Our Team
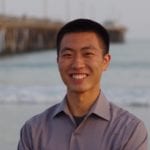
Jonnah Lee
I am a fourth year Materials Engineering student. I was born and raised in Orange County, California. My hobbies include hiking, running, and baking.
Acknowledgements
I would like to thank my project sponsor Dr. Shanju Zhang from the Chemistry Department, as well as my senior project advisor Dr. Trevor Harding. Without their help, this project would not have been possible. I would also like to thank and acknowledge Madeleine Schleinitz for all her help on this project.
Digital Poster
Background
While plastics provide many benefits in everyday products, they also have problems. The main problem is ironically due to their low cost. Since plastics are so cheap, many consumers will not think twice before throwing out a plastic product. In fact, plastic is so cheap, it is possible to produce large quantities of various plastics and products. According to the Environmental Protection Agency (EPA), the United States produced 35,370,000 tons of plastic in 2017. This total has only increased since then. Unfortunately, according to the EPA, from 1960 through 2017, none of the plastics produced in this time span were commercially compostable. This means that plastic waste either ended up getting recycled, incinerated for energy, or ended up in a landfill. In fact, the majority of plastic waste ends up in landfills.
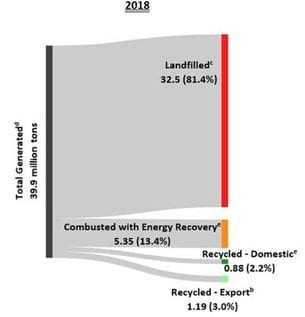
Solvent Casting
To produce the films the technique used was solvent casting. In this method, a film is produced by evaporating out solvent. For this project, the solvent used for both the PLA and CNF stock solutions was dichloromethane. Once the stock solutions were combined, sonicated, poured into an aluminum dish to evaporate the solvent, the pans were then placed in a desiccator to remove any residual solvent. Once completely dried, the films were then separated from the pan and were ready for testing. The main difficulties with using this technique is the formation of bubbles in the films that contained nanocellulose. The formation of bubbles is an issue due to the bubbles negatively impacting the mechanical properties of the film. As a result, when performing mechanical testing, these portions of the film were discarded. Additionally, solvent casting is not a suitable method for mass production for this reason, but was adequate in producing samples to be used for testing.
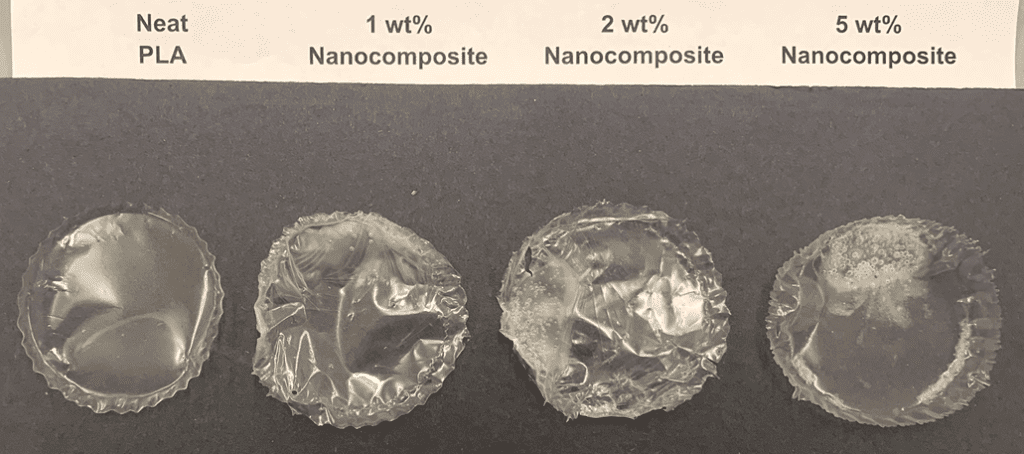
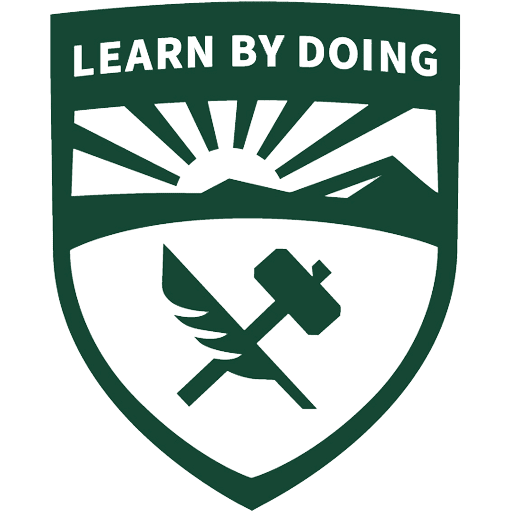
Problem Statement
The goal of this project is to produce polylactic acid (PLA) films reinforced with cellulose nanofibrils (CNF). Through this, the goal is to determine if surface modifications on the CNF helped improve dispersion of the CNF particles in the PLA matrix as well as determining how the thermal and mechanical properties of the film are affected. The expected effect is to see a decrease in degradation temperature as the nanocellulose content increases. For mechanical properties, the expected effect is to see an increase in storage modulus as the nanocellulose content increases.
Testing
Thermograviometric analysis (TGA)
The TGA data collected showed the expected trend of the degradation temperature; decreasing degradation temperature with increasing nanocellulose content. This is important to note for the processing side (production of bags) because this indicates a shrinking processing window (temperature range at which the films can be processed). The processing window is bound by the glass transition temperature and degradation temperature.The DMA test performed on the films were used to determine the storage modulus of the different films. The expected trend was to observe an increase in storage modulus as the nanocellulose content increased. However, what was observed was a decrease in storage modulus in the 1 wt% and 2 wt% films but an expected increase in storage modulus in the 5 wt% film. One possible explanation for this unexpected trend is due to agglomeration of the nanocellulose particles.
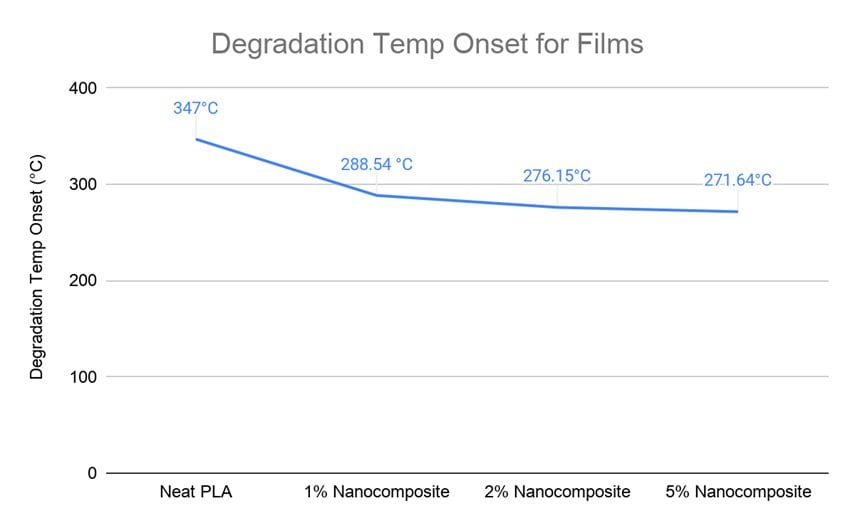
differential scanning calorimetry (DSC)
Based on the DSC data shown below, there was no significant change with the added nanocellulose content. When combined with the data collected from the TGA tests, the data suggests that the processing window for these films decreases with increasing nanocellulose content. This is because the processing window is the temperature range between the melting temperature and degradation temperature. Since the melting temperature is consistent but the degradation temperature decreases, the allowable processing window shrinks.
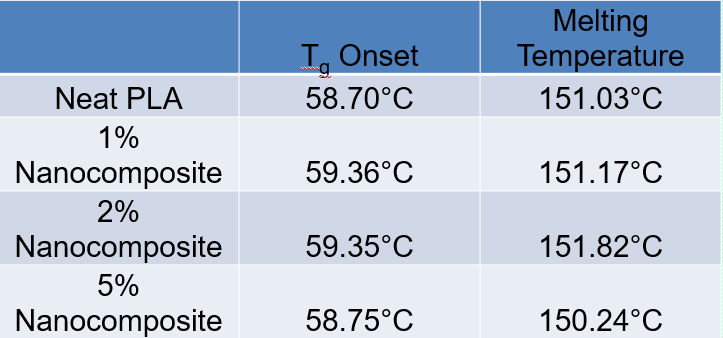
dynamic mechanical analysis (DMA)
The DMA test performed on the films were used to determine the storage modulus of the different films. The expected trend was to observe an increase in storage modulus as the nanocellulose content increased. However, what was observed was a decrease in storage modulus in the 1 wt% and 2 wt% films but an expected increase in storage modulus in the 5 wt% film. One possible explanation for this unexpected trend is due to agglomeration of the nanocellulose particles.
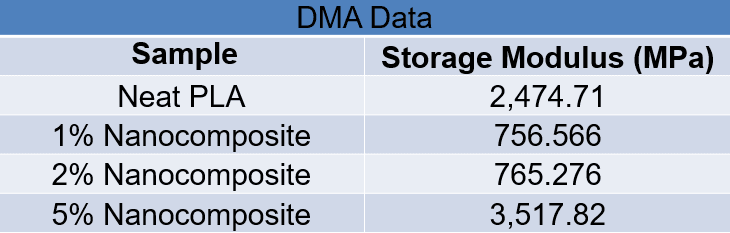
Experimental Procedure
To perform the experiment for this project, the first step was to produce a neat PLA film and three other PLA films reinforced with varying amounts of CNF. In total, four films were produced: a neat PLA film that acted as the control, a 1 wt% film, 2 wt% film, and 5 wt% film. To produce the films, two stock solutions were used. One stock solutions contained PLA pellets dissolved in dichloromethane and the other stock solutions contained the surface treated CNF dispersed in dichloromethane. The stock solutions were then measured according to their calculated content. The stock solutions were combined in vials and sonicated. The combined solutions were then poured in aluminum dishes to evaporate the solvent. Following this, the films were then tested using the TGA, DSC, and DMA. The TGA was used to determine the degradation temperature of the films, the DSC was used to determine the glass transition temperature and melting temperature, and the DMA was used to determine the storage modulus of the films.
Conclusion
1.Nanocellulose content interacts with polymer matrix in both predictable and unpredictable ways
2.Based on the DMA data, a biodegradable plastic bag is possible, but further mechanical testing is required for a definitive conclusion
Future Work
•Use different dispersion methods (longer sonication times or different polymerization techniques)
•Perform more mechanical testing (tensile testing)