Our Team
We are a team of Mechanical Engineering seniors interested and involved in robotics applications.
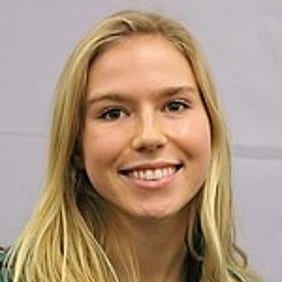
Michelle Chandler
I am a fourth year mechanical engineering student with a concentration in mechatronics. My interests lie in aeronautical engineering and robotics applications.
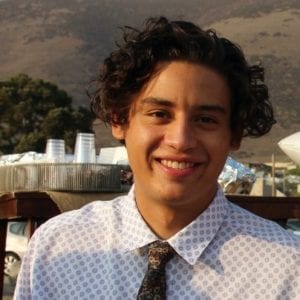
Jacob Nelson
I am a fourth year mechanical engineering student concentrating in general mechanical engineering. I am very passionate about design in aeronautical, automotive, and robotic industries.
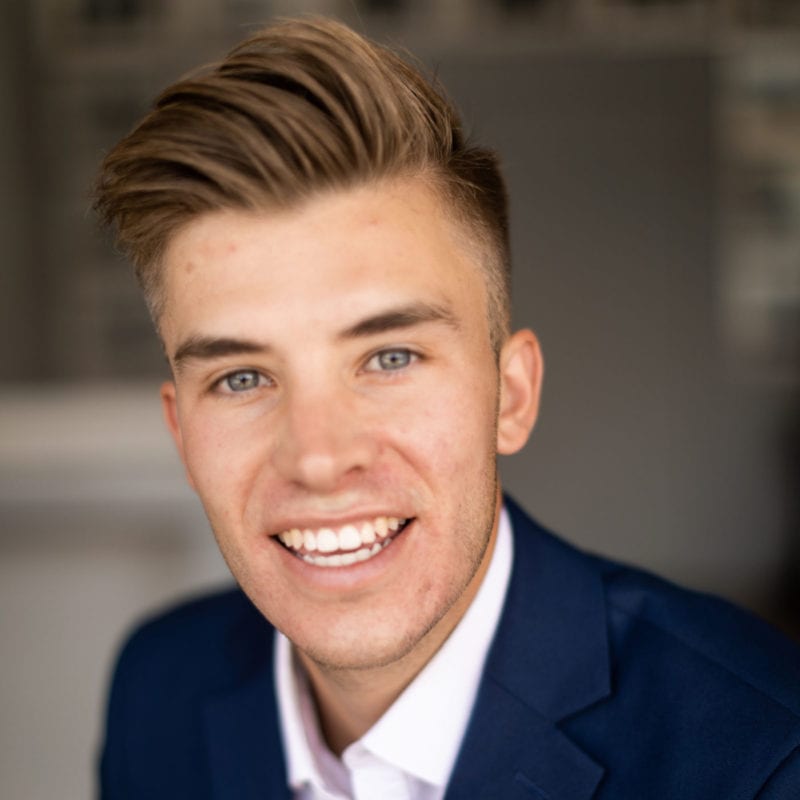
Adam Ivelia
I am fourth year mechanical engineering student with a concentration in manufacturing. I love all things design and manufacturing specifically within aerospace, defense, sports, and outdoor industries.
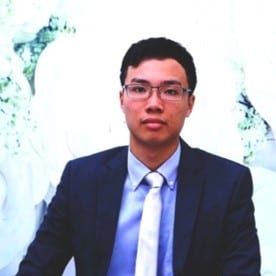
Quang Truong
I am text block. Click edit button to change this text. Lorem ipsum dolor sit amet, consectetur adipiscing elit. Ut elit tellus, luctus nec ullamcorper mattis, pulvinar dapibus leo.
Acknowledgements
We would like to thank the Cal Poly Machine Shop technicians for their assistance with our manufacturing, our sponsors, Blueline Robotics for their support and resources, and our project advisor, Professor Sarah Harding, for her invaluable insight and advice.
Our Project's Videos
Our Project's Digital Poster
Problem Statement
Blueline Robotics requires the development of an attachment system that will allow their robot to be fitted with a variety of tools so that it may be used for a multitude of missions and situations. The modular attachment system will improve the robot’s performance by allowing for the quick switching of tools while on the ground, providing first responders with the flexibility to assess a situation and determine the best course of action.
Design Constraints
- Withstand maximum cantilever load of 25lbs.
- Be waterproof to IP65.
- Able to support a variety of attachments and interface with mechatronic systems.
- Survive rugged terrain and rough treatment.
Design Process
Initial Design
Our initial design utilized 4 springs for suspension and a gardenia connector for the quick release mechanism. This gardena connector was a collar that was pulled open by the user, allowing for the insertion of tools, and which snapped closed, holding those attachments in place.
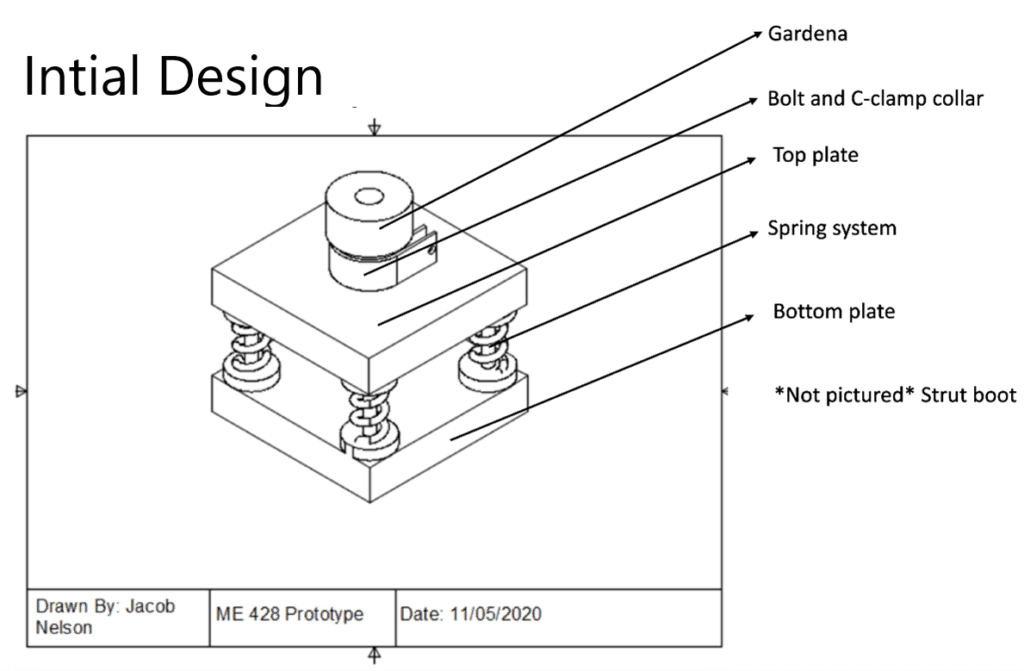
First iteration of the design.
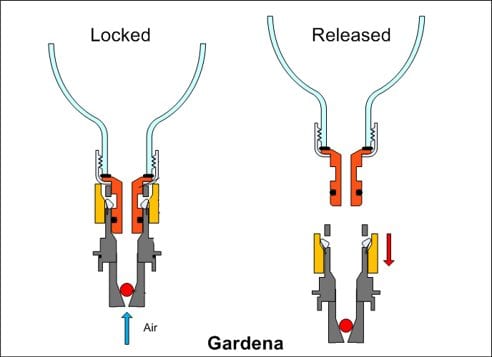
Cross-sectional view of the gardena connector concept
Issues with the Initial Design
Available gardenia connectors were too small for our design and manufacturing a custom connector would be too costly to be feasible. We replaced the gardena connector with a simpler bayonet locking mechanism, seen in the Final Design section.
The spring suspension system had issues with pinch points and instability. Replacing the springs with a polyurethane jounce bumper corrected these issues.
Industrial pins were added to the design to provide support under loading and to restrict the movement of the top plate.
Final Design
Top Assembly
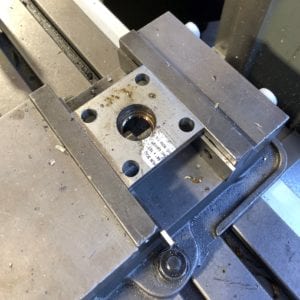
The bottom plate in the vise of the manual mill.
Consists of:
- Bayonet Locking Mechanism: Mating interface between the attachments, such as the robotic arm, and the main robot. Locking the two halves together is as simple as pushing the two together and twisting.
- Top Plate: connects the bayonet locking mechanism to the suspension assembly and provides clearance holes for the suspension system to move through
The Top Assembly’s function is to connect to attachments.
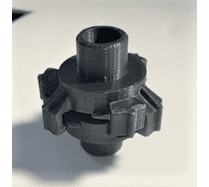
The two halves of the bayonet locking mechanism when they are locked together. This is a 3D printed model
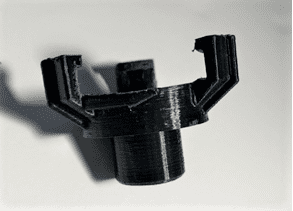
One half of the bayonet locking mechanism. Note the three fins which move on tracks on the opposite half, identical to the tracks seen on this one.
Absorption System
Consists of:
- Industrial Pins: Provides support to the jounce bumper under applied dynamic loads by keeping the top plate constrained to vertical motion.
- Industrial Pin Nuts: Prevents the top plate from separating from the rest of the design.
- Jounce Bumper: Polyurethane jounce bumper that absorbs vibrations and isolates the attachment from vibrations from the main chassis
The absorption assembly’s function is to isolate the attachments from vibrations from the main chassis, allowing for greater precision and clarity from the tools.
Other design choices to note:
- The jounce bumper is epoxied onto the top and bottom plates to ensure a waterproof seal.
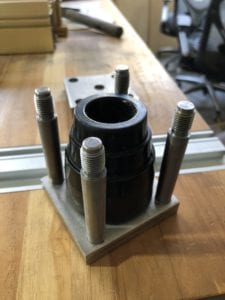
The bottom plate with the press-fitted industrial pins and the jounce bumper in the center. Does not include the Top Assembly.
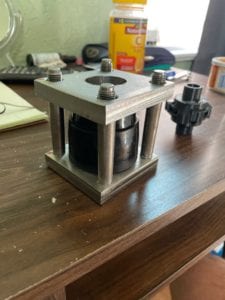
The same picture as to the right except with the top plate on top. The threaded portion of the rod sits above the top plate, allowing for the nuts to be screwed on.
Bottom assembly
Consists of:
- Bottom Plate: Provides the base that the industrial pins are set into and that the jounce bumper is epoxied to. Will be connected directly to the main chassis
Other design choices to note:
- The bottom plate was designed in place of directly building the attachment system into the chassis. This is in part to provide extra modularity for the system. Another reason for this bottom plate was that we were not given any specs on the main chassis of the robot.
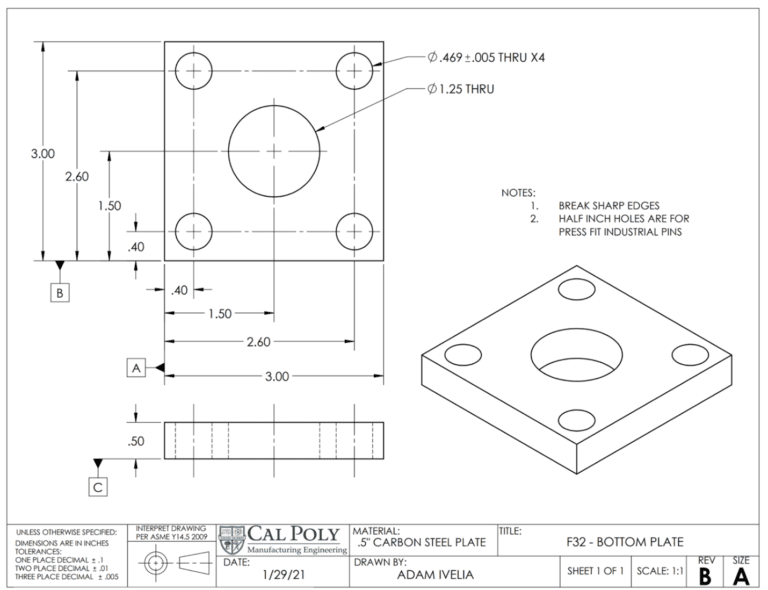
The bottom plate with press-fitted pins and epoxied jounce bumper.
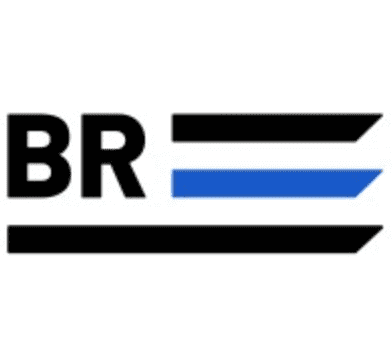
Blueline Robotics
Design Verification
Finite Element analysis
Finite Element Analysis (FEA) was completed on the design with focus on the bayonet locking mechanism, the top and bottom plates, and the industrial pins. This testing was completed using SolidWorks. The passing criteria for this test was as follows:
- The maximum displacement of the parts should not exceed .002mm.
- The safety factor for the material strengths should be no less than 5.
Three different load conditions were tested:
- Cantilevered load accelerating horizontally and vertically at 2 radians per second.
- The impact force of the robot tipping over onto the arm attachment.
- The axial force of 50lbs on the system from heavy attachments.
In a static study, the bottom plate was defined as fixed in the places it would be welded to the main robot chassis. A rectangular block was fixed over the top bayonet connector piece to simulate a miscellaneous attachment for the robot. The different load cases were then applied to this mock attachment piece.
Bayonet Locking Mechansim fea
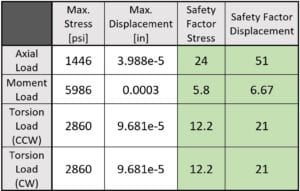
This table summarizes the quantitative results of all of the different load cases placed on the bayonet locking mechanism. The table shows that the locking mechanism meets both passing criteria for each test.
Top and Bottom Plates fea
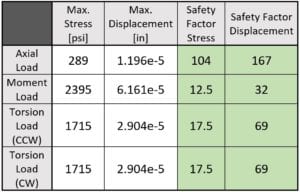
This table summarizes the quantitative results of all of the different load cases placed on the top and bottom plates. The table shows that the plates meet both passing criteria for each test.
industrial pins fea
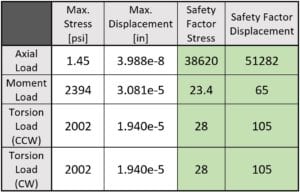
This table summarizes the quantitative results of all of the different load cases placed on the industrial pins. The table shows that the pins meet both passing criteria for each test.
Absorption System Testing
To complete the absorption testing, a phone with an accelerometer application and the complete prototype was required. The phone was secured to the top of the prototype with the accelerometer application running. The prototype was then subjected to vibrations. This process was run in two different trials: one with the jounce bumper active, one without the jounce bumper active. The data from the accelerometer application for each trial were compared to see if the amplitude of vibrations was lower when the jounce bumper was active. The amplitudes of vibration were nearly identical for each trial showing that the attachment system was unable to absorb vibrations. Recommendations to fix this issue and allow the attachment system to absorb vibrations are outlined in the Recommendations sections.
WaterProof Testing
To test if the design is watertight to an IP65 standard it must be able to stay dry when subjected to a water jet. This test was conducted using a garden hose as a water jet. There are three epoxy seals that must keep the inside of the attachment system dry to an IP65 standard. There are two that connect the jounce bumper to the top and bottom plate and on inside the bayonet locking mechanism keeping the bushing sealed. Each one of these epoxy seals had the water jet directed at them for a minute. Each seal was tested three times. At the end of each test the inside of the jounce bumper and bayonet locking mechanism was visually inspected to see if any water got in. All nine tests succeeded in keeping the inside of the attachment system dry and it was determined that the attachment system is watertight to an IP65 standard.
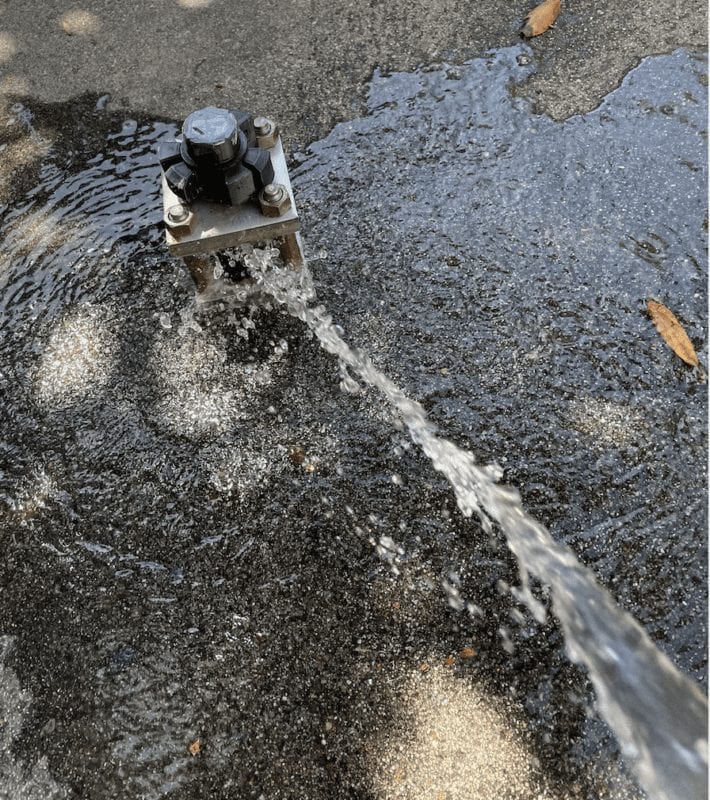
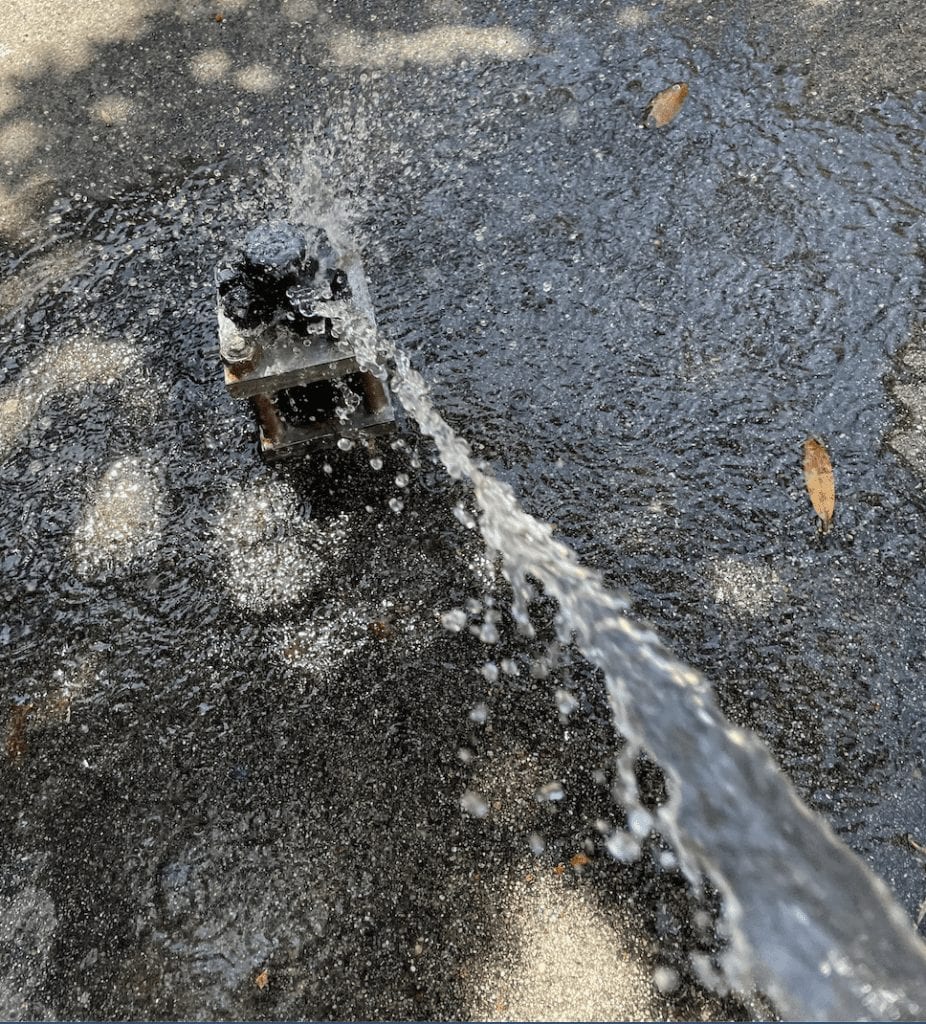
Quick Release Testing
Ideally the bayonet locking mechanism will be cast and welded directly onto the top plate. Due to time and financial constraints the bayonet locking mechanism was 3D printed and epoxy sealed into the top plate. This was then tested to see if the time to attach and detach the two halves of the bayonet locking mechanism was under the allotted 8 minutes. Using a timer on a phone, the time to attach and detach the attachments system was recorded 20 times each. An average of this data was found resulting in an average attach time of 1.65 seconds and an average detach time of 1.65 seconds. This is well under the allotted 8 minutes and so it was determined that the attachment system succeeds in being quick release.
Power Passing Testing
To test if power can be passed from the chassis of the robot through the attachment system and into the attachments the completed prototype and a power cord were required. The power cord was physically passed through the attachment system, proving that power would be able to pass through.
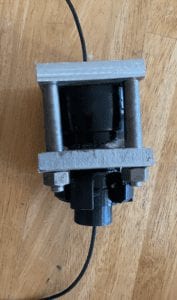
Next, a test was conducted to ensure the power cord would not be damaged via pinching or crushing. While the power cord was passing through the attachment system a 25 pound weight was placed on top of the prototype for 10 seconds. After 10 seconds the power cord was removed and visually inspected for any sign of pinching or crushing. There was no sign of pinching or crushing and so it was determined that the power cord will not be damaged while the attachment system is supporting the dynamic loads.
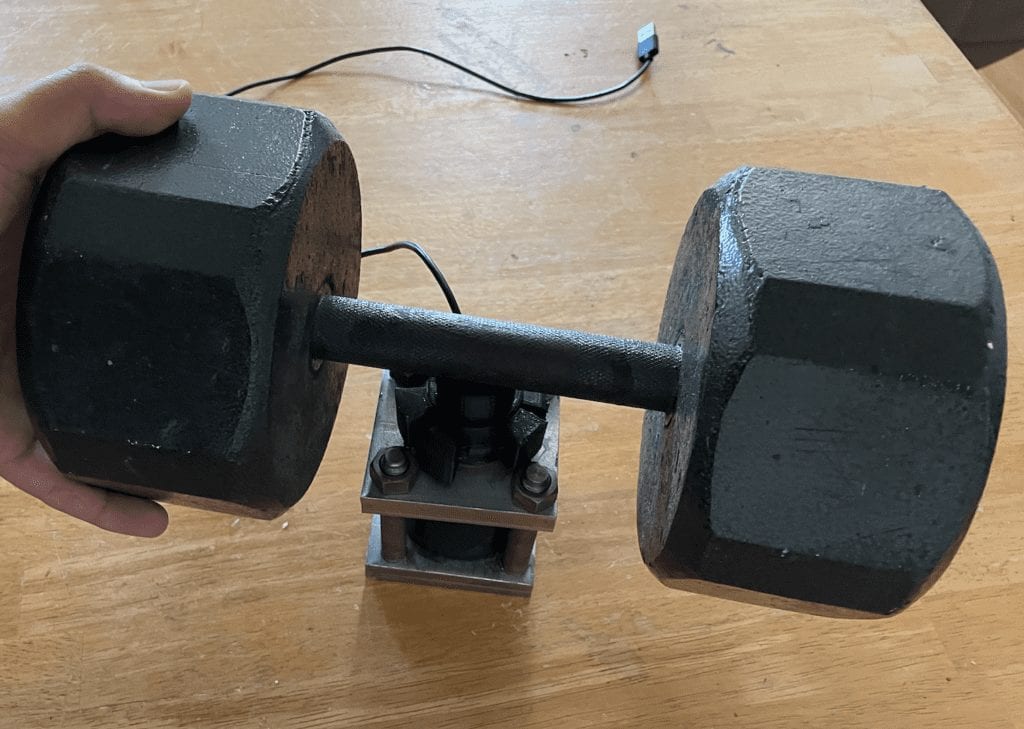
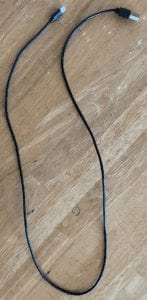
Final Design
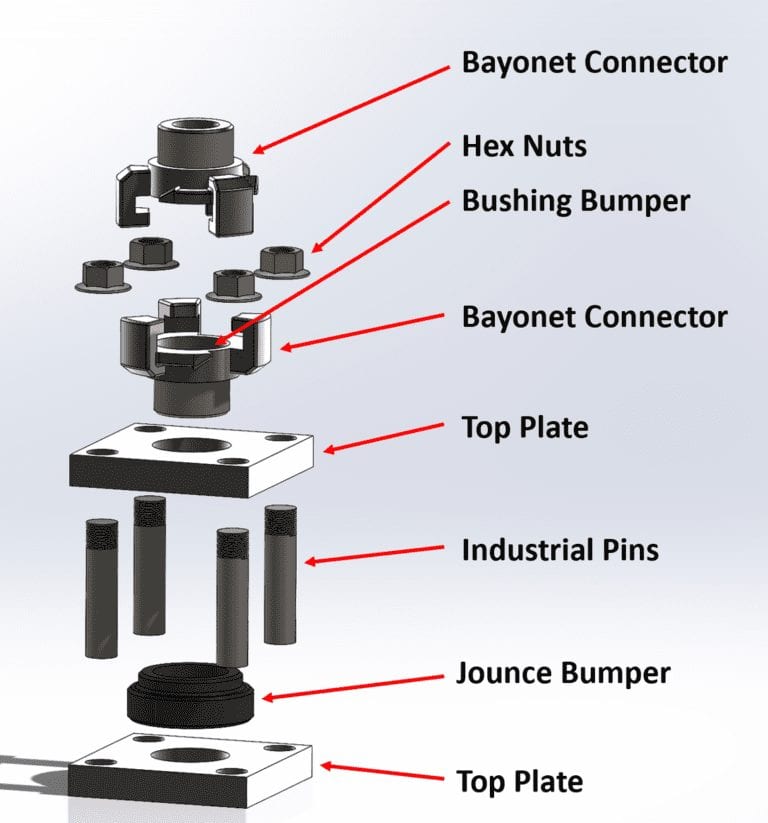
Custom Components
- Bottom Plate
- Top Plate
- Bayonet Locking Mechanism
Stock Components
- Industrial Pins
- Jounce Bumper
- Bushing
Manufacturing Process
Part Procurement
The stock industrial pins and jounce bumper components outlined in the Final Design section were ordered online from McMASTER-CARR. The stock bushing is a medium/soft 92A skateboard bushing bought online from Shorty’s Doh Doh Skate Bushings. The bottom and top plates were bought as 6″x6″ and a 1/2″ thick plates from McCarthy Tank and Steel. The bayonet locking mechanism was 3D printed by one of the team members using their personal 3D printer. All together the cost of part procurement totaled $131.77 which is well within the allotted budget of $500.
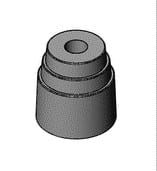
The CAD model of the polyurethane jounce bumper from McMaster-Carr
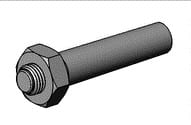
The CAD model of the industrial pins from McMaster-Carr
MANUFACTURING
The top and bottom plates were cut to size. The five holes in the bottom plate were cut using a manual mill. To ensure the tight tolerances of the holes were met, each hole was milled with multiple passes. A slow speed was required so that the material was not heated to the point of hardening and tapping oil was used to reduce this friction heat.
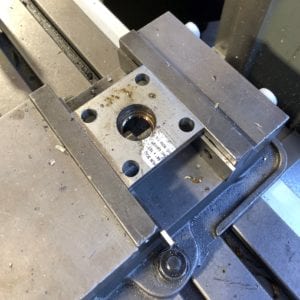
The bottom plate in the vise of the manual mill.
The same process of the bottom plate was repeated with the top plate, using the manual mill.
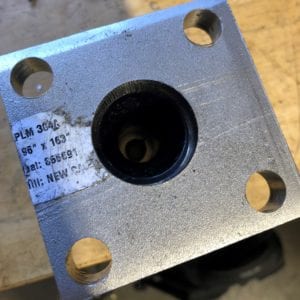
The deburred plate post-milling process.
The top and bottom plates were then deburred and measured to make sure the tolerances were met. The jounce bumper was shortened using a saw for a better fit between the plates.
ASSEMBLY
The industrial pins were press fit into the bottom plate with Loctite metal adhesive. Next, the jounce bumper was sealed to the bottom plate using epoxy. The entire circumference of the jounce bumper was sealed with epoxy thoroughly, leaving no gaps to ensure a water tight seal.
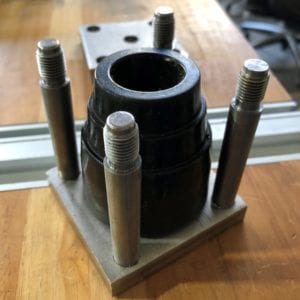
The bottom plate with press-fitted pins and epoxied jounce bumper.
The top plate was then placed over the industrial pins to rest on the jounce bumper. The jounce bumper was then sealed to the top plate using epoxy. Once the epoxy had set, the four nuts were screwed onto the industrial pins. After this, the bayonet locking mechanism was placed into the center hole on the top plate and sealed in using epoxy to ensure a watertight seal. Lastly, the bushing was sealed to the inside of the bayonet locking mechanism.
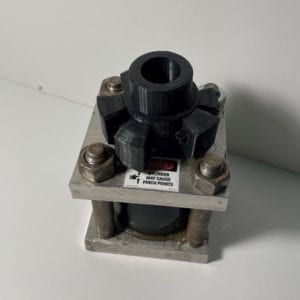
The final assembled prototype.
CHALLENGES
Top and Bottom Plates
Originally the plates were going to be manufactured using a CNC mill. We weren’t able to find a shop technician willing to take on this project for us. Instead, the holes in the plates had to be manually milled. The manually milled plates:
- Have a lower tolerance
- Take more time to manufacture.
- Are made of stainless steel leading which is very difficult to mill.
Bayonet Locking Mechanism
There was also difficulty finding a way to manufacture the bayonet locking mechanism. Due to the complexity of the part it is impossible to manually machine, and nearly impossible to machine using a CNC mill. For the final prototype, the mechanism was 3d printed. We recommend Blueline Robotics cast this part in the future, as they plan to produce these parts on a large scale.
Recommendations
We recommend machining the top and bottom plates using a CNC machine. The small tolerances required for the interference holes in the bottom plate and the clearance holes on the top plate were difficult to get on the manual mill. Using a CNC machine will save time and money.
Due to time and financial constraints the bayonet locking mechanism for this prototype was 3D printed. For large scale production of this attachment system we recommend that the bayonet locking mechanism be cast due to the complexity of the part.
This prototype failed to absorb vibrations due to the stiffness of the jounce bumper. We recommend that a jounce bumper with a lower stiffness be used. This will allow the system to absorb more vibrations allowing the attachments to operate with a higher degree of accuracy. It is also believed that the testing method used was not accurate enough. It is suggested that the attachment system be tested in a vibrations lab using an accelerometer and a shake table.