Our Team
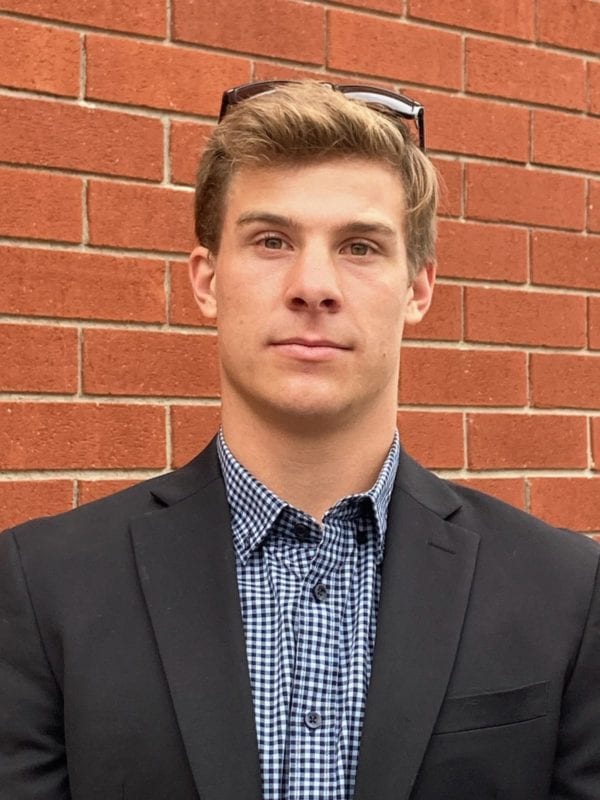
Chandler Jones
Cal Poly has provided me with an exceptional education. Our team has pushed our limits to design and communicate well. As a college, we have made the best of this COVID situation and have pulled together our projects with great gumption. In all my years I have yet to see a better example of engineering in action.
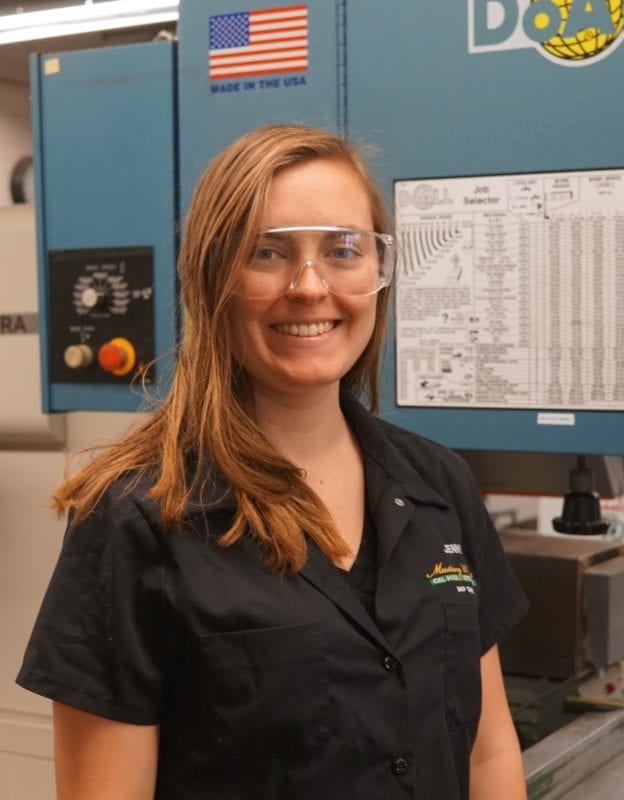
Jenny Verheul
Over the course of my five years at Cal Poly, I have had the privilege of learning the intricacies of engineering problem solving.
This project has been a great hands-on experience for working in an extreme environment, and I look forward to future discoveries.
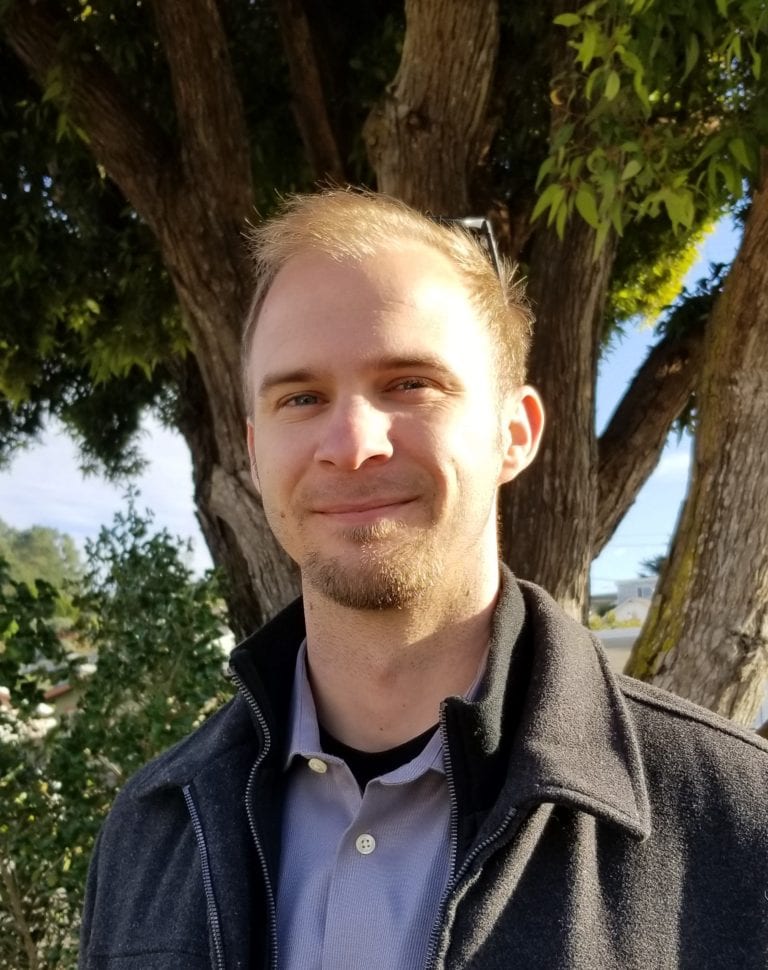
Michael Di Giorgio
Working on this project has been a great experience as designing a product that redefines the conventional way of doing things is one of the best parts of being an engineer. I have enjoyed my time at Cal Poly and will be moving on to work at Lawrence Livermore National Laboratory after graduation.
Acknowledgements
Background Video:
Our Project's Digital Poster
Problem Statement
Design a small, neutrally buoyant device that can interface mechanically and electrically with the Marine Applied Research & Exploration’s UROVs, Beagle and BATFish, to collect seawater at target locations at depths down to 1000 feet.
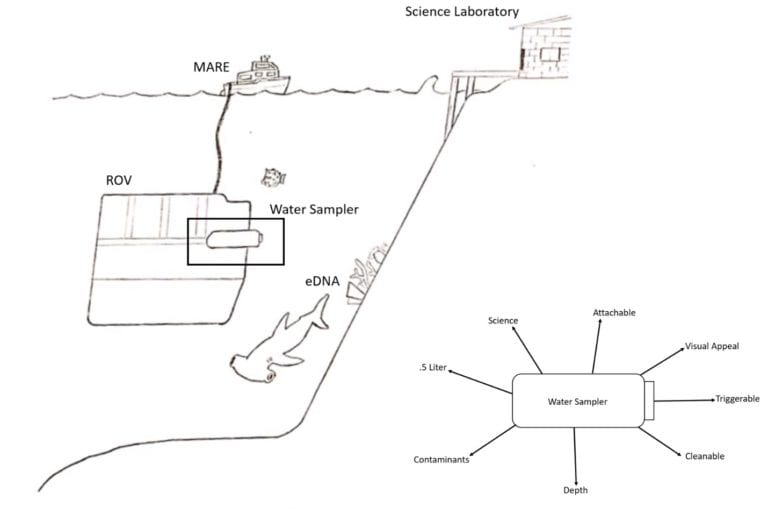
Above is our boundary diagram. Our focus is to collect and protect sample water columns so that researchers in a science laboratory can analyze the environmental DNA within. Our device is attached to an ROV that is controlled by MARE.
Engineering Specifications
The project’s final design must satisfy the following:
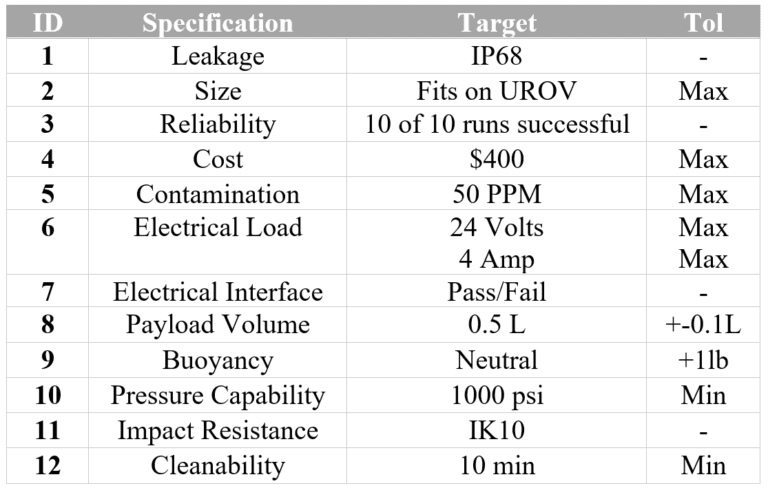
Design Concept
A modular Bag design was chosen for the following reasons:
- Creates a compact layout and housing, with subsystems able to be mounted in separate areas of the craft.
- An IV bag was decided upon due to its sterile design from the manufacturer, its characteristic of being compressible, and their availability for continued sampling long after the end of our project.
Other design choices to note:
- Valve with input and exhaust, allows water to continually flow, reducing reservoirs of non-relevant water which may contribute to sample dilution.
- 3D-printed housings & bulkheads allow for reduced corrosion in Sea-water, as well as quickly reproduced parts if/when needed.
- Material choice of 6061 Aluminum on our connecting plates allow for reduced corrosion in seawater, as well as the conductivity required for a sacrificial zinc anode.
Design Iteration
First
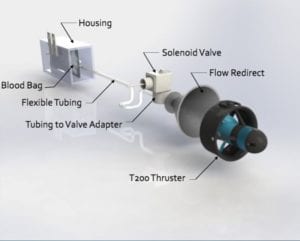
This CAD model shows our preliminary design which implements a thruster that pumps the water into the system directed by a funnel. We were initially hoping to use the ROV thruster or something onboard the ROV as a pump, to flow water into the sample container by only needing to control a single solenoid valve.
Second
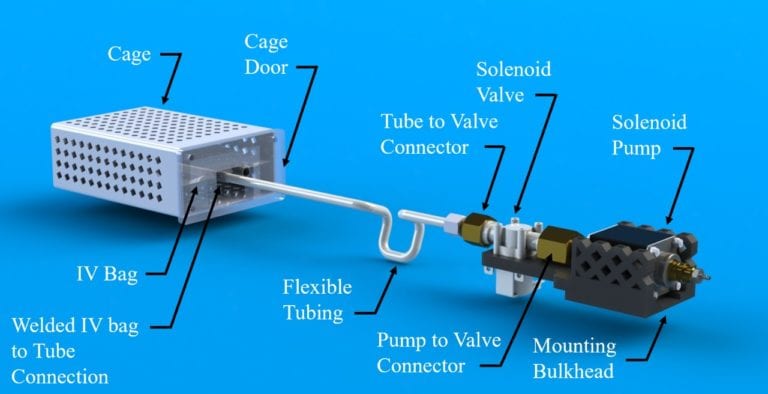
This CAD model shows our critical design which implements a solenoid pump that pumps the water into the system and a mounting bulkhead to align it with the solenoid valve. The pump is fully flooded and shaftless.
Third
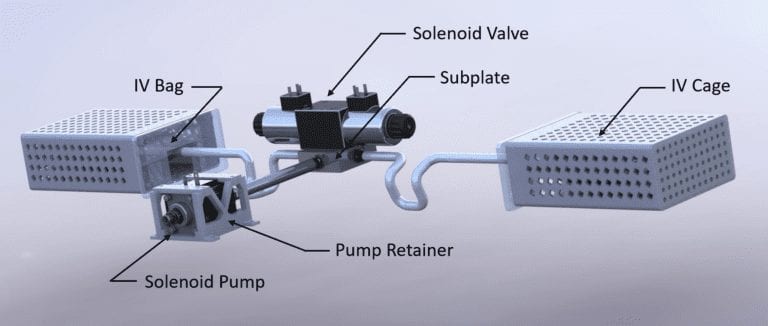
This CAD model shows our final design which implements our final selection of fittings, subplate, solenoid pump ad valve, and the solenoid pump retainer. The valve is a 3-way 4-position direct control valve which acts as manifold that can redirect a single inlet to three outlets, one at a time. This allows multiple collections from a single pump with minimal headloss.
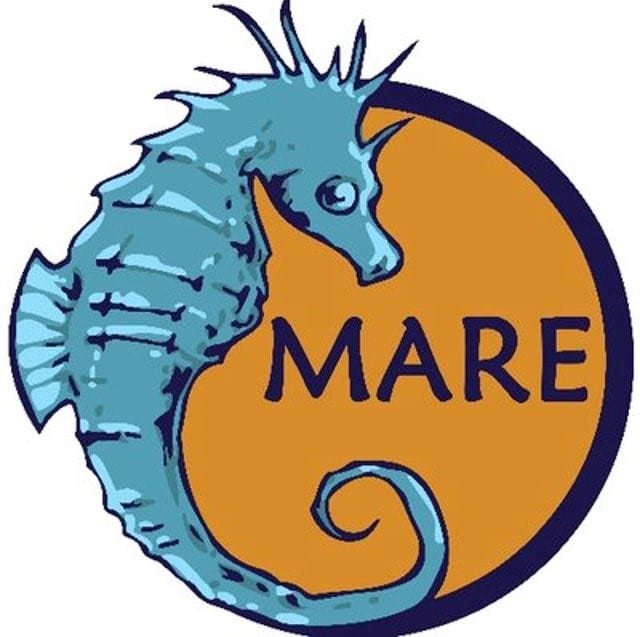
Marine Applied Research & Exploration
Our team thanks our sponsor Dirk Rosen.
Preliminary Analysis
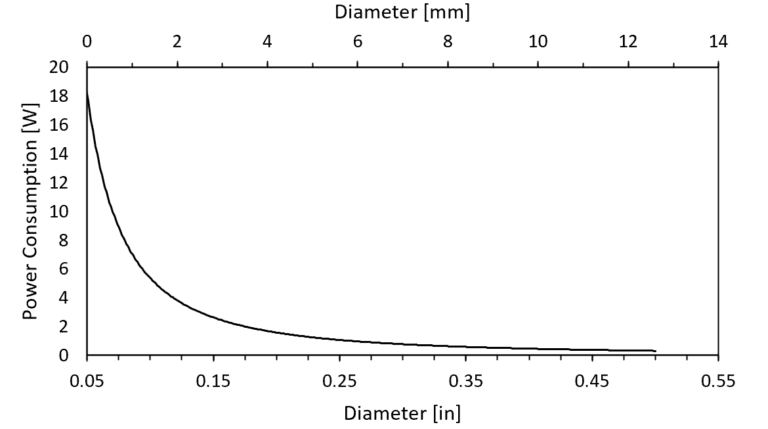
As shown above, smaller tubing diameters cause high headloss. Typical IV tubing is 2-3mm which is in the high loss range, which led us to contacting IV bag manufacturers for custom fit bags with larger tubing.
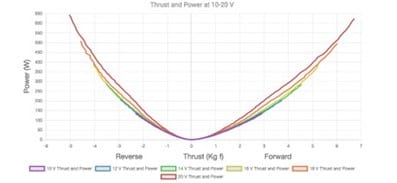
The curve shown above is for our initial idea of using a T200 brushless thruster. However, at high RPM to meet headloss, the power required exceeds our system limit. This led to researching shaftless pumps.
Pump Selection

A solenoid pump was chosen because it is shaftless and has epoxy sealed wiring with a corrosion resistant stainless/brass housing. As a shaftless pump, it is self-priming and is able to fully flood with water which minimizes chance of cavitation and led us to believe it would work at high pressures.
Design Verification
Hyperbaric Testing
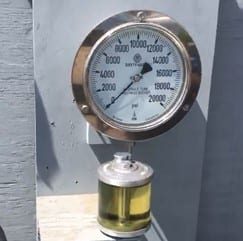
Pressure readout for the hyperbaric chamber.
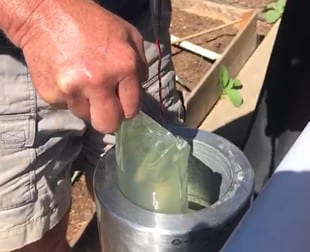
A filled IV bag is retrieved from the chamber after a 600 psi trial run.
Due to COVID, we were not able to perform hyperbaric testing ourselves. Our sponsor performed all pressure tests. The chamber is equipped with a lid that has an sealed electrical connection which allowed our system to operate in a medium (oil) at various pressures. The system was controlled by DC power and a PWM driver. Pressure was slowly ramped to various pressure testing points (1500 psi max) but was ramped faster than would be anticipated during an expedition.
Fill Time
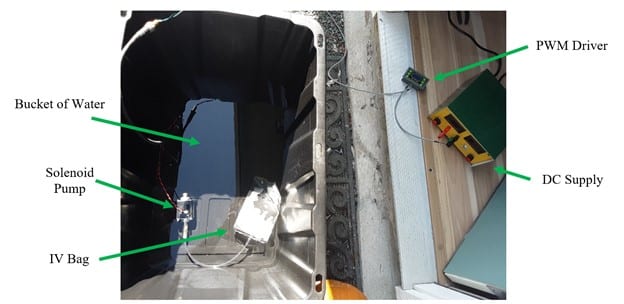
To best determine the fill time, we looked to see average fill time at various duty cycles. We used the same PWM driver as was used in pressure tests to ensure results could be reproduced by MARE with their electrical system.
Local Contamination
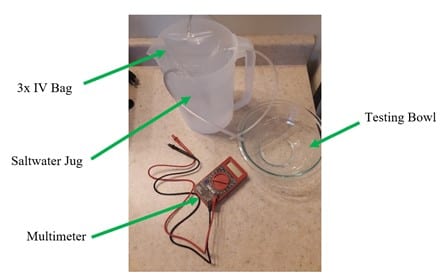
We tested the permeability of IV bags when submersed in a highly saltwater to ensure that sample integrity would be obtained during a maximum 14 hour dive. We tested filtered tap water for electrical resistance before and after prolonged submersion in the saltwater bath.
Final Design
Our design is a single input, multiple output system. Each component is modular, interconnected by tubing, and electrically compatible with the Beagle and BATfish UROV. The design is made of corrosion resistant materials (Stainless, Nickel-coating, and PLA).
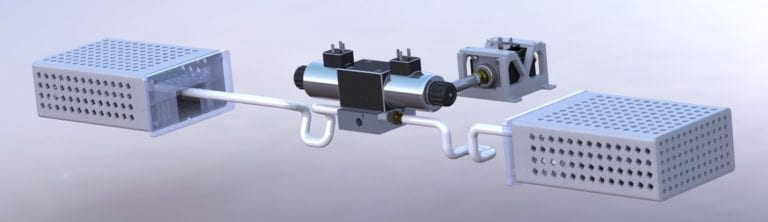
We designed our product so components could be easily sourced and reliable by choosing commercially available items. All components shown above can be purchased excluding the storage cage and pump retainer, which are 3D printed.
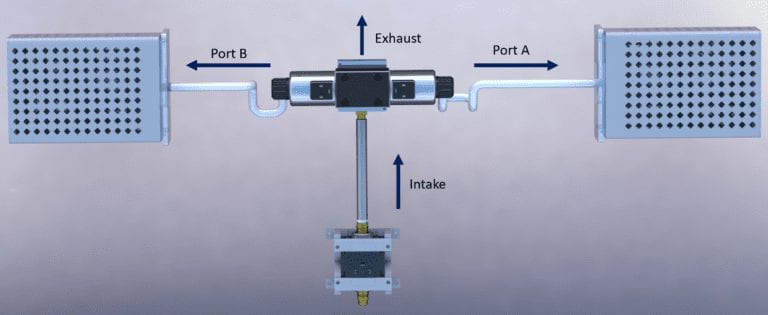
One of the unique features about this design is that it is always exhausting, allowing the system to be flushed of contaminants before beginning sample collection. There are two solenoids in the valve, powering one of them opens the respective port (A or B) and closes the exhaust port. For a single input, 3 controllable outputs are achieved.
Final Prototype
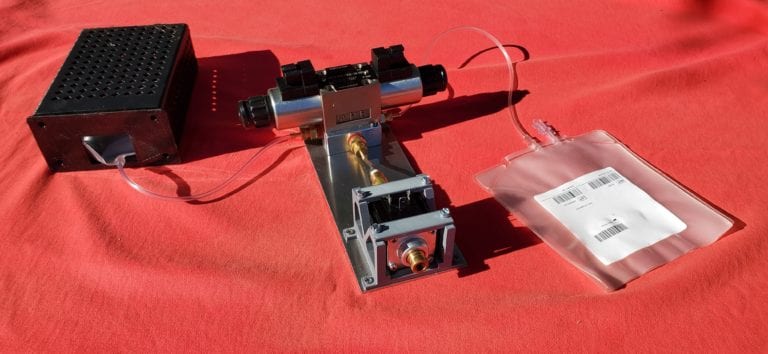
The aluminum plate that connects the pump to the valve in our final prototype is an addition which is provided for ease of mounting the entire unit, but is not required for the operation of this device. A disk of zinc can also be affixed to this plate, acting as a sacrificial anode, which will protect the valve from corrosion. This protection can be extended to the solenoid pump by a wire.
Final Test Results
Our tests verified that our product will not leak and is resistant to contamination from its local environment. We also verified that our product can seamlessly integrate with the UROV electrical system. Testing also shows a duty cycle of 35% provides the best flow rate at STP but that may change at depth. Our product did not plastically deform when tested at over 1000 psi, but we did not have reliable collection past 600 psi.We were unable to determine the root cause of failure as a result of the testing equipment becoming inaccessible. The table below shows our design specifications and our ability to meet them – green means we met the specification and red means we could not.
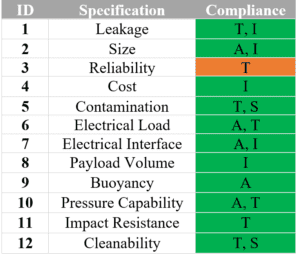
“A”, “I”, “T”, and “S” mean we verified our design by analysis and simulation, testing, inspection, or by similarity, respectively.
Conclusions & Recommendations
Progress at Conclusion of Project:
- Verified to 600 psi.
- Compatible with Beagle and BATFish.
- Modular Design compatible with N*2 samples, where N is the Number of Valves.
Improvements to be made for re-design:
- Adapt design to be compatible with the Beagle’s CTD pump.
- Test water emitted from CTD for quality loss or order a new 5P/5T pump from Seabird Scientific.
- Upgrade to 5/8OD 3/8ID Tygon tubing to fit on the provided fittings and decrease head loss in the system. Alternatively, perform more rigorous, testing with a higher quality pump. Recommended pump is designed by Gotec and sold through Clark Solutions to the USA.
Lessons Learned
Our project involved operating in a harsh medium and at a high pressures and to do so on a tight budget. We learned how to be innovative with how we employed commercial solutions to best meet our needs and accomplish the mission. We also learned that modularity in a design can be incredibly useful, as it allows for easy upgrades and can fit in tighter geometric constraints.