the WIND squad
Fourth-year mechanical engineering students at Cal Poly SLO: the Wind Squad brings together their unique lenses and interests to collaborate on the design of a wind turbine prototype.
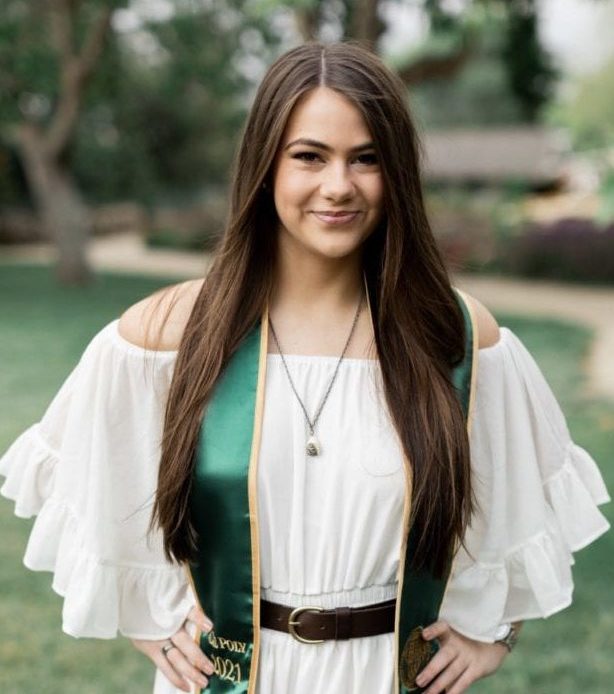
Sophie Spencer
CPWP EXPERT
Sophie is a fierce team lead for the Cal Poly Wind Power Club and amazes all with her diligent hard work and attention to detail. She is a fourth-year mechanical engineering student with a minor in sustainable environments graduating in June 2021. In the fall, Sophie will be attending graduate school in Switzerland to explore renewable energy.
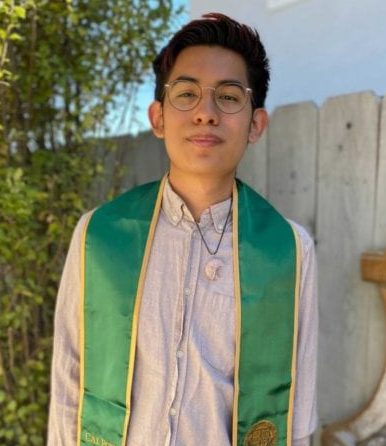
Michael Reyna
Flow sim wizard
Michael is a fourth-year mechanical engineering student with a science, technology, and society minor pursuing a master’s in mechanical engineering at Cal Poly in the fall. With a hot chocolate in hand and a candle lit in the background, there is no task that Michael cannot tackle, including and especially combatting socio-technical dualisms in engineering.
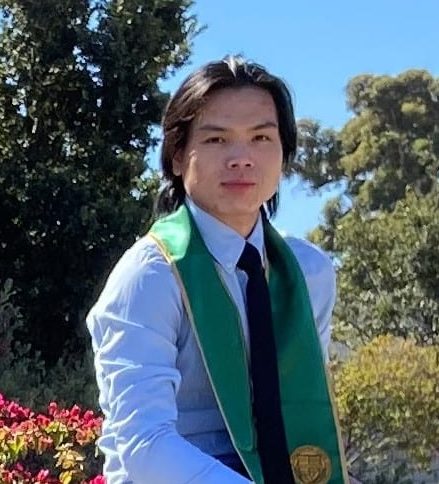
Loi Nguyen
mill maestro
Graduating in June 2021, Loi is a fourth-year mechanical engineering student. He plans to spend the summer traveling, including a trip to Vietnam to visit family. Loi enjoys all kinds of movies, cooking food with friends, and belting karaoke. With a dedication to the engineering design process like Loi’s, the future is sure to hold much in store.
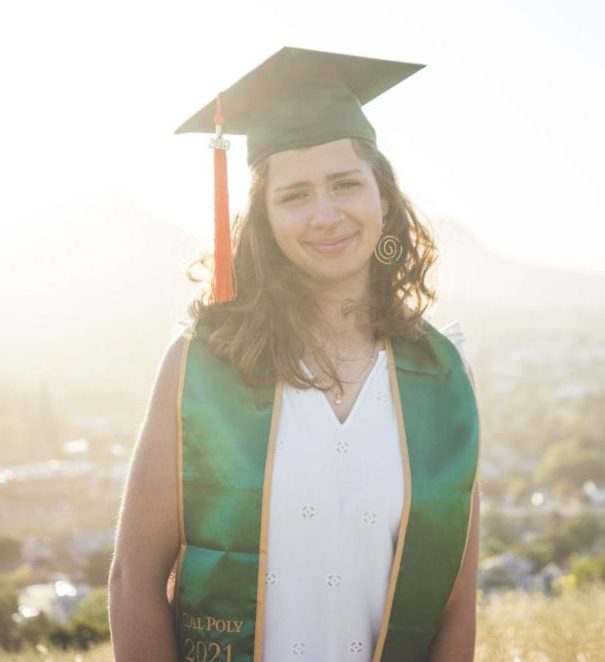
Maggie Nevrly
strain gauge novice
A fourth-year mechanical engineering student graduating in June 2021, Maggie will be working at an HVAC consulting firm in San Francisco. A lover of bicycles and breakfast foods, she is looking forward to lazy Sundays where both can occur with family and friends. Moving forward, she hopes to obtain her PE or return to graduate school.
Acknowledgements
Special thanks Cal Poly Wind Power, for financial and engineering support throughout this process. We’d also like to thank the National Renewable Energy Laboratory and the Department of Energy for giving us the opportunity to participate in this experience. Lastly, thank you to the College of Engineering faculty, administrators, and staff members for administrative and technical support throughout our project process.
Prototype Wind Turbine Videos
Check out our project video where we describe the engineering design process used to develop the prototype of our small scale wind turbine.
Prototype of a Small Scale Wind Turbine
Background
CPWP is competing in the Collegiate Wind Competition, hosted by the National Renewable Energy Laboratory. Multiple teams are working on different components of a prototype turbine; our senior project group is working on a tower, nacelle, yawing mechanism, and passive fin design.
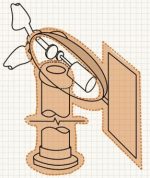
Problem definition
House and protect internal electrical components.
Minimize power losses by orienting the turbine in the direction of the wind, ideally with the yaw moving as fast as possible.
Adhere to competition size and safety requirements outlined by the Collegiate Wind Competition, operating in a variety of simulated weather conditions.
Design for distributed manufacturing due to the difficulty of accessing manufacturing facilities during the COVID-19 pandemic.
Design with quick assembly and access to parts in mind.
Ideation
The tower, nacelle, and yawing mechanism are largely independent of each other. With unique functions, our team underwent several concept design processes in parallel to determine concept designs.
Pugh matrices were used to narrow the proposed mechanisms to the top 3-4 ideas for each system. A weighted decision matrix was used to determine the top two ideas each shown below in Figures 2, 3, and 4.
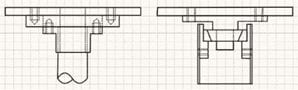
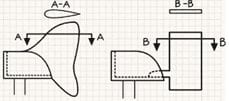
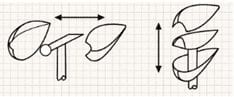
Concept Design
Nacelle subassembly
The nacelle protects the internal components and assists in turning the turbine. The nacelle top and bottom cover are fastened together. Then the top vane slides into the nacelle and secures with a tab on the bottom vane.
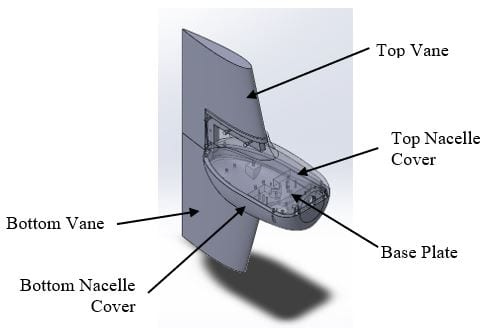
Tower subassembly
The tower secures the turbine to the wind tunnel by holes in the tower base as specified by the CWC. The tower tube is then welded to the tower base and ribs to support the nacelle and the rotation about the vertical axis.
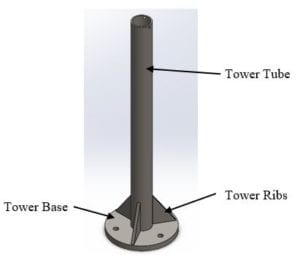
Yaw subassembly
The yaw allows for rotation about the vertical axis with a slew bearing and interfaces between the nacelle and the tower subassemblies.
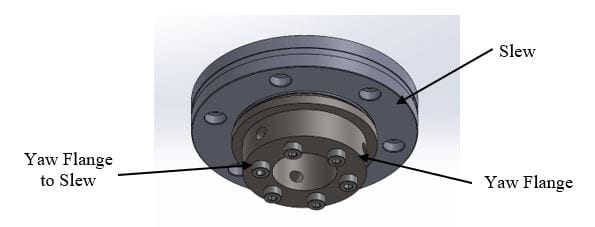
Design Justification
structural analysis
We assumed the tower to be a cantilever structure with a distributed load of 100N and axial load from the weight of nacelle of 40N. The calculations of deflection and stresses were checked through FEA and produced a maximum deflection of 0.098mm, maximum bending stress of 1.75 MPa, and maximum shear stress of 1.26 MPa.
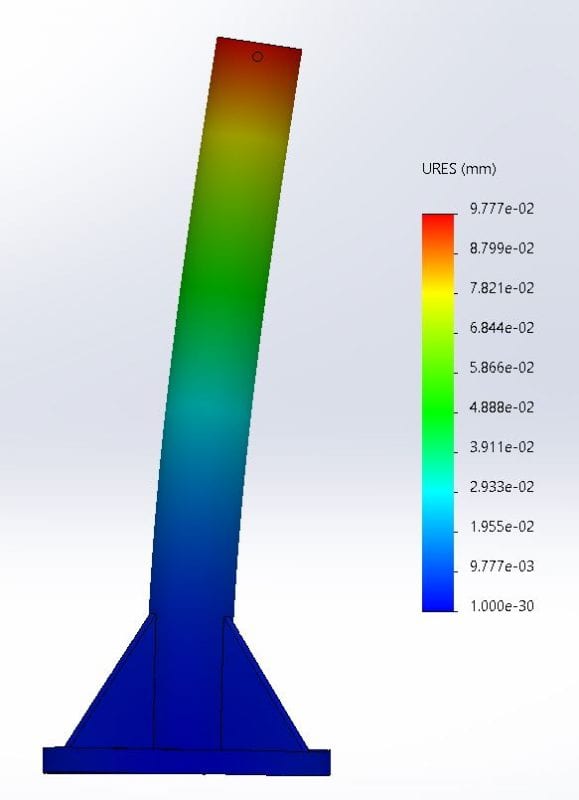
For the base plate of the nacelle, we calculated expected deflection and stress in the plate at the highest expected loads of 14.5 N on the front ledge. We found a maximum deflection of 0.005mm and yielding stresses at the corners with a safety factor of 100.
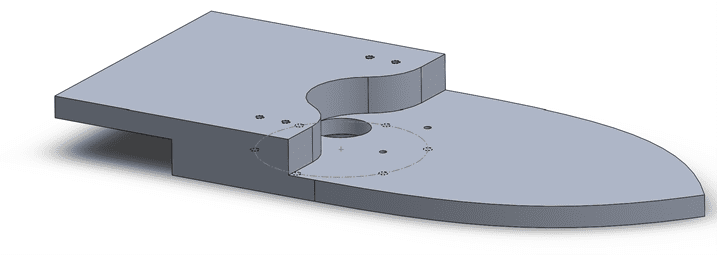
Yaw sizing and test
The slew bearing for the yawing mechanism was selected because it was able to handle axial, radial, and moment loads. It was sized based on the dynamic and static load factor as specified by the manufacturer. Since the loads on the tower are small relative to the loads a slew bearing is capable of handling, we were limited by the size of the center hole to allow for passage of wires.
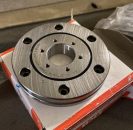
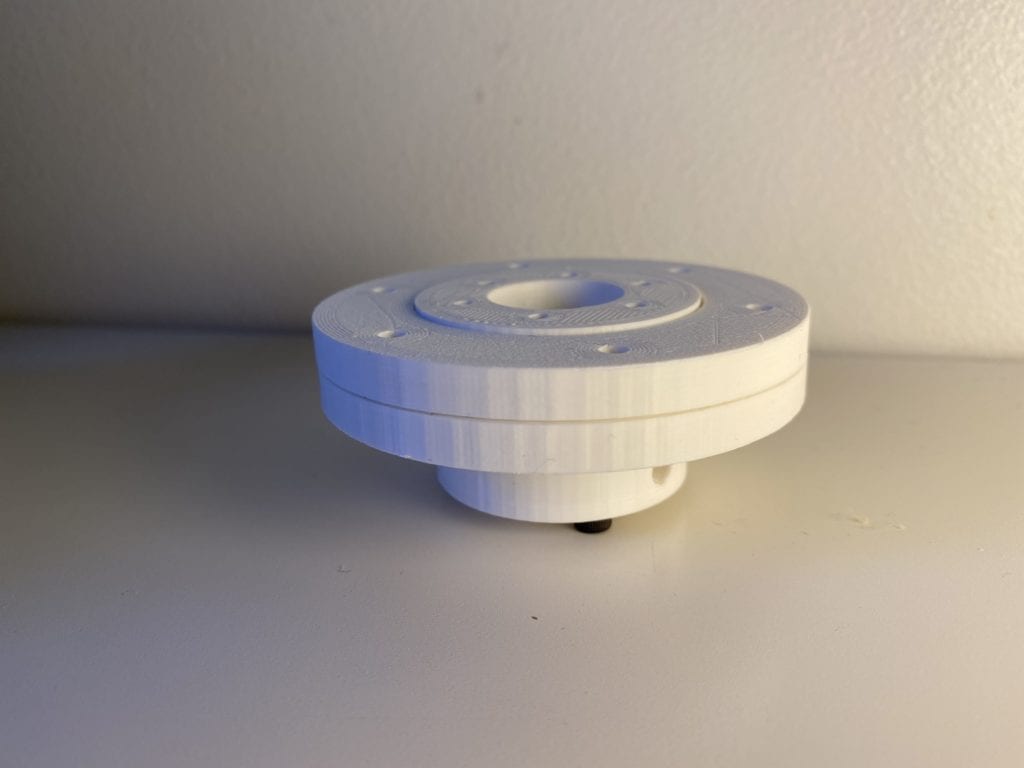
Nacelle simulation
CFD simulation was performed at 22 m/s, to find anticipated surface pressures and deflections. CWC speeds will not exceed 13 m/s. Two simulations were used, one with wind parallel to the fin, and one with wind perpendicular to the wind.
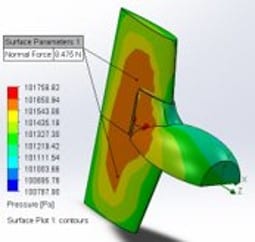
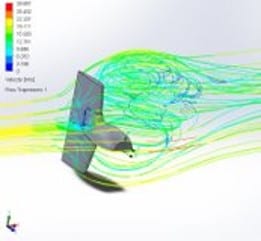
Concept Prototype
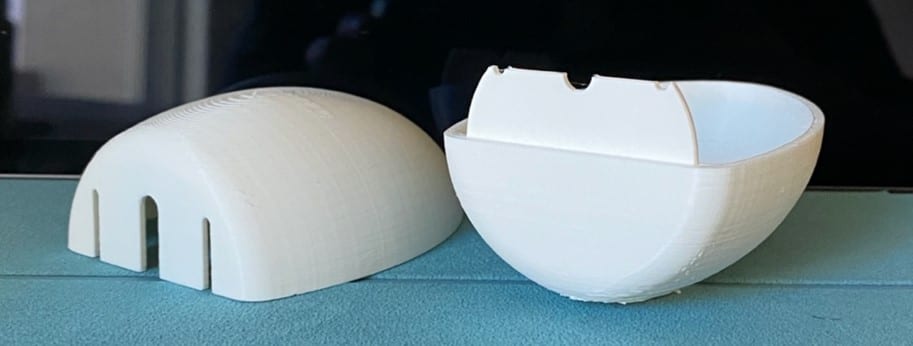
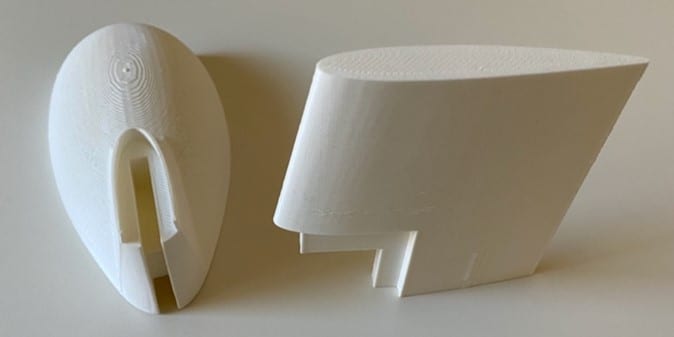
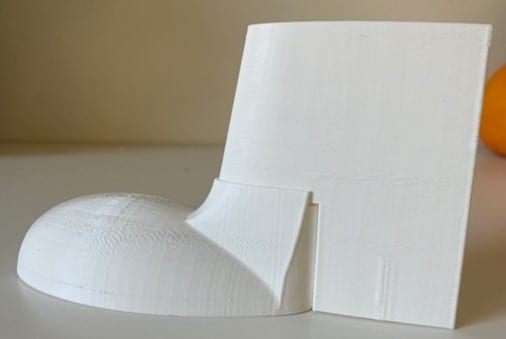
Manufacturing
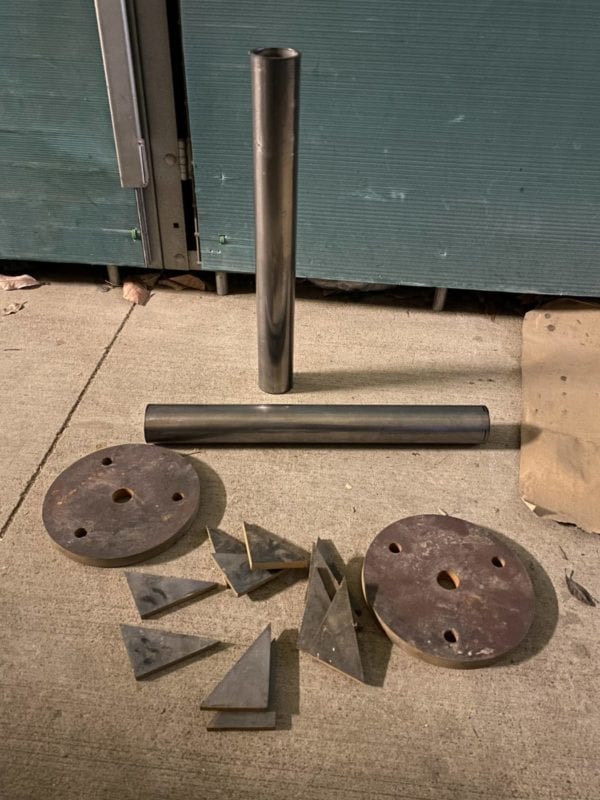
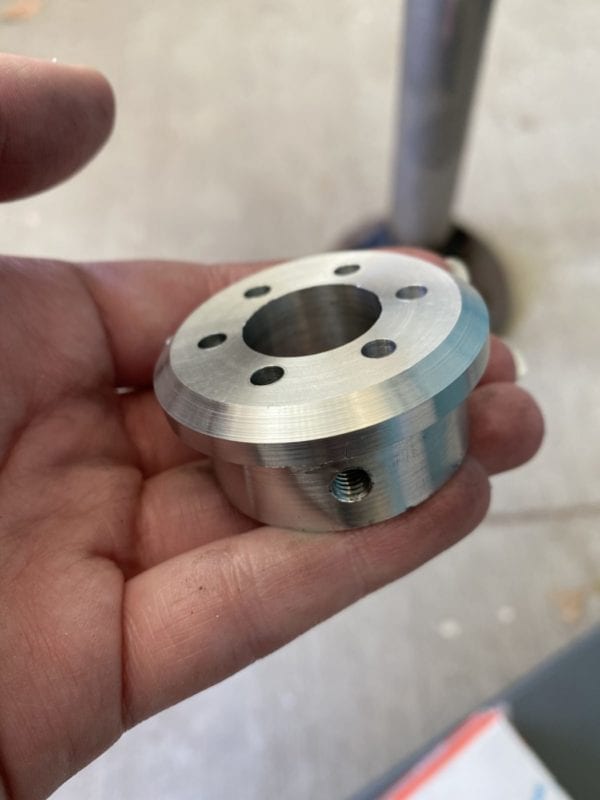

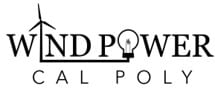
Cal Poly Wind Power Club
This project is sponsored by Cal Poly Wind Power Club as a part of the National Collegiate Wind Competition for the National Renewable Energy Laboratory and the Department of Energy.
Final Design
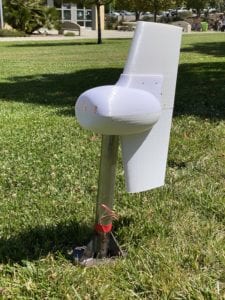
Testing
Our team facilitated several tests and surveys, including on yawing rates, collision, and tower strain. Doing so allowed our team to verify our design fulfilled the necessary requirements.
stress and deflection test
The stress on the tower can be analyze by the tower strain gauge test which we use the Vishay P3 Strain Indicator and recorder as the measurement tools. The expected strains were within the range of the device, but many confounding factors caused the test to be inconclusive including application of the strain gauge, temperature, and resistance of the wires. We also tested the deflection of the fin and could not see any visible movement.
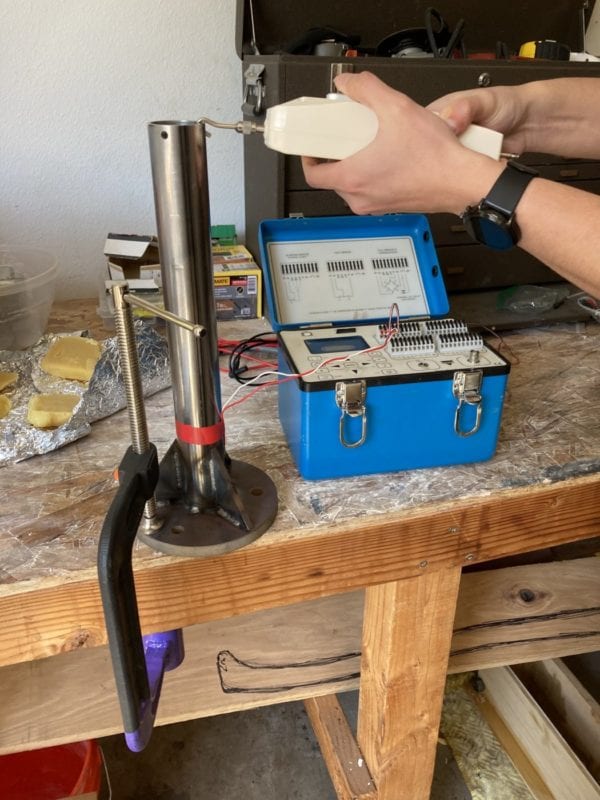
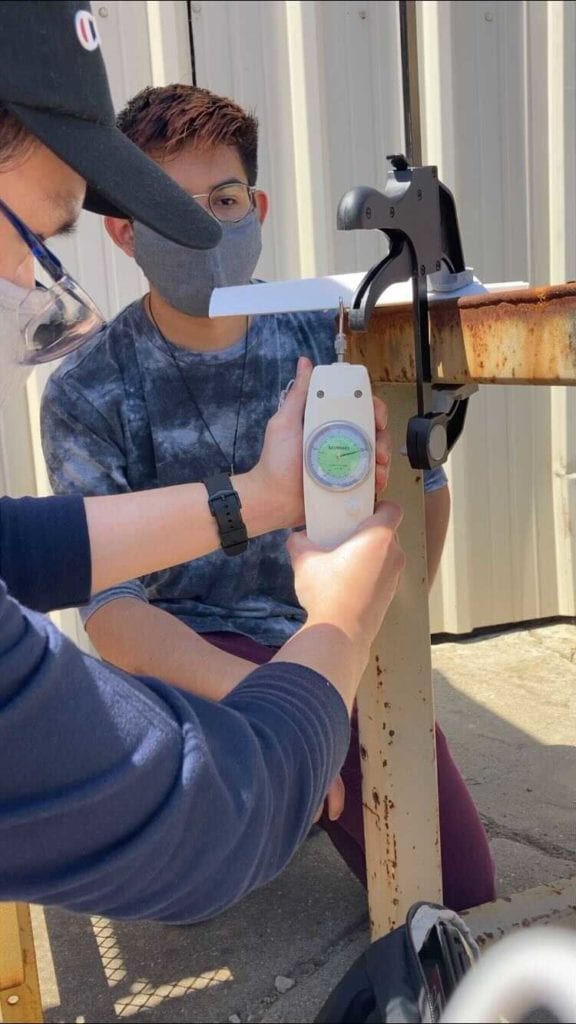
Yaw test
We conducted field testing to ensure the functionality of the yawing mechanism. On a windy day, we subjected the turbine to the wind and positioned it in the wrong orientation to see how well it would self-correct as shown below.
Collision and assembly test
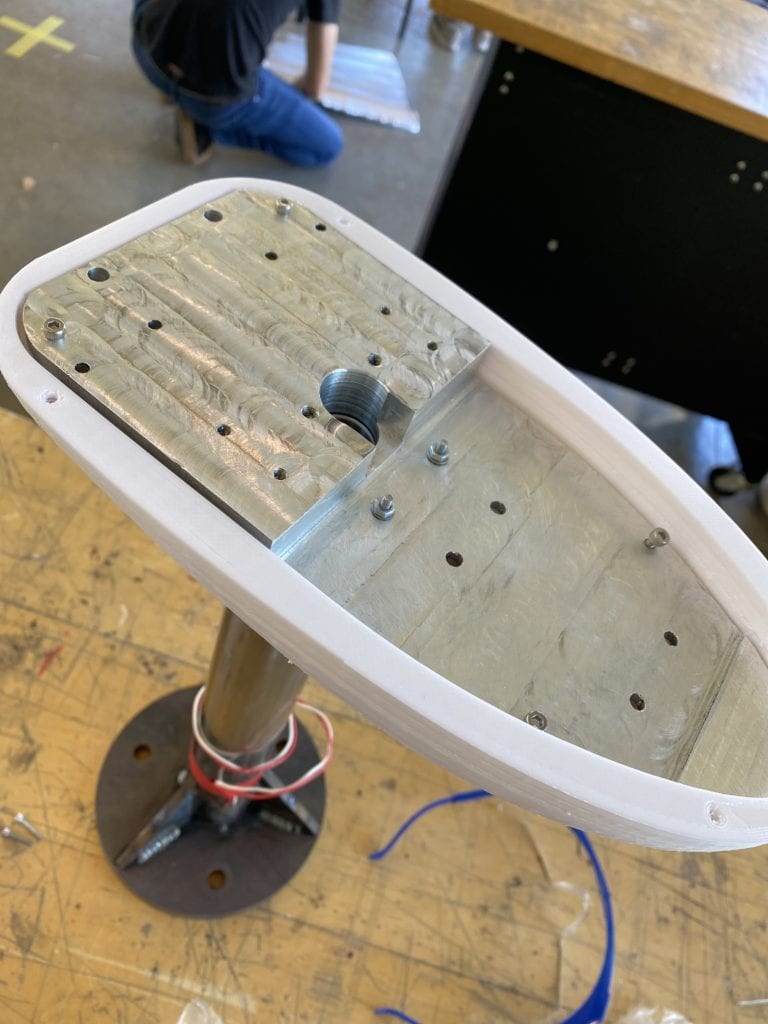
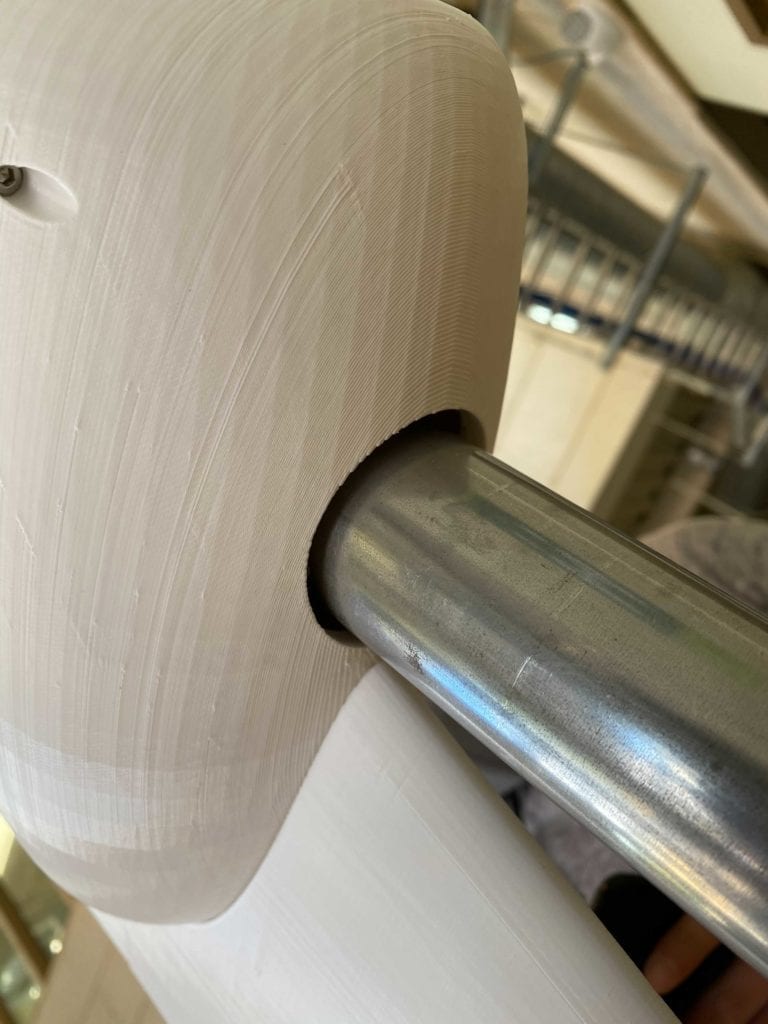
Recommendations
Due to COVID-19 safety precautions, our team was unable to access a proper wind tunnel in order to verify system performance. We did test at particularly windy areas of campus, as well as with large fans on campus, but future testing will need to be completed in the wind tunnel.
While we were able to verify size, yawing, and collision requirements, our team found difficulties in setting up and executing a stress and strain test on the fin and tower. We recommended to Cal Poly Wind Power that they conduct further testing focused on deflection or vibrations instead of stress or strain.
The yaw fins are very heavy because of the amount of infill. If the turbine were to be imbalanced, a solution would be to reprint the nacelle and yaw fin with different amounts if infills. Future iterative testing could also be completed to make the shape more aerodynamic.
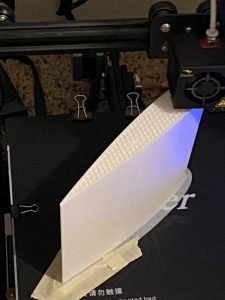