Our Team: SAVER 1 (Body & Payload)
We are a team of three senior Mechanical Engineering students at Cal Poly SLO
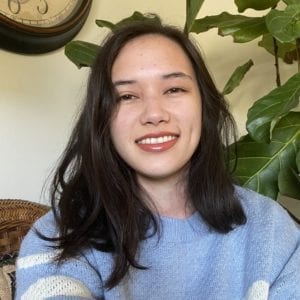
Holly Johnson
I am a fourth-year mechanical engineering student concentrating in manufacturing. I have worked in the aerial firefighting industry and have additional experience and interest in aerospace, manufacturing, automotive, and audio.
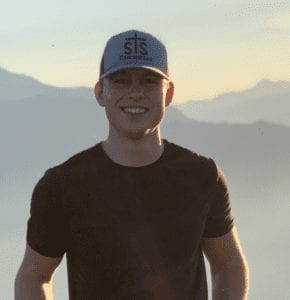
Adam Swarthout
I am a fourth-year mechanical engineering student with a general concertation. Upon graduation, I plan to work in the aerospace industry working to modify decommissioned military aircraft for commercial use.
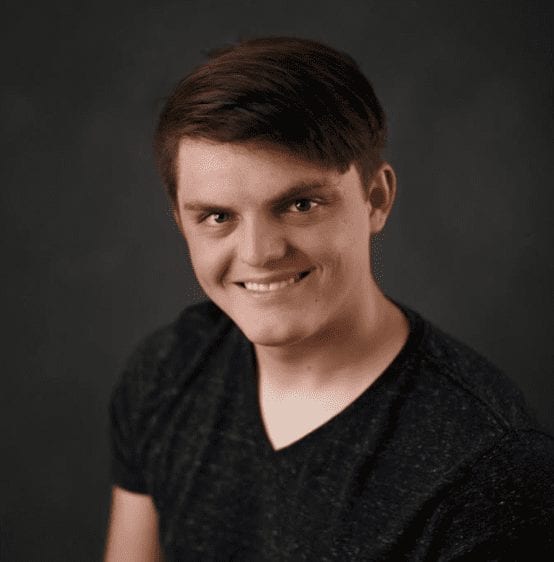
Zach Rannalli
I am a fifth-year mechanical engineering student in the general concentration. I want to go into the aerospace field and more specifically the space travel/satellite industry.
Acknowledgements
We would like to acknowledge the Cal Poly Mechanical Engineering Department for their funding and resources. We would also like to thank our advising coach Sarah Harding for her guidance and help along the way. Lastly, we would finally like to acknowledge our sister team SAVER 2 (Navigation & Controls) for their companionship and contribution throughout this journey.
Our Project's Videos
The following video introduces our project and design.
Our Project's Digital Poster
Problem Statement
Create an autonomous surface vehicle to locate and bring supplies to astronauts in the case of a maritime event where the team responsible for retrieving them is unable to get to them in a timely manner.
Design Constraints
- – Minimum drop height of 2 m
- – Minimum top speed of 2 m/s
- – Fully autonomous operation
Design Choices
Scaled design by half:
- After not being selected for the second phase of competition, the team decided to half the scale of the project for time and resource benefits.
Other design choices to note:
- – Flat top allows antenna and payload box to be secured externally.
- – Hull is 3D printed for ease of manufacturing.
- – Hull thickness of 5mm for contact area during assembly, surface area for the waterproofing gasket, and strength during the drop.
Design Verification
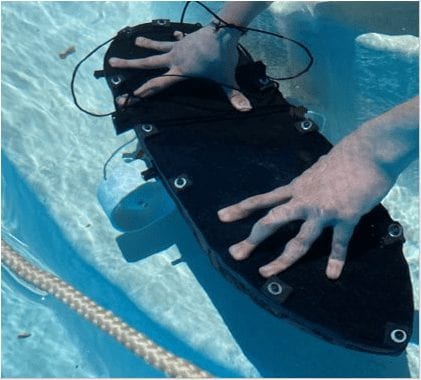
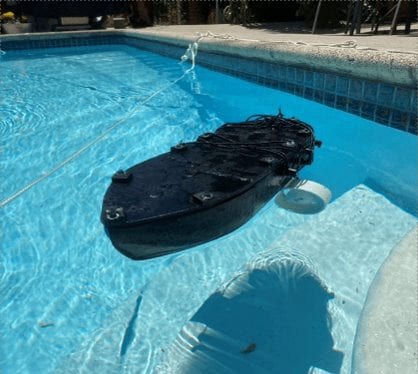
Waterproofing Test (left): In order to verify that SAVER is waterproof it was held underwater for about 20 seconds, while the team watched for any air bubbles coming out from the seams. The team found no leaks in the hull.
Stability Test (right): SAVER was placed on the water with the propellers attached. The team identified the angle SAVER sat in the water. They then put a 500 gram weight on the lid at various locations and recorded the angle of the vehicle at each location. It was concluded that SAVER is stable and will stay upright during operation.
Impact Test: The team dropped SAVER from two meters above the surface of the water five times and checked for any loss of integrity after each drop. The center section of the hull cracked after the first test, and the team rectified this by increasing the thickness of the hull and reprinting it. The team concluded that SAVER had survived all the drops with no damage after the reprint.
Payload Detachment Test: SAVER was put into the water with the Pelican Box secured on top. Two team members then attempted to retrieve the box using their dominate hand, non-dominate hand, and gloved dominate hand. It was concluded that the box is able to be taken off with ease in all cases.
Analysis
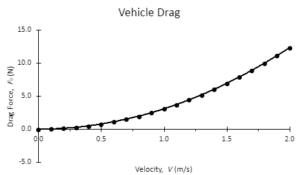
The graph shows how the drag force changes as a function of velocity.
The team also used the sum of moments about the CG in order to find the best location for the propellers to be so that the vehicle does not over rotate when accelerating.
The team also found the velocity that the vehicle will hit the water from different heights.
CAD Models
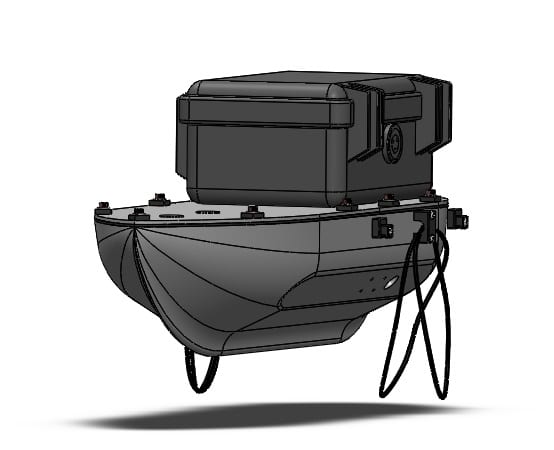
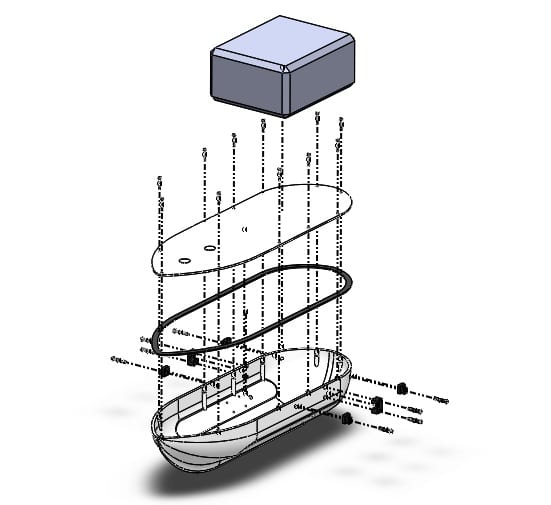
Final Design
Specifications
Weight: 7.594 kg
Dimensions: 525mm X 175mm X 110mm
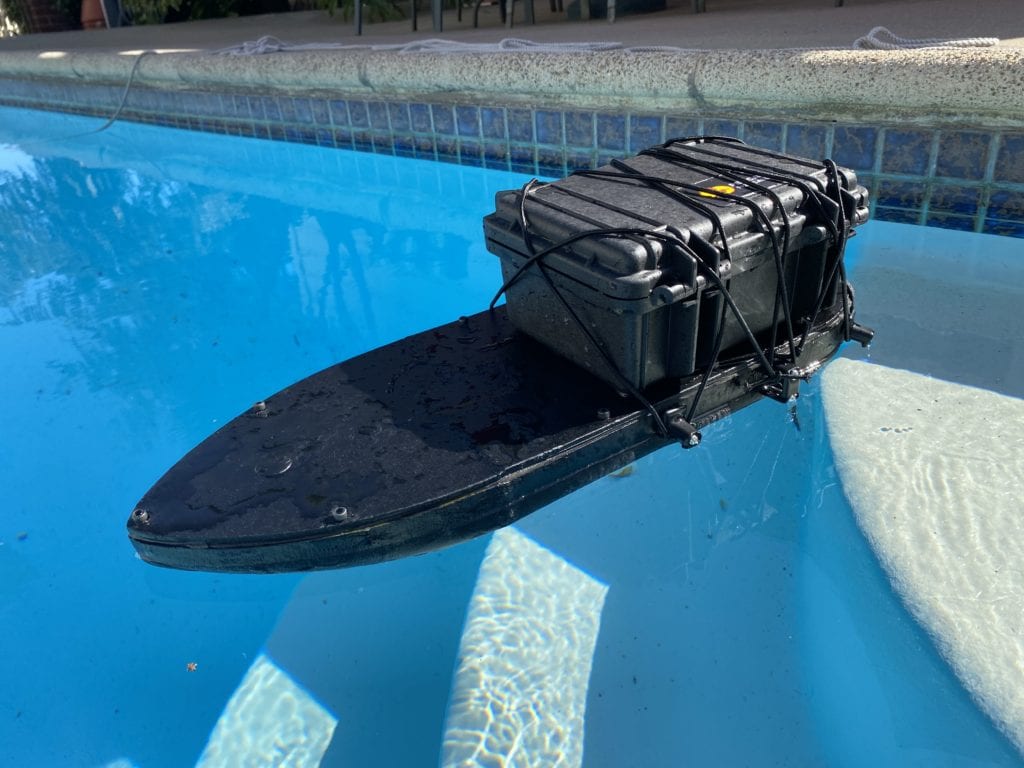
Custom/Modified Components
- – 3-D printed hull
- – 3-D printed lid
- – Weatherproofing foam with adhesive
- – Elastic cables
Stock Purchased Components
- – 1120 Pelican Box
- – Flex Seal Spray Rubber Sealant
- – M4 Cap Screws
- – M4 Nuts
- – M4 Washers
- – Payload securing connectors
Future Application
SAVER can have many helpful uses once has been fully developed and tested and is ready to be produced. One is the main purpose sought out by the competition; using SAVER to locate and provide astronauts with survival supplies. After SAVER has been put in to practice it could be use for civilian or coast guard uses too, in order to help bring small payloads to people that may be stuck somewhere or even used to locate a boat is displaying a distress signal.
Recommendations
Recommendations for future teams taking on the SAVER project:
- – Maintain constant communication with team members.
- – Iterate early and iterate often.
- – The vehicle is prone to being top-heavy, which interferes with stability. Ballasts are the most efficient way to bring the center of gravity down and toward the center.
- – Use heat-set inserts if working with threaded fasteners and plastics.
- – Avoid 3D printing for the final model if possible. Larger models require lots of print time and resources, and the process of joining pieces together with plastic welding is very time consumptive.