About Me
My name is Alex Laurence and I am a 4th year MATE student. I am currently working full-time at Lawrence Livermore National Laboratory as a Metrology Engineer for the NIF and enjoy spending my free time rock climbing, surfing, or hiking.
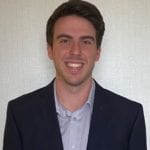
I came up with the idea for directly recycling plastic at the consumer level during my freshman year of college. I later pitched the idea to my advisor, Professor Jean Lee, and, after several meetings and emails where we refined the scope of the project, I decided to pursue it for my senior project. While COVID did restrict some aspects of the experiment, we were able to adapt and collect meaningful data to support the proposed design.
Acknowledgements
I would like to thank Professor Jean Lee for her help with navigating senior project during COVID, MATE Alumnus Cristian Sion for his generous donation of a 3D printer and advice about 3D printing, 2nd-year MATE student Sydney Fultz-Waters for her help my lab assistant and the MATE department for allowing me to use their facilities to complete my project.
Analysis of the Use of Waste Material in 3D Printing
Problem Statement
- Inefficiencies in large scale recycling programs lead to large operational costs and contaminated material. This, along with lack of access to recycling programs in many areas around the world, is a significant contributing factor to only 9% of plastic by mass being recycled globally. The rest ends up in landfills or as pollution in the environment.
- Additionally, 3D printed parts often include a plastic infill to provide structural support. This infill, however, wastes plastic that will often end up in landfills.
Solution
- Allowing consumers to directly convert polyethylene terephthalate (PET) waste into 3D filament can increase the recycling rate by reducing contamination and costs from traditional large-scale recycling methods.
- Replacing polylactic acid (PLA) infill material with wheat straw pulp can reduce plastic consumption for 3D printed parts while still providing structural support and utilizing a material that would typically be unused.
Proposed Designs
- Recycled 3D Printer Filament Production
- An axially symmetric PET bottle is first cut into a strip with a rectangular cross section in a process similar to peeling an apple (Figure 1). Strips from previous bottles are joined by spot melting.
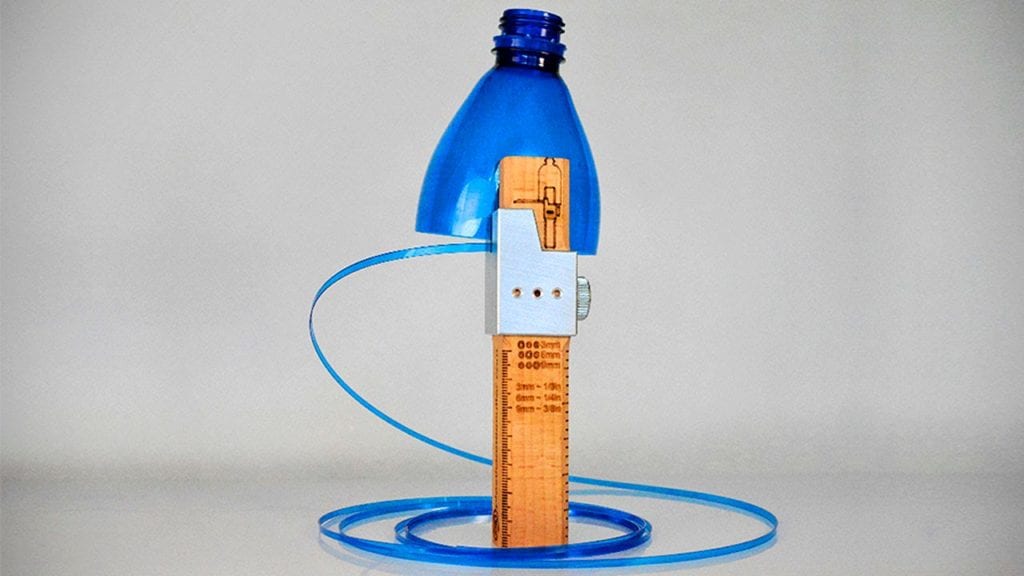
- The strip is then heated within its the glass transition region and fed between two rollers with semi-circular indentations to produce a filament (Figure 2).
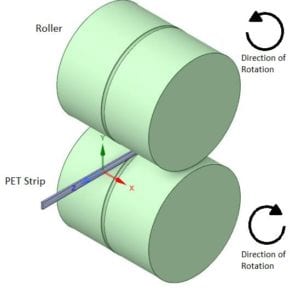
- New filament is then fed into 3D printer and used to print new parts.
- Wheat Straw Pulp as Infill Substitute
- 3D printed parts are made of two components, the shell (which gives the part its shape) and the infill (which provides structural support) (Figure 3).
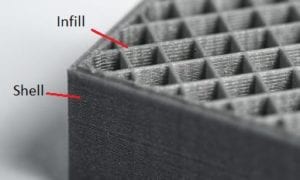
- Removing some of the structurally supportive lignin and cellulose from the straw can allow it to form a pulp. The shape of this pulp is easily manipulated when wet and retains its shape once dry. Depositing it layer by layer in an intermediate step of the 3D printing process should produce a biodegradable infill substitute.
Methodology
Recycled 3D Printer Filament Tests
- One Sided Roller Test
- To determine how well PET can be deformed at various temperatures in the glass transition region by rolling, PET strips were deformed with one roller.
- First, a 1 cm by 7 cm PET strip was cut from a PET water bottle.
- The strip was then placed on an aluminum cooking sheet with steel weights on each end of the sample to prevent deformation due to the heat.
Methodology (cont'd)
- One Sided Roller Test (cont’d)
- Samples were then placed at low, mid, and high temperatures in PET’s glass transition region for 15 minutes and then quickly removed from the oven and deformed (Figure 4).
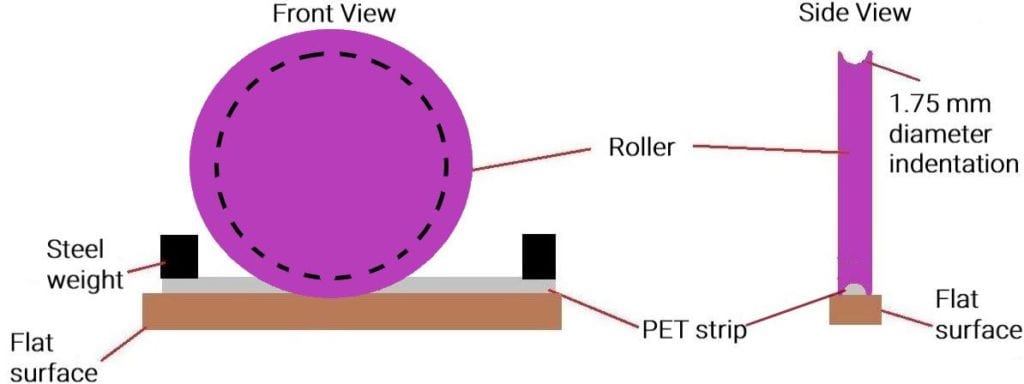
- Gravity Extrusion Test
- To determine whether the bottles can be recycled into filament at a small scale through extrusion due to gravity, 5 g of PET strips were cut into 1 cm by 1 cm squares and placed into a 5 cm diameter Teflon coated steel well with a 1.75 mm diameter hole drilled at the bottom (Figure 5). The plastic was then heated to 260 °C for 30 minutes and results were observed.
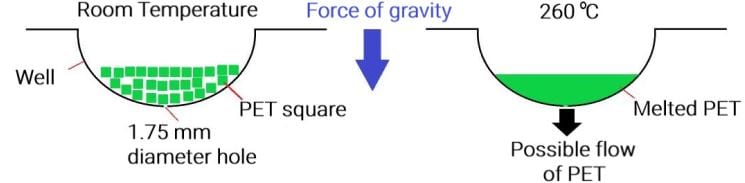
Wheat Straw Infill Test
- 50 g of EZ-StrawTM brand wheat straw was placed in a 1 L solution of water containing 11 g of NaOH to remove lignin and cellulose. The solution was boiled for 2 hours and mixed every 15 minutes. The waste liquid was then drained and the pulp was rinsed with water to remove any remaining NaOH.
- The pulp was then blended until no particles larger than 1 cm in length could be visually detected. After draining the excess liquid, the remaining pulp was placed in a baker’s icing bag and extruded into strips. The strips of wheat straw pulp were then deposited into a 50 mm x 50 mm x 25 mm PLA frame to fill 50% of the area by volume. The infill was then allowed to dry before compression testing. The maximum load experienced by the sample was then compared to the maximum load withstood by equally sized PLA frames with no infill and 12.7% PLA infill by volume. 12.7% PLA infill was chosen because, at this percentage, the mass of the PLA infill is the same as the mass of the 50% wheat straw infill.
Results
Recycled 3D Printer Filament Tests
- One Sided Roller Test
- At 95 °C, a hollow ridge shape was produced by permanent deformation (Figure 6). The diameter was inconsistent and the cross section was hollow.
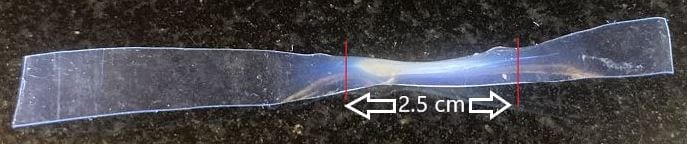
- At 135 °C, the cross-section in the deformed area was solid and there was a consistent diameter of 1.5 mm +/- 0.05 mm (Figure 7).
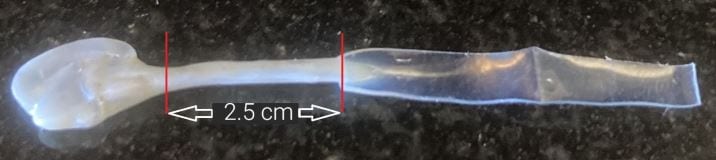
- At 275 °C, the PET adhered to the roller and tray, producing a non-usable filament.
- Gravity Extrusion Test
- 5 g of PET produced no filament, so PET was added in increments of 2.5 g until filament was produced at 12.5 g.
- After 30 minutes, 4 mm of filament was produced with a diameter of 1.7 mm +/- 0.05 mm. This is equivalent to a feed rate of 0.07 mm/s.
Wheat Straw Infill Test
- The frame without any infill supported a maximum load of 616 N.
- The frame with 50% wheat straw infill by volume supported a maximum load of 1495 N.
- The frame with 12.7% PLA infill by volume supported a maximum load of 2700 N.
- The maximum loads of all three samples can be seen in Figure 8.
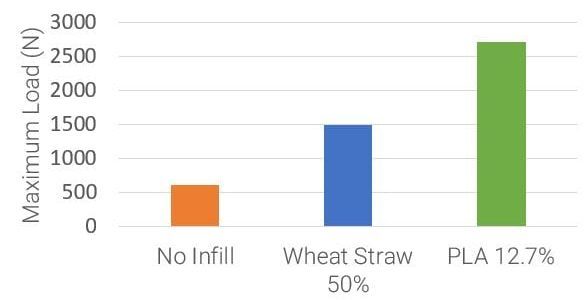
Analysis
- One Sided Roller Test
- PET strips deformed in the middle of the glass transition region (around 175 °C) formed a filament with a solid semicircular cross section similar to a traditional filament. The diameter of the deformed strips was uniform. Adjusting the diameter of the roller indentation and the width of the PET strip should increase the average diameter to 1.75 mm.
- PET strips that were heated to temperatures in the lower part of the glass transition region did not produce a filament with a solid or uniform cross section.
- PET strips heated to the upper glass transition region were too sticky to be used.
- Gravity Extrusion Test
- The feed rate was 0.07 mm/s, however, a typical 3D printer requires a 5.6 mm/s feed rate.
- When modeling the extrusion process as a billet extrusion, the following equation was used:
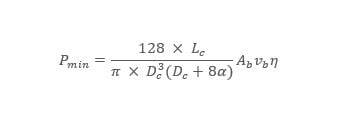
- where:
- Pmin = the minimum pressure required to extrude
- Lc = the length of the die channel
- Dc = the diameter of the die
- Ab = the area of the billet (in this case the cross-sectional area of the top of the cake pop well)
- vb = the ram speed
- ƞ = the viscosity of the PET
- α = the slip coefficient of the surface
- The minimum pressure required to extrude a PET filament to be fed directly into a 3D printer was determined to be 92.6 kPa. This seemed unusually large compared to the observed results. To verify this, the maximum pressure due to gravity was found for the 12.5 g of PET and a die with 1.75 mm diameter using the following equation.
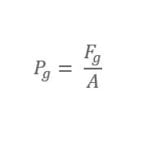
where:
Pg = the pressure exerted on the liquid by gravity
A = the cross-sectional area of the die
Fg = the force of gravity on the liquid
- The maximum pressure experienced by the PET was 12.7 kPa. This difference in theoretical vs observed pressure is likely due to the difference in feed rates. Typical 3D printers require a feed rate of 5.6 mm/s; however, the observed feed rate was 0.07 mm/s. The larger required feed rate was used to calculate the billet velocity in the first equation.
- To reach desired pressure, a minimum of 1 kg of PET is required which may be difficult to maintain at a small scale.
Wheat Straw Infill Test
- Wheat straw can be used in prints with lower load requirements, however, long drying times and shrinking make wheat straw pulp unattractive for directly printing infill into 3D printed parts that typically require fast production times.
- Printing infill ahead of may save time by removing drying step and shrinking will no longer be an issue. The dried infill can then be quickly added in an intermediate printing step.
Conclusions
- Deforming a PET strip through rolling produces a filament with the best properties when heated to 175 C
- Fully melting PET and extruding with gravity alone can produce filament provided sufficient PET is present.
- Wheat straw is a viable alternative to PLA infill for 3D printed parts with low strength requirements.
- Citations
- (1) Plastic Bottle Cutter. https://www.kickstarter.com/projects/910418035/plastic-bottle-cutter (accessed March 29, 2021).
- (2) Cain, P. Selecting the optimal shell and infill parameters for FDM 3D printing. https://www.hubs.com/knowledge-base/selecting-optimal-shell-and-infill-parameters-fdm-3d-printing/ (accessed Mar 12, 2021).
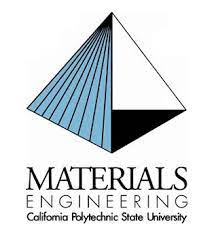
This project was sponsored by the Cal Poly MATE department