The Three Stooges
Meet the team!
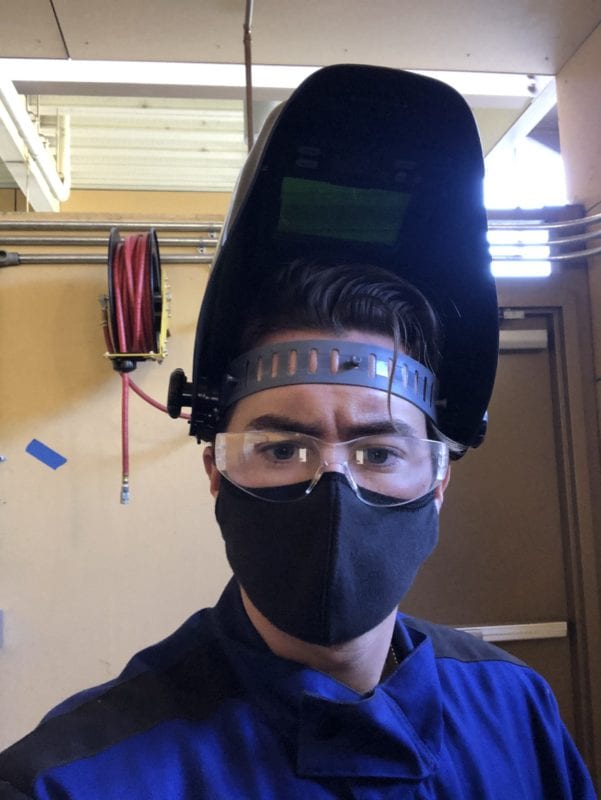
Jared Nash
Team member
Hello! My name is Jared Nash. I’m a fifth year M.E. student with a ‘General’ concentration. I enjoy spending time with friends and staying active. Please enjoy looking over our senior project!
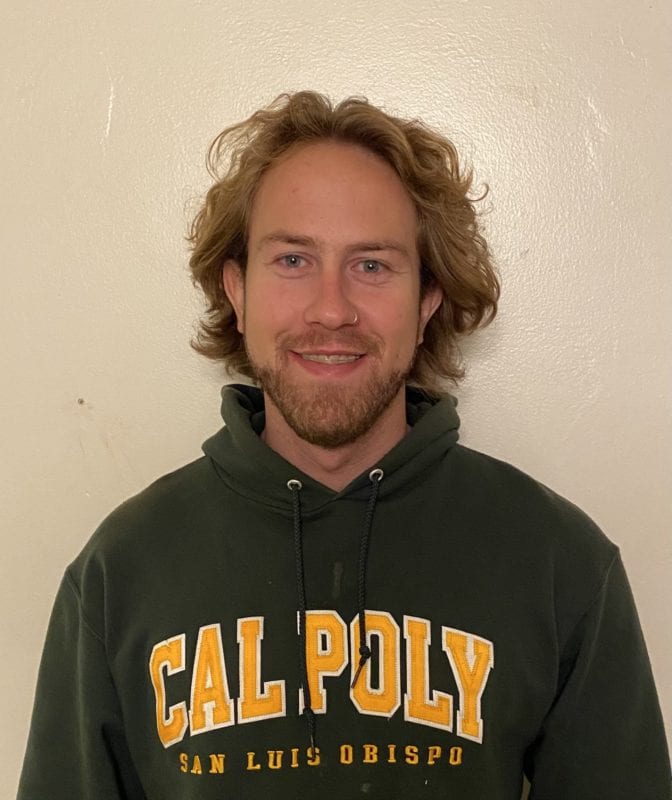
Aaron Shein
Team Member
Thank you for checking out our Senior Project! My name is Aaron Shein and I am a currently enrolled in the blended BS/MS Mechanical Engineering program with an expected graduation date of June 2021. I very much enjoyed the CAD designing and metal manufacturing that this project had to offer. Outside of the classroom you can find me riding around SLO on my moped or out of town on a backpacking trip.
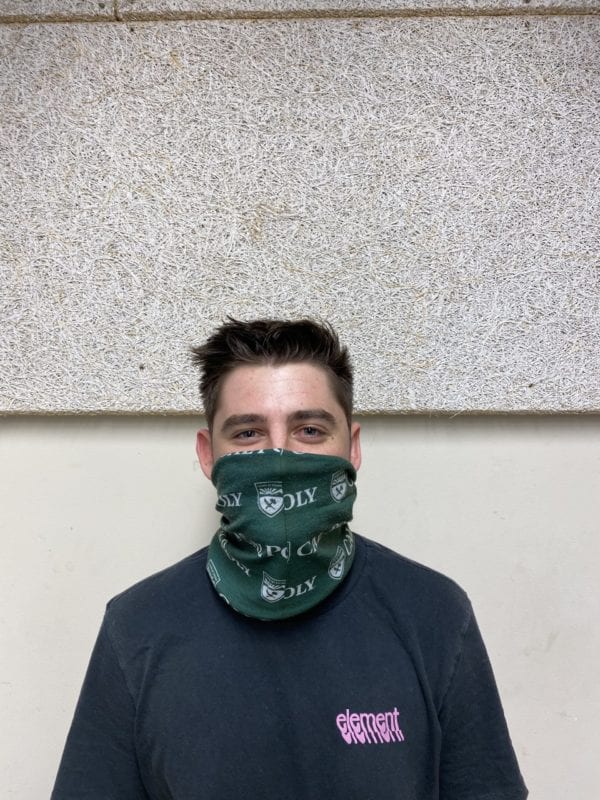
Laurence Duclos
Team Member
Hi my name is Laurence Duclos. I am a fifth year M.E. student with a ‘General’ concentration. I really enjoy stress analysis and have a job as a stress engineer at an aerospace company after I graduate. Outside of class I enjoy spending time with friends and family.
Acknowledgements
Our group would like to thank first and foremost our sponsor Daniel Ochoa for making this project possible. We would like to thank all of the different shop technicians who gave us help along the way, and we would also like to thank Professor Rossman for being a wonderful advisor throughout the entire process.
W22: Senior Project Videos
Below are a few videos of our vibratory tumbling verification prototype in action.
Vibratory Tumbling Machine Digital Poster
Problem Statement
C&M Topline’s current product, a 3 cubic-foot vibratory tumbling machine, allows manufacturing companies and machinists to deburr and finish metallic parts, but has not been re-designed in over 30 years. C&M Topline requests a redesign of this machine to match and improve on competitor’s features including noise reduction and increased portability and to satisfy customer’s feedback.
Requirements

Early Prototype
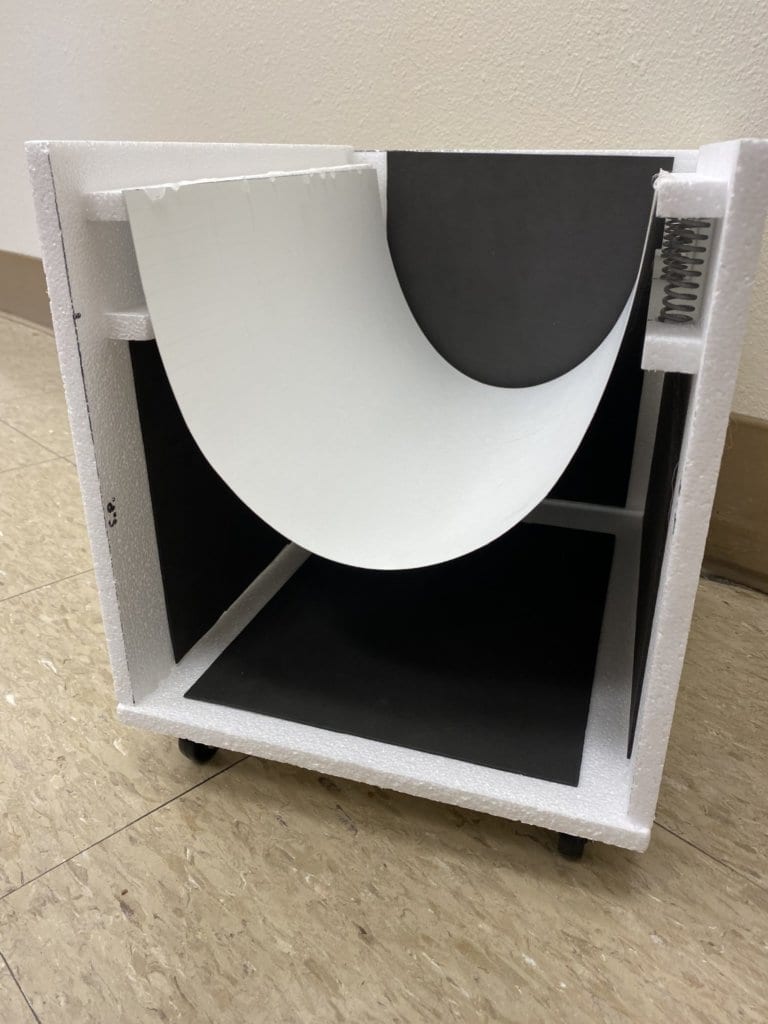
Prototype Testing
With Covid-19 restrictions in place at the beginning of our prototyping and manufacturing, we were limited to testing functions of our design at a small scale. We physically tested for heat and noise generation while in an enclosed environment, while Abaqus was used for structural FEA.
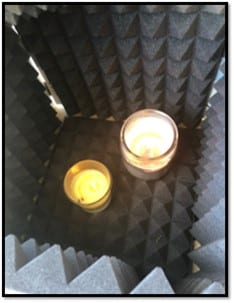
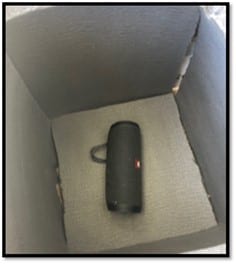
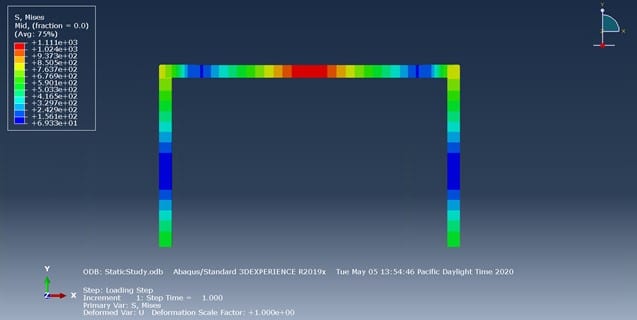
CAD Model
The design can be broken down into four subsystems: structural, tub, vibration, and fluid. One key component of our project was to utilize as many existing parts as possible from the current Mr. Deburr DB300. This led to most of the redesign focusing on the structural system while incorporating the existing tub and fluid system accordingly. The final design incorporated 53 unique parts.
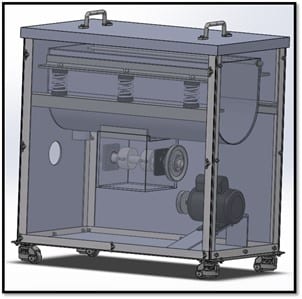
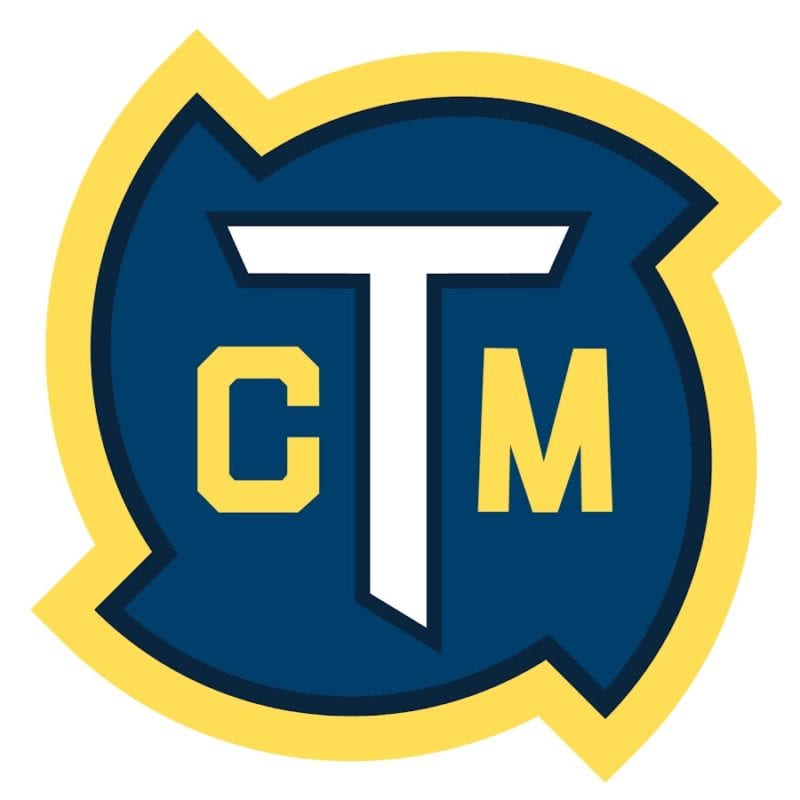
This project was sponsored by Daniel Ochoa, Owner/President of C&M Topline.
Manufacturing
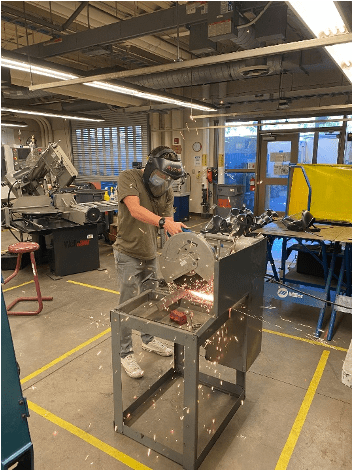
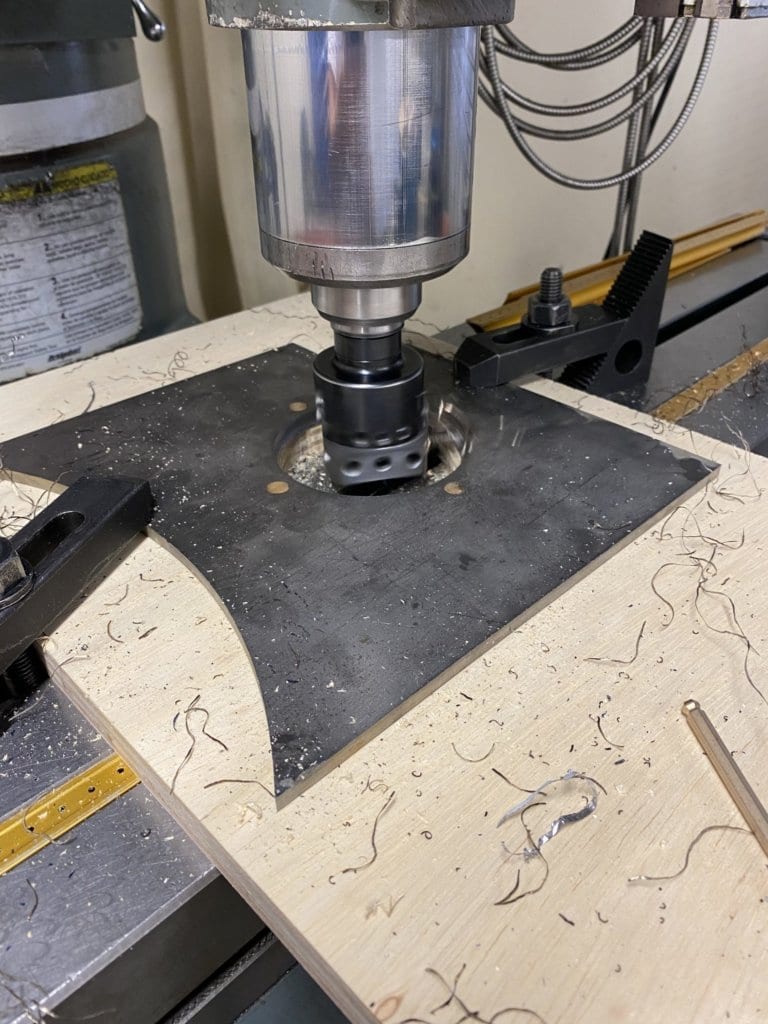
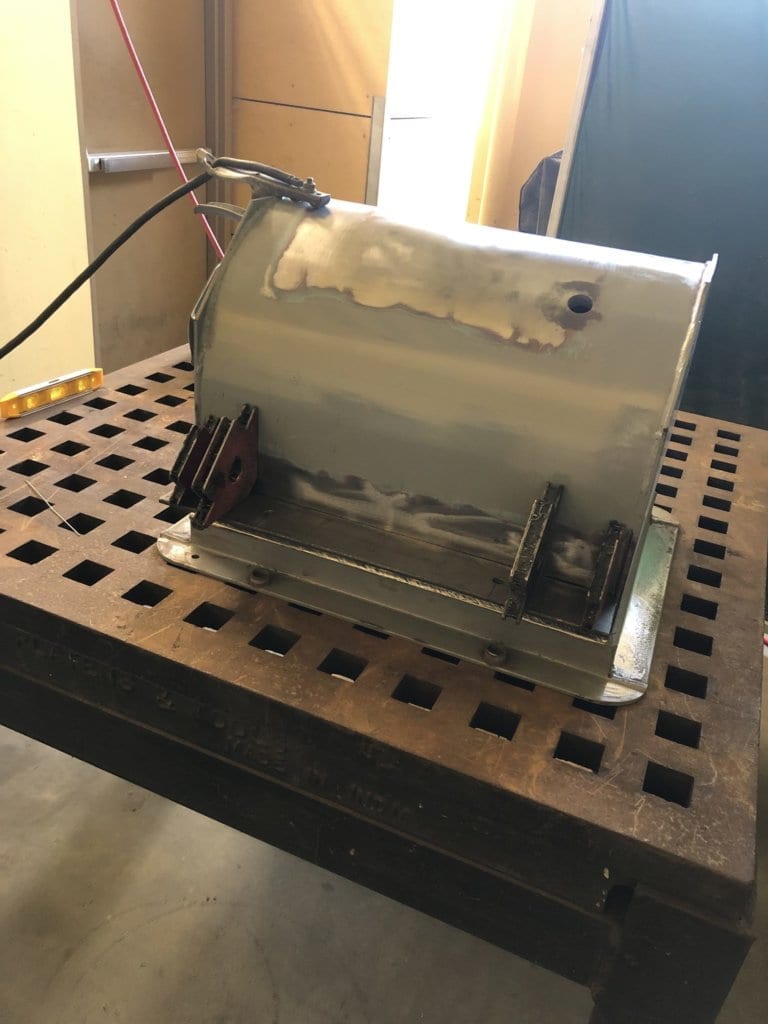
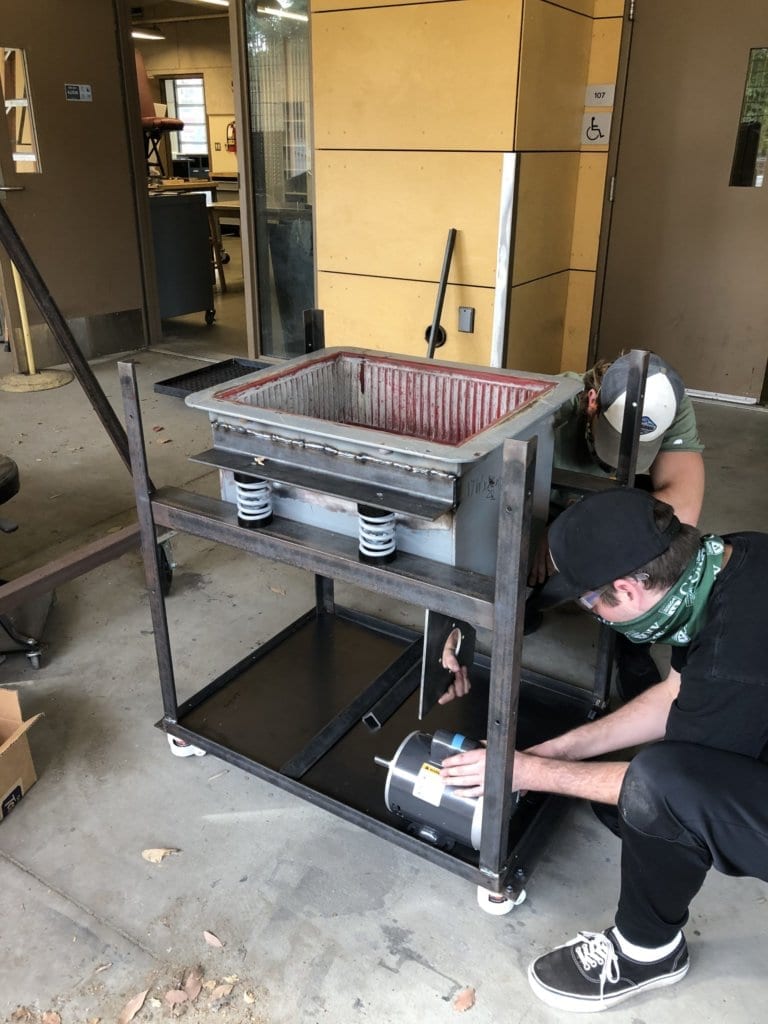
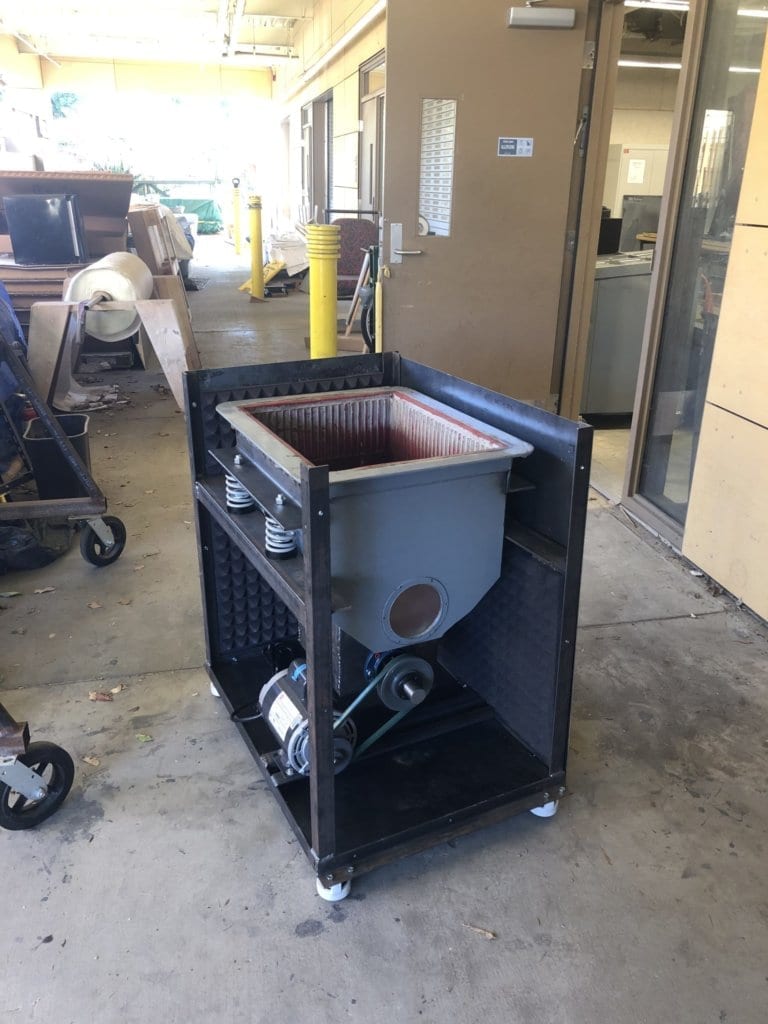
Our team manufactured the machine mostly out of angle steel and sheet metal. All the steel and metal was cut to size, drilled for holes, and welded together. Our sponsor provided us with an old tumbling machine to repurpose the tub and he provided the motor and springs. The rest of the material like the sound paneling and caster wheels were purchased and assembled together to complete the manufacturing of the prototype.
Final Design
Below you can see the final manufactured design. The lid and front panel are removed for visual purposes. With our manufacturing capabilities in mind, we are pleased with the final result.
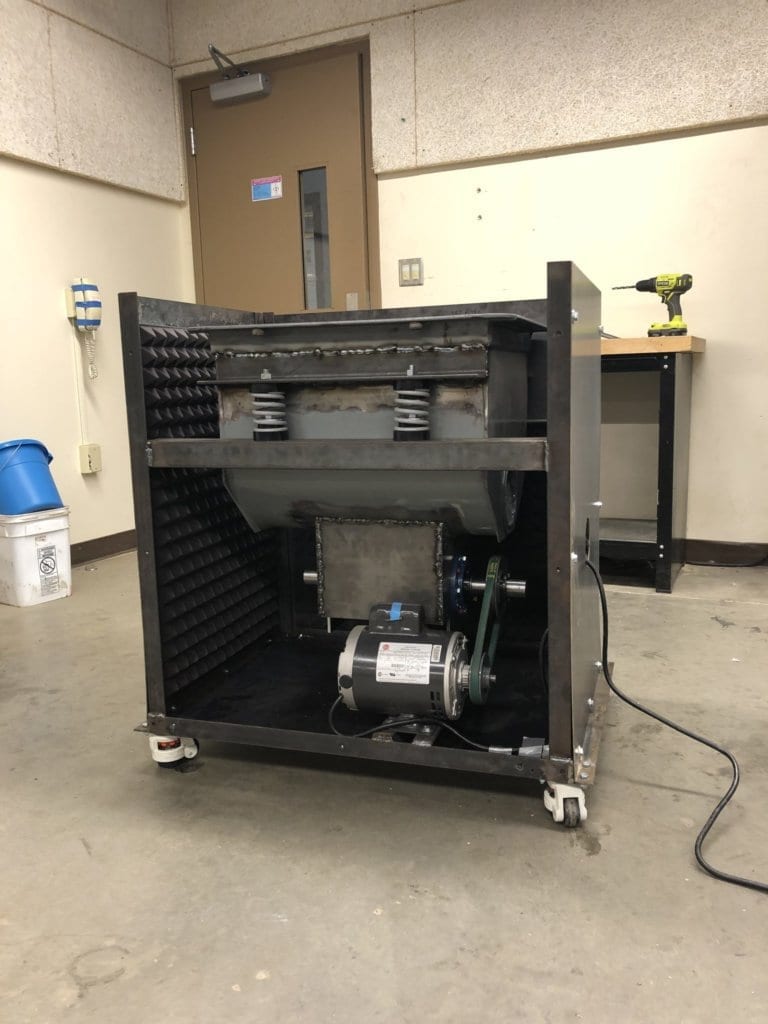
Testing Results
Unfortunately the parts for our machine were different than originally anticipated. We had a larger diameter shaft and heavier offset weights. This in turn caused the motor we had to be undersized for the machine and caused it to draw too much power from the wall outlets eventually leading us to trip the breakers. This repeatedly happened so we could only run the machine for around 20 seconds at a time before the outlet died. However, in running those 20 seconds we found that the sound of the machine was quieter than the original Mr. Deburr 300 design just by listening and comparing.
Conclusion
While Covid-19 restrictions hampered our early manufacturing during the Spring, we were able to make good progress during the Fall. Due to this restricted timeframe along with limited machine shop time, we were not able to fully test our prototype based upon the requirements set forth. The recycling of the old tub with different dimensions also slowed down and altered our manufacturing process.
Taking these challenges into consideration, we as a team are still happy with the results produced. This prototype demonstrates that the updated structural design is an effective step forward for C&M Topline. The closed box design in addition to foam paneling highlights the noise reduction capabilities.
Recommendations:
- Analyzing the benefits of plastic versus sheet metal casing
- Manufacturing techniques to reduce sheet metal rattling
- Align motor belt to be in line with the tub’s center of gravity
- Improve upon motor railing to allow for further belt tensioning
- Engineering analysis to optimize rotor dynamics of the vibration producing system
References
Cal Poly Senior Project: Student Success Guide