Our Team
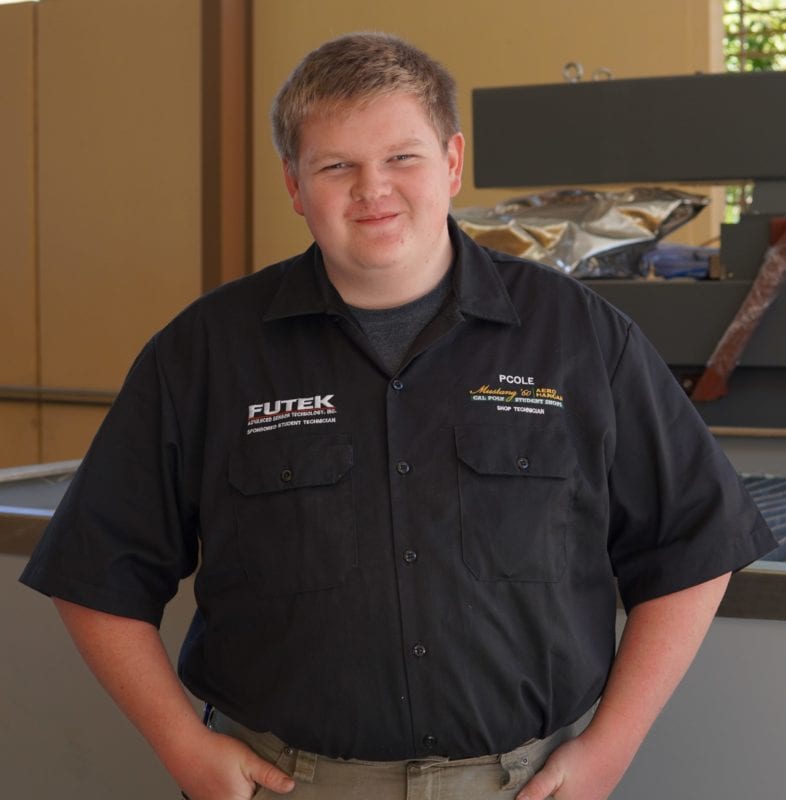
Philip Coleman
I am a fifth year mechanical engineer student in the general concentration. I am originally from Seattle, Washington. I have been a shop technician in the mechanical engineering shops for 3 years and have been involved with the campus SAE chapter Cal Poly Racing. Outside of school I enjoy bikes, beer, and a competitive round of Settlers of Catan.

Paulina Delgado
I am a second year transfer student in mechanical engineering with a general concentration from Santa Maria, California. I have been involved in many clubs over my time at Cal Poly, but found interest in this project to improve the overall quality and efficiency in craftsmen from Phillips 66. Outside of my academics and working full time, I enjoy traveling, hiking, and spending time with my two frenchies.
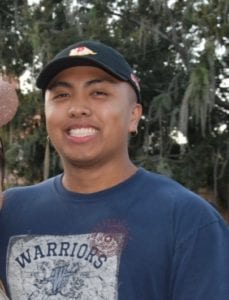
Mark Sunga
I am a fifth year mechanical engineering student with a general concentration from South San Francisco, California. Outside of school, I enjoy lifting, playing basketball, video games, and skating.
Acknowledgements
We would like to thank our advisor, Professor Lee McFarland, our contact, Jesus Gutierrez, and our sponsor, Phillips 66, for all their help through these challenging three quarters. In addition, we would like to thank all the instructors who have guided us through our time at Cal Poly.
Our Project's Digital Poster
Problem Definition
Phillips 66’s Santa Maria Refinery hires specialized craftsmen to perform maintenance on bolted flanged joints, shown below. Sometimes, the maintenance is not always completed to refinery-specific standards. Such errors can lead to costly repairs and can even compromise worker safety. Our group has been tasked to develop a test and a test stand to evaluate a craftsperson’s ability to properly assemble bolted flanged joints.
Flange Types
In order to test craftsmen’s knowledge of various pipefitting applications, three types of flanges were to be included on the test stand:
Flat Face
Raised Face
Ring Type Joint
For the flat face and raised face flanges, a gasket sits in between the flanges to create a leak-proof seal. With the ring type joint, a ring sits deep in the groove that is cut into the flange face. When the ring is compressed, a seal is made. In a setting such as a refinery, where hundreds or thousands of pipes might be running in different directions, flanges are crucial to connecting the pipes and ensuring leakage does not occur. In addition, flanges allow for ease of disassembly and maintenance to occur. However, when maintenance does occur, improper flange alignment and torque may lead to leaks, which can lead to delays in refinery operation.
Engineering Specifications
The test stand must meet the following:
- Test a variety of flanges – flat face, raised face, and ring type
- Test must be completed within 15-20 minutes
- Interface with a forklift for transportation around the refinery
The test stand must test the following:
- Correct part selection
- Proper lubrication
- Correct bolt tightening pattern
- Adequate flange alignment
- Torque
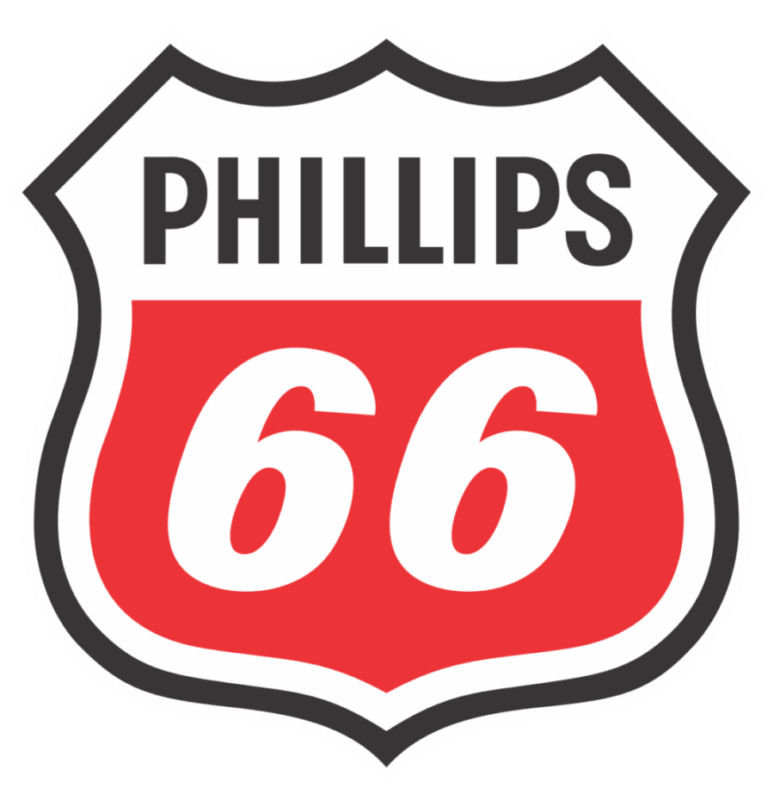
Our project was sponsored by the Phillips 66 Santa Maria Refinery.
Bolting Patterns
It was determined that a larger flange would be required to test knowledge of bolting patterns. Following proper bolting pattern is crucial to ensuring proper flange alignment and adequate sealing, A general “star” pattern should be followed. After examining flange sizes and weights at the refinery, it was determined that the largest flange that could be safely secured to the test stand was a 12-bolt flange.
As an example, the proper bolting pattern for a 12-bolt flange, taken from ASME PCC-1-2019, is shown below.
Design Concept
Shown below is an early concept model.
- Three flanges on left – flat, raised, and ring – aim to test correct part selection and familiarity with different flanges
- Larger flange (fourth from left) tests knowledge of bolting patterns
- Rightmost flange tests full assembly – bolting pattern, torque, and lubrication
First Design
Shown below is the first design iteration.
- Three small 4-bolt flanges – one of each type to test part selection
- One large 12-bolt flange to test tightening pattern
- One medium 8-bolt flange to test full assembly procedure
- Flanges oriented both horizontally and vertically
- Forklift pockets under table
Final Design
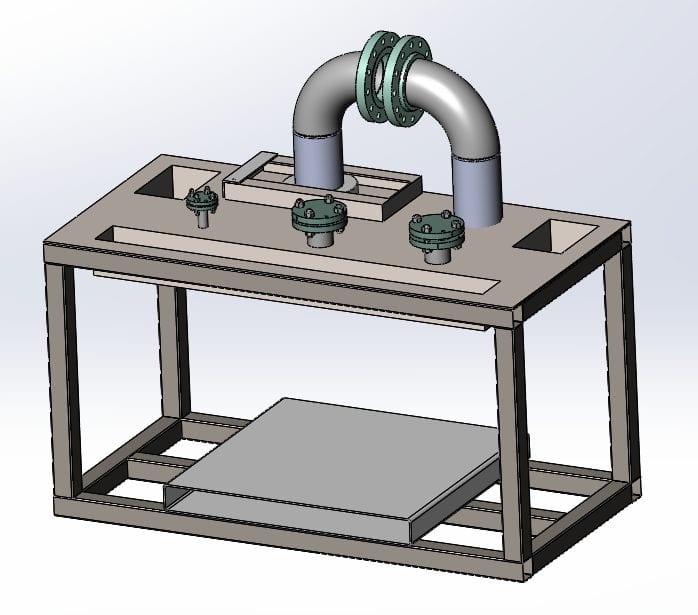
Final test stand design.
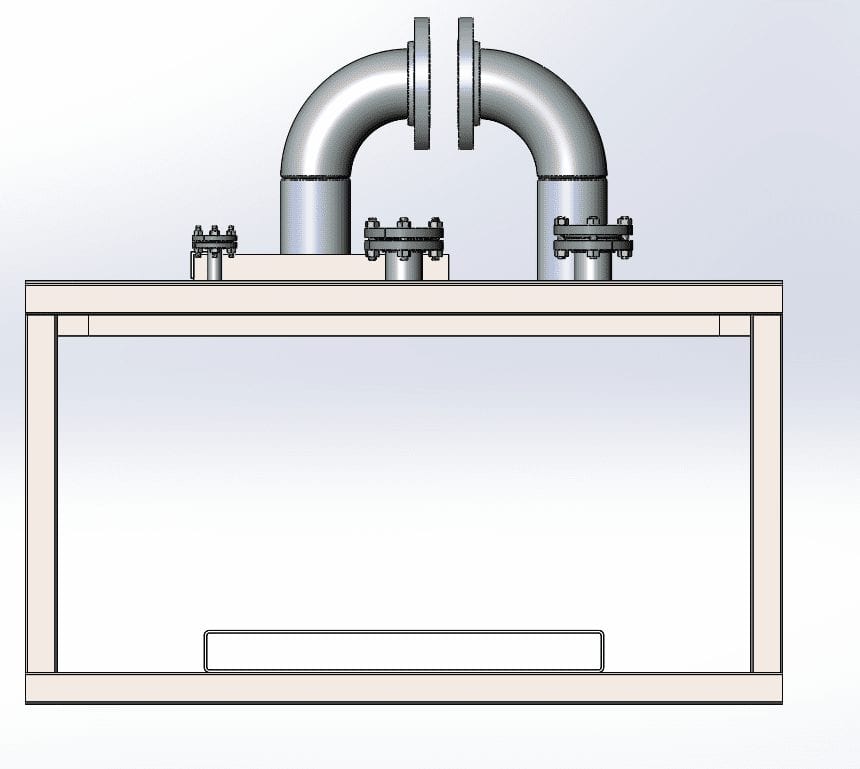
Front view of test stand.
Top view of test stand.
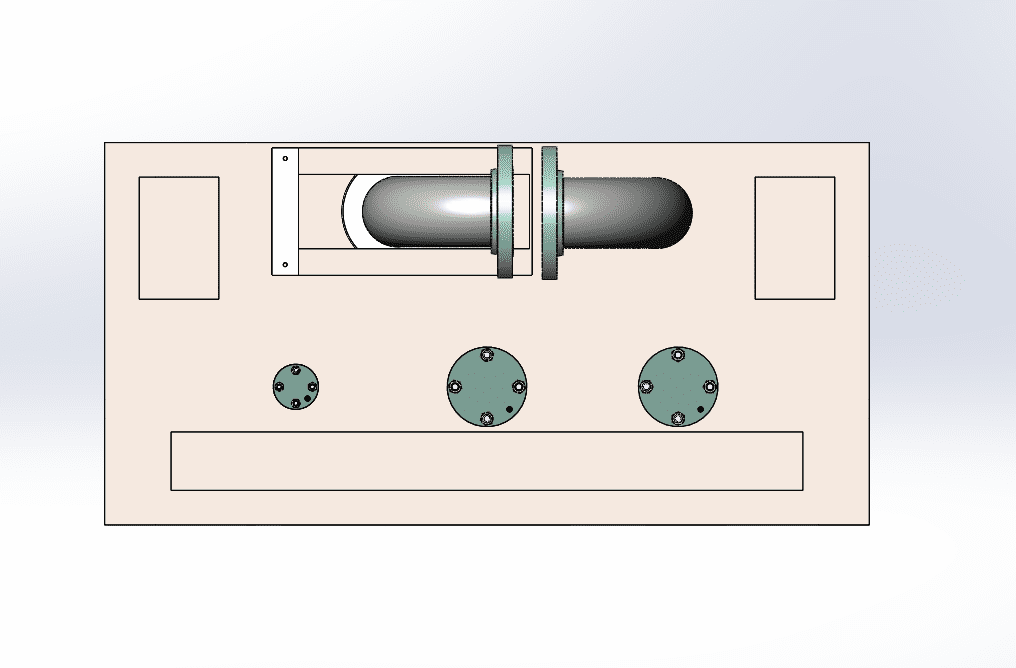
Changes from first design:
- Merged 8-bolt and 12-bolt tests into one 12-bolt test that tests for complete assembly, including bolt pattern and alignment
- Added a slot for one flange in large assembly to move – lead craftsmen to have to bring flanges together and simulate what they would encounter on-site
- Added trenches to hold parts
- Moved forklift attachment to bottom and extended pockets through entire stand
Final Testing Procedure
The final evaluation procedure is described below.
Small flange group test
- Craftsperson must read tag on each joint
- Craftsperson must then select the appropriate: mating flange, gasket, stud and nut, stud lubrication
Large flange test
- Craftsperson will be informed of what they are being evaluated for and what tools and information are available for use
- Craftsperson must assemble 12-bolt flange within remaining time
Evaluators will check:
- Correct mating distance between fixed flange and sliding flange, using the square tooth tool shown below
- Gasket alignment
- Correct bolting pattern is followed
- Proper torque value applied
Square tooth tool to be used by evaluator to check alignment.
References
- ASME PCC-1-2019