Our Team
This project was completed by our two person team of Ryland and Colin, both of whom are Materials Engineers.
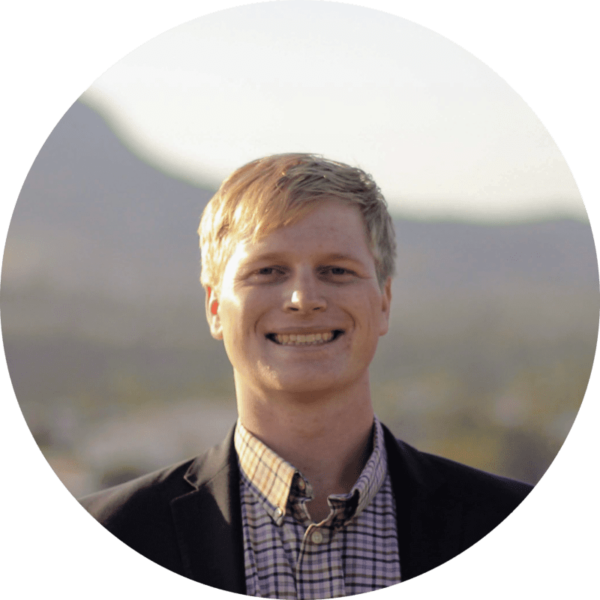
Colin Masterson
Team Role/Title
4th Year Senior from Placerville, CA. Graduating Spring 2021.
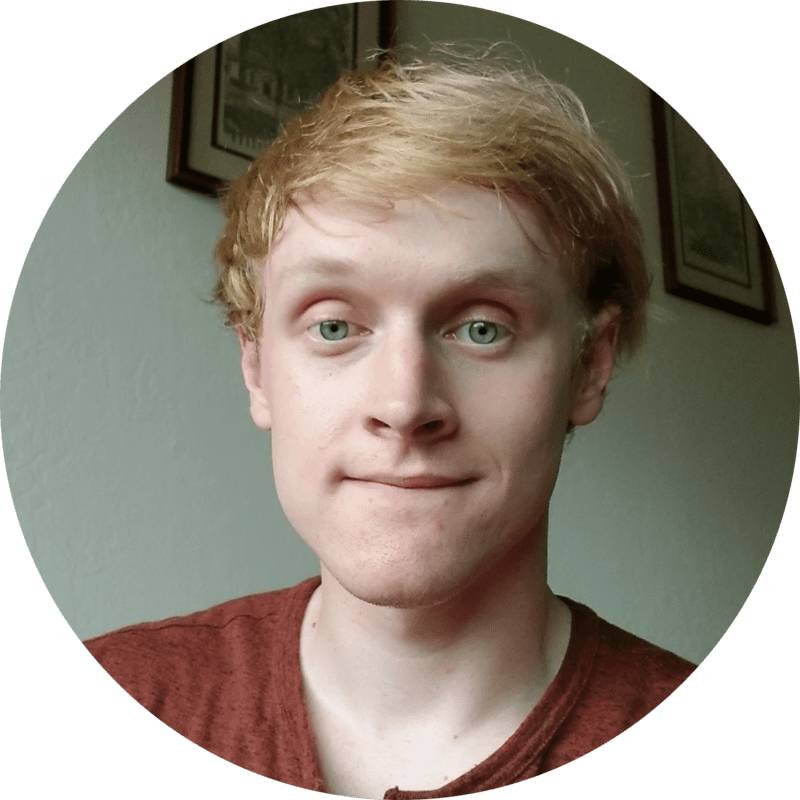
Ryland Jolliffe
Team Role/Title
4th Year Senior from Chico, CA. Graduating Fall 2021
Acknowledgements
Thank you to the following people for their guidance and support that made this project possible:
Prof. Blair London: advising the team on the project
Mark Timko and Henrik Harwood: producing the samples for the team to test, testing EC blocks, and guiding the progression of the project.
Company Sponsor
Weber Metals
Weber Metals was originally a scrap metal business that turned into a forging business to help supply parts for the west coast aerospace industry during the early 1940s. After the death of the owner, Edmund Weber, his wife sold the company to OTTO FUCHS Metallwerke a Germany company in the 1980s, and during the next decade they increased the production capacity with larger closed die presses. These new presses are used in aluminum and titanium forgings for the aerospace industry. During the 1990s the company continued to grow and become a major supplier for the aerospace industry.
Problem Statement
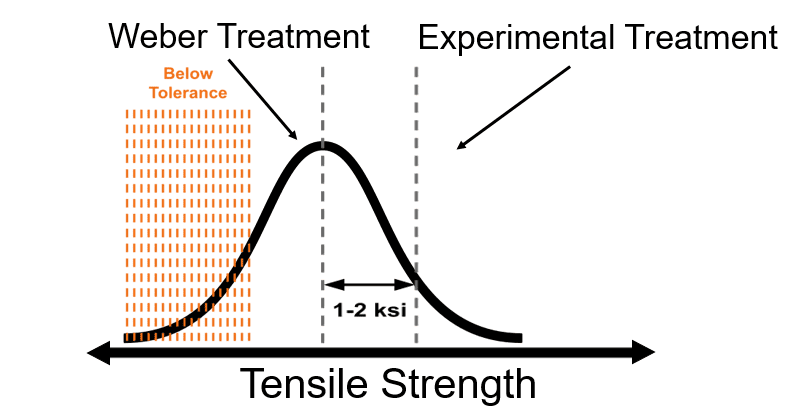
- Increase the Tensile and Yield Strength by 1-2 ksi
- Maintain an acceptable stress corrosion cracking resistance
Box Furnace Calibration
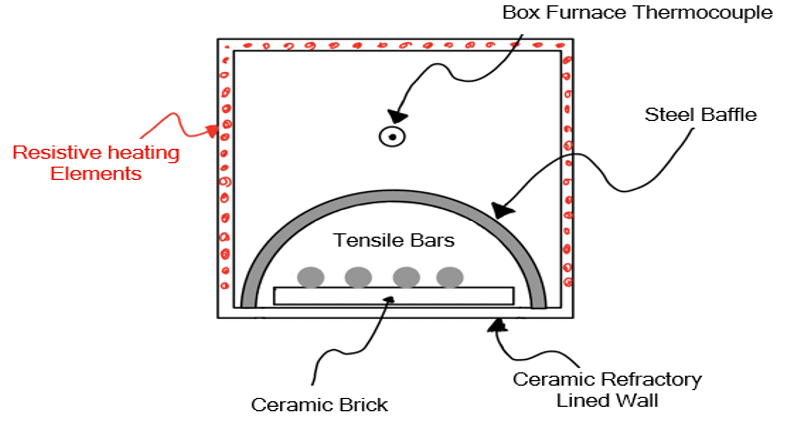
- Schematic of the sample placement in the box furnace. The baffle works as a radiation shield and produces a colder area under the baffle so the box furnace thermocouple reads a higher temperature than what the samples experience.
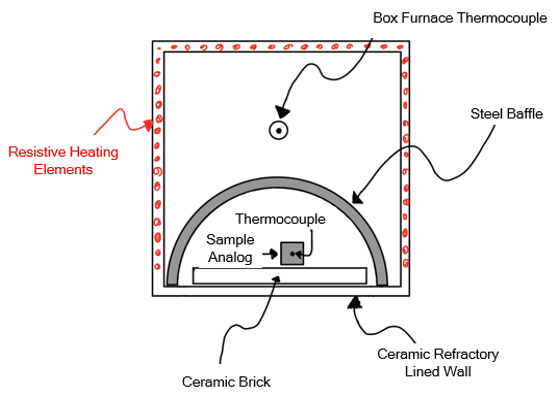
- To solve the issue of the temperature difference we placed a sample analog with an internal thermocouple to determine the difference between the furnace and sample temperatures at any range of temperatures.
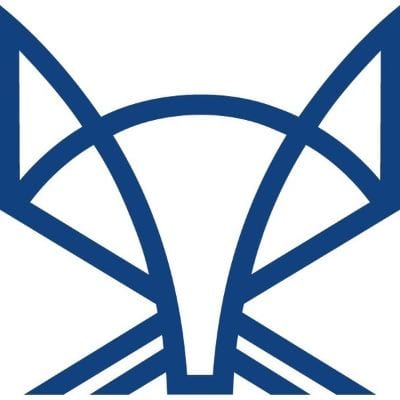
WEBER METALS, INC.
This project is sponsored by WEBER METALS, INC. AN OTTO FUCHS COMPANY
Background Information
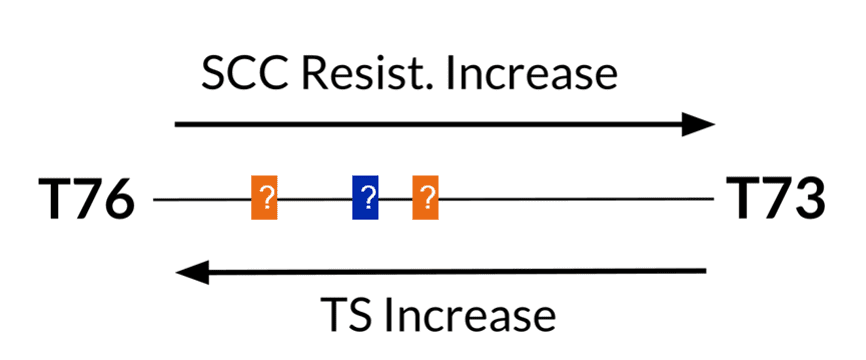
- There are two current ASM heat treatments that the produce the upper and lower bounds of properties of the samples
Results
Two-Step Aging
Results
Retrogression and Reaging
Conclusions
- 1. A sample temperature of 107°C for 6 hours followed by 169°C for 13 hours (Group 4 HT) reached the project goal.
2. No retrogression and reaging treatments met the project goals.
Recommendations
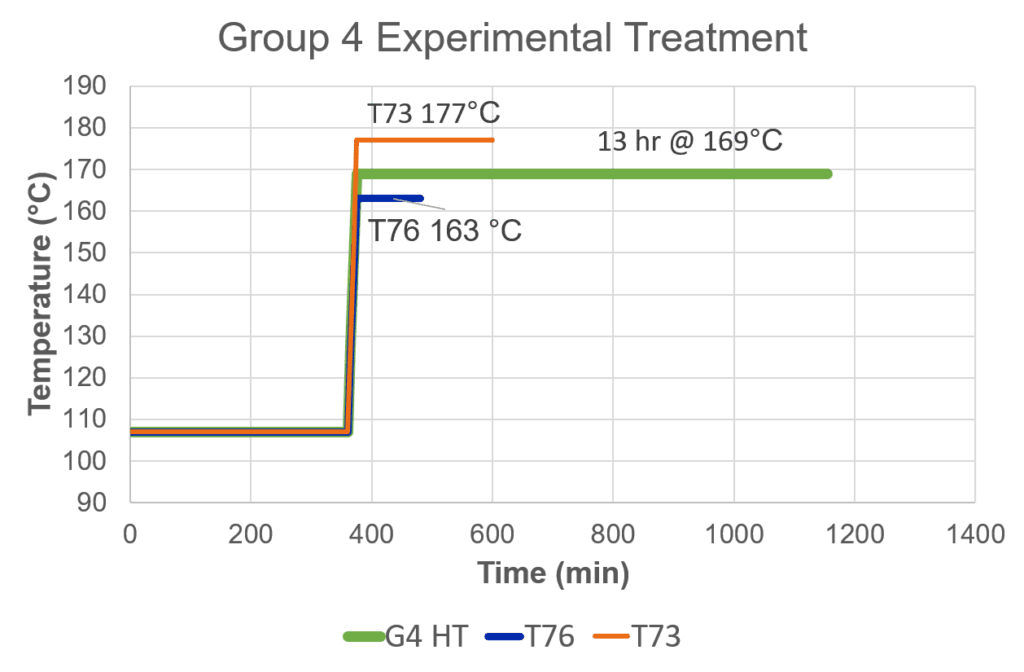
- The G4 heat treatment produced the best results and met the minimum strength requirements and conductivity requirements. The next steps is to try this heat treatment on the industrial scale to see if its viable.