Our Team
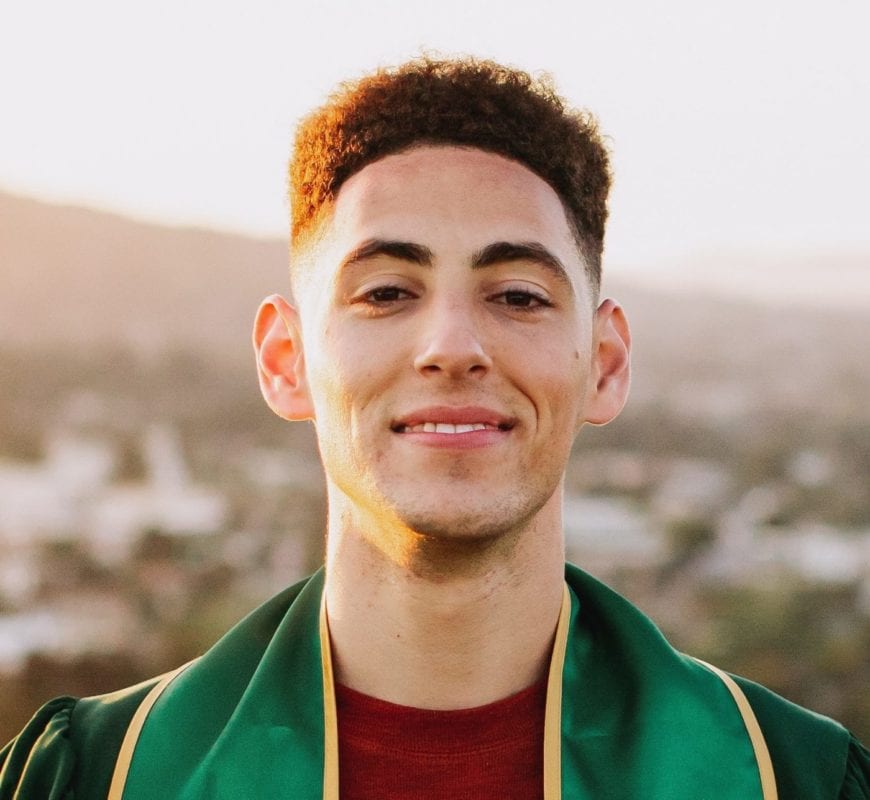
Camden Boshart
My background includes a bit of vehicle design through multiple years working with Cal Poly Racing on campus with the driver controls team. My time working on Cal Poly Racing’s two formula cars gave me an interest for anything involving wheels and specific experience with driver interface and steering. With such a background, I was immediately interested in working on a bicycle, especially on a project that directly affects the ride and response of the vehicle.
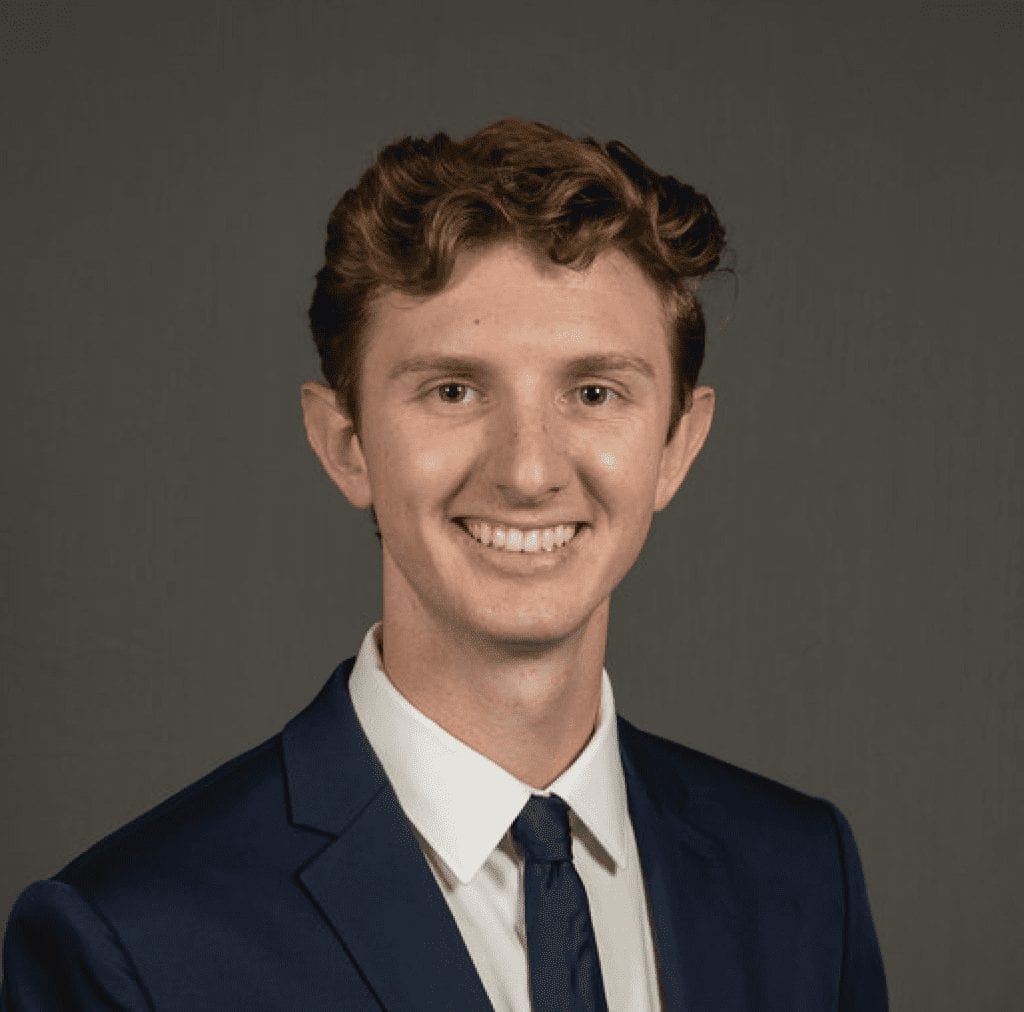
Drew Drees
As a member of the Cal Poly Cycling team and frequent mountain/road rider, I hope to bring a unique perspective to our team. This project highlights my interest in component design as well as improving the user experience. I plan to call upon my previous experience as an intern for a Bay Area public works construction management firm to set and achieve the goals necessary for success.
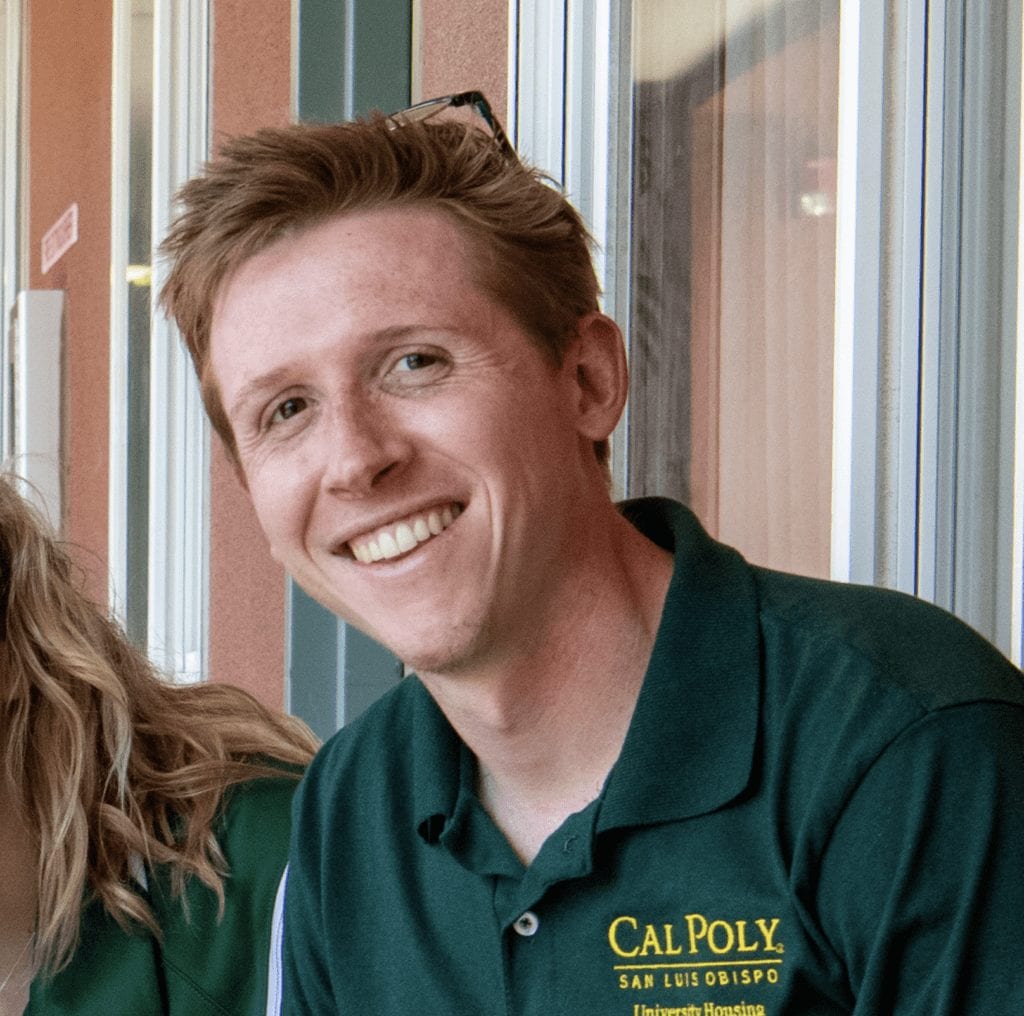
Matthew Mounteer
As an avid cyclist and general outdoor enthusiast, I was excited to apply the skillset developed in my design classes to this project and hopefully draw new users to the wonderful world of bikes. I am passionate about visualization as well and was able to use my skills in 3D animation to successfully communicate complex mechanical designs shown in the GIFs below. I was excited to sink my teeth into this project as it highlighted my interest in part design, visualization and modeling.
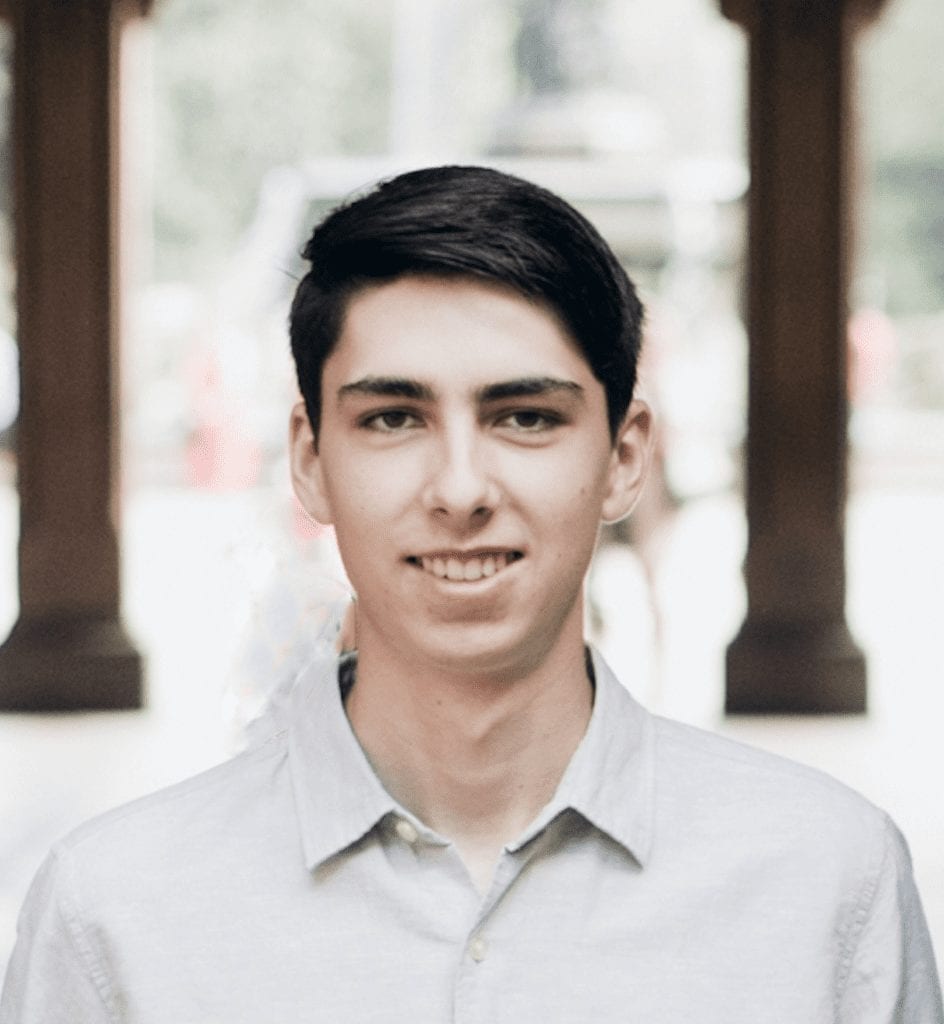
Jonah Masumoto
I have a lot of passion for two wheeled vehicles, from some exposure to mountain biking to more experience with motorcycles and dirt bike riding. I plan to offer a unique perspective to this project from these interests. I am hoping to add to the team some of my manufacturing experience from the Cal Poly Racing Baja team and fabrication of parts.
Acknowledgements
Special thank you to Professor Kean for his guidance and support through the design, build, and testing process. His enthusiasm and passion for our project topic took this design to the next level, enabling our team to work creatively while developing the best possible solution. Thank you, Professor Kean.
Our Project's Video
Below is a project video provided to give a quick overview of our team’s design and how it was created. This video also provides a look at some of the design verification testing and results
Our Project's Digital Poster
Problem Statement
Mountain bikes have extremely slack geometry in their design which causes the unfortunate effect of fork flop when climbing up hills and inclines. This phenomenon makes climbing up hills at a slow speed more difficult and even impossible at times. To correct this flop, a device is required to counteract the forces created on the bike due to its geometry.
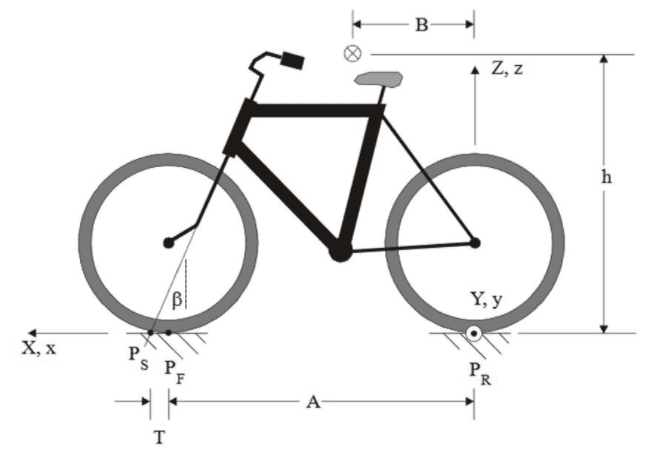
- Fork flop is described in depth in the Patterson Control Model for bicycle stability and handling which uses the upper dimensions to develop an equation for fork flop.
Engineering Specifications
This Design must satisfy the following:
– Decrease fork flop moment when device is installed
– Maintain 80% of function under elevated heat
– Maintain 80% of function under muddy/wet – conditions
– Install time < 20mins
– Adjustment time < 60s
– Weight < 2 lbs
– Volume < 57 in3
– User Feedback > 75% satisfaction
– Aesthetics > 75% satisfaction
These specifications were determined based on user needs and the intended direction of the sponsor. A rigorous evaluation process using a House of Quality approach was taken to decide on specific values for certain targets. Some values changed with the design.
Mechanism Description
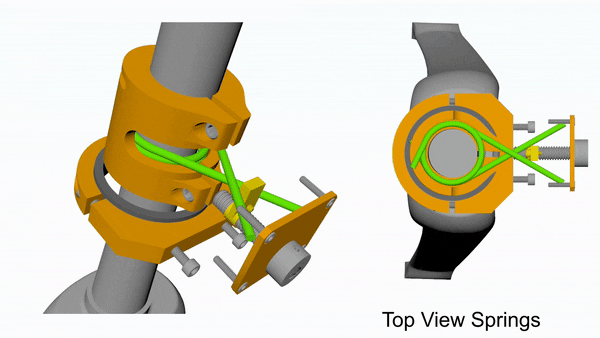
Torsion springs tucked inside of two spacers are engaged depending on the direction of the handlebar turn. When not engaged, the other leg of the torsion spring slides in a slot on the rear side of spacer as shown below.
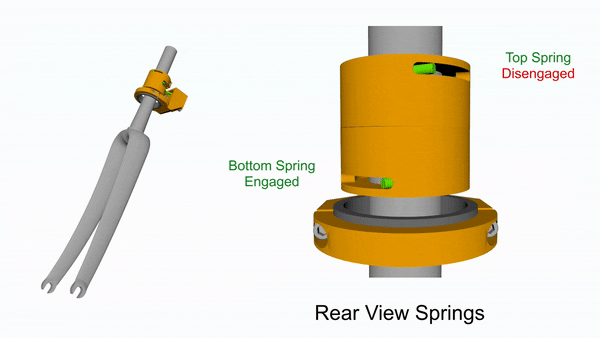
Lead screw mechanism
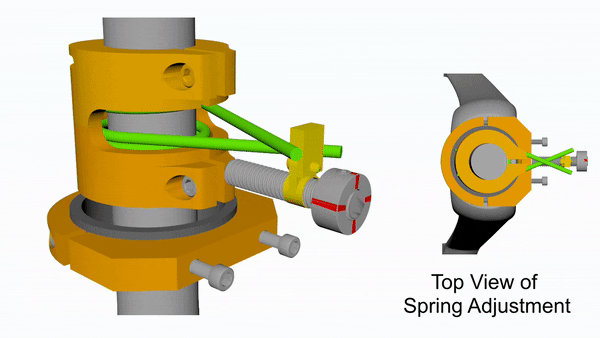
Rotating the lead screw allows for the user to change the position of the adjustment tab. When this tab is nearest to the spacers and steerer tube, the rider will experience the largest correction for fork flop. When backed all the way out, the least amount of correction will be provided.
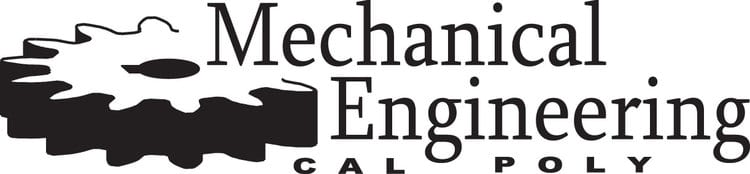
Project Sponsor
This project is sponsored by Professor Andrew Kean of Cal Poly's Mechanical Engineering Department. Professor Kean is an active mountain bike enthusiast who has a passion for improving rider experience.
Design Description
Completed Design
Our final design uses two torsion springs that counteract unwanted steering moments about the steering axis. These springs are fixed to the bike using custom spacers. Our design also makes use of a clamp attached to a housing, which interacts with the spring legs in order to provide the necessary spring forces.
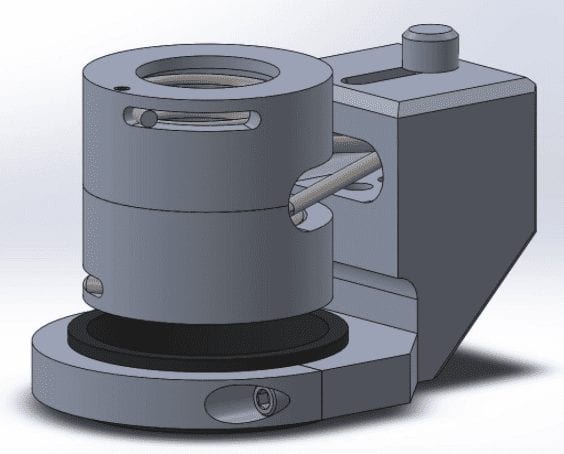
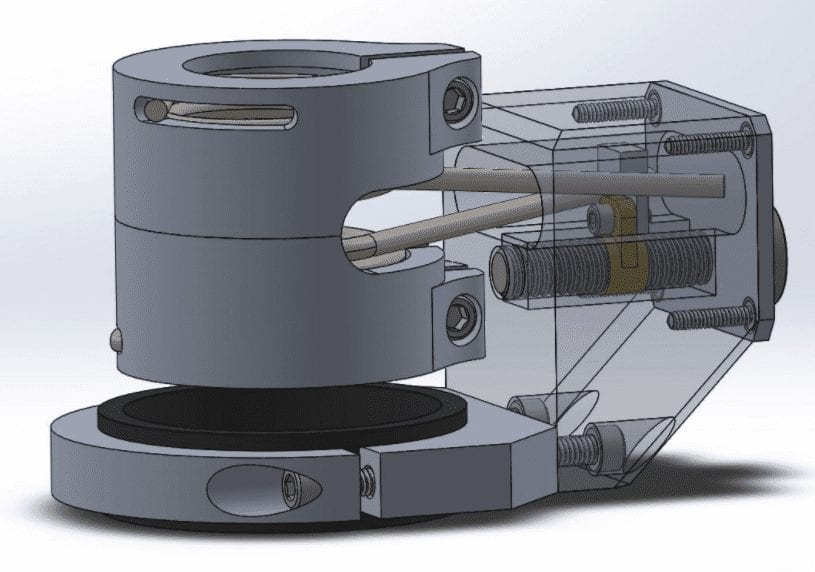
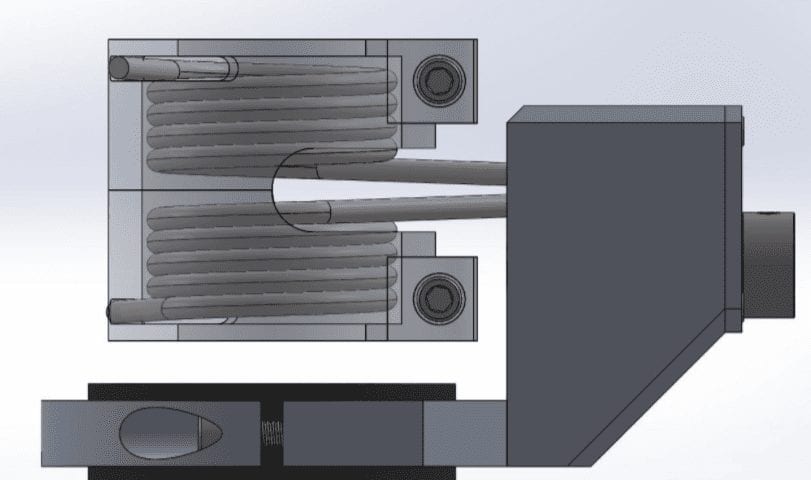
Views of the torsion springs tucked inside of spacers and sticking out into the main housing.
Manufacturing
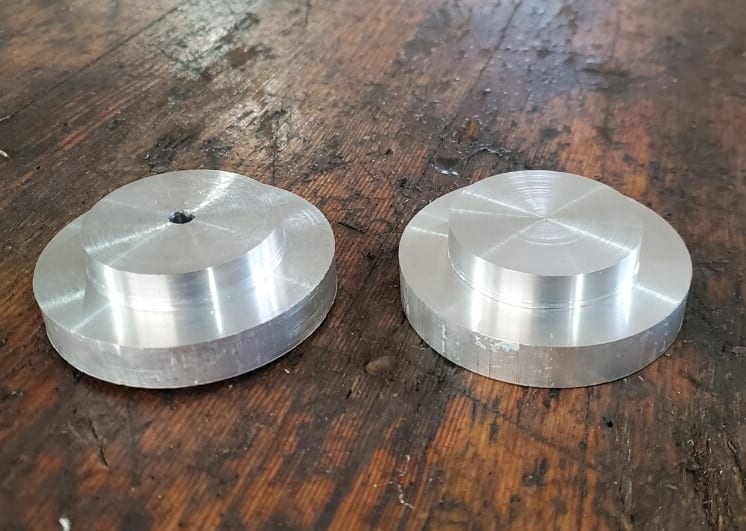
Two aluminum blanks cut from a rod of aluminum were turned down to their proper size to ensure the lamp arms would be able to be made.
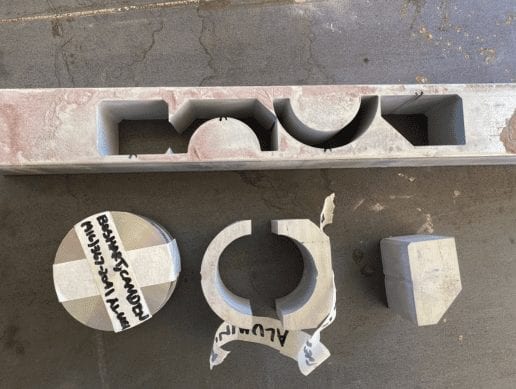
The initial profiles of all parts manufactured were cut from the bar stock using a waterjet. To complete the housing and clamps, manual milling techniques were used.
Machining and completed Assembly
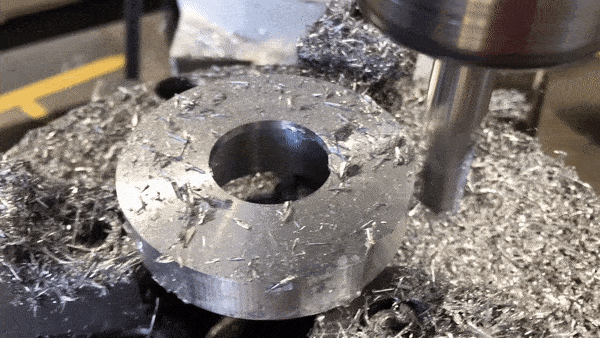
Rotary Chuck- Milling precise slots over in a circular path so that our springs can fit into the spacers required a rotary chuck. This chuck can rotate a certain number of degrees while the milling tool is stationary, allowing the slots to be machined for the designed sweep of 180°.
Milling the housing cavity – A 0.5” x 0.5” centered cavity was added to the existing cavity to provide space for the lead screw to run through.
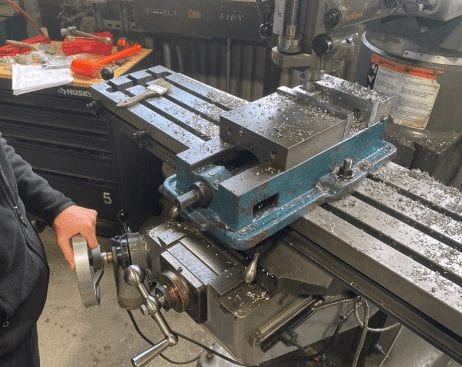
Machining the cavity for the torsion springs and lead screw. Manual milling techniques were most commonly used in the manufacturing.
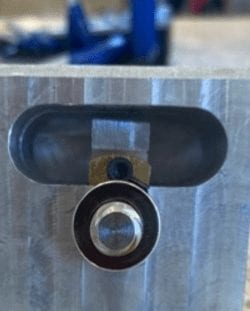
Pin assembly showing lead screw, lock collar, square nut, and pin.
Completed Assembly
Specifications
Weight – 0.970 pounds
Volume – 7.88 in^3
Moment Reduction – 38.6%
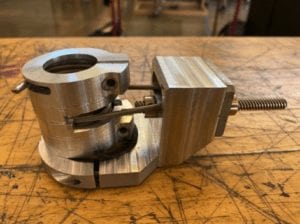
Testing and Results
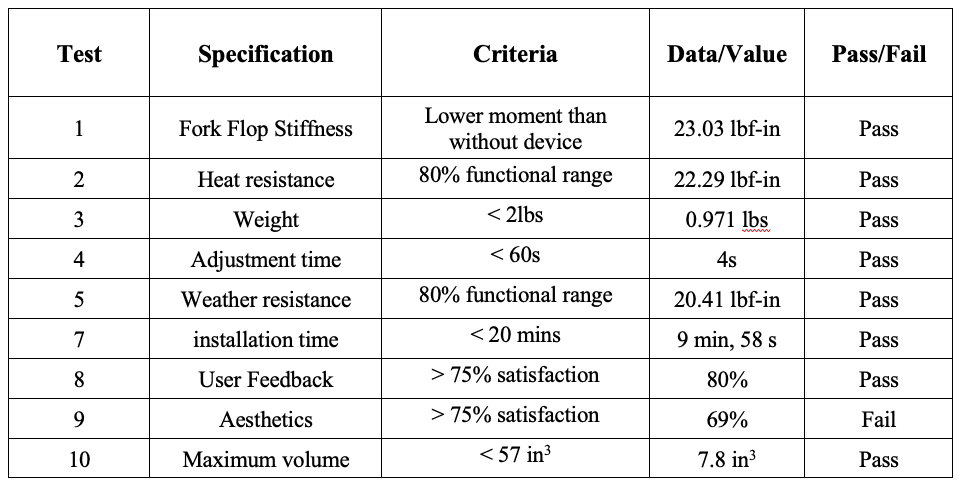
Specifications set fourth at the beginning of the project managed to be mostly met after completed testing.
The fork flop equation was used as a starting point for analysis and test results. Ideal testing would have involved calculating a nominal value for fork flop of the test bike and then performing an experiment to measure fork flop and compare. However, fork flop is a difficult phenomenon to measure and therefore moments about the steering axis were measured instead because fork flop is essential a moment about the steering axis.
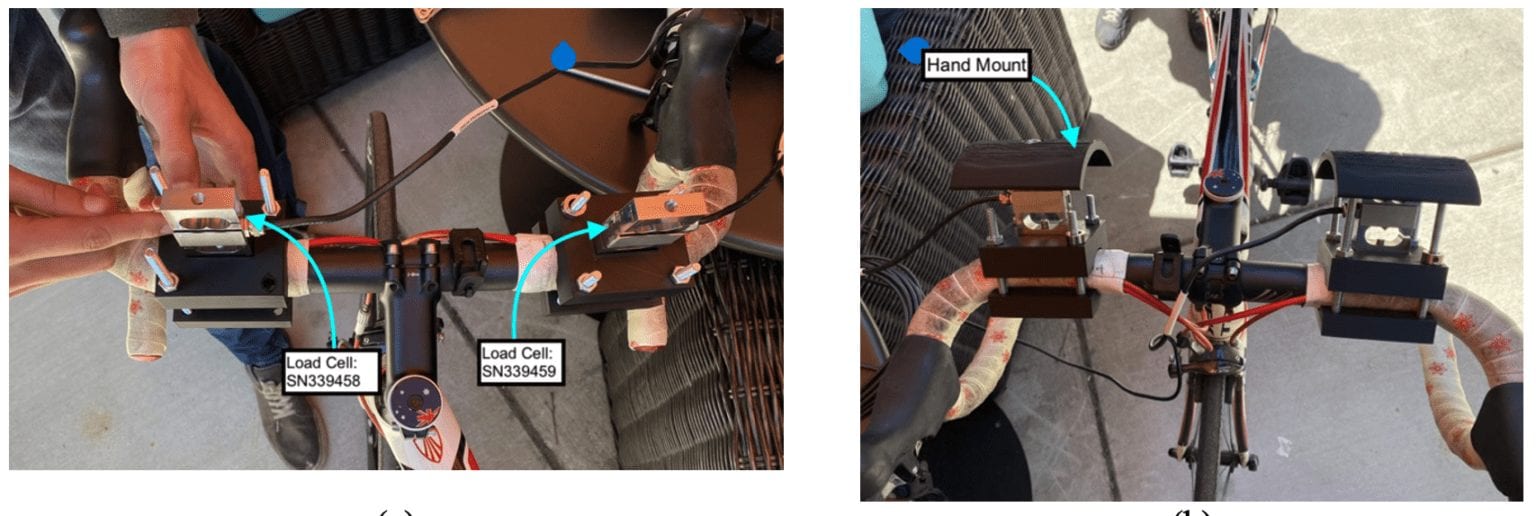
Multiple tests were conducted to measure the moment about the steering axis using load cells. Data was taken with the adjustable headset on and off the mountain bike and the results were then compared to data taken on a safety bike with a standard head tube angle. The results can be seen in the table below.
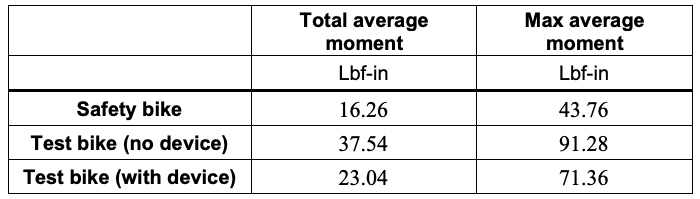
Additional Test Results
Design Verification
From the testing conducted without the device installed, we saw a peak moment close to 100 lbf-in. This plot was used as a baseline for the improvement we expect with the device installed.
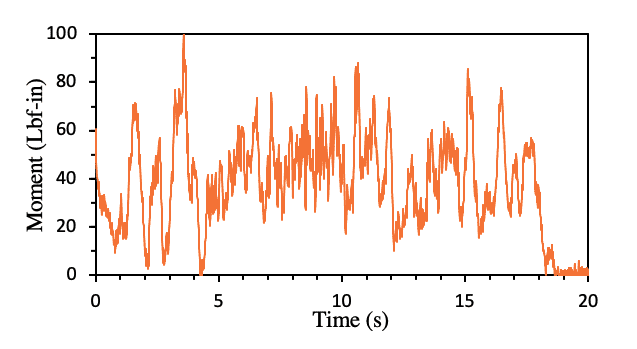
Data recorded from one of the load cells without the device installed. The image below shows data recorded from one of the load cells with the device installed and a significant decrease in moment can be observed. After installing the device on the bike, we saw almost a 40% decrease in steering moment applied by the rider. We are able to conclude that fork flop decreases when the device is installed.
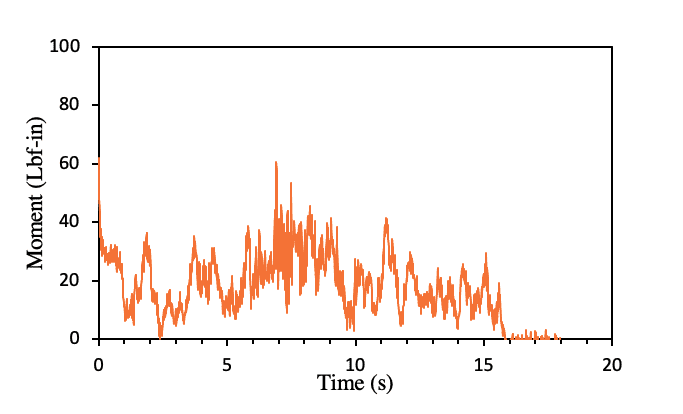
Future Applications
The geometry of mountain bikes change as riding styles change. With current head tube angles becoming increasingly slack, we find the need to correct fork flop more important. For future designs and improvements, this device will be fully integrated into the headset and be internal to the head tube. This is vastly improve the aesthetics of the assembly on the bike and allow for riders to buy complete bikes that use utilize this solution.