Our Senior Project Team
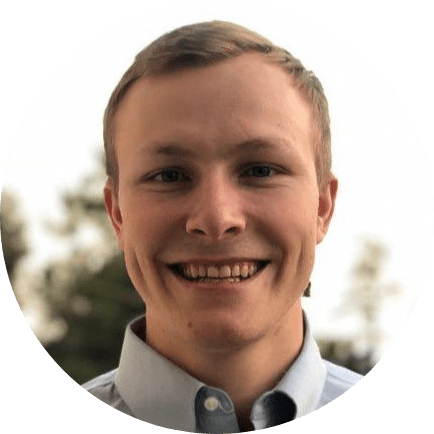
James Andrews
Pleasant Hill, California
I really enjoyed working on this project because designing an electric grill was a perfect mix of product design, electronics and heat transfer. The project was challenging, but very enjoyable. I felt that I learned a lot about the engineering design process and am so thankful to Bull Outdoor Products for the opportunity to work on such a great project. Outside of school, I like playing sports, videos games and travelling.
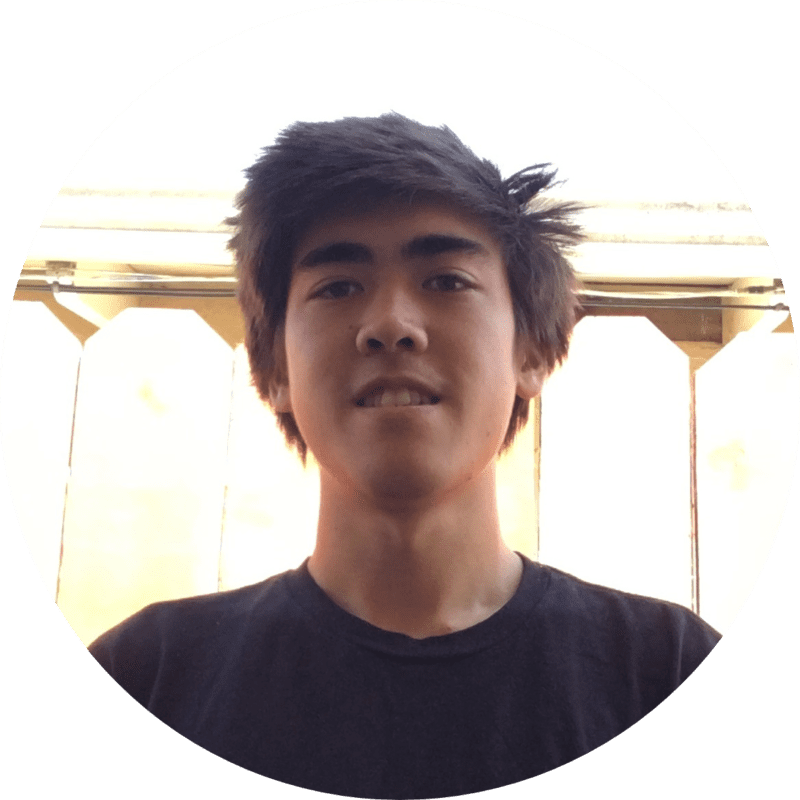
Makai Baker
North Shore Kauai, Hawaii
I’ve always enjoyed cooking and wanted to delve deeper into the world of product design. This project was a great segue into this world and I’ve learned a lot about how much really goes into it. Outside of school and work, I enjoy skateboarding, the outdoors, listening to and collecting rare records, and making hip-hop beats.
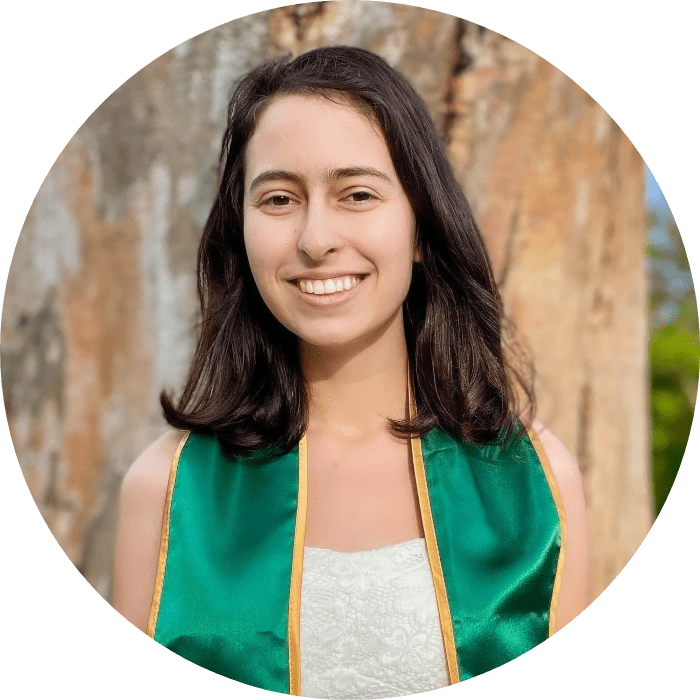
Sofie Groberman
Northridge, California
I am a fourth year Mechanical Engineering major with a concentration in Energy Resources. I have always liked cooking and love how grilling can be a social activity that brings people together. This project taught me a lot about product design, and how much work goes into every component of the grill to create a functional product. In my free time, I like hiking, reading, and trying new cuisines.
Acknowledgements
Our team would like to thank our advisor Sarah Harding for pushing us to succeed without being overbearing (and giving us doughnuts). We would also like to thank our sponsor Frank Mello and his team from Bull Outdoor Products for giving us feedback and motivation throughout the project.
Thank You!
Our Project's Videos
This was a video that was made to show how we envisioned our product to look like and be used, before it was manufactured.
This video goes through the design process of the grill, the components that are involved, and the results of our testing.
Our Project's Digital Poster
Our Objective
Bull Outdoor Products customers need a premium, high temperature electric grill with even heat distribution because they want to barbeque in their back patios and balconies without the increase in fire insurance costs that is associated with installing a conventional gas grill.
Design Constraints
- Use wall power at 120V, ~11A
- Reach temperature above 500 °F
- Weigh less than 50 lbs
- Give conventional grilling experience
Ideation
- Initially, we created several sketches as to what we envisioned our product to look like.
- We also created a structural prototype out of wood and other grill components. This was to get an idea of how big we wanted our grill to be, as well as how the components would come together.
Design
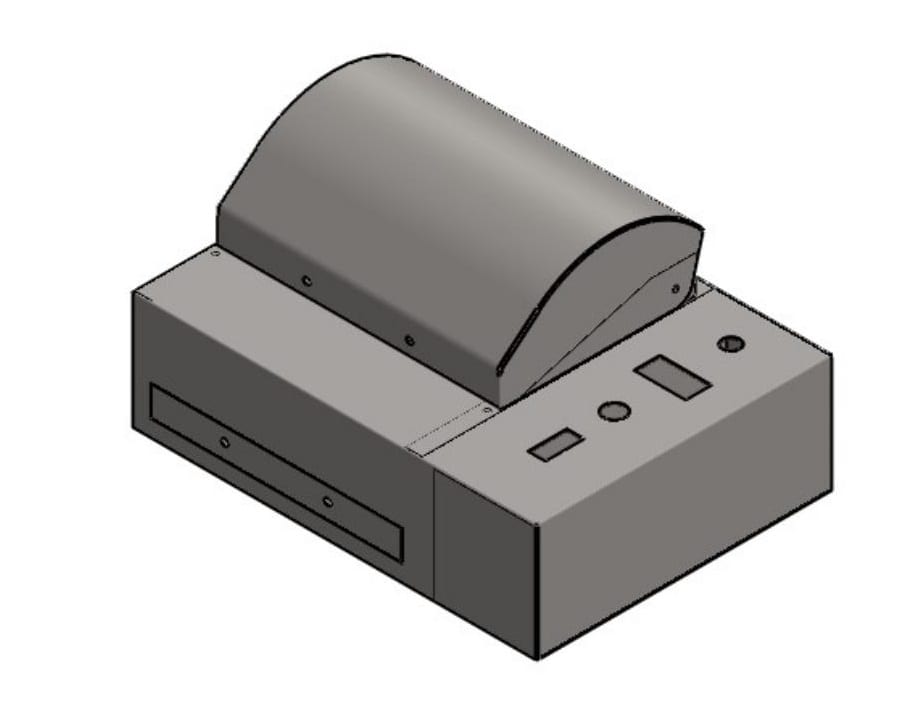
CAD model of assembled grill created in SolidWorks.
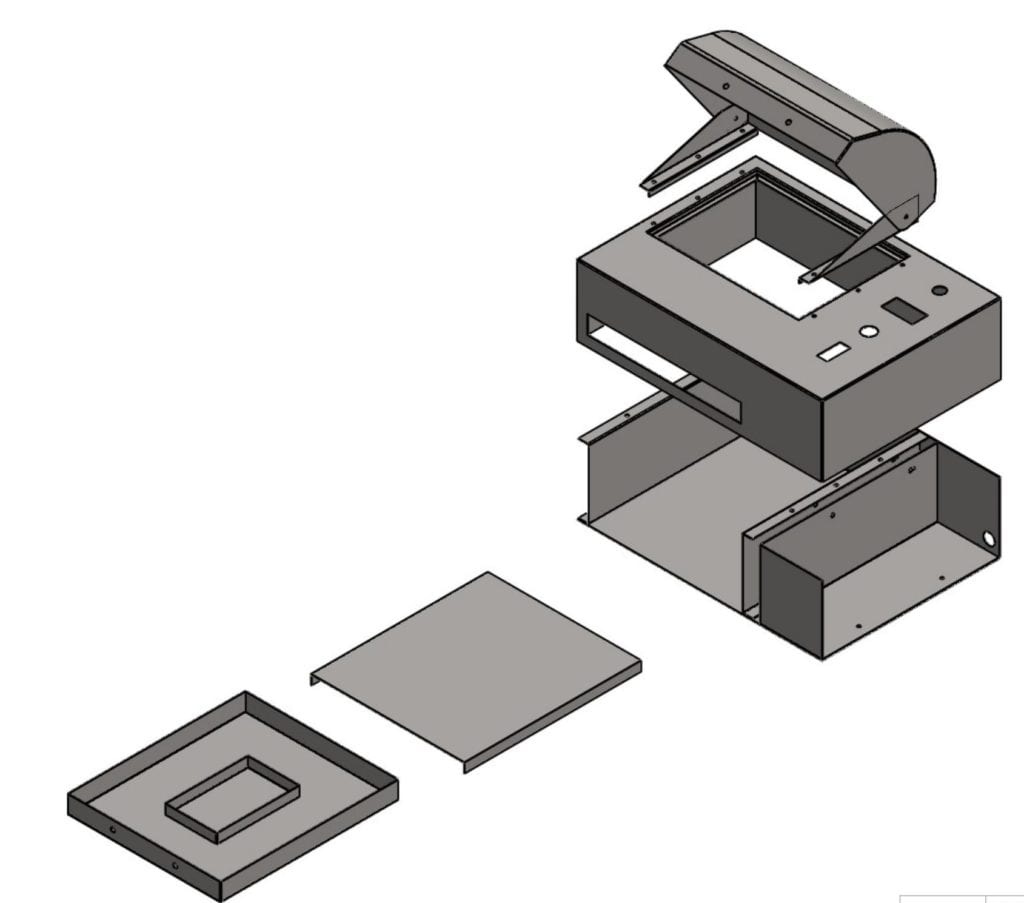
Exploded view to show sheet metal components included in the fully assembled grill.
Sheet metal Manufacturing
With a SolidWorks CAD model of the grill, we were able to complete a drawing package of the parts. We sent these parts to our sponsor’s sheet metal factory overseas and they were able to cut, bend, and weld the entire housing for us. This process would’ve been too expensive and time-consuming for us to perform so this saved us both time and money.
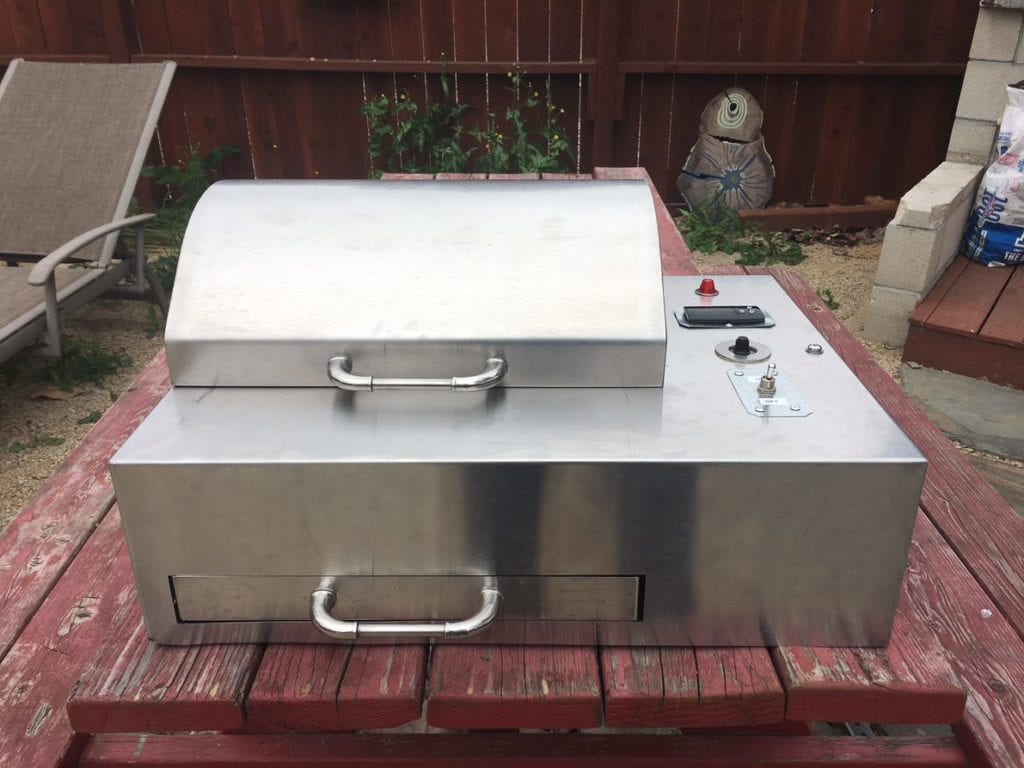
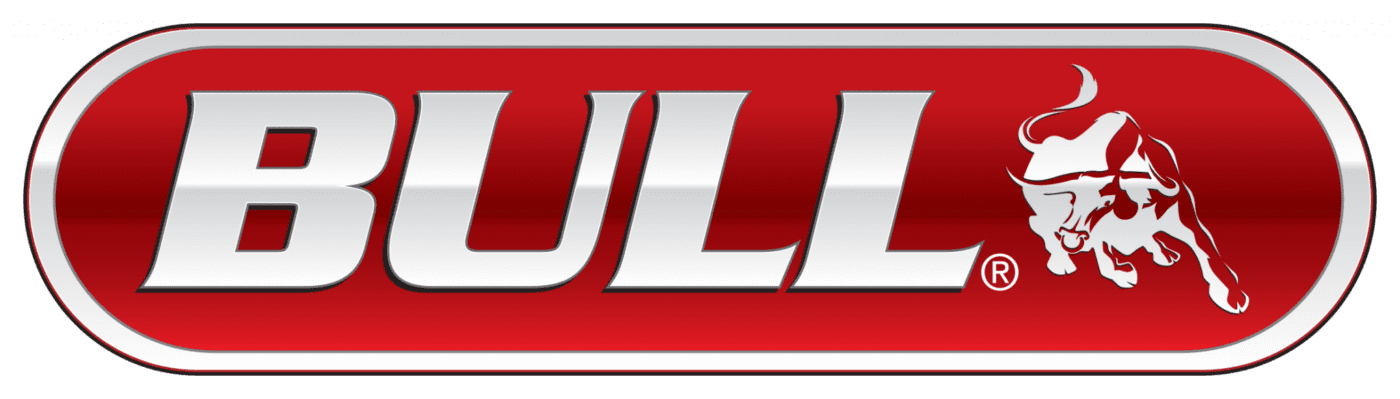
This project is sponsored by Bull Outdoor Products
Manufacturing
We outsourced the manufacturing of the housing to Bull’s sheet metal factory but we were still able to get into the shops. Makai and James cut and drilled holes into the grill top while Sofie worked on assembling the electronics with a certified electrical technician.
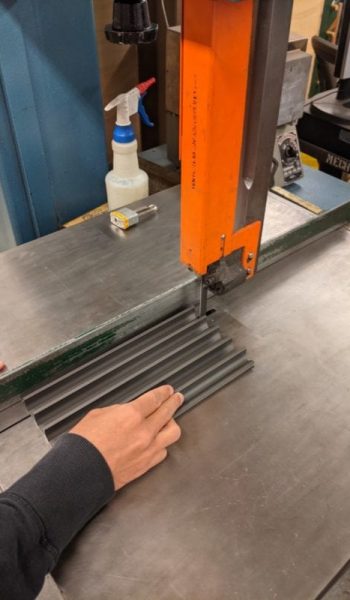
- Cutting the grill top to the correct dimensions with a bandsaw.
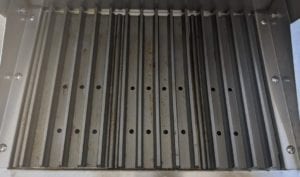
- Finished grilltop after machining.
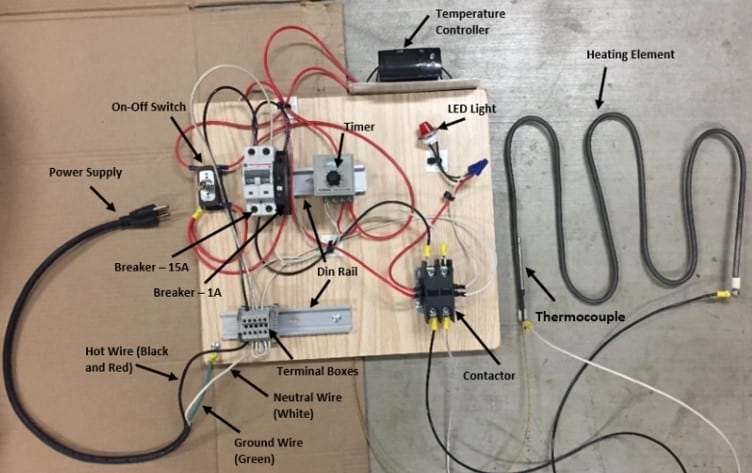
- Configuration of the electronics with labeled components.
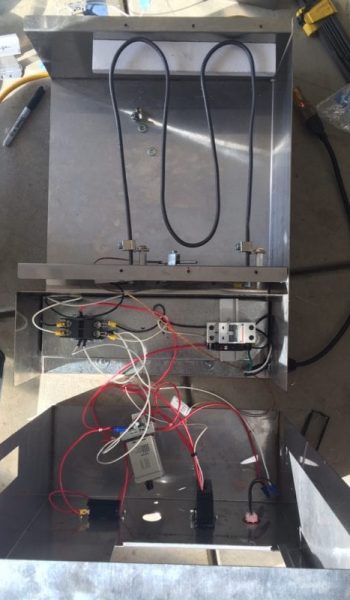
- A snapshot of the electronics assembly process. These components were taken from the original mock up and placed onto steel inside of the electronics housing.
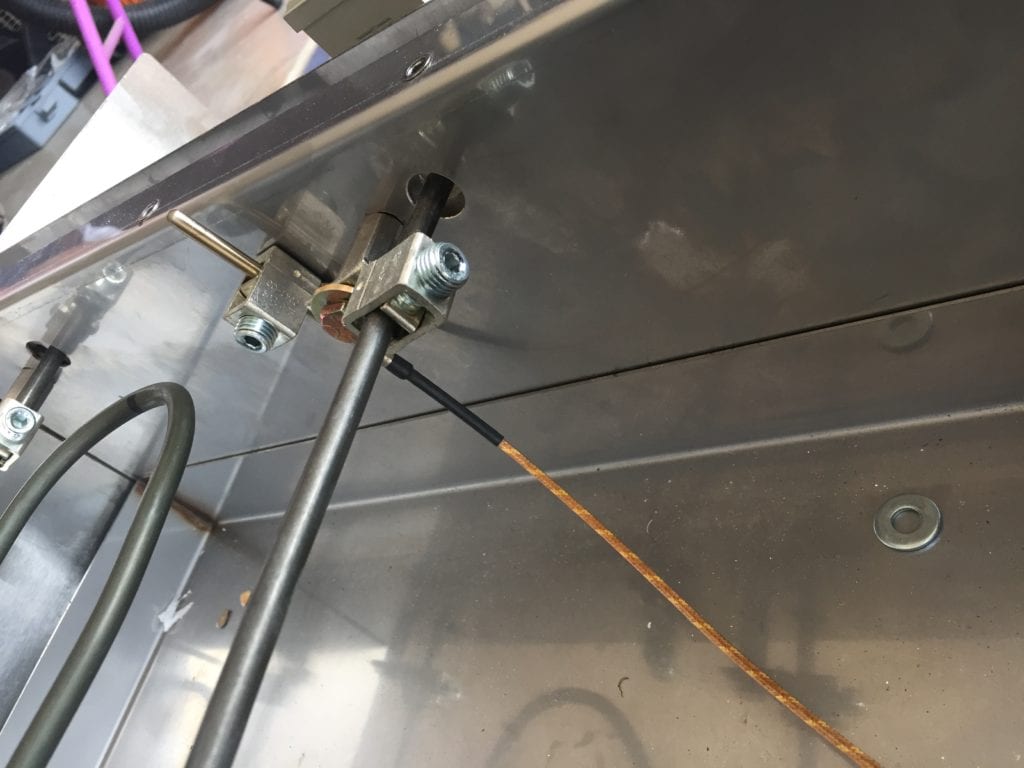
- Set screw configuration for the thermocouple that relays the temperature to the controller.
Recommendations
One of the limiting factors of our prototype was not being able to make our own grill top. If we were to make our own, we would recommend creating grooves in the grill top for the heating element to sit in. This would allow more of the heat from the heating element to transfer to the grill top, rather than to the surroundings. We also recommend finding electronics that are more compact, as they were the driving factor for the overall dimensions of the grill. This would make the grill smaller and lighter.
Final Design
Specifications
Max Temp – 540 °F in 20 minutes
Required Power – 120V at 11A
Cooking Surface Area – 150 in^2
Overall Dimensions – 18.5” X 23.5″ X 12.5”
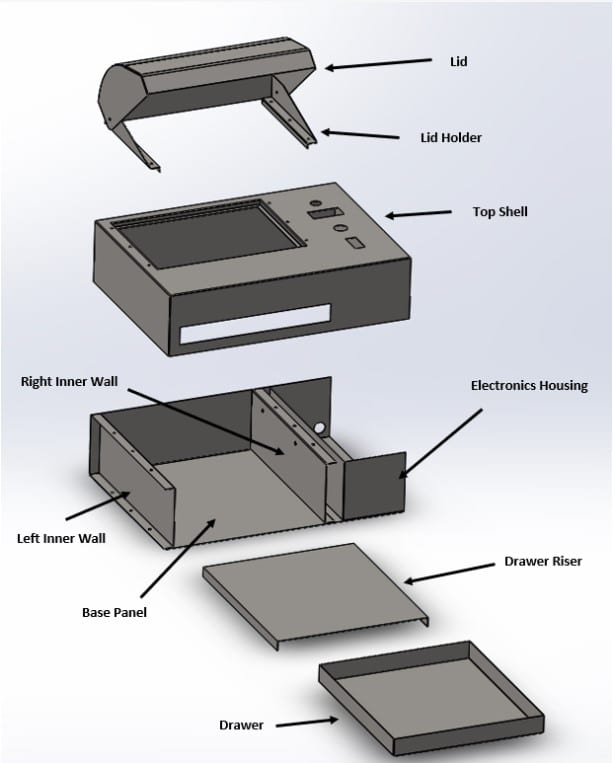
- Final CAD Model of the Grill
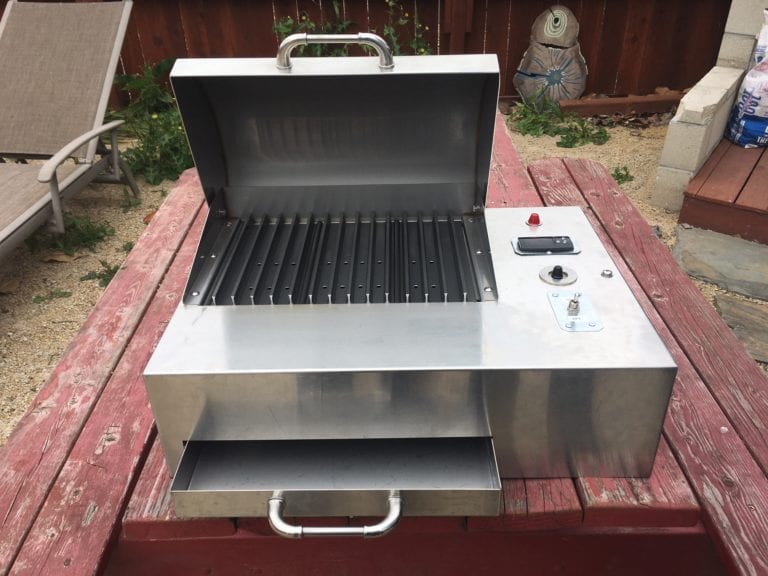
- Final Product
Future of Design
Our prototype, along with our final design review, will be received by our main point of contact, Frank Mello. He will consult with his factory and own engineers to further the design of this project. We hope to hear back from it in the future.
Testing
Maximum Temperature – The surface of the grill top measured with the IR thermometer reached 540 °F.
Time to Maximum Temperature – It took our grill around 20 minutes to get to its maximum temperature.
Steady State Temperature Variance – The maximum difference between temperatures at the same spot was 8 °F.
Temperature Distribution – The maximum difference between temperatures measured at 33 equally spaced spots on the grill surface was 120 °F.
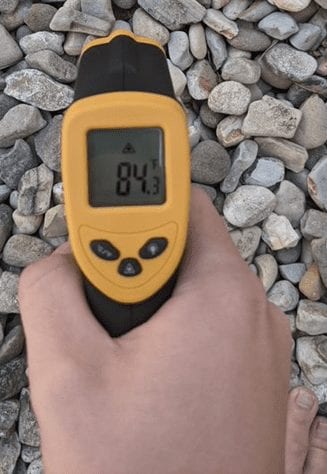
The IR Thermometer that we used to measure the temperature of the top of the grill surface.
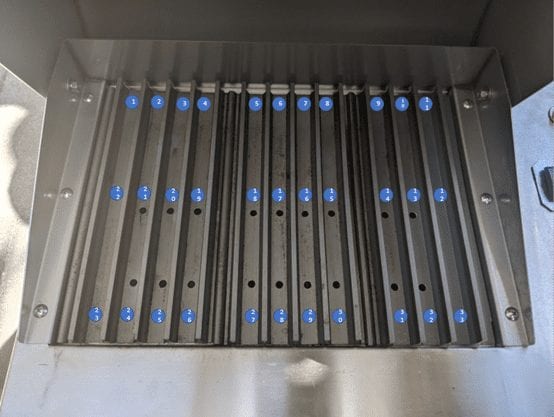
The spots where we measured the temperature distribution laid out on the surface of the grill top