Our Team
Two transfer students in Materials Engineering that both ended up pursuing the same Masters program that joined forces to complete this senior project.
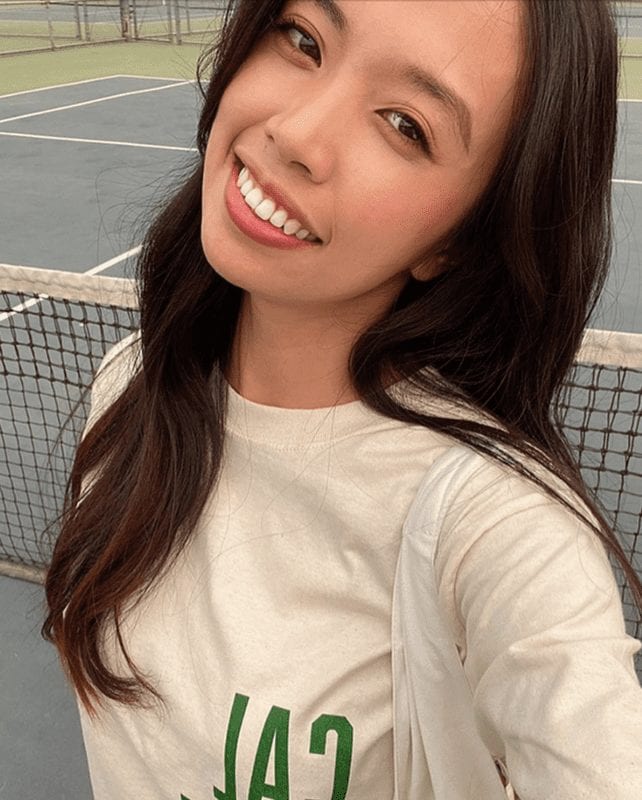
Sixin Zhai
Team Member
I am a senior Materials Engineering major and am pursuing a master’s degree in Polymers and Coatings Science. Meanwhile, I teach in a Materials Engineering lab as a Teaching Associate. In the past few months, I have done researches focused on wastewater treatments using nano materials and the rheology study of associative thickener (HEUR) in an acrylic latex. During my free time, I enjoy hiking and golfing.
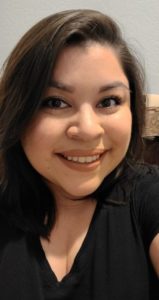
Crystal Ipong
Team member
I am working towards completing a Bachelor’s degree in Materials Engineering and a Master’s degree in Polymers and Coatings Science. During this past year I have been involved in graduate research, classes, the MESS club, two part time jobs, and being a mom to two lovely cats.
Acknowledgements
A special thank you and acknowledgement was due to all those that made this project possible. The sponsoring company, Safran Cabin, provided a valuable opportunity to learn and explore an interesting topic. The technical contacts from the company, Jennifer Montejano and Adam Olzick, provided stimulating conversation and direction for the project. The senior project advisor, Dr. Blair London, gave valuable feedback, structure, and guidance for the best possible project outcomes. The facilities that had the testing equipment for the project are the Materials Engineering Department and the Western Coatings Technology Center. The assistance of Dr. Shanju Zhang and Professor Eric Beaton was a source of clarity and knowledge needed for the project to succeed.
Our Project's Digital Poster
Problem Statement
Phenolic resin glass fiber reinforced prepregs are highly suitable for airplane components due to their high fire resistance, high temperature performance, and low-density characteristics. This is capitalized upon by Safran Cabin who seeks to improve their prepreg manufacturing process. The issue the company faces is the occasional composite delaminates or loss of tackiness rendering it unfit for use. The objective of the senior project was to better understand the volatile loss the prepreg experiences during out-time through solvent analysis to achieve a more consistent product performance.
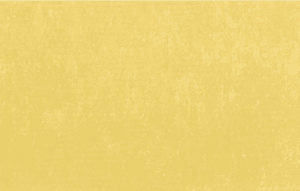
An example of a fully cured, single layer of prepreg.
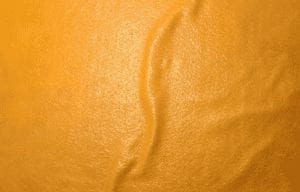
An example of a delaminated composite laminate where the loss of tackiness was too high.
Background
Prepregs are thin sheets of fibers that have been preimpregnated by a thin layer of resin matrix. Phenolic resins, or phenolics, are thermoset resins that are the result of a reaction between a phenol, or substituted phenol, and an aldehyde. Resoles, the specific type of phenolic resin under investigation, is base-catalyzed and self-curing. A cross-linked phenolic resole structure is produced as the resin cures and methylene bridging occurs (Figure 1).
Figure 1. An example of a cross-linked phenolic resole structure which is produced as the curing reaction progresses and methylene bridging occurs.
Phenolic resin glass fiber reinforced prepreg is high performing, yet light-weight and fire resistant. The characteristics make it well-suited for the air-craft storage applications produced by Safran (Figure 2).
Figure 2. The phenolic resin glass fiber reinforced prepreg is used in the manufacturing of the overhead cabins of an A220 aircraft.
Experimental Design
To explore the loss of volatiles over the various out-time lengths and temperatures the conditions were replicated by simulated storages. The storage temperature at Safran is replicated by the 2.6ºC temperature, room temperature or a cool day was represented by the 16-18ºC temperature range, and the warm summer day is represented by the 28-33ºC temperature (Table I).

The testing methods we used to monitor the loss of volatiles include: physical observations, FTIR, and TGA. The samples were tested every 3-4 days during the simulated storage periods to replicate the out-time length of 10 days that is experienced by prepreg at Safran (Figure 3).
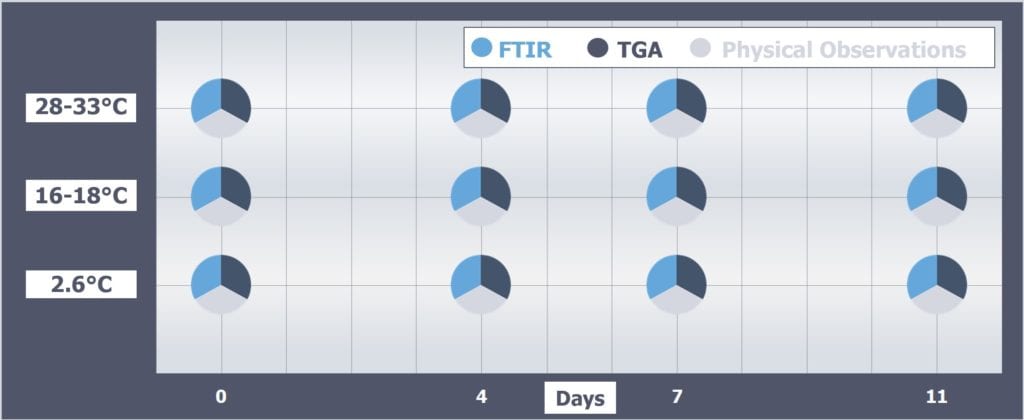
Physical Observations
Physical observations were performed on each sample as they were moved from the simulated storage to the long-term composite storage freezer (Figure 4). The tackiness and rigidity of the prepreg samples were scored on a scale of 1-5, with 1 being the original rigidity and tackiness conditions of the prepreg upon delivery and a 5 being a fully cured condition.
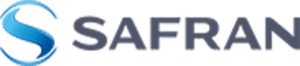
This project is sponsored by...
Physical Observations
The tackiness (Figure 4) and rigidity (Figure 5) between the lower temperature samples (2.6°C and the 16-18°C) were almost exactly the same. The 28-33°C samples lost most volatiles by day-4 and were no longer malleable by day-7 and day-11 without cracking.
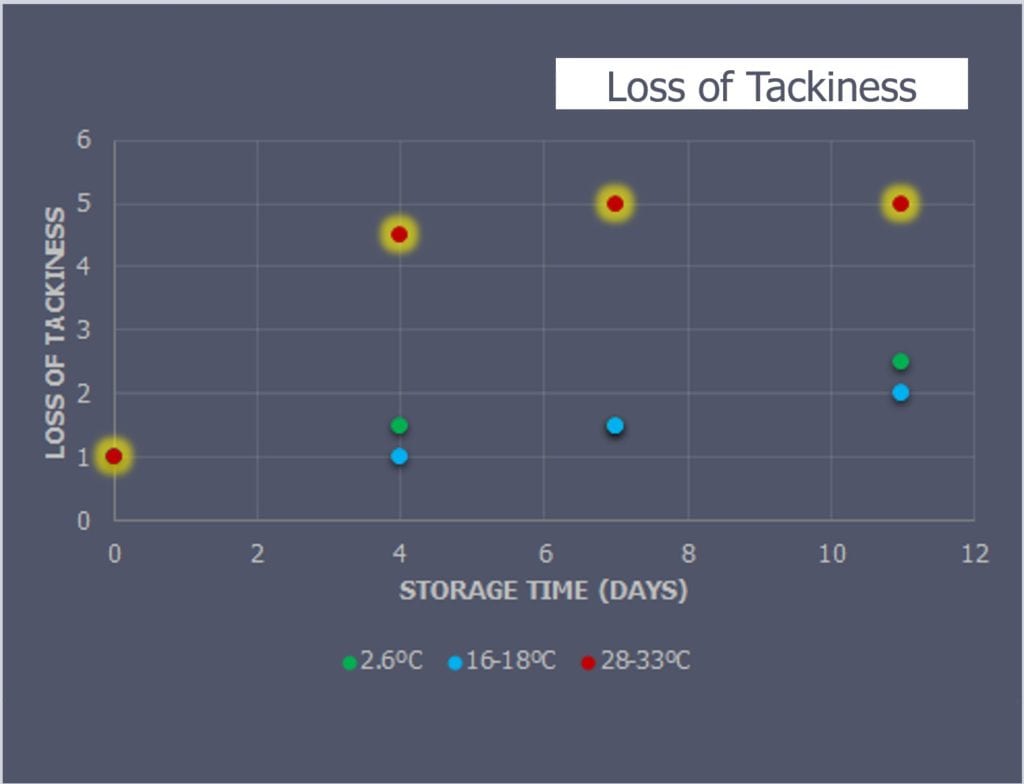
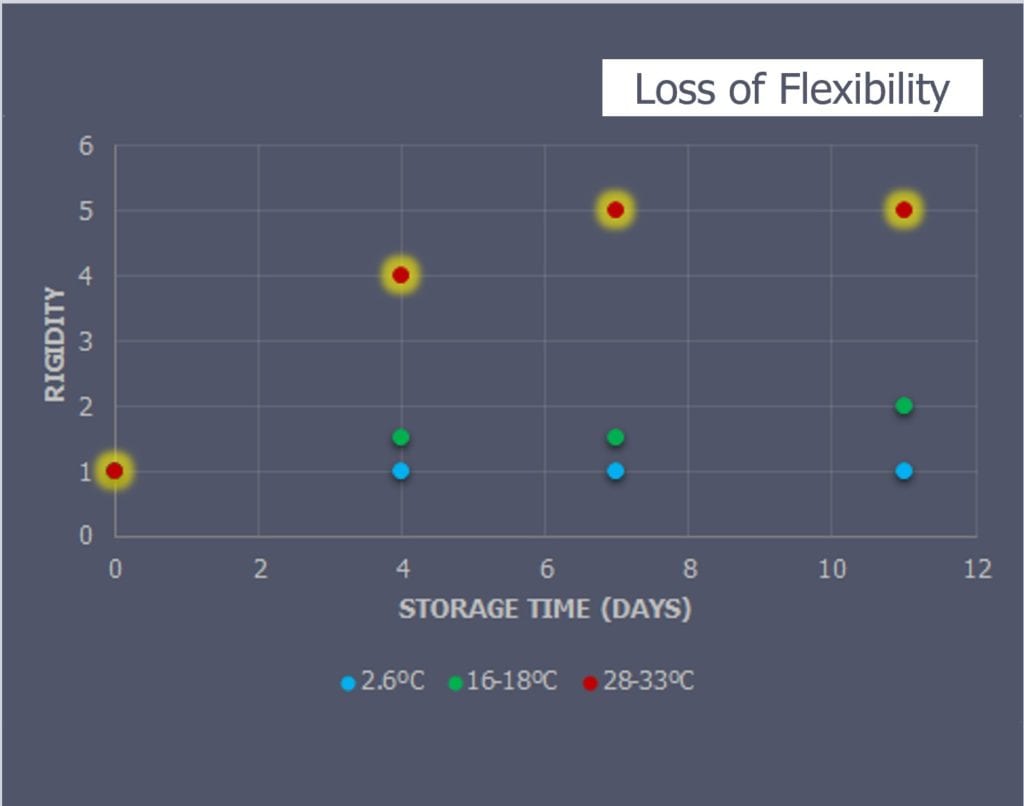
FTIR Results
Overlaid FTIR spectra of prepregs by storage temperature
Overlaid FTIR spectra of prepregs were compared to monitor bond population of the key volatiles in percent transmittance. Note that an increase in percent transmittance is a result of decreasing bond population of functional groups detected by FTIR. The changing variable on each overlaid spectra plot is storage length. Throughout 11 days, the overlaid spectra of storage temperature at 2.6°C and 16-18°C were close to identical indicating that the low storage temperatures experienced a similar loss of volatiles. The greatest change in percent transmittance was evident on the overlaid spectra of samples stored at 28-33°C, implying the samples that experienced the greatest loss of volatiles were stored at the 28-33°C. Additionally, the vanishing peak around 1000 cm-1 (C-O) at 28-33°C indicated that the prepreg experienced curing as methylene bridging occurred through the elimination of alcohol (OH) groups from the etheric bonds.
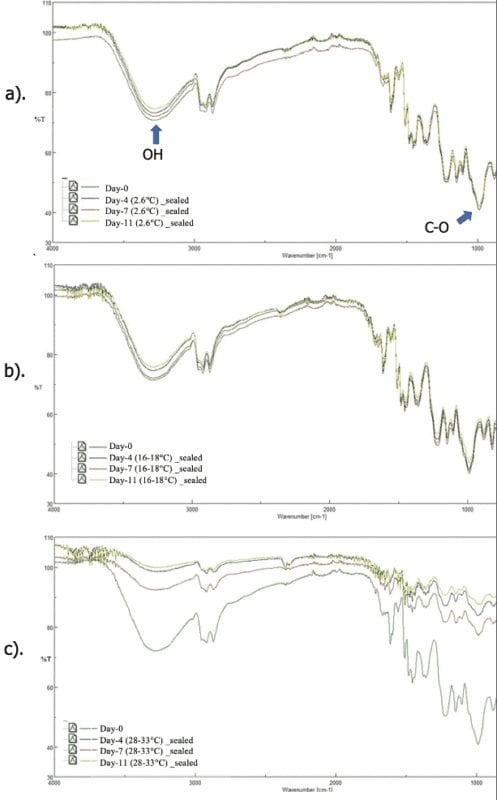
Percent Transmittance change in FTIR curves
The percent transmittance of functional groups was compared between different storage temperatures on day-4, day-7, and day-11 (Figure 4). For low temperature simulated storages, the percent transmittance of the ether bridge (1000 cm-1) and alcohol groups (3200-3550 cm-1) were close to constant. However, at the storage temperature of 28-33°C, the percent transmittance of both etheric
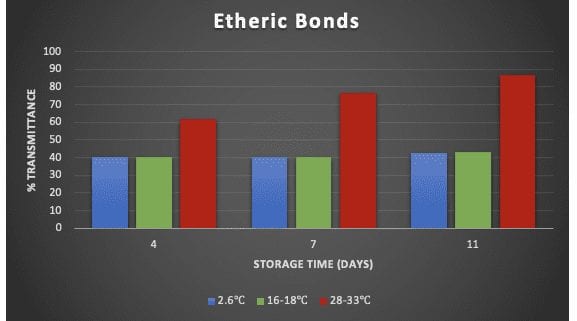
FTIR Results
bonds and alcohol groups increased significantly, implying minimal bond population of volatiles was detected by FTIR. The increase in percent transmittance is an indication of volatiles loss during storage.
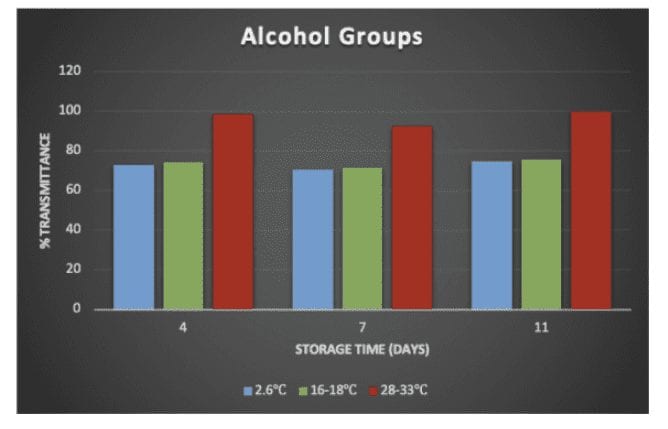
TGA Results
The presence of remaining volatiles of prepregs were compared as weight loss in percentage on TGA curves at 120°C, which is the curing temperature of phenolic resin. A small change in weight loss represented a small weight loss in the remaining volatiles in the prepreg after simulated storage. A trend similar to the trend seen on the FTIR results was shown on the TGA data of prepregs. There was no discernible difference in weight loss of volatiles between samples stored at 2.6°C and 16-18°C after 4 days of simulated storage. However, weight loss of remaining volatiles decreased with increasing storage temperature shown on the comparison TGA data on day-7 and day-11. Overlaid TGA curves at 2.6°C, 16-18°C, and 28-33°C throughout the 11 days of simulated showed weight loss of remaining volatiles decreased with a longer storage period.
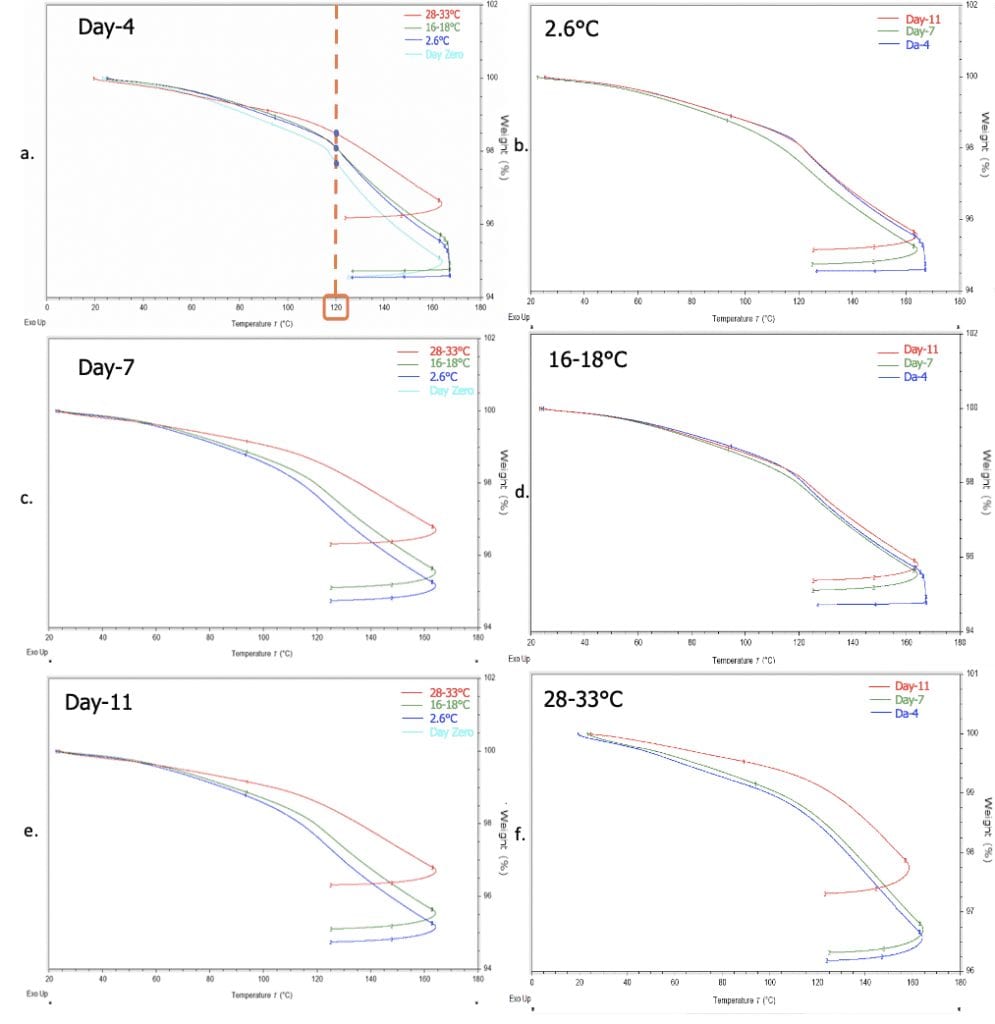
TGA data Summary
The weight loss of volatiles of prepreg throughout different storage lengths and storage temperatures were compared at 120°C (Figure 6) to better differentiate the volatiles loss during simulated storages. A higher weight loss value represents a higher amount of volatiles remaining in the prepreg after storage. A larger decrease in the remaining volatiles was observed when the comparison was made between storage temperature rather than storage length. The increase in remaining volatiles at storage temperature of 2.6C and 16-18C could be indicative of water by-product produced by the prepreg upon curing.
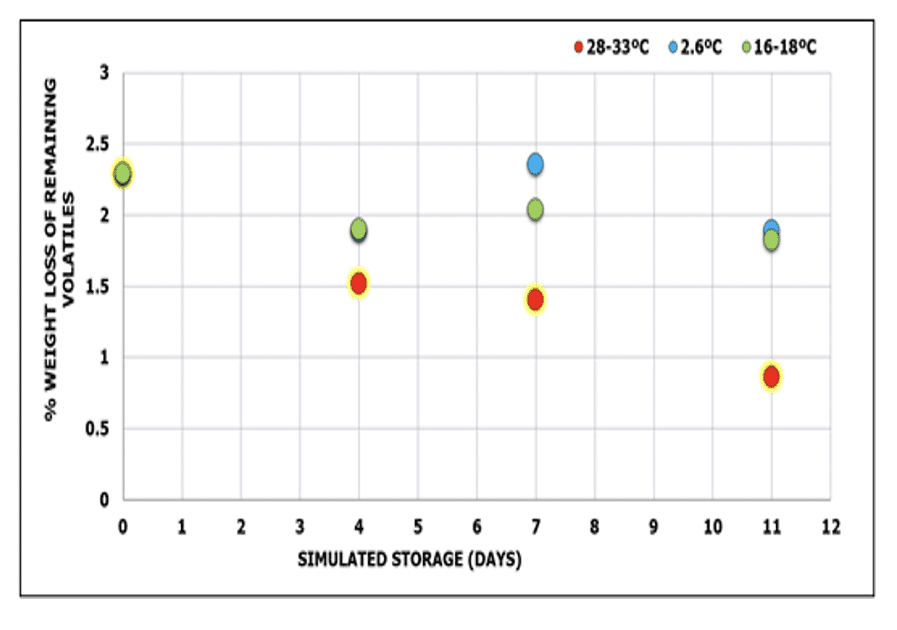
Conclusions
1. At high temperatures, the prepreg lost most of its flexibility and tackiness during out-time.
2. Greatest decrease of volatiles occurred at 28-33°C.
3. Volatiles are more sensitive to high temperature than the length of out-time.
Recommendations
1. Provide low-temperature transport during summer or hot days
2. Store prepreg in temperature-controlled areas on hot days at the facility