Our Team
Cal Poly Mechanical Engineering Students
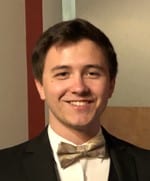
Matt Lundgren
Project Leader
I am a graduating 4th year mechanical engineering student at Cal Poly. I’ll be working as an HVAC Design Engineer in Roseville upon finishing school.
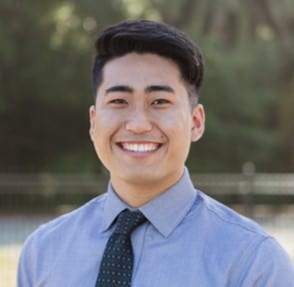
Adam Mayeda
Testing Lead
I am a graduating 5th year mechanical engineering student at Cal Poly. I’ll be staying in SLO and working as a Process Engineer after graduating.
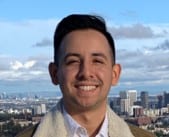
Dallas Rocha
Analysis Lead
I am a graduating 3rd year mechanical engineering transfer student at Cal Poly. I am currently seeking employment and focusing primarily on construction, petroleum, and utility industries.
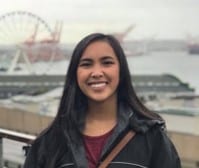
Ariel Tolentino
Project Captain
I am a graduating 4th year mechanical engineering student at Cal Poly. I am happy to have had the opportunity to work on a project that benefits the quality of life of a veteran.
Acknowledgements
We could not have done this project without help from our faculty advisor Dr. Brian Self, QL+ Project Manager Vanessa Salas, QL+ CEO Jon Monett, and our QL+ engineering mentor Don Hannula.
Our Project Videos
Our Project's Digital Poster
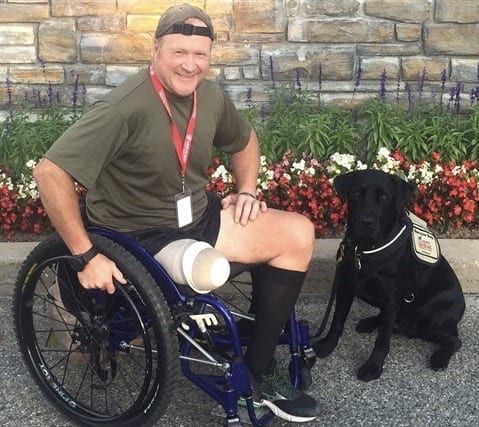
peter way and rory
Project Challenger
Problem Statement
Design a portable and compact ramp to help Rory the dog get into his owner’s truck more easily. This must be independently operated by a wheelchair user.
Why?
- Rory is getting older and Labradors are prone to joint issues
- Service dogs are expensive and time-consuming to train
Design Constraints
- Weight 25±15 pounds
- No rust
- No deflection over 10% of ramp length under 150 pound load
- Thickness 6±1 inches
- Cleaning time under 5 minutes
- Deployment time under 2 minutes
- Cost under $1000
Ramp Component Analysis
3 areas of the final design warranted concern and extra attention:
- Flat Platform Cross-Member
- Linkages
- Potential Inward Collapse
Hand calculations proved that the 3 areas would not fail under a 160 pound load on the ramp. They also showed that 1-inch square aluminum tubing with 1/8-inch walls was a solid material to use. Finite Element Analysis confirmed the findings from hand calculations.
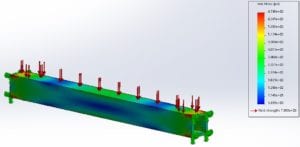
The Cross-Member on the Flat Platform is due to undergo the worst-case loading. With a total load of 160 pounds, this piece of aluminum came nowhere near its yielding point.
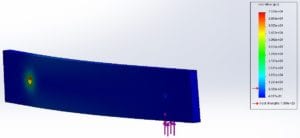
The Linkages are locating elements, but there is still a chance for misuse and a load to be placed on them. FEA once again showed we would not reach yielding.
Design Verification
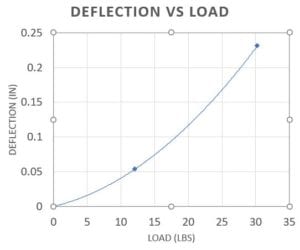
Deflection Test – Only the deflection test was completed for the ramp.We used the human biomechanics lab at Cal Poly and placed 5 sensors on the side of the ramp and determined deflection at different loads. The data was extrapolated for larger loads but it was unreliable. We planned to go back to the lab and test with heavy weights we had acquired access to, but those plans had to be cancelled.
What’s left to test?
- Weight Test – Test how much the finished product weighs
- Compatibility Test – Test how the product works with other vehicles
- Deployment Test – Test how long it takes to deploy the ramp
- Dog Test – Test how comfortable a trained dog is on the ramp
- Storage Test – Can the ramp be stored without interference?
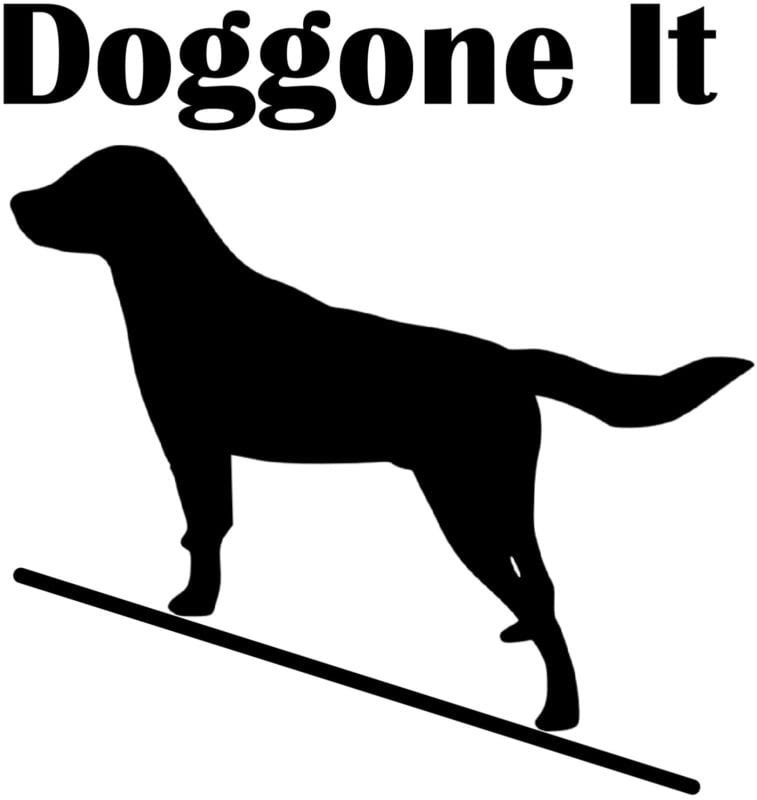
Service dog ramp
Matt Lundgren, Adam Mayeda, Dallas Rocha, Ariel Tolentino
Faculty Advisor: Dr. Brian Self
Manufacturing
The primary part of our product to be be manufactured is the flat platform and the parts that interface with it. The telescoping ramp and X-stand are purchased parts. Unfortunately, we are unable to finish all manufacturing due to the pandemic.
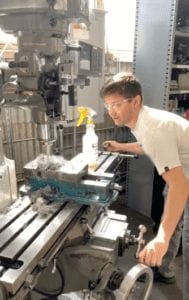
Above: Matt machining aluminum end caps.
Right: Adam showing the component layout.
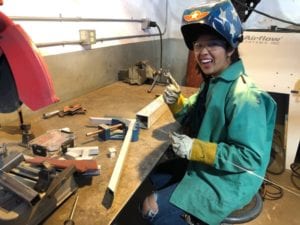
Above: Ariel practicing her welding.
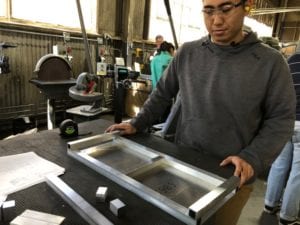
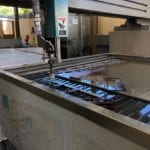
Water jet cutting linkages.
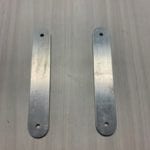
Finished linkages.
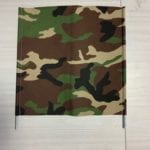
Finished canvas guard.
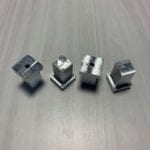
Finished end caps.
What’s left to Manufacture?
- Frame TIG Welding
- Sheet Metal Riveting to Frame
- Drilling Holes for Canvas Guard
- Coating Top, Vehicle Side, and Sharp Points with Flex Seal
- Final Interface Assembly with Purchased Components
Product Deployment
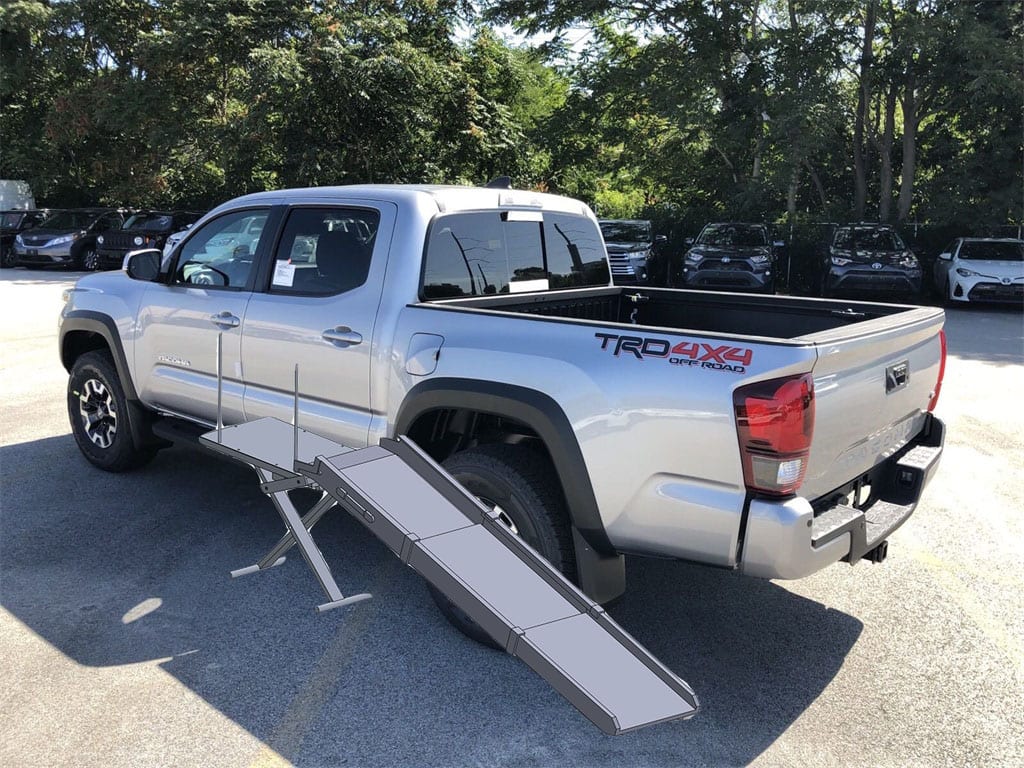
The ramp will run along the length of the truck, allowing easy use and deployment in handicap parking spaces.
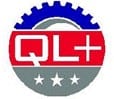
Quality of life plus
Sponsor
Project Manager: Vanessa Salas
Final Design
Specifications
Dimensions – 26” X 16.25” X 5.9”
Estimated Weight – 30 lbs
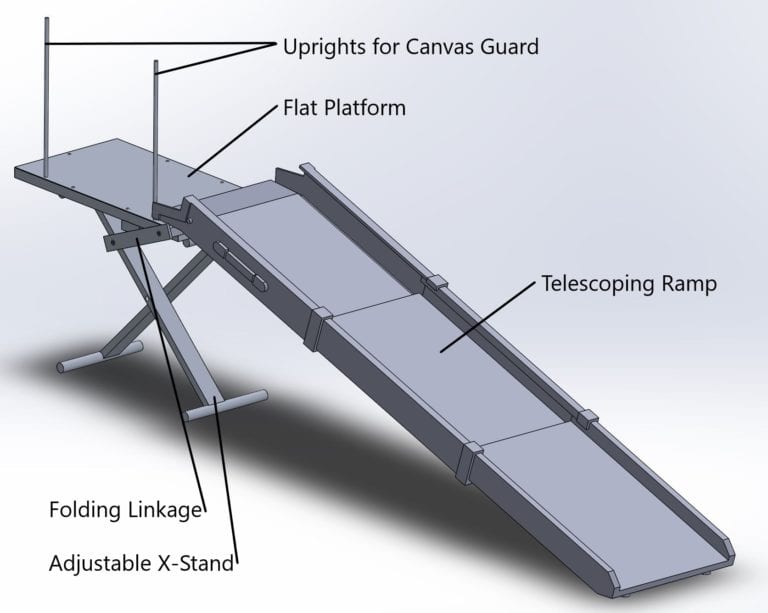
Custom Components
- Aluminum End Caps
- Linkages
- Rectangular Aluminum Frame
- Sheet Metal Cover
- Canvas Guard Rail
- Aluminum Spacers
Stock Components
- PetSafe Solvit Triscope Telescoping Pet Ramp
- Musician’s Gear Padded Piano Bench (X-Stand used)
- Flex Seal Liquid Rubber
- Bolts and Rivets
Future Application
We have talked with Dr. Brian Self and QL+ about the future of this project. Depending on how Fall Quarter 2020 pans out, Dr. Self may be able to have a project team finish the remaining manufacturing, assembly, and testing as part of his Rehabilitation Engineering course.
We have given QL+ all of our CAD files and engineering drawings so that they can continue and improve this project themselves if they choose. The pandemic does not mean that Peter and Rory don’t still need help with the problem at hand.
Conclusions
We are disappointed that we could not deliver a product to Peter and Rory, but ultimately the course of this project was out of our control. We believe that through our discussions with Peter and Vanessa Salas, this would have been a great product that Peter would have enjoyed and used frequently. We are proud of our design and the progress we made before school moved online, and we hope that whoever continues this project is able to improve upon it and put a smile on Peter’s face. Projects that directly help someone in need yield a great sense of satisfaction.
Recommendations
Improvements to be made if the ramp were to be re-designed:
- Utilize T-Slotted Framing Rails instead of relying on square tubing and TIG welding.
- Hire a machine shop technician or Kevin Williams to perform welding operations.
- Utilize fewer moving components.
- Design a cleaner aesthetic.
- Try to make the deployment involve one step only.