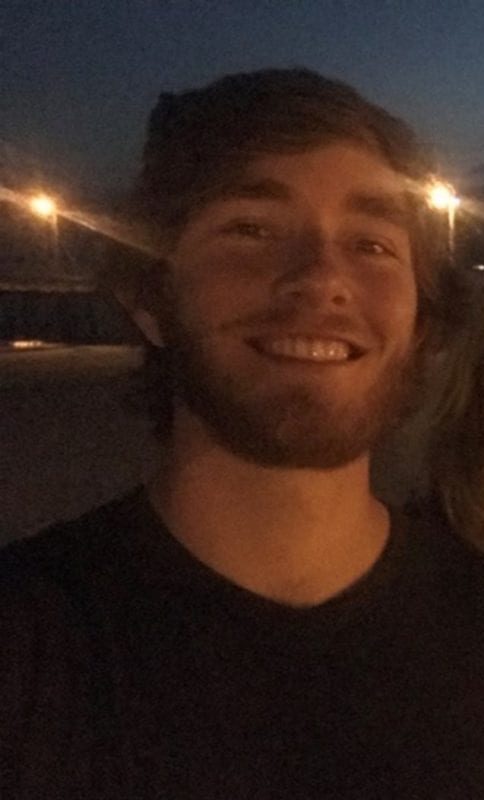
Jacob Everest
My name is Jacob and I am the Controls Lead. I am a fourth year ME pursuing a concentration in mechatronics and my Blended Master’s degree at Cal Poly. I have hands-on work experience from interning in the tech industry and working at The Home Depot during the school year.
Mid-Project Review Video
The following video was sent to NASA, to demonstrate that we had made progress on the build of our robot, and are including all the systems specified in the Project Plan. This video along with the Mid-Project Review was sent to NASA and guaranteed us one of the 10 competition spots.
PROJECT POSTER
Project Requirements
Collect subsurface layer data and extract liquid water from subsurface ice deposits via a robotic platform in simulated Martian conditions provided by NASA.
Main Specifications:
- Max Weight: 60 kg (132 lbs)
- Max Power: 9A, 120VAC
- Max Dimensions: 1m x 1m x 2m
- Max Downward Applied Force: 150 N
- Provide: Regolith Layer Thickness Data
- Provide: Regolith Layer Hardness Data
- Provide: Maximum Possible Quantity and Clarity of Liquid Water
- Recommended: Autonomous Operation
Design Process
Ideation methods like brainstorming and concept sketching were combined with decision-making strategies such as functional decomposition and Pugh matrices to drive the final design direction.
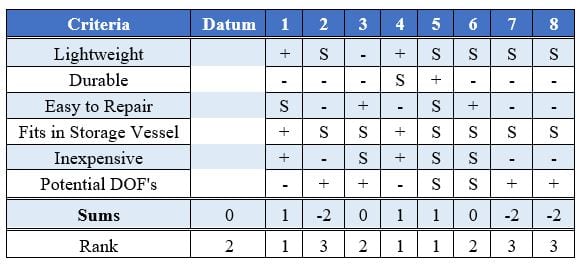
Concept Prototype/Preliminary Testing
One of the first choices to make was the penetration method. Core drilling and ultrasonic drilling were considered, but hammer drilling was decided as the best path forward.
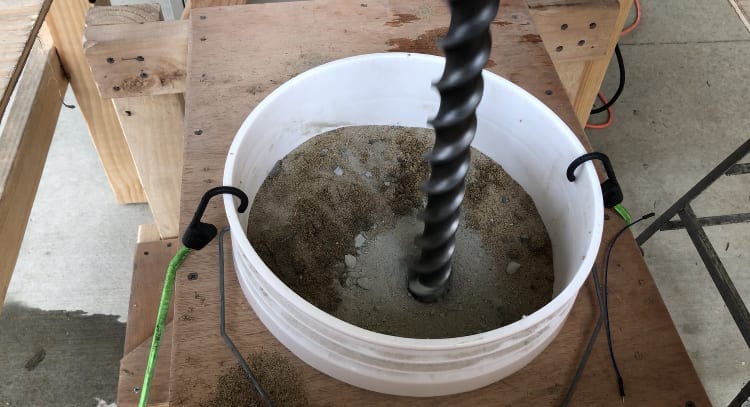
A RH432VCQ Bosch rotary hammer and 1.5” diameter masonry drill bit were verified to clear through all possible types of simulated regolith. This was proven by last year’s team and affirmed with a simple test in November 2020.
A method for extracting liquid water was the next big choice. Actuating probes and simple heaters were considered, but ultimately a recirculating water jet design was chosen. An internal cartridge heater allows the heater probe to melt the ice, then a pump takes water from the melt pool and recirculates it back down through a nozzle.
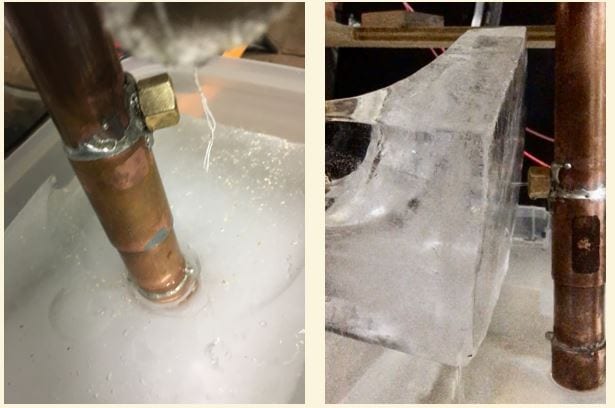
The water jet mechanism was prototyped using a 200W cartridge heater and copper tubing to verify the concept in January 2021. The test results were as follows:
- The heater probe melted down into the ice at an average speed of 0.38 inch/min.
- The water jet penetrated the ice at an average speed of 11.5 inch/min with the water at 120 +/- 10 degrees Fahrenheit.
Final Design
The final system features were chosen to be:
- Aluminum tube frame
- 2-axis linear motion
- 2-step prospecting process
- Hammer drill
- Heated auger hybrid tool
- Two-stage water filtration
- Weight-On-Bit (WOB) Correlation for Telemetry
- Control via TI MSP432 microcontroller
- Autonomy via Finite State Machine (FSM) architecture
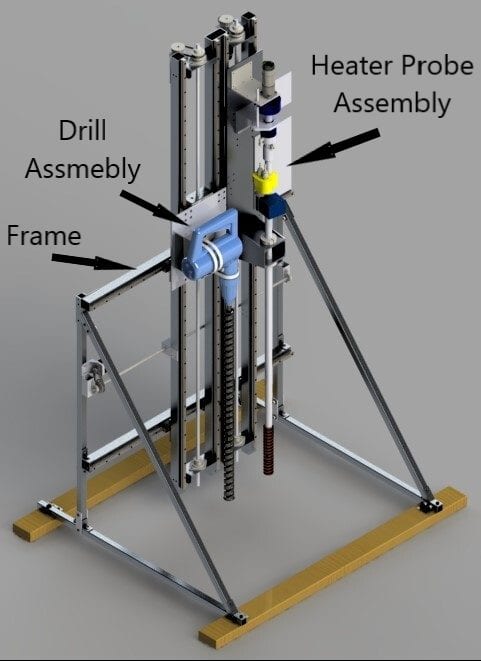
Analysis
Several analyses were conducted to validate the design choices before constructing the verification prototype. Once the design was validated, the team began building the frame and drilling subsystem for NASA’s Mid-Project Review demonstration.
FRAME ANALYSIS
An extreme load case where the drill bit catches the edge of the drilled hole upon exit was analyzed using SolidWorks FEA. A safety factor of 1.5 was used for the load that is transmitted through the leadscrew collar to one of the bottom bearing brackets on the Z-axis assembly. A maximum deflection of 0.65 inches was observed at the top of the frame, which is suffiecient given that tool alignment occurs at the bottom of the frame.
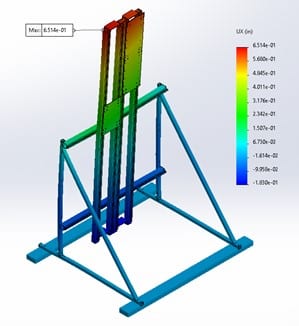
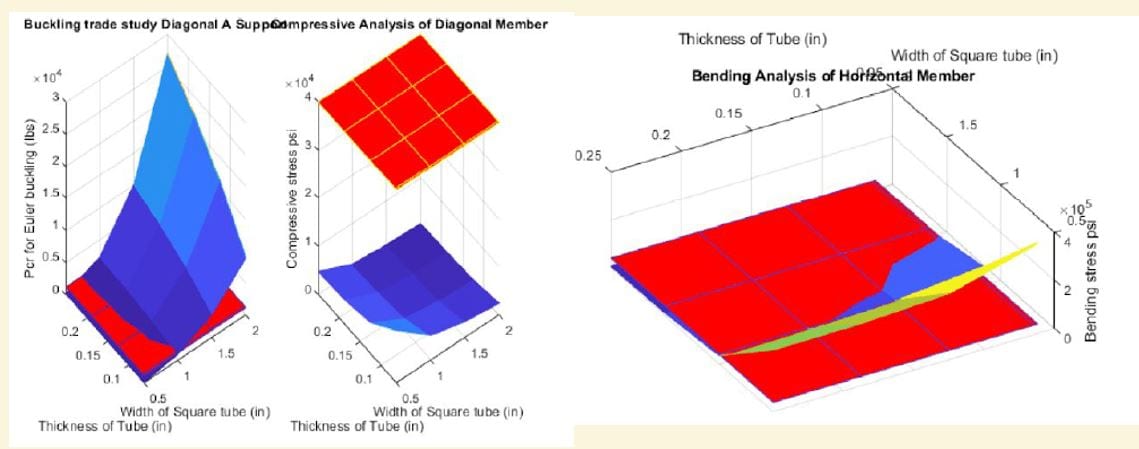
DRILLING SUBSYSTEM ANALYSIS
To ensure proper alignment of the drilled hole and heater probe, the rotary hammer must be attached to a spacer such that the drill bit is 4.5″ off of the mounting plate. The team confirmed that the proposed mounting method would only incur minimal deflection by performing finite element and vibrational analysis.
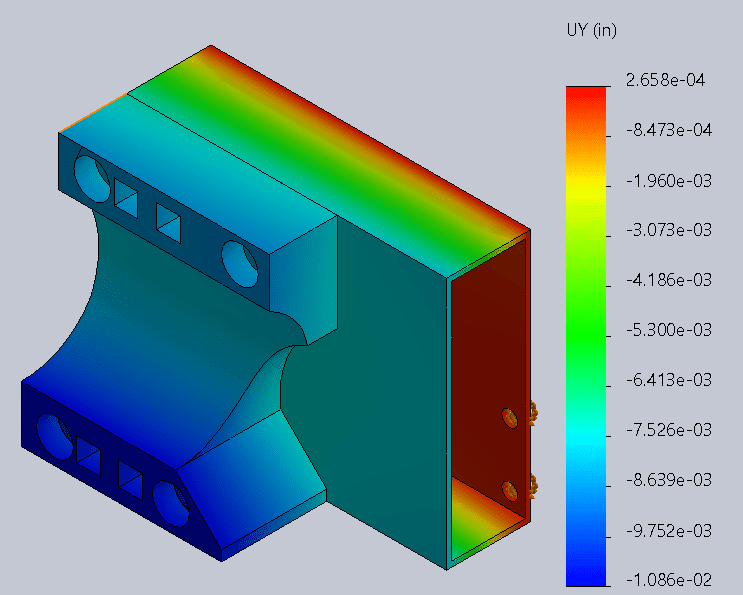
Using SolidWorks Simulation, the max static displacements were transformed to max dynamic displacements using vibrational analysis. The loading case considered was the rotary hammer operating at full power with a WOB of 500N.
HEATED-AUGER ANALYSIS
To ensure the pump was sufficient, the team estimated the major and minor losses due to all of the components and created a system curve. Steady state operation with constant kinematic viscosity, well-insulated piping, and turbulent flow throughout (based on Re > 2300) was assumed. The resulting operating conditions are as follows:
Fluid System Data
- Pressure rise across pump: 1.4 bar
- Flowrate: 1000 mL/min
- Water Jet Nozzle Exit Diameter: 1/16″
- Water Jet Exit Velocity: 8.4 m/s
At the pump suction, the calculated static pressure is 0.5 atm (vacuum). To avoid water vaporization, the local water temperature at the pump suction must remain lower than 175 deg. F. Prior to testing, the team verified that the pump was able to pump water vapor without issues if this temperature is exceeded.
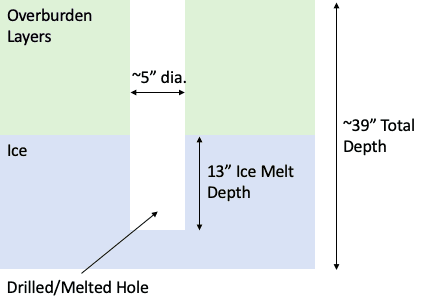
The team is confident that the rotating water jet will be able to create at least a 5″ diameter cavity within the ice layer. Based on the 38″ auger length requirement, the melted hole will be about 13″ deep. Considering the change in density upon melting, the team concluded the following:
- Water Retrieved Per Hole: ~16 qt
- Average Melt Rate (including Water Jet): 1.5 qt/hr
- Time per Hole: ~12 hr
Note: Competition allows for 12 hours total run time. Assuming two days of 5 hours of water collection each, the team estimates a total collection amount of 15 qt.
The previous winning amount was 7.7 qt.
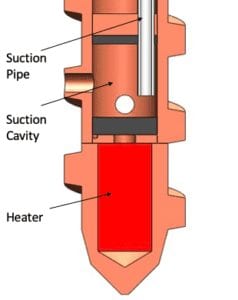
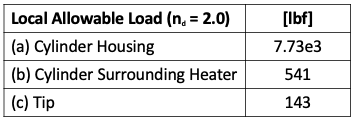
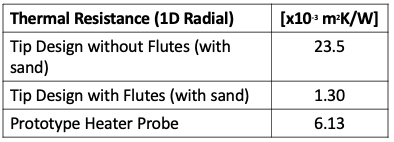
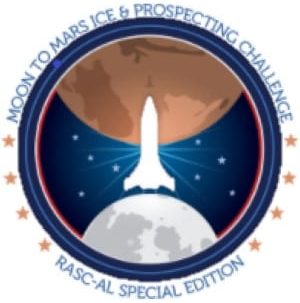
STYX & STONES
This project is sponsored by NIA, Capstan, and MESFAC
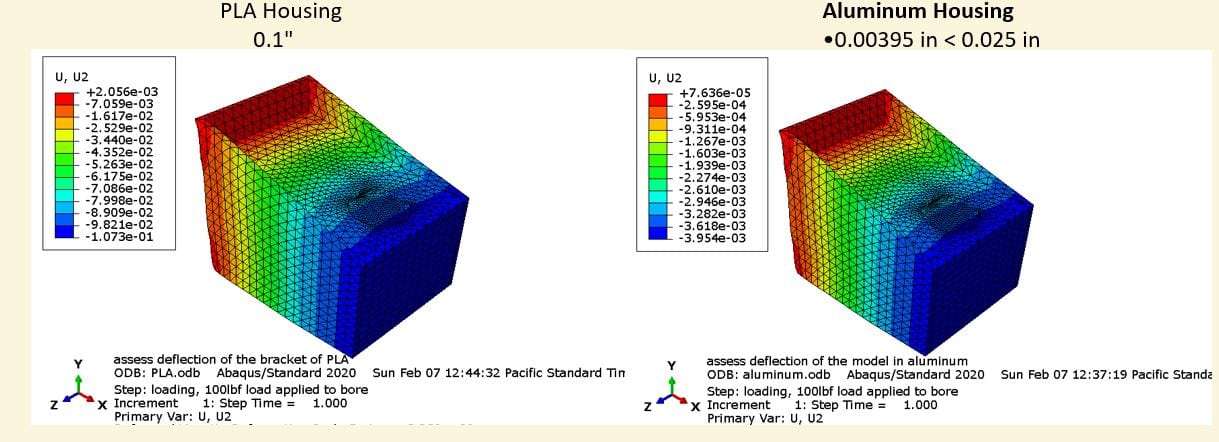
A rigid tool collar to support the heated auger tool shaft was evaluated in finite element software to determine the best material to manufacture it from. Under the maximum loading case where the auger gets frozen in the ice and the Z-axis gear motor must operate near stall torque to remove it, the aluminum version of the part prevailed.
ELECTRICAL SYSTEM ANALYSIS
To verify that all components after the 9 A fuse remain under the current limit, the team initially simulated the system using Simulink. Each block was meant to simulate the different combinations of components that would run at the same time. The system was then run in pieces; each combination was turned on and off in order with breaker blocks, and the current was monitored.While this was only useful for an approximation, the team was able to determine which pieces of the system would draw more power.
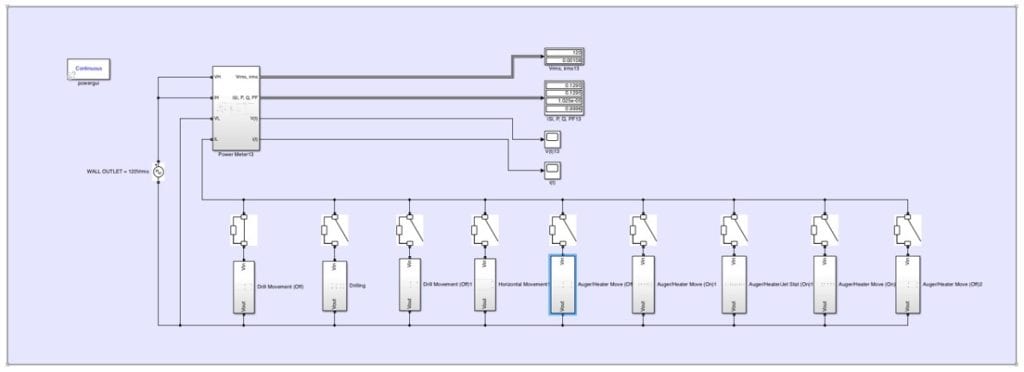
The system was then put together piece by piece to ensure the right pieces worked as expected. The drill system and heated auger system were run at full power and determined to use less than 9 A. To ensure any malfunction would be unrelated to the electrical system, control components were wired to power supplies instead of logic outputs from the motor driver.
Subsystems
FRAME
The frame is made of square aluminum tubing with bolted joints to allow for convenient dissassebly. Each joint features an angle bracket or custom waterjetted-bracket (sheet aluminum) for increased stiffness.
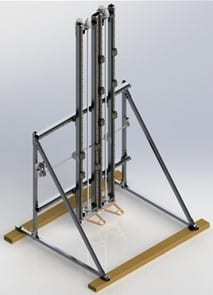
To mimic the competition testing environment, it was mounted on wooden 2x4s to attatch the the mock-testbed. The overall dimensions of the frame were kept as small as possible to reduce weight and meet NASA’s size requirements while maintaining a sufficient range of motion for each of the tools.
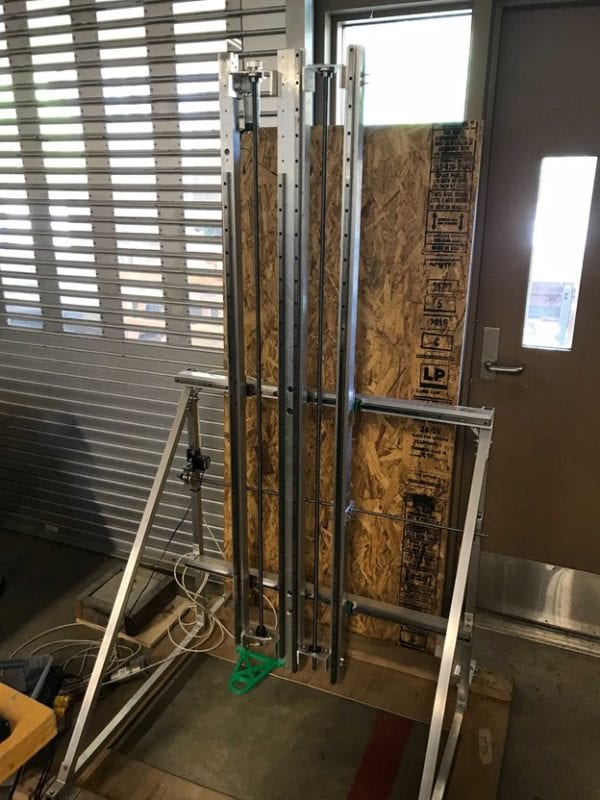
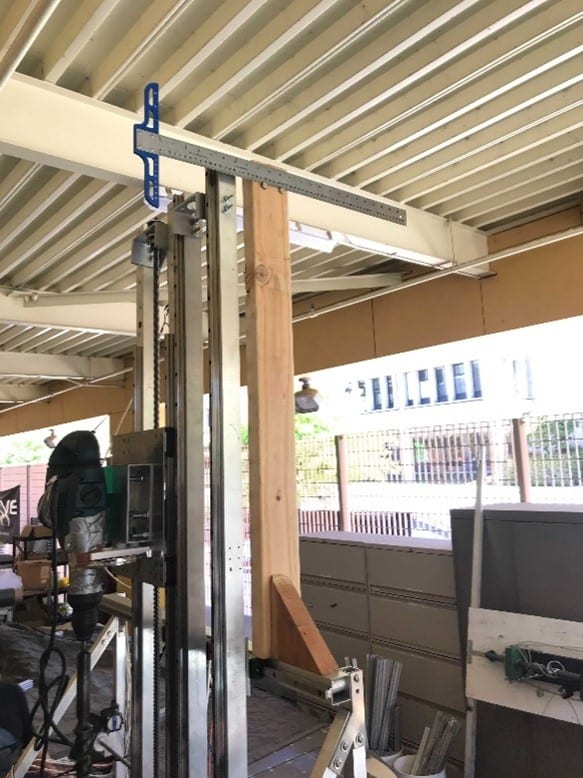
The resulting stiffness of the frame was found to be adequate; minimal deflection and zero damage was demonstrated during concrete penetration. The durability of the frame will be continue to be verified with repeated full system testing.
X-Z MOTION
Linear motion is achieved with ACME leadscrews, steel rails, linear bearings, a stepper motor for horizontal motion (“X-axis”), and gearmotors for vertical motion (“Z-axis”). All motors are connected to the leadscrews via aluminum pulleys and neoprene-rubber belts.
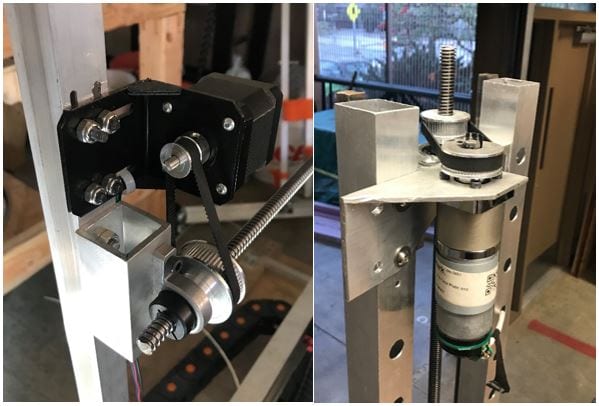
Control code for the X- and Z-axis motors was developed in C and includes failsafes/axis-homing via limit switches. This allows the lead screw movement to stop automatically when the tool carriage or drilling/heated auger tool plates meet their limit switches on the X- or Z-axis, respectively.
DRILLING SUBSYSTEM
The two main prospecting subsystems are the rotary hammer with masonry drill bit, and the heated auger. The rotary hammer is mounted to an 1/8″ aluminum “tool plate” that translates vertically on the frame via ball sliders. Once the rotary hammer has created a hole through the regolith layers and ~4″ into the solid ice, a servo motor flips the direction of the drill bit rotation to remove it from the testbed leaving an ~1.5″ diameter, ~0.5 m deep hole.
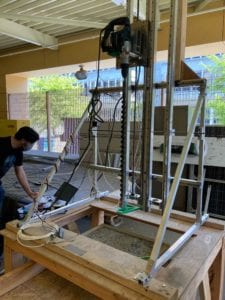
During the Mid-Project review test, it was observed that the drill bit could not cut through the concrete as quickly as it was being lowered into the material. To address this, the drill was lowered into the material and then the Z-axis gear motor was stopped to allow time for the rotary hammer to cleanly cut through ~1.5″ of concrete. Then the program was resumed to plunge further into the concrete. Using this intermittent descent strategy, a plunge rate of ~10 in/min was found using this method.
HEATED AUGER SUBSYSTEM
After drilling concludes, the heated auger is translated along the X-axis to align with the hole created by the rotary hammer. To remove debris from the drilled hole, a copper auger is plunged into the hole along the Z-axis as it is rotated by a gearmotor.
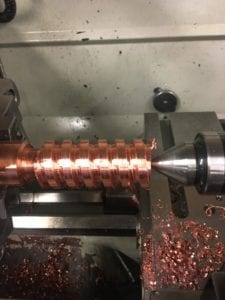
A cartridge heater is housed inside the tool shaft to heat the copper auger once it has come into contact with ice. A thermocouple is epoxied to the interior of the tool to monitor the temperature. A suction orifice for water intake and the nozzle for the waterjet are located along the auger flutes as shown in the Heated Auger Analysis section. The intake orifice is covered by a course mesh.
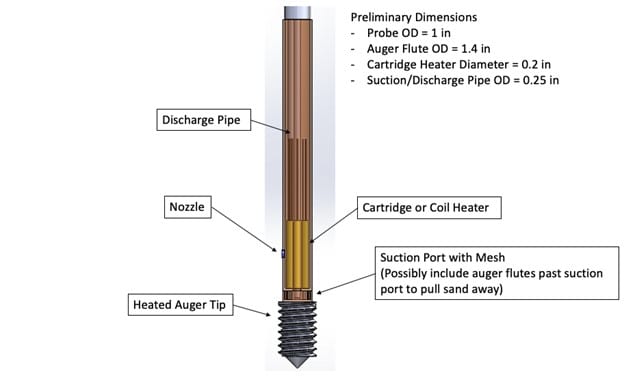
The tool shaft is ~1 m in length, so a rigid tool collar fixed to the tool plate was designed to supply structural support and alignment as it is lowered into the hole. The shaft is free to spin on needle roller thrust bearings housed in the collar.

WATER FILTRATION
Once the copper auger tip is below the surface of the ice:
- 1. The cartridge heater is turned on to melt a well in the ice.
- 2. Liquid water is drawn from the suction orifice through a 40-micron prefilter and recirculated for the waterjet.
- 3. The waterjet maximizes the ice well by spraying ~120ºF water at the well walls while the tool is slowly rotated.
- 4. Once the waterjet has been running for ample time, the water collection process begins.
- 5. The water is drawn through a Capstan 5-micron sintered bronze filter and deposited into the collection bucket.
The diagram below describes the water flow for both the recirculation and collection modes.
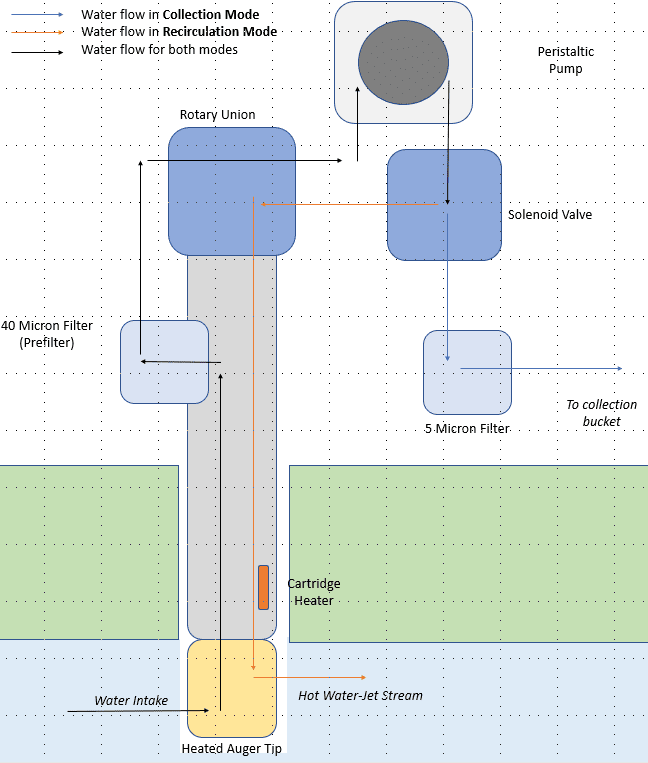
The main components within this subsystem are:
- Self priming peristaltic pump to pull water from ice layer
- 40 micron pre-filter to protect rotary union and pump
- Motorized ball valve to empty sediment trap of pre-filter
- Solenoid valves (2)
- Capstan 5-micron sintered bronze filter*
- Pressure transducers to monitor clogging
- Thermocouple to monitor auger and water temperatures
These components were assembled for an endurance test in May 2021 as shown below.
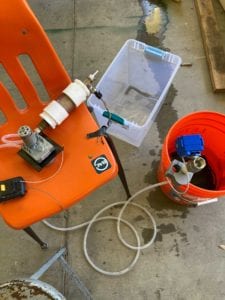
For this test, collection mode was considered. It was found that the average flowrate of the system is .122 gpm for clean intake water. An additional test was performed to verify filter efficacy. The following photos show the intake water and compares it to the water collected after passing through both filters.
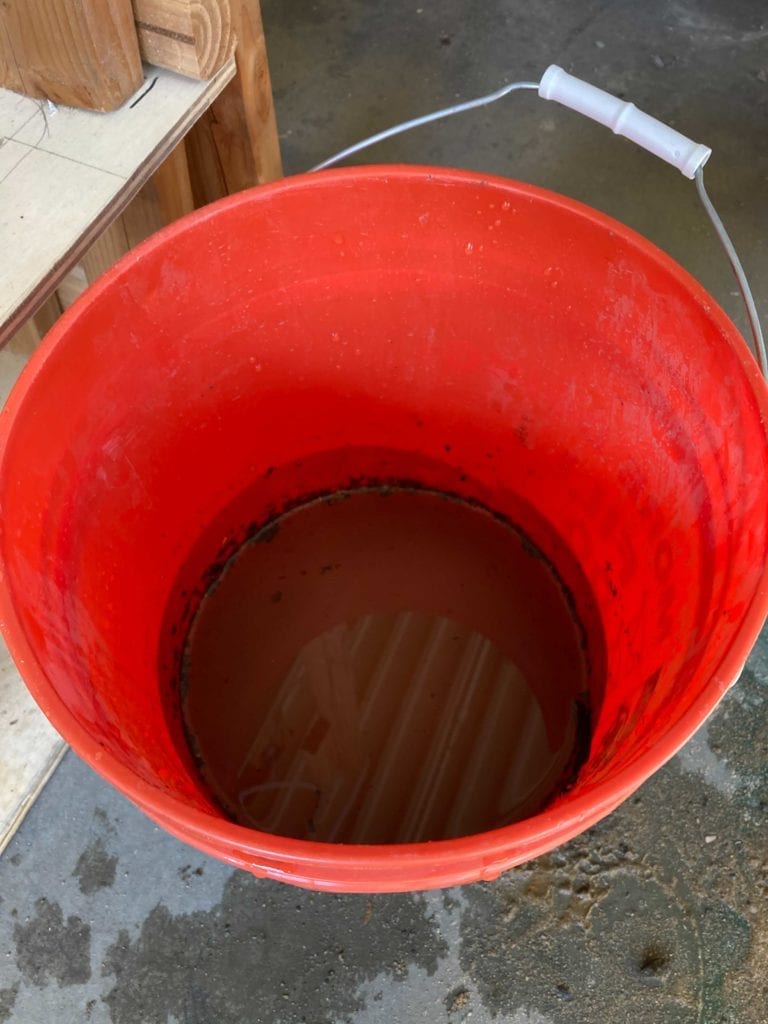
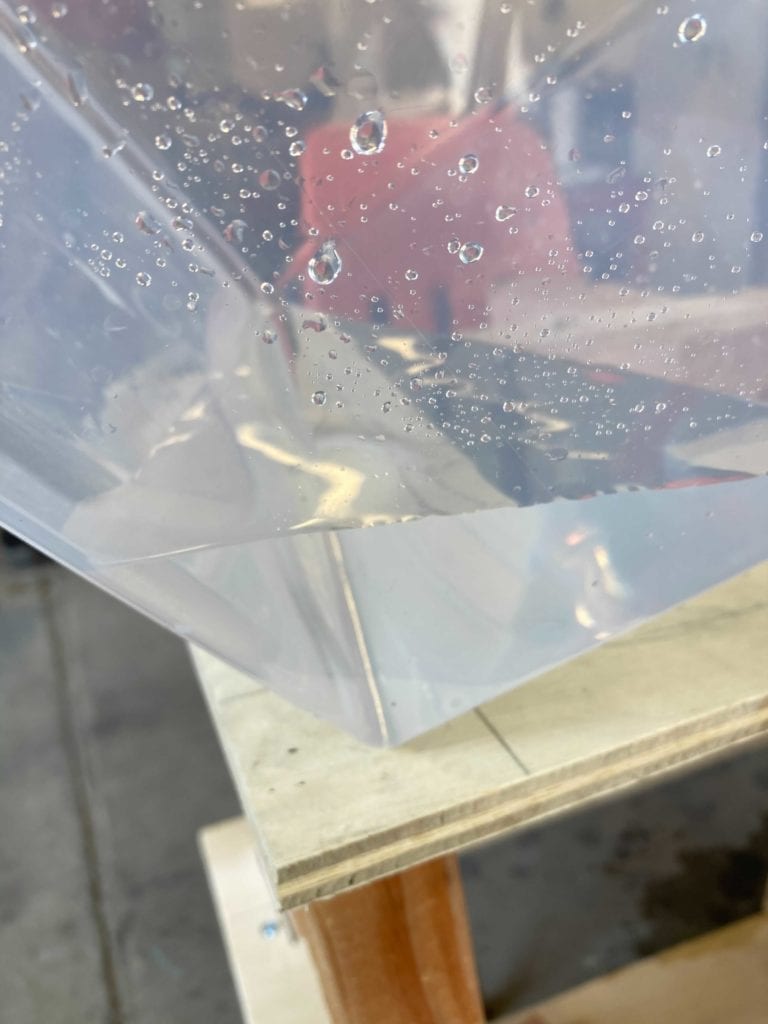
TELEMETRY
The telemetry system monitors the Weight-On-Bit (WOB) during drilling to ensure 150N (~33lbf) is not exceeded. The load cells were calibrated within +/- 10% accuracy to ensure accurate WOB readings. The WOB recorded during drilling was viable in producing insight into the varying overburden layer thicknesses and relative hardness.
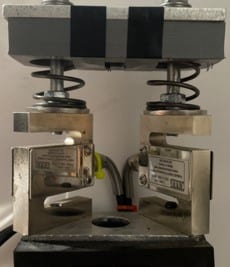
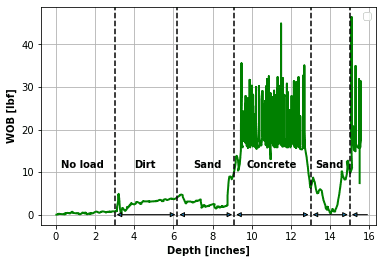
CONTROLS
An FSM was created to encapsulate the controls of the overall system. A task scheduler was developed for task sequencing and interrupt handling to enable tasks to run autonomously with no need for user input. Basic error handling was included to ensure autonomous operation is not compromised when something unexpected occurs.
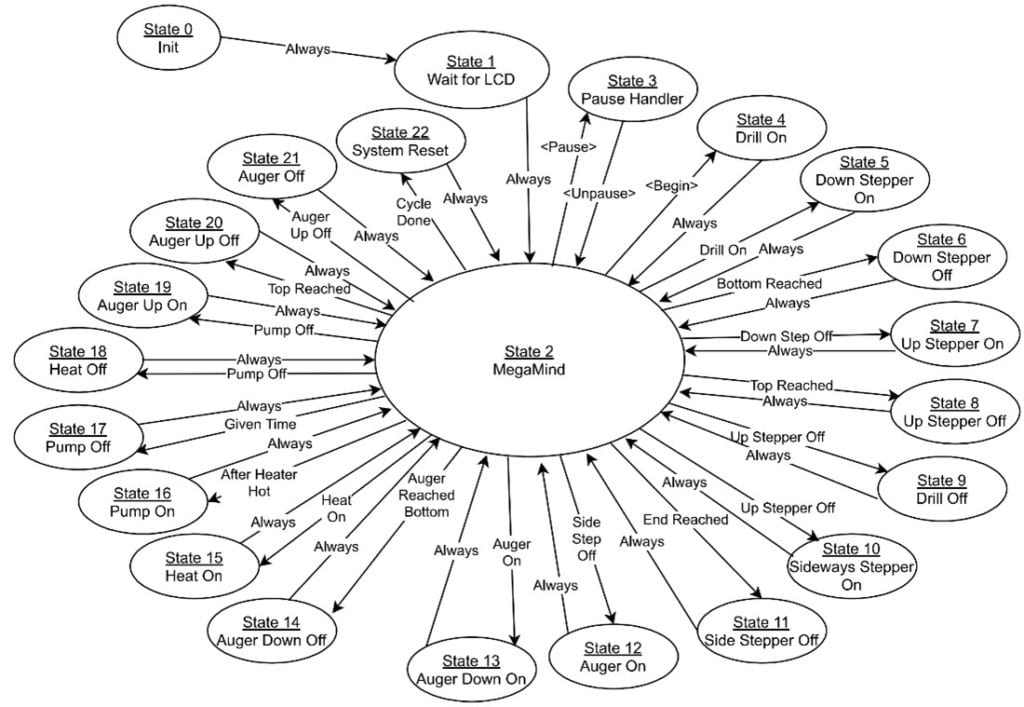
An example of one branch of the FSM is the program for the heated auger subsystem. Using thermocouples placed inside the heated auger, the team used a temperature control system (simple on/off based on if-else logic) to develop the most efficient method for melting ice quickly. The LED representation pictured below was used to test that subsystem independently of the rest of the system.
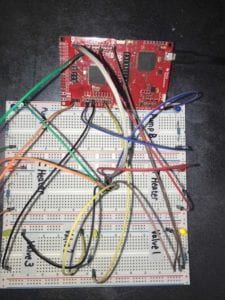
The software also allows for manual operation in the case where the program malfunctions and cannot put itself back on track. In this scenario, a computer can be connected to the system and commands can be run from the command line.
ELECTRICAL
The X-axis stepper motor and Z-axis gear motors run using 12 VDC, while the TI MSP432 microcontroller, servo motor for the rotary hammer’s rotation, and encoders run at 5 VDC. DC motor drivers are used for the operation of each gear motor, as well as the pump in the heated auger system with PWM logic control from the microcontroller. There are six relays, with three of them controlling 12 VDC for the valves, and the other three controlling 120 VAC for the Rotary Hammer, Heater Cartridge, and Rotational Heater.
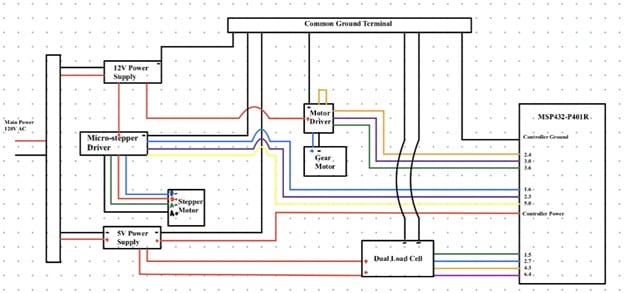
All electronics are housed in a central containment unit at the base of the platform within which a common grounding bond was made with every component to avoid shorting. On-board DC power supplies are used to convert the 120 VAC power source (wall outlet) to 5 VDC and 12VDC which is linked to each component through a terminal block. An ammeter is currently used to monitor the system’s overall current draw in order to remain below the 9 A ceiling.
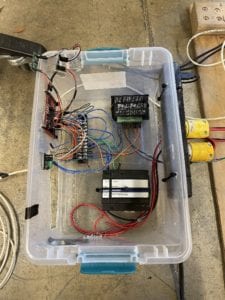
Verification Prototype
To satisfy NASA’s Mid-Project Review (MPR) requirement, a mostly integrated test demonstrating drilling capability, linear motion, and the water collection system was completed in March 2021. The video above contains footage of that test.
The STYX & STONES final verification prototype was completed on May 27th, 2021 and full system testing to simulate the competition environment began.
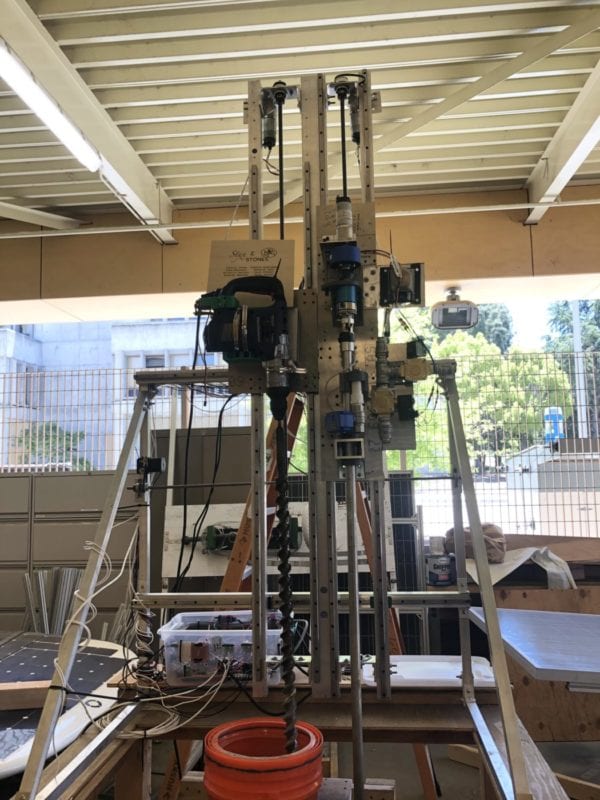
The results of the first full system test on the final prototype yeilded the following:
- Full system autonomy achieved; no operator intervention necessary
- Vibration during hammer drilling requires lock nuts everywhere
- Clogging from debris in the auger orifices is negligible
- Frame design is excellent – no noticable deflections
Current Status and Recommendations
Full system testing of the prototype is continuing at the Bonderson Project Center on Cal Poly’s Campus until the competition in September 2021. Schuyler is improving the system’s autonoumous control, while Rebecca continues to validate the telemetry system’s ability to recognize layer hardness. Brad and Michelle are continuing to assess the heated auger’s structural integrity while Jacob improves its control system. Alex continues endurance testing on the water filtration system, while Dom and Tyler continue to monitor the frame stability and system power use. Michelle and Schuyler developed plans for a the system test and are working with the rest of the team on documentation.
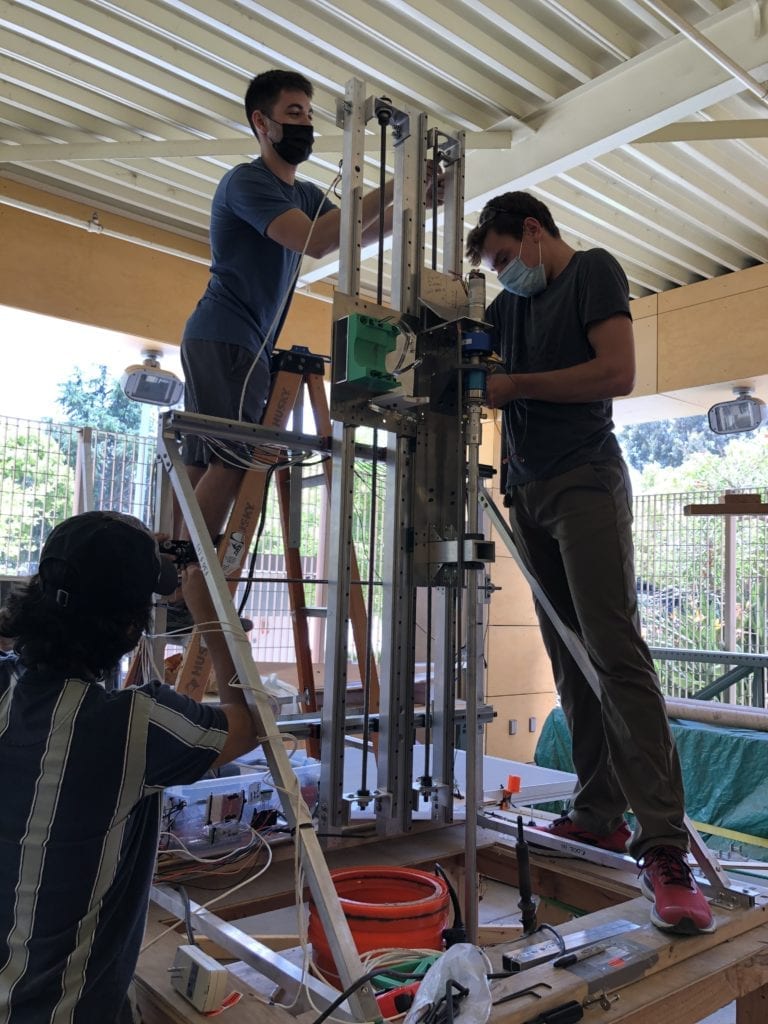
Once testing is complete, the prototype will be shipped to the NASA Langley Research Center for the competition. Following competition, the project will be returned to Cal Poly for potential use of future senior projects.
The major recommendations from this prototype are:
- Wire routing is not simple, plan ahead.
- Plan for contingencies, both engineering and logistical.
- Future teams recommended to focus on improving a few subsystems instead of building from scratch.
- Off the shelf parts wherever possible saved a lot of time.
- Test incrementally so problems can be isolated as they occur.
- Organization for a project of this scope is imperative.
Project Links
Our Project Plan and Mid-Project Review reports that were submitted to NASA are available below to learn more about our design process.
STYX & STONES Project Plan
STYX & STONES Mid-Project Review
Some insights from the team throughout the process.