Our Team
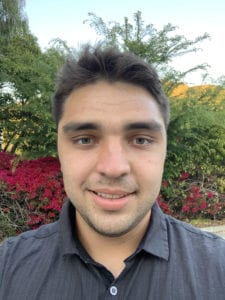
Jimmy Algeo
Jimmy will be graduating with a Bachelor’s degree in Industrial Engineering during Spring 2021 commencement. As part of his major courses, he is interested in programming and data analytics. He has worked with companies to improve workflow and standardize numerous facilities in course projects. He is hoping to earn industry experience by securing a job or internship in the Santa Barbara area.
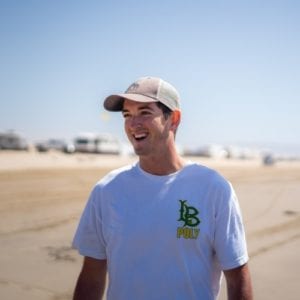
Peter Bishop
Peter Bishop is a graduating Industrial Engineering student at Cal Poly, upon completion of his senior year, he will be staying in the central coast area of California enjoying an internship at Atlas Copco Mafi-Trench in a process improvement position. Throughout this senior project, Peter learned a lot about project management, risk management, and impact analysis. In the future, Peter plans on pursuing an Engineering Management Master’s degree at Cal Poly to stay on the beautiful central coast.
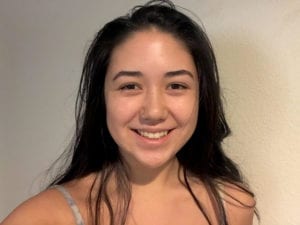
Maria Brown
Maria is a fourth year Industrial Engineering student graduating this spring. She has been interning with Lam for the last year as a Business Function Intern. Her goal is to get into Software Project Management particularly in blockchain technologies. She hopes to stay in SLO for another year and work remotely on the Central Coast
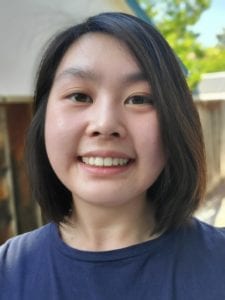
Elizabeth Yuen
Elizabeth Yuen is working towards a Bachelor of Science degree in Industrial Engineering from California Polytechnic State University, San Luis Obispo class of 2021. Throughout her college career, she has participated in various cultural club events. She is a part of her college’s System Optimization Club. She has partnered with companies on projects related to warehouse optimization to process standardization. She is interested in data analytics and project management. She is currently working in research and development, getting industry experience.
Acknowledgements
We thank Carla Bietz and Hope Caronan for taking in Cal Poly interns to work on the MOMS Project. Their assistance and mentorship has helped us greatly in understanding the project planning and Business Process Reengineering (BPR) process. We would also like to thank Tali Freed and Liz Schlemer for their cooperation and professional knowledge that we used throughout this project.
Our Project's Digital Poster
Problem Description
Lam Research does not have the flexibility to manufacture their equipment in other sites. Their four main manufacturing sites’ business processes are not aligned to support this flexible manufacturing.
Objectives
1. Improved visibility of performance data to enhance productivity, quality, and labor efficiency through the new manufacturing operations management system (MOMS).
2. Aligned business processes between four facilities
Final Design
Our final process flow combines all similar business processes in Assembly and standardizes them with the Best Known Methods (BKMs). Our three implementations are the use of RFID module tracking, digital tools connected to MOMS, and tablets for work instructions and dashboards. These solutions would be implemented depending on each factory’s assembly process and production needs. All of the factories would collect metrics to track these implementations.
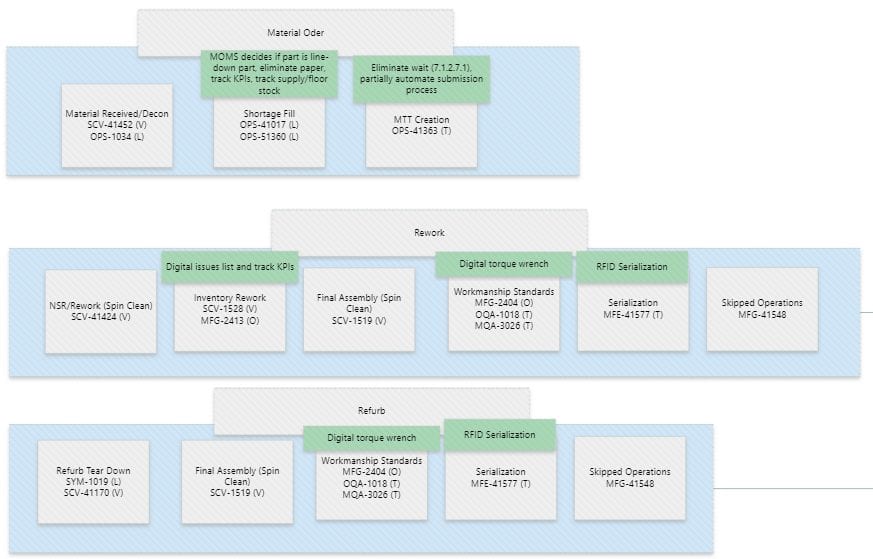
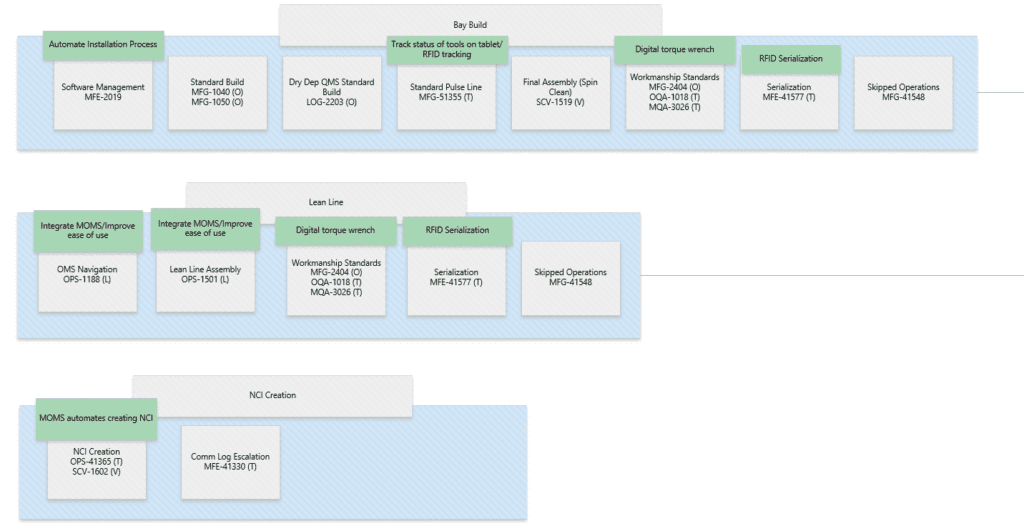
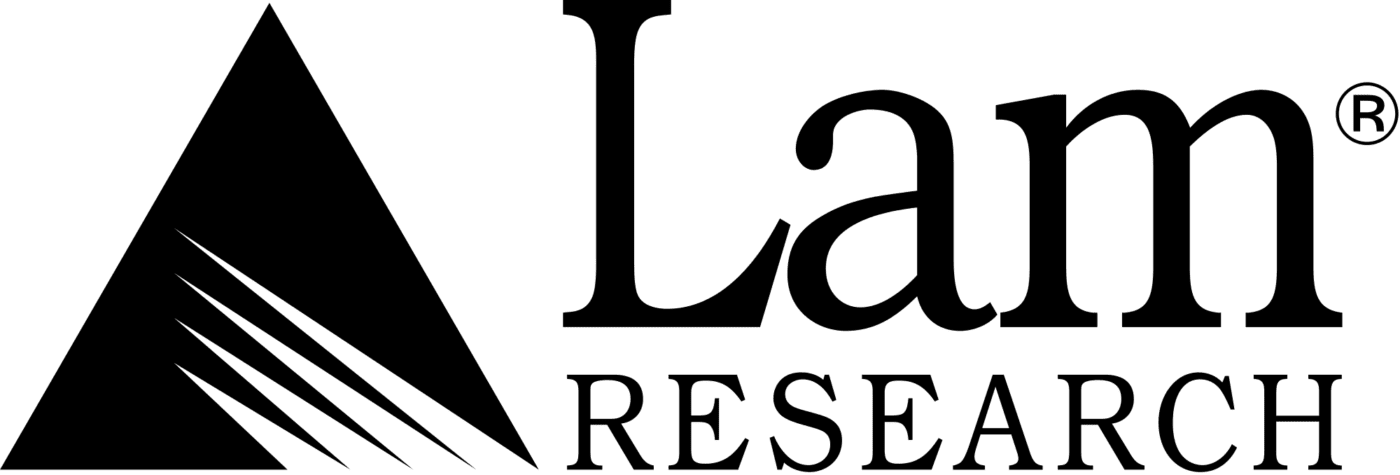
This project is sponsored by Lam Research
Analysis
The current business processes were organized in order to understand the process flows that each factory follows. From these process flows, there were similar procedures that could be used as one standardized procedure for all four sites. Certain factories still had manual processes integrated that could be automated. Workmanship standards were not emphasized. Lean line and pulse line builds distinguished factories from one another which did not allow for complete standardization.
Development
To create the future state set of standardized process documents, we merged, deleted, or similar documents. Of the new document set, we determined which processes were non-value added (NVA) and could be optimized. The technological solutions aimed to improve key metrics in the processes.
Conclusions
Tablets:
Tualatin wet manufacturing, Villach and Osan tracking and work instructions
Digital Tools:
Upgrade to MES connected digital tools at all locations except Livermore
RFID Tracking:
Strongly recommend for Villach and Osan, pilot program used at Tualatin
Validation
Our solution validation came through interviews with subject matter experts (SMEs) familiar with each factory as well as each ERP vendor to ensure compatibility with Lam’s future MOMS.
Implementation Plan
Pilot testing phase (1-2 months)
- Factors to consider:
- Supervisor judgement
- Training time
- Cost of implementation/testing
- Performance during ramp times
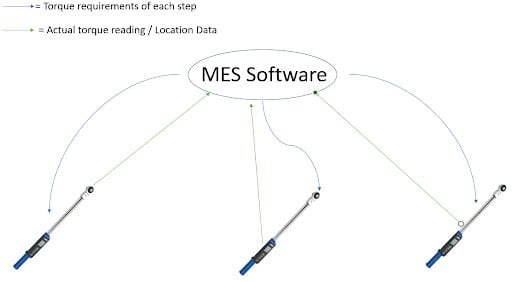
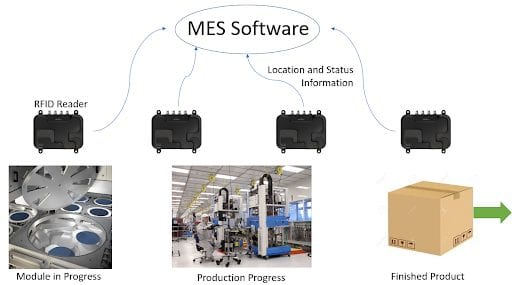
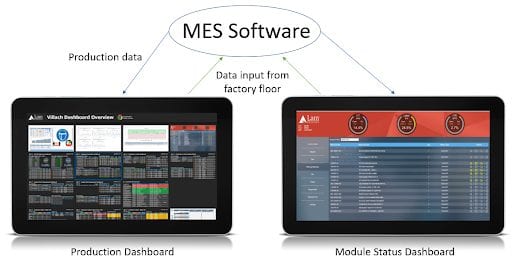