Meet Our Team
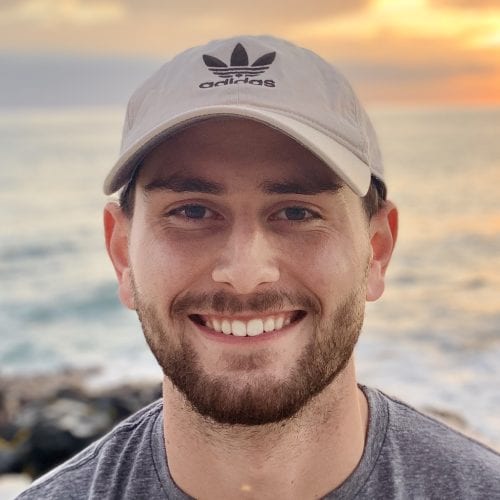
Grant Gallagher
I am a fifth year Mechanical Engineering student concentrating in Mechatronics. I was born and raised in Napa Valley, California and transferred from NVC in 2018. My professional interests include R&D, mechanical design, robotics, and control systems. In my personal time I enjoy relaxing at the beach, working out, and building anything with my hands.

Raul Gonzalez
I am a fifth year Mechanical Engineering student with a concentration in Mechatronics. I was born and raised in Santa Maria, California. I transferred from Allan Hancock College in 2018. I enjoy working with my hands, mechatronic systems , and the design aspect of solving a problem. I have been involved in the Northrop Grumman Collaboration project working with a diverse group and learning skills that will help me in my career.
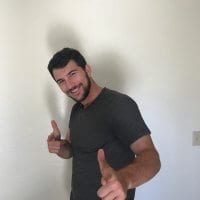
Beau Bikakis
I am a Mechanical Engineer pursuing a career as a design engineer in the automotive industry. I enjoy doing 3D modeling, running FEA simulations, and hands on machining. At Poly, I have been design lead for the Hyperloop Club and the Wind Power Design Club and I hope to put these skills to use in my professional career.
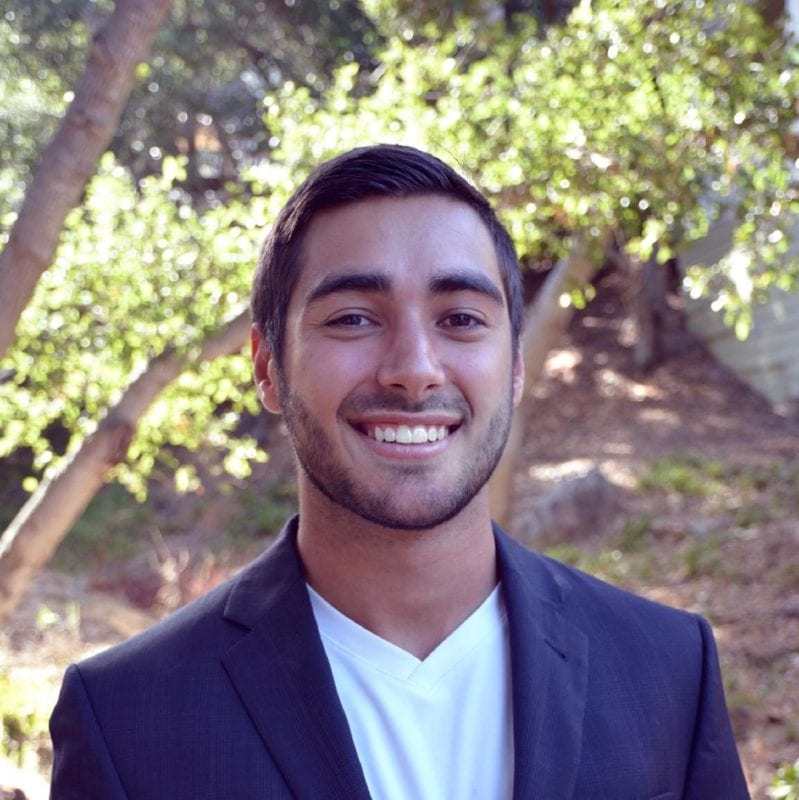
Jonathan Bergum
I am a fifth year Mechanical Engineering student concentrating in General concentration. Though, I am not a California native, I have lived here and various parts of the state for the last 9 years and transferred to Cal Poly in 2018. Ever since my first internship, I have been interested in R&D. I enjoy outdoor activities such as hiking, biking, and relaxing at the beach.
Acknowledgements
We would like to thank our project sponsors Javier Davila and Anthony Gutierrez from GAF, as well as our senior project advisor Eileen Rossman. Without their help, this project would not have been possible.
Our Digital Poster
Problem Statement
The GAF manufacturing plant currently has no method of preventing foreign objects from entering their glass fiber mixing vat. This can lead to defective products, extensive downtime, and lost revenue. The team at the GAF Shafter plant need a way to autonomously separate adulterants from the glass fibers on the production line before they enter the mixing chamber.
Design Constraints
We used the following design constraints to develop the foreign object remover:
- Safe for operators
- Removes all foreign objects of varying sizes, weights, and materials from the production line with a 100% success rate
- Does not wear down GAF’s conveyor belt
- Does not slow down production
- Be adjustable to account for higher or lower production speeds
- Easily serviceable
Initial Design Concept
Our initial design prototype centered around a belt-driven linear actuator that would drive a silicon-bristle brush across the conveyor belt at speeds great enough to prevent any material from passing through. The team at GAF had two primary concerns with this concept:
- They wanted a design that could effectively block material while active
- Material would be swept off in both directions, requiring more cleanup
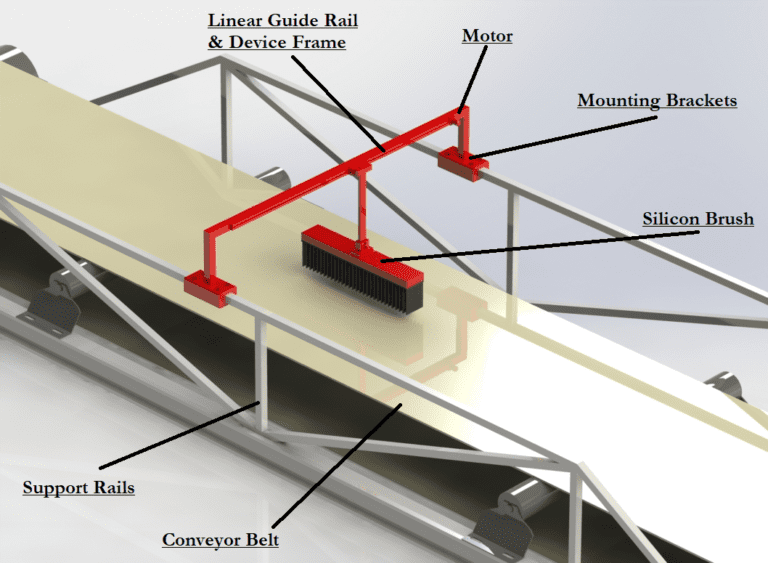
Final Design Concept
In response to GAF’s feedback from our preliminary design review, we made heavy modifications to our prototype design to satisfy their recommendations
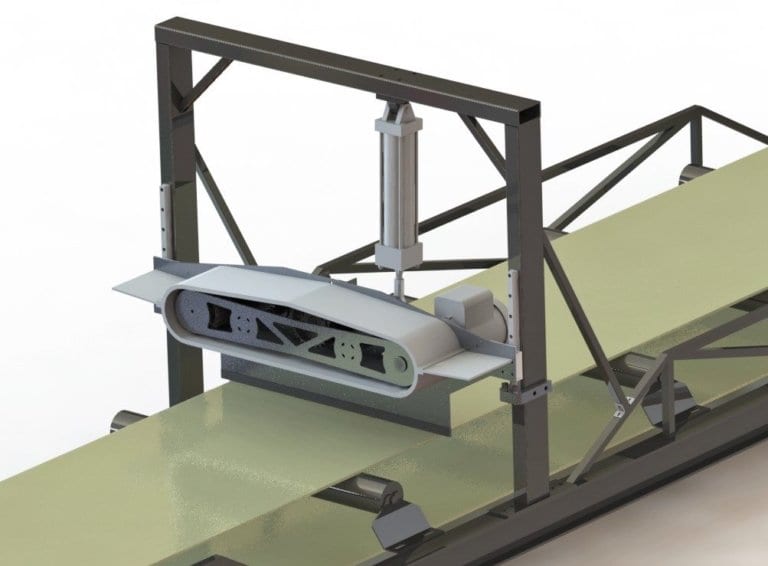
Featured Components
- Rotational sweeping mechanism
- Uni-directional sweeping motion
- Variable speed control
- Aluminum drop-down gate
- Blocks fiberglass and foreign objects
- Bottom lined with stop mat to prevent conveyor belt wear
- Steel 2″ x 4″ frame
- Bolt-on integration to production line
- Heavy-duty nylon bump-stops
- Prevents gate from damaging conveyor belt
- 1.5″ of adjustability
CAD Model
Due to the nature of online collaboration, we focused extensively on designing a model that was precise and accurate. We based our dimensions on a combination of engineering drawings and measurements sent from GAF. Pictured in the slides below are detailed images of subassemblies/components for our final design concept.
Not including nuts and bolts, there are a total of 168 solid components in our CAD model. All slots and holes were designed with proper tolerances in mind to ensure that each component could fit together with ease. For a better understanding of how the design fits together, the animation below depicts the exploded animation of the wall and drivetrain subassemblies.
All shafts and sprockets are held in-place by external snap rings and ridges. For an additional safety factor, the sprockets include set-screws that further prevent them from walking.
Computational Analysis
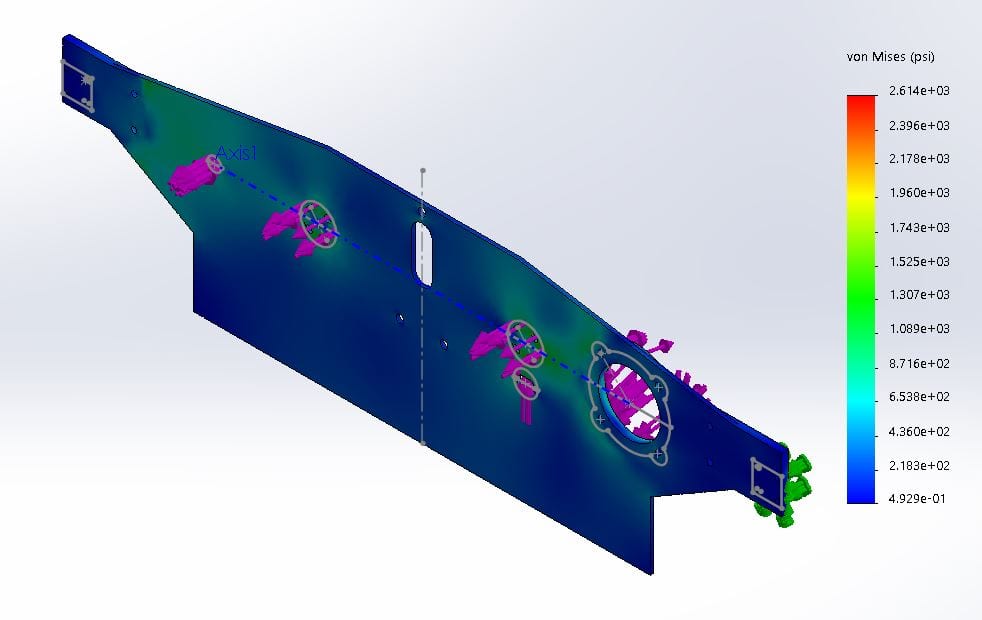
To ensure that there would be no material yield due to the loading of the motor, slat-top, and weight of the components, we performed FEA on the aluminum wall and steel support plates. Through our analysis, we determined that the loads would be acceptable, with a factor of safety of over 4.
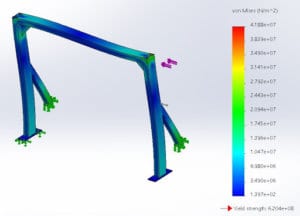
A 500lbf load was applied to the top-right side of the frame. The frame yielded a conservative factor of safety of 14.8.
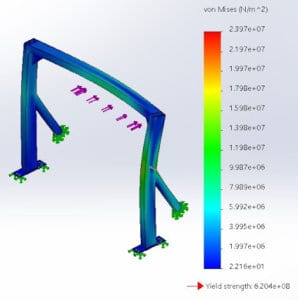
A 500lbf load was applied to the top-front face of the frame. The frame yielded a conservative factor of safety of 25.9.
Hand Calculations
Sweeping Parameters
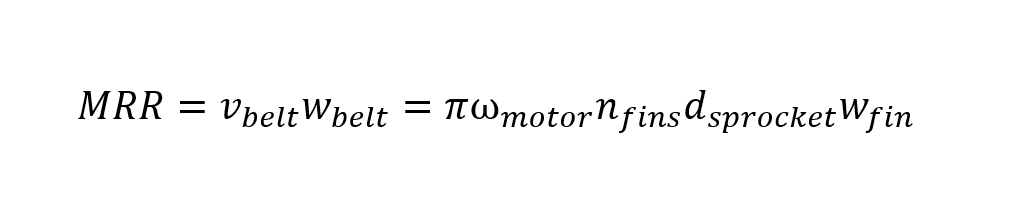
The Material Removal Rate (MRR) is the rate of area that the prototype is able to sweep, in square feet per second. To prevent pile-up, the area rate of the conveyor belt must be equal to the area rate removed by the fin. After various tests and discussion, we determined that our prototype would use: 2 fins, a 6in sprocket, 7in wide fin, and a motor capable of spinning at least 200rpm.
Pneumatic Cylinder Sizing
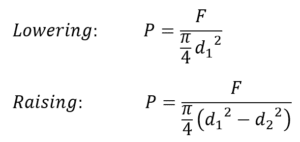
Double-acting cylinders exert different levels of force in each direction because the piston reduces the surface of area one face of the piston. Using a conservative 400lb dynamic load and 100psi pressure supply, we determined a 3″ pneumatic cylinder with a 3/4″ piston would be sufficient for our design.
Weld Strength


To ensure that the welds would be able to withstand the expected loading, we performed weld calculations at critical points using the eq’s above – we determined the lowest factor of safety to be 11.4
Manufacturing
Due to Covid-19, we incorporated as many off-the-shelf parts as possible, reducing the amount of time needed in the shops to account for the limited access. For more pictures, please visit our project gallery at the below our poster.
Parts Manufactured from Scratch
- Clevis adapter
- Test stands
- Fins
- Fin holders
- All three shafts
- Snap-ring groove tool
Parts that were Modified
- Drilled holes in support flanges
- Trimmed slat-top width
- Slotted guide rail mounting holes
- Drilled mounting hole in wall for ball-joint connection
- Extended aluminum bracket threads
- Enlarged steel motor mount bracket
Testing
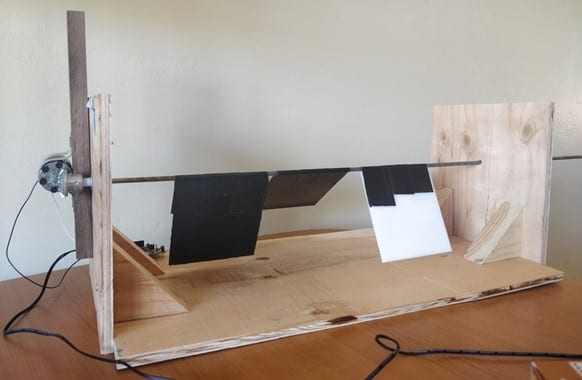
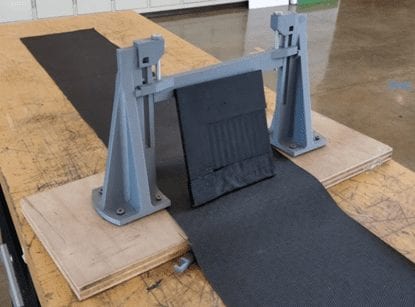
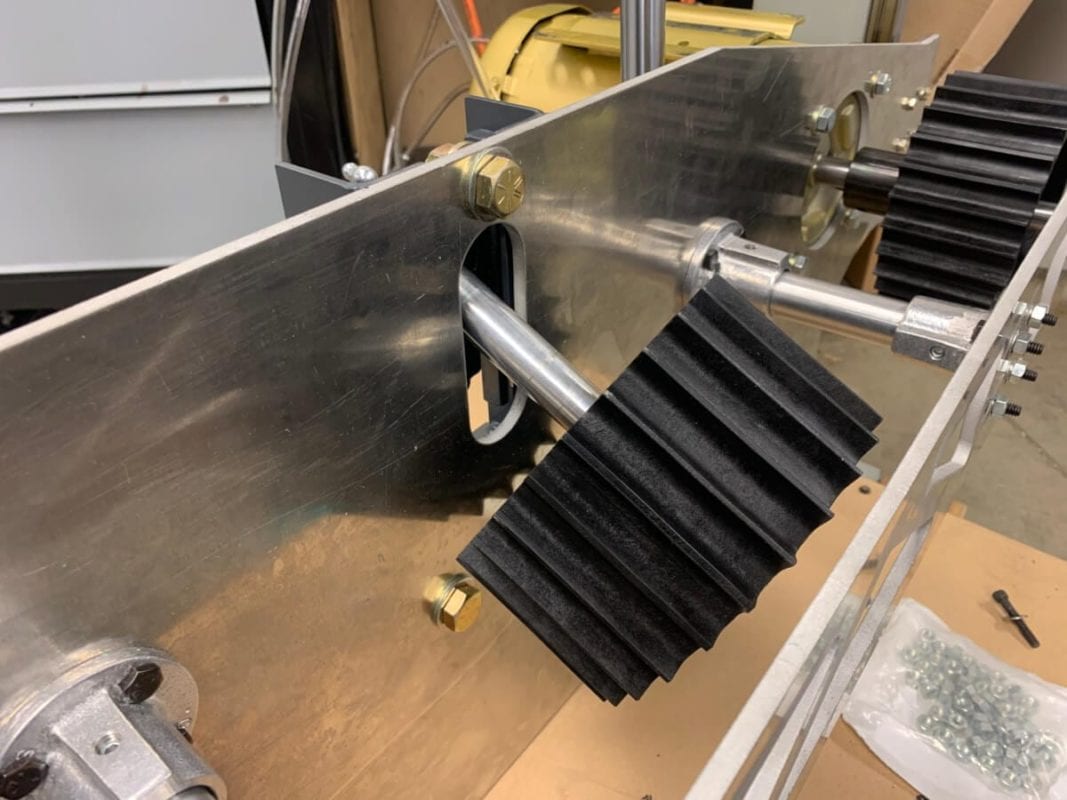
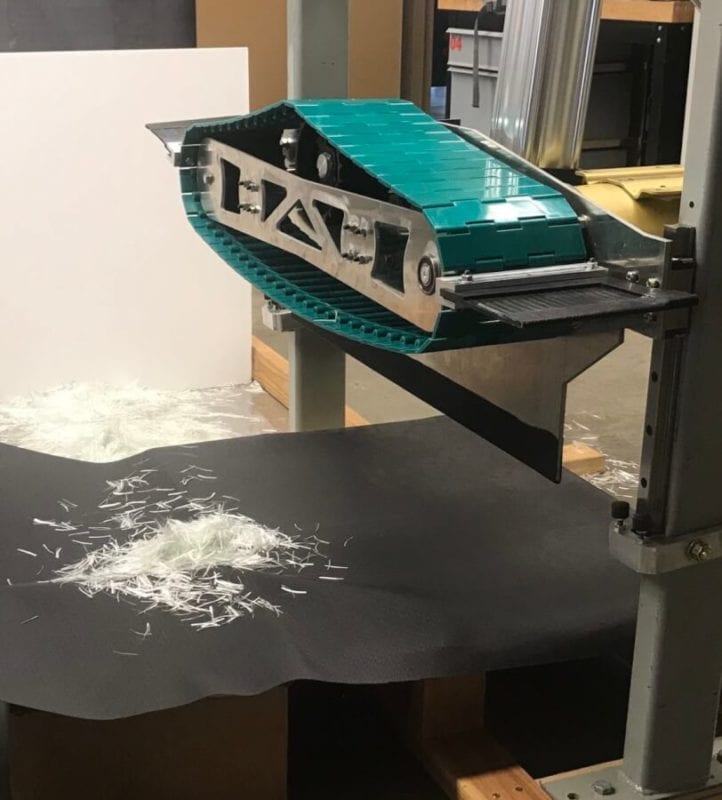
The Final Design
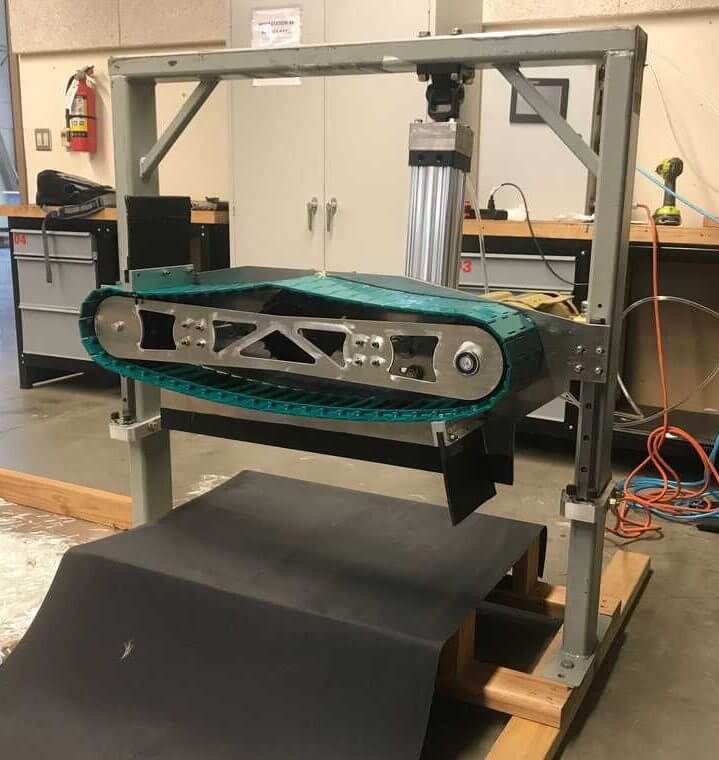
Specifications
Weight – 204 lbs
Physical Dimensions – 18″ x 4′ x 4′
Actuating Time – 1.2s
Fin Speed – 0ft/s to 2700ft/s
Electrical Power Supply – 120 VAC
Air Supply – 20psi to 80psi
Demo
Below is a short video demonstrating the how to prototype behaves when it is activated. Once a signal is sent to the control box, the pneumatic cylinder lowers the sweeping mechanism and the fins sweep across the conveyor at a user-defined speed.
As shown in the video, a thin credit card and 1/2″ bolt replicate foreign objects being swept away by the prototype. Less noticeable, the slat-top has slack because of the broken tensioner shaft bearing. This problem prevented us from performing subsequent tests.
Components
Custom Components
- All Shafts
- Bumper Brackets
- Clevis Adapter
- Frame
- Wall
- Faceplate
- Fins
- Fin Brackets
- PLC lockbox
Off-the-shelf Components
- Pneumatic Cylinder
- Motor
- Linear Guides
- Tensioner
- Clevis
- Bearings
- Fasteners
- Slat-top Chain
Recommendations
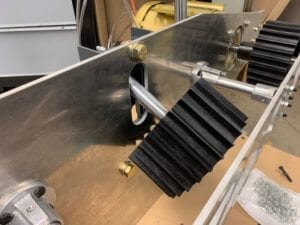
Improvements to be made if autonomous foreign object remover for glass mat fiber feeder if it were to be redesigned :
- Shafts should be made 3/8″ in longer to keep the slat top chain from hitting the wall bolts.
- Reduce the number of snap rings needed by adding shoulders to the drive and tensioner shaft to keep the sprockets in place.
- Replace the motor with a smaller, more efficient BLDC motor.
- Increase the rigidity of the fins by adding additional support or changing material. Rubber fins work well with small clumps of fiberglass but flex too much with larger clumps and does not remove all material.
- Reprogram the control box to include bidirectional control of the motor rather than fully extended/retracted. This would add more adjustability and control of the gate.
- Additional mount for the tensioner shaft so it can with stand the cantilever force and provide higher tension to the belt.
- Include some form of auditory/visual cue that would notify workers that the device is moving (sirens or lights).
Conclusion
Over the course of a year, our team invested countless hours of hard work and dedication to design, build, and test a prototype that could solve GAF’s problem of foreign objects adulterating their glass mat process. Initially we intended for the prototype to be ready-to-integrate into their existing production line as a polished product. However, we encountered numerous obstacles in regards to the Covid-19 pandemic. We had to adjust to various new school/business policies, were unable to access the machine shops as much as needed, and had difficulties meeting in-person. As a result, our project timeline was set back on multiple occasions. Despite not having enough time as we would have liked, we are proud of what we have been able to accomplish.
With lots of modifications, we were able to construct what we envisioned gather the testing results needed. Late in the process, we discovered an issue with the tensioner shaft bearing that prevented the prototype from operating adequately. Although out of time, we have left GAF with recommendations that can help finalize the prototype design. We believe that with light modification, the final design prototype will be suitable for implementing on the GAF production line – removing foreign objects, preventing damage, reducing downtime, saving money.
References
Alblaihess , Mohamad, et al. Designing a Robotic Arm for Moving and Sorting Scraps at Pacific Can, Beijing, China. pp. 1–139, Designing a Robotic Arm for Moving and Sorting Scraps at Pacific Can, Beijing, China.
Behymer, Lance E., et al. Conveyor Belt Cleaning System. 3 Oct. 2006.
Cole, Michael. Foreign Object Separation Apparatus. 20 Mar. 1990.
“Conveyors and Full Materials Handling Systems from Australia’s Leading Specialist Conveyor Manufacturer.” Adept Conveyors, Adept Conveyor Technologies, adeptconveyor.com.au/.
“Food Conveyors: Conveyor Equipment for Food Handling: AMBiT.” Ambit Projects, Ambit Projects Limited, ambitprojects.co.uk/equipment/food-conveyors/.
Gmbh, Sesotec. “Recycling Sorting Systems with Conveyor Belt.” Sesotec, www.sesotec.com/na/en-US/products/groups/recycling-sorting-systems-with-conveyor-belt
Iguider, Youssef; Kornbluh, Roy; McCoy, Brian; Pelrine, Ronald; Prahlad, Harsha; Von Guggenberg, Philip, et al. Active Electroadhesive Cleaning. 17 Nov. 2015.
International, ASTM, editor. “ASTM Standards.” Standard Guide for Inspecting Crosscut, Sweep-Arm, and Auger Mechanical Coal-Sampling Systems for Conformance with Current ASTM Standards, vol. 7, 2003.
Kale, Vishnu R, and V A Kulkarni. “International Journal of Advanced Research in Electrical, Electronics and Instrumentation Engineering .” OBJECT SORTING SYSTEM USING ROBOTIC ARM, vol. 2, no. 7, 7 July 2013, pp. 1–8.
Loma systems: What reject system is right for my application? (2019). Retrieved January 28, 2020, from https://www.loma.com/en-US/About-Us/News-and-Press-Releases/What-reject-system-is-right-for-my-application
Long, Arthur J, et al. Foreign Object Removal System for a Coin Processing Device. 21 Oct. 2008.
Peariso, D. (2006). Preventing Foreign Material Contamination of Foods.
“Pie Separator – AquaPruf Conveyor.” YouTube, Dorner Surveyors, 26 Oct. 2011, www.youtube.co.m/watch?v=TUzs6xykXmw.
“The Art of Sortation in the Conveyor Industry.” YouTube, YouTube, www.youtube.com/watch?v=SMEQgGcl1ik.
“Tomato Sorting Machine Sentinel II – TOMRA Sorting.” YouTube, YouTube, 11 May 2016, www.youtube.com/watch?v=j4RWJTs0QCk.
Tomra. “Sentinel II Optical Food Sorter.” SENTINEL II SORTING MACHINE BY TOMRA, TOMRA, www.tomra.com/en/sorting/food/sorting-equipment/sentinel.
“WHICH ONE TO USE? NATURAL OR SYNTHETIC BRISTLES.” Banner Systems, Banner Systems, 19 June 2013, bannersystemsma.com/which-one-to-use-natural-or-synthetic-bristles/.
Wilmo, Michael, and Joseph Krueger. Self Cleaning Conveyor with Roller Scraper and Debris Reduction Skirt. 9 Jan. 2007.
여정동 . Debris Removal Devise. 30 Sept. 2019.
김현춘 , et al. Refuse Sorting Structures of Intermediate Handling for Disposal of Construction. 29 June 2007