Our Team
We are a team of Cal Poly senior Mechanical Engineering students. We met in the fall of 2020 and have enjoyed the opportunity to work together on this project. It wasn’t always easy to collaborate in the midst of a global pandemic, but we made it work!
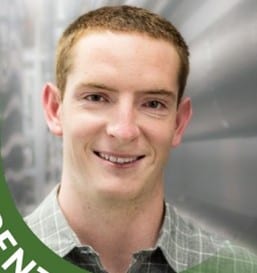
Jason Behrens
I am a fourth year ME student with an interest in control systems and mechanical vibrations. In my free time, I can often be found rock climbing or running. I am looking forward to moving to Boston for full-time employment this summer!
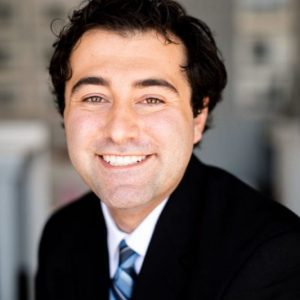
Stephen DeHerrera
I am a fifth year ME student interested in biomechanics and sustainability. Outside of school I enjoy rock climbing, hiking, and playing the guitar.
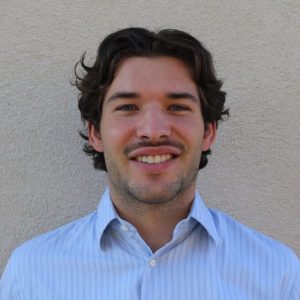
Seth Ewing
I am a fourth year ME student interested in vibrations and controls. In my free time I enjoy DJing and producing house music, reading and cooking.
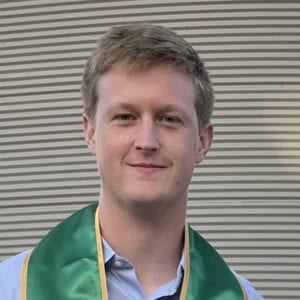
Ryan McMullen
I am a fourth year ME student with a focus in Mechatronics. My interests are in control systems, vibrations, and the use of magnets for levitation and damping .
Acknowledgements
We would like to thank Dr. Gregory Scott and Toan Le for sponsoring this project. We would like to thank our advisor, Dr. Eltahry Elghandour, for his guidance over the course of this project, and the Cal Poly Mechanical Engineering Department for making this project available to us during the COVID-19 pandemic. We would also like to thank Dr. Ashraf Elbarbary for his help with our magnetic modelling, Ben Carr and Colin Harrop for their help with the shaker table in the vibrations lab, and Rob Brewster, Peter Moe-Lang, and Virgil Threlkel for their help with our manufacturing.
Our Project's Videos
Our Project's Digital Poster
Project Overview
This senior project is a continuation of a master’s thesis by Toan Le. Our objective is to design a product that can isolate a scanning tunneling microscope from ambient vibrations so that it can take accurate atomic resolution images. The scope of our project is to expand upon previous design work already completed, and manufacture, test and validate Mr. Le’s designs as well as our own.
Design Specifications
- Housing natural frequency above 400 Hz
- Mass-spring-damper system natural frequency below 2 Hz
- Magnetic damping ratio between 0.10 and 0.2
- Viscoelastic damping coefficient between 50 and 400 Ns/m
- Stage vibration amplitude below 2 mm
- User satisfaction when swapping samples within the VIS
- Ease of removing/replacing VIS within vacuum chamber
Design Choices
Mass Spring Damper System
- Pairs of angled springs to counter motion in yaw and wobble modes in addition to up and down
- Relatively massive stage and soft springs to drive down the natural frequency
- Springs connected to stud anchors in top cap and stage for adjustability
Housing
- Aluminum cylinder for stiffest possible walls
- Mass-spring damper system integrated into top cap
- Magnetic adjustment system integrated into bottom cap
- Viton rings at metal-to-metal interfaces between caps and housing to damp high range frequencies
Magnetic Adjustment System
- Magnets located in housing below stage
- Size and strength of magnets determined by our testing
- Magnets press-fit into aluminum swash plate that can be raised or lowered via hex head screws in the bottom cap
- Can be locked in place with more hex head screws that thread into nuts below bottom cap
- Adjustable magnet height gives us a tunable damping ratio
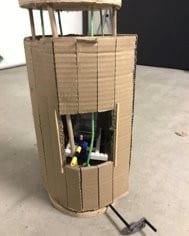
Ideation model used to test oreliminary ideas in our prototyping process.
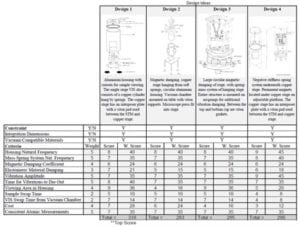
Weighted decision matrix that we used to compare various options and come up with our final design.
Final CAD Model
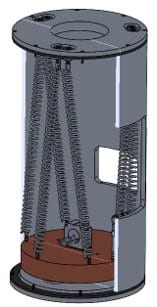
Assembly level CAD model with housing wall cut away so internal components can be seen.
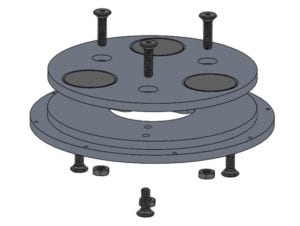
Exploded view of magnetic adjustment system. Magnets press-fit into an aluminum swash plate which can be raised or lowered using the hex head screws in order to fine tune the damping ratio.
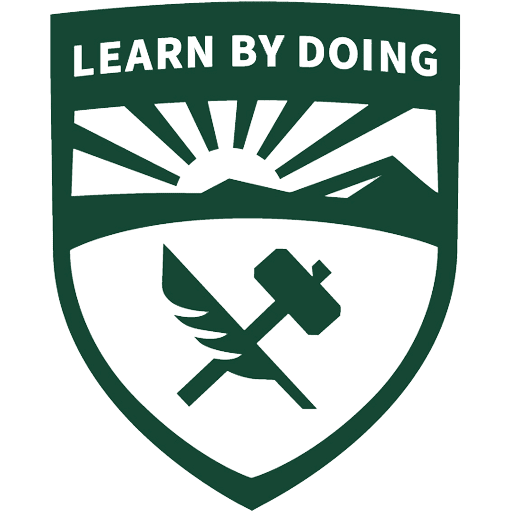
Cal Poly Chemistry Department
This project is sponsored by Dr. Gregory Scott of the Cal Poly Chemistry Department and Cal Poly master's student Toan Le.
Design Justification
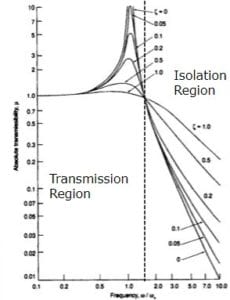
Theoretical transmissibility plot of a mass-spring-damper system. To isolate vibrations, incoming vibrations must be in the “Isolation Region,” to the right of the natural frequency. Hence, a low natural frequency is needed.
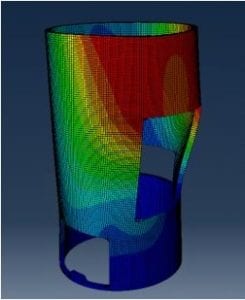
Results of Finite Element Analysis performed on the housing predicting a housing natural frequency around 500 Hz. A softer housing would risk amplifying incoming vibrations into the mass-spring-damper system.
Damping Ratio Calculation
We calculated the damping ratio from our test results using the log-decrement method. This method allows us to use the amplitudes of any two consecutive peaks to determine the damping. First, the log decrement is calculated as follows:
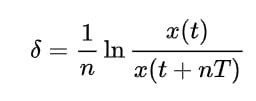
This log decrement value is then used with the following equation to calculate the damping ratio of the system.
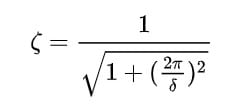
Design Verification
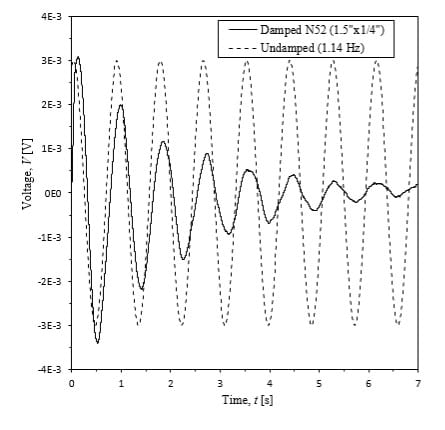
Results of damped and undamped linear perturbation test.
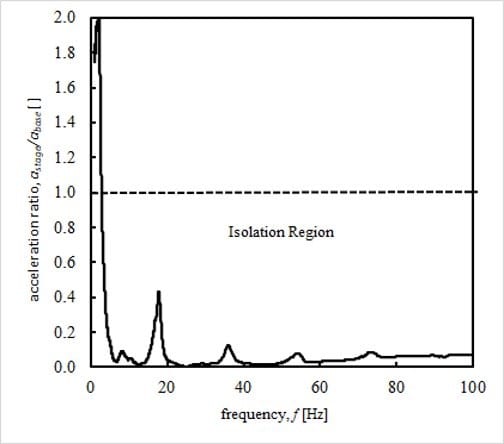
Results of entire assembly shaker table test in the frequency domain.
Testing Performed
Mass Spring System Natural Frequency Test- Our design was verified by subjecting the copper stage to a small linear perturbation and recording the acceleration output on an oscilloscope. Our theory predicted a natural frequency of 1.2 Hz and we achieved a natural frequency of 1.14 Hz.
Magnetic Damping Test- Our design was verified by subjecting the copper stage to a small linear perturbation and recording the acceleration output on an oscilloscope. With a single magnet and a gap distance of 3 mm, we measured a damping ratio of 0.09.
Housing Shake Table Test- We performed a sine sweep on the housing using the vertical shaker table in the vibes lab. We measured a housing natural frequency of around 500 Hz, confirming our FEA model.
Full Assembly Shake Table Test- We performed a sine sweep on the completed assembly using the vertical shaker table in the vibes lab. We measured a natural frequency of 2.21 Hz, slightly over our target of 2 Hz but still low enough to isolate most incoming vibration frequencies. We found that the isolation region for our full system begins at 2.82 Hz. We were also able to tune our damping ratio to 0.2 by lowering the magnet swash plate to obtain a gap distance of 12 mm.
Final Design
Specifications
System Natural Frequency – 2.21 Hz
Mass-Spring-Damper Natural Frequency – 1.14 Hz
Damping Ratio – 0.2 (Tunable)
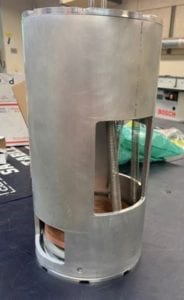
Purchased Components
- Stainless Steel Springs
- #4-40 Vented Screws
- #8-32 Stud Anchors
- 1/4-20 Stud Anchors
- 1/4-20 Thin Hex Nuts
- 1″ Dia. x 1/4″ N52 Neodymium Magnets
- 1/4-20 Ultra Low Profile Hex Head Screws
Custom Components
- Aluminum Housing
- Top Cap
- Bottom Cap
- Copper Stage
- Magnet Swash Plate
- Viton Rings
Vacuum Chamber Integration
Our design needed to be compatible with a high vacuum environment. This means that the materials we used needed to be inert with relatively low outgassing properties. This is why we used Viton, a vacuum compatible viscoelastic material, for our gaskets. Additionally, no lubricants can be used in a high vacuum environment, so all of the screws and nuts we used were silver plated, to minimize wear and extend the life of the hardware without needing any lubrication.
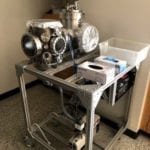
Dr. Scott’s vacuum chamber. Our design needed to fit within the cylinder on the left and be compatible with a high vacuum environment.
Conclusion
What we learned:
- How to take advantage of previous research and experimentation to inform and improve our own design
- Quickly gianed competence in multiple areas, including multi-DOF vibrational systems, eddy current damping, magnetic modeling, and shake table testing
- Manufacturing takes at least three times longer than we planned for
What we’d do next time:
- Build a better functioning model of our eddy current damping system to compare the results of our testing
- Perform additional testing on the housing with and without Viton, and with different thicknesses of Viton, to determine the material’s contribution to our final damping coefficient and natural frequency
- Use the VIS with an actual scanning tunneling microscope to verify it can take atomic resolution images with our vibration isolation system