Our Team
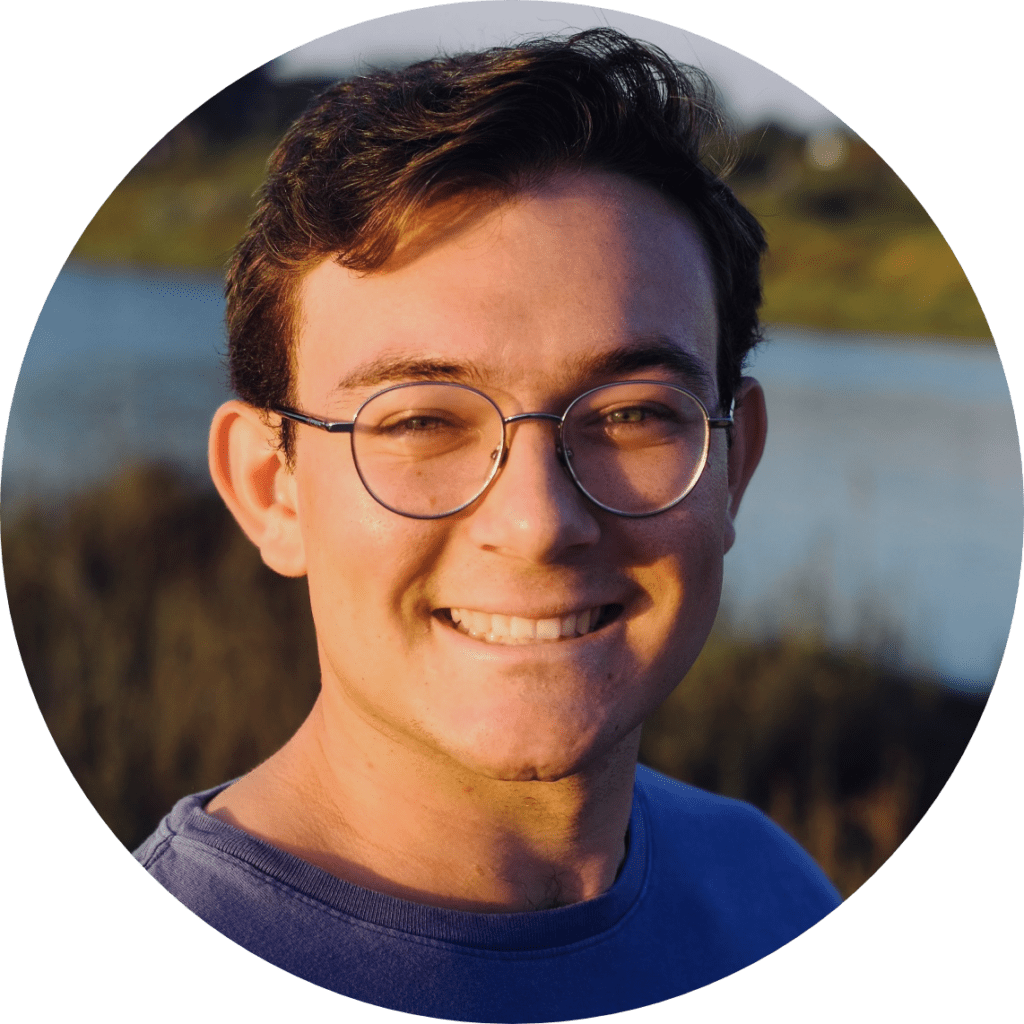
Jack Rocca
Project Manager
Jack is an Industrial Engineer from San Francisco, California. Fascinated by the power of Augmented Reality, he sought to put together a team and work with MBH Architecture to look at how AR could be implemented into the building industry. During the project, he lead communication between the project mentors and sponsors, and spearheaded the utilization of the HoloLens 2 headset along with Revit and Trimble Connect softwares.
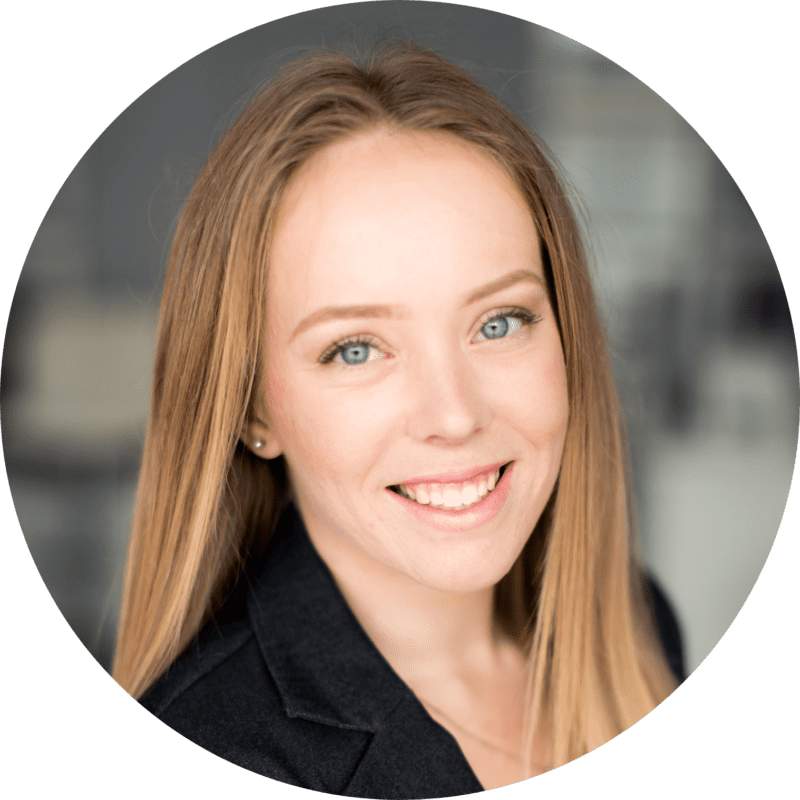
Laila Schnebelt
Industrial Engineer
Laila is an Industrial Engineer from Napa, California. With an interest in construction and project management, Laila was drawn to this project due to the immense potential of implementing technology within such a huge industry. Laila was also passionate about the possibility to make an environmental impact by reducing wasted materials used in rework. Laila will be returning to Cal Poly in the Fall of 2021 to complete her degree.

Matt Akins
Industrial Engineer
Matt is an Industrial Engineer from Irvine, California. Interested in construction, Matt thrived at implementing Industrial Engineering practices into the various areas of the building industry. Matt recently graduated after the Winter Quarter of 2021 and has begun working as a Sales Engineer at Trane in San Francisco, California.
Acknowledgements
We would like to thank our Senior Project Advisor Karen Bangs, IAB Member Sam Aborne, and our sponsors John McNulty and Kevin Albaugh from MBH Architects. Without their guidance and support, the success of our project would not have been possible.
Project Presentation
Please enjoy the final presentation that highlights the important aspects of our project.
Digital Poster
Problem Statement
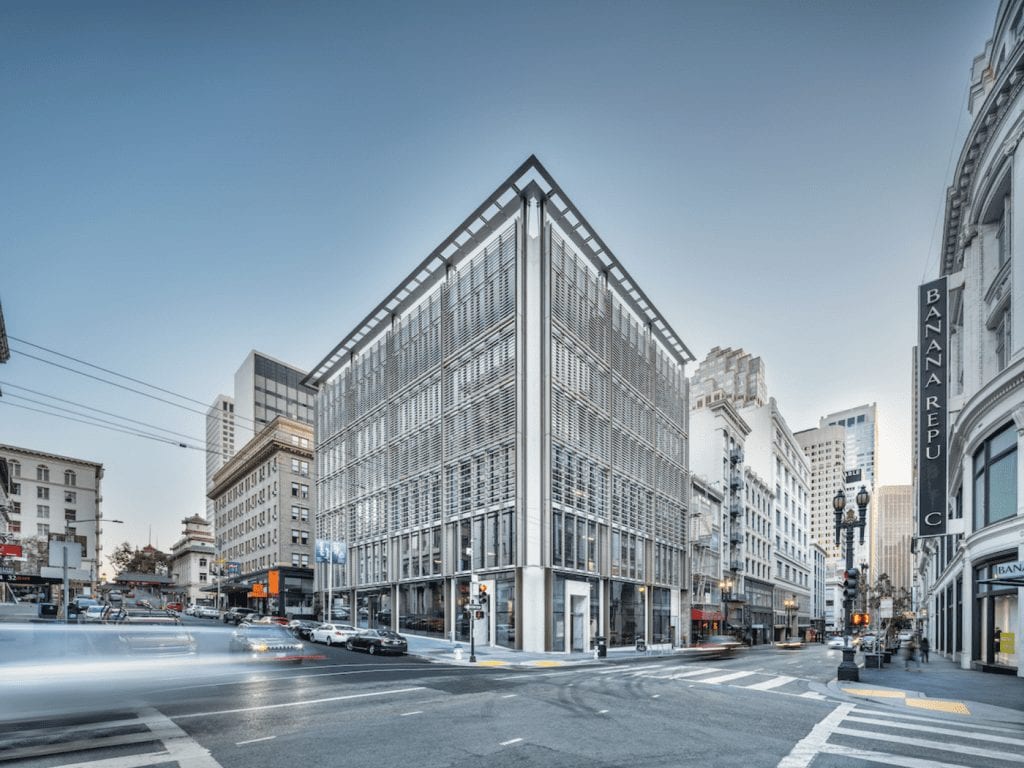
On MBH’s 300 Grant Street Project, there were over 300 Requests-for-Information (RFI). These RFIs arise when contractors in the field need more information than what is on the design plans to complete their work. RFIs take a significant amount of time to process and lead to additional costs that could otherwise be avoided.
Current State
What is an rfi?
A Request-For-Information is a formal document that the General Contractor of a project files when the design plans do not contain all the necessary information needed to complete the build. The information in the design plans may not be clear, or there may be physical conflicts that the design plans did not account for. Below is an RFI that was used on the 300 Grant Street Project. (Sensitive information has been blocked out)
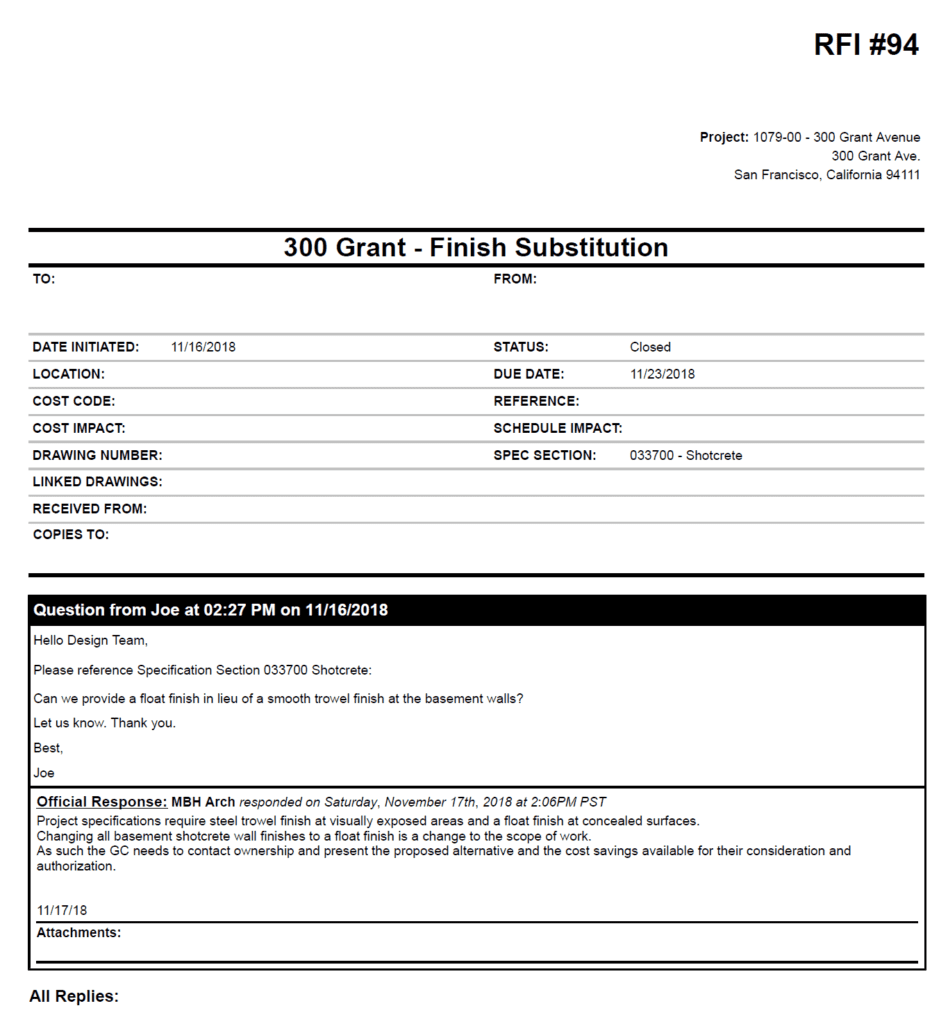
statistics
- – Average project has 9.9 RFIs per $1MM of construction
- – RFIs have average response time of 10 days
- – Avgerage price to process one RFI is $1,080*
Current Process Flow
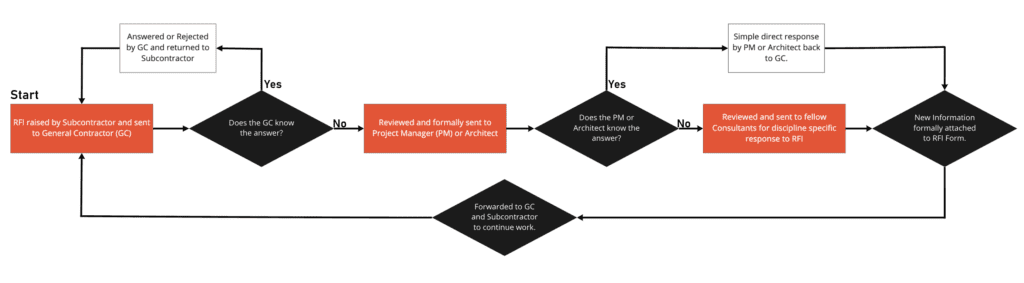
Project Objectives
KPI Goals
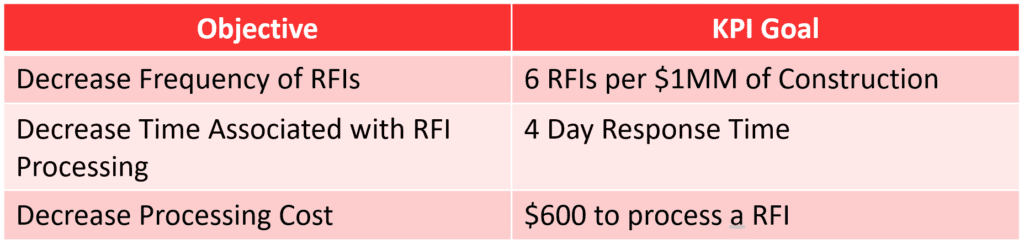
Literature Review
Types of Errors in Construction
Three most common errors in construction:
– Scheduling
– Communication mistakes
– Overspending budget
Most errors occur due to miscommunication between subcontractors and GC’s
Current Solutions
No technology or project management style used unanimously across industry. This is mainly because of the resistance to changing habits, limited budgets, avoidance of standards, interoperability issues, and limited relevance.
Three most common solutions currently used:
– Project management software (BIM, Procore, etc.)
– Construction delivery methods:
– Design-Build (DB)
– Integrated Project Delivery (IPD)
Future Solutions
It is difficult to implement new technology in companies because most do not have a role within the company to assist in new technology implementation. This is because construction companies usually have low barriers of entry, low capital margins, and limited risk ability.
Future Solutions that are currently at the early stages of development include:
– Drones
– Monitor progress, catch errors
– Augmented Reality (AR)
– Enhanced Communication
– 3D visualization that can be overlaid onto reality
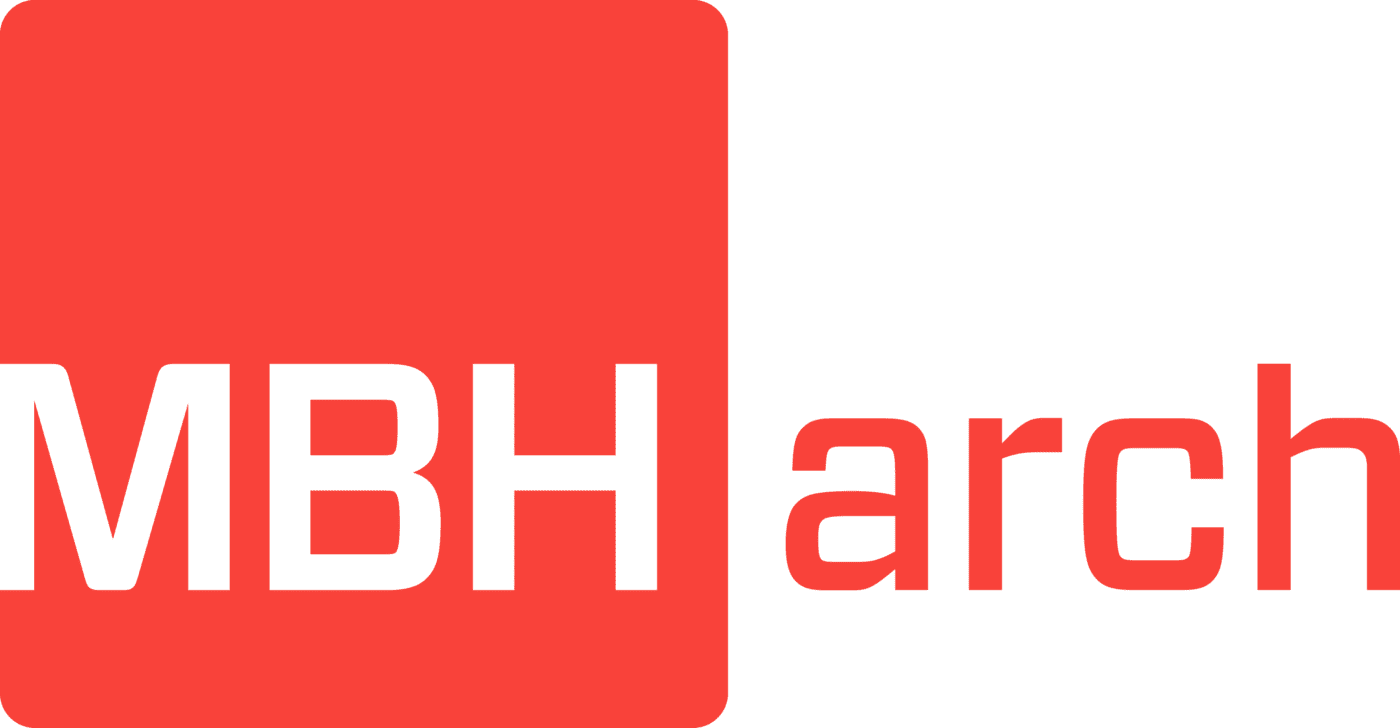
This project is sponsored by MBH Architects
Potential Solutions
Augmented Reality
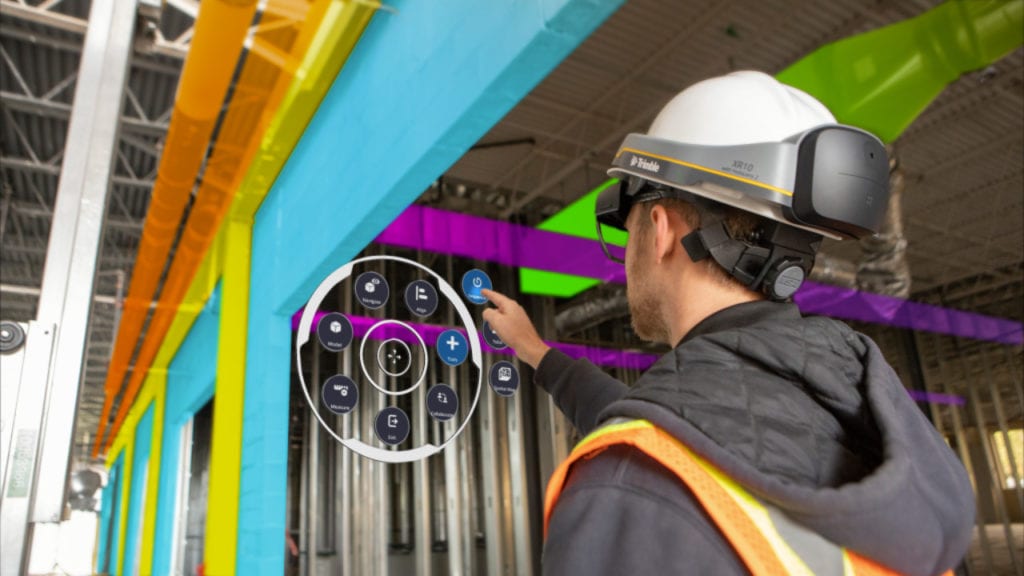
Our Augmented Reality solution was focused on incorporating pre-visualization into the building process to reduce RFIs from occurring. This would be done by having jobsite walkthroughs where Revit models of the project could be visualized on the jobsite before physical work is carried out. We decided that the best headset to use was Microsoft’s HoloLens 2 as it is the most used AR headset for industry applications and our group had access to the device. We also decided to use Trimble Connect as the AR software which was concluded after extensive research into the numerous softwares currently offered.
Central Jobsite workstation
This solution would be a large touch screen smart board in the central area of the jobsite. The general contractor, architect, subcontractors, and owner would have access to this device and it would serve as a “check-in” like project management portal. This would allow for all essential documents to be stored in one location. Furthermore, it would allow RFIs to be submitted and viewed on the jobsite. All GC’s and subcontractors could check the board each morning before beginning work to see if any notifications are present for them regarding their RFIs or work that needs to be done.
Standard Documentation Portal
All stakeholders on the project would utilize the same software that would be created to adopt the AIA standard RFI format with necessary supporting documentation formatting. This would prevent stakeholders from using different software or RFI formats for the processing of their RFIs. All industry professionals on the project would be able to access the portal as registered users and view RFIs related to jobs they are assigned. The main goal of this would be to decrease the processing time of RFIs.
Solution Selection
After creating an analyzing the solution alternatives, we decided that an Analytical Hierarchal Process along with a Financial Analysis would be the best tools to determine which solution would be best. We then compared these on the below chart to visualize our results.
AHP Criteria & Results
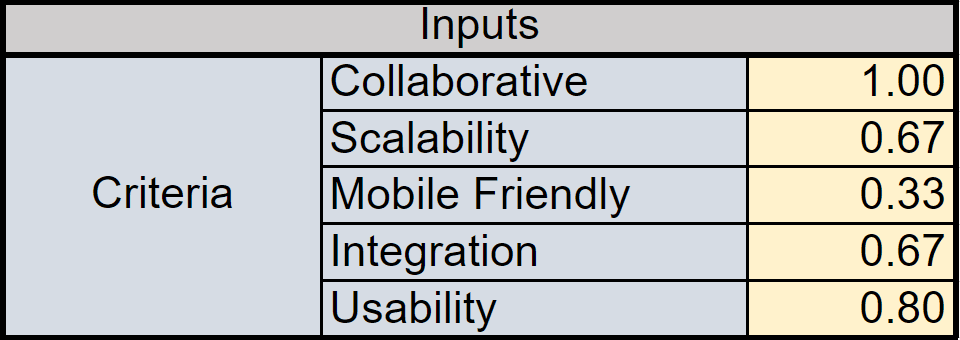
We decided to go with the bove criteria for the following reasons. Collaboration was the most important aspect because we viewed that to be the greatest weakness in the current process flow. Usability was the next most important criteria because a solution is only beneficial if the end user is able to effectively use the technology. Scalability & Integration were next in weight because we wanted our solution to be future-proof while also easy to integrate into the business process. Lastly, we valued mobile-friendliness because construction sites are very busy and people and materials are constantly moving around the jobsite. Below are the results of our AHP.
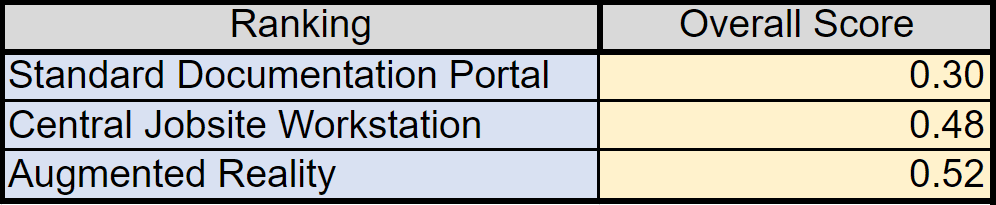
Financial Analysis
For the financial analysis, we calculated our results by performing an IRR analysis on the savings that would be provided to MBH if they implemented each of the solutions to their business. Below are the results.
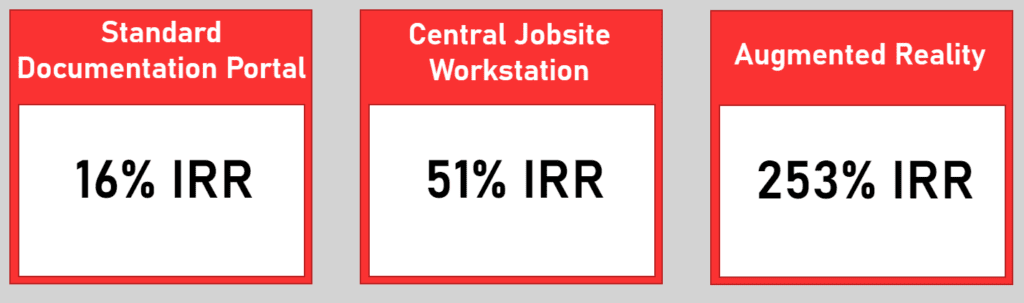
Results
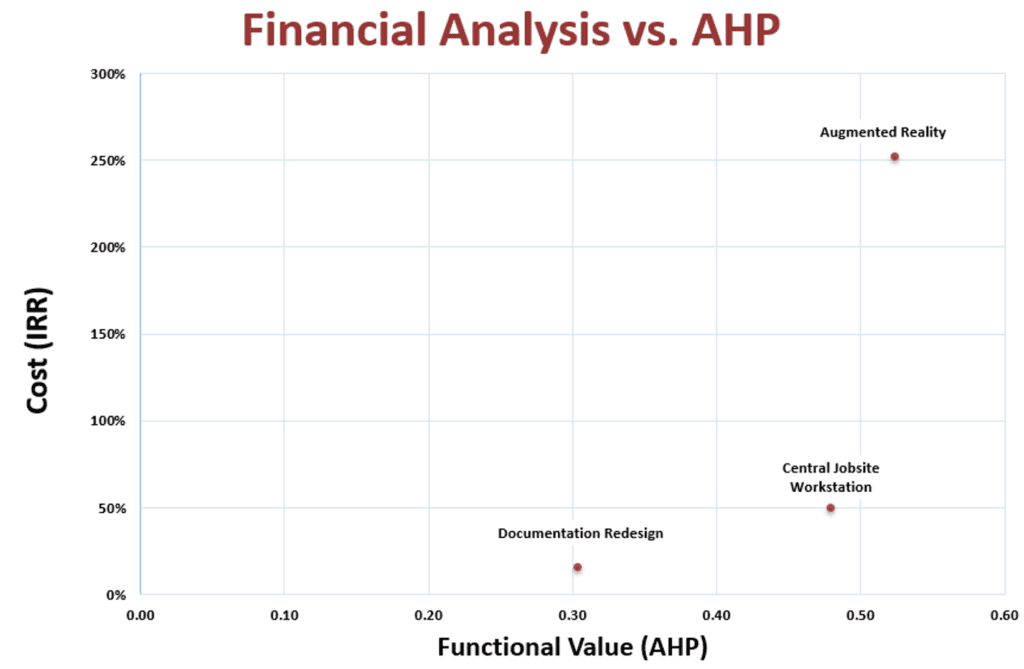
As displayed in the chart, Augmented Reality scored highest on our AHP and in our Financial Analysis and was selected as out solution.
Social, Environmental, & Economic Impact
Social Impact
By incorporating a previsualization walkthrough with several stakeholders, it would improve the relationships between owner, architects, general contractors, and subcontractors.
Environmental Impact
Reducing RFIs has the potential to reduce the amount of rework on a project. This can lead to dramatic reduction in material waste.
Economic Impact
AR can improve company revenue by creating a more efficient work process. By meeting our goal of 6 RFIs per $1M of construction and the cost of RFIs decreasing form $1080 to $600, we offer a savings of $6,720 per $1MM of construction. To put it in perspective, this would total $336,000 of savings on RFI processing on a $50MM construction project. Furthermore, this does not include the cost of rework or time delays associated with the RFIs that would occur.
Verification & Validation

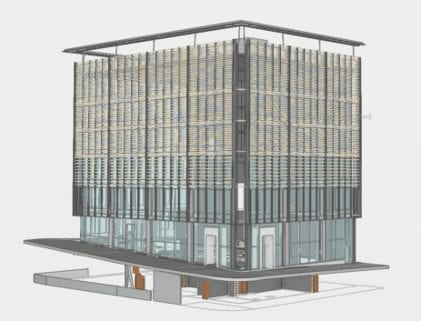
For our Verification & Validation, we recorded how the Trimble Connect software could be used with Microsoft’s HoloLens 2 Augmented Reality headset and MBH’s Revit CAD models of the building. Along with the in-depth video, we sent a survey to MBH asking for their thoughts and opinions on the product. With overwhelming support for the solution, MBH verified that this was the solution they thought would be best to move forward with.
Implementation Plan
After receiving validation from our sponsors, it was determined that Trimble Connect could be implemented on the architect or general contractor’s side in approximately 4 weeks, mainly relying on the user guide we developed for MBH along with YouTube videos made my Trible Connect which highlight how to use software features. Outlined below is the process flow for how the Augmented Reality would be utilized on the jobsite. The main change from the original process flow is that AR would be used in a previsualization walkthrough where the architect, general contractor, and subcontractor would see how the plans overlay onto the jobsite before any work has been completed. This will allow for errors to be spotted prior to the subcontractor beginning, which would prevent RFIs from occurring later on in the project.
Implementation Gantt Chart & CostNew Process Flow

For training, the assumption was made that an employee would be not be training with the software full-time. Instead, the plan was developed with the idea that employees could spend a couple hours each day. This plan was developed with input from MBH. Knowing that subcontractors would not be paid for training, our plan outlines how the architect or General Contractor would need to train their employees to pre-load the model and get everything set so the subcontractors can put on the HoloLens and easily see the 3D models on the jobsite. Thus, the implementation plan is specifically for training architects and GCs. Below is the schedule for how this would be done. It was also calculated that the total price per employee to be trained and use the software would be about $9,700.
Implementation Gantt Chart & Cost
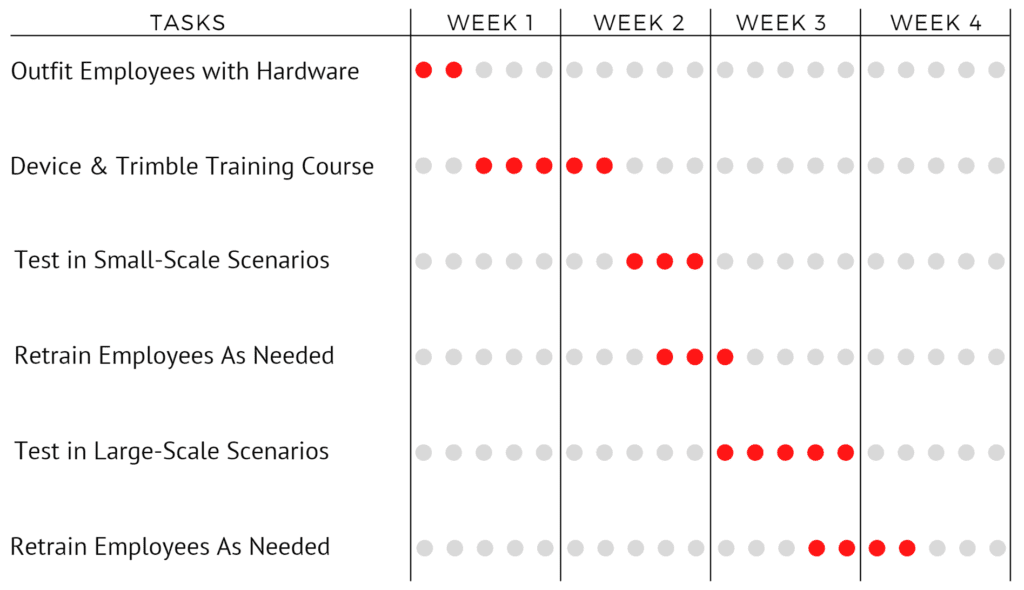
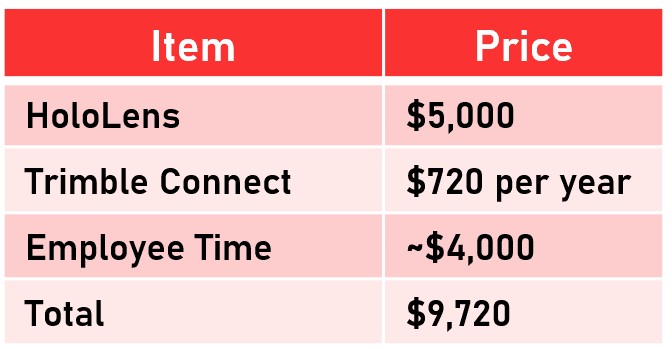
Conclusion
In conclusion, our process found that the RFI Process contains several inefficiencies that lead to increased cost, time, and resources on a construction project. To keep MBH at the forefront of architecture and innovation, we recommend that they begin to consider implementing Augmented Realty because of the efficient process flow it enables through previsualization. At first, it can be used to streamline communication channels in the RFI process. In the future, however, we believe that the technology will become exponentially powerful and have applications throughout the building industry and the world.
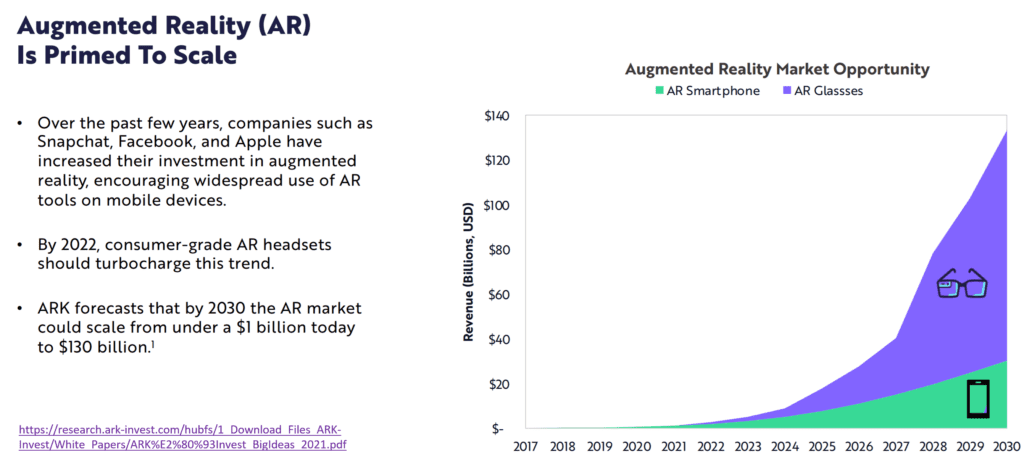
To further prove the point that Augmented Reality is going to grow in popularity, a study from Ark Invest is pictured above. Ark Invest is a venture capital firm at the forefront of innovative technology investment. In their 2021 shareholder letter, they included a section on Augmented Reality that displayed a chart showing the potential growth of the technology. While Augmented Reality currently has an annual revenue of approximately $1 billion, Ark sees this growing to $130 billion by 2030.