The Group
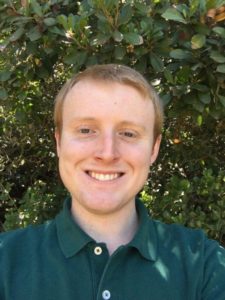
Christopher Fahey
Class of 2021
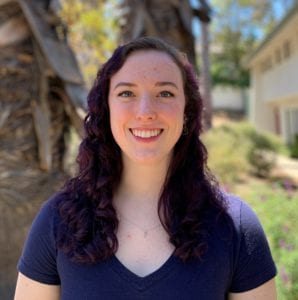
Robin Payne
Materials Engineering
Class of 2022Newly Developed Antifouling Coating Alloys for Hydraulic Cylinder Applications
Christopher Fahey* Robin Payne* Prof. Blair London* Jonathon Bracci** James Vecchio**
*California Polytechnic State University, Materials Engineering Department **Oerlikon Metco
Background
Marine fouling is the accumulation of organisms on a surface in a marine environment. The organisms can range from algae to barnacles and can cause drag on surfaces as well as inhibiting mechanical components. Typically, marine fouling is mitigated with a fouling resistant coating, which resists fouling using a biocide. Oftentimes these coatings take the form of a paint which contains copper. There are some applications where these traditional coatings cannot be applied, for this project the application of interest is offshore hydraulic cylinders. These cylinders are often clad for corrosion resistance, several examples of alloys used for this purpose and designed for this purpose were tested to compare their marine fouling properties.
Copper containing alloys are expected to exhibit the best resistance to fouling as copper is an effective biocide, it has a well understood relationship with fouling resistance. The other alloys do not have any factors that should affect fouling performance based on the literature.
Samples
Inconel 625
70% Ni, 20% Cr, 8% Mo
Metco 1720
NiCr based, carbide containing, similar to Inconel 625
P105-X3
NiCr based, carbide containing
Ultimet
54% Co, 26% Cr, 9% Ni, 5% Mo
P76-X24
16% Cu, boride containing
Monel 400
70% Ni, 30% Cu
CuproNickel
50% Ni, 50% Cu
Monel 450
70% Cu, 30% Ni
Testing Methods
The mass of each sample was measured using a precision balance, and samples were engraved with a number to identify them. The samples were then secured in a modified crab cage at four points using high strength monofilament fishing line. The cage doors were closed using zip ties, and the outside of the cage was covered in steel mesh to catch any samples if they came loose. A polyethylene rope was used to tie the cage to the lower platform of the Cal Poly Pier, and to attach a ten-pound mushroom anchor to the bottom of the cage to keep tension on the rope and stabilize the cage in the surf. The cage was tied off with enough length on the rope to ensure it stayed submerged at low tide. The samples were left in the ocean for a total of nine weeks and were checked twice to make sure the testing rig was holding up and to assess fouling amount.
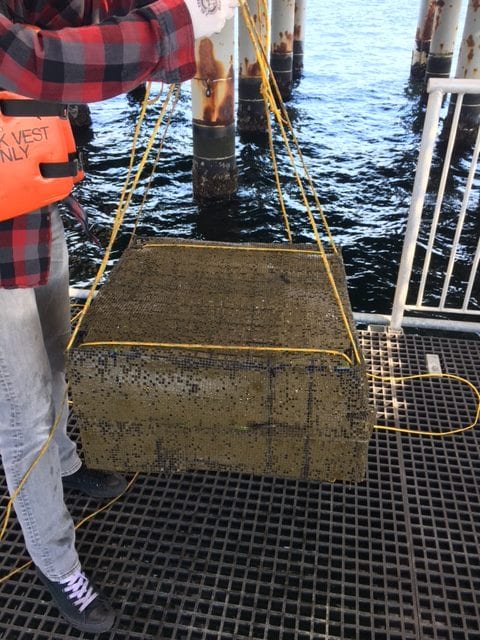
Fouling Mass
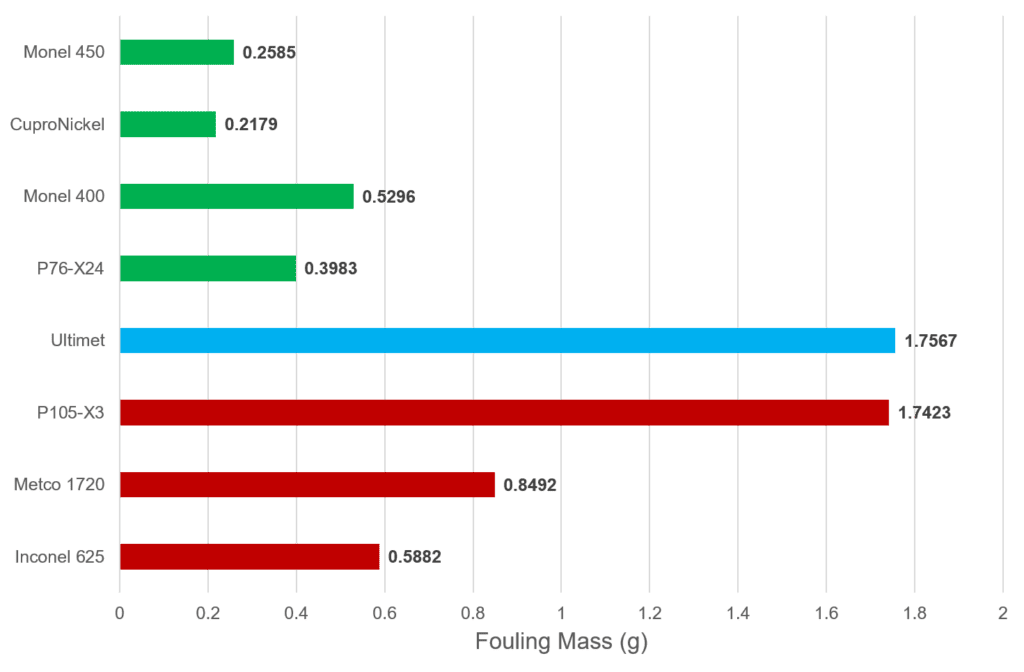
Samples were weighed before and after immersion to determine the mass of fouling that developed on each sample.
Fouling Area
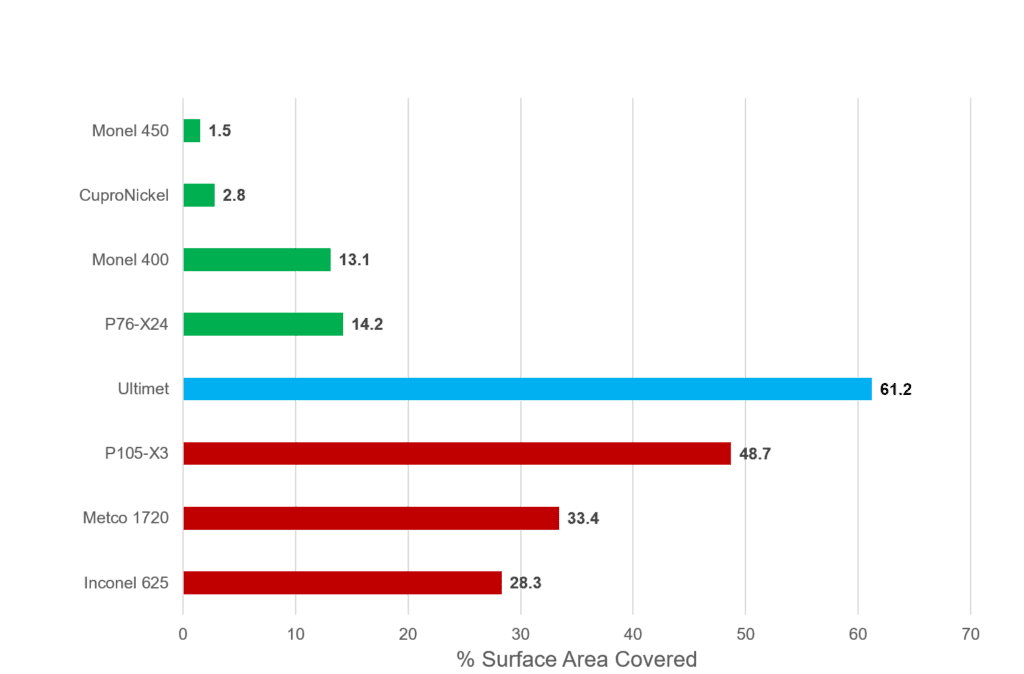
The percentage surface area covered by fouling was determined for each sample. This more clearly shows the trends in fouling behavior. The Cu containing alloys fouled the least, and generally a higher Cu content resulted in better fouling resistance, with P76-X24 as an exception. Ultimet was the most fouled alloy. The Ni-Cr alloys fouled more than the Cu containing alloys but less than the Ultimet and there was variation within the category.
Fouling Adhesion
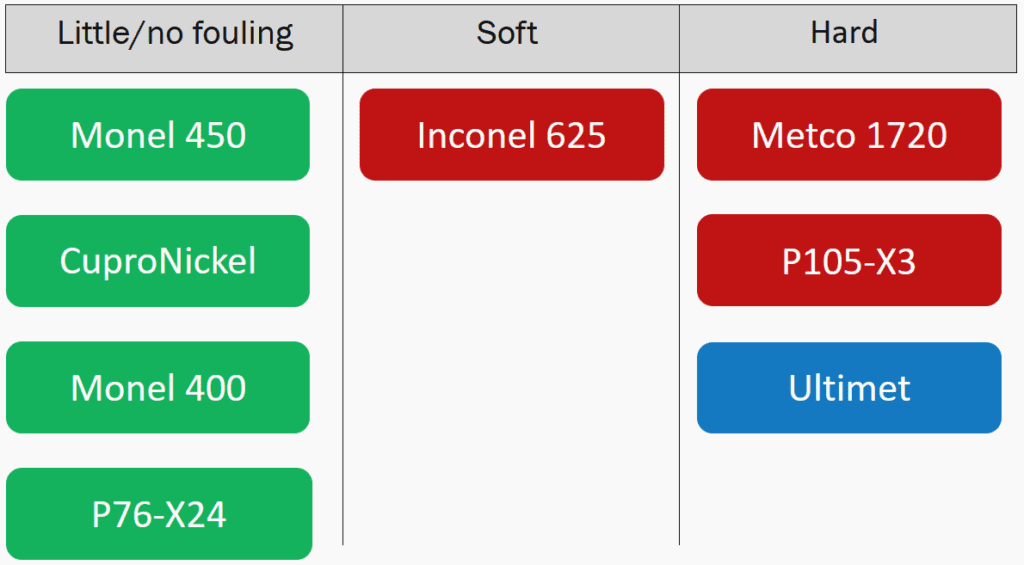
Samples were qualitatively compared by breaking them into three categories. All of the Cu containing samples were either not fouled or what fouling there was easily came off. The Inconel 625 was extensively fouled but lacked any hard fouling. The Metco 1720, P105-X3 and Ultimet were the most fouled and also had hard fouling establish on them.
Mass Lost to Corrosion
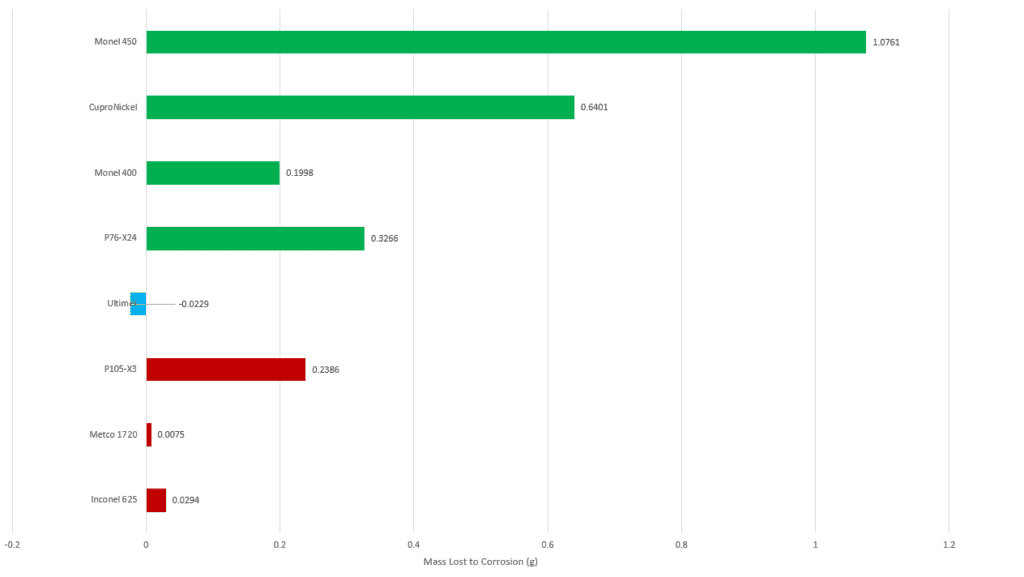
Sample masses were also used to determine the mass each sample lost to corrosion. With the Cu containing alloys corrosion was generally correlated with Cu content, the alloys with higher Cu contents corroded more, with the exception of P76-X24. The Ultimet sample exhibited no corrosion. The Ni-Cr based alloys corroded less than the Cu containing alloys, though the P105-X3 corroded significantly more than the other two in the category.
Fouling Area and Hard Phase
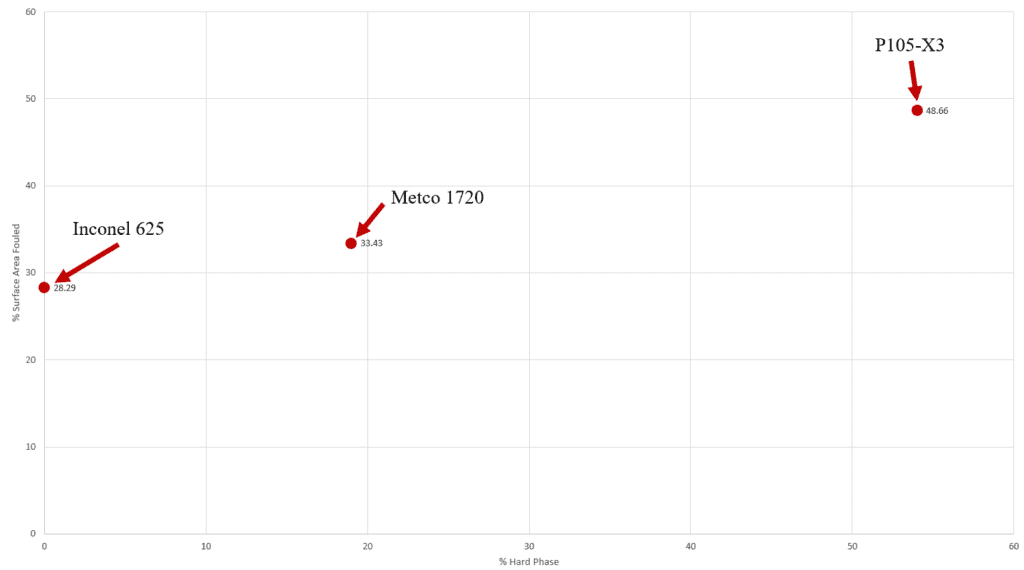
Graph shows the hard phase fraction and surface area fouled for the three NiCr samples.
Fouling Area and Cu Content
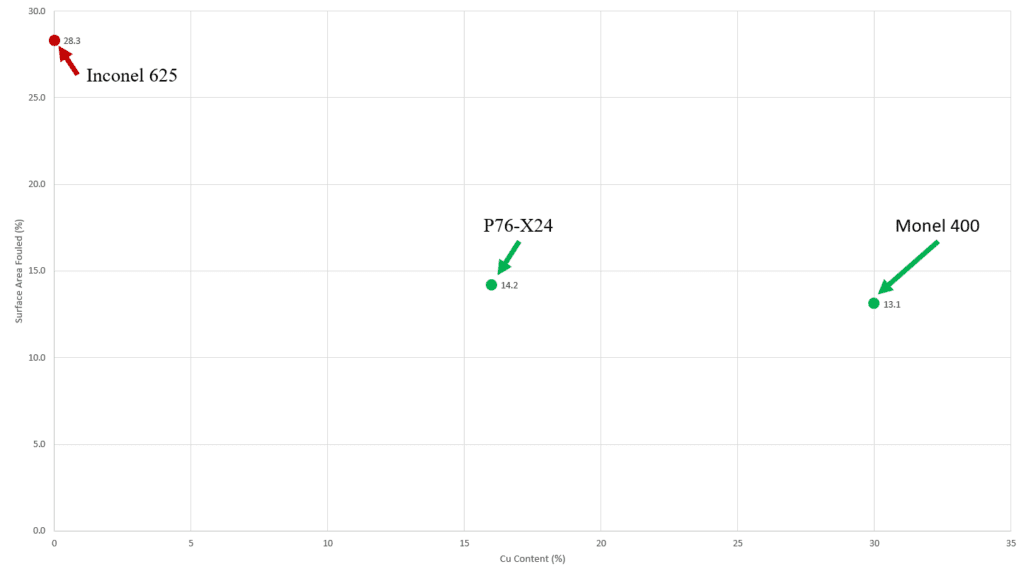
Graph shows the copper content and surace area fouled for Inconel 625 (0% Cu), P76-X24 (16% Cu), and Monel 400 (30% Cu).
P76-X24 Corrosion
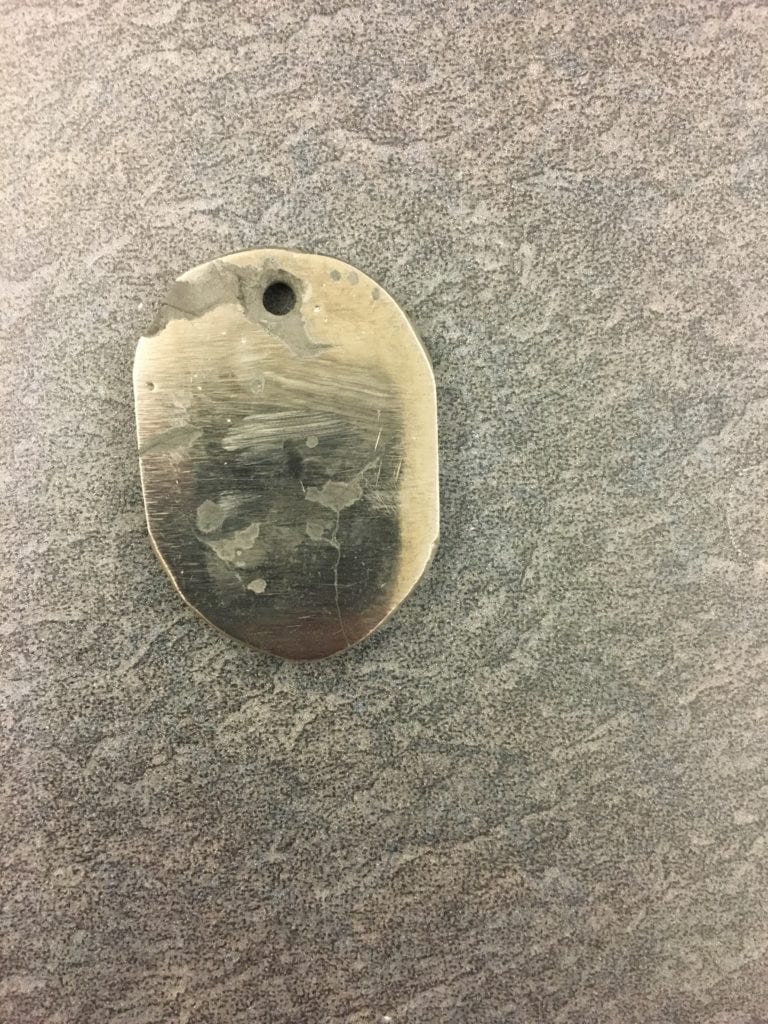
The P76-X24 corroded differently than the other samples, the other alloys primarily exhibited uniform corrosion with minor pitting, P76-X24 exhibited highly localized corrosion underneath the fouling.
Discussion
There appears to be a correlation between hard phase fraction and fouling in the NiCr alloys. This suggests that alloys with more hard phase present will foul quicker.
The P76-X24 exhibited fouling resistance similar to the Monel 400, despite X24 only having 16% Cu compared to the Monel 400’s 30% Cu. An explanation for this is that the X24 has a multiphase structure with about 55% borides. This concentrates the Cu in the matrix phase resulting in a local Cu composition of 40%, which suggests that the Cu leaching behavior is de localized enough to protect the Cu deficient boride phases.
The P76-X24 performs slightly worse than the Monel 400. This is potentially due to the Cu being present in only 45% of the alloy resulting in the fouling resistance being less efficient. Another explanation could be that the high fraction of hard phase in the alloy results in worse fouling than the single phase Monel 400.
P76-X24 corroded differently than the other Cu containing alloys, it corroded heavily underneath the fouling. It is thought that this is due to the presence of borides in the structure, as this is the primary difference between P76-X24 and the other single phase Cu containing alloys. P105-X3 corroded more than the other Ni-Cr alloys, the explanation for this is that a lot of the Cr content is in the hard phases present, leaving the matrix phase with a lower Cr content and reducing the alloy’s corrosion resistance.
Conclusions
- 1. There is a correlation between hard phase fraction and fouling.
- 2. Multiphase alloys with Cu concentrated in a single phase can achieve better fouling resistance than a single-phase alloy with the same overall Cu content.
- 3. Boride strengthened alloys are not suitable for use in a marine environment.
Recomendations
- 1. For marine applications, hard phase fraction should be limited to resist fouling.
- 2. Overall Cu content in marine alloys can be lowered by concentrating it in the matrix phase through the incorporation of preferential multiphase structures.
Inconel 625
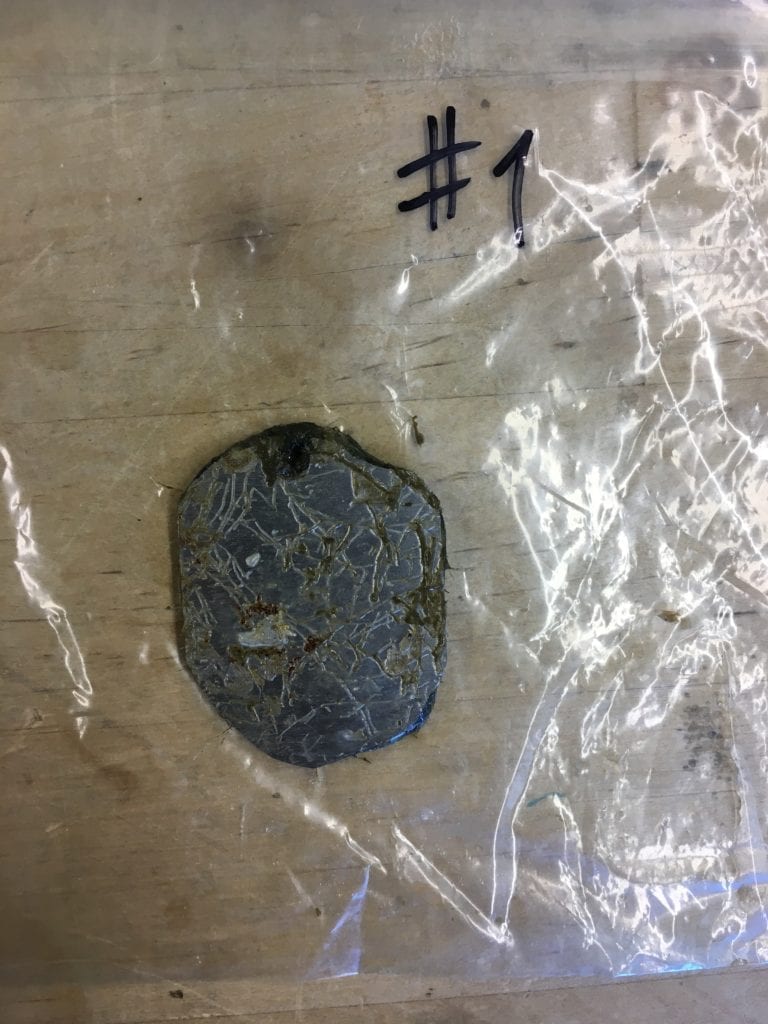
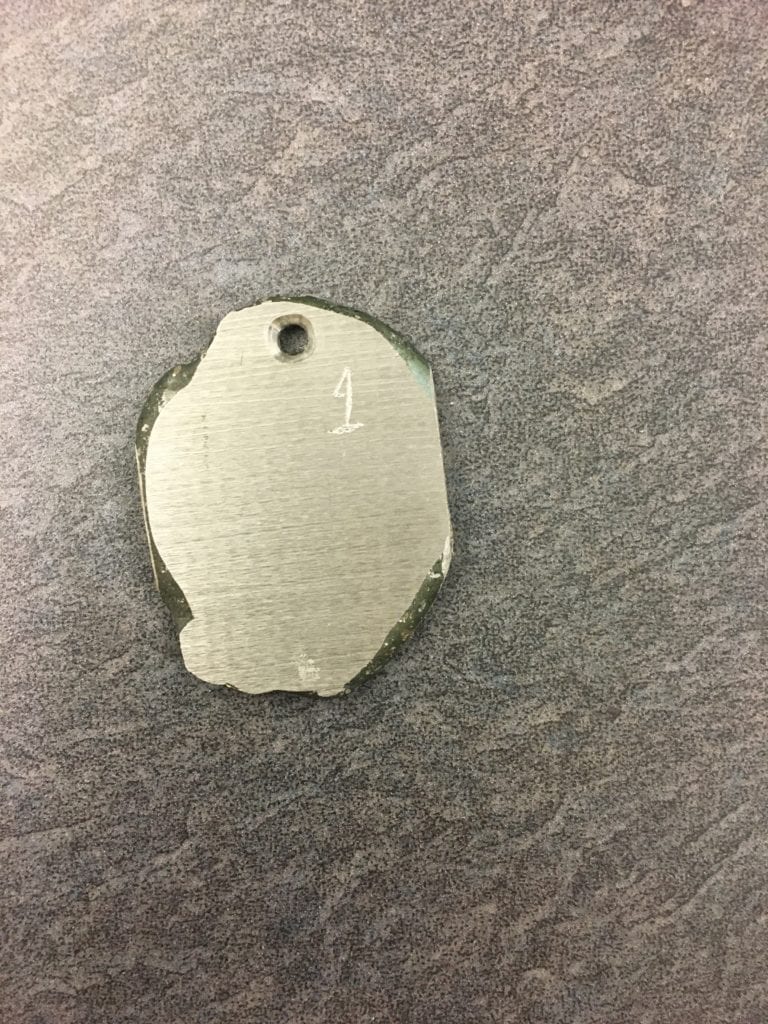
Metco 1720
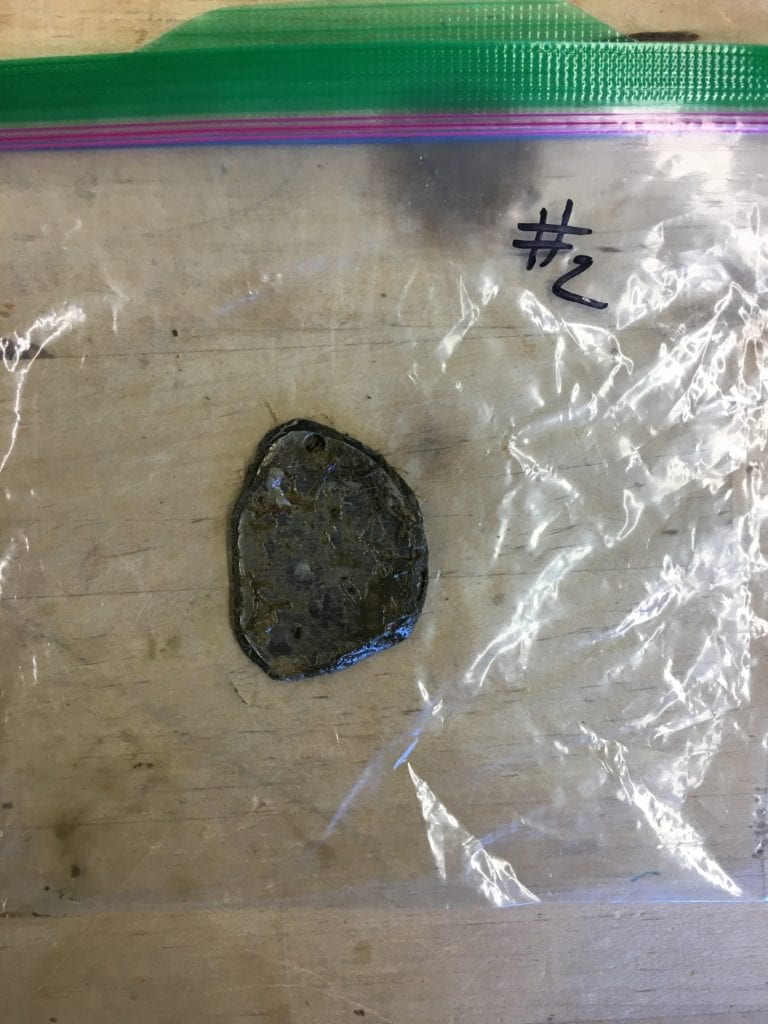
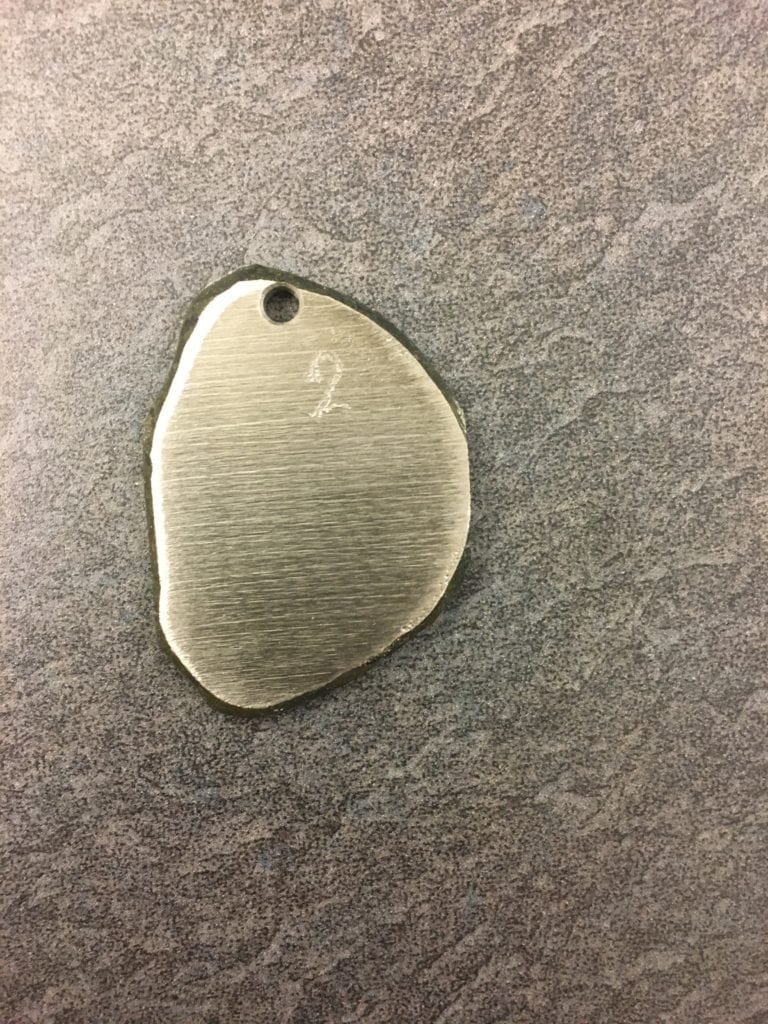
P105-X3
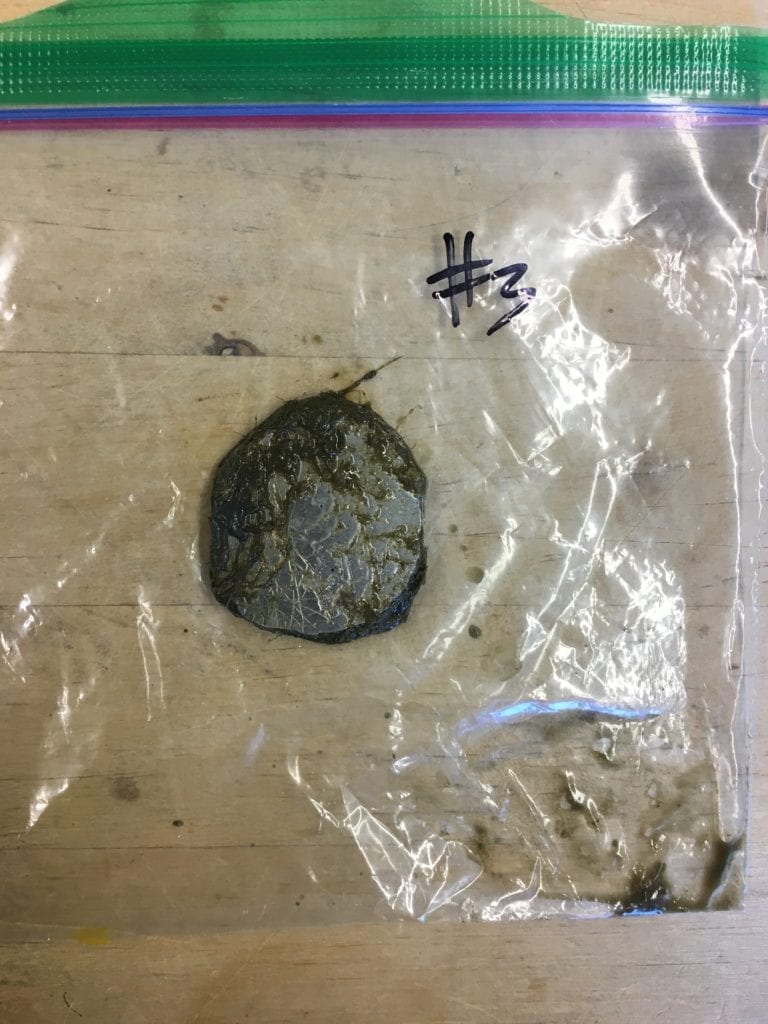
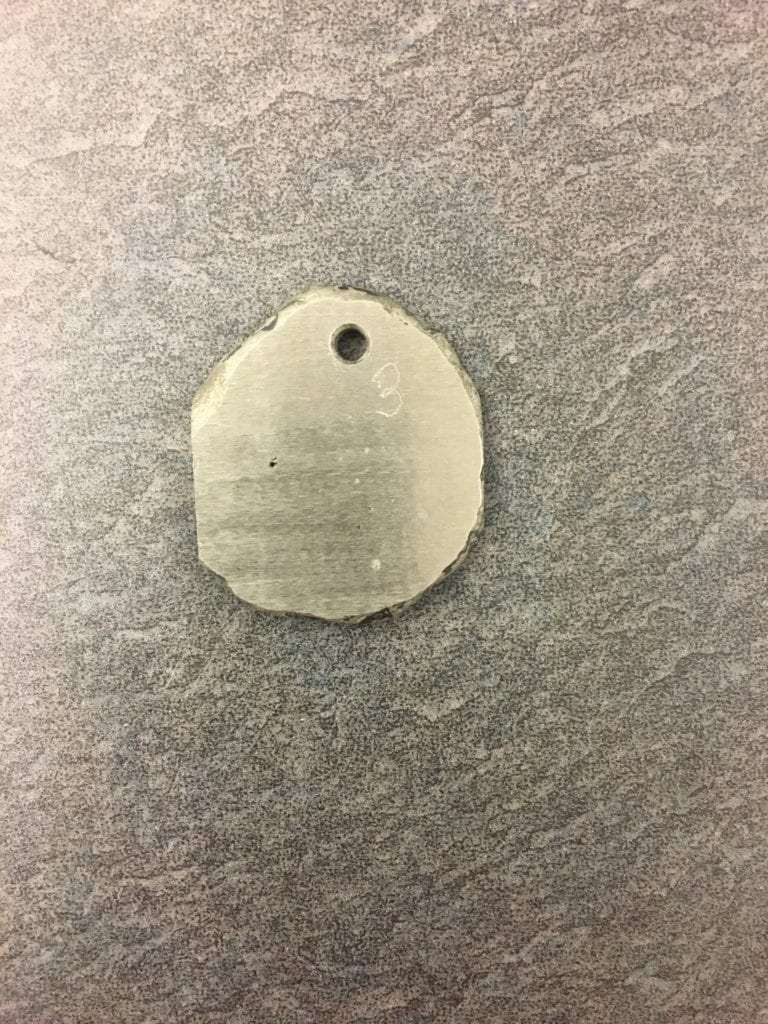
Ultimet
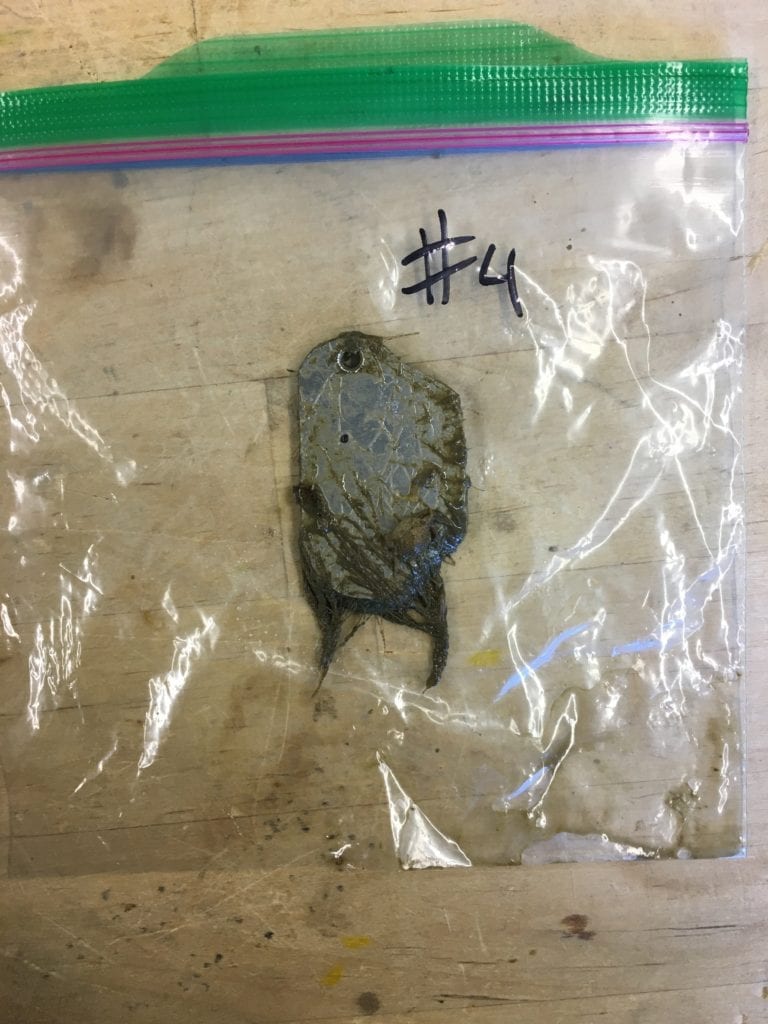
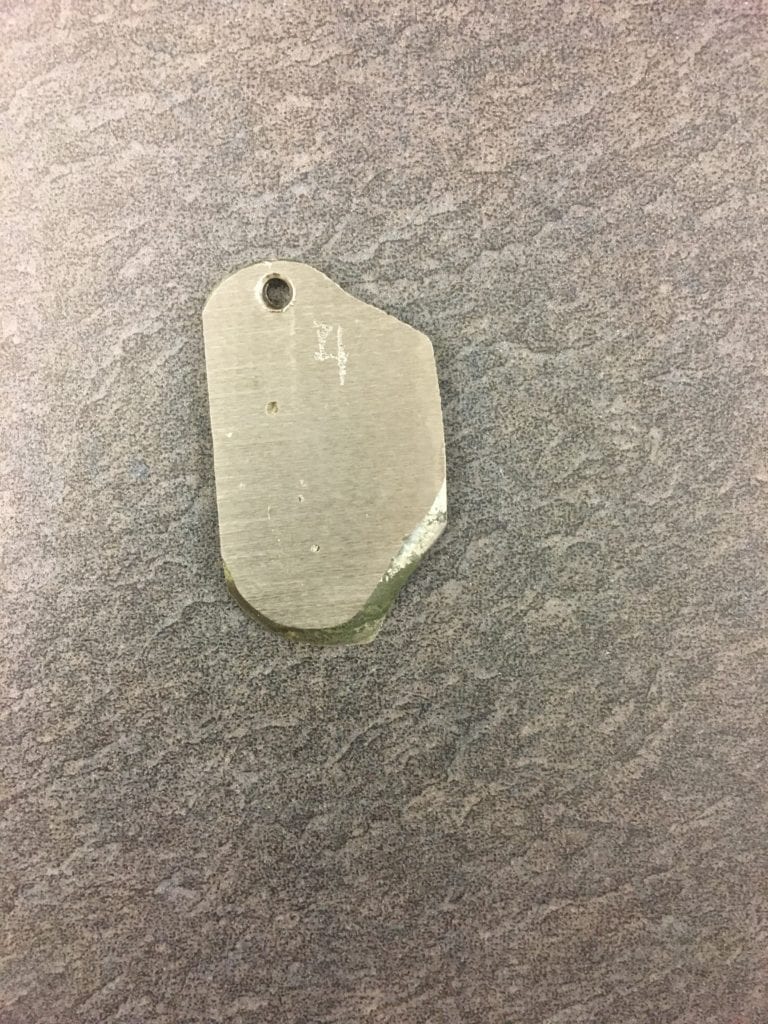
P76-X24
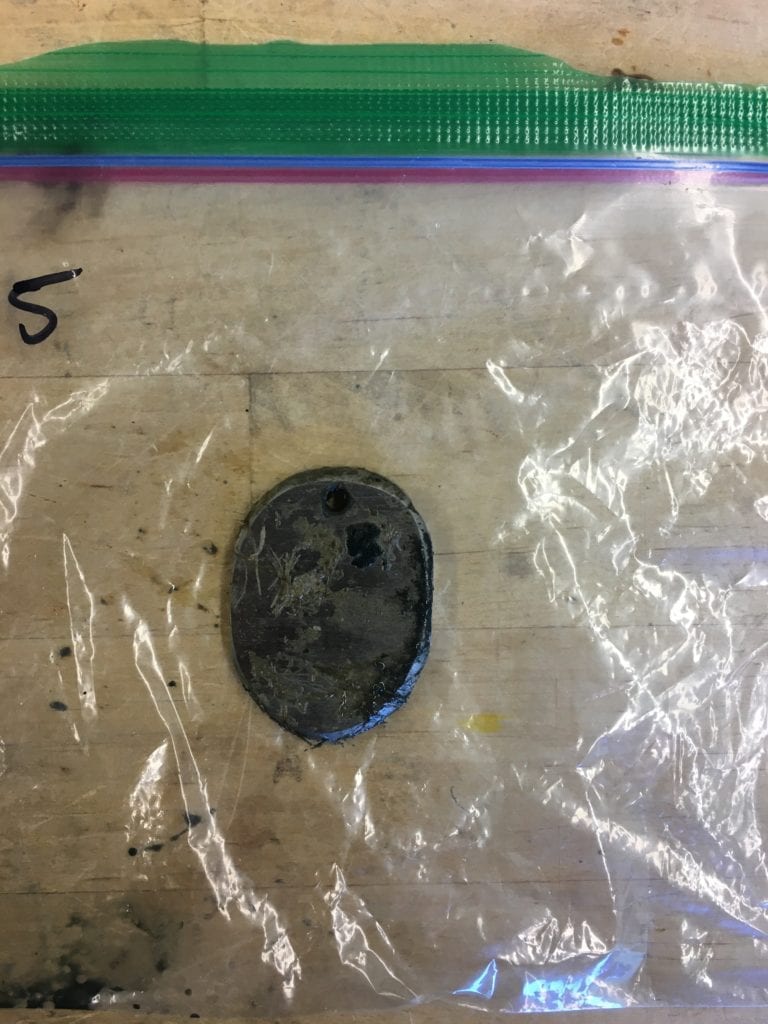

Monel 400
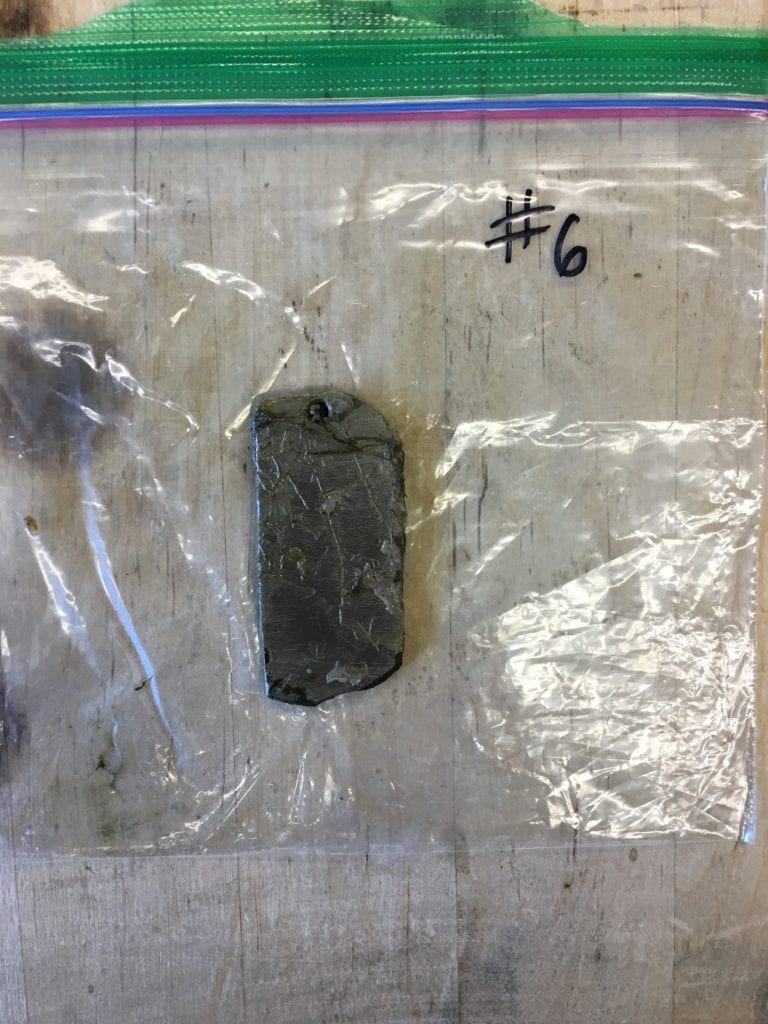
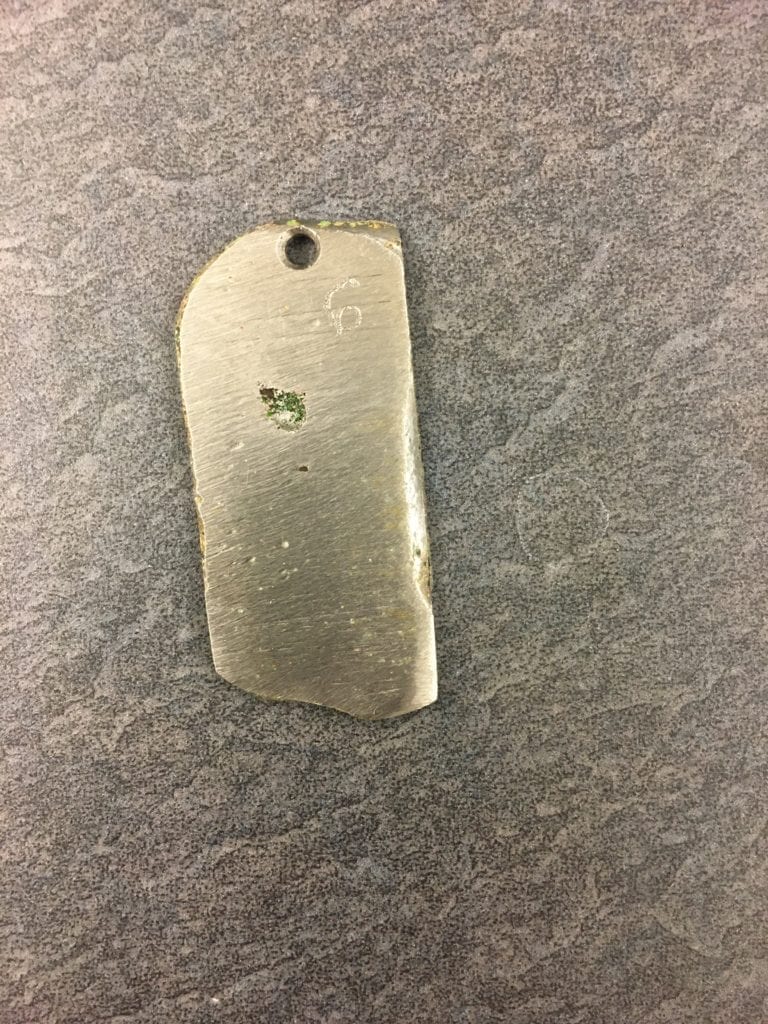
CuproNickel
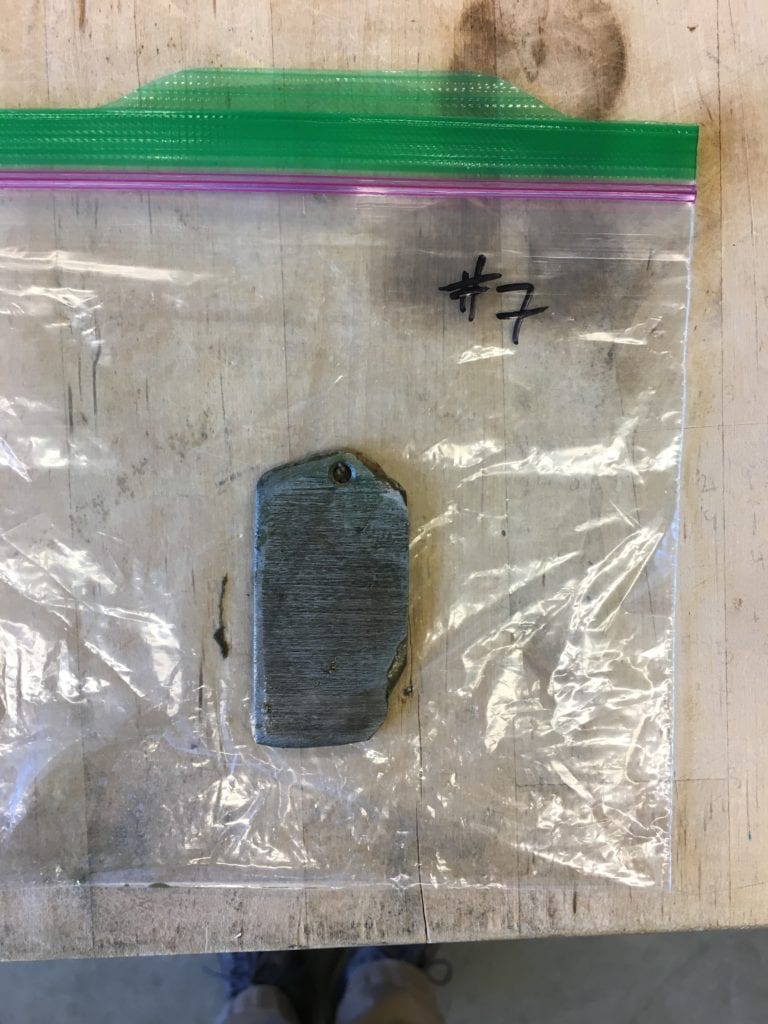
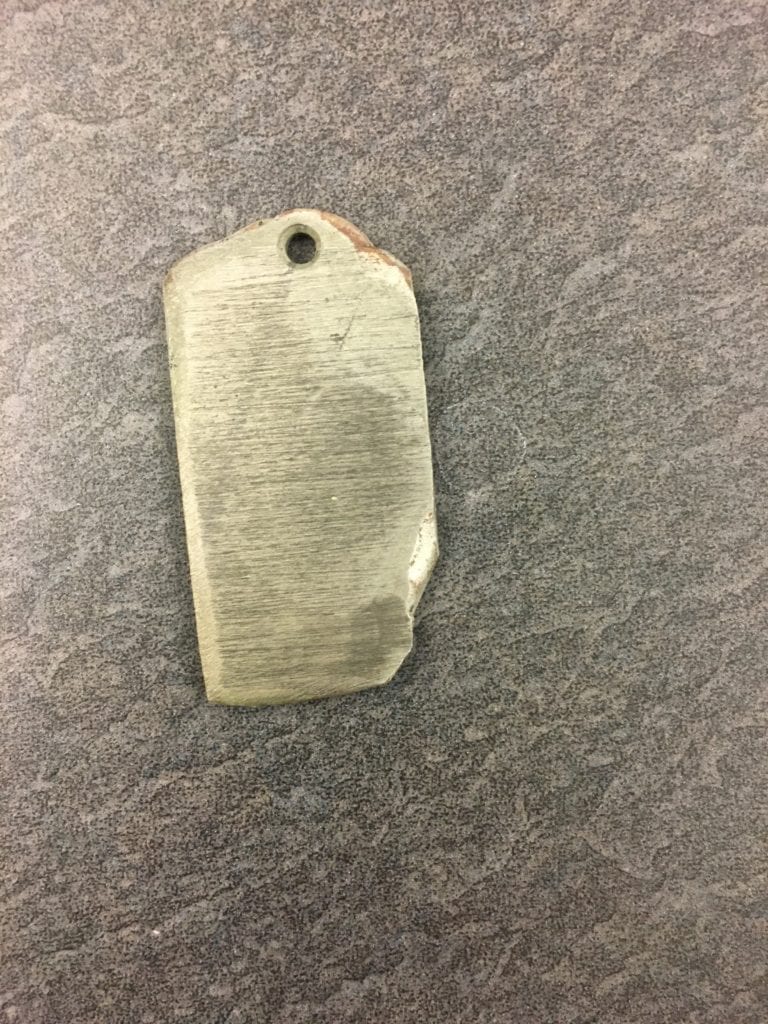
Monel 450
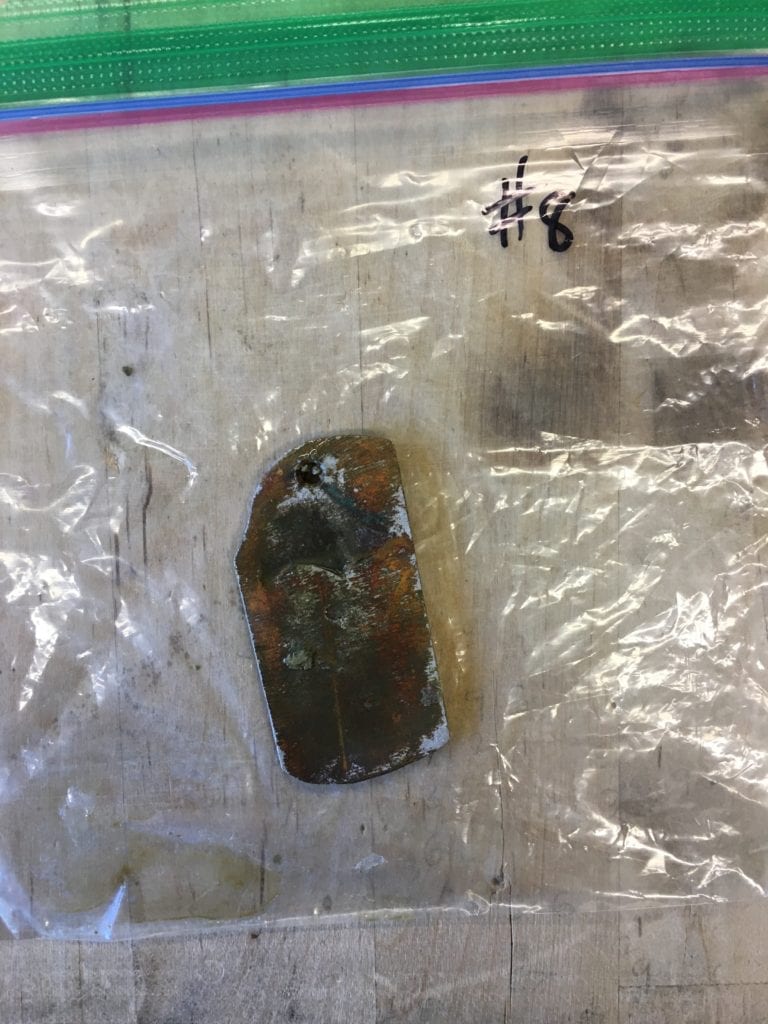
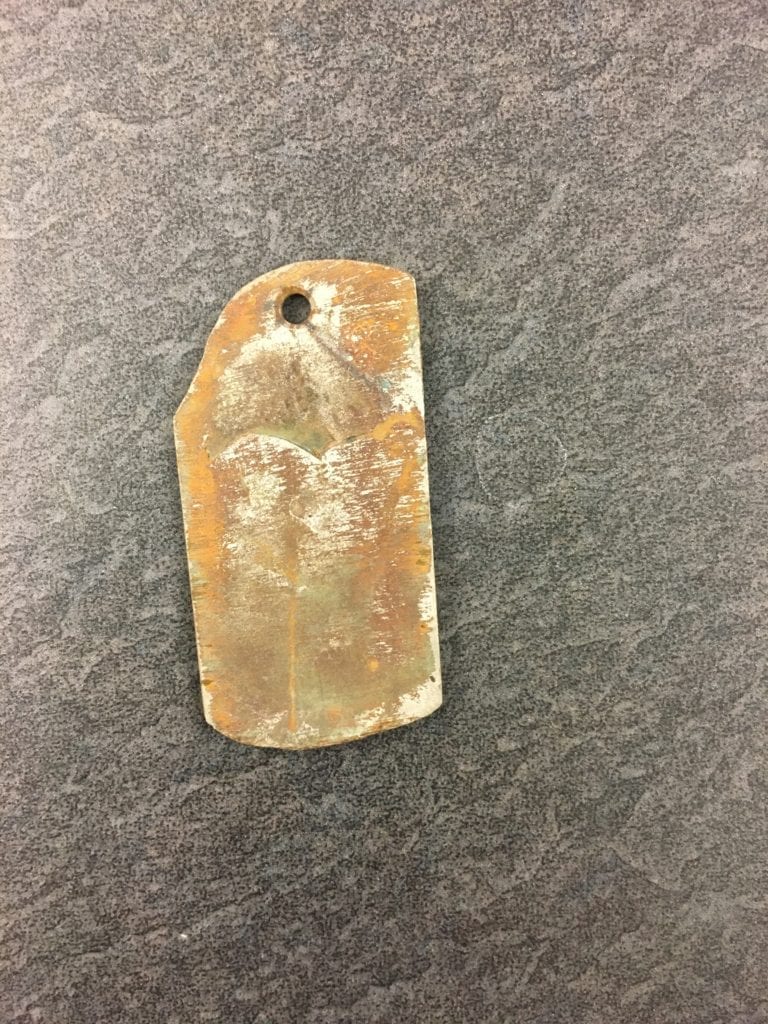