The Team
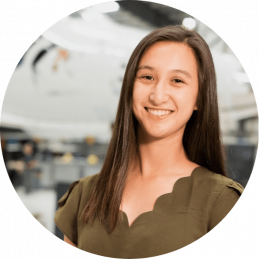
Allyse Birken
Allyse is a materials engineering student graduating in June 2021. Her interests include electric vehicles, motorsports, music, and photography.
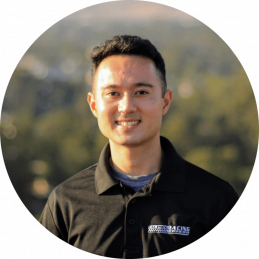
Derek Noel
Derek is a materials engineering student graduating in December 2021. His interests include metallurgy, automotive engineering, wilderness backpacking, and motorsports.
Acknowledgements
Thank you to everyone who supported our project! Thank you to Bryce Simmons, Matthew Williams, Greg Kayser (Aerojet Rocketdyne) and Paul Gradl (NASA) for sponsoring this project. Additionally, thank you to Dr. Blair London (California Polytechnic State University – San Luis Obispo, Materials Engineering Dept) for providing guidance as our project advisor. Thank you to Eric Beaton (California Polytechnic State University – San Luis Obispo, Materials Engineering) and the Materials Engineering department. Finally, thank you to Louis Gerny, Aditya Garg, and Bryan Neill (California Polytechnic State University – San Luis Obispo, Machine Shops) for machining sample specimens.
Our Project's Digital Poster
Background
Aerojet Rocketdyne is the premier propulsion system supplier for the space and defense industry. One of their most notable engines is the RS-25 engine, otherwise known as the Space Shuttle main engine. A new generation of these RS-25 engines are currently contracted to be used on NASA’s Space Launch System (SLS) rocket. Aerojet Rocketdyne is investigating the use of additive manufacturing processes, such as directed energy deposition (DED), to produce components such as nozzle structural jackets and manifolds for the RS-25 at a lower cost and lead time than with traditional manufacturing methods.
Problem Statement
Aerojet Rocketdyne is investigating the use DED to produce parts such as nozzle structural jackets and manifolds using two alloys of interest, JBK-75 and NASA-HR-1. These alloys are fully austenitic, age-hardenable, Fe-Ni-base superalloys, and possess high strength, oxidation resistance, and hydrogen embrittlement resistance at high temperatures. Because these alloys are age-hardenable, heat treatment is required to reach the high strength levels required for the design of these components. Aerojet Rocketdyne has asked the senior project team to characterize these alloys’ response to heat treatment after additive processing.
As-Built Characterization
JBK-75
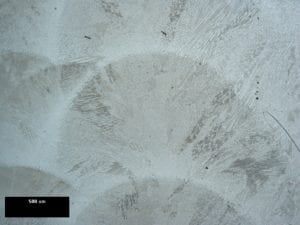
Etch reveals dendritic growth in the direction of the melt pool.
50X magnification
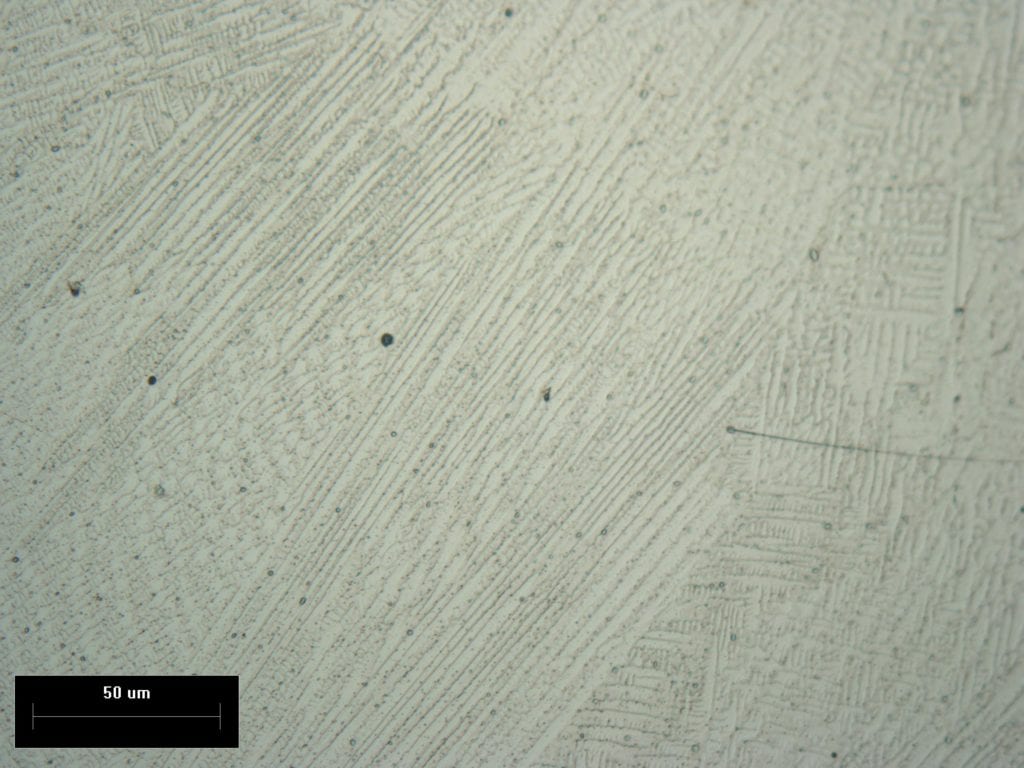
Columnar, dendritic microstructure in the as-built condition due to rapid solidification during DED.
500X magnification
NASA-HR-1
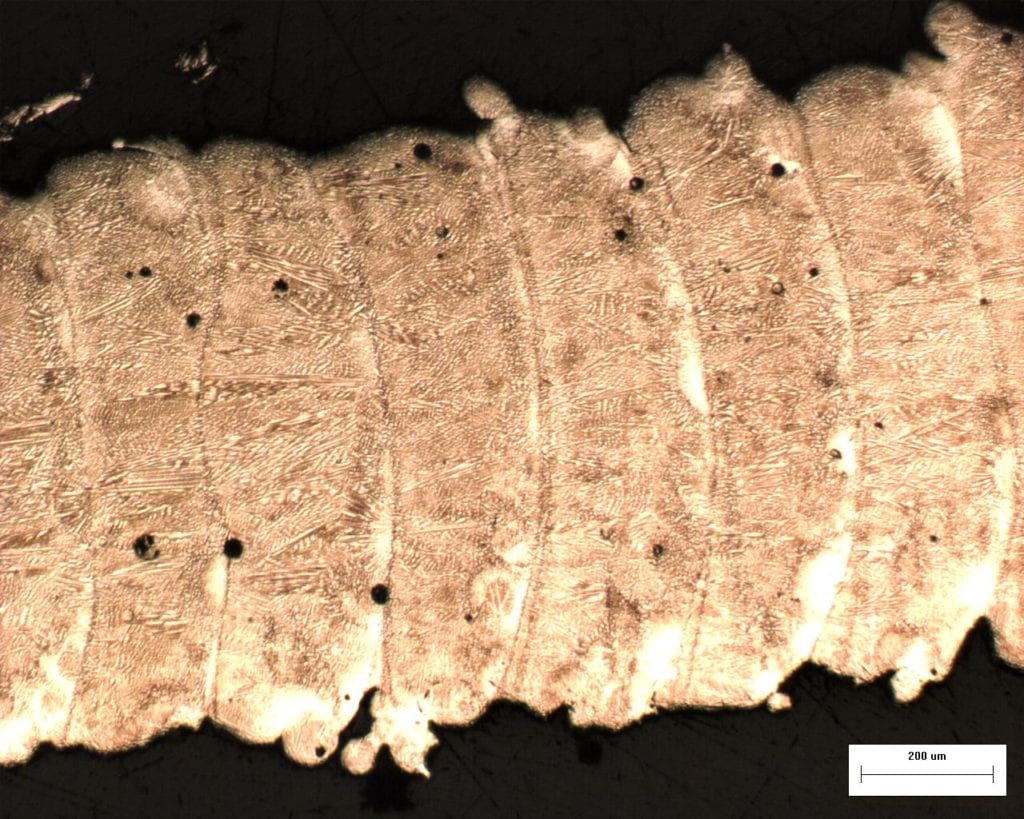
High degree of porosity and poor surface finish observed for as-built NASA-HR-1 material.
50X magnification
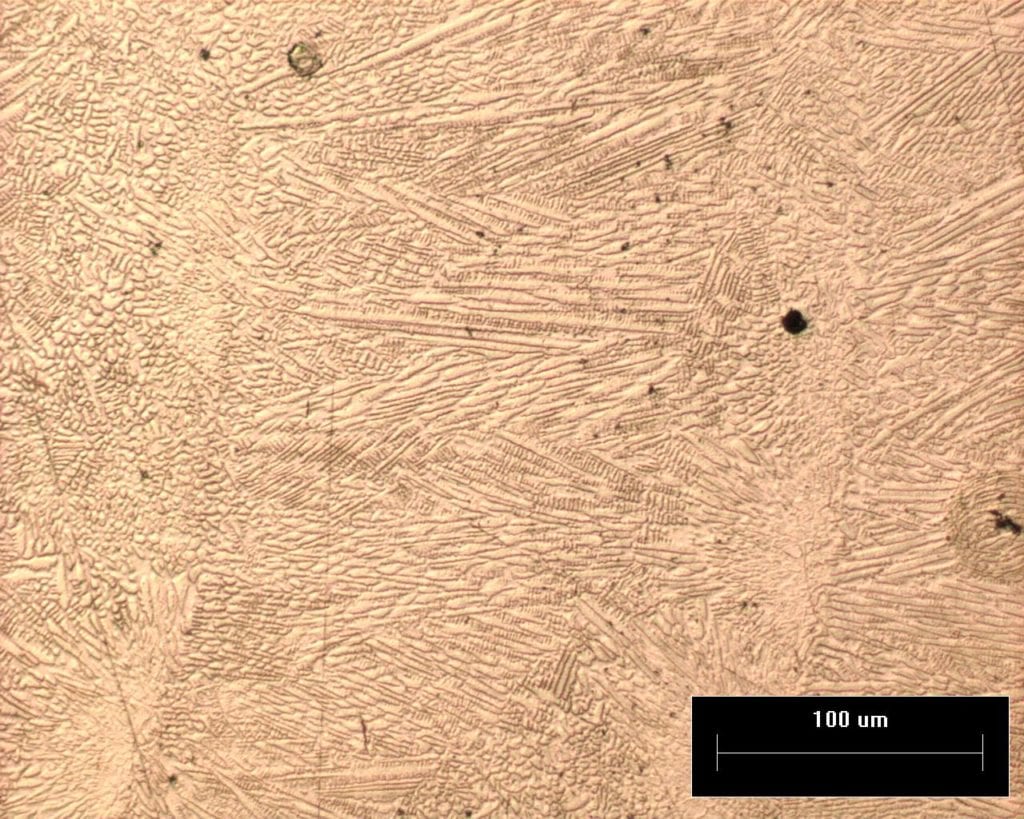
Columnar, dendritic, as-built microstructure observed, similar to JBK-75.
500X magnification
Sample Preparation
JBK-75
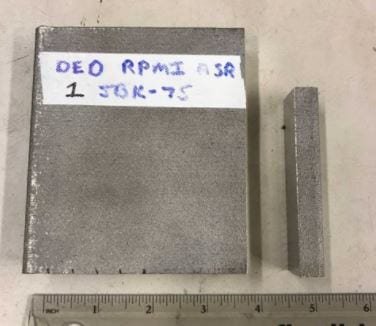
DED JBK-75 received as ~4″ x 4.5″ x 0.8″ blocks.
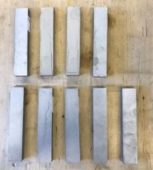
JBK-75 blocks waterjet into bars.
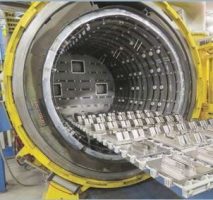
JBK-75 bars sent to Aerojet Rocketdyne for vacuum heat treatment.
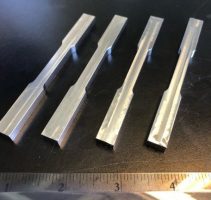
Heat treated JBK-75 bars CNC machined into ASTM E8 subsize tensile specimens.
NASA-HR-1
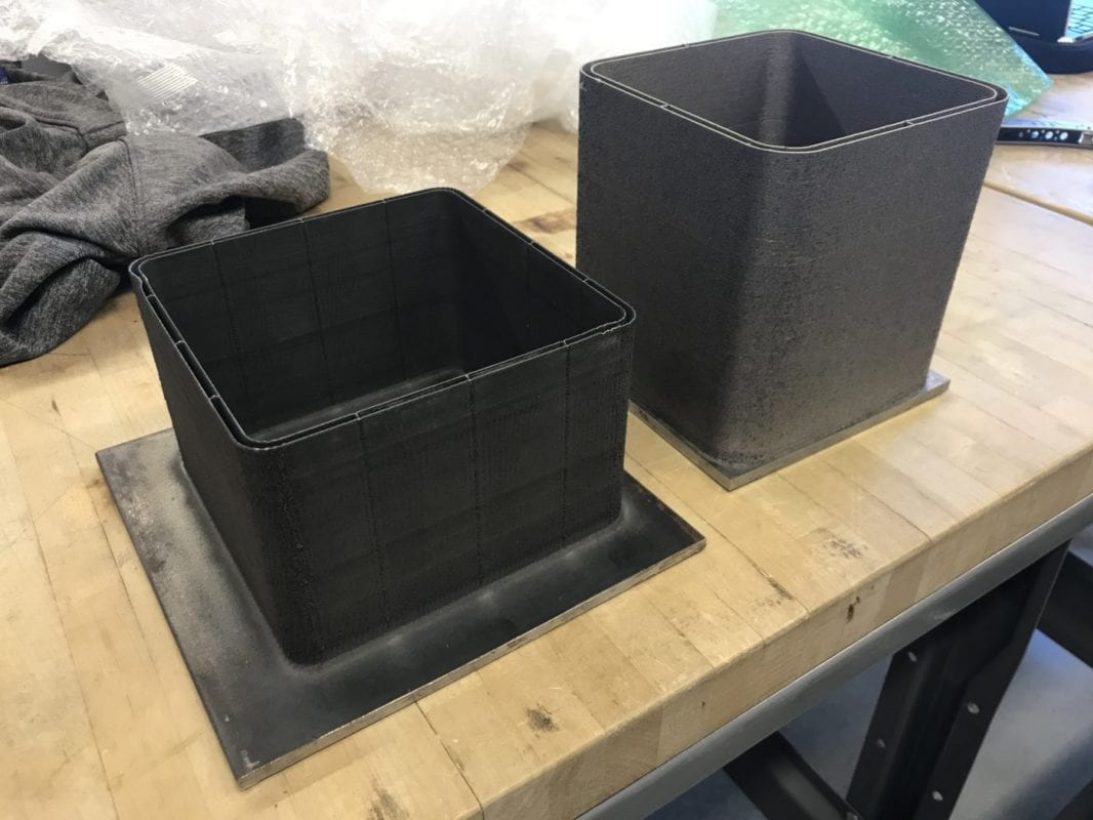
Two as-built NASA-HR-1 sample boxes.
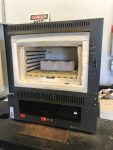
Panels stress relieved prior to waterjetting (1950F for 2 h)
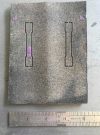
Tensile specimens waterjet out of panels (ASTM E8 subsize).
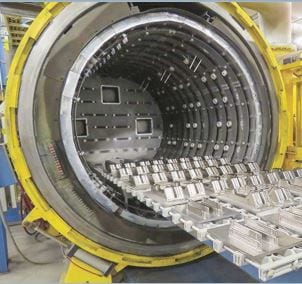
NASA-HR-1 samples sent to Aerojet Rocketdyne for vacuum heat treatment.
Two as-built NASA-HR-1 samples were received in the form of thin-walled boxes attached to the build plate. Each box was produced with different processing parameters and were treated independently throughout the project. Throughout the following sections, the box with the darker surface finish will be referred to as Box 1 NASA-HR-1 and the box with the lighter surface finish will be referred to as Box 2 NASA-HR-1.
This project is sponsored by
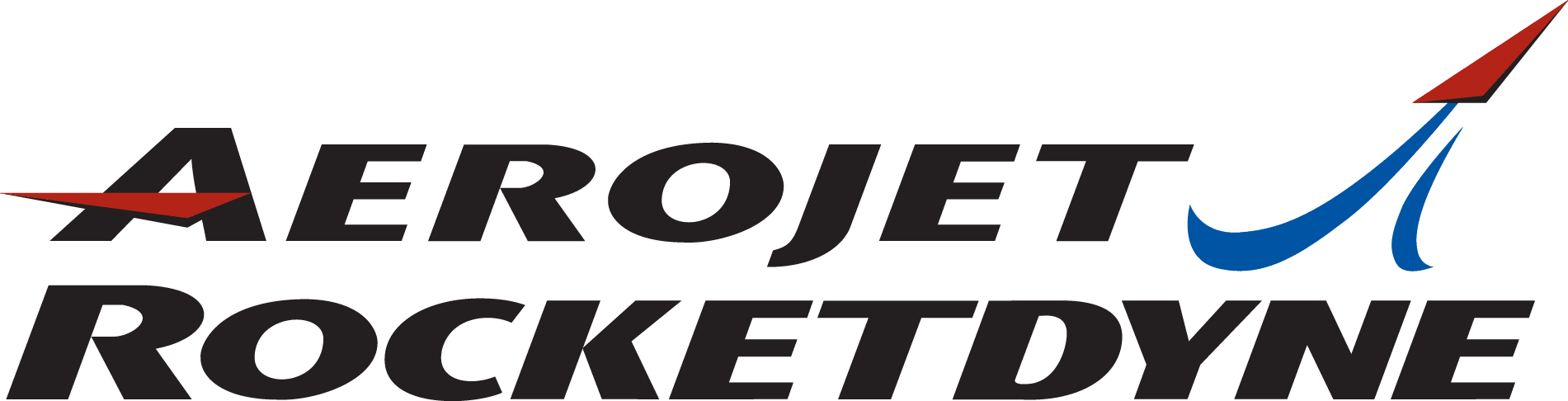
Heat Treatments
JBK-75
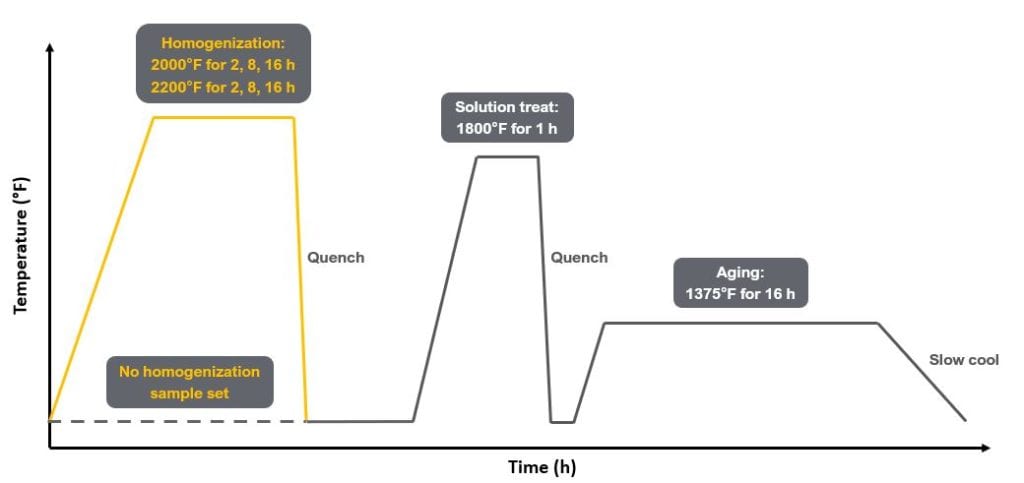
JBK-75 samples were homogenized at various times and temperatures to evaluate the effect of varying homogenization parameters on mechanical properties and microstructure in the age-hardened condition. All samples were solution treated and aged after homogenization to the same parameters.
NASA-HR-1
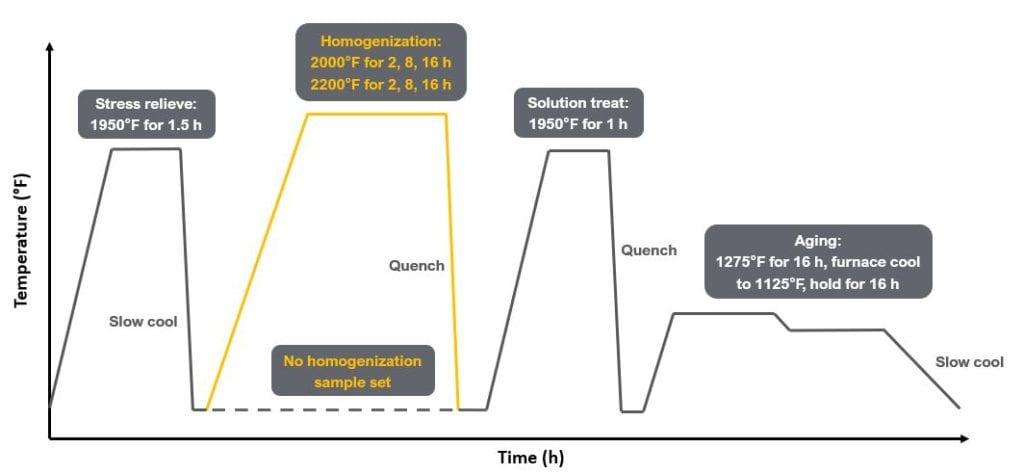
NASA-HR-1 samples were homogenized for the same set of temperatures and times as the JBK-75 samples. HR-1 panels were stress relieved prior to being cut out into tensile specimens to prevent warpage. The solution treat and aging treatments were given to the team by NASA.
Tensile Testing Results
JBK-75
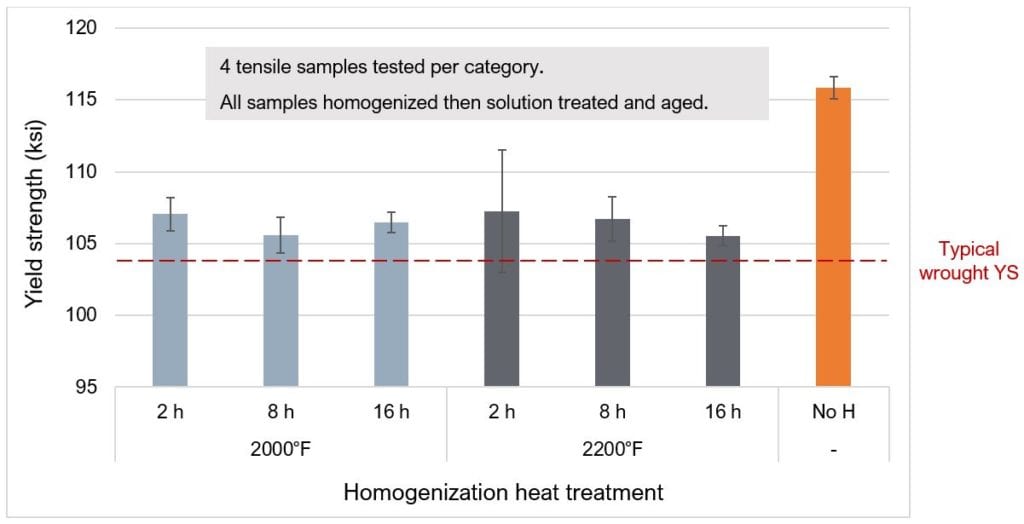
Yield strength summary for JBK-75. The samples that were not homogenized, only solution treated and aged, exhibited the highest yield strength. Among the homogenized samples, there was no significant variation in yield strength.
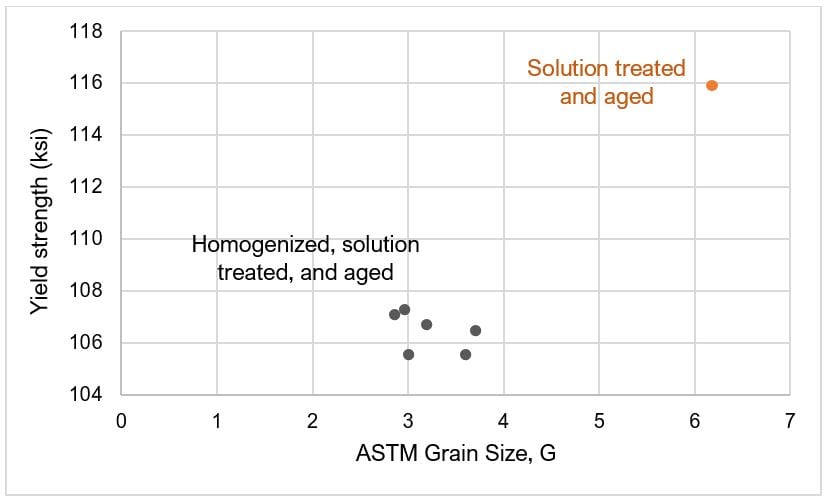
This difference in yield strength could possibly be attributed to grain size, as the non-homogenized samples exhibited a finer grain size than the homogenized samples, since the homogenized samples were held at high temperature for longer times.
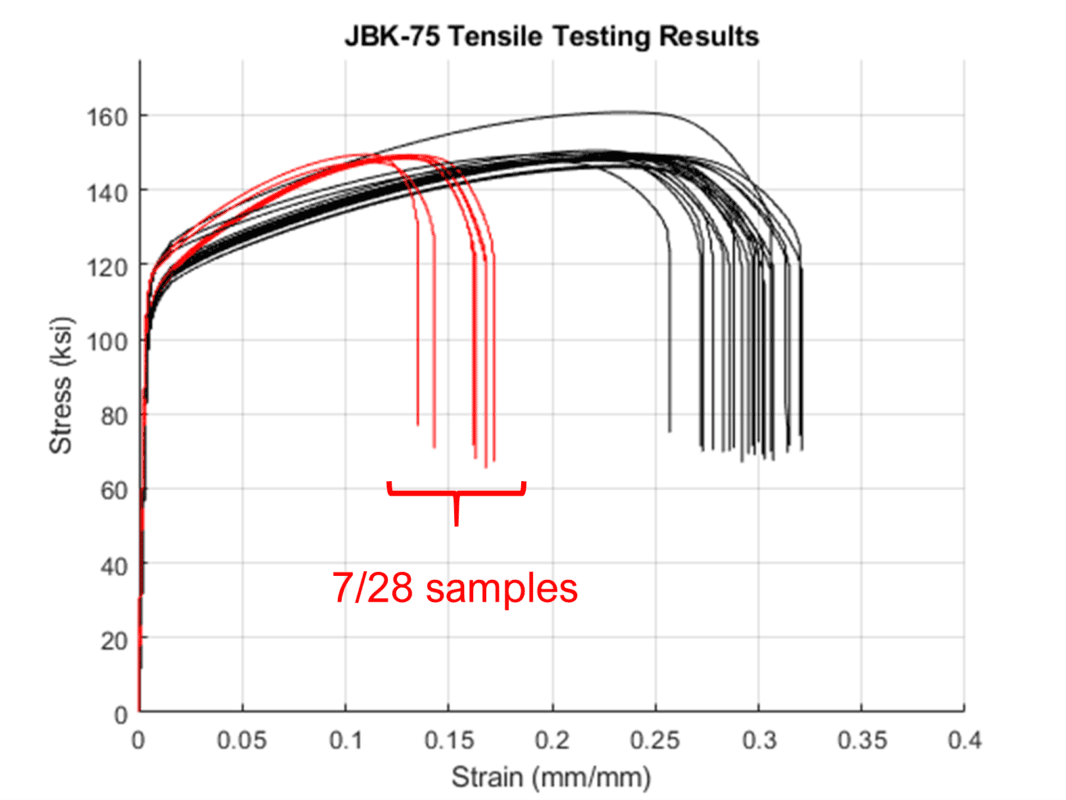
Stress-strain curves for heat treated JBK-75 samples. 7/28 samples exhibited lower ductility than expected.
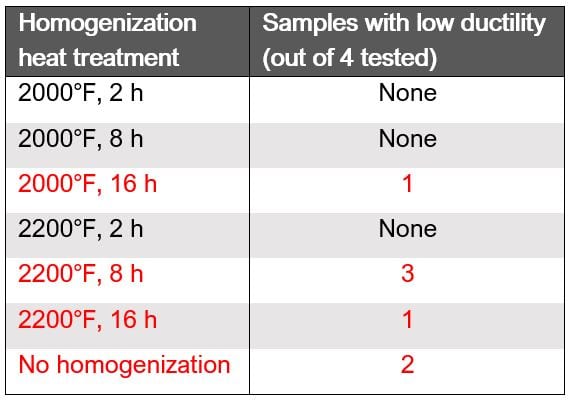
Samples with low ductility are shown in this table by homogenization heat treatment.
NASA-HR-1
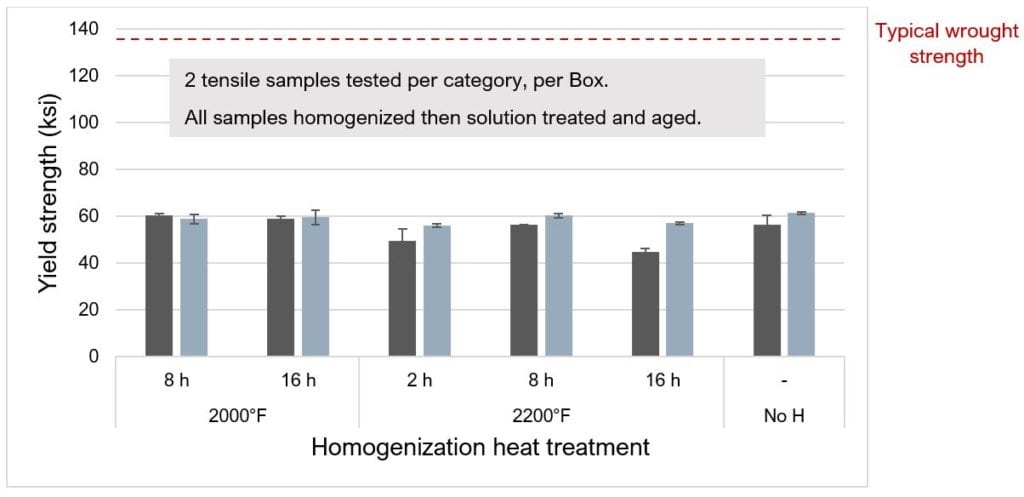
The summary of yield strengths for NASA-HR-1 samples shows that all samples fell far below the typical yield strength of wrought NASA-HR-1, and there was no relationship between homogenization time and yield strength for either Box. Box 1 is denoted by the dark bars, and Box 2 is denoted by the light bars. Notice that there are no significant differences in yield strength between Box 1 and Box 2.
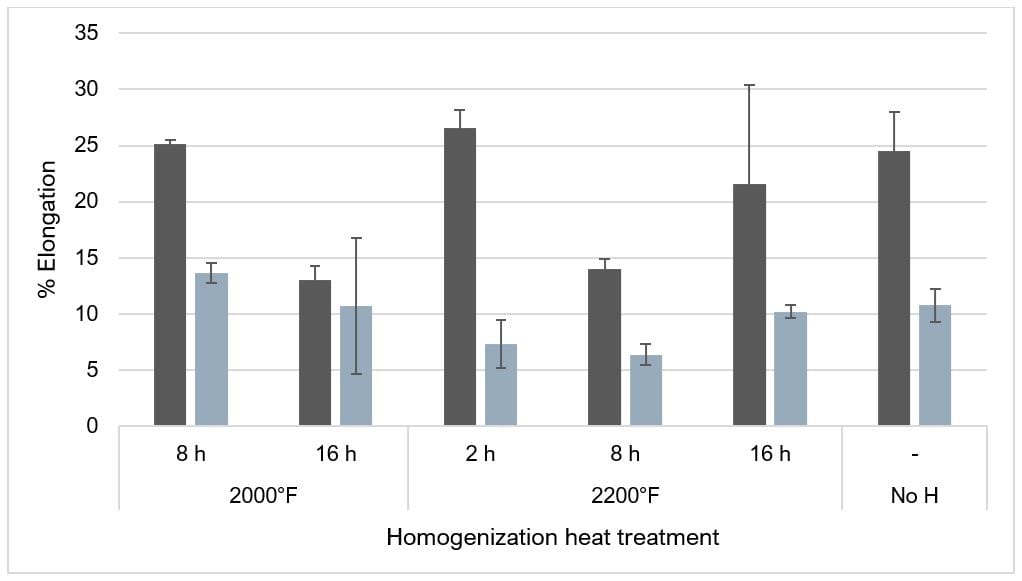
There was a significant difference in ductility between Box 1 and 2, where Box 2 had substantially lower ductility for nearly all samples. The reason for this can be shown by the as-built characterization of the NASA-HR-1 samples, where Box 2 showed a substantially higher degree of porosity and a higher surface roughness that could potentially have a notch effect during a tensile test.
Metallography
Homogenized
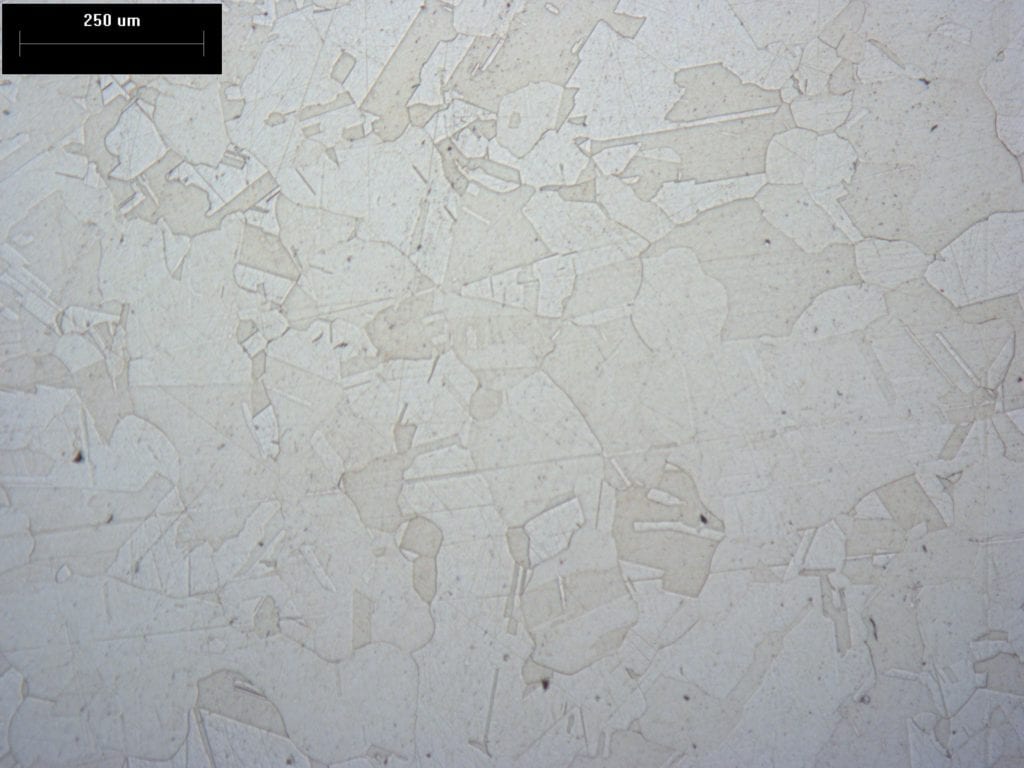
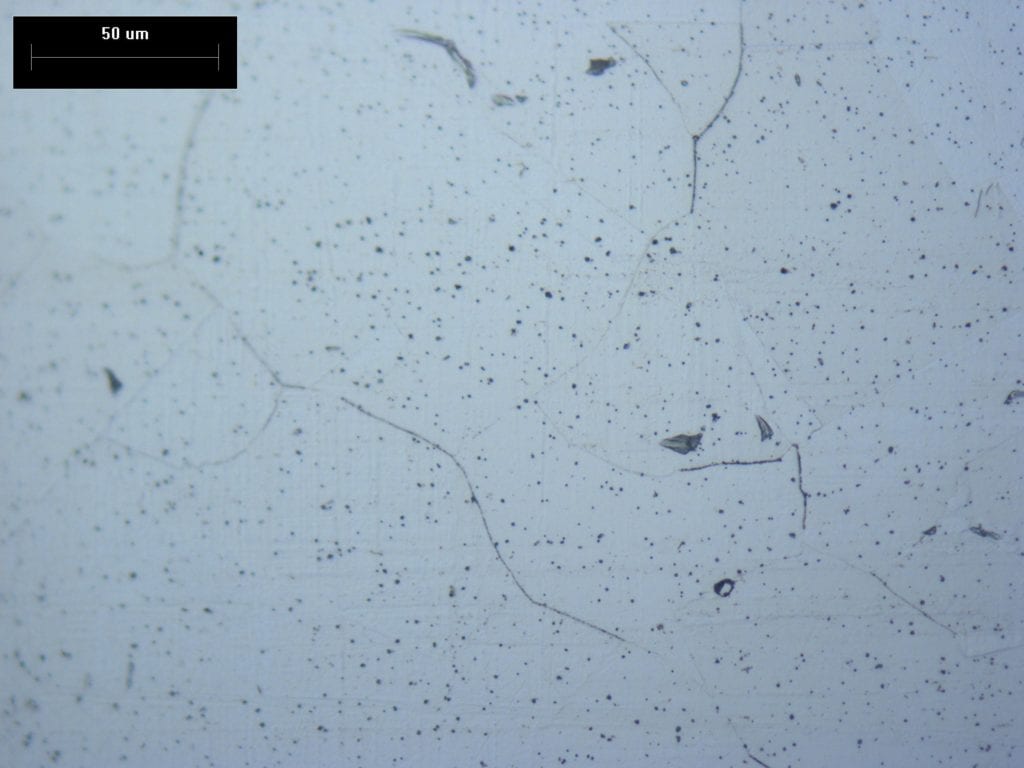
All JBK-75 homogenized samples fully recrystallized and all micro-segregation was eliminated. However, secondary phases, either carbides or eta phase, were observed along some of the grain boundaries. This is a possible cause for some samples having low ductility, but this was not confirmed and is an item for future work.
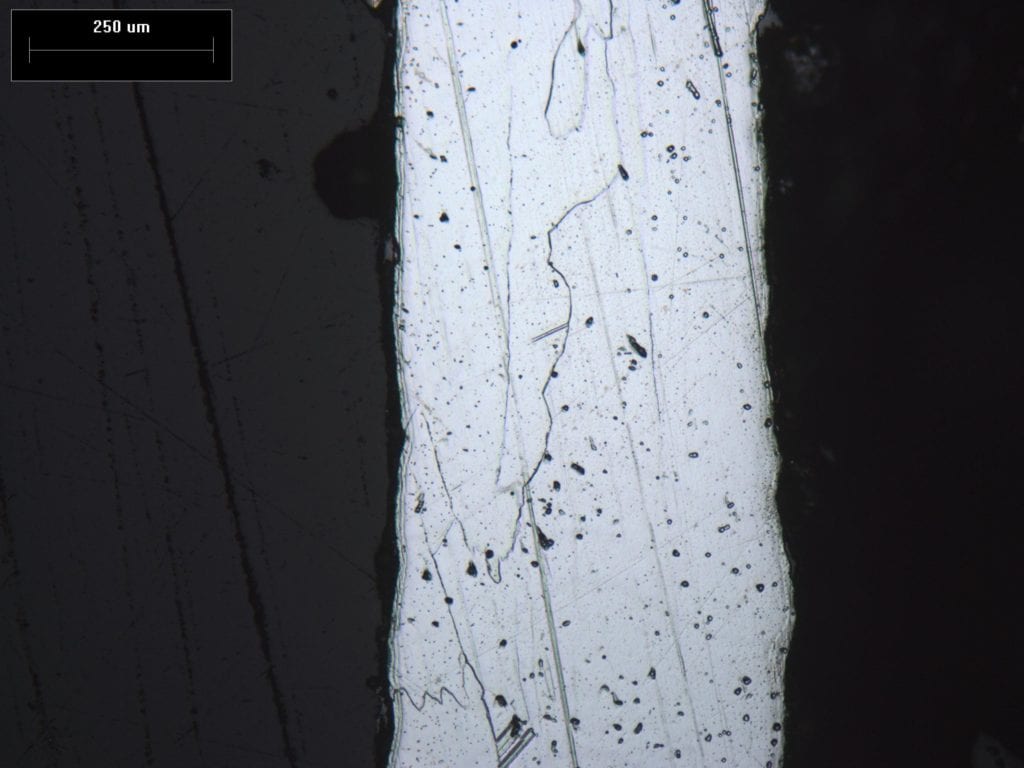
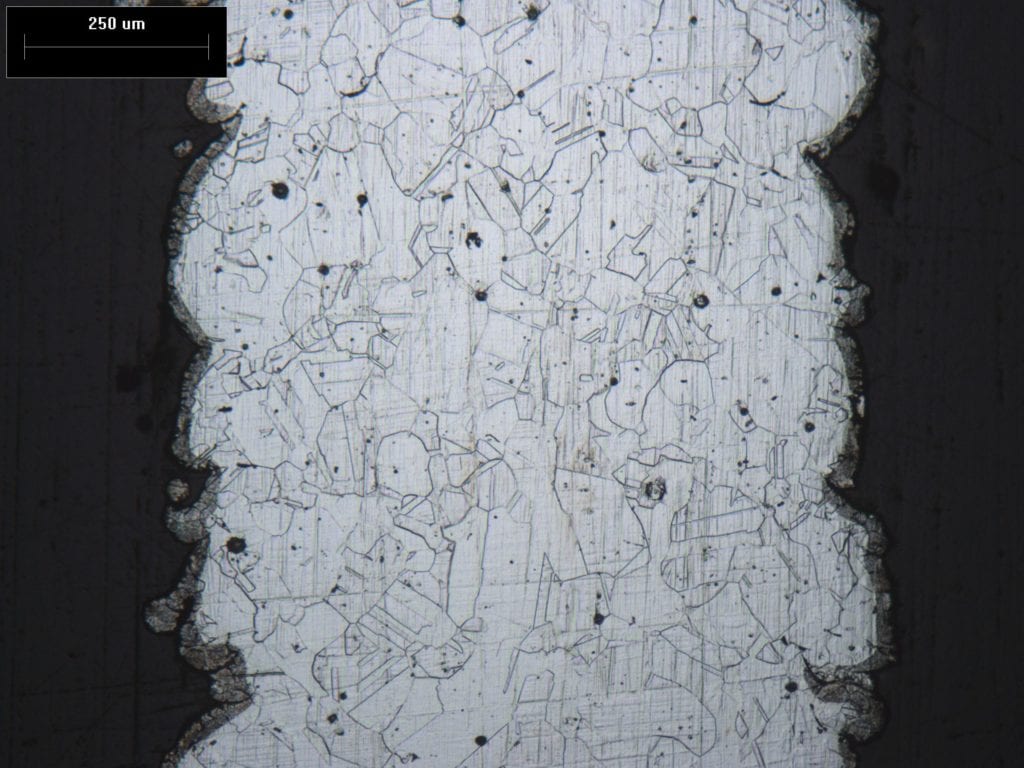
All NASA-HR-1 samples full recrystallized and homogenized, but the box 1 samples showed large, directional grains while the box 2 samples formed a more familiar, equiaxed structure. The higher porosity and surface roughness caused lower ductilities for box 2.
Non-Homogenized
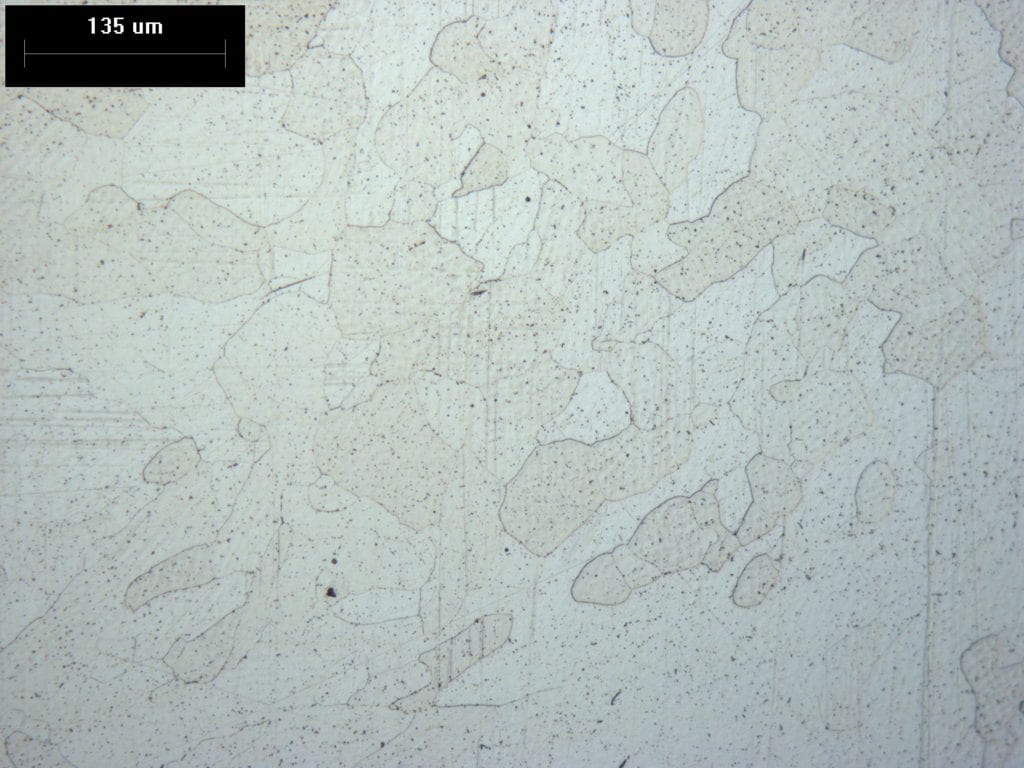
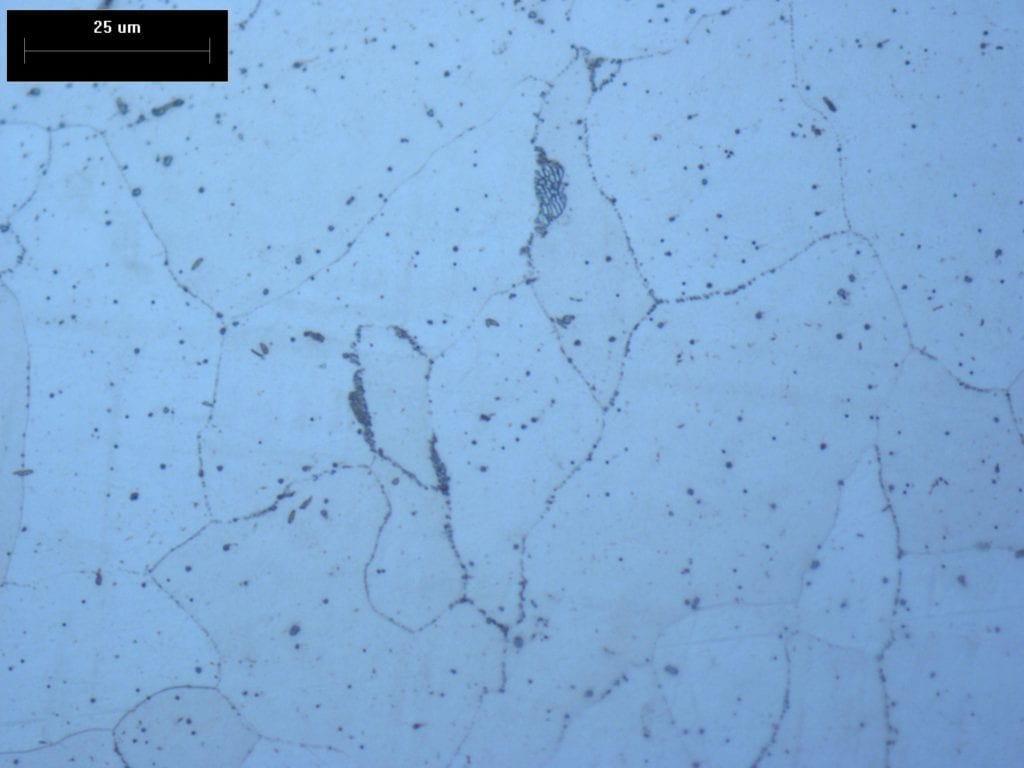
The non-homogenized JBK-75 samples recrystallized as evidence by grain boundaries that were not present prior to solution treating and aging. However, these samples did not fully homogenize as prior dendritic structure is still visible upon etching, meaning that some degree of microsegregation is still present in the microstructure.
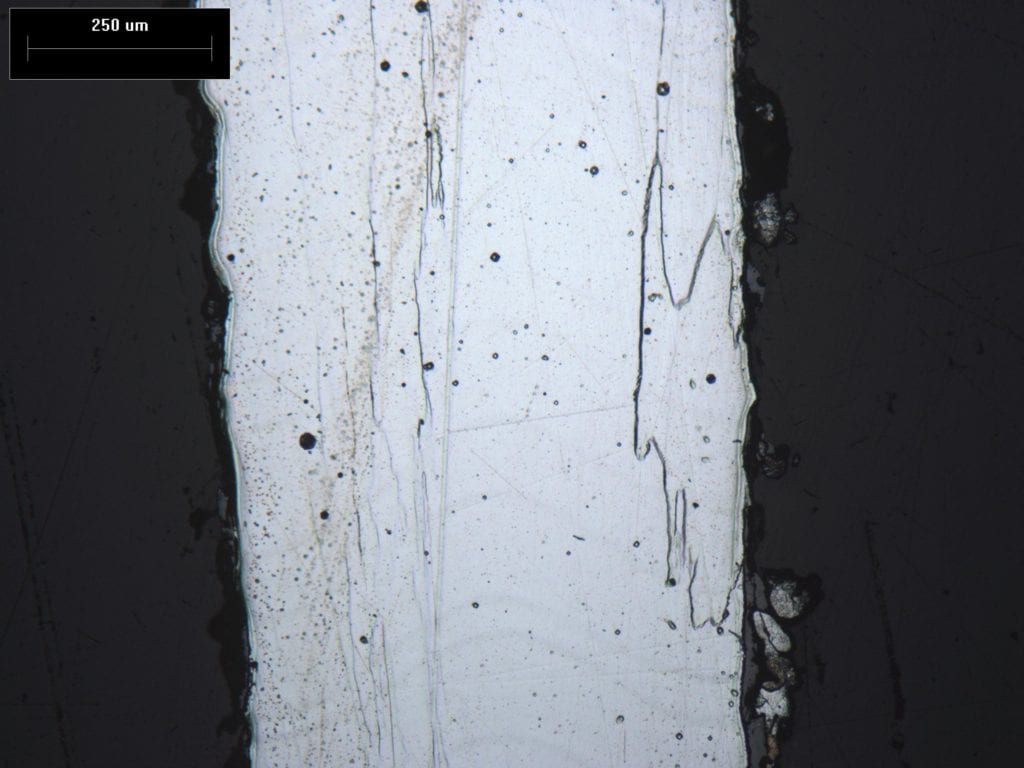
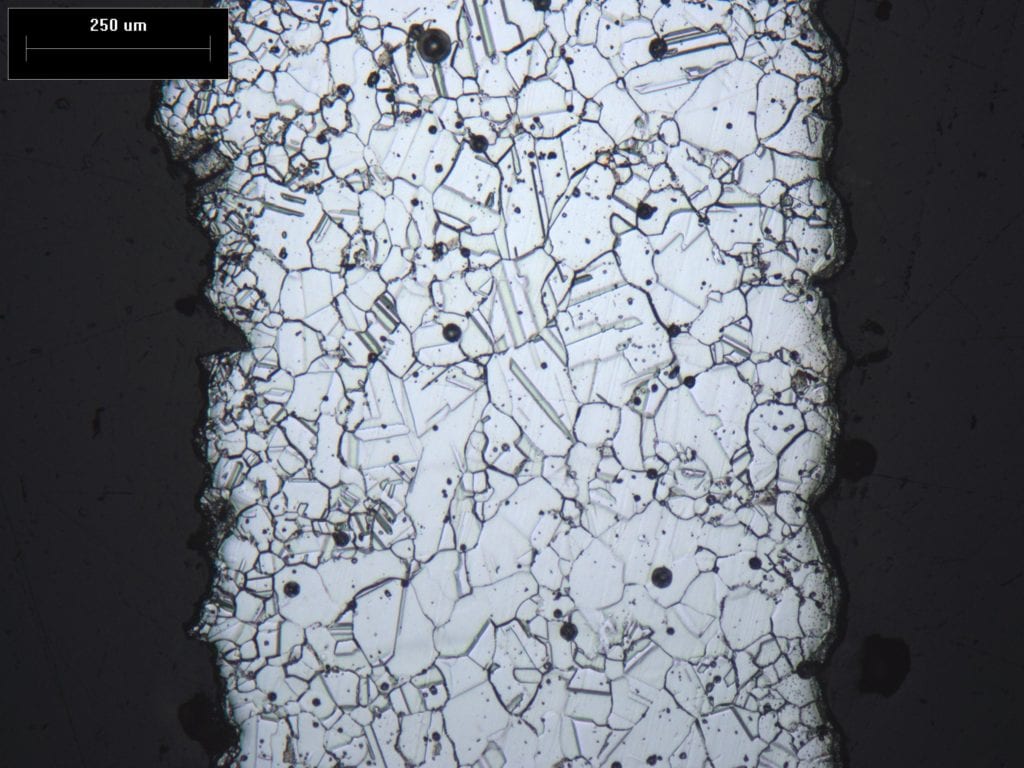
The non-homogenized NASA-HR-1 samples did not exhibit a significantly different structure than the homogenized samples . This is likely due to the stress relief heat treatment also permitting recrystallization and homogenization of the microstructure.
Conclusions
JBK-75
1. Recrystallization and full homogenization can be achieved with the lowest selected homogenization temperature and time (2000°F for 2 hours).
2. The strength of wrought JBK-75 was reached with DED JBK-75.
3. The non-homogenized samples exhibited the highest yield strength – possibly due to finer grain size.
4. Large losses in ductility can occur – the cause is an item for future work.
NASA-HR-1
1. The surface quality and porosity lead to a large difference in ductility between the two sample boxes. Box 2 HR-1 had a significantly higher degree of porosity and higher surface roughness, causing lower ductility.
2. The strength of DED NASA-HR-1 was low and did not meet the typical strength of wrought NASA-HR-1.
3. The yield strength of the NASA-HR-1 samples was independent of the homogenization heat treatment for the range of times and temperatures tested.
4. All Box 2 HR-1 samples recrystallized into an equiaxed structure.
Recommendations
JBK-75
1. Homogenization can be incorporated into the same step as solution heat treatment, since recrystallization and homogenization can occur at short times and lower temperatures than the ones tested. Conduct a similar study but with shorter times and lower temperatures to determine the minimum time and temperature needed to recrystallize and homogenize the microstructure.
2. Study the occurrence of low ductility in the material and what aspects of microstructure and heat treatment influence this behavior.
NASA-HR-1
1. Improve DED processing to reduce porosity and improve surface finish, especially for thin-wall applications.
2. Study the effect of DED processing and as-built microstructure on recrystallization behavior.
3. Combine homogenization and solution treatment into a single step. Homogenization times can be shorter than the shortest time tested in this study (2 hours).
4. Investigate the cause of low strength.