meet the Team
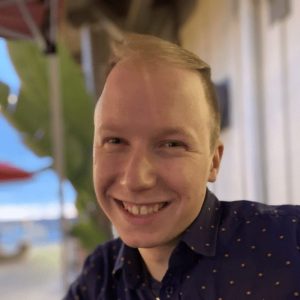
Kyle Ladtkow
Kyle is a 4th year Mechanical Engineering student, graduating with a concentration in Mechatronics this Spring. Over the past four years, he has worked on numerous formal design projects with the Quality of Life Plus Student Association (QL+SA) at Cal Poly. He served as the Technical Director for the 2020-2021 year for E.M.P.O.W.E.R. (formerly QL+SA). His past project and internship experience have enabled him to conduct the operations of the team to ensure the completion of the design. After graduation, he is moving to Boulder City, NV to work at CIMON Inc.
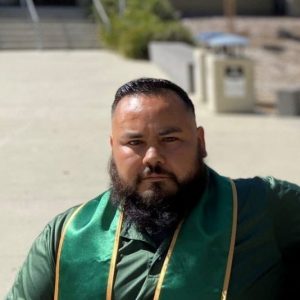
Javier Guerra
Javier is a Marine Veteran who transferred from MiraCosta Community College in Oceanside, Ca. He is a senior Mechanical Engineer student, graduating with a General Concentration this spring. Throughout his time in college he has participated in several clubs and organizations on campus. He was the President for the MiraCosta Community College Veterans Club 2016-2017. He was also part of the Cal Poly Robotics Club from 2018-2020 where he worked on the design and manufacturing of the Autonomous Golf Cart braking system. Javier has had 2 internships while at Cal Poly with Phillips 66 as a Reliability Engineer. After graduation, he is moving to the Bay Area to work for Phillips 66.
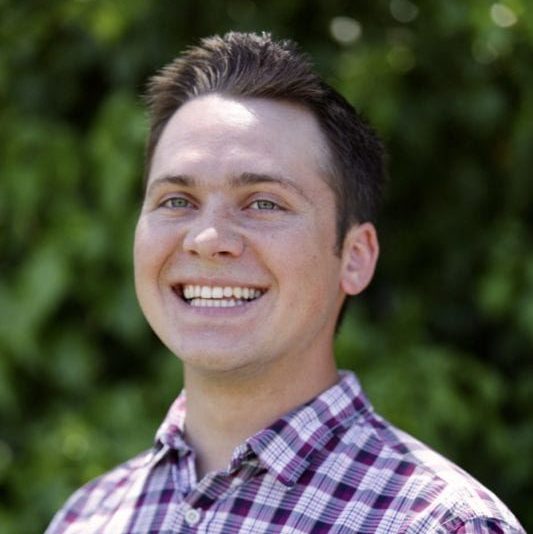
Ryan Heryford
Ryan is a 4th year Mechanical Engineering student, graduating with a concentration in Manufacturing this Spring. Throughout his college career he has been in multiple school clubs including Cal Poly Hyperloop and American Society of Mechanical Engineers (ASME). He has worked two internships with Northern California Power Agency (NCPA) in hydro power. After graduating, Ryan plans on thru-hiking the Pacific Crest Trail (PCT) and then searching for a career in power production.
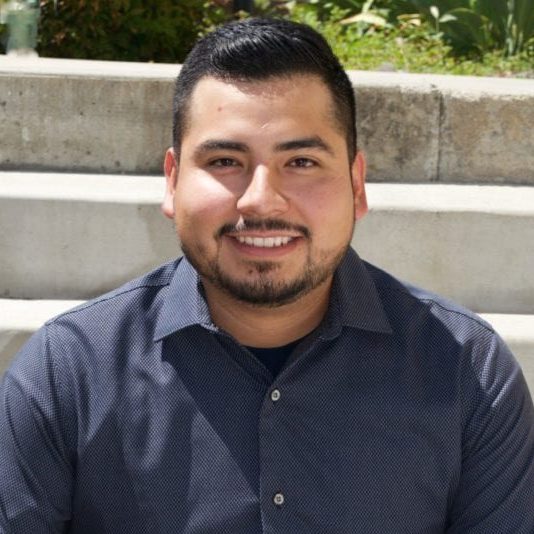
Jose Velazquez
Jose is a senior Mechanical Engineering student with a concentration in Manufacturing graduating this Spring. Throughout his college career, he has been involved in clubs like Society of Hispanic Professional Engineers (SHPE) and Society for the Advancement and Process Engineering (SAMPE). After graduation, Jose will be staying in the Central Coast, searching for a career in construction or HVAC.
Acknowledgements
Our team would like to thank our advisor, Sarah Harding, for her continued support and guidance over the past year. We would also like to thank all of the technicians at the Cal Poly Machine Shops for the hard work and technical knowledge they provided. Finally, we would like to thank our sponsor, Alejandro Jauregui, who was extremely kind and helpful throughout our time together.
project video
Our project's digital poster
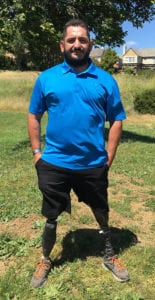
Alejandro Jauregui
Project Challenger
Problem Statement
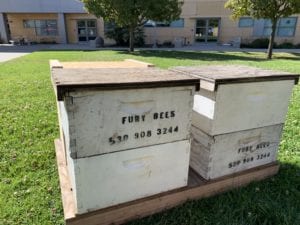
During his service in the US Army, Alejandro Jauregui lost both of his legs. He now has two prosthetic legs, which allow him to work as a commercial beekeeper. However, he has found that these prosthetics cause him significant pain and stress in his lower back, specifically when he inspects his bee boxes. Our goal was to design a device that would assist Mr. Jauregui when he lifts and rotates the top bee box in a stack for inspection.
Design Constraints
- Lift and rotate up to 80 lbs
- Rotate the box 90 degrees
- Fit between bee box pallets and bee box stacks
- Fit onto the back of Mr. Jauregui’s pickup truck
- Be as fast if not faster than his current process
- Be weather resistant
Design Concepts
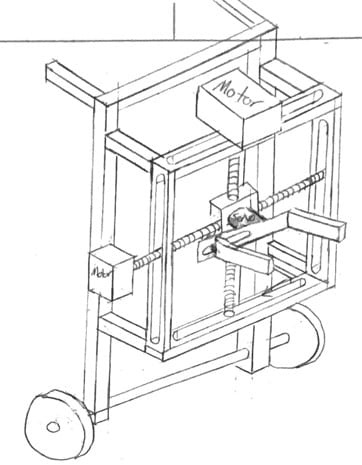
In this design, several motors and a pneumatic mechanism would work in tandem to grip, rotate, and move the top bee box. The main mechanism would be attached to a standard dolly.
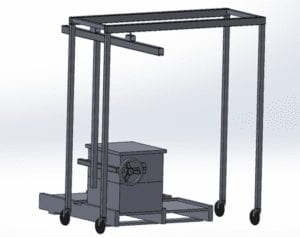
The “Moving Crane” would have wheeled over the entire pallet, rather than up to a bee box stack like all the dolly designs. Like a claw machine, it would pick up and rotate a top bee box before putting it down and moving to the next stack on the pallet.
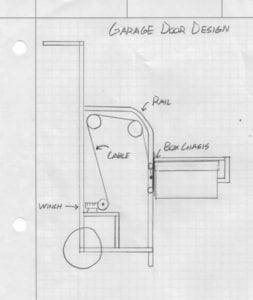
Similar to the “CNC Dolly” design, the “Garage Door” would have used a motor to lift and rotate the box. However, this design would have only required one motor in the form of a winch, pulling the box chassis up a curved track, similar to that of a garage door.
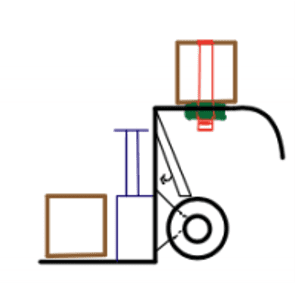
Unlike the other designs, the rotation of the “Broken Dolly” design would have come from a hinge in the dolly frame itself. In the original iteration, a linear actuator or pneumatic mechanism would have also provided a lifting action to properly get the box out of the way.
Chosen Design
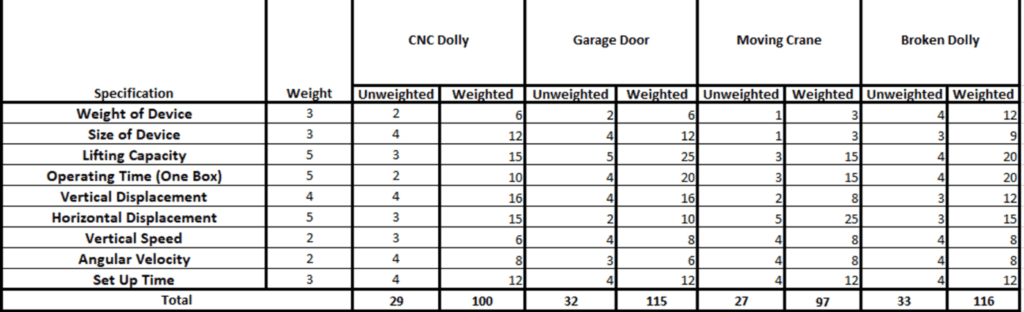
Weighing several factors and specifications, we decided to move forward with a modified version of the “Broken Dolly” design.
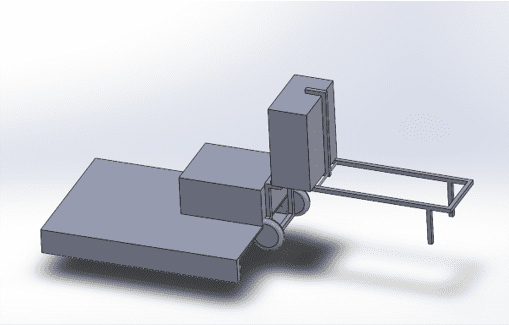
Design Analysis
Dynamic model
To ensure the “Broken Dolly” would work, we created a dynamic model of the system. The model was designed to accommodate a maximum bee box weight of 80 lbs. We used it to determine the required force from Mr. Jauregui for four cases:
Case 1: Mr. Jauregui pulls the upper dolly from rest in the upright position.
$$F_{required} = 22.7 lbs$$
Case 2: Mr. Jauregui lowers the box/upper dolly 90 degrees.
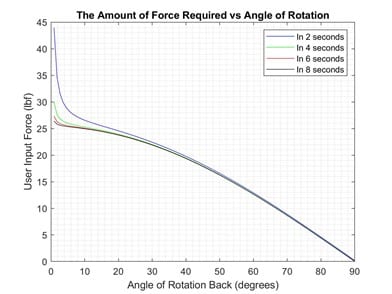
Case 3: Mr. Jauregui pulls the upper dolly from rest in the lowered position.
$$F_{required} = 11 lbs$$
Case 4: Mr. Jauregui raises the box/upper dolly 90 degrees.
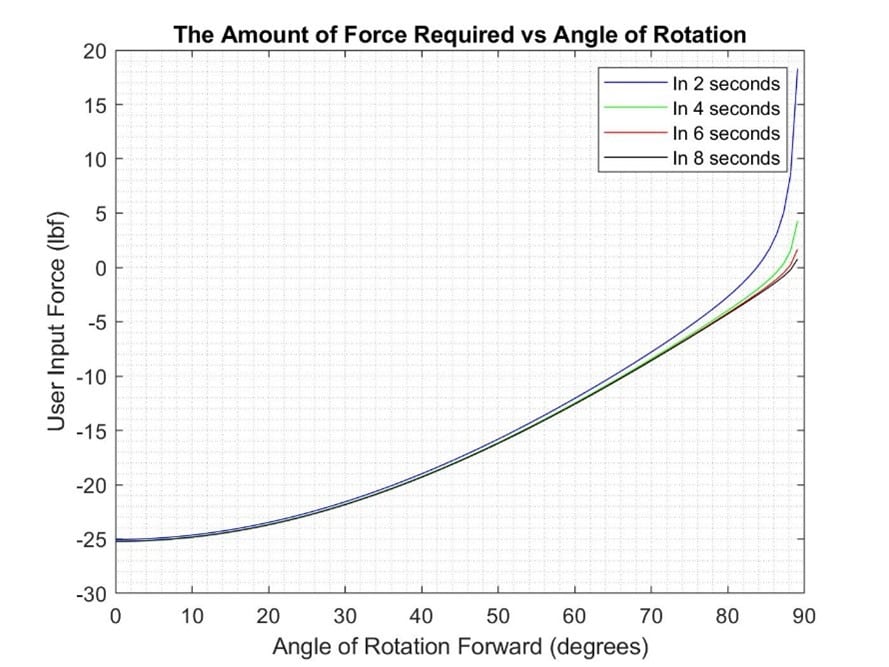
Stress analysis
To ensure that the “Broken Dolly” could withstand the stresses of its operation, we conducted several stress analyses. The most critical was the attachment arm, which was almost entirely custom built. Many finite element analysis (FEA) simulations were conducted on a simplified model of the arm and the rest of the device to verify its safety.
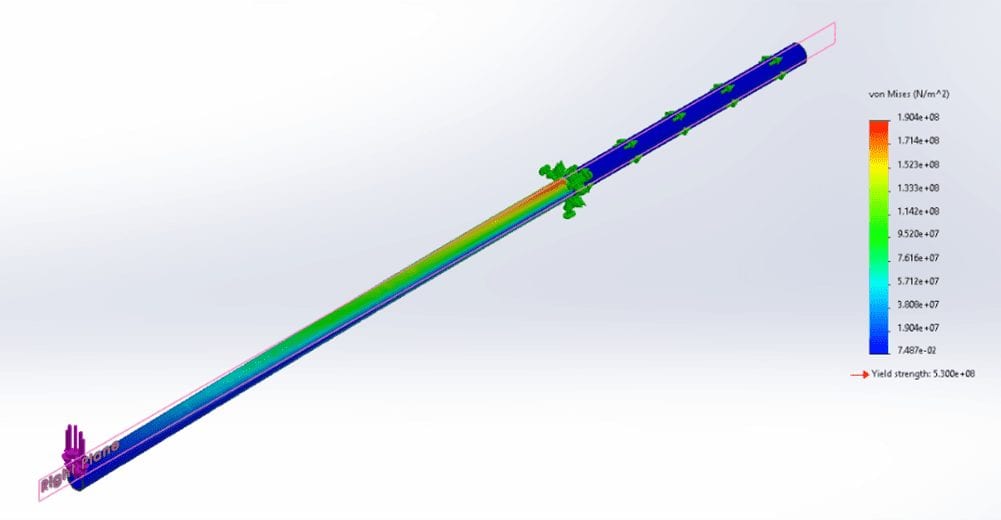
Manufacturing
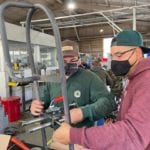
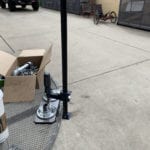
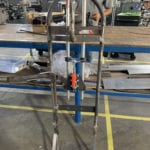
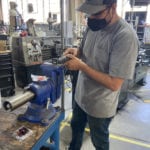
Design Verification
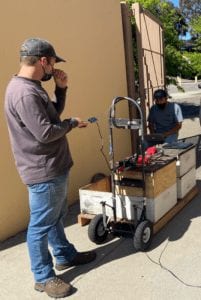
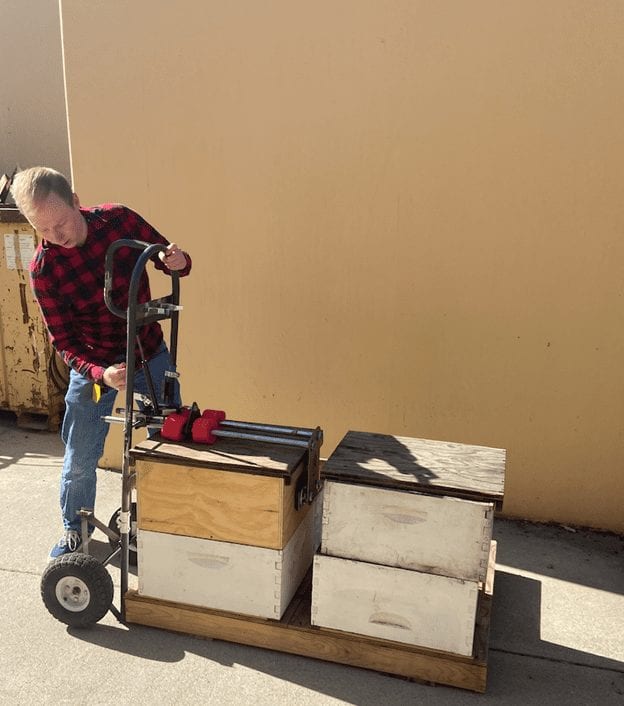
We verified that our device worked mostly by running through its operation like Mr. Jauregui would. We used authentic bee boxes and corresponding pallet from his farm. The boxes were loaded with weights up to and above our maximum weight of 80 lbs. We measured time to set up, weight of the device, required forces, etc.
Final Design
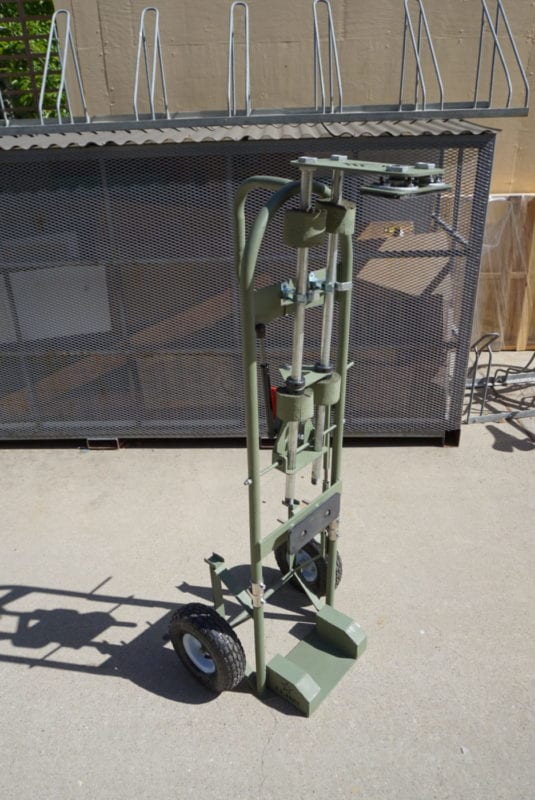
Weight: 50.4 lbs
Average Setup Time: <6 s
Average Time to Rotate Back Safely: <5 s
Rubber Pad Static Friction Coefficient: 0.954
Average Case 1 Required Pull Force: 34.76 lbs
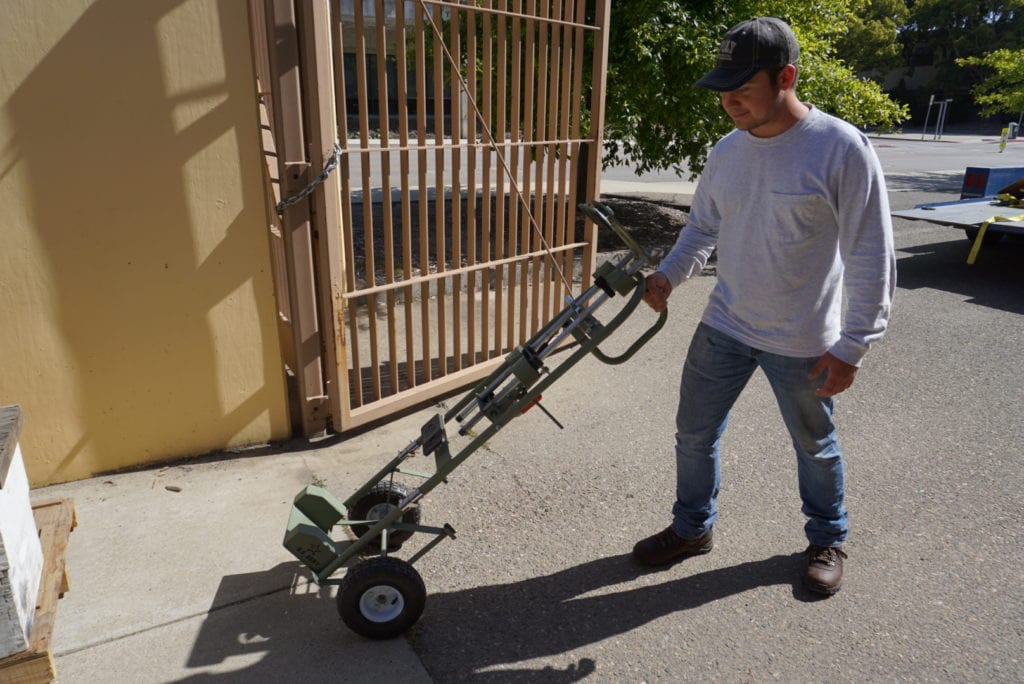
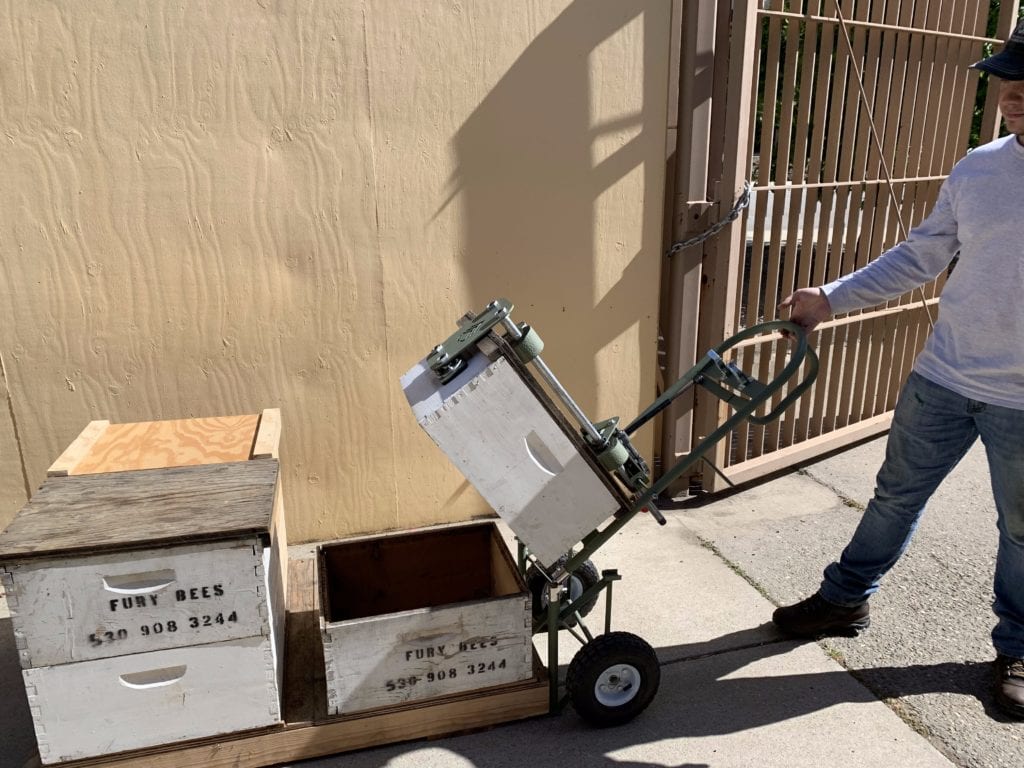
Future Applications
During our preliminary research, we weren’t able to find another device on the market that both lifted and rotated bee boxes. The design of the Beekeeper Assist gives it the potential to be useful to beekeepers of all kinds, not just Mr. Jauregui. While it took us a while to fully manufacture it, the design is straightforward enough that, with some modifications, the device could easily be manufactured on a larger scale. In addition, this device could be used for any other box lifting and rotating operations similar to beekeeping.
Recommendations
Improvements to the design if we were to redesign it:
- Powder coat instead of paint
- Custom mold urethane spacers to keep the lid on rather than foam
- Use some sort of compliant material like rubber or foam to bridge the gap between the forks and the pallet
- Use a stronger damper for the rotation blocker
- Create a cover for the device so that it can be better left outside