Meet the team
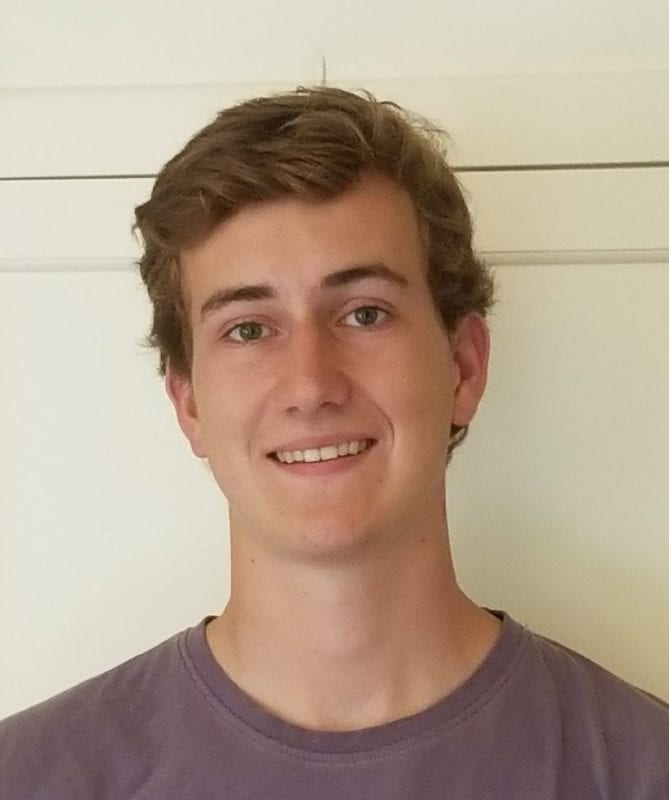
Ben Sahlin
I am a fourth-year mechanical engineering student concentrating in mechatronics. After graduating, I plan to move back to Seattle. In my free time, I enjoy skiing and mountain biking.
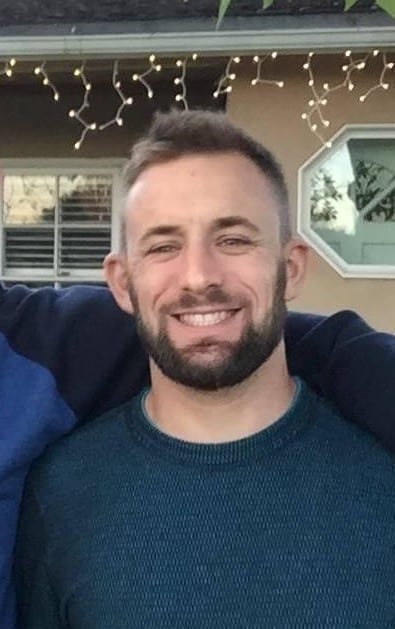
Eric Stone
I am a fourth-year mechanical engineering student and Army Veteran. I am from the LA Area and have worked in the aerospace and defense industries and hope to do so again in the future to continue to support the scientific community as well as my brothers and sisters in the arms.
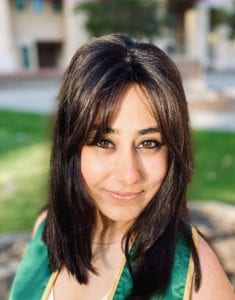
Mandy Kaur
I am a fourth-year mechanical engineering student with a general concentration. I am originally from the Bay Area and will be graduating in Spring 2021, after which I will be pursuing my career in the Oil & Gas industry.
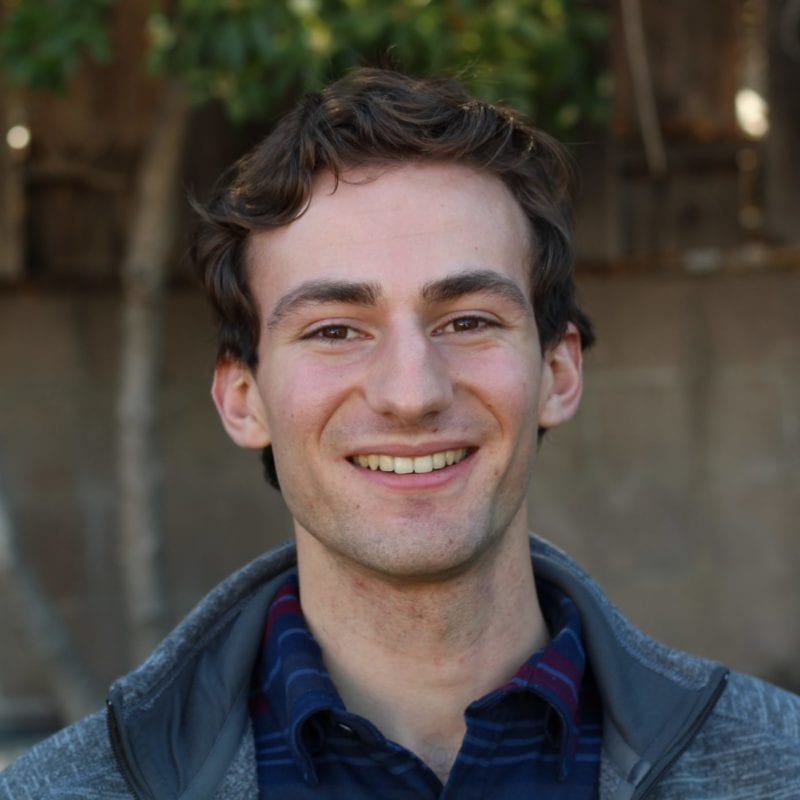
Mark Iknoian
I am a fourth-year mechanical engineering student with a concentration in mechatronics. Next year I plan on continuing my education at Cal Poly through the Blended master’s program.
Acknowledgements
Our team would like to thank all of the individuals that helped make this project possible. We would like to thank our advisor, Sarah Harding, for providing us with guidance and feedback at every step along the way. We are also very grateful to our sponsor, Zurn Wilkins, for facilitating this entire project. This project would not be possible without our sponsor’s constant support and guidance from designing, to building, and testing while we were not allowed to visit the site due to COVID restrictions.
Our Project's Videos
This video provides an overview of our project over the course of three quarters. The team explains our overall design process, from ideation to prototyping to testing, and then walks through the results and conclusions for the project.
Our Project's Digital Poster
Background
Problem Statement
A check valve is a valve that only allows flow in one direction. Our group was assigned the task of designing a check valve for Zurn Wilkins that has a smaller pressure drop while in use than the current Zurn 350XL model. A smaller pressure drop would allow for more efficient water systems and would benefit the end consumer by allowing them to size down in piping.
Zurn 350XL
Key Specifications
Our final prototype had to meet the following specifications:
- Reduce pressure drop while in use at rated flow to below 7 PSI
- Meet drip tightness specification from ASSE Standards
- Meet hydrostatic pressure specification from ASSE Standards
Ideation
During the ideation stage, our team used different techniques to brainstorm potential designs. We used methods including braindumping and “worst idea” to generate our ideas, and consolidated our final designs using Pugh, morphological, and weighted decision matrices. Our final three concepts are all variations of an in-line poppet valve and are detailed below:
CONSTANT FORCE SPRING
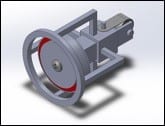
This design incorporates a constant force spring to create a non-linear spring rate. Issues with this design include debris accumulation and spring cycle life concerns.
buckling coil SPRING
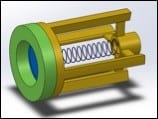
The buckling coil spring design utilizes a narrow diameter coil spring to create a non-linear spring rate. Issues with this design include packaging concerns once the coil spring has buckled, and a lack of design documentation for the buckling coil spring
buckling leaf SPRING
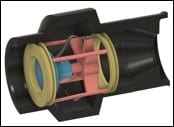
The buckling leaf spring design uses two buckling leaf springs to create a non-linear spring rate. Off-axis buckling forces are canceled out by the two leaf springs situated 180 degrees apart. Issues with this design center around life cycle concerns.
Initial design direction
Initial ideation and calculations led us to pursue the buckling leaf spring design due to the degressive spring rate, well defined spring rate equation, and ease of packaging. We also planned to make geometry modifications to the design with the goal of reducing flow restrictions through the valve.
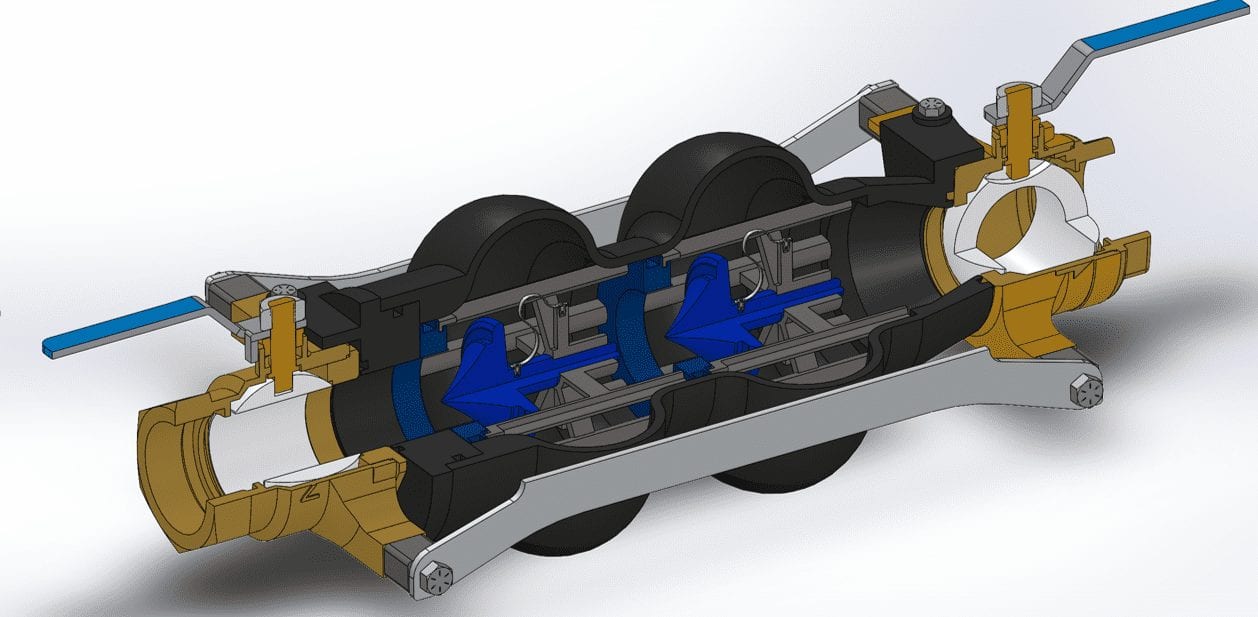
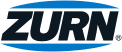
This project is sponsored by Zurn Wilkins. We would like to thank Brian Yale, Reuben Westmoreland, Chris Corral, and Brendon Morey for assistance on this project.
Analysis
Following our ideation phase, our team decided to make two geometry modifications compared to the 350XL design, including changing the poppet shape and extending the housing around the spring retainer. A Computational Fluid Dynamics (CFD) software within SolidWorks was used test out different variations and provide analytical confirmation of pressure loss reduction before proceeding with our prototypes.
Poppet shape
Using the CFD software, our team tested three types of poppet shapes: hemisphere, bullet, and cone. After multiple iterations, we compared the top performing shape in each category against one another. The cone shape outperformed the other two, and we proceeded with this design for our prototype.
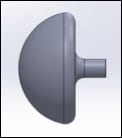
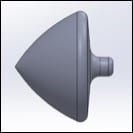
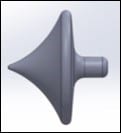
HOUSING DESIGN
After multiple design iterations and CFD simulations, our team found that an extended bubble-shaped housing resulted in the lowest pressure drop. The figure below is the pressure contour plot for our best housing design, with our final poppets inserted, at the rated flow for a 2-inch diameter valve. Compared to the Zurn 350XL, the CFD results showed a reduction in pressure losses of approximately 36% at all flowrates.
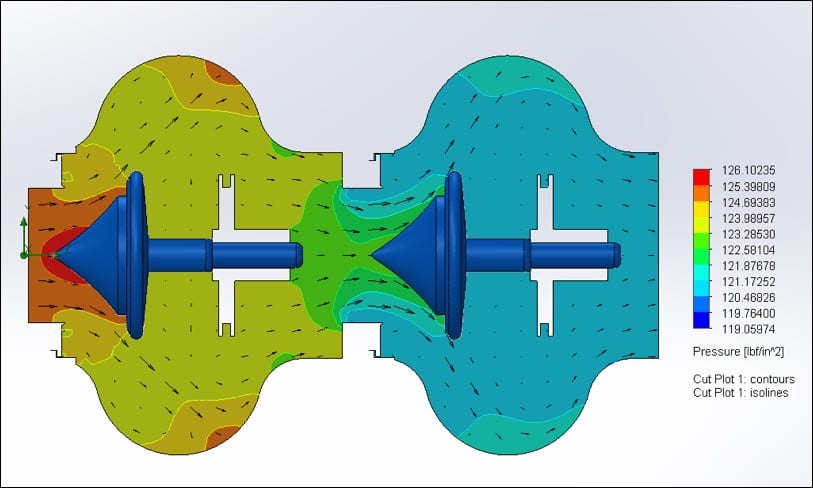
Manufacturing
pROTOTYPES
Structural Prototype – In our first prototype we used an elastic material to attempt to create a better seal during non-operating conditions as we had changed from a large flat area to a sharp thin ring of contact with our poppet head. We found that this did not 3D print well or hold enough stiffness to work effectively during its movement. We also found that the material we were using for other 3D printed parts was too brittle and could not be hydrotested effectively. Some printed parts also became warped during printing.
Because of these issues, we adjusted to a two piece poppet with a seal ring, changed 3D printing materials, and adjusted CAD designs by adding supports to produce an accurate and testable prototype.
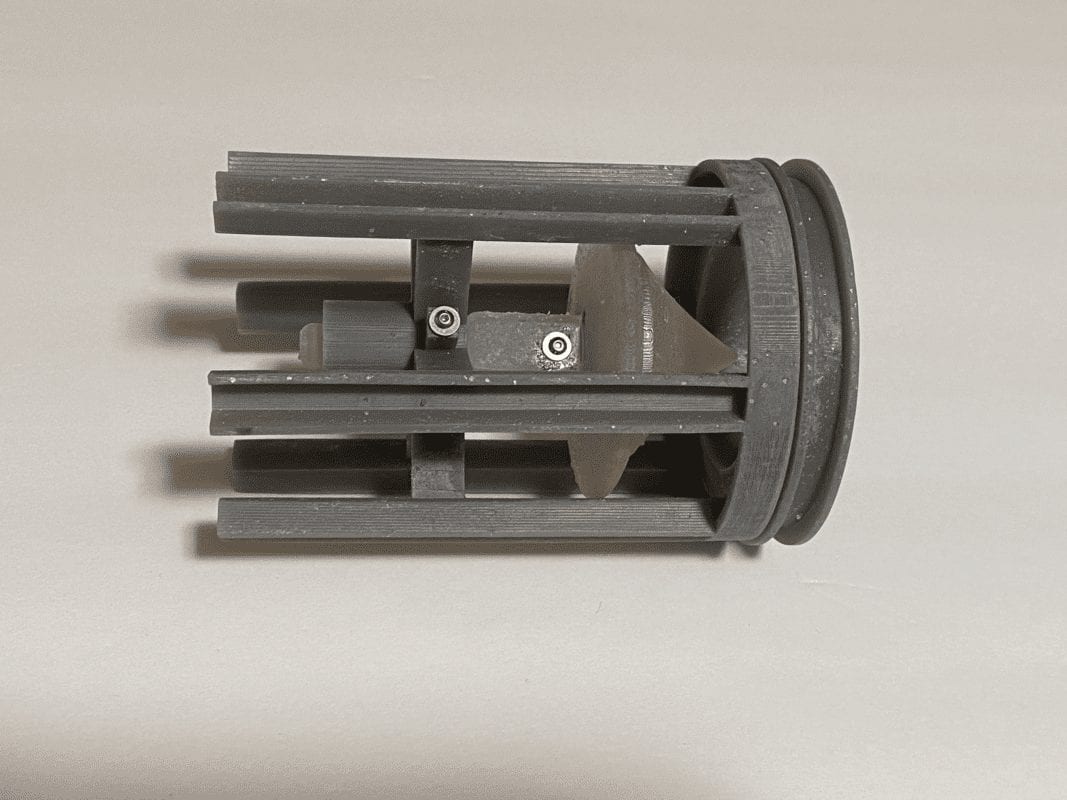
First prototype poppet design with hyrdo-dynamic shape to reduce drag and redirect flow inside the check valve.
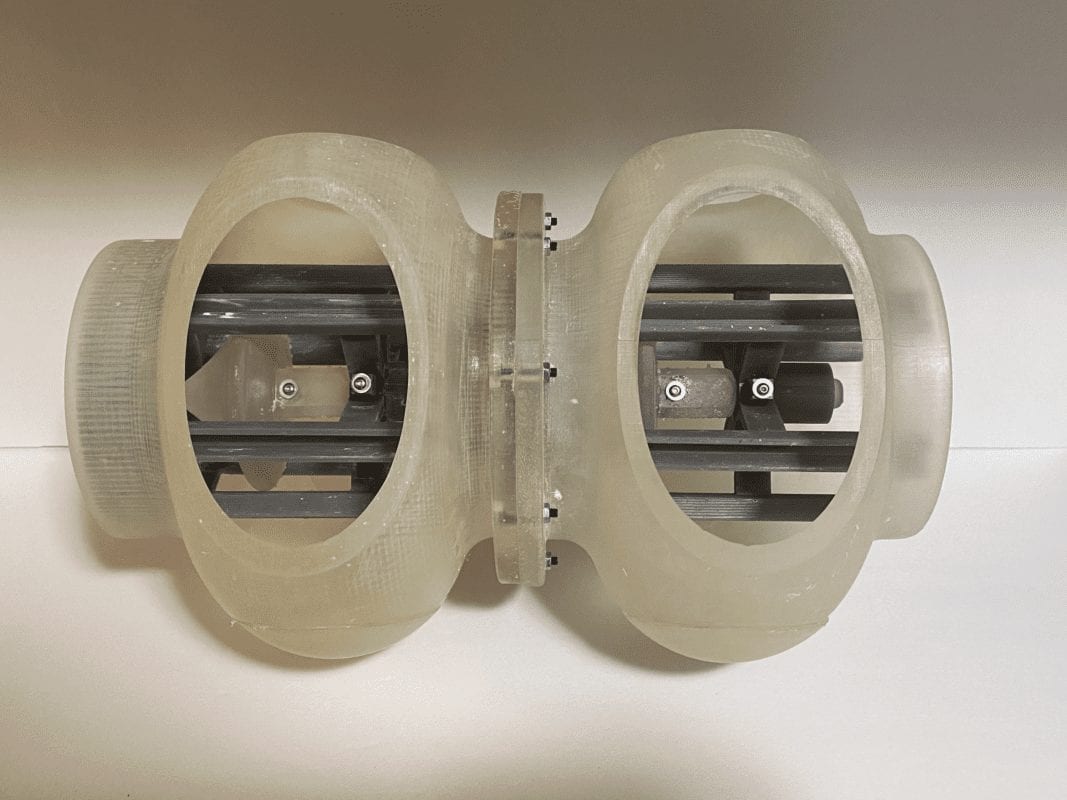
Full prototype assembly with cutouts to view poppets and moving parts inside assembly.
Verification Prototype – For our final design, we moved away from our buckling leaf springs and utilized the coil springs out of the current Zurn 350XL design and moved forward with a two piece poppet with a seal ring as well as different 3D print materials that produced accurate sizes and shapes for our design to work properly during final flow testing. We also utilized a final single-print housing contracted through Protolabs to allow for handle large capacity prints.
Testing
Spring Testing – Our first round of testing included spring force testing on our buckling leaf springs to ascertain force curves for a few different sizes of springs to verify our governing equations.
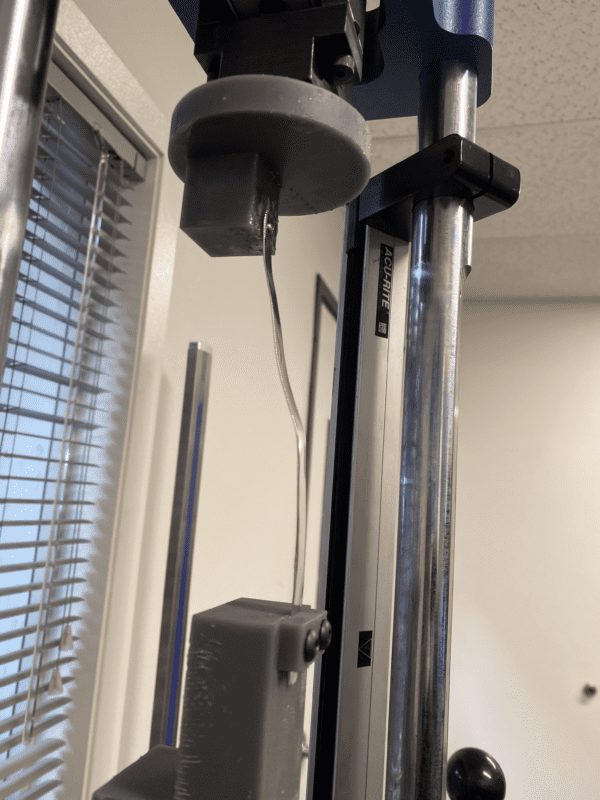
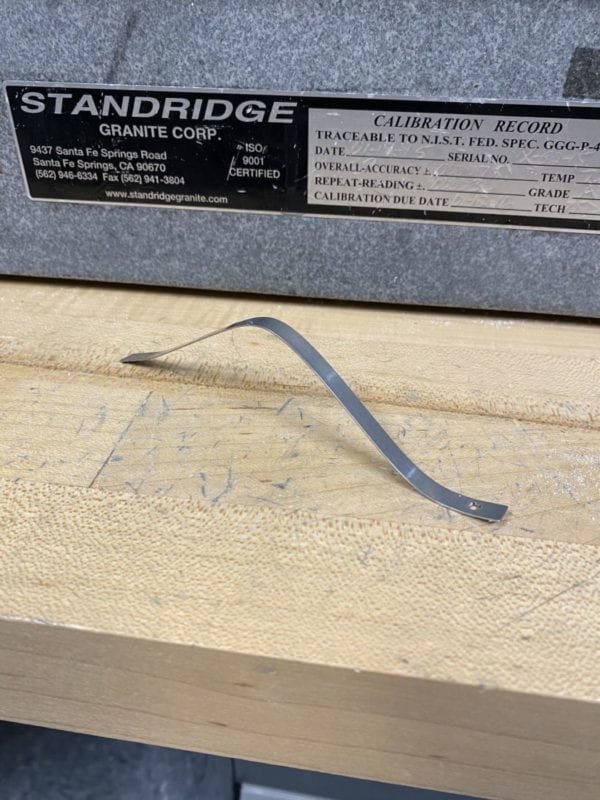
As can be seen above, our springs became permanently deformed and did not follow the digressive force curves we were hoping to have. Because the springs failed, we did not move into cycle testing them to assess life-cycle requirements.
Flow Testing – Our final rounds of testing included flow testing of the complete assembly to find pressure loss characteristics throughout a range of flow levels. This was done both with the current Zurn 350XL springs as well as with no springs installed to assess geometry modification effects on the pressure losses and see if we had improved the design point pressure loss for the check valve.
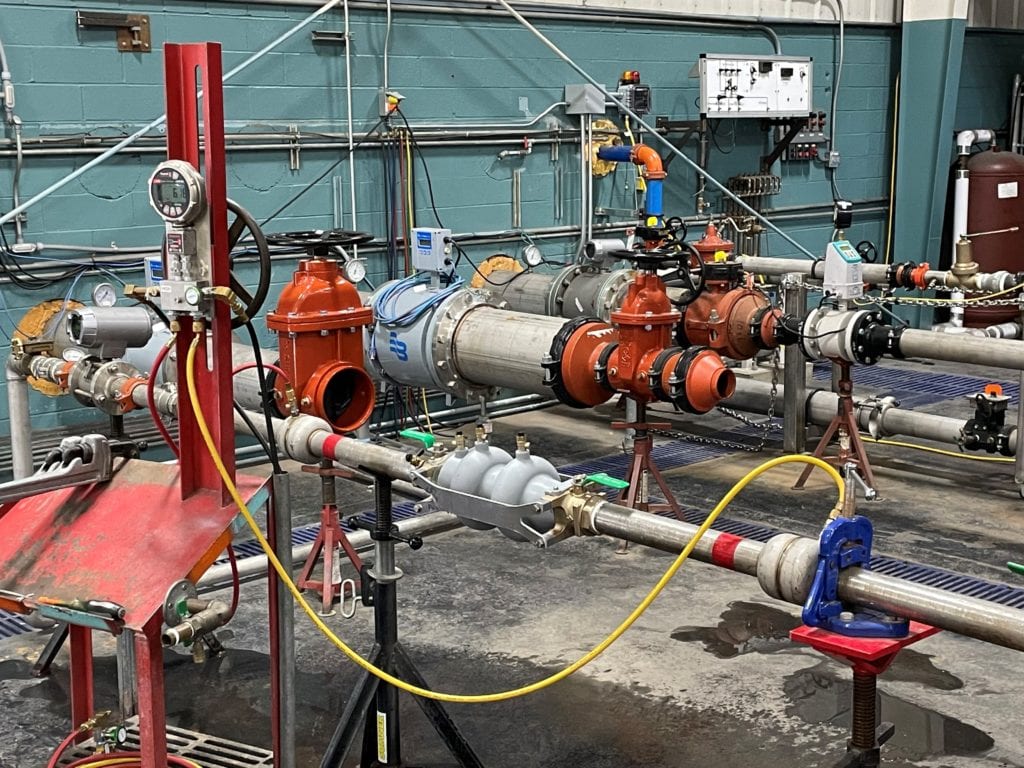
Testing Results
What we found from our first iteration testing is that our buckling leaf springs did not accurately follow the governing equations with which we had modeled them. They became permanently deformed during our spring force testing and therefore would not close the poppet after the flow and pressure differentials disappeared.
Our design was then adapted to use the current Zurn 350XL spring. The reduced drag of our modified poppet shape resulted in us being unable to reach a full-open condition during flow testing and did not reach our assumed pressure loss target.
The final flow test was conducted with no springs installed to see if we could match our preliminary CFD results at a full-open condition. The resulting differential pressures were higher than anticipated. Our CFD model did not accurately predict pressure loss trends, possibly due to inaccurate turbulence modeling and unaccounted differences in interior surface finish.
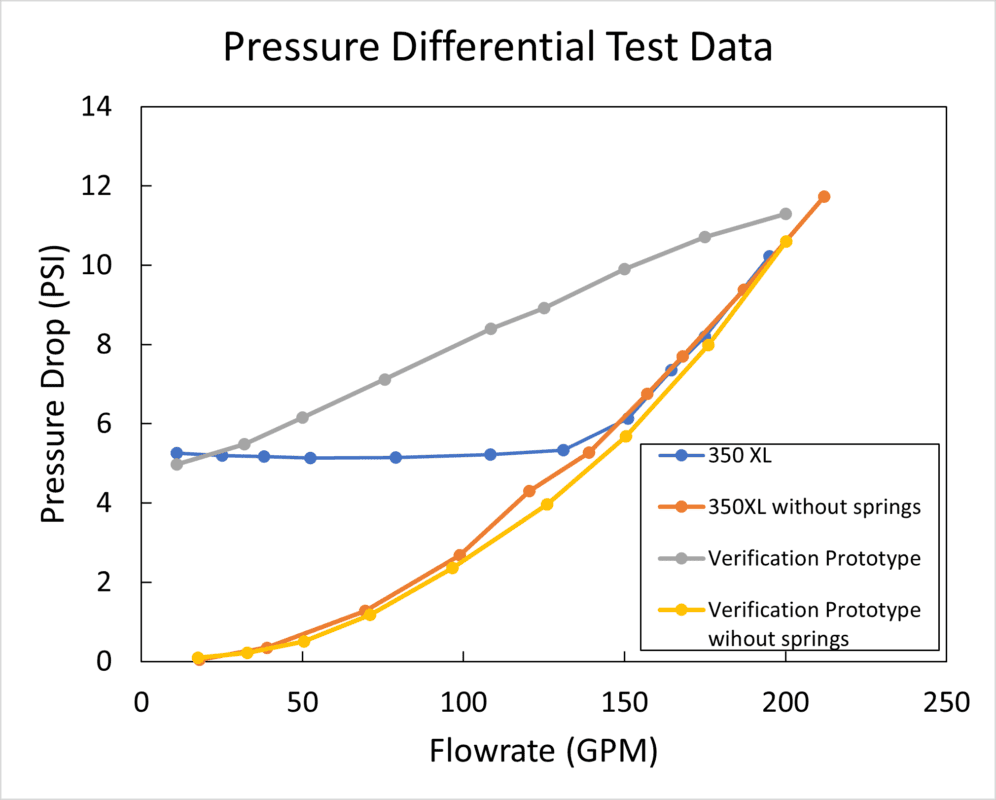
Conclusion
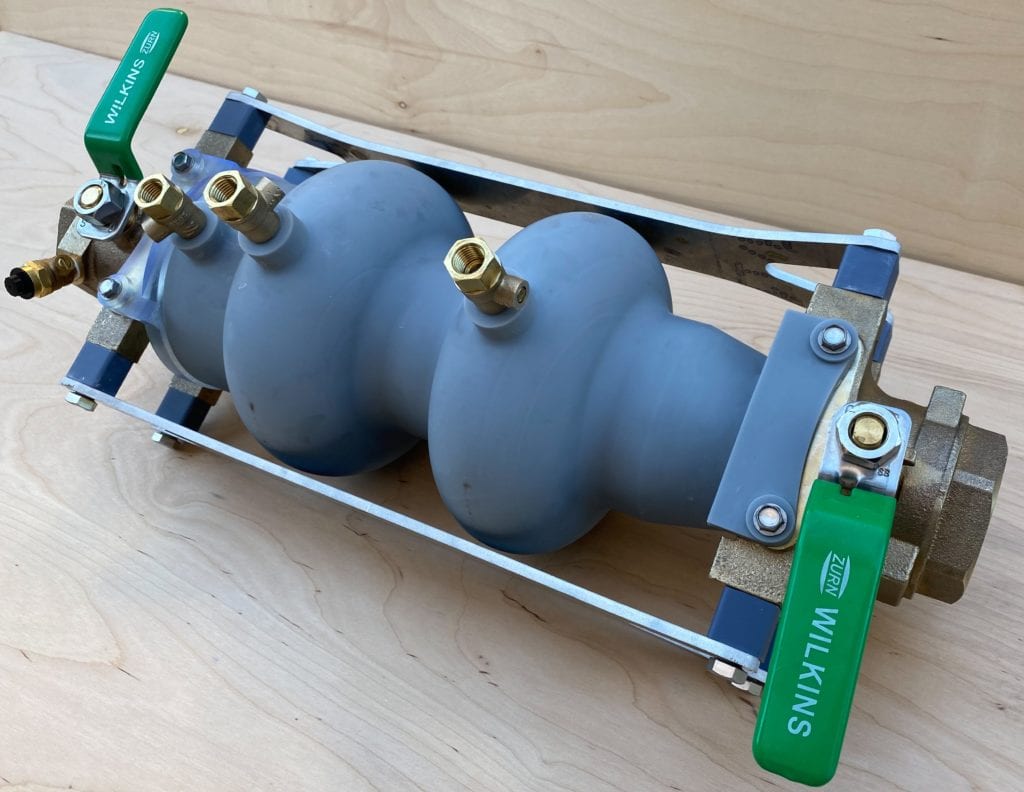
Based on the results of the pressure differential testing, our design did not perform better than the Zurn 350XL. However, there is still further potential testing to establish which aspects of our design caused it to not perform as well as expected compared to our CFD model.
Given time for additional design and testing iterations, we would have liked to further explore our geometry changes by setting the poppet travel at different positions with spacers and testing for the pressure drop. This would provide a more complete understanding of how geometry modifications effect pressure loss. With this data we could determine how far the poppet moved through its travel during the previously performed pressure differential tests. Other avenues we would have liked to pursue would be to test new combinations of housings and poppets between the Zurn 350XL and our modified design.