Without A Paddle: A Cal Poly Senior Project
The Cal Poly 2020 Solar Regatta Team consisted of two senior project teams. Up a Creek focused on the boat’s hull, while Without a Paddle (that’s us!) took on all things propulsion.
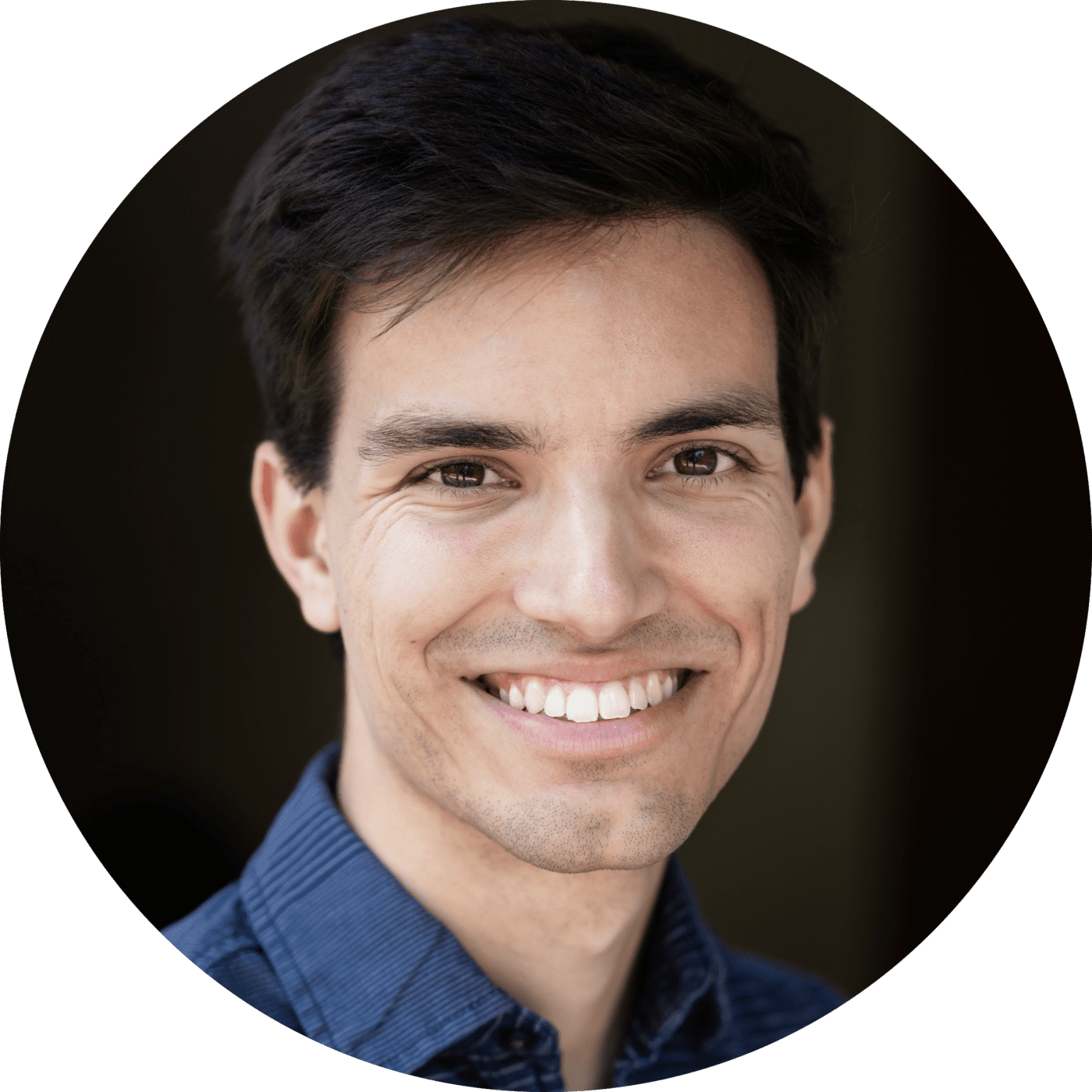
Niko Banks
Design Lead
Designed and manufactured propellers, conducted testing and analysis of solar panel energy conversion and motor efficiency, and assisted with CAD modeling.
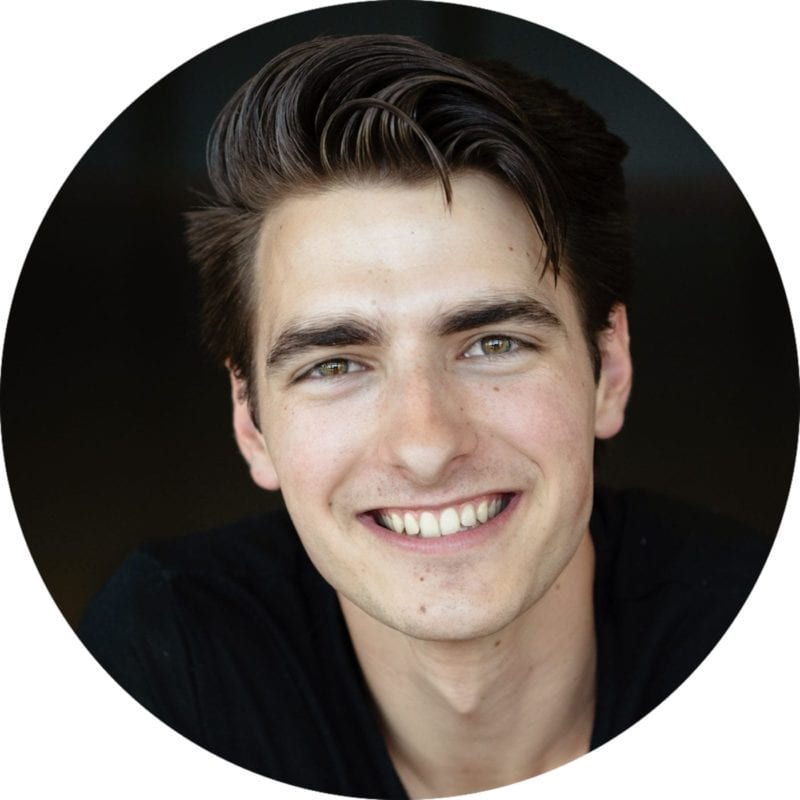
Nathan Carlson
Systems Lead
Coordinated between sponsors, advisors, faculty and peers to ensure both the Hull and Propulsion Teams worked together to design a boat that met competition requirements.
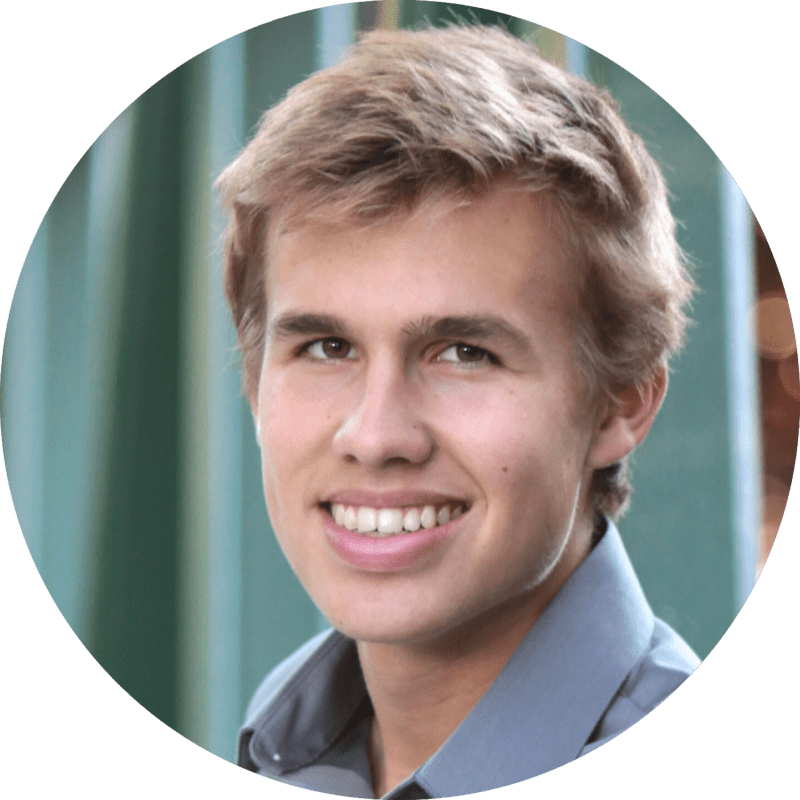
Eric Rinell
Manufacturing Lead
Designed gearbox and motor mount. Reviewed designs for manufacturability. CNC programmed and machined the gearbox. Performed CAD integration with Hull Team.
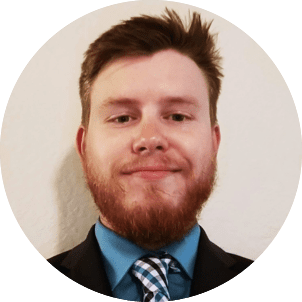
Alex Larson
Test Lead
Designed and manufactured the rudder. Put together testing plans for custom manufactured components. Solutions expert resource for teammates.
General Overview
Technical Overview
Our Project's Digital Poster
Problem Statement
Design and build a propulsion system for a solar powered boat to compete in the 9th Annual SMUD Solar Regatta. The propulsion system will be powered by either the solar panels or the battery (depending on the race) and will be suited to maximize scores in all three races.
Competition Overview
The SMUD Solar Regatta consists of three races (Endurance, Sprint, and Slalom) as well as a presentation and various bonus awards.
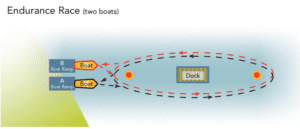
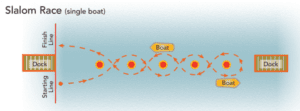
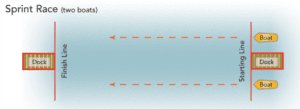
Design Constraints
- Maximum boat dimensions: 20’ x 8’ x 5’
- Solar Panels and Battery are only allowed forms of energy storage (no capacitors)
Propulsion Design Layout
Two propulsion units were chosen for the final design for a number of reasons, including:
- Multiple, smaller propellers are more efficient than one larger propeller
- Improved stability over a single unit in the center
Other notable design choices:
- Steering system designed with cable system in order to be adaptable to different pontoon configurations
- Each propulsion unit rotates to provide steering rather than changing speeds of each propeller- keep each propeller at max efficiency speed
- Gearbox machined out of aluminum for ease of manufacturing
- Propellers 3D-printed for ease of manufacturing and comparatively low cost
- Rudder has a wood core for shape laminated with carbon fiber to keep it light but also strong enough to support gearbox and propeller
- Solar panels planned to articulate toward the sun to provide maximum power input
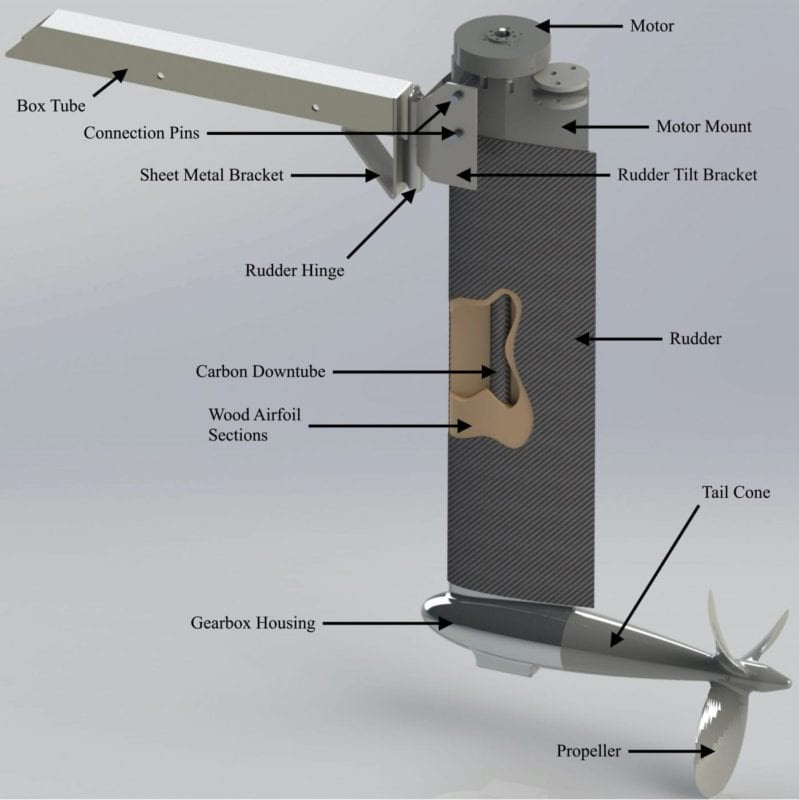
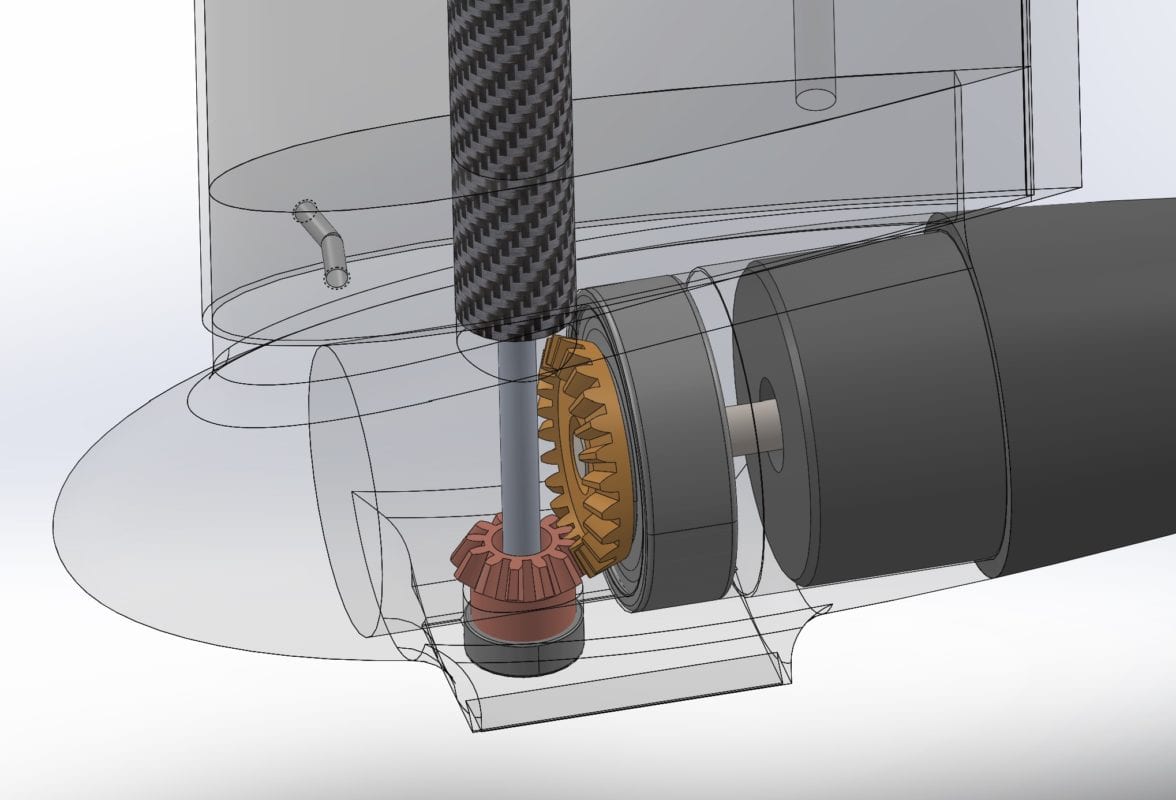
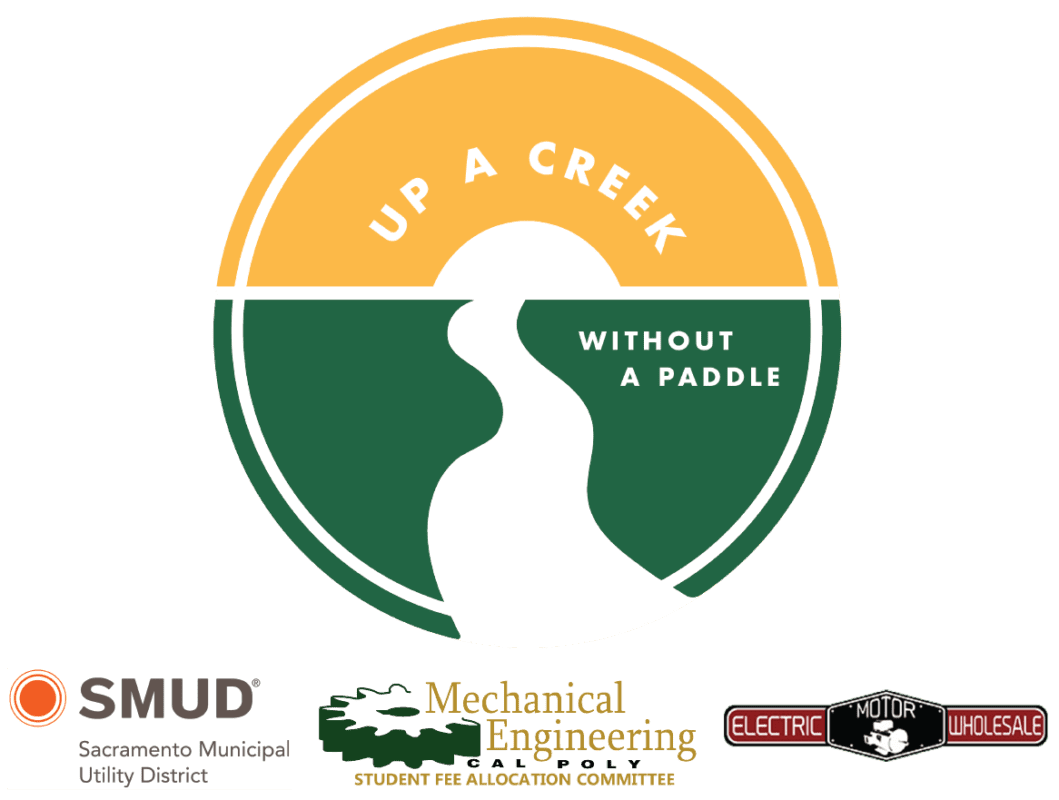
This project was sponsored by Cal Poly Mechanical Engineering, SMUD, and Electric Motor Wholesale.
Design Concept
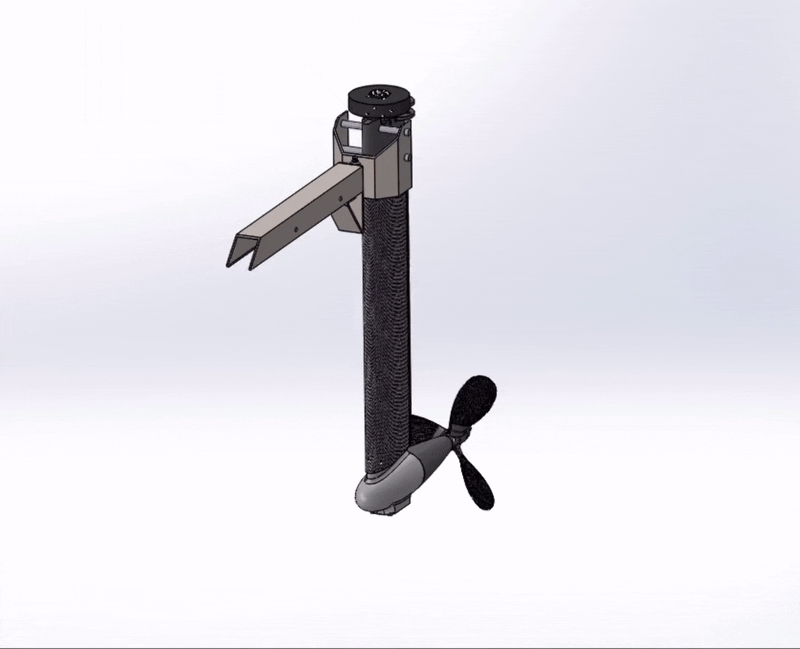
The chosen design was to have two propulsion systems, one on the back of each pontoon. The CAD model of a single propulsion unit allowed the dimensions and tolerances to be finalized for each component of the subsystem.
Propeller Analysis
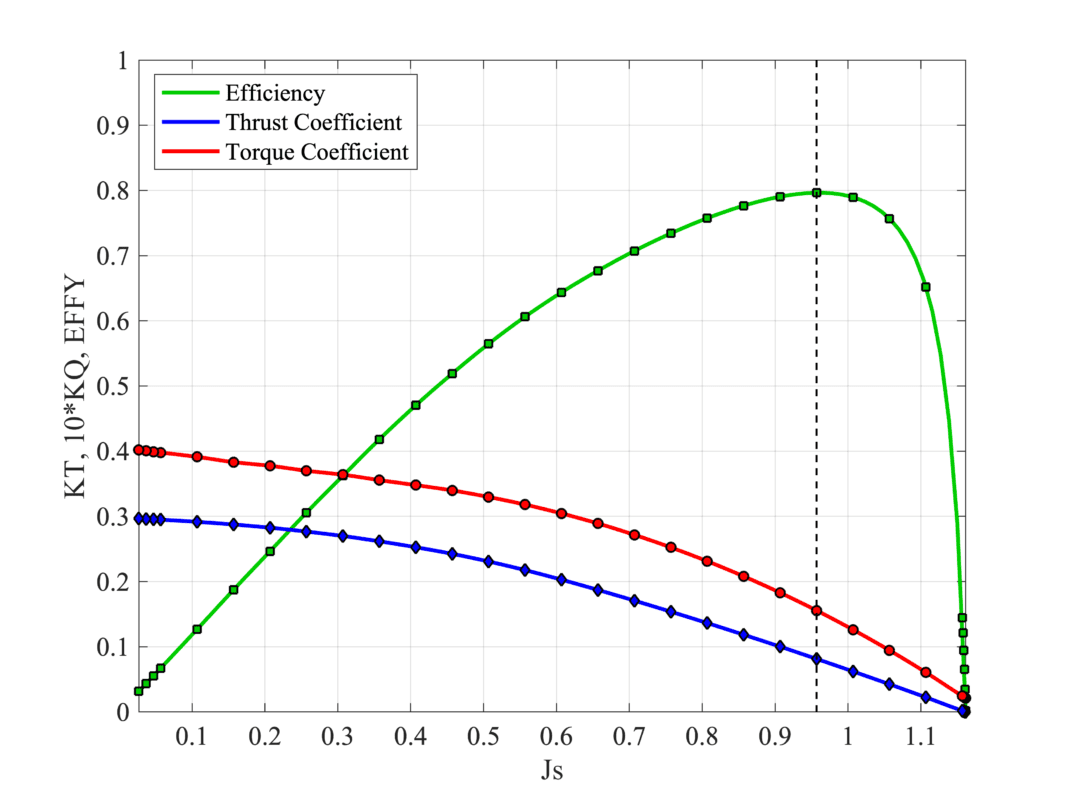
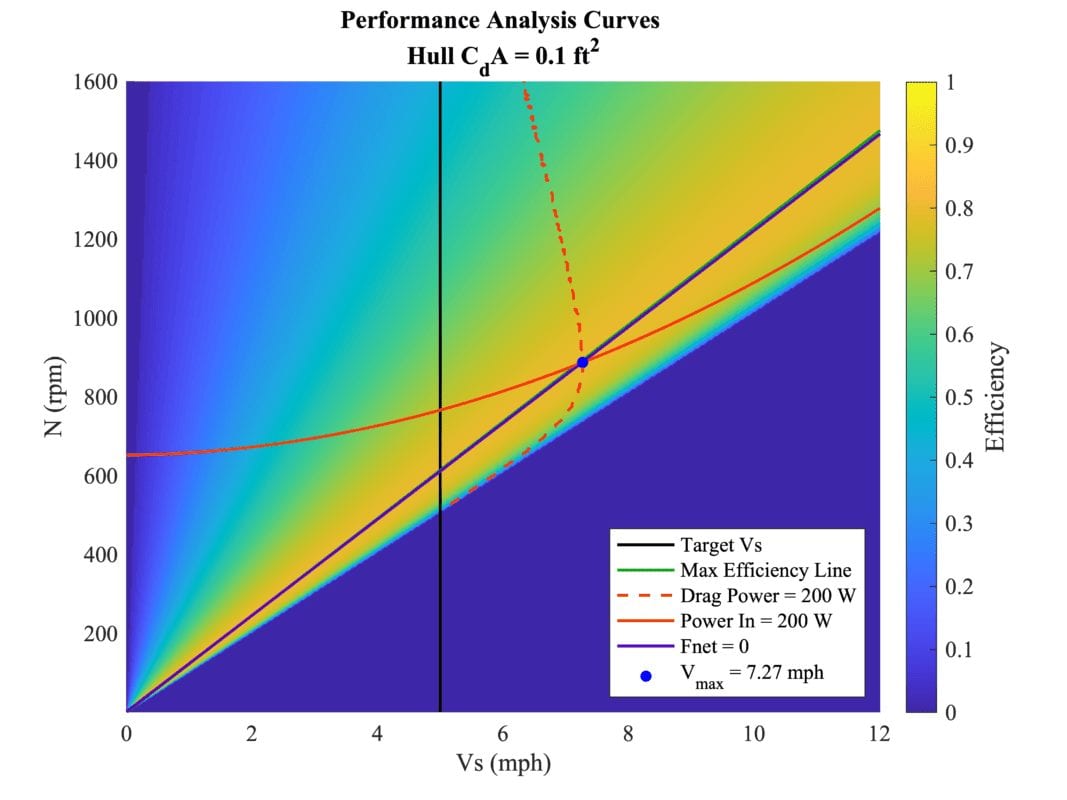
Through analysis, a propeller diameter of 9″ and an operating speed of 900 RPM was chosen to provide the maximum possible efficiency. The torque and speed of the propeller were designed to coincide with the same torque and speed required for high motor efficiency.
Using the dimensioned performance curve the top boat speed was determined to be 7.3mph. Each unit, at 900 RPM, produces 11.25 lbf of thrust at an efficiency of 80%.
Manufacturing Process and Components
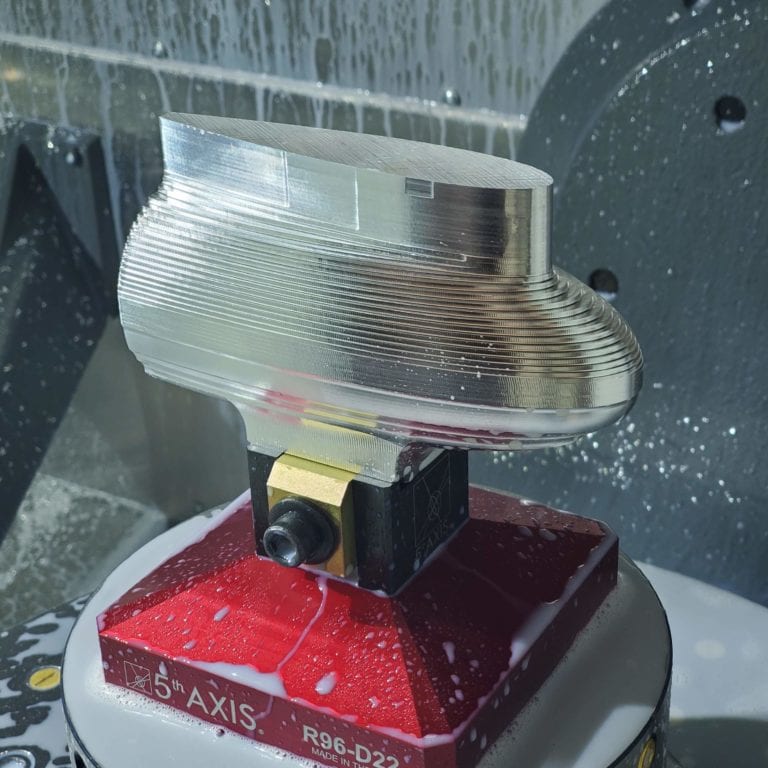
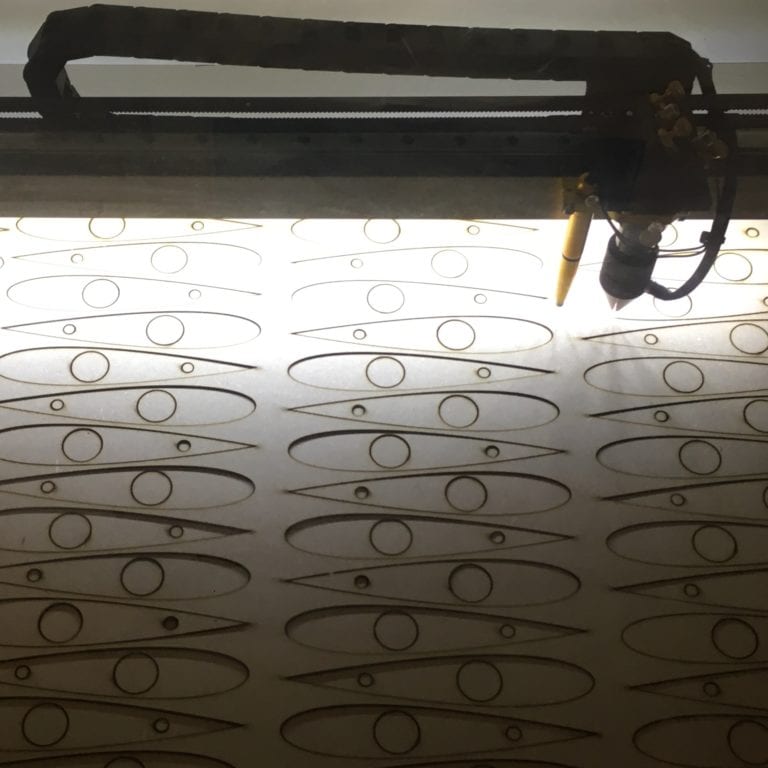
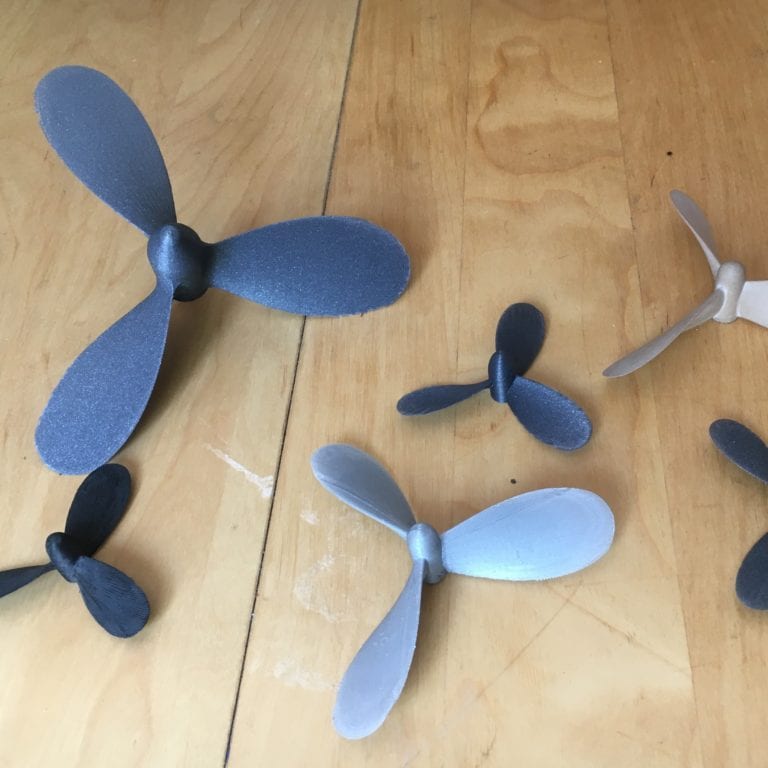
We used the manufacturing process that best fit the part and application:
- CNC machining for tight tolerance aluminum parts
- 3D printing for small complex parts
- Laser cutting for wood
- Carbon composites for strong and smooth submerged surfaces
- Sheet metal for simple but strong components
Design Verification/Testing
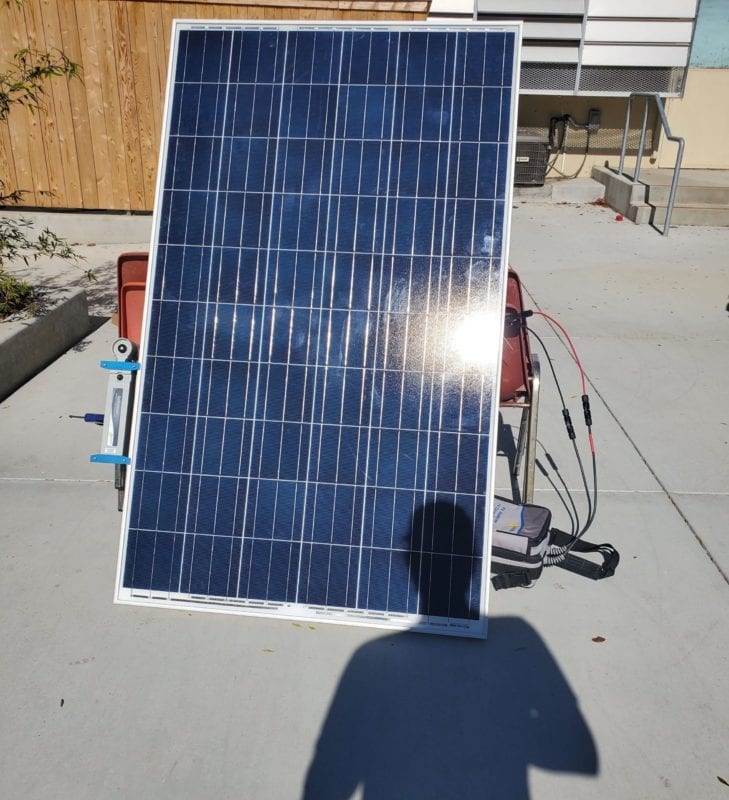
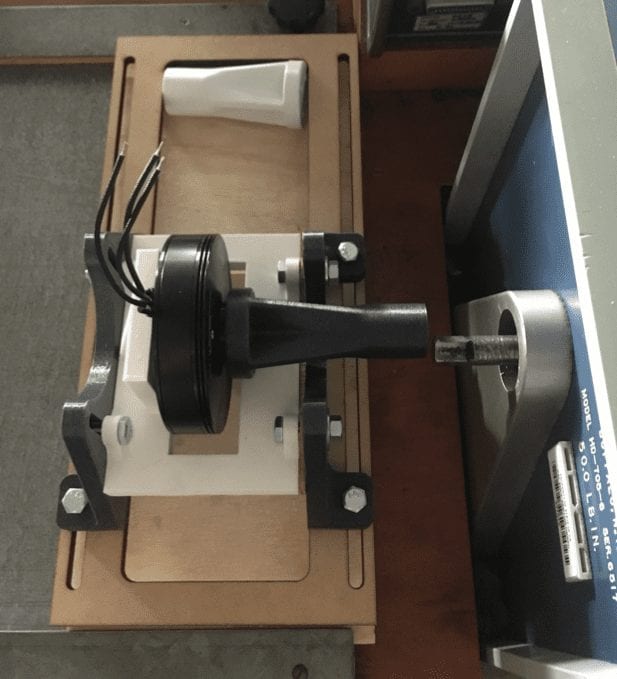
Solar Panel Output – The solar panels specified output (235 Watts) were verified using a PV test device. The panels were also tested in their response to changing lighting conditions. It was found that a head-sized shadow reduced power by nearly 30% and that angling the panels away from the sun caused a significant power drop.
Motor Testing – A dynamometer was used to generate torque-speed curves for the motor. Early motor testing led us to purchase a higher KV motor (faster) and an electronic speed controller better suited for its operation.
Final Design
Specifications of One Unit:
Weight – 6.5 lbs
Height – 34 Inches
Thrust – 11.25 lbf
Boat Top Speed – 7.3 mph
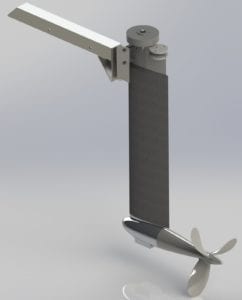
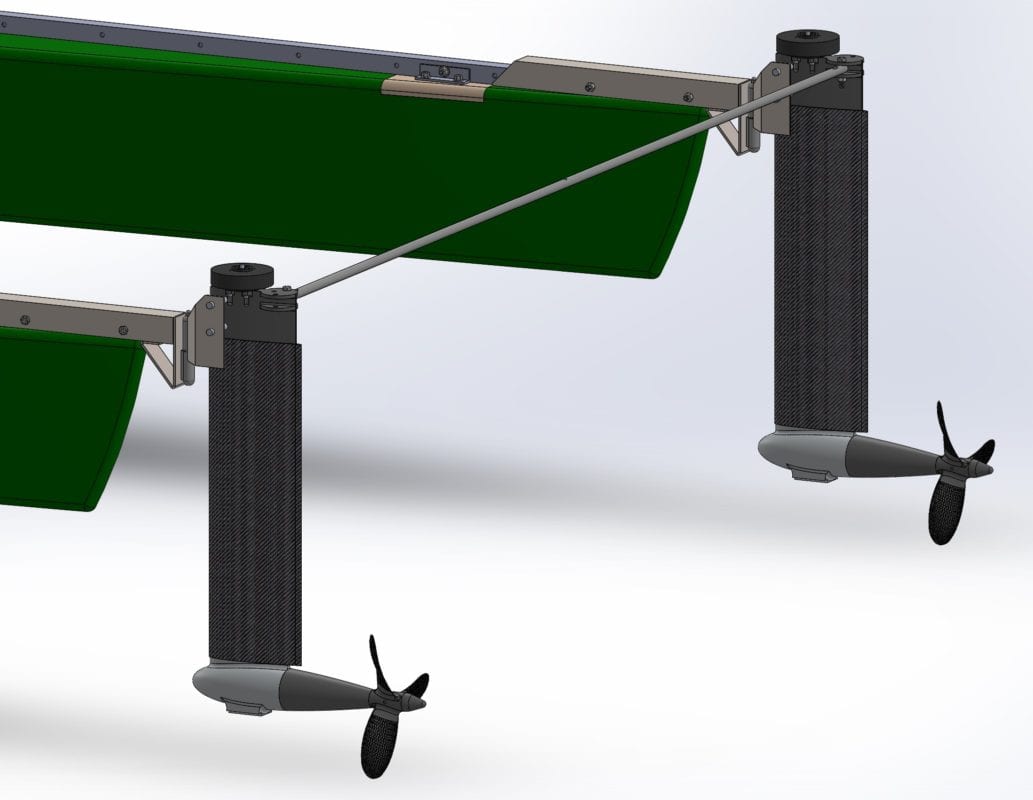
Custom Components
- Propeller
- Gearbox Housing
- Rudder
- Motor Mount
- Mounting Bracket
Stock Components
- Bearings
- Bevel Gears
- Drive Shafts
- Carbon Downtube
- Electric Motors
- Box Tubing
- Fasteners
Future Application
This design and manufacturing processes will be used by the 2021 Cal Poly Solar Regatta team. The prototype unit we manufactured will be used for testing and optimization before completing two final units to be used in competition next year. This design could also be modified for personal use for boats with low speed requirements such as fishing trollers and water taxis.
Recommendations
Improvements to be made for next years design
- Solar tracking to get maximum power from solar cells
- Gearbox design to simplify manufacturing
- Custom electrical regulator to reduce losses
- Utilize a water channel to perform flow visualization on the propellers and rudder.
- Design different propellers for each race to ensure the maximum efficiency under different conditions
- Verify simulation results and confirm the model matches the unit’s performance
CAD Gallery
Manufacturing Gallery
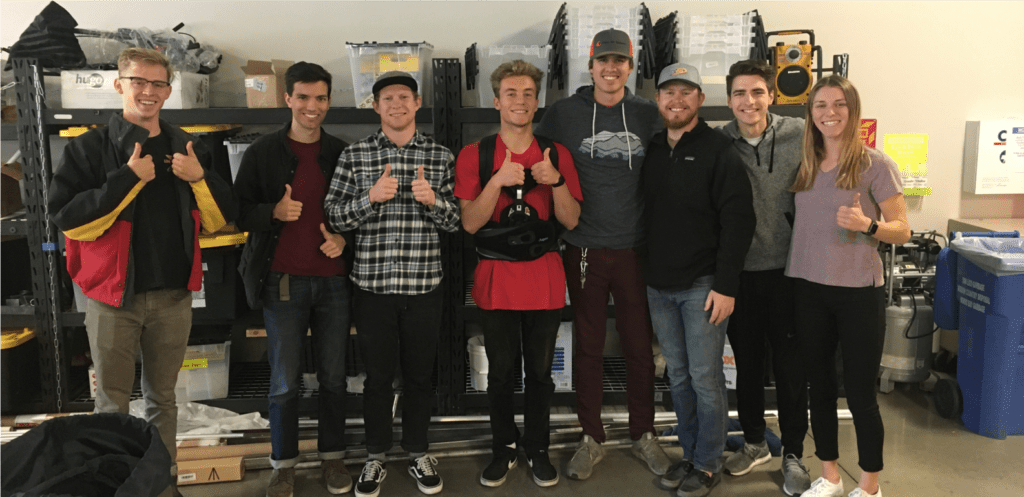
From all of us at Up a Creek Without a Paddle, Thank You!
Acknowledgements
First off, a huge thanks to our project advisor Dr. Brian Self for helping our team throughout the year, he was always a voice of reason and encouragement. Special thanks to Dr. Peter Schuster for being our senior project coordinator, and for working with Dr. Self to adeptly transition to a virtual workspace our last quarter. We could not have completed this project without the support and funding from Cal Poly and the Mechanical Engineering Department, we were very thankful for this opportunity. Thank you to SMUD for hosting this competition and for sponsoring our team, we were sad you had to cancel the 2020 competition, but Cal Poly is excited to participate again in 2021!
A list of other individuals that assisted in our design includes: Hans Mayer, Andrew Davol, Dale Dolan, Ali Dehghan Banadaki, Majid Poshton, and Eric Pulse. This project was successful because of your support and insight, thank you.