Our Team
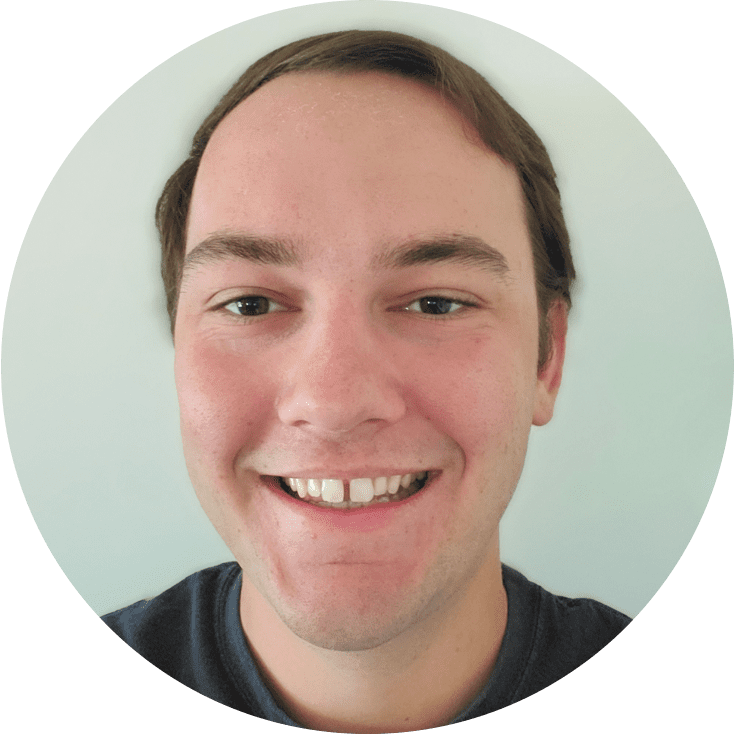
Logan Smith
Project Manager
4th Year General Concentration
Hometown: Phoenix, Arizona
Hobbies: Running, hiking, swimming, going to the beach
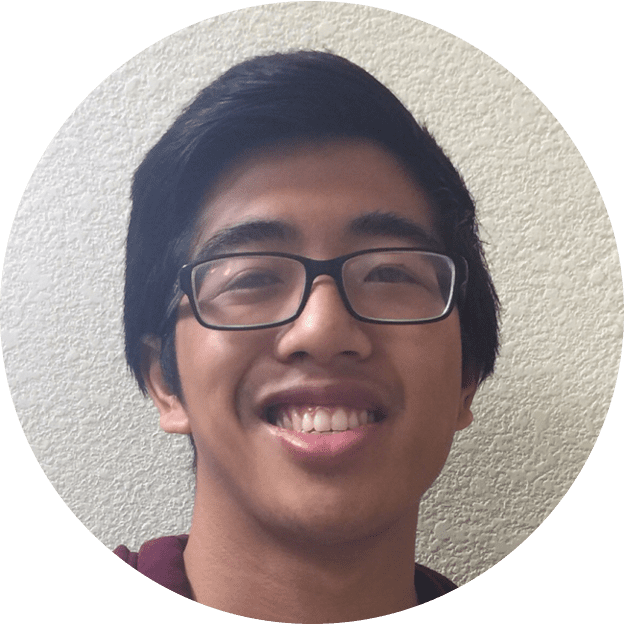
allen tecson
Mechatronics Engineer
4th Year Mechatronics Concentration
Hometown: Sacramento, California
Hobbies: Gaming, playing instruments, basketball
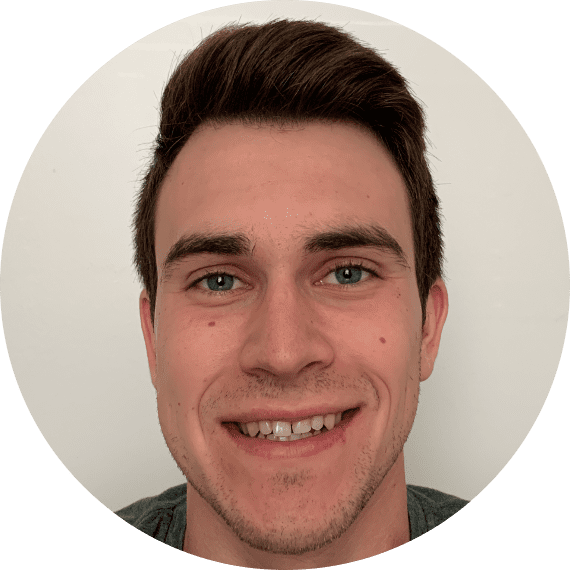
Jaret Wedow
Design Engineer
4th Year General Concentration
Hometown: Dixon, California
Hobbies: Club Baseball, hiking, going to the beach
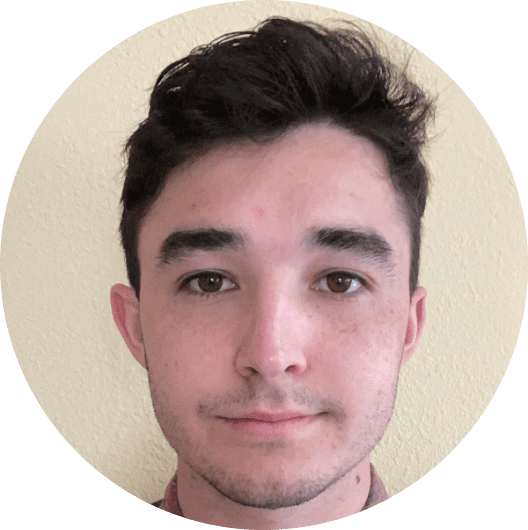
Kai Workman
Manufacturing Engineer
5th Year General Concentration
Hometown: Santa Cruz, California
Hobbies: Skateboarding, working on cars, 3D printing
Acknowledgements
Thank you to our sponsor, QL+; our challenger, Melissa Oliver; our QL+ advisor, Vanessa Salas; and our senior project advisor, Sarah Harding.
Our Project Videos
Our Project's Digital Poster
Problem Statement
Design a mug to hold 16 ounces of liquid while reducing the effect of tremors from essential tremor experienced by veterans. The mug will be able to last through a full meal, be lightweight and compact, as well as be aesthetically pleasing.
Design Constraints
- Have a carrying capacity of 16 ounces
- Reduce tremors by 50%
- Have a battery life of 1 hour
- Cost less than $200 to produce
- Weigh less than 5 pounds
- Survive a 4 foot drop test
- Have an overall size of less than 6″x4″x4″
- Have a handle with length of approximately 4″
Design Process
Phase 1:
The first design iteration compared a 2-axis and 3-axis gimbal system to counteract tremors. It was decided that a 3-axis system was unnecessary and would only increase the weight of the mug.
Phase 2:
After choosing a 2-axis system, a preliminary prototype was made that could test our controller board and motors. The prototype was large and less aesthetically pleasing than desired. This design also used threads to attach the mug liner to the mug shell which did not 3D print effectively.
Phase 3:
After printing the phase 2 prototype, many issues arose with the size and effectiveness of the motors. To improve the design, the mug liner and shell were made thinner and shorter, and new motors were purchased. A new handle was made to protect fingers from hitting the mug and the bracket was made to be more aesthetic. The threads were replaced with a key and keyway locking mechanism.
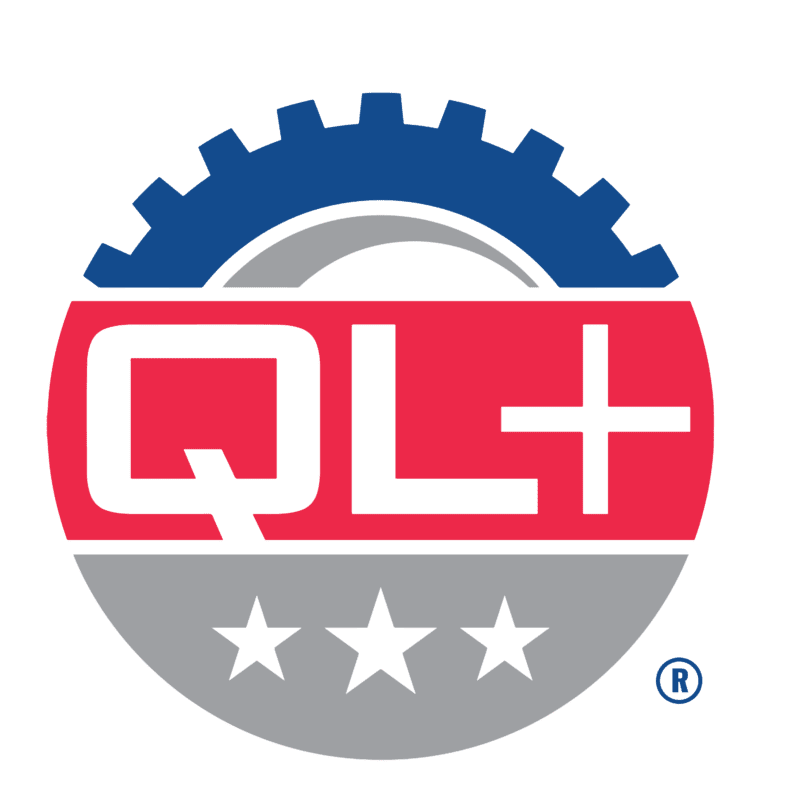
Quality of Life+
This project is sponsored by QL+
Software
In order to control the motors, open source software is used to counteract tremors. Sensor inputs are received and the software sends the corresponding signal to the motors to rotate a certain amount. Parameters can be changed in order to calibrate the electronics and counteract the tremors more effectively.
Electronics
Several electronic components are used to create an active stabilizing system. An 11.1 V battery is used to supply power to the controller board. The controller board uses inputs from sensors and stabilizing software to send power to the motors. The inertial measurement unit on the top of the fixture measures accelerations and positions to detect how the mug is moving. For our prototype, a hole was cut into the mug shell in order to more easily access the electronics for calibration and testing.
Manufacturing
All components were manufactured using PLA 3D printing. After 3D printing, the pieces were put together using mounting screws and the electrical components were connected using the appropriate wires.
Final Design
Specifications
Liquid Capacity: 16 ounces
Dimensions: 7.35” X 6.15” X 4.5”
Battery Life: 1 hour
Weight: 1.9 pounds (with 16 ounces of water)
Cost: $123.28
Custom Components
- 3D Printed Components
- Mug liner
- Mug shell
- Handle
- Motor bracket
- Mounting fixture
Purchased Components
- 2 Motors
- Controller Board
- Sensors (Inertial Measurement Unit)
- 11.1 V Lithium Ion Battery
- Mounting screws
Future Application
Currently, veterans with essential tremor are forced to use ineffective small cups or even no spill cups meant for kids. This mug can be used by veterans to drink without spilling and be aesthetically pleasing enough to bring into public. In the future, an online guide can include the 3D printed part files and other components so veterans and people living with Parkinson’s disease around the world can have access to this technology.
Recommendations
Improvements to be made if the mug were to be re-designed:
- Optimize motors to be smaller but handle the appropriate load
- Optimize the software to reduce tremors further
- Include a button or lever to allow the motors to disengage for easier drinking
- Incorporate a dishwasher safe mug liner by using silicone molds