Our Team
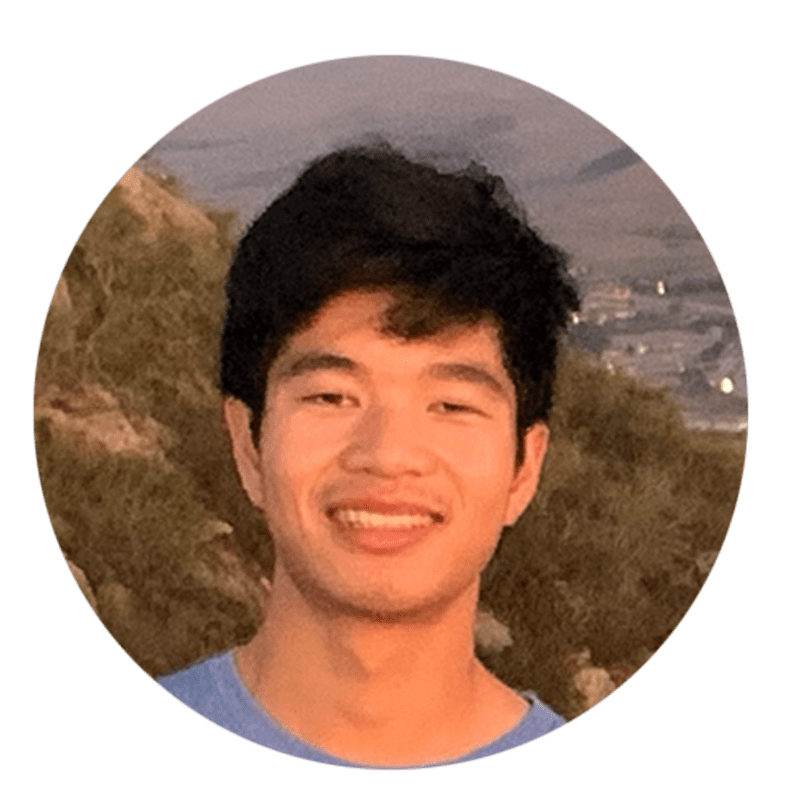
Alex Pham
I am going into my fifth year of Biomedical Engineering. I am studying to eventually go to dental school and work as a general dentist, potentially opening my own practice. One day I would hope to apply my engineering skills in this field to update the instruments that dentists use. I grew up in the northern San Diego area. In my free time, I enjoy mountain biking, rock climbing, and working on cars.
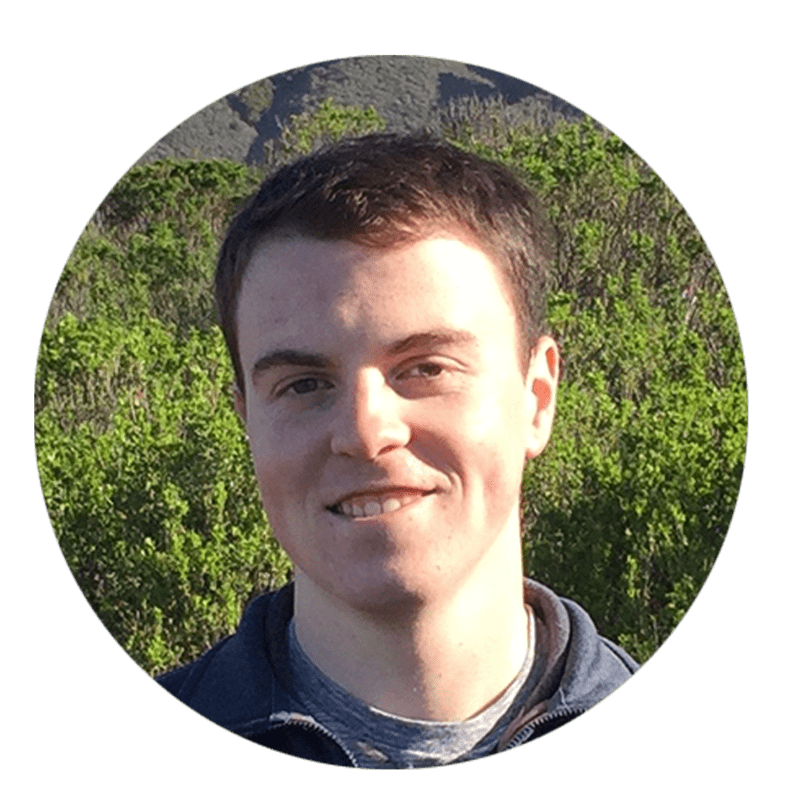
Nick Dion
As I finish up my final year at Cal Poly, I plan to gain industry experience in the field of Biomedical Engineering and attend medical school in the near future. Aside from class, I love all the outdoor activities that the Central Coast has to offer including hiking, rock climbing, and skiing at Tahoe. Cal Poly has been an amazing experience and I am appreciative of the skills I have acquired and the people I have met.
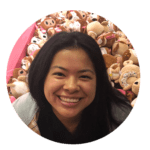
Cristina Andrade
I am a fourth-year Biomedical Engineering student concentrating in Mechanical Design. I absolutely love animals and was able to take a number of Animal Science courses throughout my time at Cal Poly. I hope to combine my love of animals and the Biomedical field to create innovative ways of improving their quality of life. In my free time, I like to work on arts and crafts projects, read books, and explore new areas of SLO with my friends.
Acknowledgements
We would like to thank our project sponsor Dr. Dimitri Delagrammaticas and our advisor Dr. Britta Berg-Johanson for all their help and dedication. This project would not have been possible without them.
We would also like to thank the Machine Shop technicians, that helped us weld and mill a number of parts for our wagon.
We would like to acknowledge the Biomedical Engineering Department and all of the Hannah Forbes Grant sponsors for funding our project.
Our Project's Videos
Please enjoy this video of our Stair Wagon in action.
Our Project's Digital Poster
Introduction
Our team was tasked with creating a wagon that can safely transport cargo across flat ground and up and down stairs. The stakeholders that aided in development of this device include our sponsor, Dr. Dimitri Delagrammaticas, and California Polytechnic State University, San Luis Obispo. The goals of this project were to make a functioning prototype that can transition from flat to ascending stairs and descending stairs without comprising the ergonomic benefits of a conventional wagon on flat ground.
Background
According to the American Journal of Emergency Medicine, 1.1 million Americans are treated in the ER annually as a result of stair related injuries. Of these injuries, 68% occur in people between the ages of 11 and 60 years old. Additionally, the number of injuries is increasing year after year. These statistics exemplify the risk of causing damage to the musculoskeletal system when transporting heavy loads up and down stairs.
Specifications
- – Carry 30 lbs with a max volume of 15 gallons.
- – Compact down to almost half its height.
- – Require no more than 15 lbs of force to go up stairs and no more than 10 lbs of force to go down stairs.
- – Have a turning radius of 4 ft
- – Allow for little to no extra strain on the body while carrying heavy loads up or down a staircase.
Indications for Use
- – For people +13 w/ full motor control
- – Traverse up and down stairs with variety of geometries
- – Multi-terrain capable
- – Remain effective on wet surfaces
- – Make tight turns in stair wells
- – Portable, able to fit in car trunk or closet
- – Able to handle daily use and abuse
- – Not designed for safe transport of children or other live cargo or as an assistive mobility devices
Computer Model
CAD models of each individual component were developed and assembled using SolidWorks to confirm that geometry did not overlap and that the design could function properly. Furthermore, these models facilitated new iterations and were also used to direct fabrication. This was especially important for the stability elbows, tri-star wheel hubs, and gears.
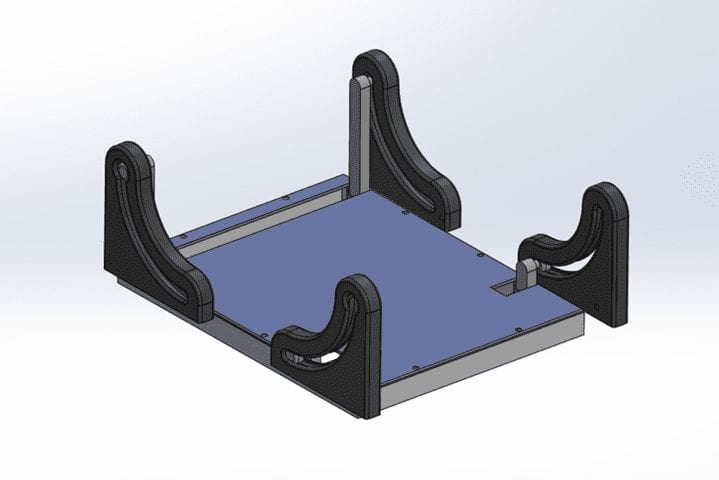
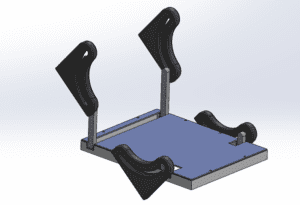
The wagon basket is supported on a platform that swings inside an outer frame via wheels that roll within four structures dubbed “stability elbows.”
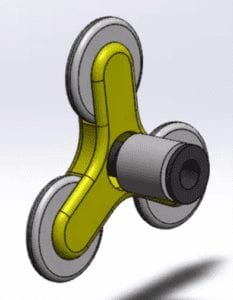
Similar to other stair-climbing devices, the wagon has a tri-star wheel design that allows it to traverse across various staircases.
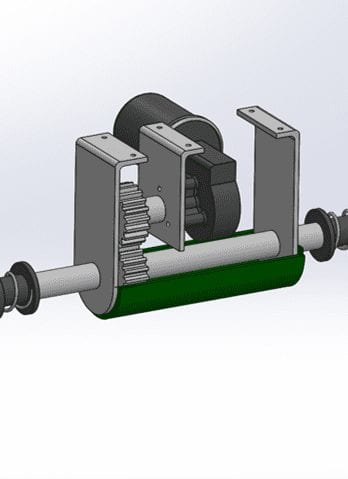
To aid in its stair-climbing ability and act as a partial brake, a motor was implemented. The motor and its accompanying gears are housed in a container called the “Clam Shell.”
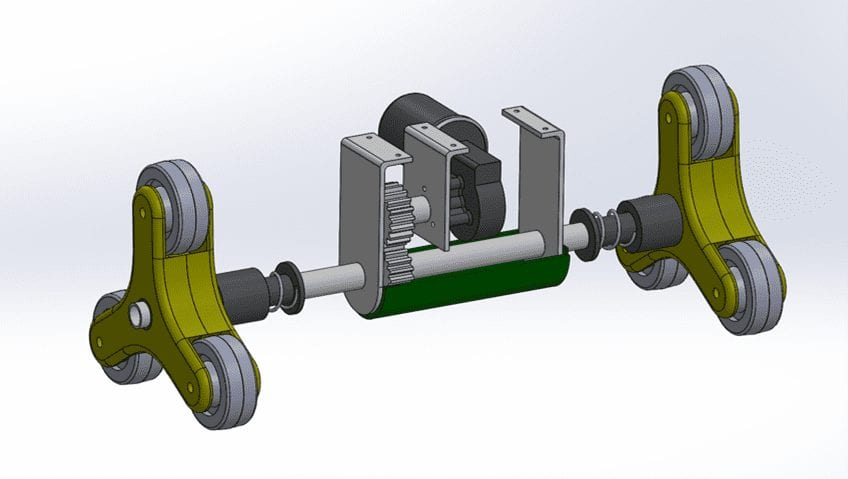
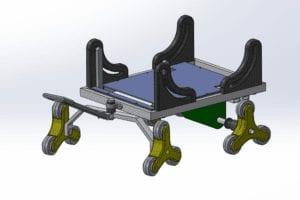
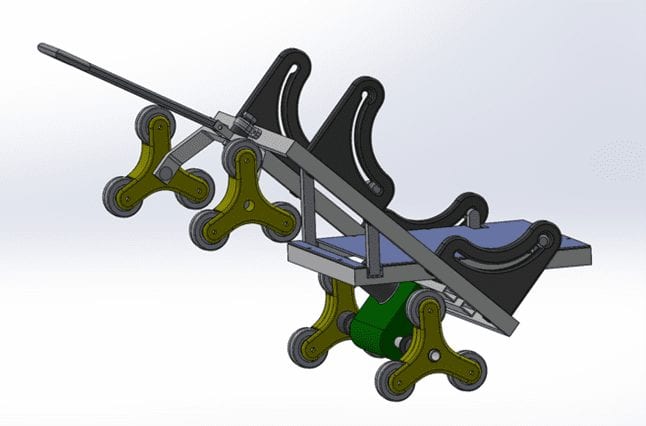
To better visualize places for improvement and evaluate the feasibility of our design, our SolidWorks models were a one to one scale of our actual prototype. This made it easy to find and order stock parts.
Materials
Outsourced Parts
Worm Gear Motor, Lithium-Ion Battery, Handle, Foldable Basket, Nucleo Board, Toggle Switch, and Luggage Wheels
Raw Material
Aluminum square tubing and round and rectangular bars, Polyethylene Terephthalate Glycol (PETG) filament, Nylon filament, Polylactic Acid (PLA) filament, High-Density Polyethene (HDPE) sheet, Bungee Cord, and Hardware
Testing Material
Pulley, Rope Engineering Scale, and Chalk
Wagon Components
There are multiple components that make the stair climbing wagon unique compared to a conventional wagon.
Stability
To hold the cargo stable while the wagon rolls over stairs there are four slotted elbows that keep the inner frame level while the outer frame pitches up the staircase. The slotted elbows are custom printed from PETG plastic which was chosen for strength and durability.
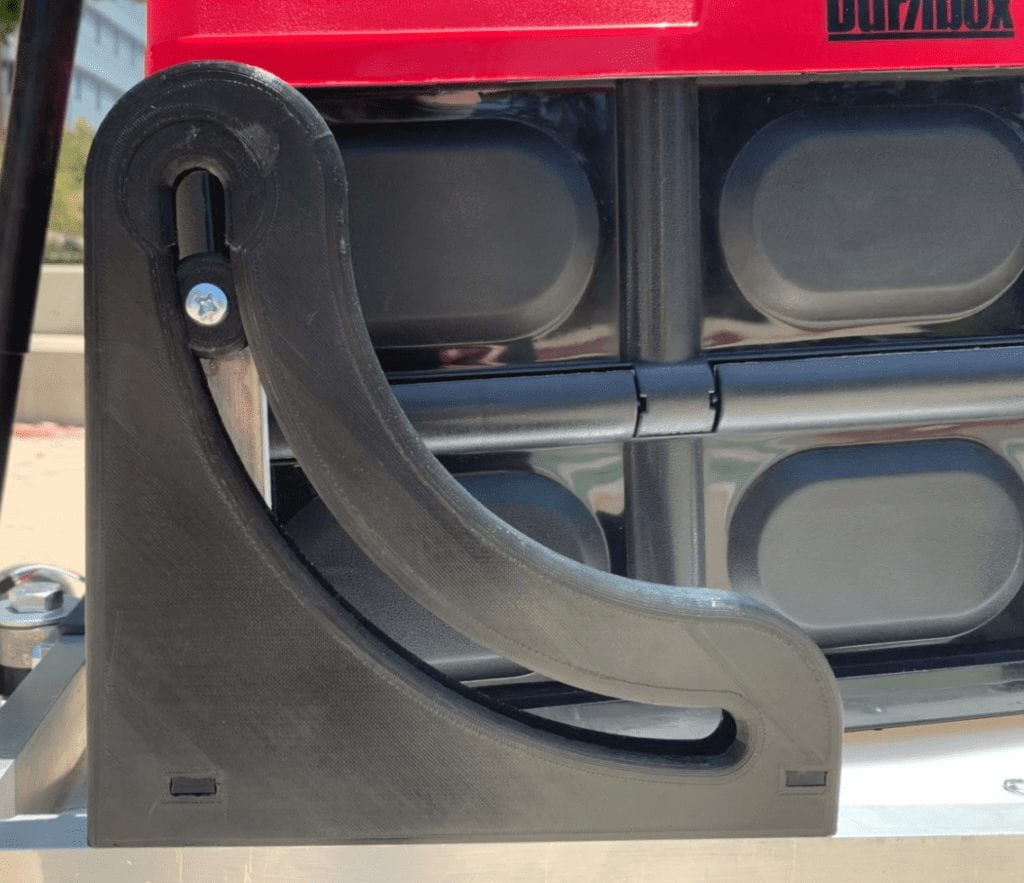
Collapsibility
Each elbow is mounted to the frame via two bungee cords. When storing the wagon, the elbows can be lifted over the pegs and folded down to decrease the total size by half.
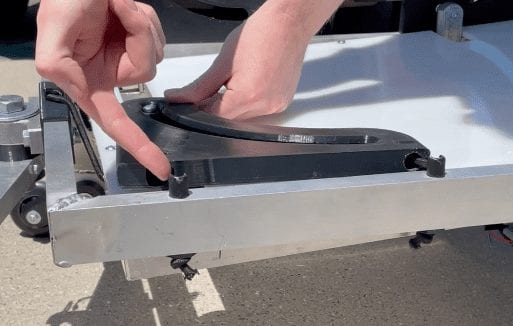
Assistive Lifting
The wagon is also fitted with a 6 Nm electric motor to assist in transporting heavier loads up the stairs. This motor is mounted to the rear axle and can be activated by a switch embedded in the handle. The switch has two modes for up and down stairs. A Nucleo serves as the controller and is powered by 16800mAh battery that can provide 2 hours of continuous use.

Tri-Star Wheel Design
A Tri-star wheel design was used to provide a smooth transition over each step and decrease strain on the user. These wheels are compatible with a step size up to 5.5” and are suitable for pavement, dirt, and grass.
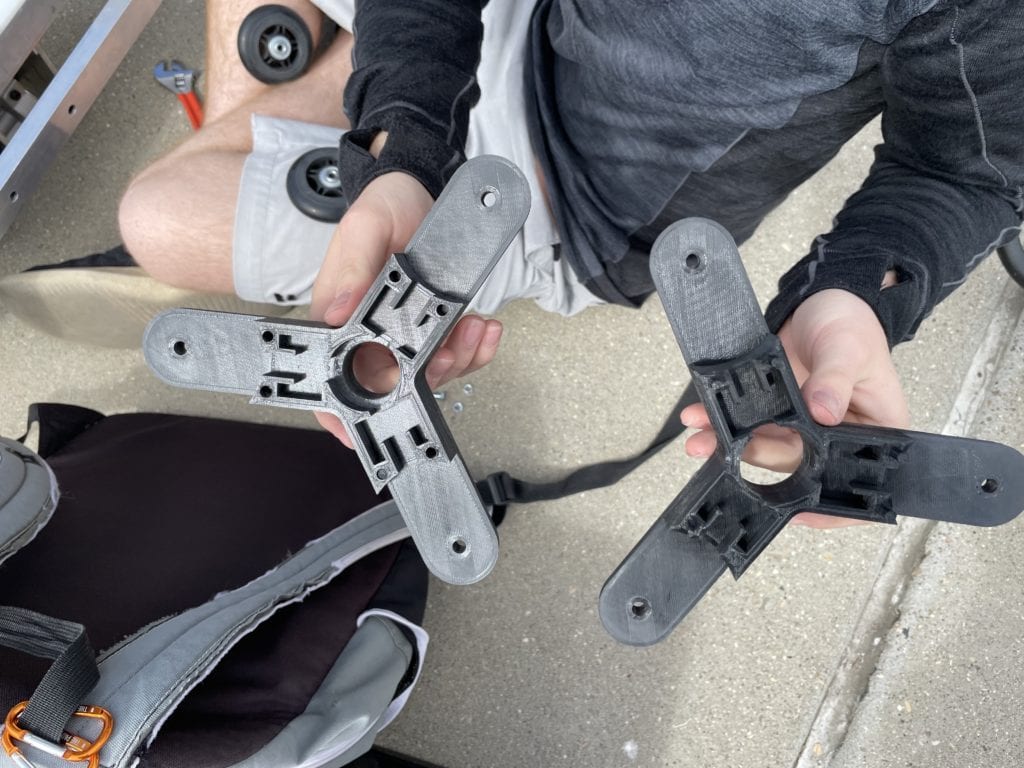
Finally, the entire frame is made from 6063 aluminum to provide strength and durability. All printed components were extruded from PETG or Nylon. These materials have great strength and durability characteristics. All wiring has been insulated and is mounted internally where possible.
Testing
In order to test the functionality and ease of use of the Stair Wagon, a variety of Functional and User tests were performed. Each test had a set number of trials, a protocol, target values, and tolerances that would deem a success or a failure. The staircase chosen for some of the Functional Tests was the staircase outside Engineering East. The users in the User Testing were our BMED Senior Project classmates.
Functional Testing
Weight, Volume, Dimension, Force Climbing, Radius, Ergonomics, All Terrain, Dirt, and Longevity Test
User Testing
Timed Fold/Unfold, Timed Install/Uninstall, and Timed Climbing Test
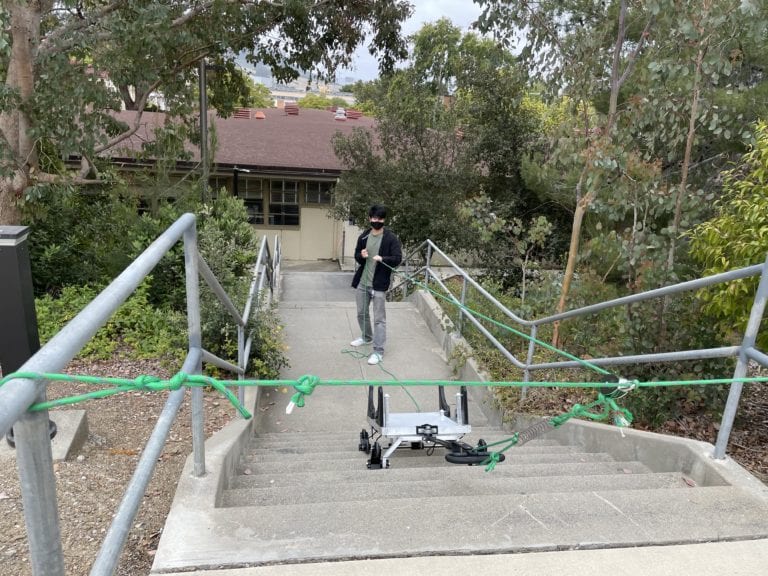
For the Pulley Assembly, used in the Force Climbing Test, rope was tied around the two railings of the staircase, a pulley was placed in the middle and the Stair Wagon was attached to the pulley via rope and a spring. A team member would pull on one end of the rope to pull the Stair Wagon. The spring movement was recorded as the Stair Wagon went over each step.
Testing Data
Functional Testing
After collecting data from the Functional Testing and User Testing, the results were analyzed.
Since the full length of the spring was not used in the Force Climbing Test, the equation in Figure # was used to calculate the new spring constant. The displacement in the spring and the New Spring Constant equation were used to calculate the force in the spring.
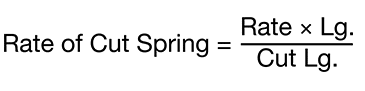
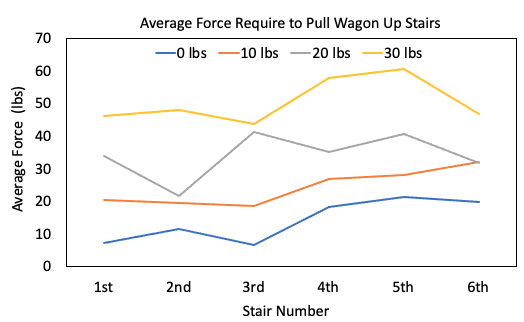
The angles the spine makes with the vertical axis when someone is carrying a heavy load with and without the Stair Wagon were compared.
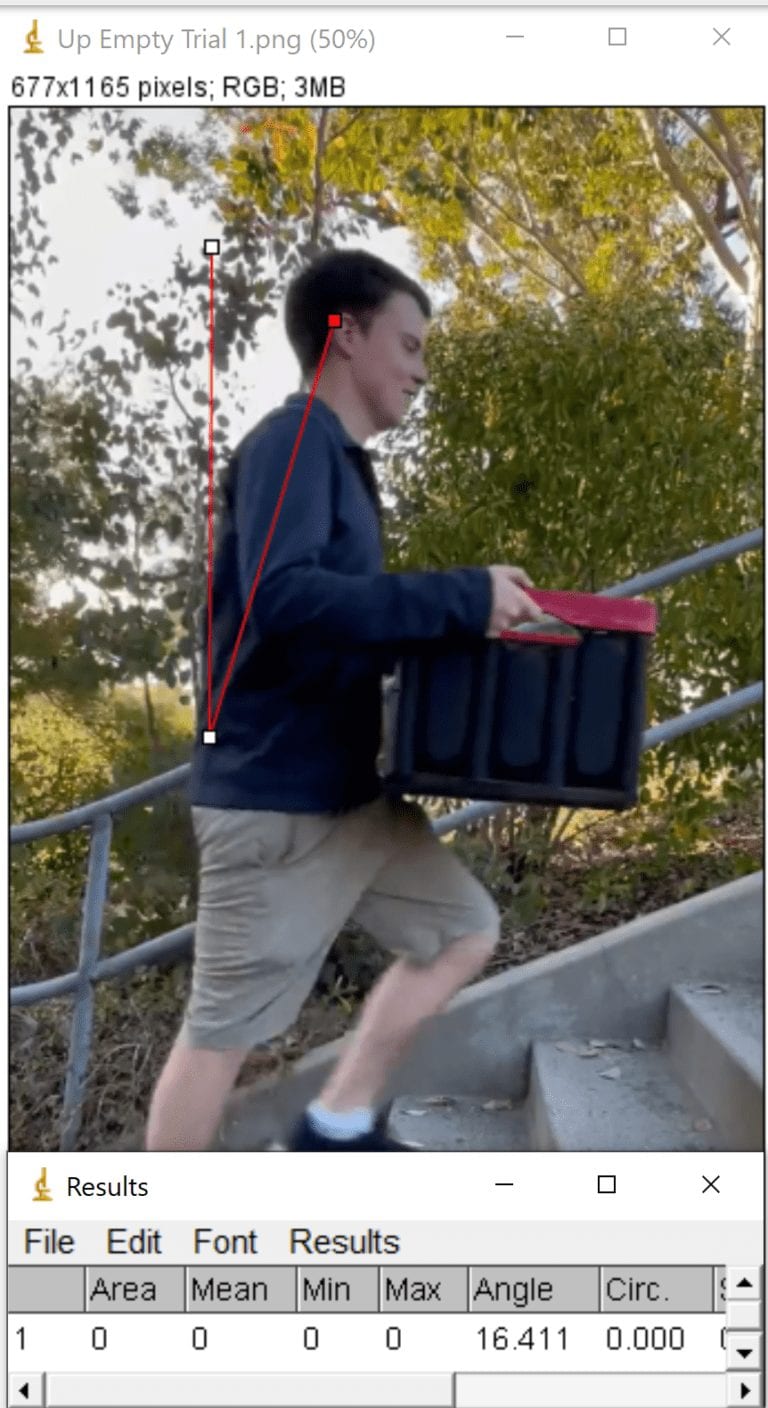
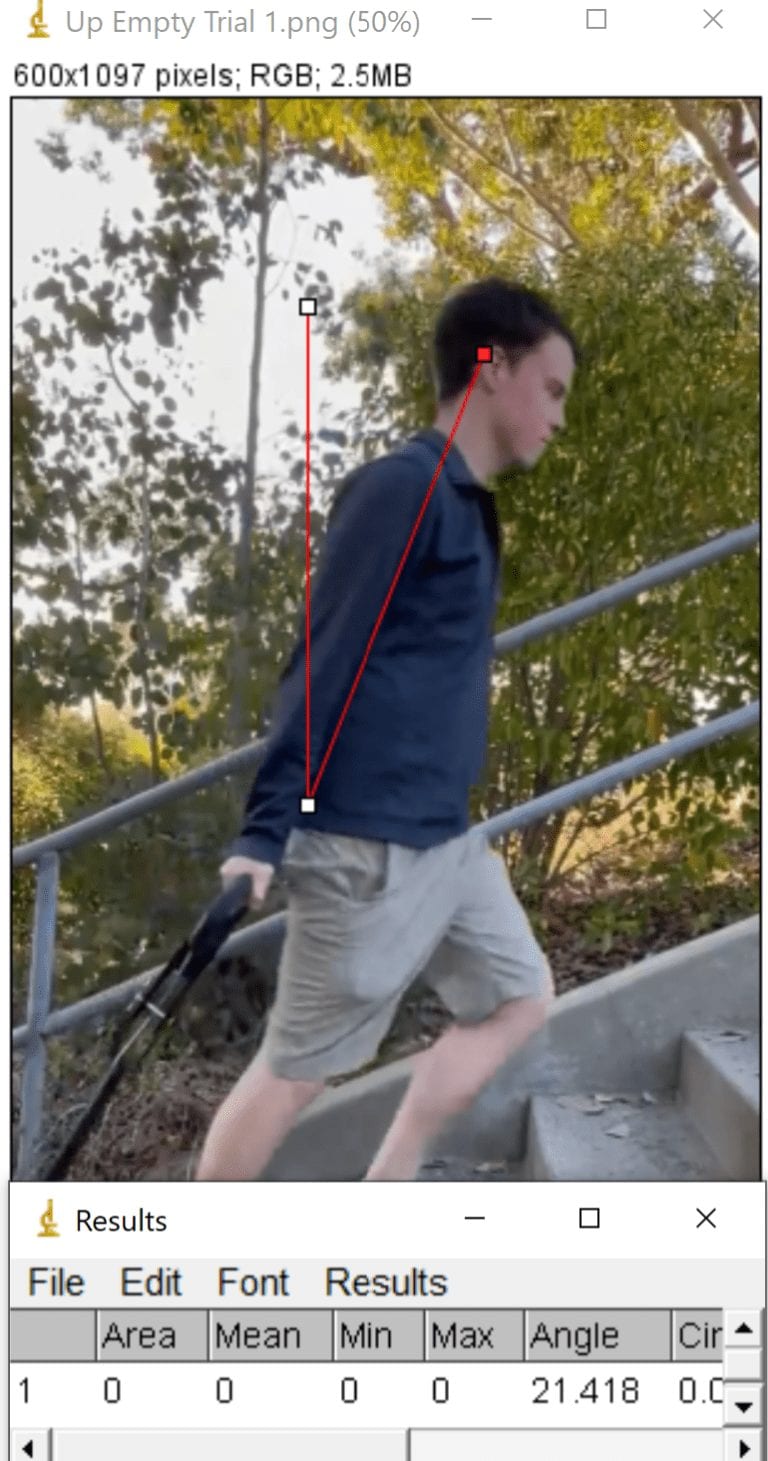
User Testing
Each user was asked to fill out a survey at the end of User Testing. The survey included three rating scale questions that evaluated the Stair Wagon from 1 (very bad) to 5 (very good) and one free-response question for comments and suggestions.
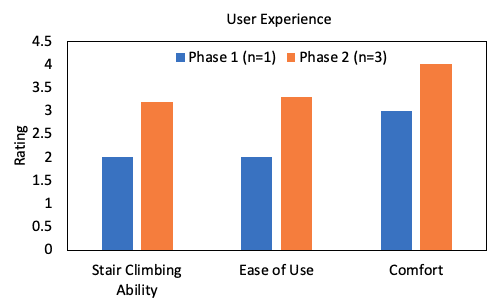
User Ratings
Users rated the Stair Wagon’s stair-climbing ability, how much effort they felt they needed to put in to make the Stair Wagon climb up and down stairs, less effort is better, and how comfortable they felt while using the wagon.
User Comments
- Phase 1
- Too heavy.
- Make tri-star wheel hub larger.
- Phase 2
- Handle mount is difficult to use.
- Driving the Stair Wagon is not intuitive.
- Stair Wagon tends to buck objects off the platform.
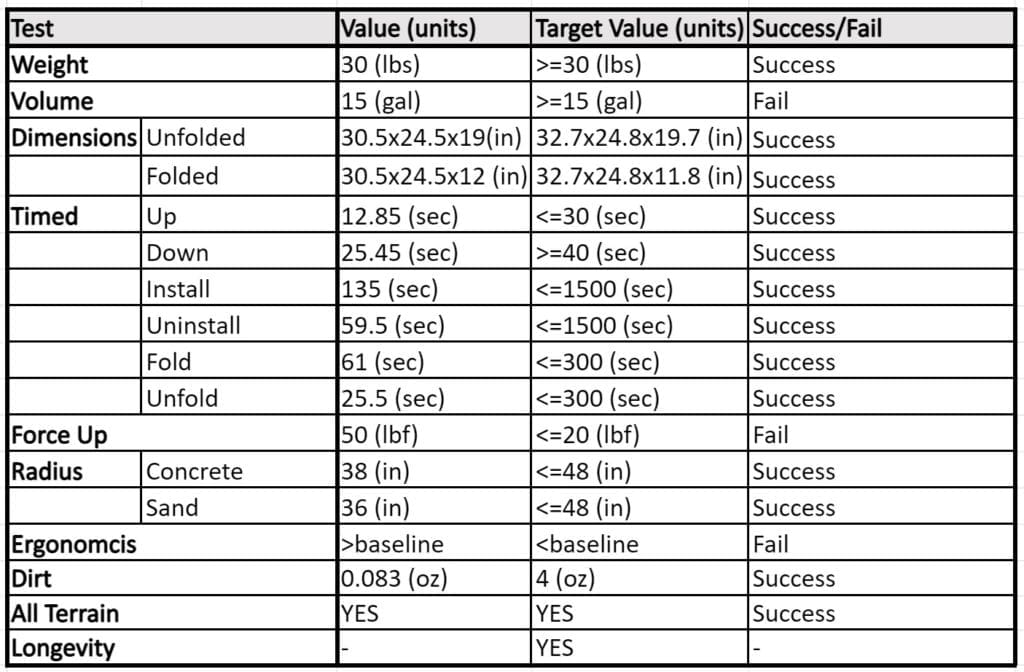
Future Modifications
Making wagon frame out of thinner stainless steal tubing to decrease weight and optimize ease of welding.
Make tri-star wheel hubs longer to accommodate more step heights.
Use wheels with larger widths so the wagon can traverse sand.
Final Prototype
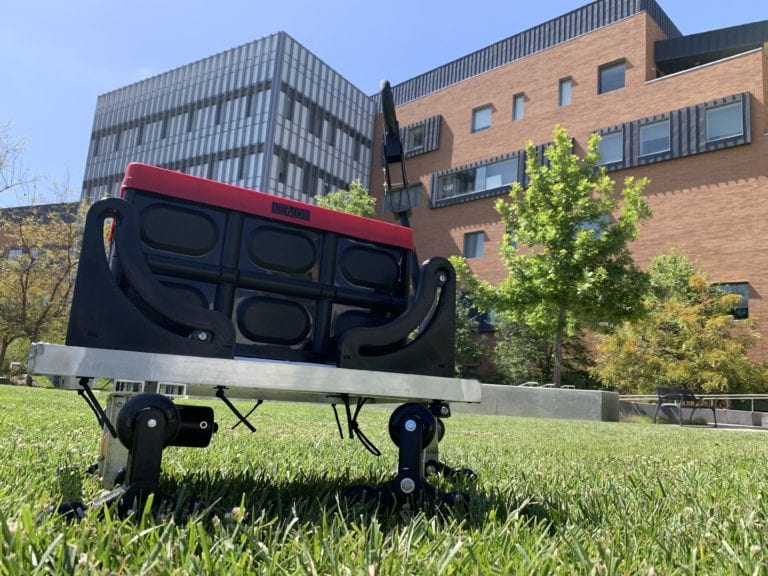
The Stair Wagon met the specifications of the Weight, Volume, Dimensions, Ergonomics, and All Terrain Test.
After our user testing, we decided it would be to the operator’s benefit to implement our drivetrain system in the final product. The test participants also all struggled with threading the nut and bolt to mount the handle to the front subframe, so we plan on attaching the handle with a cotter pin instead of a nut.
Our Project Slides
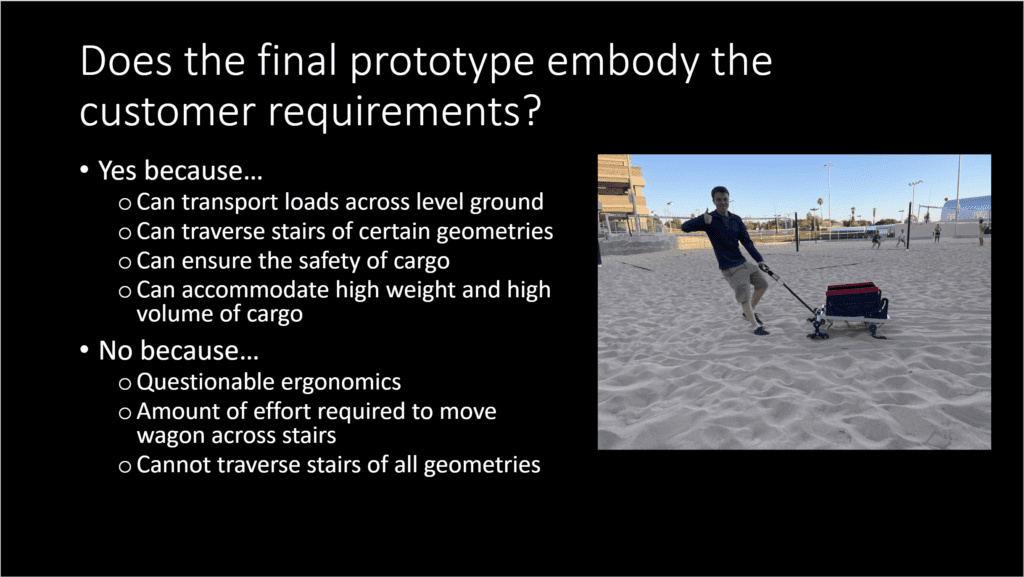