Our Team
We are a group of fourth-year industrial engineers who have been inspired to tackle the next generation of environmental challenges.
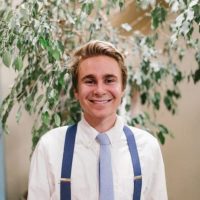
Hudson Brooks
Process Design Expert
Hudson Brooks is a graduating Industrial Engineering major at California Polytechnic State University, San Luis Obispo, with experience in facilities planning, cost estimating, and value engineering. Hudson will be starting as Cost Manager at Cumming Corporation in August of 2021. In this role, he will be estimating construction costs for multi-million dollar projects and implementing value engineering when possible.
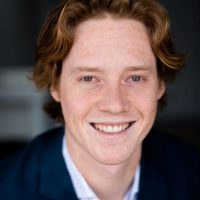
Nolan Brown
Financial Lead
Nolan Brown is an Industrial Engineering student in his fourth year at California Polytechnic State University, San Luis Obispo, and is also in his first quarter as a graduate student in the Engineering Management program. This past summer, he interned at Deloitte Consulting and is planning on returning as an Analyst in their Business Technology Solutions practice in San Francisco, California upon graduation.
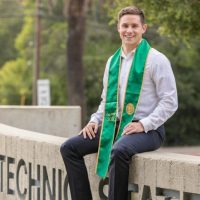
Ian Goulding
Project Manager
Ian Goulding is a fourth year Industrial Engineering student at Cal Poly, San Luis Obispo with a passion for utilizing systems thinking, analytics, and creative technologies to tackle complex problems. Previously, he has interned on a business software R&D team at Arrow Electronics in Denver, Colorado. Upon graduating, Mr. Goulding will be joining Deloitte Consulting as a Strategy Analyst in San Francisco, California.
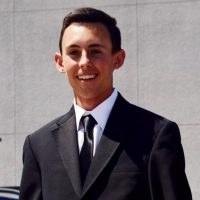
Jack Dwyer
Logistics Specialist
Jack Dwyer is an Industrial Engineering major with a minor in Statistics at California Polytechnic State University, San Luis Obispo. During his time at Cal Poly, Jack worked extensively with the Mustang baseball team, highlighted by his role as Co-Director of Analytics during the 2021 season. Upon graduation, he will begin a role as a Demand Planner with Callaway Golf in Carlsbad, California.
Acknowledgements
A special thanks to our sponsor and advisor Dr. Lizabeth Thompson for her guidance throughout this project.
Our Project's Video
Our Project's Digital Poster
Problem
Reusable economies are a necessary value-stream for the future in order to reduce the amount of greenhouse gasses and energy consumption in the process of creating and recycling materials. To do so, communities need to be able to assess their resources and utilize a framework to implement reuse-based economies and businesses.
Instead of glass ending up in landfills or being recycled in a costly way, the glass product lifecycle in the city of San Luis Obispo needs to be changed so that the reuse of glass containers is a part of the glass lifecycle and economy.
Objective
To create a profitable, glass bottle reuse startup that transitions local breweries away from one-way glass beer bottles to reusable ones. The startup will provide both the glassware and the services needed to distribute, collect, clean, and redistribute bottles up to 25 times each.
Current State
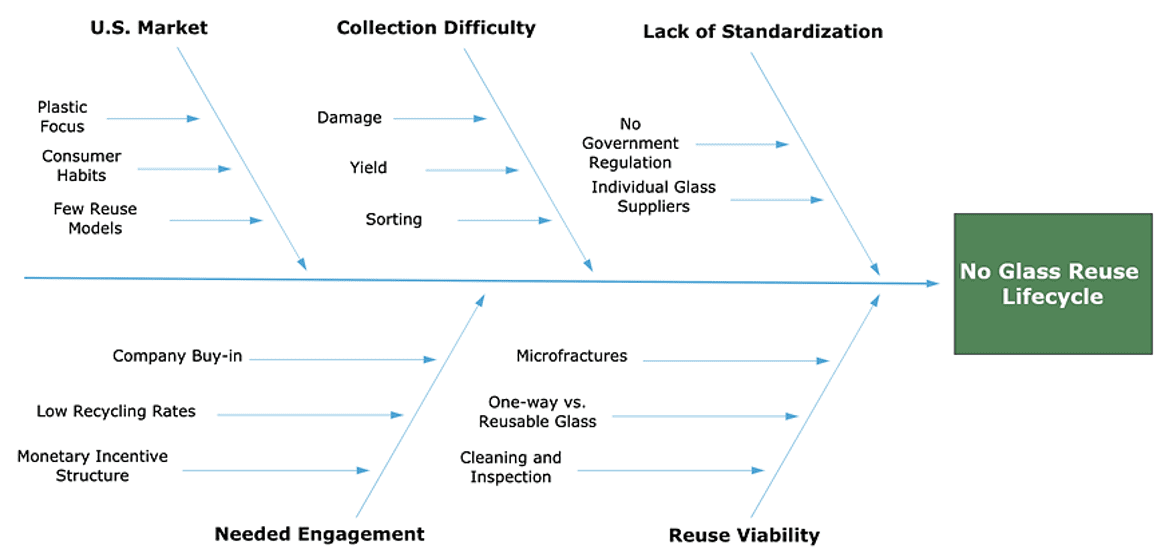
US Market: The U.S. container market, driven by companies and consumers, has been, and continues, to move away from glass and towards plastic and aluminum for packing. The lack of reuse models, along with plastic and aluminum being cheaper and easier to recycle, have led to this shift.
Needed Engagement: Current U.S. engagement in recycling programs is low, with only 30% of glass being recycled. To combat this, company and consumer buy-in, along with a monetary incentive structure for engaging in the reuse cycle, must be a large part of the solution.
Collection Difficulty: Glass breaks more easily than other containers which makes it difficult to collect in good condition. It takes damage when being used, thrown into bins, and sorted. Any collection model for reuse must address these difficulties and ensure that the bottles are collected with minimal damage.
Lack of Standardization: In successful glass reuse models, government regulation with standardized, reusable bottles has played a large part in this success. There is currently no such system in the U.S. outside of Oregon.
Reuse Viability: Most glass containers in the U.S. are not reusable, as they are designed and manufactured in a way to only be used once and are too brittle for the cleaning and inspection process.
Success Criteria
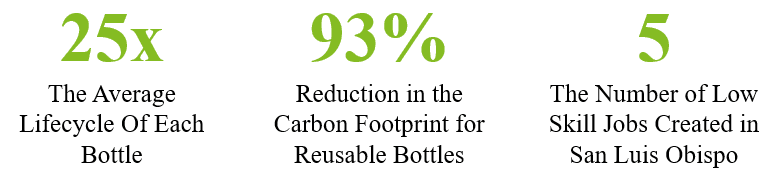
Evaluation of Market
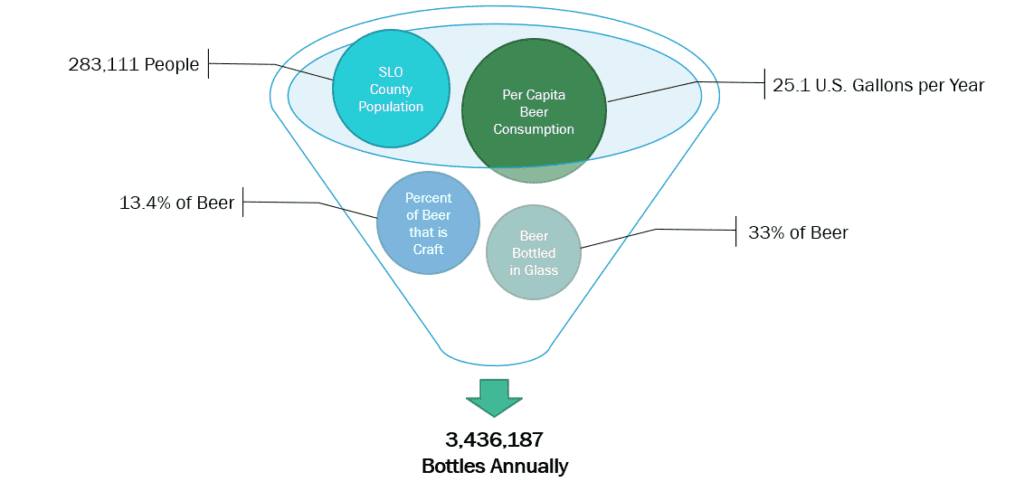
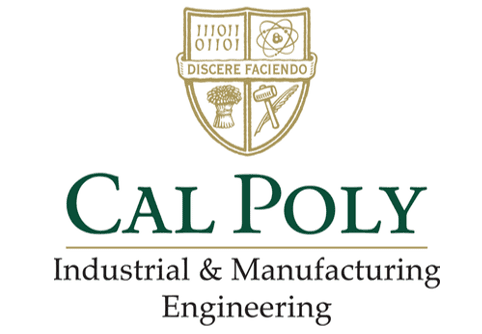
This project is sponsored by Dr. Lizabeth Thompson
Reusable Bottle Processing
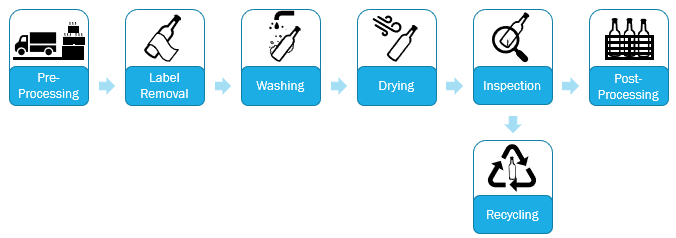
- The processes designed can be summarized through six steps:
- 1. The bottles will be collected from drop-off zones, transported to our facility, and unloaded from the truck in pre-processing.
- 2. The labels of the incoming bottles will then need to be removed fully with no glue residue left.
- 3. The bottles will then go through a washing step, which will thoroughly clean the bottles, inside and out. The washing step also includes sterilizing the bottles at a certain temperature, killing potential existing bacteria.
- 4. Next, the bottles are dried.
- 5. They will be run through a high-tech inspection machine in order to be sure the bottle can be used again. The inspection machine will be looking for microfractures or any sort of damage to the bottle that cannot be seen just from the human eye.
- 6. Good bottles are packed up and shipped back out to the breweries for bottling.
- 7. Rejected bottles are sent to be recycled.
Solution Designs
1ST ITERATION - lOW tECH
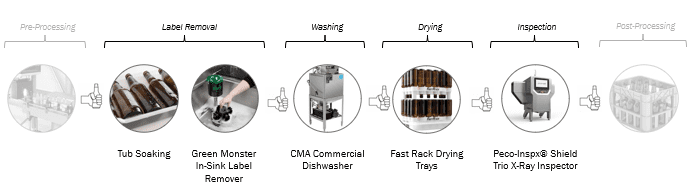
The first iteration was designed as a highly manual process that kept upfront investment costs low. When evaluated using a simulation model, the process was far too manual and slow to be scaled with the business.
2ND iTERATION - mEDIUM TECH
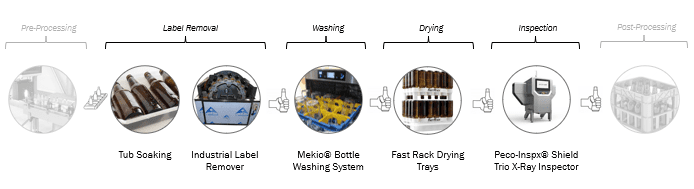
The second design iteration upgraded our label removal and washing machinery to increase throughput. After an economic analysis, it was discovered that as the number of bottles being processed increased, operational costs skyrocketed, blocking a path to profitability.
Final iteration - high tech
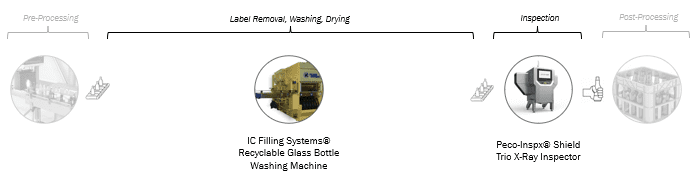
The third, and selected solution design, replaced the label removal, washing, and drying steps with an automated machine. Although the most costly, this design provided scalability and efficiency as the business grows.
Impact Analysis
Profit
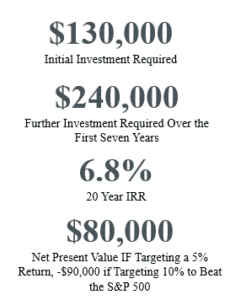
Planet
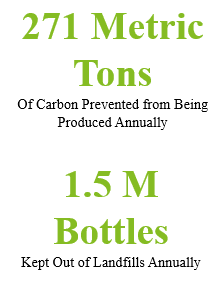
People
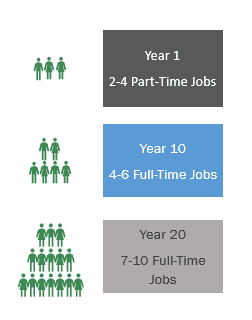
Collection
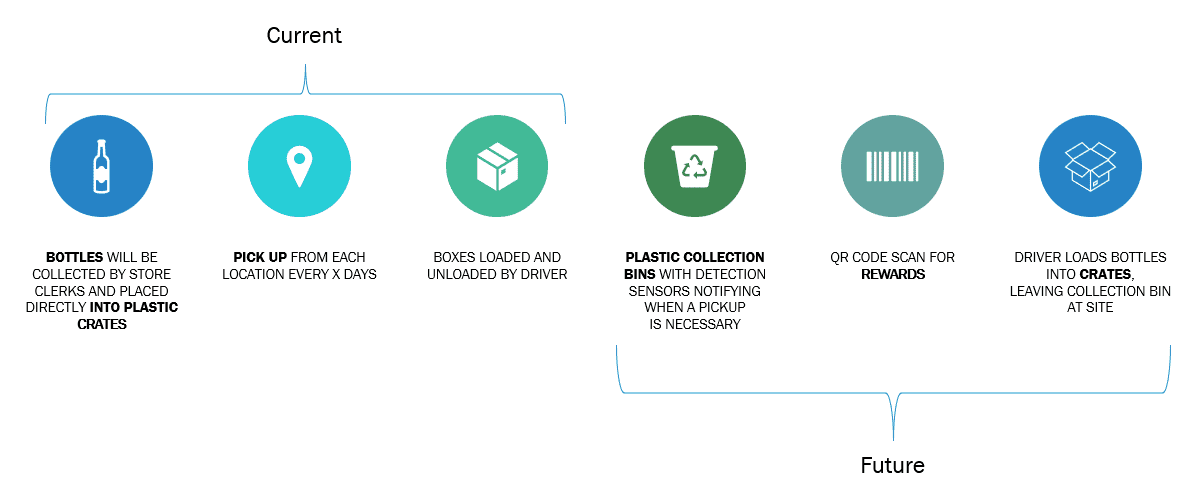
Brewery Partnerships
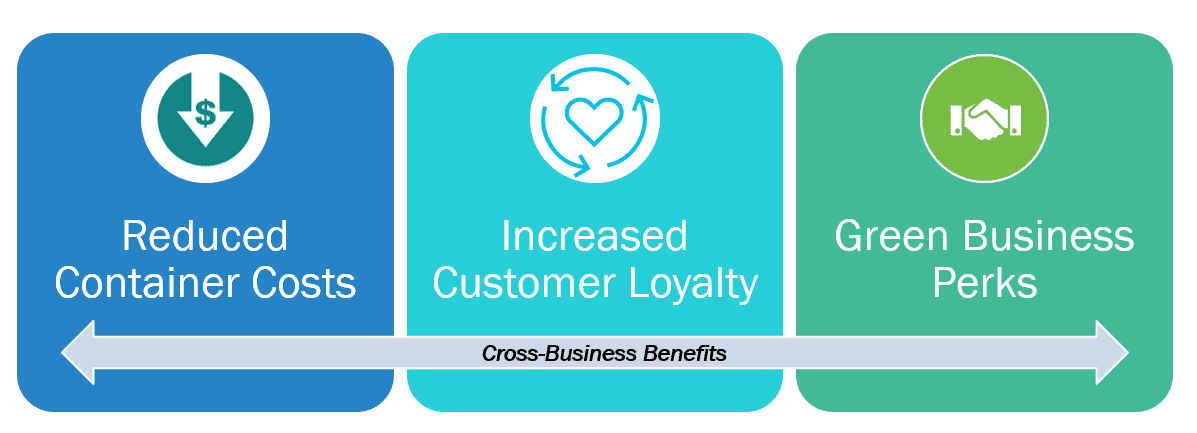
Our bottles are priced two cents less than the average one-way bottle, a 10% unit saving for breweries.
Customers bring bottles back to the brewery storefront.
Green PR, Tax Incentives, and increased brand respect drive business and reduce costs