Our Team
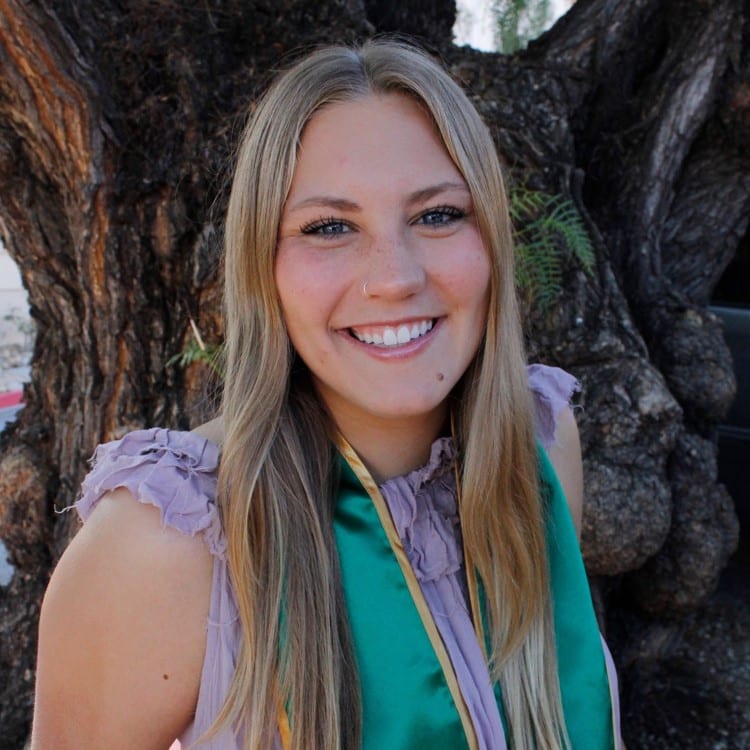
Kelsi Cappetto
technical engineer
I am a fourth year Biomedical Engineering student concentrating in mechanical design. I am interested in working with orthopedic medical devices and have experience working on a project designing a prosthetic arm, as well as exposure to quality through a summer internship. I am from Seattle, WA and I enjoy playing volleyball, skiing, and relaxing at the beach with friends.
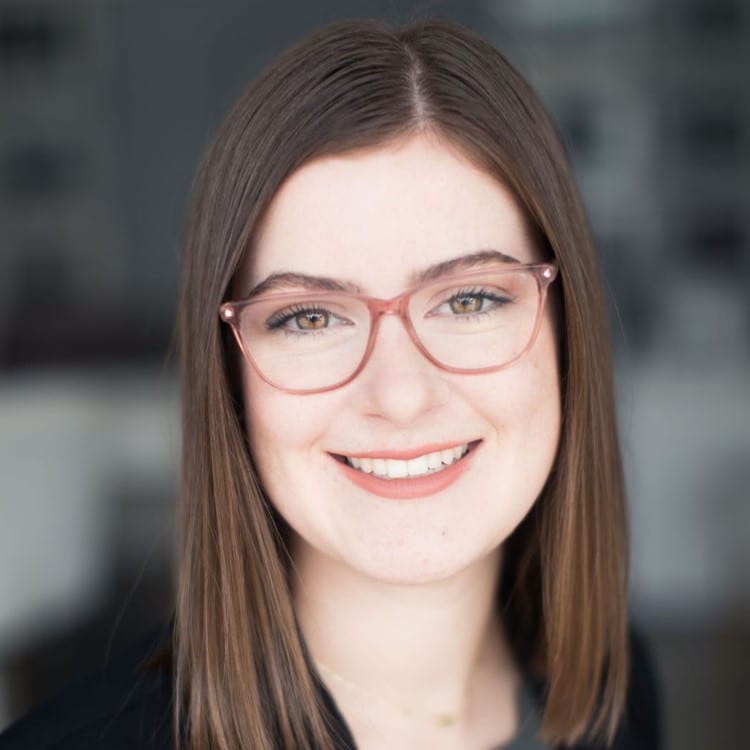
Bethany Hall
project manager
I am a fourth-year Biomedical Engineering student, concentrating in mechanical design. I am originally from Portland, Oregon and have experience working in research and development on implantable heart devices. In my free time, I enjoy running and going to the beach.
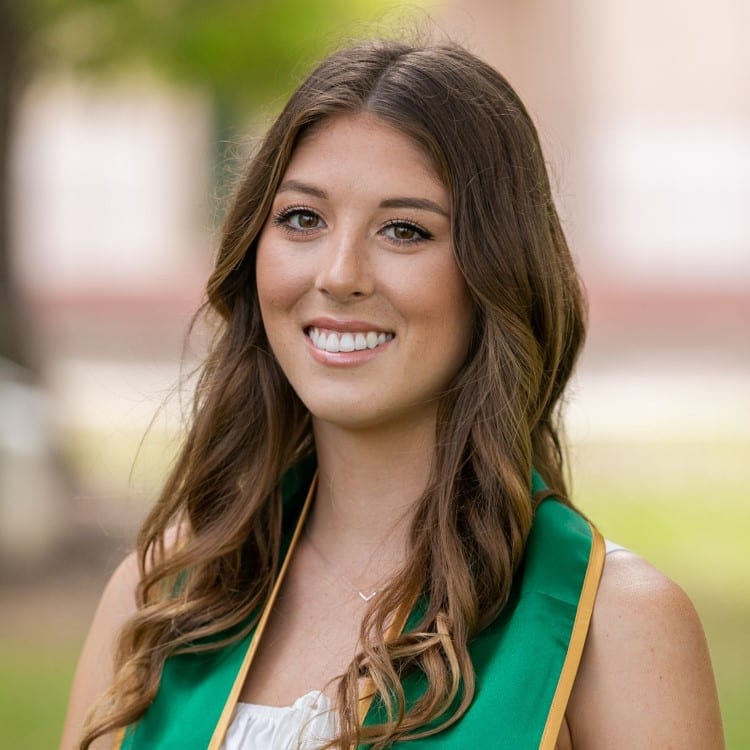
Jessica Chow
CAD engineer
I am a fourth-year Biomedical Engineering student, concentrating in mechanical design from Chino Hills, California. I am interested in working in immunotherapy for cancer treatment. I have experience working in product development and research and test engineering roles. Some of my hobbies include surfing, yoga, traveling, and spending time with friends.
Acknowledgements
We would like to thank our senior project advisor and project co-sponsor, Dr. Britta Berg-Johansen, and our other project co-sponsor, Dr. Long Wang. We appreciate all of the guidance and advice that contributed to the success of the Smart Spine Tape project.
We would like to acknowledge our Hannah Forbes funding and recognize how it enabled us to make otherwise unattainable developments to our senior project.
Our Project's Digital Poster
Problem Statement
Low back pain costs Americans $50 billion dollars annually in health insurance, and another $50 billion in lost wages and impairment of productivity [1]. The purpose of this project is to develop a flexible, wearable device that attaches to lower back to allow for continuous, in-field, real-time monitoring of spinal kinetics and/or kinematics to help understand the specific movements that contribute to lower back pain.
Design Constraints
- 10° minimum rotation detection in the frontal plane
- 10° minimum flexion detection
- 5° minimum extension detection
- Minimum sensor lifetime of 4 days
- Minimum 125% stretchability
- Minimum 90° flexibility
- Maximum 3″ tape width
- Maximum 12″ tape length
- Maximum 0.15″ tape thickness
- 2 minute accurate application time
Design Concept
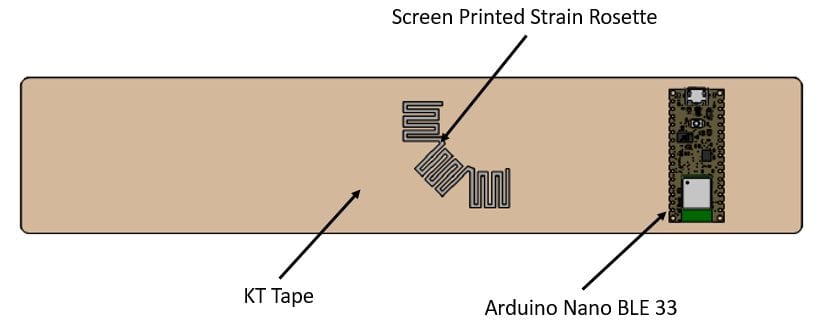
Piezoresistive screen printed ink was chosen for the following reasons:
- Piezoresistive ink eliminates need for multiple iterations of ink development
- Shorter manufacturing time
- Strain sensing properties
- Acceptable sensitivity properties
Arduino Nano BLE 33 was chosen for the following reasons:
- Built-in bluetooth module will allow for the efficient transfer of data from the Arduino to an app or PC
- Small in weight and size
- Can be sewn into fabric
- Built-in accelerometer can allow for sudden high velocity forward bending movements to be recorded
- Designed to remain adhesive during physical activity and long durations of time
- Easy to apply and remove
- Stretchable and moves with the wearer
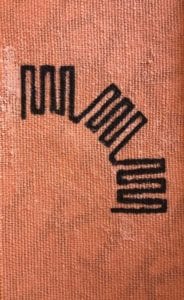
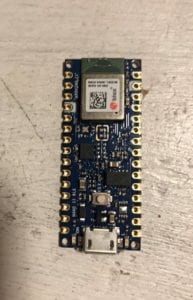
Preliminary Prototype
Our preliminary functional prototype was constructed using flex sensors and an Arduino Uno to gain familiarity and develop the Arduino data acquisition system.
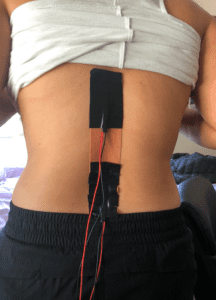
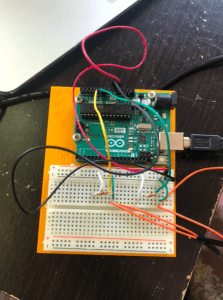
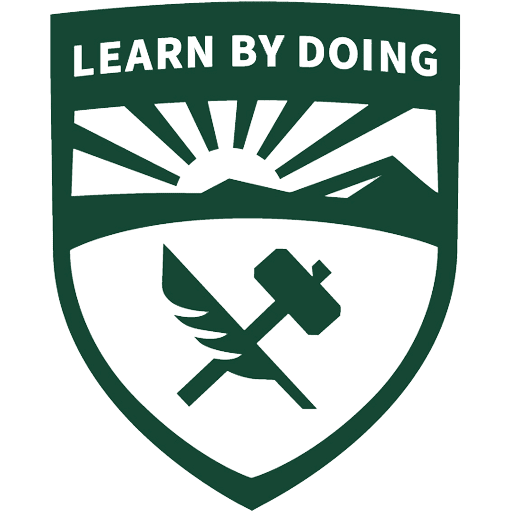
California Polytechnic State University, San Luis Obispo
This project is sponsored by Dr. Britta Berg-Johansen and Dr. Long Wang with the Cal Poly, San Luis Obispo College of Engineering.
Piezoresistive Sensor Manufacturing Process
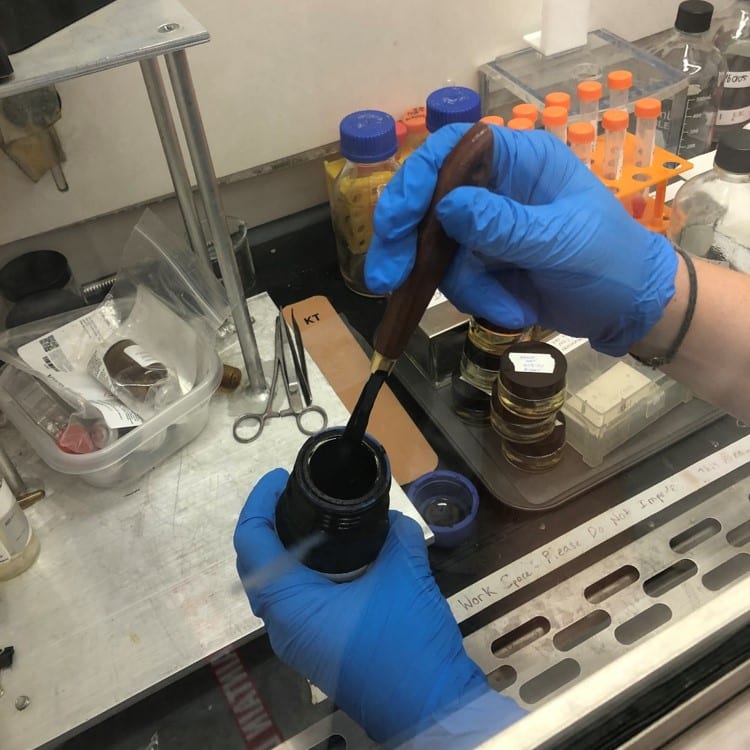
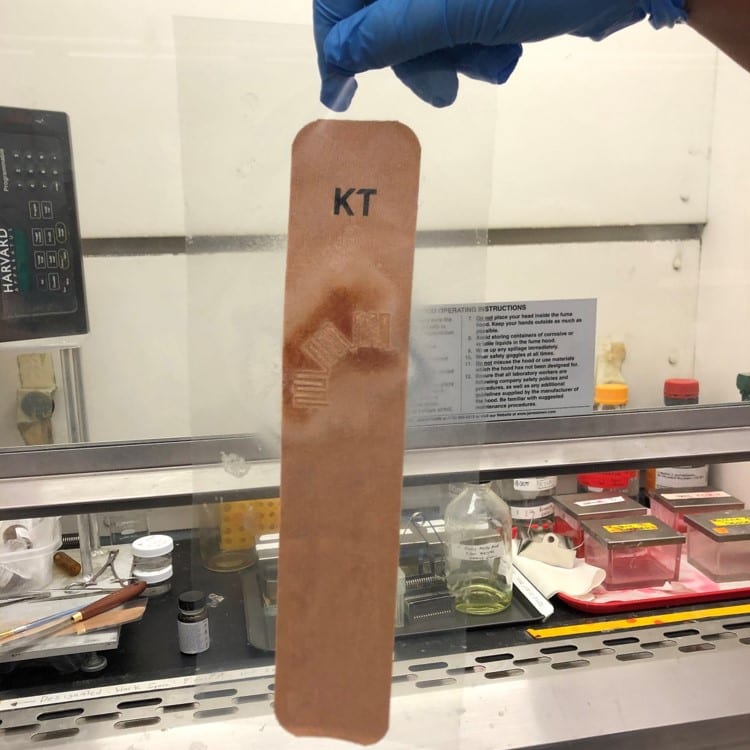
Our manufacturing process of the sensors began with mixing the piezoresistive ink with a stir stick and adhering the strain rosette mask to the KT Tape.
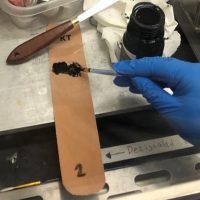
The ink was then screen-printed or painted on to the KT Tape over the mask in a fume hood.
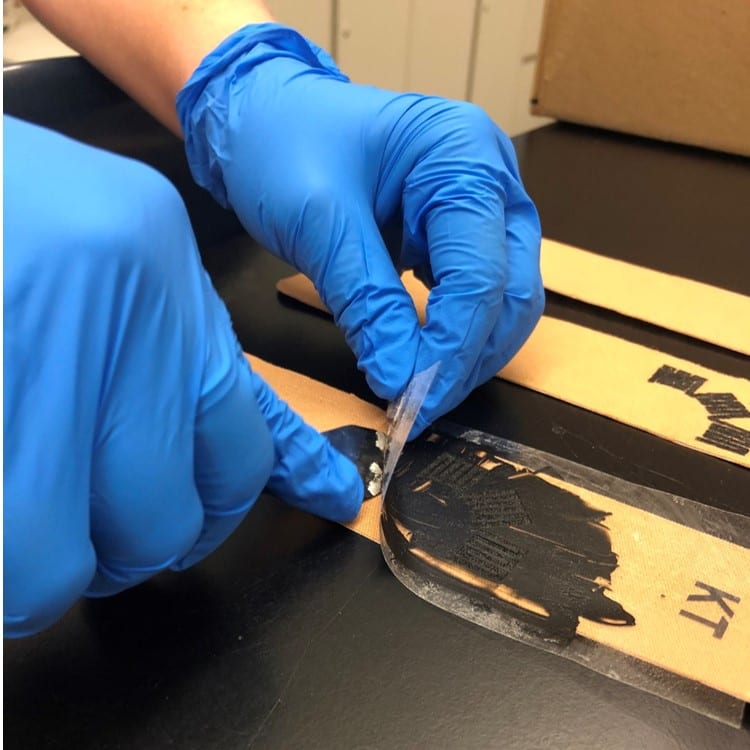
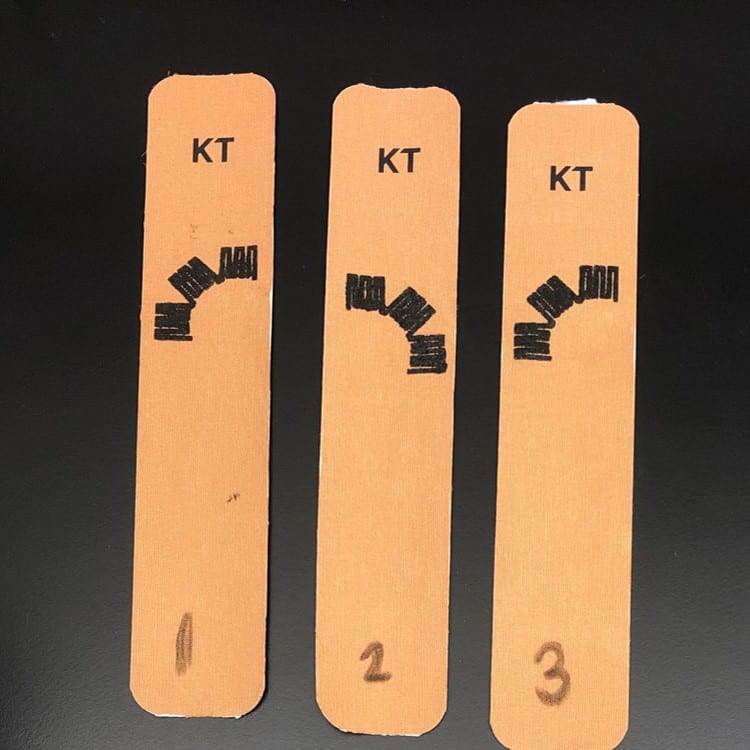
The sensors were left to dry for 1 hour before removing the mask. The masks are then thermally cured for 20 minutes at 60°C.
Design of Experiments
The following demonstrates the different iterations of the Smart Spine Tape that were manufactured to determine the best and most effective sensing capabilities:
- Wide sensors, light spray adhesive, painted on
- Wide sensors, heavy spray adhesive, painted on
- Wide sensors, glue stick, painted on
- Thin sensors, light spray adhesive, painted on
- Thin sensors, heavy spray adhesive, painted on
- Thin sensors, glue stick, painted on
- Thin sensors, light spray adhesive, screen-print
- Thin sensors, heavy spray adhesive, screen-print
- Thin sensors, glue stick, screen-print
KT Tape Mechanical Analysis
A finite element analysis (FEA) was performed to verify the mechanical integrity and stretchability of the KT Tape. The tape was simulated to stretch 125% of it’s original length to simulate max stretching it will undergo. The tape was modeled as an elastic material since KT Tape behaves as such until 30% elongation where it begins to behave as a viscoelastic material. Below are the determined properties of KT Tape:
- Modulus of Elasticity: 688.9 psi
- Poisson’s Ratio: 0.42
- Thickness: 0.022″
- Length: 10″
- Width: 2″
- Ultimate Tensile Strength: 910.0 psi
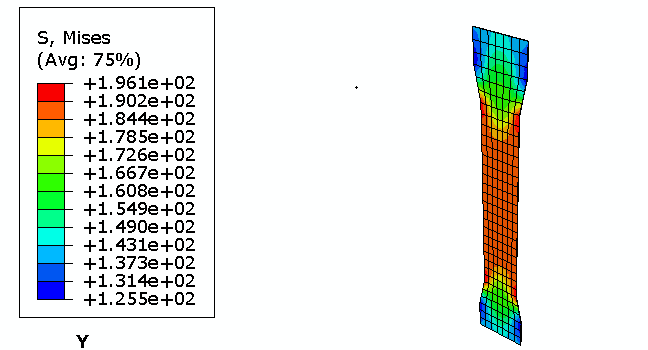
Based on this finite element analysis model, an estimated force of 8.47 lbf is required to elongate the KT Tape to 125% beyond the original length. Therefore, the calculated stress on the tape for 125% elongation is 185.4 psi indicating that the KT Tape will not fail mechanically.
Final Prototype
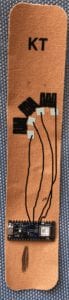
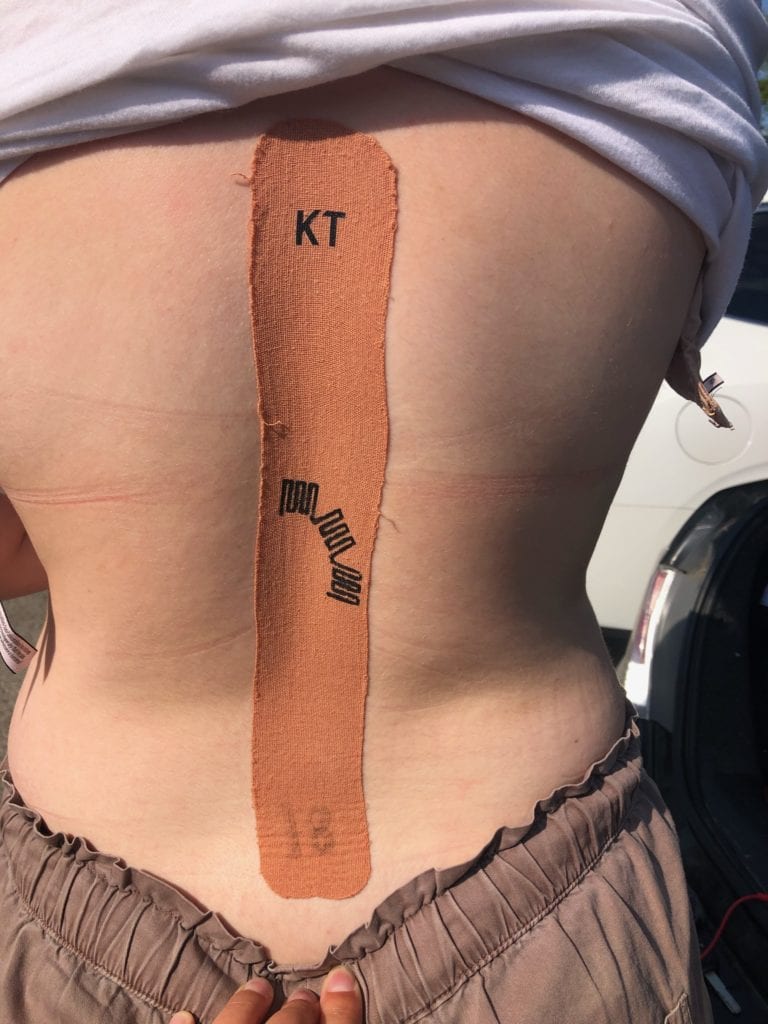
Bill of Materials
- Piezoresistive P2 ink for strain rosette
- KT Tape
- Arduino Nano BLE
- 20 gauge silicone covered wire
- Electrical tape
- Stripboard
- AA battery
- 3x AA battery mini USB-b connection
- Conductive thread
Design Verification
Test FIxtures
Two test fixtures were designed to enable testing the Smart Spine Tape in flexion and rotation as shown below:
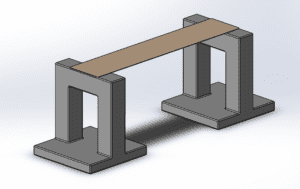
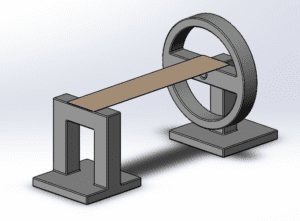
Tests performed
Three-Point Bending Test: This test ensures that the sensors function properly when subject to spinal bending movement. The tape will be subject to 3.5″ of deflection.
Minimum Flexion and Extension Detection Test: This test ensures a minimum of 5° bending detection. Subject the tape to 0.035″ deflection.
Minimum Rotation Detection Test: This test ensures a minimum of 10° rotational detection. Rotate tape to 5°, 10°, 20°, 30°, and 40°.
Adhesive Lifetime Test: This test ensures that adhesive lasts for over 14 hours. Have individuals wear the tape for 14 hours and perform physical exercise.
Accurate Application Time Test: This test ensures that the device can be consistently applied in under 2 minutes. Have multiple individual apply the device while being timed.
Size Measurements: This test ensures that the size of the assembled device is equal to or smaller than 12″ x 3″ x 0.15″.
Future Recommendations
Future recommendations and improvements of the Smart Spine Tape:
- Utilize the Bluetooth module to allow for real-time spinal movement tracking
- Develop a method of rapidly alerting wearer of when a dangerous movement was made
- Enable data acquisition system and piezoresistive strain rosette to be resuable to minimize cost of Smart Spine Tape unit